增值与八大浪费
工业工程八大浪费简介

四、加工过剩浪费
定义: 在品质、规格及加工过程的投入主动超出客户需 求从而造成企业资源的浪费。
分类: 1.过剩品质:过分精确品质带来的浪费。 2.过剩加工:超过最经济加工的浪费。 3.过剩检验:内部的、客户不付费的检验造成的浪
费。 4.过剩设计:冗余设计带来的浪费。
五、搬运浪费
搬运不会产生价值,我们应该努力减少搬 运造成的浪费。
1.福特生产方式:库存是必须的。 2.Lean production、TPS:库存是浪费、应该被消
除。
库存损失分类: 1.表面损失 2.潜在损失 3.掩盖问题
三、不良修正浪费
定义: 因来料或制程不良造成的损失,需进行处置的时 间、人力和物力的浪费。
原因: 1.Human error 2.inferior quality 3.weaken process control 4.Design error 5.技术限制 6.客户需求不被理解
2.设计不合理
(1)可同时完成未同时(2)不必要但被增加 (3)物料需要翻找
七、等待浪费
定义: 人机处于等待状态造成的资源浪费。
原因: 1.工作量不平衡 2.机器故障 3.来料品质不良、不及时 4.换线造成的等待
八、管理浪费
基于工厂的管理和运作方式使公司不能获取最大
利润而造成的浪费.是竞争力强弱的表现﹔用于衡 量工厂管理水平,包括管理者对管理技术的认知高 度和整个供应链的综合质素.
7.等待浪费
4.加工过剩浪费
8.管理浪费
一、制造过多浪费
定义:
前制程制造过多、过早,大于后制程当期的最小需求量。
原因:
1.生产排配不合理,预测不准确 2.产线不平衡 3.机器昂贵 4.换线时间长 5.机器维修时间长 6.良率低 7.提前期长
增值和8大浪费
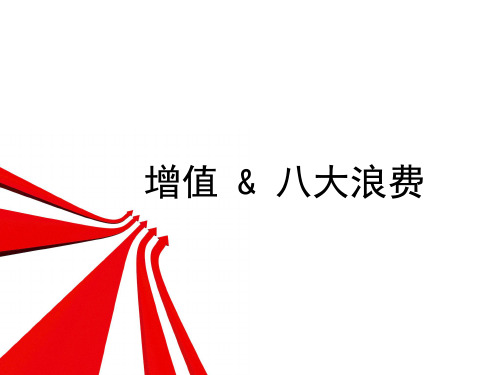
• 过多处理 • 搬运 • 等待 • 未使用的创意
我们日常工作中有超过 90+% 的行为均属于浪费
1:不良
2: 等待
3:过多动作
识别浪费
4:库存
5:过多搬运
6:过多生产
7:过度处理
生产周期的缩短: 通过识别和消除浪费开始!!!
8:未使用的创意
1: 不良品 (次品)
定义: 在送到客户之前需要返工或修理的产品
料 多余复印的一些资料 不清晰的指示或目标 整理文件资料
识别浪费 找出根本原因 减少/消除浪费
减少浪费的七个好处
1): 减少半制品,容易发现问题 2): 平衡生产线,提高生产效率 3): 确保质量,减少不良品 4): 最大化的优化和使用空间 5): 改善部门交流和沟通 6): 减少批量生产,实现一件流 7): 加强竞争,促进持续改善
增值 & 八大浪费
目录
1. 增值与非增值 2. 八大浪费在生产中的实例 3. 减少浪费有何好处
1:增值
提高
活动
增值&非增值
非增值
2:非增值必要的 3:非增值不必要的
减少
消除
增值 浪费
工作动作
工作
必要但不增值
必要 非增值但是
的:
双手操作拿部件的过程, 将相应的部件放在需要加 工的产品上
增值&非增值实例
课程回顾
增值与非增值 8种浪费在生产中的实例 减少浪费有何好处
增值行为:
改变部品/制品的形状或性能的行 为。 (图片中组装的过程)
不必要 非增值但是
的,
即是浪费:增加了成本但没 有增值的行为。 (图片中将部件从盒子里拿 出来放在桌面上需要的时候 再进行加工的过程)
八大浪费介绍

避免过量生产的同时,减少库存管理的 人员浪费
八大浪费—过度加工浪费
定义:
超出规格、或过于繁琐的流程
产生原因:
● 对标准不清楚 ● 产品规格没有标准 ● 流程设计太谨慎 ● ……
例子:
● 胶水用量超过标准 ● 反复擦拭 ● 反复检外观 ● 签核流程太复杂
八大浪费—不良浪费
定义:
缺陷品或失误
