DFX面向产品生命周期的设计详解
设计中的DFX技术

五、SPC理论及模型的研究与改进
SPC的基础是传统的概率与统计理论,它建立 在对大量原始数据统计与分析的基础上。当原始 数据不足时,其分析结果准确性就较差。另外, 对以前数据的分析比较有效,对未来过程发展趋 势的预测显得不足。
新的研究正在寻找SPC与其它方法相结合或 改进的算法,如将人工神经网络(Artificial Neural Networks, ANN)应用到SPC中,利用ANN的统计 概率模型,发挥人工智能在SPC中作用,解决原 始数据不足或预测困难的问题。
各种先进的产品开发模式如: 并行工程(Concurrent Engineering, CE) 先进制造技术如敏捷制造(Agile Manufacturing,
AM)、 精良生产(Lean Production, LP)、 虚拟制造(Virtual Manufacturing, VM)、 及时生产(Just in Time, JIT) 快速响应制造(Quick Response Manufacturing,
之一就是SPC.
三、面向过程的质量控制
传统的SPC,通过检验产品的最终质量参 数如零件/工件尺寸及表面精度,对检验结果进 行统计分析,进而判断是否符合产品设计和工 艺设计要求。这种质量控制实际上带有一定的 被动性。
新的观念是对整个生产过程的过程参数, 如设备运行参数、刀具参数及各种工艺参数等 进行监控,利用SPC对各参数进行统计分析, 判断过程是否正常或是否有不正常的发展趋势, 以预防质量问题的发生,从而从根本上消除质 量问题隐患。
而通过QFD与SPC的集成实现设计与制造过程质 量保证的集成方面的研究还较少。
三、QFD与其它管理技术的结合
许多文献对QFD在可靠性设计、系统工程
(System Engineering, SE) 、 价 值 工 程 (Value
面向产品全生命周期的设计技术 DFx

面向产品全生命周期的设计技术,即DFx技术是一种集成化设计技术,其综合了计算机技术、制造技术、系统集成技术和管理技术,充分体现了系统化的思想。
利用DFx技术,可以在设计阶段尽早地考虑产品的性能、质量、可制造性、可装配性、可测试性、产品服务和价格等因素,对产品进行优化设计或再设计。
最常见的DFx技术有:面向装配的设计(Design for Assembly,DFA)、面向制造的设计(Design for Manufacturing,DFM)、面向性能的设计(Design for Compatibility,DFC)、面向方案的设计(Design for Variety,DFV)、绿色设计(Design for Green,DFG)和后勤设计(Design for Logistics,DFL)等。
面向装配的设计是一种针对零件配合关系进行分析的设计技术。
它为产品设计在早期提供一种确定装配所用的定量方法。
其原则包括最小零件数、最少接触面和易装配。
类似地,面向制造的设计则引入诸如零件最少原则和易制造原则等指导产品的设计。
在面向性能的设计中,设计团队从产品整个生命周期的角度审查有关产品的所有独立的规则集,从而完成产品界面及功能设计、零件特征设计、加工方法选用、工艺性设计和工艺方案的选择等。
面向方案的设计是为了从不同设计方案中选择花费最小的方案,它涉及产品设计方案的数量、产品设计阶段和产品设计更改的代价等因素。
绿色设计指在产品设计时从对环境的影响角度出发,考虑产品在全生命中的使用。
后勤设计是指设计人员在设计时利用不同的约束进行产品设计,如费用驱动约束、最小时间约束等。
第五章 设计过程质量管理

4.保障性
