PVD薄膜沉积工艺及设备
半导体pvd设备原理

半导体pvd设备原理
半导体物理气相沉积(PVD)设备是一种常用于制备薄膜材料的技术。
这种设备基于物理原理,通过在真空环境下加热材料,使其升华并沉积在基底上,形成所需的薄膜。
PVD设备的工作原理如下:
将待沉积的材料放置在真空室中。
真空室的设计是为了排除外部空气,以确保材料在无氧环境下处理。
然后,通过加热材料,使其升华成为气态。
升华的材料蒸汽会扩散到真空室中,并沉积在基底表面上。
基底通常是需要涂覆薄膜的物体,例如电子器件或太阳能电池。
沉积过程可以通过不同的方法实现。
其中一种常用的方法是磁控溅射,它利用磁场将金属靶材的离子击打到基底上。
这种方法可以控制沉积速率和薄膜的成分。
另一种常用的方法是电子束蒸发,它使用电子束加热材料,使其升华并沉积在基底上。
电子束蒸发具有较高的沉积速率和较好的薄膜均匀性。
PVD设备的优点在于可以制备高质量的薄膜,并具有较好的控制能力。
通过调节沉积条件,可以控制薄膜的成分、厚度和结构。
这使得PVD设备在半导体制造、光电子学和纳米器件制备等领域得到广泛应用。
然而,PVD设备也存在一些局限性。
首先,沉积速率相对较低,需要较长的时间来制备较厚的薄膜。
此外,PVD设备对材料的选择性较差,只能用于制备一些高熔点的材料。
总的来说,半导体PVD设备是一种重要的制备薄膜材料的工具。
通过控制沉积条件,可以制备具有特定性质和结构的薄膜,满足不同应用的需求。
随着技术的不断进步,PVD设备将继续在材料科学和工程中发挥重要作用。
pvd涂层工艺

pvd涂层工艺PVD涂层工艺是一种常见的表面处理技术,用于在各种材料上形成薄膜涂层。
PVD是物理气相沉积(Physical Vapor Deposition)的缩写,主要包括蒸发、溅射和离子镀等技术。
PVD涂层工艺的基本原理是利用物理方法将固态材料转化为气态,然后通过沉积在工件表面形成一层薄膜。
首先,将待处理的材料作为靶材放置在真空腔室中,然后通过加热或者离子轰击等方式将靶材转化为气态,形成蒸汽。
接着,将工件放置在腔室的靶材正对位置,通过离子轰击或者磁控溅射等方式将蒸汽沉积在工件表面,形成均匀而致密的薄膜涂层。
PVD涂层工艺具有许多优点。
首先,由于是在真空环境下进行,因此可以避免氧化和污染等问题,从而提高了涂层的质量和附着力。
其次,PVD涂层可以在各种材料上进行,如金属、陶瓷、玻璃等,具有广泛的应用范围。
此外,PVD涂层具有较高的硬度、耐磨性和耐腐蚀性,可以提高材料的使用寿命和性能。
根据不同的需求,PVD涂层可以选择不同的工艺。
其中,蒸发是最常见的一种工艺,通过加热靶材使其蒸发,然后在工件表面形成涂层。
溅射是另一种常用的工艺,通过离子轰击靶材使其溅射,然后沉积在工件表面。
此外,还有离子镀、磁控溅射等工艺,可以根据具体需要选择合适的工艺。
在实际应用中,PVD涂层工艺具有广泛的应用领域。
例如,在汽车行业中,PVD涂层可以用于改善汽车零部件的耐磨性和耐腐蚀性,提高汽车的整体质量和使用寿命。
在电子行业中,PVD涂层可以用于生产显示屏、太阳能电池等产品,提高其光学性能和耐候性。
此外,PVD涂层还可以应用于航空航天、医疗器械、机械制造等领域,为各种材料赋予特殊的功能和性能。
然而,PVD涂层工艺也存在一些挑战和限制。