产生原因:
等待浪费
智力浪费
八大浪费—搬运浪费
定义:
物品的位置变更
产生原因:
● 现场存在多余的产……
例子:
● 工站距离远需要人工运输
八大浪费—搬运浪费举例
问题:组装线尾到打包间举 例为50米,每次运输过程很 远,浪费很多时间。
改善后:将打包出货区域规 划在组装线尾后面,组装直 接出料到打包出货区,节约 了人力及运输浪费的时间
八大浪费—库存浪费
定义:
产品、物料的堆积和储存
产生原因:
● 未按需求排计划 ● 没按需求买料/备料 ● 工站间产出不平衡 ● ……
例子:
● 成品/物料堆在现场
八大浪费—库存举例
问题:仓库存储量大,大部 分物料在仓库存放时间比较 长
改善后:按客户要求安排生产 计划,计算好出货计划。
八大浪费—动作浪费
● 未按作业指导书作业 ● 培训不到位 ● 设备异常 ● 工具异常 ● 来料异常
例子:
工段加工不良过多
八大浪费—不良浪费举例
问题
改善后
八大浪费—智力浪费
定义:
未充分利用人的能力
产生原因:
● 未鼓励员工参与改善 ● 授权不够 ● 未提供必要条件 ● ……
例子:
● 没让员工参与讨论 ● 员工本可以成为多能工 ● ……
精益生产之八大浪费的识别

精益生产之八大浪费的识别
精益管理的八大浪费
传统意义上人们认为只有材料的报废、退货、废弃才是浪费。
现在,企业生产中的浪费指一切不增值的活动,包括时间、成本等的浪费。
接下来给大家介绍企业管理中精益生产管理最常见的八大浪费。
一、制造过剩的浪费
制造过剩的浪费是最大的浪费,因为过量生产会掩盖很多的浪费,让人们蒙蔽双眼,因会计上的数字而沾沾自喜。
二、等待的浪费
停工待料、设备故障、工序流转不起来等都会造成等待的浪费。
三、搬运的浪费
由于作业台的设置和存放库的位置设置不合理等都会造成实际搬运上的浪费。
四、动作的浪费
无附加价值的分工、无效的作业等无效的作业称之为动作上的浪费。
五、库存的浪费
库存过量会衍生出仓储成本,而库存过量的根源往往是生产能力低下、产能不平衡、供应链级别不高等,库存的浪费被视为最恶劣的浪费。
六、加工的浪费
一般指加工方法或工艺上的不得当或不必要的加工。
七、不良品的浪费
不良品的产生直接会造成物料成本和人员成本的产生,频繁不良品的产生与没有从根本上解决不良品产生的源头有关。
说到精益浪费大家一般会想到以上7种浪费,而今天我想重点说一下第八种浪费。
那就是沟通的浪费,这是在很多企业都会被忽视的浪费。
例如领导交代工作时内容不清晰,而负责人当时出于某种原因没有详细追问,
导致理解上出现偏差、执行力差甚至与领导的想法背道而驰,走了很多弯路。
在制造业现场如果缺少沟通环节,领导不能真实地了解现状,现场的声音没地方传达,很多信息不能顺畅流通,将会造成意想不到的损失。
精益生产之增值与八大浪费

Lean Manufacturing System
P 11
2.1 识别浪费 等待
定义: 由于工人不能进行下一个作业的时间和空间方面 的闲置
• 生产计划出现问题 • 不合理的工序安排 • 原材料没有及时供应 • 机器故障 • 质量问题没有得到及时处理 ……
Lean Manufacturing System
不明确的交 流和沟通
不合理的工位安排
不合理的生产计划
Lean Manufacturing System
缺乏培训 材料供应问题
P 17
3.1 关于办公室浪费的实例
寻找资料,文件
利用 拿资料文件去签字 无人阅读的闲置的文件或资
P4
1.增值与非增值
Value-Adding Activities …增值活动… 将物料与信息转变成客户需要的产品与服务及 產品質量乎合要求並不需要任何返工
NON-Value Adding Activities ...非增值活动 消耗资源, 而又不直接贡献于产品和服务