系统(装备)的设计特性和计划的保障资源满足平时和战时使用要求的 能力称为保障性。保障性是装备系统的固有属性,它包括两方面含义, 即与装备保障有关的设计特性和保障资源的充足和适用程度。 设计特性是指与保障有关的设计特性,如与可靠性和维修性等有关的, 以及保障资源要求装备所具有的设计特性。这些设计特性可以通过设 计直接影响装备的硬件和软件。如使设计的装备便于操作、检测、维 修、装卸、运输、消耗品(油、水、气、弹)补给等设计特性。从保障 性角度看,良好的保障设计特性是使装备具有可保障的特性或者说所 设计的装备是可保障的。 保障资源是保证装备完成平时和战时使用的人力和物力。从保障性的 角度看,充足的并与装备匹配完善的保障资源说明装备是能得到保障 的。 装备具有可保障的特性和能保障的特性才是具有完整保障性的装备。
12
5.可用性和可信性
可用性是在要求的外部资源得到保证的前提下,产品在规定的条 件下和规定的时刻或时间区间内处于可执行规定功能状态的能力。 它是产品可靠性、维修性和维修保障的综合反映,这里的可用性 定义是固有可用性的定义,外部资源(不包括维修资源)不影响产品 的可用性。反之,使用可用性则受外部资源的影响。可用性的概 率度量称为可用度。可用性通俗地说是“要用时就可用”。实际 上,可靠性和维修性都是为了使顾客手中的产品随时可用。可靠 性是从延长其正常工作时间来提高产品可用性,而维修性则是从 缩短因维修的停机时间来提高可用性。可用性是顾客对产品质量 的又一重要的需求。 可信性是一个集合性术语,用来表示可用性及其影响因素:可靠 性、维修性、维修保障。可信性仅用于非定量条款中的一般描述, 可信性的定性和定量具体要求是通过可用性、可靠性、维修性、 维修保障的定性和定量要求表达的。
通过DFX设计提高电子产品的质量与可靠性

・传 统 的设计流程
◆导入D x 的设计流程 F后
性 、高效性和经济 性 ,DM 目标是 F的
在保证产 品质量与可靠性的前提 下缩 短产品开发周期、降低产品成本 、提
高加工效 率 。DX 电子产 品设计 中 F在 的 出现有其深刻的历史背景 ,这是 由
于 电子产品竞争越来越激烈 ,公司必 须保证产 品能够快速 、高质 量的进入
二 、电子产 品设计 中采用D X 设计看成为一个孤立的任务,利用现 F 的意义
D X 目的是提倡在产 品的前期 F的 设计中考虑包括可制造性 、可装配性 代 化设计 工具和 DX F 分析工具 设计具 有 良好工程 特性 的产 品。图l 所示为 电子产 品传统 设计流程 与D x F 设计流
品的概念设计和详细设计阶段就综合
三、业界领先公 司的D X F 设计
成 功实施D X F 的一个关键 因素就
过程和系统设计时不但要考虑产品的 考虑到制造过程 中的工艺要求、测试
F 设计 团队进行沟通 。 功能和性 能要求,而且要 同时考虑产 要求 、组装的合理性 ,同时还考虑 到 是 要尽早 与DX 品整个生命周期相关的工程 因素,只 有具备 良好工程特性的产 品才是既满 足客户需求,又具备 良好 的质量、可 靠性与性价 比产品,这样的产品才 能 在市场得 到认可 。D M F 中最重要 F 是D X 的部 分,IM ) 就是 要考虑制造 的可 能 F 维修要求、售后服务要求、可靠性要 在项 目正式启动前就要经常进行工程
可 靠性 ( R la iiy 等 。DX 要 等相关 问题 。传 统的电子产品开发方 R e ib lt) F主 包 括 : 可 制 造 性 设 计 DM D sg 法通常是设 计一 生产制造一 销售 各 F : e in
DFX面向产品生命周期的设计

项目管理与实践
项目管理
将DFX的实施纳入项目管理范畴,制定详 细的项目计划和时间表,确保各项任务 按时完成。
VS
实践经验
借鉴和总结实践经验,不断完善DFX的实 施流程和方法,提高实施效果和产品质量 。
持续改进与优化
持续改进
在DFX实施过程中不断发现问题和不足,及时采取措施进行改进,提高DFX的成熟度和 可靠性。
dfx面向产品生命周期的 设计
