高炉高铝渣问题的探索与解决
高炉炼铁中渣化反应的机理与优化措施
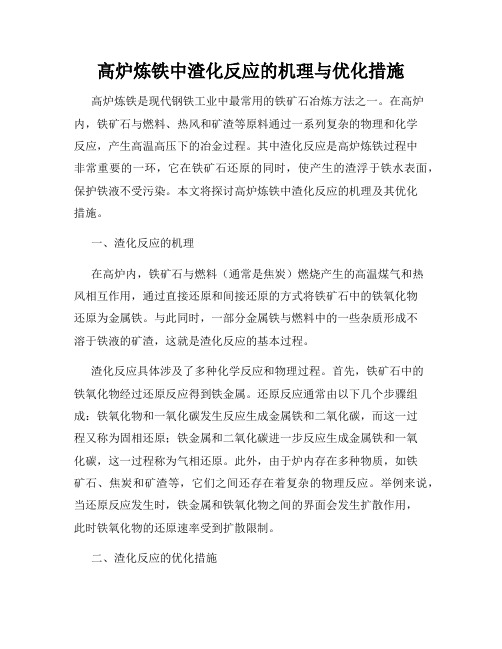
高炉炼铁中渣化反应的机理与优化措施高炉炼铁是现代钢铁工业中最常用的铁矿石冶炼方法之一。
在高炉内,铁矿石与燃料、热风和矿渣等原料通过一系列复杂的物理和化学反应,产生高温高压下的冶金过程。
其中渣化反应是高炉炼铁过程中非常重要的一环,它在铁矿石还原的同时,使产生的渣浮于铁水表面,保护铁液不受污染。
本文将探讨高炉炼铁中渣化反应的机理及其优化措施。
一、渣化反应的机理在高炉内,铁矿石与燃料(通常是焦炭)燃烧产生的高温煤气和热风相互作用,通过直接还原和间接还原的方式将铁矿石中的铁氧化物还原为金属铁。
与此同时,一部分金属铁与燃料中的一些杂质形成不溶于铁液的矿渣,这就是渣化反应的基本过程。
渣化反应具体涉及了多种化学反应和物理过程。
首先,铁矿石中的铁氧化物经过还原反应得到铁金属。
还原反应通常由以下几个步骤组成:铁氧化物和一氧化碳发生反应生成金属铁和二氧化碳,而这一过程又称为固相还原;铁金属和二氧化碳进一步反应生成金属铁和一氧化碳,这一过程称为气相还原。
此外,由于炉内存在多种物质,如铁矿石、焦炭和矿渣等,它们之间还存在着复杂的物理反应。
举例来说,当还原反应发生时,铁金属和铁氧化物之间的界面会发生扩散作用,此时铁氧化物的还原速率受到扩散限制。
二、渣化反应的优化措施为了提高高炉炼铁的效率和产能,必须优化渣化反应的过程。
以下是几种可行的优化措施:1. 选择合适的铁矿石:铁矿石的种类和质量对渣化反应有着重要影响。
选择具有较高还原性的铁矿石可以提高还原反应速率,从而加快渣化反应的进行。
此外,铁矿石中的含水和粉尘等杂质也会影响渣化反应的过程,因此在选择铁矿石时需要谨慎考虑。
2. 控制燃料的质量和供给:燃料是高炉炼铁中的重要组成部分,它不仅提供热量,还对渣化反应产生影响。
控制焦炭的质量和粒度可以影响还原反应的速率,进而影响渣化反应的进行。
此外,合理控制燃料的供给速度和方式也是重要的优化手段。
3. 优化高温煤气的利用:高温煤气中含有大量的一氧化碳和水蒸气等还原剂,可以与铁矿石中的氧化铁进行反应。
2024年高炉炉渣处理方法

____年高炉炉渣处理方法引言:高炉炉渣是一种由铁矿石在高温条件下熔化产生的废弃物,主要成分为氧化铁、氧化硅等。
传统的高炉炉渣处理方法主要是堆放和填埋,但这种处理方式存在着很多的问题,例如占地面积大、对环境造成污染等。
因此,研究和开发高效、环保的高炉炉渣处理方法非常重要。
本文将重点介绍____年高炉炉渣处理领域的新方法和技术。
一、循环利用炉渣制备建筑材料炉渣可以通过适当的处理方法用于制备建筑材料,例如水泥、混凝土等。
在____年,预计会有更多的研究和开发集高炉炉渣处理和建筑材料制备于一体的综合技术。
这种方法可以同时解决炉渣处理和建筑材料供需不平衡的问题,并且还可以减少原材料的使用,节约资源。
二、高炉炉渣的磁选处理高炉炉渣中的铁矿石矿物相对较多,通过磁选处理可以分离出其中的铁矿石,进一步回收利用。