Activities which are non-value added but necessary 必要的非增值活动 不能直接创造价值,但是实现增值所必须的活动
Lean Manufacturing System
P 23
课程回顾:
> 1.增值与非增值 > 2.八大浪费在生产中的实例 > 3.产生浪费的原因 > 4.识别浪费的练习
Lean Manufacturing System
P 24
结束
Lean Manufacturing System
P 25
料 多余复印的一些资料 不清晰的指示或目标 整理文件资料
IE之八大浪费

PPT文档演模板
IE之八大浪费
•3.3等待的浪费
• 1. 等待的浪费:即等待下一个动作的来临,不仅是人、机 器存
• 在等待,物料也有等待,即等待加工;工艺中的等待。
• 2. 表现形式: • --自动机器操作中,人员的“闲视”等待 • --作业充实度不够的等待 • --设备故障、材料不良的等待 • --生产安排不当的人员等待 • --上下工程间未衍接好造成的 • 工程间的等待
• 1.库存是指:工厂里的原材料﹑零部件﹑半成品(WIP)﹑
成
•
品等。 (万恶之源,也是必要的恶物)
• 2.三种错误的观念造成库存的浪费:
•
1)材料库存:大量采购成本低。
•
2)在制品库存:不良维修;机器故障。
•
3)成品库存:预测生产与实际需求量不同•。库存水平
•不良品
•故障
•点点 停
•能力 不平衡
•调整时 间长
•选对的人,做对的事,并将事情做对。 •组织再造,流程优化,简化,标准化。
PPT文档演模板
IE之八大浪费
• 四. 如何发现浪费
• 1.发现浪费的重点: • 1)三现原则:到现场 、看现物、掌握现状。
•任何企图在座在办公室里解决现场问题都是徒劳的。
PPT文档演模板
IE之八大浪费
• 四. 如何发现浪费
PPT文档演模板
IE之八大浪费
•二、什么是浪费 ?
Anything other than absolute minimum resource of material,machine and manpower required to add value to the product
精益管理中增值与浪费的例子

精益管理中增值与浪费的例子
以下是一些增值和浪费的例子:
1. 增值活动:
- 按照客户要求生产产品:根据客户的订单和需求,生产符合其质量标准的产品。
- 提供优质的客户服务:及时、有效地回应用户的咨询和投诉,提供满意的解决方案。
2. 浪费活动:
- 过量生产:生产超过客户需求的产品,导致库存增加和资金占用。
- 不必要的搬运和运输:在生产过程中,物料和产品的搬运和运输过程没有优化,导致时间和资源的浪费。
- 等待时间:在生产流程中,由于设备故障、原材料短缺或工作安排不合理等原因,导致工人等待时间过长。
- 过度加工:对产品进行超过质量要求的加工,增加了成本但没有为客户带来额外的价值。
- 缺陷和返工:生产出的产品存在缺陷,需要进行返工或修复,导致资源和时间的浪费。
通过识别和消除这些浪费活动,企业可以提高生产效率、降低成本,并提供更好的客户价值。
精益管理的目标就是通过持续改进,最大限度地减少浪费,实现资源的有效利用和价值的最大化。
精益改善基础之八大浪费
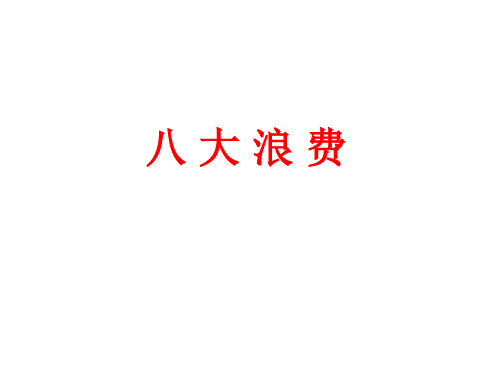
三﹑有关场所布置方面 15. 定点放置原则; 16. 双手可及原则; 17. 按工序排列原则; 18. 使用容器原则; 19. 用坠送法原则; 20. 近使用点原则; 21. 避免担心原则; 22. 环境舒适原则;
八大浪费---动作浪费
3.案例分享
八大浪费---等待浪费
1.定义:
人员,设备,物料,因异常或分配不合理,造成的等待