• 引言 • DFX概述 • DFX在产品生命周期中的应用 • DFX实施的关键因素 • DFX实施案例分析 • DFX的未来发展与挑战
01
引言
主题简介
主题概述
dfx面向产品生命周期的设计是一种全面、集成的方法,旨在确保产品在整个生 命周期内具有最佳的性能、可靠性和可维护性。
人工智能与DFX
利用AI技术进行数据分析和预测,优化产品设计、生产和维护过 程。
数字化与DFX
借助数字化工具和平台,实现产品生命周期的全面数字化管理,提 高设计效率。
增材制造与DFX
利用增材制造技术,实现定制化、复杂化产品的快速设计和生产。
DFX在全球化环境中的挑战
跨文化沟通
在全球团队中,需克服语言和文化差异,确保信息准确传递和有效 协作。
03
DFX在产品生命周期中的应用
需求分析阶段的DFX应用
需求分析
DFX可以帮助团队更好地理解产品需求,包括功 能、性能、可靠性、可用性和可维护性等。
需求优先级排序
DFX可以协助团队对需求进行优先级排序,以便 在资源有限的情况下,优先满足最重要的需求。
需求变更管理
DFX可以帮助团队更好地管理需求变更,确保产 品设计的灵活性和可维护性。
DFX意义讲解
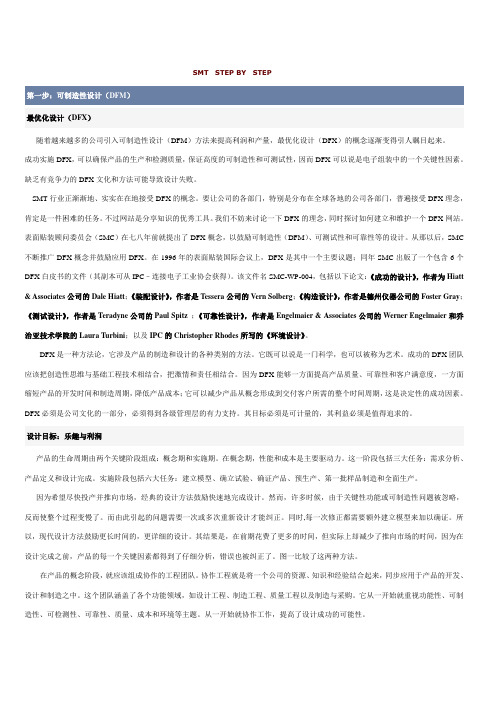
SMT STEP BY STEP最优化设计(DFX)随着越来越多的公司引入可制造性设计(DFM)方法来提高利润和产量,最优化设计(DFX)的概念逐渐变得引人瞩目起来。
成功实施DFX,可以确保产品的生产和检测质量,保证高度的可制造性和可测试性,因而DFX可以说是电子组装中的一个关键性因素。
缺乏有竞争力的DFX文化和方法可能导致设计失败。
SMT行业正渐渐地、实实在在地接受DFX的概念。
要让公司的各部门,特别是分布在全球各地的公司各部门,普遍接受DFX理念,肯定是一件困难的任务。
不过网站是分享知识的优秀工具。
我们不妨来讨论一下DFX的理念,同时探讨如何建立和维护一个DFX网站。
表面贴装顾问委员会(SMC)在七八年前就提出了DFX概念,以鼓励可制造性(DFM)、可测试性和可靠性等的设计。
从那以后,SMC 不断推广DFX概念并鼓励应用DFX。
在1996年的表面贴装国际会议上,DFX是其中一个主要议题;同年SMC出版了一个包含6个DFX白皮书的文件(其副本可从IPC–连接电子工业协会获得)。
该文件名SMC-WP-004,包括以下论文:《成功的设计》,作者为Hiatt & Associates公司的Dale Hiatt;《装配设计》,作者是Tessera公司的Vern Solberg;《构造设计》,作者是德州仪器公司的Foster Gray;《测试设计》,作者是Teradyne公司的Paul Spitz;《可靠性设计》,作者是Engelmaier & Associates公司的Werner Engelmaier和乔治亚技术学院的Laura Turbini;以及IPC的Christopher Rhodes所写的《环境设计》。
DFX是一种方法论,它涉及产品的制造和设计的各种类别的方法。
它既可以说是一门科学,也可以被称为艺术。
成功的DFX团队应该把创造性思维与基础工程技术相结合,把激情和责任相结合。
DFX 案例整理

7
77
PCBA案例說明-DFM
零 件 標
內 容
PCBA EMI彈片選擇類型建議兩種: 板邊側面彈片選用圖一類型61.00011G018 上壓彈片選用圖二類型安全彈片.41.8WY01G002
準 化
目 減少物料類型. 的 改善彈片抗壓能力和撞擊變形風險.
圖示說明
圖一,側面彈片
圖二,上壓彈片
評論
產品零件標準化為採購標準化奠定基礎 及優化制程統一管理.
標 準 化
2.光機內部光照區域禁用rubber等易揮發材質
目 的 避免因溫度或MTBF 燒機后揮發異物影響畫面品質.
