高炉冶炼的理化过程
冶金概论5-高炉冶炼的基本原理(二)

(2)煤气分布得到改善,中心煤气明显发展, 从而有利于均匀炉缸温度。喷吹后,煤气中的H2 量增多,气体粘度减小,煤气渗透能力提高。 (3)炉缸冷化,顶温升高,有热滞后现象。
炉缸冷化是指风口前理论燃烧温度(风口 前燃料燃烧产生的热量全部用于加热燃烧产物所 能达到的温度)降低。
热滞后现象是指高炉增加喷吹量后,由于 入炉总燃料量增加,炉温本应升高。但在喷吹之 初,炉缸温度不升反而暂时下降,过一段时间后, 炉缸温度才上升的一种现象。
为液态,金属铁与炉渣也完全分离开来,金属铁 经固体焦炭缝隙往下流动。
金属铁在下降过程中继续渗碳,并且不断吸 收由液态渣中还原出来的铁和其他合金元素。
炉渣则在下降过程当中,由于还原作用, FeO含量继续降低,SiO2和MnO含量也由于Si和 Mn还原进入生铁而有所降低。
另外由于熔剂CaO不断溶入渣中,故渣的碱 度不断提高。
很显然,只有当F>0时炉料才能下降;F愈 大,则愈有利于炉料顺利下降;当F接近或等于零 时,则炉料产生难行或悬料。
需要指出的是,要使炉料顺利下降(可简称 为顺行),不仅要求整个料柱的F大于零,而且还 要求各个不同高度截面上和同一截面不同位置上 的F大于零。
显然,某处的F=0时,则该处的炉料 处于悬料状态。
高炉内不断出现的自由空间只是为炉料的下降 创造了先决条件,但炉料能否顺利下降。还取决于 下述的力学关系:
F=Q-(P1+P2+△P)=Q有效- △ P 式中 F—炉料下降有效作用力; Q—炉料的自重; Pl—炉料与炉墙之间的摩擦力; P2—炉料之间的摩擦力; △ P—上升煤气对炉料的阻力; Q有效—料柱有效重量。
八 高炉强化冶炼
高炉强化冶炼的主要目的是提高产量, 即提高高炉有效容积利用系数。
高炉炼铁的原理及化学方程式

高炉炼铁的原理及化学方程式高炉炼铁的原理是什么样子的?下面由小编为你精心准备了“高炉炼铁的原理及化学方程式”,持续关注本站将可以持续获取更多的考试资讯!高炉炼铁的原理炼铁过程实质上是将铁从其自然形态——矿石等含铁化合物中还原出来的过程.炼铁方法主要有高炉法、直接还原法、熔融还原法等.其原理是矿石在特定的气氛中(还原物质CO、H2、C;适宜温度等)通过物化反应获取还原后的生铁.生铁除了少部分用于铸造外,绝大部分是作为炼钢原料.高炉炼铁是现代炼铁的主要方法,钢铁生产中的重要环节.这种方法是由古代竖炉炼铁发展、改进而成的.尽管世界各国研究发展了很多新的炼铁法,但由于高炉炼铁技术经济指标良好,工艺简单,生产量大,劳动生产率高,能耗低,这种方法生产的铁仍占世界铁总产量的95%以上.高炉生产时从炉顶装入铁矿石、焦炭、造渣用熔剂(石灰石),从位于炉子下部沿炉周的风口吹入经预热的空气.在高温下焦炭(有的高炉也喷吹煤粉、重油、天然气等辅助燃料)中的碳同鼓入空气中的氧燃烧生成的一氧化碳和氢气,在炉内上升过程中除去铁矿石中的氧,从而还原得到铁.炼出的铁水从铁口放出.铁矿石中不还原的杂质和石灰石等熔剂结合生成炉渣,从渣口排出.产生的煤气从炉顶导出,经除尘后,作为热风炉、加热炉、焦炉、锅炉等的燃料.炼铁的原理化学方程式炼铁的原理化学方程式:FeO+CO=Fe+CO2、Fe0+C=Fe+CO。