____年,磁选处理技术将会更加高效和环保,能够在更短的时间内实现高炉炉渣的分离和回收。
这种方法可以大幅减少对铁矿石的需求,并且减少炉渣对环境的影响。
三、高炉炉渣的固化处理固化处理是指将高炉炉渣转化为无害、稳定的固体物质,以便安全地储存和处置。
____年,预计固化处理技术将有更大的突破,可以选择更环保的固化材料,提高固化处理的效果。
这种方法可以大大减少炉渣的体积,减少对土地资源的占用。
四、高炉炉渣的化学提取高炉炉渣中存在着一定的有价值金属元素,例如锌、锰等。
通过化学提取方法,可以将这些有价值的金属元素从炉渣中提取出来进行回收利用。
____年,随着化学提取技术的进步,将会有更多的高炉炉渣处理厂使用化学提取方法进行炉渣的资源化利用。
结论:综上所述,____年高炉炉渣处理方法将更加注重循环利用和资源化利用。
通过制备建筑材料、磁选处理、固化处理和化学提取等方法,可以实现高炉炉渣的有效处理和利用。
这不仅可以解决炉渣处理带来的环境问题,还可以减少对原材料的需求,节约资源。
同时,这也是对高炉技术发展的一种推动,使高炉产能得到更充分的利用。
济钢高炉高Al2O3炉渣渣系优化试验研究

济钢 高炉 高 AI 炉渣渣 系优化试 验研究 2 O3
李 学付 , 贻 留, 方 杨金 福 , 马继 波 , 杨雄 文
( 济钢集团有限公司 , 山东 济南 20 0 ) 511 摘 要: 以济钢现场高炉 渣样为基 准 , 正交 设计方法 , 采用 设计 了2 组试验方案 , 5 研究 了w A , 1%~ 3 ( 1 ) 5 2 %的高炉炉渣 0 为
区 间 ( 图 3 、 ) 炉 渣 熔化 性 温 度影 响 不 大 。在 见 ab对 图 3 , A ,2 .%、 O 1 . c中 当 1 = 09 Mg = 32 O %为熔 化 性温 度
最低 。此时 , 降低 M O, 渣 的熔化性 温度将 升 g 炉
2 l 2 2 2 3 2 4
此, 必须采取合理的措施 , 降低高 A:, l 对炉渣黏度 O 的影 响 。研 究炉 渣 中铝 、 二元 碱度 对炉 渣黏 度和 熔
化性 温度 的影响 , 提出济钢 高炉合理 的渣 系组 成 。
1 1 1 1 l 3 50 9 0 .0 8 . 1 1 1 1 13 2 5 9 1 . 5 9 . 2 9 11 1 3 25 0 .5 9 . 2 1 12 140 . 0 0 .0 30 2 l 1 1 13 3 0 O 1 .0 9 . 21 1 1 1 13 0 0 3 .0 6 . 2l 1 1 1 l3 3 5 4 .5 9 .
1 1 11 138 . 7 O .5 14 1 1 1 2 1 3 9. 7 1 -O 8 3 1 9 1 1 l37 . 8 .O 28 1 1 1 1 l38 . 8 O .5 41
试验 号 A B c
1 4 1 5 1 6 1 7 l 8 l 9 2 O
2 1 l2 1 3 7 3 3 3 _0 9 . 2 l 1 1 13 5 0 3 2 .0 8 . 2 l 12 l3 90 l 2 .O 8 . 2 1 12 l3 80 2 4 -0 9 .