圖示說明
畫面霧氣
Chip 表面 附著揮發物
OFF RAY PAD 材質: PPS
評 論 差異化材料使用到不同平臺,同樣做標準化
9
OFF RAY PLATE 材質:壓鑄+電槳陽極
9
Engine案例說明-DFM
DFM
DFA
DFC
DFx
DFE
DFT
DFR
4
4
DFx同步工程
設計 週期
C0~C1 kick off
C2 Mock Up
驗證 週期 DFx1
DFx2
Review 重點
ID共用性及包裝標準化傳輸于PM/務和客戶端定義.
設計端review.包含標準化,模組化,自動化及DFM 中功能性項目確認.
C3 EVT
2
2
Contents
1 DFX定義與發展 2 各項內容特點 3 案例應用
3
3
DFx定義
What’s the DFx ?
DFx是Design for X(面向產品生命週期各環節的設計)的縮寫 期待能夠順利完成NPI 流程,并達成符合市場客戶成本,品質,交期,服務,技術需求. DFx 需與產品設計同步進行,可有效縮短設計週期,避免設計變更“牽一處,動全身”
面向产品生命周期的设计王欣

2012年9月内蒙古科技与经济September2012 第17期总第267期Inner M o ngo lia Science T echnolo gy&Economy N o.17T o tal N o.267面向产品生命周期的设计王 欣,段小宇,郭砚荣(内蒙古化工职业学院测控与机电工程系内蒙古呼和浩特 010070) 摘 要:介绍了面向产品生命周期设计的概念、内涵及分类,探讨了绿色设计系统的开发及绿色设计的应用。
关键词:产品生命周期;绿色设计;系统开发 中图分类号:T H122 文献标识码:A 文章编号:1007—6921(2012)17—0072—01 可持续发展和环境污染问题对制造业提出了越来越高的要求,面向产品生命周期设计是绿色设计的重要方向,是当前研究的难点与热点。
笔者在综合相关研究的基础上,探讨了面向产品全生命周期的有关核心理念。
1 面向产品生命周期的设计的概念面向产品生命周期的英文缩写是DF X。
它是并行工程的关键环节,而并行工程其实就是DFX在产品生命周期上的进一步拓展。
DFX本身是一种设计评价分析方法,为工程设计提供依据,而不是一种设计方法,也不能直接产生设计方案。
DF X方法一般用于改进产品相关过程、改进产品本身(比如,加工过程,装配过程等),它着重强调过程设计和产品设计的同时进行。
首先,作为产品开发人员都应该认识到:只有在设计阶段尽早地考虑产品全生命周期,才会有利于产品竞争力的提高。
其次,作为产品设计人员和产品开发管理人员要积极使用DF X方法于产品设计。
最后,产品设计人员可以借助计算机实现的DF X工具很好地按照DF X方法进行设计。
在产品的设计过程中,DFX方法的具体步是:首先应用DF X方法依据设计要求对已有产品的设计方案进行分析,然后再提供改进设计建议,最后得到新的最优的设计方案。
2 DF X的分类按照面向对象的不同,可以把DFX设计技术分为以下5类。
2.1 面向制造的设计首先要提到的是,这里说的的制造的概念是指组成产品的单一零件的铸造、切削、焊接、锻造、冲压等热冷变形的加工过程。
- 1、下载文档前请自行甄别文档内容的完整性,平台不提供额外的编辑、内容补充、找答案等附加服务。
- 2、"仅部分预览"的文档,不可在线预览部分如存在完整性等问题,可反馈申请退款(可完整预览的文档不适用该条件!)。
- 3、如文档侵犯您的权益,请联系客服反馈,我们会尽快为您处理(人工客服工作时间:9:00-18:30)。
2011年7月
出现背景
自80年代以来, 市场竞争的国际化, 促使制 造业企业不断寻求产品开发的新思路、新 方法并应用于有竞争力的产品的开发
一个典型的例子是美国企业在承受着日本 70年代以后在汽车、半导体等行业逐步确 立的世界市场优势地位的压力下, 积极调整 产业结构, 学习和采用新的产品开发思想、 策略、方法, 如并行工程、虚拟制造、敏捷 制造、精良生产等等, 为美国经济在90年代 的振兴产生了重要的促进作用
DFA 面向装配的设计
最早,目前最成熟的DFX方法 旨在提高装配的方便性以减少装配时间、 成本的设计
DFA 面向装配的设计
原则:1.减少零件数 2.采用标准紧固件和其他标准零件 3.零件的方位保持不变 4.采用模块化的部件 5.设计可直接插入的零件 6.尽量减少调整的需要 7.适合自动生成线生产