首先,PVD涂层的设备和工艺较为复杂,需要高度的技术和设备支持。
其次,涂层的厚度和均匀性受到一定的限制,无法在大面积和复杂形状的工件上实现均匀的涂层。
此外,PVD涂层的成本相对较高,不适合大规模生产。
pvd镀膜设备原理

pvd镀膜设备原理PVD镀膜设备,全称是物理气相沉积(Physical Vapor Deposition)镀膜设备,是一种常用的薄膜制备技术。
它利用高能离子束或高温蒸发源将材料原子或分子蒸发,然后沉积在基底表面,形成均匀的薄膜。
PVD镀膜设备主要包括蒸发源、真空系统和基底台三个组成部分。
蒸发源是主要设备,通过加热材料使其蒸发,并产生高能离子束。
真空系统则能够提供高真空环境,以确保薄膜沉积的质量。
基底台则是放置待镀膜基底的位置。
PVD镀膜设备主要有以下几种工作原理:蒸发、溅射和离子镀。
蒸发是最常见的PVD镀膜技术之一。
蒸发源内的材料通过加热,使其蒸发并沉积在基底上。
蒸发源的加热方式有电阻加热、电子束加热和感应加热等。
蒸发源内的材料蒸发后形成蒸汽,蒸汽经过运输管道进入真空室,在高真空环境下,蒸汽与基底表面相遇,凝结成薄膜。
溅射是另一种常见的PVD镀膜技术。
在溅射过程中,材料源被离子束轰击,使其离子化并溅射出来,然后沉积在基底上。
溅射镀膜可以通过直流溅射、射频溅射、磁控溅射等方式进行。
溅射镀膜的薄膜均匀性更好,适用于复杂形状的基底。
离子镀是一种利用离子束轰击基底表面的技术。
在离子镀过程中,材料被加热并离子化,然后通过高能离子束轰击基底表面,使薄膜原子或分子沉积在基底上。
离子镀技术可用于提高薄膜的致密性和附着力。
PVD镀膜设备在各个领域有着广泛的应用。
在电子行业中,PVD技术可用于制备导电薄膜、光学薄膜和防腐蚀薄膜等。
在光学行业中,PVD技术可用于制备反射镜、透镜和滤光片等。
在装饰行业中,PVD 技术可用于制备金属涂层,增加产品的质感和美观度。
此外,PVD 技术还可用于制备硬质涂层、陶瓷涂层和生物医学涂层等。
总结起来,PVD镀膜设备是一种基于物理气相沉积原理的薄膜制备技术。
通过蒸发、溅射和离子镀等工作原理,能够在基底表面形成均匀致密的薄膜。
该技术在电子、光学、装饰等领域有着广泛应用,为产品的性能和外观提供了强大支持。
pvd原理及工艺流程

pvd原理及工艺流程
PVD(Physical Vapor Deposition)是一种物理蒸发沉积技术,通过将材料加热至蒸发温度,使其蒸发成气态,然后再将蒸发的材料沉积到基材表面形成薄膜。
PVD工艺流程一般包括以下步骤:
1. 清洁基材:将基材放入超声波清洗机中使用溶剂或碱性溶液进行清洗,去除杂质和污垢。
2. 加热基材:将经过清洗的基材放入真空室中,通过加热使其达到蒸发温度。
3. 蒸发源蒸发:打开蒸发源,使其蒸发材料释放出来。
4. 沉积:蒸发材料在真空室中形成气体,然后通过吸附作用沉积到基材表面。
5. 冷却:在沉积过程中,基材需要保持一定的温度以确保薄膜的质量,在沉积完成后,基材需要冷却至室温。
6. 分离:将沉积好的基材从真空室中取出,完成PVD工艺。
PVD工艺流程中的主要设备包括真空室、蒸发源(可以是电阻加热、电子束、离子束等)、
基材夹具、高真空泵等。
不同的材料和应用场景可能会有一些额外的步骤或设备,但整体流程大致相似。