炼铁的原理是将铁矿石、油、煤、焦炭等原料放入高炉中加热,将铁中的氧夺取出来从而形成铁的过程。
高炉冶炼用的原料主要由铁矿石、燃料(焦炭)和熔剂(石灰石)三部分组成。
高炉炼铁的特点:规模大,不论是世界其它国家还是中国,高炉的容积在不断扩大,如我国宝钢高炉是4063m3。
生铁是高炉产品(指高炉冶炼生铁),而高炉的产品不只是生铁,还有锰铁等,属于铁合金产品。
锰铁高炉不参加炼铁高炉各种指标的计算。
高炉炼铁过程中还产生副产品水渣、矿渣棉和高炉煤气等。
高炉炼铁的主要工艺流程

高炉炼铁的主要工艺流程
《高炉炼铁的主要工艺流程》
高炉是钢铁企业中用于炼铁的主要设备,其工艺流程是将铁矿石和焦炭加入高炉内,经过一系列的化学和物理反应,最终得到熔融的生铁。
下面将介绍高炉炼铁的主要工艺流程。
1. 搅拌坩埚法:将原铁矿石和焦炭按一定的比例混合,放入高炉的上部,即炉料层。
在高炉内,炉料层受到高温和高压的影响,发生一系列的物理和化学反应。
2. 燃烧:通过给炉料层加入空气或者氧气,点燃炉料层的顶部,使其燃烧。
燃烧产生的热量使炉料层内的焦炭燃烧,并提供高温条件,促进各种反应的进行。
3. 还原反应:当焦炭燃烧释放出一定量的一氧化碳时,与高炉内的铁矿石发生还原反应,使氧化铁还原为生铁。
4. 精炼:在高温下,生铁中的杂质和一些有害元素(如硫、磷等)会被氧化成气体,并通过炉顶排出。
这一过程称为精炼,是炉料中杂质清除的重要环节。
5. 收得生铁:经过一定时间的冶炼,高炉内的炉料最终产生了熔融的生铁。
生铁通过炉口排除,并进入铁水槽中,成为炼铁的产物。
通过上述简单介绍,可以看出高炉炼铁的主要工艺流程是一个
复杂的过程,包括搅拌坩埚法、燃烧、还原反应、精炼和收得生铁等环节。
这一流程不仅需要科学合理的原料比例和控制方法,还需要高炉操作者的丰富经验和技巧。
只有合理的工艺流程和专业的操作技术,才能保证高炉炼铁的顺利进行和生产出优质的生铁产品。
炼铁工艺05高炉冶炼过程的物理化学

高炉冶炼主要是以 CO 和 C 作为还原剂,还原区域的温度一般不大于 1500℃, 在此条件下,CaO、A1203 和 MgO 在高炉冶炼过程中不可能被还原。
氧化物中的金属(或非金属)和氧亲和力的大小,也可用氧化物的分解压力 大小来表示,即氧化物的分解压力越小,元素和氧的亲和力越大,该氧化物越稳 定。
用 H2 还原铁氧化物高炉在不喷吹燃料条件下,煤气中 H2 量一般在 1.8-2.5% 范围内,主要是鼓风中水分被 C 还原产生的。在喷吹煤粉、天然气等燃料时,煤 气中 H2 浓度显著增加。H2 和氧的亲和力很强,可夺取铁氧化物中的氧而作为还原 剂。