八大浪费---动作浪费
1.定义:
指实际操作过程中有多余或不合理的动作
2.浪费产生的原因:
动作幅度太大 双手/单手空闲 作业动作不流畅 重复/不必要的动作
思考?如何消除浪费
八大浪费---动作浪费
八大浪费---动作浪费
12种常见的动作浪费:
1.双手空闲的浪费 2.单手空閑的浪费 3.作业动作停顿的浪费 4.作业动作太大的浪费 5.左右手交换的浪费 6.步行过多的浪费
八大浪费
大纲
➢ 八大浪费总括 ➢ 各个浪费:定义,产生原因,危害,解决方法 ➢ 总结 ➢ 现场互动
浪费的定义
浪费的定义:
指凡是不能直接创造出价值的一切活动,均视为浪费。
强调
对JIT来讲,凡是超出增加产品价值所绝对必须的最 少量的物料,设备,人力,场地,时间的部分都是浪费 这里有两层意思:
不增加价值的活动,是浪费 增加价值,但是所用的资源
八大浪费---动作浪费
动作经济的22条原则:
一﹑有关人体动作方面 1. 双手并用原则; 2. 对称反向原则; 3. 排除合并原则; 4. 降低等级原则; 5. 免限制性原则; 6. 避免突变原则; 7. 节奏轻松原则; 8. 利用惯性原则; 9. 手脚并用原则; 10. 适当姿势原则;
二﹑有关工具设备方面 11. 利用工具原则; 12. 万能工具原则; 13. 易于操作原则; 14. 适当位置原则;
- 1、下载文档前请自行甄别文档内容的完整性,平台不提供额外的编辑、内容补充、找答案等附加服务。
- 2、"仅部分预览"的文档,不可在线预览部分如存在完整性等问题,可反馈申请退款(可完整预览的文档不适用该条件!)。
- 3、如文档侵犯您的权益,请联系客服反馈,我们会尽快为您处理(人工客服工作时间:9:00-18:30)。
增值&非增值实例
我们日常工作中有超过 90+% 的行为均属于不增值
1:不良 Defects
2: 等待 Waiting
3:过多动作 Over motion
4:库存 Inventory
5:过多搬运 Transportation
6:过多生产 Overproduction
7:过度处理 Excessive processing
人力浪费(Man)
步行浪费 寻找浪费 工序动作浪费 看不见的浪费
管理浪费(Management)
资料的浪费 会议的浪费 管理的浪费 通讯的浪费 收据的浪费
遵守安全( Safety )
防止灾害,事故 灾害事故是浪费以前的浪费 所有解除浪费是安全第一
设备浪费(Machine)
大型机械的浪费 法定机械的浪费 传送带的浪费 空气加工的浪费 故障的浪费 机械等待的浪费
对浪费对认识
( 物的 ( 物的 ( 人的 ( 物的 ( 人的 ( 物的 ( 物的 ( 人的 ( 人的 ( 物的 ( 物的 ( 物的 ( 人的 ( 物的 ( 物的 ( 物的 ( 物的 ( 人的 ( 人的 ( 物的 ( 物的
) 紧缺材料到达不及时 ) 材料取集困难 ) 作业Error多 ) 设计图面过于复杂 ) 不遵守计划日程 ) 不检查材料 ) 作业没有进行改善 ) 检查作业不充分 ) 作业Error发现不及时 ) 作业没有标准化 ) 动力系统故障过多 ) 设备故障过多 ) 监督者不严厉 ) 修理设备不够精细 ) 没有具备手工具 ) 测量仪器精度不达标 ) 搬运方法没有计划性 ) 作业指示不明确 ) 缺少熟练工 ) 受伤者过多 ) 没有安全装置
• 费用方面的浪费
工 作
制 造 活 动
活 动
对浪费对认识
产生附加价值的动作
收款的动作(大)
非效率动作
收款的动作(小)
单纯动作 附带动作
浪费钱的动作 无法收款的动作
对浪费对认识
工作动作方面的浪费
由于一个工作由多种动作来完成,需要划分动作并找出各动作的浪费因素。
向零件箱子伸手 拿零件
把零件拿到工作台上
时候再进行加工的过程)