PVD技术广泛应用于镀膜、表面改性和纳米材料制备等领域。
PVD镀膜工艺简介

PVD镀膜工艺简介PVD镀膜(Physical Vapor Deposition)是一种利用物理气相沉积的技术,在高真空环境下,通过蒸发、溅射等方式将金属、合金、化合物等材料以薄膜的形式沉积到基材表面的一种工艺。
PVD镀膜工艺被广泛应用于各个领域,如光学、电子、机械、汽车、建筑等。
蒸发是PVD镀膜中最早应用的一种工艺。
通过加热源将材料加热至蒸发温度,使其转变为气态,然后在真空室内的基板上形成薄膜。
蒸发工艺可以通过电阻加热、电子束加热等方式来进行。
这种工艺的特点是操作简单,成本较低,但适用于蒸发温度较低的材料。
溅射是PVD镀膜中应用较广泛的一种工艺。
通过高能粒子的轰击使靶材表面的原子或离子脱落,然后被沉积在基板表面上形成薄膜。
溅射工艺一般可分为直流溅射、射频溅射、磁控溅射等不同方式。
这种工艺具有较高的沉积速率和较好的膜层均匀性,适用于多种材料的沉积。
离子镀是一种利用离子轰击作用在基材表面上形成薄膜的工艺。
通过向沉积膜层的材料供应高能离子,使其在基板表面发生化学反应并沉积形成薄膜。
离子镀工艺能够提高薄膜的致密性和附着力,适用于复杂形状的基板和高精密要求的镀膜。
在PVD镀膜过程中,需要注意以下几个关键环节。
首先,要确保真空室内的气压稳定,并保持高真空状态,以避免杂质对薄膜质量的影响。
其次,镀膜前需对基材进行表面处理,如清洗、抛光等,以提高薄膜的附着力。
再次,镀膜材料的纯度和均匀性对薄膜性能起着重要影响,因此需要对材料进行精细的处理和选择。
最后,要通过适当的加热、冷却以及离子轰击等方式,使沉积的薄膜具有良好的致密性和均匀性。
PVD镀膜工艺具有许多优点。
首先,它可以在室温下进行,避免了高温对基材产生的热应力和变形。
其次,沉积的薄膜具有较高的质量和均匀性,具有良好的机械性能和化学稳定性。
再次,PVD镀膜可用于多种材料的沉积,如金属、合金、化合物等,具有较大的灵活性和可扩展性。
此外,PVD镀膜还具有低污染性、无溶剂使用、高效节能等环保优势。
pvd电镀工艺流程及详解
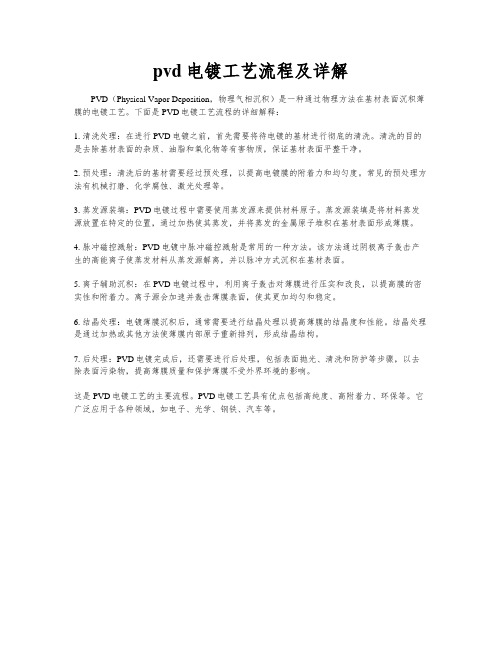
pvd电镀工艺流程及详解
PVD(Physical Vapor Deposition,物理气相沉积)是一种通过物理方法在基材表面沉积薄膜的电镀工艺。
下面是PVD电镀工艺流程的详细解释:
1. 清洗处理:在进行PVD电镀之前,首先需要将待电镀的基材进行彻底的清洗。
清洗的目的是去除基材表面的杂质、油脂和氧化物等有害物质,保证基材表面平整干净。
2. 预处理:清洗后的基材需要经过预处理,以提高电镀膜的附着力和均匀度。
常见的预处理方法有机械打磨、化学腐蚀、激光处理等。
3. 蒸发源装填:PVD电镀过程中需要使用蒸发源来提供材料原子。
蒸发源装填是将材料蒸发源放置在特定的位置,通过加热使其蒸发,并将蒸发的金属原子堆积在基材表面形成薄膜。
4. 脉冲磁控溅射:PVD电镀中脉冲磁控溅射是常用的一种方法。
该方法通过阴极离子轰击产生的高能离子使蒸发材料从蒸发源解离,并以脉冲方式沉积在基材表面。
5. 离子辅助沉积:在PVD电镀过程中,利用离子轰击对薄膜进行压实和改良,以提高膜的密实性和附着力。
离子源会加速并轰击薄膜表面,使其更加均匀和稳定。