高炉渣铁持续排放不净的原因分析及改善措施

高炉渣铁持续排放不净的原因分析及改善措施摘要:柳州钢铁集团中金不锈钢有限公司炼铁厂2号1680m³高炉,于2021年5月10日正式建成投产,设计年产合格炼钢生铁146万吨,2021年5月开炉至今2022年2月,高炉多次持续的渣铁排放对高炉稳定构成严重威胁,本文从进气燃料质量、铁口运行状况、高炉运行状况等几个方面分析渣铁连续非净排放的原因,采取炉体局部灌浆等相应措施,延长铁口排放时间,改善高炉运行状况,炉渣排放明显改善,高炉冶炼强度明显提升,高炉运行稳定性增加。
关键词:高炉;铁口喷溅;渣铁;排放不净;点火开炉初始稳定生产指标,事故为零休风率。
由于焦炭价格上涨等国内外市场因素,日产铁水平均为5000t,平均系数2.97 t/(m3·d),焦、煤、燃料比,分别为358、150、510 kg/t,平均0.532%含硅。
但投产以来,炉前渣铁排放困难,喷溅严重,炉前工作量大,炉内压量关系紧张,高炉稳定平稳的趋势受到影响,风力萎缩,产量下降,生产计划难以保证稳步提升。
1.高炉渣铁持续排放不净原因分析1.铁口串煤气喷溅的影响。
柳钢中金2#高炉的铁口炉壳砌体是由微孔刚玉组合砖砌筑而成,过渡平稳,浇注料由超低水泥刚玉质浇注料浇筑而成,在冷凝过程中,在浇注料中不可避免的会出现小裂纹缝隙,与铁口组合砖接缝处易出现分层现象,在高炉烘炉过程中,耐材见少量水汽的蒸发通道及耐材间的热应力作用,产生大量的缝隙,给炉内串煤气带来了可趁之机,高炉生产过程中,炉内液态渣铁与渣铁自生力相结合,不断地从铁口孔排出炉外,在渣铁排放时,炉内高压气体通过这些缝隙进入铁口孔道,破坏了原力平衡的稳定性,并在排放渣铁时产生喷溅。
严重铁口喷溅大大缩短了主沟耐材的寿命,导致铁大量流失,影响了高炉经济指标。
渣铁喷溅排放不净,直接影响高炉,造成较大的经济损害。
1.炉温及炉渣碱度的影响。
5~8月高炉处于开炉初始阶段,新设备故障率,原材料管控不是很到位,经常因原材料问题炉温出现波动,9月份后设备人员原材料等管理成熟,高炉操作系统开始向运转正常标准操作制度转变,在试生产期间,经常出现长时间亏渣铁,影响高炉的稳定顺行,导致了动态波动,影响了正常生产。
高炉炉渣处理与资源化利用技术研究

高炉炉渣处理与资源化利用技术研究近年来,随着工业生产的不断发展,高炉炉渣作为一种常见的工业废弃物,如何进行有效的处理和资源化利用已成为一个备受关注的问题。
本文将从高炉炉渣的特点、炉渣处理技术以及资源化利用方面展开论述。
首先,我们需要了解高炉炉渣的特点。
高炉炉渣主要由矿渣和工艺渣两部分组成。
矿渣主要是铁矿石在高温条件下还原和熔化生成的,而工艺渣则主要是焦炭灰、烧结矿砂等在高炉内燃烧生成的。
由于高炉操作的连续性,炉渣中也会包含少量的冶炼渣、废弃物等杂质。
传统上,高炉炉渣的处理方式主要是填埋和堆放。
然而,这种处理方式存在很多问题。
填埋会导致土地资源的浪费和环境污染,而长时间的堆放则容易造成渗滤液的渗出和大气中有害气体的排放。
因此,炉渣处理技术的研究和创新势在必行。
目前,炉渣处理技术主要包括物理处理、化学处理和生物处理等几种方法。
物理处理主要是利用筛分、磁选、重力分选等方法将炉渣中的金属物质和其他有用物质分离出来,以达到减少炉渣体积和减少对环境的影响。
化学处理则是利用酸碱等化学试剂对炉渣进行脱硫、脱磷等处理,使得炉渣中的有害物质得到降解和转化。