增值&非增值实例
工厂中有90+% 的部分是不增值的时间和动作
库存
多余动作
过多处理
工序时间
等待
过量生产
不良/返品 搬运
浪费 (时间 & 活动) 价值 (主要流程)
• 不良/返品 • 过量生产 • 多余动作 • 库存
• 过多处理 • 搬运 • 等待 • 管理浪费
缩短生产周期可以从识别和消除不增值活动开始……
•相似的混用 •因异物进入要洗涤
•不必要, 过盈,长期再库等没有利益的利息 增加
•再库有必要进行 物的,人的资源管理 •随时了解再库,清扫,整理整顿实施
改善,迟延
•因再库过多看不到问题 产品不良,设备故障,纳期延误,交换时间 等的问题隐藏 所以改善活动进展不好
识别浪费
备注
经费增加 生产减少 经费增加 经费增加 生产减少 利息增加 经费增加 人件费增加
提高售(卖)价 降低成本
• 消除浪费 • 提升效率
企业经营与浪费
利润与成本
通过管理使制造成本下降20%,而利润增加114.2%
当前状况
增加销售50% 削减支出50% 降低成本20%
销售
$ 100,000 $ 150,000 $ 100,000 $ 100,000
成本
- 80,000
- 120,000
把零件夹紧于 设备上
把手柄降下来
把成品放进 箱子里
把零件从工作部位拿 从设备松开零件 下来
把手柄拉上去
除了“加工处理”以外,其他动作都是浪费。
加工处理
附加价值
发生浪费的原因
由于不知材料在哪儿 而停止生产线。
对浪费对认识
混有不良产品, 推迟工作时间。
在哪儿、怎么、 有多少、为什么发生浪费?
材料供应不及时, 暂时停止生产线。
等待的 浪费-原因与改善方向
说明:
资材,作业, 搬运,检 查等的全部等待和检 查作业。
等待的 浪费
识别浪费
内容:
人,作业,时间,机械的 浪费提供,再库的增 大。
对策:
标准化生产 单元生产/单件流 JIT生产 人机分析/TPM 快速切换
原因:
大批量生产 平衡性差 计划/物料不科学 设备异常多
对策 自动化、标准化作业 防错法(防呆法) 全面质量管理 品质7大手法的运用 不制造不良检查
原因 依据检查的分类重点 检查的方法 基准等不足 标准作业的遗漏 品质过程控制疏漏
识别浪费
等待浪费
定义: 由于工人不能进行下一个作业的时间和空间方面的闲置 • 生产计划出现问题 • 不合理的工序安排 • 原材料没有及时供应 • 机器故障 • 质量问题没有得到及时处理 ……
(
) 不合理的事强行
(
) 设备点检不彻底
(
) 不合理的工作硬要执行
(
) 作业训练不充分
(
) 作业方法不知道
(
) 作业标准改正过慢
(
) 不清楚工厂的纪律
(
) 作业环境恶劣
(
) 作业间信息传达不通畅
(
) 缺少测量仪器
(
) 参加没有效果的会议
(
) 慢性加班过多
(
) 同样的事故反复出现
(
) 没有工作欲望
(
) 事故不及时向工厂反映
• 较长的准备时间 • 工厂不合理的布局 • 过大的生产批次 • 不合理的工位设计 • 不合理的生产计划
库存的 浪费-原因与改善方向
区分
场所的 浪费 保管用具 浪费 异物/混入 浪费
利息的 浪费 管理的 浪费
现状
•工厂越来越狭窄. •真正重要的物品没地方放
•货价,柜子过多使用 •木盘,搬运用具过多使用
课程安排
1
为什么要消除浪费
2 增值&非增值
3
浪费的识别
4
八大浪费
5
浪费案例演练
企业经营与浪费
企业经营与浪费 企业是 把产品卖给顾客 通过利润持续发展
售价=成本+利润 利润=售价-成本
利润 原 售 价 成本
增利 利润 新
售 成本 价
利润 成本
利润 新 增利 售 成本 价
企业经营与浪费
企业经营与浪费 提高卖价(销售价)或降低成本... • 没有价格优势就灭亡. eg.小卖部生意不可观
我的工具 在哪儿呢?