6. 结晶处理:电镀薄膜沉积后,通常需要进行结晶处理以提高薄膜的结晶度和性能。
结晶处理是通过加热或其他方法使薄膜内部原子重新排列,形成结晶结构。
7. 后处理:PVD电镀完成后,还需要进行后处理,包括表面抛光、清洗和防护等步骤,以去除表面污染物,提高薄膜质量和保护薄膜不受外界环境的影响。
这是PVD电镀工艺的主要流程。
PVD电镀工艺具有优点包括高纯度、高附着力、环保等。
它广泛应用于各种领域,如电子、光学、钢铁、汽车等。
PVD镀膜工艺范文

PVD镀膜工艺范文PVD(Physical Vapor Deposition)是一种通过物理手段将具有良好特性的薄膜沉积在基底材料表面的工艺。
它是一种干法沉积工艺,主要适用于金属、陶瓷和有机材料的沉积。
1.蒸发法:蒸发法主要通过加热源将材料加热到高温,使其蒸发成气态后,通过凝结在基底材料表面。
蒸发法主要分为电子束蒸发和电弧蒸发两种。
电子束蒸发是将材料放置在真空腔中,利用加热的钨丝或电铲,通过加热材料使其蒸发成气态,然后通过真空腔中的电子束,将材料蒸发沉积在基底材料表面。
这种方法最大的优点是沉积速度快,但腔体设计复杂,设备价格较高。
电弧蒸发是将材料放置在电弧区域中,通过电弧的高温熔化材料,使其蒸发成气态,然后通过电弧区域的高能电子束,将材料蒸发沉积在基底材料表面。
这种方法的优点是设备价格较低,但沉积速度较慢,由于电弧区域会产生气体等污染物质,膜的制备也较为复杂。
2.溅射法:溅射法是利用高能离子轰击材料表面,将材料溅射成离子,然后沉积在基底材料表面。
溅射法主要分为磁控溅射、电弧溅射、激光溅射等。
磁控溅射是最常见的溅射方法之一,它通过在真空腔中施加磁场,电离气体形成的离子在磁场的作用下,从材料表面溅射。
这种方法优点是可以得到均匀的膜厚,且适用于多种材料的沉积。
电弧溅射是在电弧区域形成高温电弧,使材料表面离子化并溅射出去,然后通过磁场将离子引导到基底材料表面。
这种方法主要适用于贵金属和高熔点材料的沉积。
激光溅射是通过激光束在材料表面进行高能量的瞬间轰击,使材料离子化并溅射出去,然后通过磁场将离子引导到基底材料表面。
这种方法的优点是可以对不同材料进行选择性的溅射,适用于薄膜和纳米颗粒的制备。
1.防护涂层:PVD镀膜可以形成一层坚硬、耐磨的薄膜,可以增加材料的抗腐蚀性和耐磨性。
在汽车工业、机械工业和航空航天工业中得到广泛应用。
2.装饰涂层:PVD镀膜可以制备出具有不同颜色和光泽度的薄膜,可以用于制作首饰、钟表、厨具等装饰品。
半导体 pvd工艺流程

半导体 pvd工艺流程半导体PVD工艺流程半导体PVD(物理气相沉积)工艺是一种常用的半导体加工技术,主要用于制备薄膜材料,如金属、合金、氧化物等,其工艺流程包括多个步骤,下面将详细介绍。
1. 基片准备半导体PVD工艺的第一步是基片准备。
基片是晶体硅或其他材料的片状基础材料。
在这一步骤中,需要对基片进行清洗,去除表面的杂质和污染物,以确保后续工艺的顺利进行。
常用的清洗方法包括溶液浸泡、超声波清洗等。
2. 蒸发源加载蒸发源是PVD工艺中的关键设备,用于提供薄膜材料。
在这一步骤中,需要将目标材料装载到蒸发源中。
装载时需要注意保持蒸发源的清洁,避免杂质和污染物的混入。
3. 抽真空在半导体PVD工艺中,需要在蒸发室内建立真空环境。