生物处理是利用微生物的作用对炉渣进行降解和转化,实现对炉渣中有机物和重金属的去除。
除了传统的处理技术外,资源化利用技术也是炉渣处理的另一个重要方向。
在资源化利用技术中,炉渣可以被转化为建筑材料、水泥、道路铺设材料等高附加值的产品。
例如,在水泥生产过程中,炉渣可以取代部分水泥原料,减少对天然资源的依赖并降低环境污染。
此外,炉渣还可以被转化为颗粒活性炉渣、高温液相炉渣等陶瓷材料,用于建筑材料和环保装备制造。
为了进一步提高炉渣处理与资源化利用的效益,需要加强技术研究和创新。
一方面,通过优化处理流程、提高处理效率和降低处理成本,可以实现对炉渣的高效处理。
另一方面,通过开展新材料的研发和产业化推广,可以扩大炉渣的资源化利用范围。
此外,还需加强对炉渣处理过程中所产生的废水和废气的处理,以减少环境污染。
高炉炼铁过程中废渣资源化利用的技术创新

高炉炼铁过程中废渣资源化利用的技术创新由于工业化的快速发展,高炉炼铁已成为现代钢铁工业中不可或缺的环节。
然而,传统的炼铁过程会产生大量的废渣,给环境带来严重污染。
为了实现可持续发展,推动高炉炼铁过程中废渣资源化利用的技术创新势在必行。
本文将探讨当前废渣资源化利用的现状和趋势,并提出一些创新的技术解决方案。
一、废渣资源化利用的现状高炉炼铁过程中主要产生的废渣主要包括烧结矿、烟气净化渣和炉渣等。
这些废渣通常被视为浪费物料,被丢弃或填埋,给环境带来负面影响。
然而,废渣中含有很多有价值的可回收物质,如铁、钢、矿物等。
因此,将废渣转化为可再利用的资源是一种解决环境问题和实现可持续发展的有效途径。
目前,废渣资源化利用主要通过以下几种方式实现:1. 废渣回收再利用:将废渣中的有价值物质进行分离和提取,重新利用于炼铁过程或其他工业生产中。
例如,烧结矿中的铁含量较高,可以再次用于高炉冶炼过程中。
2. 废渣填充利用:将废渣用于填充坑道、道路建设和土地复垦等工程中。
废渣填充可以减少对自然资源的占用,同时改善了被填充地区的土壤质量。
3. 废渣综合利用:将不同种类的废渣进行混合利用,形成新的产品或材料。
例如,烟气净化渣中的硅酸盐可以与矿产废渣混合制备建筑材料。
尽管废渣资源化利用取得了一定的进展,但仍面临一些挑战。
首先,目前的废渣资源化利用技术还不够成熟,存在成本高、技术路线不清晰等问题。
其次,相关政策法规的缺失和监管体系不健全也制约了废渣资源化利用的发展。
二、废渣资源化利用的技术创新为了推动高炉炼铁过程中废渣资源化利用的发展,需要进行技术创新和研发。
以下是一些可行的技术创新方案:1. 废渣熔融处理技术:通过高炉炼铁过程中炉渣的熔融处理,将废渣转化为玻璃状物质。
这种熔融处理技术可以减少废渣体积,提高废渣中有价值物质的回收率,并且可以将熔融后的产品用于建筑材料或其他工业领域。
2. 废渣碳化技术:利用废渣中的碳含量,将其进行碳化处理,生成高价值的碳材料。
2500立方米高炉冲渣问题以及处理措施
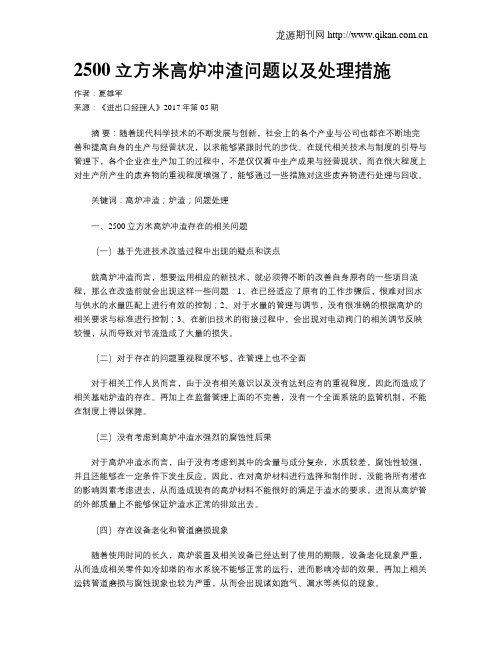
2500立方米高炉冲渣问题以及处理措施作者:夏雄军来源:《进出口经理人》2017年第05期摘要:随着现代科学技术的不断发展与创新,社会上的各个产业与公司也都在不断地完善和提高自身的生产与经营状况,以求能够紧跟时代的步伐。
