生产过程中八大浪费
精益生产现场八大浪费
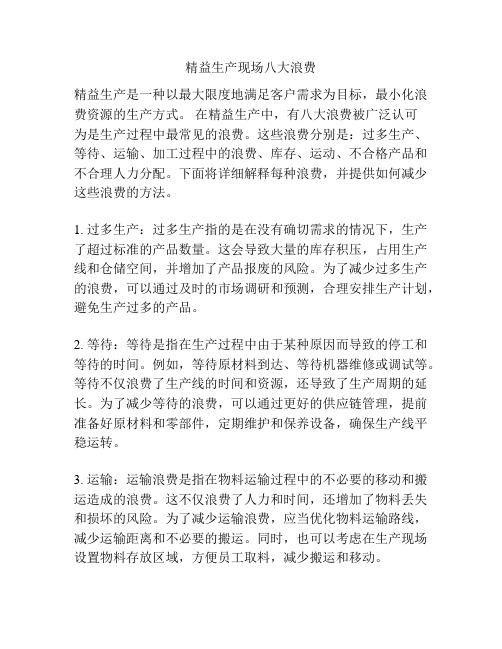
精益生产现场八大浪费精益生产是一种以最大限度地满足客户需求为目标,最小化浪费资源的生产方式。
在精益生产中,有八大浪费被广泛认可为是生产过程中最常见的浪费。
这些浪费分别是:过多生产、等待、运输、加工过程中的浪费、库存、运动、不合格产品和不合理人力分配。
下面将详细解释每种浪费,并提供如何减少这些浪费的方法。
1. 过多生产:过多生产指的是在没有确切需求的情况下,生产了超过标准的产品数量。
这会导致大量的库存积压,占用生产线和仓储空间,并增加了产品报废的风险。
为了减少过多生产的浪费,可以通过及时的市场调研和预测,合理安排生产计划,避免生产过多的产品。
2. 等待:等待是指在生产过程中由于某种原因而导致的停工和等待的时间。
例如,等待原材料到达、等待机器维修或调试等。
等待不仅浪费了生产线的时间和资源,还导致了生产周期的延长。
为了减少等待的浪费,可以通过更好的供应链管理,提前准备好原材料和零部件,定期维护和保养设备,确保生产线平稳运转。
3. 运输:运输浪费是指在物料运输过程中的不必要的移动和搬运造成的浪费。
这不仅浪费了人力和时间,还增加了物料丢失和损坏的风险。
为了减少运输浪费,应当优化物料运输路线,减少运输距离和不必要的搬运。
同时,也可以考虑在生产现场设置物料存放区域,方便员工取料,减少搬运和移动。
4. 加工过程中的浪费:加工过程中的浪费包括很多方面,例如,不必要的额外加工、过度加工、加工错误等。
这些都会增加生产时间和成本,同时也会造成不合格品和废品。
为了减少加工过程中的浪费,可以通过标准化的工艺和操作规程,提高员工的技能和培训水平,减少加工错误和废品产生。
5. 库存:库存浪费是指过多的产品、物料或半成品的库存。
这不仅占用了生产线和仓储空间,还增加了物料报废和货物滞销的风险。
为了减少库存浪费,应当通过精确的需求预测和生产计划,避免生产过多的产品。
另外,也可以采取Just-in-Time (JIT)生产方式,根据客户订单及时生产和交付产品,减少库存积压。
八大浪费是指什么

八大浪费是指什么八大浪费是生产过程中所造成的物料、设备、人力、场地和时间等的浪费。
分别是:不良、修理的浪费,过分加工的浪费,动作的浪费,搬运的浪费,库存的浪费,制造过多过早的浪费,等待的浪费和管理的浪费。
1、等待浪费。
由于生产原料供应中断、作业不平衡和生产计划安排不当等原因造成的无事可做的等待,被称为等待的浪费。
2、加工过剩浪费。
加工的浪费也叫过分加工的浪费,主要是指多余的加工和过分精确的加工或是需要多余的作业时间和辅助设备,这样增加了生产用电、气压、油等能源的浪费,另外还增加了管理的工时。
3、管理浪费。
管理浪费指的是问题发生以后,管理人员才采取相应的对策来进行补救而产生的额外浪费。
4、不良修正浪费。
不良修正浪费指的是由于工厂内出现不良品,需要进行处置的时间、人力、物力上的浪费,以及由此造成的相关损失。
5、动作浪费。
动作的浪费现象在很多企业的生产线中都存在,常见的动作浪费主要有以下几种:两手空闲、单手空闲、作业动作突然停止、作业动作过大、左右手交换、步行过多、转身的角度太大等等。
6、库存浪费。