这是为了防止气体分子对薄膜材料的干扰,确保薄膜的质量和性能。
抽真空的过程通常使用真空泵进行,将蒸发室内的气体抽出。
4. 加热基片在进行薄膜沉积之前,需要对基片进行加热处理。
加热可以使基片表面的晶格结构更加均匀,提高薄膜的结晶性和致密性。
加热温度的选择应根据具体材料和工艺要求进行。
5. 蒸发沉积当基片加热到一定温度后,薄膜材料开始从蒸发源中蒸发,并沉积在基片表面上。
蒸发源中的材料会通过热蒸发或电子束蒸发的方式转化为气相,然后在真空环境中沉积在基片上。
6. 薄膜厚度控制在薄膜沉积过程中,需要对薄膜的厚度进行控制。
这可以通过监测薄膜的生长速率和时间来实现。
常用的监测方法包括椭偏仪、石英晶体监测器等。
根据需要,可以采取闭环控制或开环控制的方式进行薄膜厚度的控制。
7. 后处理薄膜沉积完成后,需要进行后处理步骤来改善薄膜的性能。
后处理可以包括退火、氧化、磁控溅射等。
退火可以提高薄膜的结晶性和致密性,氧化可以增加薄膜的化学稳定性,磁控溅射可以改善薄膜的结构和性能。
8. 薄膜性能测试对沉积的薄膜进行性能测试。
常用的测试方法包括薄膜厚度测量、表面形貌观察、结构分析、电学性能测试等。
通过测试可以评估薄膜的质量和性能是否符合要求。
- 1、下载文档前请自行甄别文档内容的完整性,平台不提供额外的编辑、内容补充、找答案等附加服务。
- 2、"仅部分预览"的文档,不可在线预览部分如存在完整性等问题,可反馈申请退款(可完整预览的文档不适用该条件!)。
- 3、如文档侵犯您的权益,请联系客服反馈,我们会尽快为您处理(人工客服工作时间:9:00-18:30)。
五 纳米加工平台现有设备介绍
LAB-18操作注意事项
进行工艺前确保相应电源和工艺气体打开; 对腔体充气时确保打开氮气开关; 升降样品架时确保挡板打开; 充气时确保腔体温度低于50℃; 溅射时确保靶材正常起辉,溅射过程中确保起
辉正常; 溅射时核对溅射材料
31
五 纳米加工平台现有设备介绍
250
Time(S)
Rate
0 0
400
50
100
150
200
250
Time(S)
200
Thick
0 0
50
100
150
200
250
Time(S)
39
Thick(A)
五 纳米加工平台现有设备介绍
ei-5z操作注意事项
开机前注意检查水电气正常; 做工艺之前检查坩埚源的状态,如源不够及
时通知相应工作人员; 禁止在低真空条件下打开电子枪电源; 蒸发前注意晶振片的频率和所要蒸发材料的
热电子由灯丝发射后,被加速阳极加速,获得 动能轰击到处于阳极的蒸发材料上,使蒸发材 料加热气化,而实现蒸发镀膜。
特点:多用于要求纯度极高的膜、绝缘物的蒸 镀和高熔点物质的蒸镀
熔融的 蒸镀源
电子束
水
水冷 坩埚
一 PVD薄膜沉积的基本原理
溅射镀膜
溅射-用带有几十电子伏以上动能的粒子或粒 子束照射固体表面,靠近固体表面的原子会获 得入射粒子所带能量的一部分进而向真空中放 出,这种现象称为溅射。
次4片,小样品夹具
五 纳米加工平台现有设备介绍
LAB18现有靶材
Au、Pt、Ti、Ni、V、AlN、PZT、Al、 Cr、SiO2、Ag、ITO 、Fe、Pd、Ge、 Cu、W、TiN
五 纳米加工平台现有设备介绍
LAB18 工艺参数
本底真空
序 号
靶材
1 Ag
2E-6
预溅 时间
120
温度