DFX是Design for X的缩写。其中,X代表 产品生命周期或其中某一环节,也可以代 表产品竞争力或决定产品竞争力的因素 其中的Design不仅仅指产品的设计,也指 产品开发过程和系统的设计
DFX的内涵
DFX是一种哲理、方法、手段、工具 所有的产品开发人员都应该认识到, 在设计阶段尽 早地考虑产品全生命周期将有益于产品竞争力的 提高。 产品设计人员、产品开发管理人员应该积极应用 DFX方法于产品设计 借助计算机实现的DFX工具可以有效地辅助产品 设计人员按照DFX方法进行产品设计
DFS 面向维修的设计
售后服务是现代企业非常重视的环节之一。 产品的售后服务主要是指产品维修 维修总是伴随着拆卸和重装,产品维修性 主要取决于产品故障确定的容易程度、产 品的可拆卸性和可重装性,减少拆卸重装 的时间与成本是DFS的重要问题 维修性也取决于产品的可靠性,要尽量使 容易发生故障的零部件处于容易拆卸的位 置, 从而有利于维修时间与成本的减少
DFM 面向制造的设计
这里的制造主要指构成产品的单个零件的 冷热变形加工过程 为了减少该类加工的时间与成本,提高加 工质量
DFM 面向制造的设计
原则:1.简化零件的形状 2.尽量避免切削加工因为切削加工 成本高 3.选用便于加工的材料 4.尽量设置较大公差 5.采用标准件与外购件 6.减少不必要的精度要求
出高质量的产品 已成为制造企业竞争的焦点,其中成本已成为决 定产品竞争力的核心因素,如何有效的降低成本 是一个研究热点。降低产品成本的方法很多,如 企业产品成本核算等,但通过设计降低成本则是 最有效的。研究表明,设计阶段的实际投入费用 虽然只占产品总成本的5%,但是却决定了70 %—80%的产品成本。如何在产品设计初期准确 的估算出产品成本并提出有效降低成本的设计修 改方案是成本问题的研究难点。
DFX即为这些新的产品开发思想、手段、 方法之一。在介绍DFX思想与方法之前, 首 先有必要讨论产品生命周期概念和并行工 程思想。
产品生命周期
正如生物的诞生、成长直至消亡构成其生 命周期一样,人类有意识地创造出来的人 工物,包括各种产品也被赋予了生命,亦 即也有诞生、成长、消亡的过程,分别对 应其开发过程、使用过程和报废回收处理 过程。这些过程构成了产品的生命周期。
头脑风暴:
Design for X是一种哲学,请问“X”还能 是哪些因素? Design for Safety Design for Six Sigma Design for Environment Design for Conversion Design for Vision Design for You
典型应用
日本富士胶卷公司于年投放市场的一次性 相机又称带镜头的胶卷是面向回收的设计 的代表产品。 齐齐哈尔车辆厂铁路货车开发并行工程思 想的DFX方法后,大大缩短了产品的开发 周期,减少了产品试制次数和试制费用, 提高了产品质量水平,增加了出口量
DFC面向成本的设计
面向成本的设计(DFC)是指在满足用户需求 的前提下,尽可能地降低成本,并通过分 析和研究产品全生命周期的设计、加工制 造、装配、检测、销售、使用、维护、回 收和报废等多种成本因素,对原设计中影 响产品成本的过高费用部分进行修改,最 终达到降低成本的目的。
DFI 面向检验的设计
着重考虑产品、过程、人的因素以便提高 产品检验的方便性 加工中的产品检验是为了提供快速精确的 加工过程反馈, 而维修中的产品检验则是为 了快速而准确地确定产品结构或功能的缺 陷, 及时维修以保证产品使用的安全
DFI 面向检验的设计
产品检验方便性取决于色彩、零件内部可 视性、结构等等诸多因素
DFQ面向质量的设计
面向质量的设计,它要求把一系列的质量 保证措施与设计系统有机地集成,在设计 阶段进行质量保证的方法,在产品和过程 设计阶段就开始进行质量保证。质量是产 品的生命,可以理解为产品满足使用要求 的程度。
DFQ面向质量的设计
原则: 1,产品易于检查 2,采用标准件 3,采用模块化设计 4,图纸标准清楚、规范 5,尺寸公差设置合理
DFX与并行工程
并行工程是一种哲理,涉及人员管理以及 产品开发过程管理 并行工程也提供技术和方法,以DFX技术 和方法为代表。
DFX的发展历程