昨天的约会 怎么样?
不能相信。 重作检查……
为把东西保管在别的场所, 在搬运。
容易误解的浪费 : 检查、包装、Label 工作都是浪费。
浪费的种类
对浪费对认识
等待浪费
搬运浪费
8 工
不良浪费
大 厂
动作浪费
浪 常
见
加工浪费
费 的 库存浪费
地下工厂
企业每生产一件产品就在制造一份 浪费。伴随企业运营中各业务环节不被 察觉或不被重视的浪费,日本企业管理
精益系列课程
增值与八大浪费
※※※※※
名称 日期 版本 制作 课时
增值与八大浪费 2019年 V1 Peter 120min
课程目标
培训对象:
精益人才梯队预备人员
培训时长:
3.0小时
培训目标:
通过此次培训,学员能够 1、识别增值和非增值作业; 2、了解八大浪费的概念及识别浪费; 3、掌握形成的原因和有效地减少浪费的方法; 4、运用八大浪费解决生产过程中的相关问题。
人员,工数的增加 技能的隐蔽化 作业的不稳定 不必要的动作。
对策:
挑战流水线生产 U字型设备布局 标准作业和改善原则 动作经济原则实施 简易工装/夹具的使用
原因:
没有标准作业 工程布局不好 没有教育和训练 辅助制具设计不合理
识别浪费
库存浪费
定义: 从及时生产的角度出发一切材料过剩的供应和存储都属于库存
不良品 (次品)
识别浪费
定义: 在送到客户之前需要返工或修理产品而产生的损失 • 原材料不良 • 工人缺乏培训 • 机器出现故障 • 操作方法不正确 • 标准不明确 • 设计不良
……
不良的 浪费-原因与改善方向
说明
材料不良 加工不良 检查、索赔 修正等
不良的浪费
识别浪费
内容 材料费的增加 生产性低下 检查人员多、工程多 不良及索赔增多
生产性低下 安全事故发生
库存的 浪费-原因与改善方向
说明
材料、部品、组装品等 物体是否整齐摆放? 包括仓库和每个工位间
库存的浪费
识别浪费
内容 交付期过长 压制了改善欲望 空间的浪费使用 搬运、检查的发生 运转资金的增加
对策 对于库存的意识改变 U字形生产 平均化生产 看板的彻底管理 准备、交换标准化
原因 “库存是理所应当”的错误 意识 设备布局不好 批量性生产 先行生产
识别浪费
过多搬运
定义: 未能直接支援生产的所有物料,不必要的移动或转移 • 布局 (距离) • 频繁的搬运 • 大批量的生产 • 排拉合理性 • 生产计划安排合理性
搬运的 浪费-原因与改善方向
说明
不必要的搬运 物品的移动,保管等 长距离的搬运 活性度的恶化等问题
8:管理浪费 Management
浪费是什么 1)定义
没有帮助的 没有利益的 没有附加值的
对浪费对认识
为了创造产品的附加价值, 最少的设备、材料、零件、 工作空间、工作时间等要素 是必不可少的。但若这些要 素不能产生产品的附加价值, 则会成为浪费。