溅射 时间
三 PVD薄膜沉积中常见问题
镀膜前对基片进行离子轰击
三 PVD薄膜沉积中常见问题
镀膜时的加热 衬底和膜之间加
入接触金属(Cr、 Ni、Ti、W等)
三 PVD薄膜沉积中常见问题
如何在大台阶表面沉积厚度均匀的 薄膜
三 PVD薄膜沉积中常见问题
基片与蒸发源间的距离 镀膜时的压力 基片加偏压
四 PVD薄膜的表征
PVD薄膜的表征
电学性能:四探针 粘附性:划痕法 内应力:X射线衍射法 膜厚:台阶仪 表面粗糙度:AFM
21
五 纳米加工平台现有设备介绍
磁控溅射-LAB18
22
五 纳米加工平台现有设备介绍
LAB18系统组成
控
抽
制 系
电源
加热
真 空
统
系
统
真空腔体
冷却系统
五 纳米加工平台现有设备介绍
2 50
坩埚号 X/Y—Position
X/Y—Sweep 衬底转(r/m)
预蒸发时间 Gain/Time-C/Limit
Tooling
3
3
3.5
3
0
8
2min
5 5 10
8538五 纳米加工平源自现有设备介绍Power(%)
Rate(A/S)
40 30 20 10
0
5
0
Power
50
100
150
200
电子束蒸发- ei-5z
操作界面
真空腔体
32
五 纳米加工平台现有设备介绍
ei-5z系统组成
控 制
膜
坩
厚
埚
控
电 子 枪
抽 真 空
系
制
系
统
统
真空腔体
冷却系统
五 纳米加工平台现有设备介绍
膜厚控制
监视蒸镀速率的方法 是利用共振的石英晶 体。结晶的石英晶体 具有压电性的,在共 振频率时,石英晶体 产生震荡电压,晶体 放大并回授以驱动晶 体,就可监督蒸镀速 率。
3
一 PVD薄膜沉积的基本原理
PVD技术的分类
物理气相沉积(PVD)
真空蒸镀
溅射镀膜
离子镀
电子束(EB)蒸发 热蒸发 直流溅射 射频溅射 脉冲直流溅射
4
一 PVD薄膜沉积的基本原理
真空蒸镀
真空蒸镀是将镀料在真空中加热、蒸发,使蒸 发的原子或原子团在温度较低的基板上凝结, 形成薄膜。
热蒸发、EB蒸发。
LAB18 Vacuum界面
24
五 纳米加工平台现有设备介绍
LAB18 Deposition界面
25
五 纳米加工平台现有设备介绍
LAB18 腔体内部
26
五 纳米加工平台现有设备介绍
LAB 18的性能指标
真空度:2E-7Torr 工艺气体:Ar、O2、N2 衬底升温:450℃ 反溅功率:100W 直流源:500W 射频源:300W 脉冲直流:300W 厚度均匀性:< ±5% 可加工样品尺寸:6寸和4寸每次一片,2寸每
约5MHZ
电极
晶体
膜厚
蒸气
34
五 纳米加工平台现有设备介绍
ei-5z腔体内部
35
五 纳米加工平台现有设备介绍
ei-5z主界面
36
五 纳米加工平台现有设备介绍
ei-5z的性能指标
真空度:5E-6Pa 基片最高温度:300℃ 电子枪功率:8KW 厚度均匀性:< ±5% 可加工样品尺寸:6寸每次8片,4寸每次8片,
一 PVD薄膜沉积的基本原理
溅射镀膜
磁控溅射-电子在电场的作用下加速飞向基片 的过程中与氩原子发生碰撞,电离出大量的氩 离子和电子,电子飞向基片,氩离子在电场的 作用下加速轰击靶材,溅射出大量的靶材原子 ,呈中性的靶原子(或分子)沉积在基片上成 膜。
一 PVD薄膜沉积的基本原理
什么是辉光放电?