所以固体碳还原铁氧化物反应,只表示最终结果,反应的实质仍是 CO 在起 作用,最终消耗的是碳素。
反应 FeO 十 C=Fe 十 CO 的进行,决定于 C02 十 C=2CO 反应的速度。实验指 出:C02 与 C 作用达到平衡,其速度是很慢的。650 ℃时,大约需要 12h;800 ℃ 时需要 9h;温度愈低,用固体碳进行还原愈难。由于高炉内煤气流速很高,在 温度大于 700-730℃时,C02 十 C=2CO 反应有可能达到平衡,即 FeO 可用 C 进行 还原。但因碳的气化反应速度很慢,C 还原 FeO 的作用很小。只有在 800~850 ℃ 时,FeO 被 C 还原才较明显;激烈地进行反应则在 1100℃以上。
高炉炼铁的原理

高炉炼铁的原理
简介
高炉炼铁是一种重要的冶炼工艺,通过高炉将铁矿石和焦炭等原料还原为铁。
高炉通常是一个巨大的金属容器,内部通过高温反应实现铁的冶炼。
原料
铁矿石是高炉炼铁的主要原料之一,常见的铁矿石包括赤铁矿、磷铁矿等。
此外,焦炭、石灰石等原料也是高炉炼铁中必不可少的。
原理
1.燃烧过程: 高炉中焦炭等燃料在燃烧时产生高温,燃气通过矿石料床
加热矿石,并在还原区域发生还原反应。
2.还原反应: 在高炉内,煤气经过还原区域与铁矿石中的氧化铁发生反
应,将氧还原为气态二氧化碳,释放出铁。
3.融化过程: 上述反应产生的铁在高温下融化,并通过热对流从上向下
移动到高炉的熔融区域。
4.炉渣形成: 高炉中产生的碳酸化合物和石灰石在高温下融化形成炉渣,
在铁水表面形成保护膜,防止铁的再氧化。
冶炼过程
高炉炼铁过程通常会经历炉料下料、补料、冶炼、出铁等阶段。
整个过程需要
严格调控高炉的温度、气氛、矿石的质量等参数,以确保炼铁效果。
结论
高炉炼铁是一项复杂的冶炼过程,通过高炉的高温还原反应,将铁矿石转化为铁。
高炉炼铁工艺的改进和提高效率对于保障铁铸造业的发展至关重要,进一步
提高炼铁效率和降低成本是未来的发展方向。
高炉工作原理

高炉工作原理
高炉是一种高温冶金设备,用于将铁矿石转化为熔化的铁合金。
高炉的工作原理如下:
1. 原料准备:高炉的主要原料包括铁矿石、焦炭和通风剂。
这些原料首先要经过粉碎和筛分等预处理工艺,以确保其适合进入高炉。
2. 上料:原料按一定比例混合后,通过上料装置从高炉顶部加入高炉内。
铁矿石是高炉的主要原料,而焦炭用作还原剂,在高温下还原铁矿石中的氧化物。
3. 加热和还原:高炉内有复杂的燃烧反应和还原反应同时进行。
焦炭燃烧产生的高温气体在高炉内上升,将其余的氧气与铁矿石中的氧化物反应,还原为金属铁。
这些反应释放出的热量使高炉内的温度升高。
4. 分层和液态铁收集:高炉内的液态铁和其他熔融物质从高炉的底部逐渐下降,并沉积在炉底的铁口处。
液态铁具有相对较高的密度,因此能够与其他杂质分离。
由于高炉内的温度很高,液态铁在下降的过程中可以重新还原铁矿石中的氧化物。