在现代相关技术与制度的引导与管理下,各个企业在生产加工的过程中,不是仅仅看中生产成果与经营现状,而在很大程度上对生产所产生的废弃物的重视程度增强了,能够通过一些措施对这些废弃物进行处理与回收。
关键词:高炉冲渣;炉渣;问题处理一、2500立方米高炉冲渣存在的相关问题(一)基于先进技术改造过程中出现的疑点和误点就高炉冲渣而言,想要运用相应的新技术,就必须得不断的改善自身原有的一些项目流程,那么在改造前就会出现这样一些问题:1、在已经适应了原有的工作步骤后,很难对回水与供水的水量匹配上进行有效的控制;2、对于水量的管理与调节,没有很准确的根据高炉的相关要求与标准进行控制;3、在新旧技术的衔接过程中,会出现对电动阀门的相关调节反映较慢,从而导致对节流造成了大量的损失。
(二)对于存在的问题重视程度不够,在管理上也不全面对于相关工作人员而言,由于没有相关意识以及没有达到应有的重视程度,因此而造成了相关基础炉渣的存在。
再加上在监督管理上面的不完善,没有一个全面系统的监管机制,不能在制度上得以保障。
(三)没有考虑到高炉冲渣水强烈的腐蚀性后果对于高炉冲渣水而言,由于没有考虑到其中的含量与成分复杂,水质较差,腐蚀性较强,并且还能够在一定条件下发生反应。
因此,在对高炉材料进行选择和制作时,没能将所有潜在的影响因素考虑进去,从而造成现有的高炉材料不能很好的满足于渣水的要求,进而从高炉管的外部质量上不能够保证炉渣水正常的排放出去。
(四)存在设备老化和管道磨损现象随着使用时间的长久,高炉装置及相关设备已经达到了使用的期限,设备老化现象严重,从而造成相关零件如冷却塔的布水系统不能够正常的运行,进而影响冷却的效果。
炼铁技术创新高炉渣的形成与控制方法研究
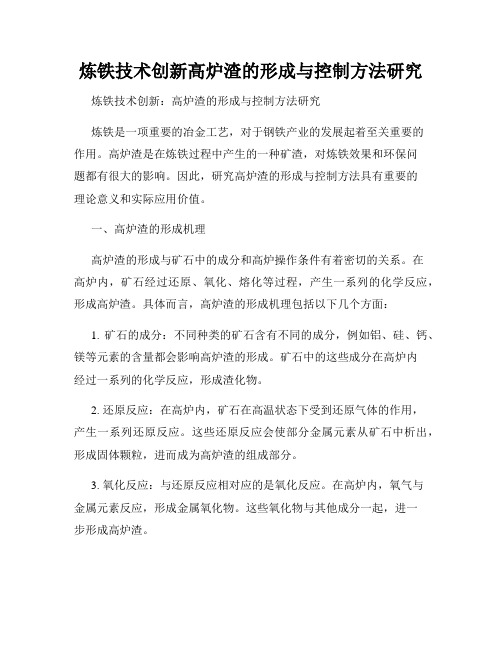
炼铁技术创新高炉渣的形成与控制方法研究炼铁技术创新:高炉渣的形成与控制方法研究炼铁是一项重要的冶金工艺,对于钢铁产业的发展起着至关重要的作用。
高炉渣是在炼铁过程中产生的一种矿渣,对炼铁效果和环保问题都有很大的影响。
因此,研究高炉渣的形成与控制方法具有重要的理论意义和实际应用价值。
一、高炉渣的形成机理高炉渣的形成与矿石中的成分和高炉操作条件有着密切的关系。
在高炉内,矿石经过还原、氧化、熔化等过程,产生一系列的化学反应,形成高炉渣。
具体而言,高炉渣的形成机理包括以下几个方面:1. 矿石的成分:不同种类的矿石含有不同的成分,例如铝、硅、钙、镁等元素的含量都会影响高炉渣的形成。
矿石中的这些成分在高炉内经过一系列的化学反应,形成渣化物。
2. 还原反应:在高炉内,矿石在高温状态下受到还原气体的作用,产生一系列还原反应。
这些还原反应会使部分金属元素从矿石中析出,形成固体颗粒,进而成为高炉渣的组成部分。
3. 氧化反应:与还原反应相对应的是氧化反应。
在高炉内,氧气与金属元素反应,形成金属氧化物。
这些氧化物与其他成分一起,进一步形成高炉渣。
4. 熔化过程:高炉温度高达数千摄氏度,这种高温下矿石中的金属氧化物和渣化物都会熔化,形成液体高炉渣。
二、高炉渣的控制方法了解高炉渣形成的机理,对于控制高炉渣的形成具有重要的指导意义。
以下是一些常用的高炉渣控制方法:1. 控制矿石成分:通过选择合适的矿石,调整矿石的成分,可以有效地控制高炉渣的形成。
例如,减少矿石中含硅和含铝的成分可以降低高炉渣中的硅酸盐含量,提高高炉渣的流动性。
2. 优化还原条件:合理控制高炉的还原条件,可以减少氧化反应产生的金属氧化物,从而减少高炉渣的产生量。