器。 充气阀充气完毕后要及时关闭。 单独用一个真空室工作时,一定要保持另一个真空室
处于低真空状态,不可是大气压状态。 束源炉在升温的过程中通过面板上的调节旋钮调节电
流不能超过3A,蒸发过程中温度不稳定可增加电流。 束源炉的温度或蒸发舟的温度必须降低到100度以下才
可关闭真空系统,开启真空室。
48
12
一 PVD薄膜沉积的基本原理
离子镀:在真空条件 下,利用气体放电使 气体或蒸发物质离化 ,在气体离子或被蒸 发物质离子轰击作用 的同时,把蒸发物或 其反应物蒸镀在基片 上。
离子镀把辉光放电、 等离子体技术与真空 蒸发镀膜技术结合在 一起
一 PVD薄膜沉积的基本原理
物理气相沉积技术基本原理的三个过程
PVD(物理气相沉积)薄 膜工艺及设备介绍
赵德胜
1
主要内容
¾一 PVD薄膜沉积的基本原理 ¾二 PVD薄膜沉积各种方式的比较 ¾三 PVD薄膜沉积中常见问题 ¾四 PVD薄膜的表征 ¾五 纳米加工平台现有设备介绍
2
一 PVD薄膜沉积的基本原理
在半导体行业PVD主要用于金属化
物理气相沉积(Physical Vapor Deposition, PVD)技术:表示在真空条件下,采用物理方 法,将材料源-固体或液体表面气化成气体原 子、分子或部分电离成离子,并通过低压气体 (或等离子体)过程,在基体表面沉积具有特 殊功能薄膜的技术。
量 蒸镀过程中,注意观察所蒸发的材料是否正
确,电子束斑位置; 禁止非授权操作人员执行开机和关机步骤。
40
五 纳米加工平台现有设备介绍
热蒸发设备外观
液晶显示器 腔体
加热控制显示
41
五 纳米加工平台现有设备介绍
热蒸发真空示意图
42
五 纳米加工平台现有设备介绍
• 热蒸发操作界面
五 纳米加工平台现有设备介绍
2寸每次180片,以及小样品夹具 现有蒸发源:Au、Ti、Ni、Cr、Au88Ge12、Al
、In、Sn、Ag、Pd
五 纳米加工平台现有设备介绍
ei-5z工艺参数
材料名称 High Vol(KV) 本底真空(Pa) 蒸发温度(℃)
蒸发功率(%) 蒸发速率(A/S)
蒸发厚度(A)
Ti 7.5 8E-5 23 28
300
工艺条件
22 衬底转速
功率 电压 电流 (W) (V) (A)
200 426 0.46
20
压
气 体
力 (mT
流量
orr)
Ar 4 19.2
工作真 空
2.8E-3
速率:8.1A/S
29
五 纳米加工平台现有设备介绍
LAB18 工艺参数
材料 Au Al Ni Ti Ag Pt
速率(A/S) 8.9 2.7 3.6 2 8 6
缺点
蒸镀化合物时由于热分解现象 难以控制组分比,低蒸气压物
质难以成膜
需要溅射靶,靶材需要精制, 而且利用率低,不便于采用掩
膜沉积
装置及操作均较复杂,不便于 采用掩膜沉积
15
三 PVD薄膜沉积中常见问题
如何提高PVD薄膜 的粘附性
基片的预处理 9 水洗 9 有机溶剂清洗 9 超声波清洗 9 蚀刻
镀料的气化 镀料原子、分子或离子的迁移 镀料原子、分子或离子在基体上凝结
14
二 PVD薄膜沉积各种方式的比较
真空蒸镀、溅射镀膜和离子镀的比较
方法
真空 蒸镀
溅射 镀膜
离子 镀
优点
工艺简便,纯度高,通 过掩膜易于形成所需要
的图形 附着性能好,易于保持 化合物、合金的组分比
附着性能好,化合物、 合金、非金属均可成膜
一 PVD薄膜沉积的基本原理