5. 出炉和冷却:经过一定时间的冶炼,高炉内的炉渣和液态铁会分别从不同的出料口排出。
此后,液态铁将被收集并转移到下一个冶炼环节中进行进一步的处理。
而废炉渣则会被冷却和处理,使其能够更方便地处理和回收。
高炉工作原理的核心是通过高温和还原反应将铁矿石转化为液态铁。
高炉除了生产铁合金外,还会产生大量的炉渣和废气。
因此,在高炉冶炼过程中,也需要采取措施进行环境保护和资源回收。
高炉炼铁的原理及工艺流程
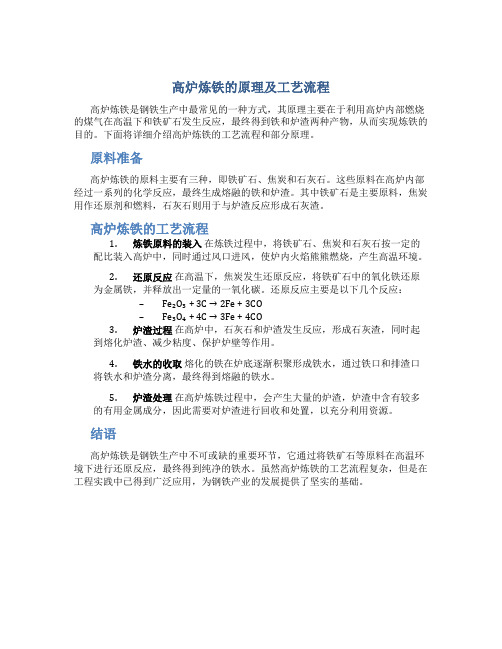
高炉炼铁的原理及工艺流程
高炉炼铁是钢铁生产中最常见的一种方式,其原理主要在于利用高炉内部燃烧的煤气在高温下和铁矿石发生反应,最终得到铁和炉渣两种产物,从而实现炼铁的目的。
下面将详细介绍高炉炼铁的工艺流程和部分原理。
原料准备
高炉炼铁的原料主要有三种,即铁矿石、焦炭和石灰石。
这些原料在高炉内部经过一系列的化学反应,最终生成熔融的铁和炉渣。
其中铁矿石是主要原料,焦炭用作还原剂和燃料,石灰石则用于与炉渣反应形成石灰渣。
高炉炼铁的工艺流程
1.炼铁原料的装入在炼铁过程中,将铁矿石、焦炭和石灰石按一定的
配比装入高炉中,同时通过风口进风,使炉内火焰熊熊燃烧,产生高温环境。
2.还原反应在高温下,焦炭发生还原反应,将铁矿石中的氧化铁还原
为金属铁,并释放出一定量的一氧化碳。
还原反应主要是以下几个反应:–Fe₂O₃ + 3C → 2Fe + 3CO
–Fe₃O₄ + 4C → 3Fe + 4CO
3.炉渣过程在高炉中,石灰石和炉渣发生反应,形成石灰渣,同时起
到熔化炉渣、减少粘度、保护炉壁等作用。
4.铁水的收取熔化的铁在炉底逐渐积聚形成铁水,通过铁口和排渣口
将铁水和炉渣分离,最终得到熔融的铁水。
5.炉渣处理在高炉炼铁过程中,会产生大量的炉渣,炉渣中含有较多
的有用金属成分,因此需要对炉渣进行回收和处置,以充分利用资源。
结语
高炉炼铁是钢铁生产中不可或缺的重要环节,它通过将铁矿石等原料在高温环境下进行还原反应,最终得到纯净的铁水。
虽然高炉炼铁的工艺流程复杂,但是在工程实践中已得到广泛应用,为钢铁产业的发展提供了坚实的基础。
高炉炼铁工艺流程
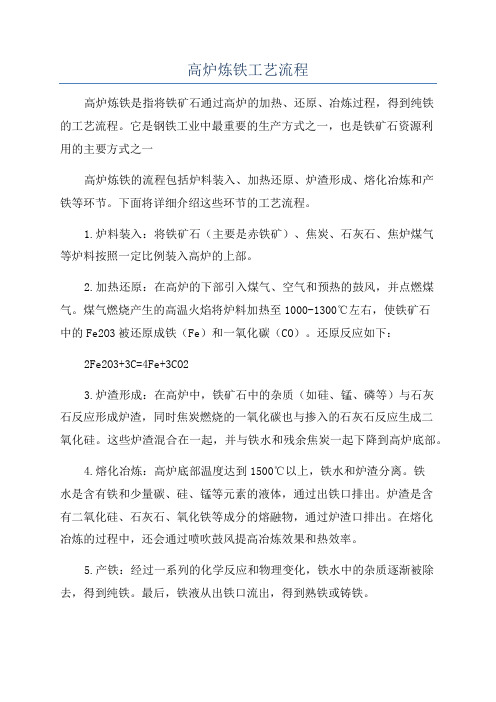
高炉炼铁工艺流程
高炉炼铁是指将铁矿石通过高炉的加热、还原、冶炼过程,得到纯铁
的工艺流程。
它是钢铁工业中最重要的生产方式之一,也是铁矿石资源利
用的主要方式之一
高炉炼铁的流程包括炉料装入、加热还原、炉渣形成、熔化冶炼和产
铁等环节。
下面将详细介绍这些环节的工艺流程。
1.炉料装入:将铁矿石(主要是赤铁矿)、焦炭、石灰石、焦炉煤气
等炉料按照一定比例装入高炉的上部。
2.加热还原:在高炉的下部引入煤气、空气和预热的鼓风,并点燃煤气。
煤气燃烧产生的高温火焰将炉料加热至1000-1300℃左右,使铁矿石