DFX思想最早产生于二战时期 50年代末,长期的设计开发经验的积累形 成了DFX的原型 60、70年代后,DFX研究得到重视
DFX的含义
DFQ面向质量的设计
采用方法: 质量功能配置QFD(Quality Function Deployment)、故障模式和效益分析 FMEA(Failure Mode and Effect Analysis)、鲁棒性设计RD(Robust Design)、优化设计、质量信息反馈的有 效利用等
DFQ面向质量的设计
产品生命周期图
并行工程与串行工程
并行工程是一种新的产品开发方法,旨在 改善产品质量、降低开发成本、缩短开发 周期、提高生产率。 与之相对,传统的新产品开发是串行工程
串行工程
长期以来产品开发工作一直采用传统的串 行工程方法,先进行市场需求分析,将分 析结果交给设计部门,设计人员进行产品 设计,然后将图纸交给工艺部门进行工艺 设计和制造准备,采购部门根据要求进行 采购,一切齐备后进行生产加工和测试, 结果不满意时再修改设计与工艺,如此循 环直到满意。
DFC面向成本的设计
面向成本的设计(Design For Cost)和按费用设 计(Design To Cost)是不同的,DFC与DTC的 不同之处主要在于:DFC是一种设计方法,DTC 在很大程度上属于管理方法;DFC主动地运用各 种方法降低产品的成本,而DTC是为了获得一个 满足给定的目标成本并符合用户要求的设计。两 者的相同之处主要体现在从设计入手考虑产品的 全生命周期成本。从两者对成本的重视程度、对 设计的改进和产生的时间顺序看,可以说DFC是 DTC的进一步发展。
质量是个综合概念,这里我们主要是指在 生产过程中的产品质量保证过程,可以说 质量的优先级应该是最高的,即一个产品 首先必须是符合一定质量标准的产品(比 如安全Design for safety),然后才会谈到 成本和绿色性问题。通过 DFM/DFA/DFS/DFE/DFC方法集成设计出 的产品就是为了得到一个高质量的产品。 从这个意义上说,本课所讨论的全部内容 都是与DFQ相关的,即全面质量管理体系。
DFX的内涵
DFX是一种设计方法论,但它本身并不是 设计方法,不直接产生设计方案而是设计 评价分析方法,为设计提供依据 DFX不仅用于改进产品本身,而且用于改 进产品相关过程(如装配和加工)和系统
以往当产品设计完毕, 再接着进行过程 设计(体现串行工程思想) DFX方法强调产品设计和过程设计的 同时进行(体现了并行工程思想)
典型的DFX方法
DFA(Design for Assembly)面向装配的设计 DFM(Design for Manufacture)面向制造的设计 DFI(Design for Inspection)面向检验的设计 DFS(Design for Service/Maintain/Repair)面向 维修的设计 DFR(Design for Recycling)面向回收的设计 DFC(Design For Cost)面向成本的设计 DFQ(Design For Quality)面向质量的设计
并行工程——生命周期工程
集成地、并行地设计产品及其相关的各种 过程(包括制造与支持) 要求产品开发人员在设计一开始就考虑产 品整个生命周期中从概念形成到产品报废 处理的所有因素 强调一切设计活动尽早开始,力争一次获 得成功,关键是产品及其相关过程设计工 作的并行集成
串行工程与并行工程的对比
DFS 面向维修的设计
原则:1.提高产品可靠性 2.经常需要维护的零件和易磨损易失 效的零件置于易发现和接近处 3.零件的拆卸尽量不需移动其他零件 4.尽量减少需要使用的维修工具种类 5.模块化设计并采用标准件 6.留有足够的维修空间
DFR 面向回收的设计
当今社会环保问题的严峻性促使产品回收 开始成为企业的责任。企业产品开发必须 将产品回收问题提到日程上来。 面向产品回收的设计重点集中在产品的可 拆卸性的提高和材料方面。 产品的可拆卸性取决于零件数、产品结构、 拆卸动作种类、拆卸工具种类等因素。
竞争 并行工程 串行工程
设计与制造之间沟通不足, 导致产品质量无法达到最 优化 产品质量 较好,在生产前已经注意到产品 的制造问题
生产成本 由于产品的易制造性提高,成本 开发成本较低,但制造成 低 本可能较高
生产柔性 适于小批量、多品种、高技术产 品 适于大批量、单一品种、 低技术产品