增加还原剂的使用量、增加还原温度等都可以有效地改善还原条件。
3. 渣化物控制技术:渣化物是高炉渣形成的关键部分,对其进行控制可以达到调控高炉渣的目的。
一种常用的方法是添加渣化剂,例如石灰石、白云石等,在炼铁过程中形成易于掌控和处理的渣化物。
- 1、下载文档前请自行甄别文档内容的完整性,平台不提供额外的编辑、内容补充、找答案等附加服务。
- 2、"仅部分预览"的文档,不可在线预览部分如存在完整性等问题,可反馈申请退款(可完整预览的文档不适用该条件!)。
- 3、如文档侵犯您的权益,请联系客服反馈,我们会尽快为您处理(人工客服工作时间:9:00-18:30)。
高炉高铝渣问题的探索与解决
高炉生产实践表明,炉渣Al2O3含量超过16%就会对炉况的稳定顺行产生较大的不良影响,甚至引起高炉失常。
例如,武钢7号高炉是3200m3大型高炉,装备水平先进,投产后,取得了很好的操作指标,但到2009年6月,由于原料成分大幅波动,烧结质量变差,矿石Al2O3含量高,渣铁流动性变差,渣铁不能及时排放,致使炉况顺行渐差,造成了炉况的失常,给高炉生产造成了巨大损失。
为此,武钢努力探索解决高炉高铝渣问题的有效措施。
根据生产实践经验,在Al2O3含量达到18%以上时,依靠高MgO渣来降低炉渣黏度是不可行的,因为提高炉渣MgO含量要靠提高烧结矿中白云石等熔剂配比来实现,当烧结矿中MgO含量增加时,粘结相的流动性变差,如燃耗不增加则必然引起烧结矿强度降低。
最近实验室研究的结论是,烧结矿中MgO含量以2.5%为宜,超过此范围,烧结矿转鼓指数将趋于下降。
因此,要应对原料来源失控引起的Al2O3含量过高的情况,需要研究适宜的高炉造渣制度。
降低黏度的途径有2个,一是加锰矿(MnO);二是加萤石(CaF2)。
由于加锰矿会影响生铁中Mn的含量,所以应研究适当加入萤石量的方法。
武钢7号高炉在2009年7月高炉渣中Al2O3含量全天平均高达18.6%,最高时达22.81%,严重影响了渣铁的流动性和渣铁的分离,直接导致了渣铁排放困难。
尽管采取了很多措施,如加锰矿、热洗炉等措施,但由于炉缸堆积严重,炉况长时间不见好转,最后决定用萤石洗炉。
从2009年7月24号到7月28号,8月3号至7号,加入萤石,萤石用完后再使用Mn矿。
洗炉期间补加大量净焦,用于补充炉缸热量。
从使用效果来看,萤石对炉身粘结的洗刷、对炉缸堆积的处理作用较为显著。
加入萤石以后,显著降低了炉渣的熔点,改善了炉渣的流动性,对炉前出铁排渣作用明显,这对于炉况的恢复起到了非常重要的作用。
应该指出,虽然添加萤石有利于改善炉渣流动性,但萤石对炉腹炉缸的冷却壁有严重的侵蚀作用,所以采用萤石洗炉要十分慎重。
武钢在处理7号高炉2009年7月的炉缸堆积时,萤石是通过炉料均匀加入炉内的,萤石分布于整个料面,萤石大面积和炉腹、炉缸处冷却系统接触,造成了大量风口损坏,延缓了恢复时间,以后在处理因炉渣中Al2O3偏高而引起的炉缸堆积时应加以改进。
实践表明,CaF2能降低高Al2O3炉渣黏度,但CaF2对高炉内的耐火材料也起损坏作用,因此CaF2的使用一般是在因Al2O3含量高,黏度大引起炉缸不活、炉缸堆积等情况下使用。
在武钢炉渣中Al2O3含量日平均小于18%的情况下,CaF2含量在2.0%左右就可以了。
如果在正常生产中长时间加入CaF2使用,则需要考虑高炉内耐火材料的承受能力等问题。