中的Fe2O3被还原成铁(Fe)和一氧化碳(CO)。
还原反应如下:2Fe2O3+3C=4Fe+3CO2
3.炉渣形成:在高炉中,铁矿石中的杂质(如硅、锰、磷等)与石灰
石反应形成炉渣,同时焦炭燃烧的一氧化碳也与掺入的石灰石反应生成二
氧化硅。
这些炉渣混合在一起,并与铁水和残余焦炭一起下降到高炉底部。
4.熔化冶炼:高炉底部温度达到1500℃以上,铁水和炉渣分离。
铁
水是含有铁和少量碳、硅、锰等元素的液体,通过出铁口排出。
炉渣是含
有二氧化硅、石灰石、氧化铁等成分的熔融物,通过炉渣口排出。
在熔化
冶炼的过程中,还会通过喷吹鼓风提高冶炼效果和热效率。
5.产铁:经过一系列的化学反应和物理变化,铁水中的杂质逐渐被除去,得到纯铁。
最后,铁液从出铁口流出,得到熟铁或铸铁。
- 1、下载文档前请自行甄别文档内容的完整性,平台不提供额外的编辑、内容补充、找答案等附加服务。
- 2、"仅部分预览"的文档,不可在线预览部分如存在完整性等问题,可反馈申请退款(可完整预览的文档不适用该条件!)。
- 3、如文档侵犯您的权益,请联系客服反馈,我们会尽快为您处理(人工客服工作时间:9:00-18:30)。
高炉冶炼的理化过程
高炉冶炼是一种重要的冶金工艺,用于将铁矿石转化为生铁。
在高炉中,铁矿石经过一系列的物理和化学反应,最终得到生铁。
高炉冶炼的过程可以分为三个阶段:预处理阶段、还原阶段和熔化阶段。
首先是预处理阶段。
在这个阶段,铁矿石会经过破碎、筛分和烘干等处理。
破碎是为了减小矿石的颗粒大小,使其更容易进行下一步的处理。
筛分是将破碎后的矿石按照颗粒大小进行分类,以便更好地控制冶炼过程。
烘干是为了去除矿石中的水分,以防止水分对冶炼过程的干扰。
接下来是还原阶段。
在高炉中,矿石中的铁氧化物需要被还原成金属铁。
还原反应是高炉冶炼中最重要的反应之一。
在高炉内,由于高温和还原剂(如焦炭)的作用,铁氧化物中的氧被还原成气体,而铁被还原成金属形态。
这个过程中产生的气体主要是一氧化碳和二氧化碳,它们在高炉中的上升过程中带动了矿石和焦炭的下降,形成了高炉的逆流运动。
最后是熔化阶段。
在还原阶段之后,金属铁和熔渣混合物会下降到高炉的下部。
在下部,金属铁会逐渐熔化,并与熔渣分离。
熔渣是由矿石中的非金属成分和冶炼过程中添加的石灰石等物质组成的。
熔渣的主要作用是吸收和分离金属铁中的杂质,使得最终得到的生铁质量更纯净。
在熔化阶段,高炉内部温度极高,达到了1500摄氏度以上,这使得金属铁能够熔化,而熔渣则保持在液态状态。
总结起来,高炉冶炼的理化过程包括预处理、还原和熔化三个阶段。
通过这些过程,铁矿石中的铁氧化物被还原成金属铁,并与熔渣分离,最终得到生铁。
高炉冶炼是一种复杂的物理和化学过程,需要严格控制温度、压力和流动等参数,以确保冶炼过程的顺利进行。
这种冶炼工艺在现代工业中仍然具有重要的地位,为人们提供了大量的铁合金和其他铁制品。