按照过去的管理理念,人们认为库存虽然是不好的东西,但却是必要的。
JIT的观点认为,库存是没有必要的,甚至认为库存是万恶之源。
由于库存很多,将故障、不良品、缺勤、点点停、计划有误、调整时间过长、品质不一致、能力不平衡等问题全部掩盖住了。
7、搬运浪费。
搬运的浪费具体表现为放置、堆积、移动、整列等动作浪费,由此而带来物品移动所需空间的浪费、时间的浪费和人力工具的占用等不良后果。
8、制造过多浪费。
制造过多或过早,提前用掉了生产费用,不但没有好处,还隐藏了由于等待所带来的浪费,失去了持续改善的机会。
生产中的八大浪费
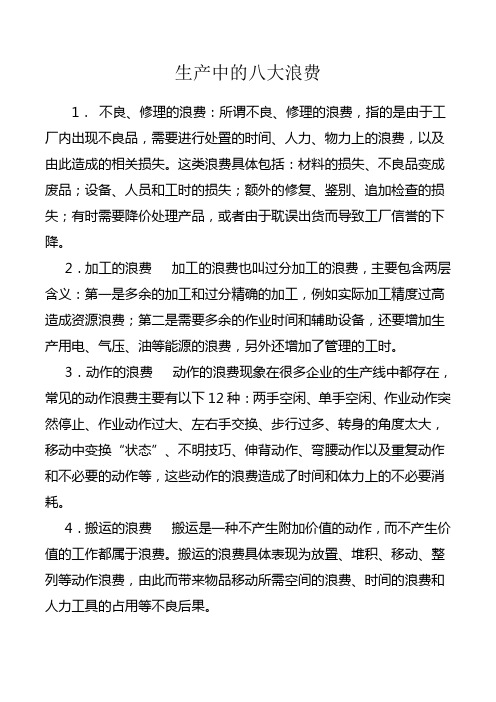
生产中的八大浪费1.不良、修理的浪费:所谓不良、修理的浪费,指的是由于工厂内出现不良品,需要进行处置的时间、人力、物力上的浪费,以及由此造成的相关损失。
这类浪费具体包括:材料的损失、不良品变成废品;设备、人员和工时的损失;额外的修复、鉴别、追加检查的损失;有时需要降价处理产品,或者由于耽误出货而导致工厂信誉的下降。
2.加工的浪费加工的浪费也叫过分加工的浪费,主要包含两层含义:第一是多余的加工和过分精确的加工,例如实际加工精度过高造成资源浪费;第二是需要多余的作业时间和辅助设备,还要增加生产用电、气压、油等能源的浪费,另外还增加了管理的工时。
3.动作的浪费动作的浪费现象在很多企业的生产线中都存在,常见的动作浪费主要有以下12种:两手空闲、单手空闲、作业动作突然停止、作业动作过大、左右手交换、步行过多、转身的角度太大,移动中变换“状态”、不明技巧、伸背动作、弯腰动作以及重复动作和不必要的动作等,这些动作的浪费造成了时间和体力上的不必要消耗。
4.搬运的浪费搬运是一种不产生附加价值的动作,而不产生价值的工作都属于浪费。
搬运的浪费具体表现为放置、堆积、移动、整列等动作浪费,由此而带来物品移动所需空间的浪费、时间的浪费和人力工具的占用等不良后果。
5.库存的浪费由于库存很多,将故障、不良品、缺勤、计划外停机、计划有误、调整时间过长、品质不一致、能力不平衡等问题全部掩盖住了。
6.制造过多或过早的浪费制造过多或过早,提前用掉了生产费用,不但没有好处,还隐藏了由于等待所带来的浪费,失去了持续改善的机会。
有些企业由于生产能力比较强大,为了不浪费生产能力而不中断生产,增加了在制品,使得制品周期变短、空间变大,还增加了搬运、堆积的浪费。
此外,制造过多或过早,会带来庞大的库存量,利息负担增加,不可避免地增加了贬值的风险。
7.等待的浪费由于生产原料供应中断、作业不平衡和生产计划安排不当等原因造成的无事可做的等待,被称为等待的浪费。
常见八大浪费和消除方法

常见八大浪费和消除方法在日常生活和工作中,我们会经常遇到各种浪费现象,这些浪费不仅消耗了资源和时间,还会降低工作效率和生活质量。
以下是常见的八大浪费和相应的消除方法。
1.非必要生产浪费:这种浪费包括过度生产、生产次品或废品、生产多余工作和指令等。
消除该浪费的方法是实施精益生产原则,分析生产过程中的不必要步骤和环节,优化生产流程,并监控和控制生产指令的发布。
2.库存浪费:库存浪费指储存成品、原材料或半成品的费用。
库存浪费的消除方法包括实施小批次生产,提高生产柔性和响应能力,通过供应链管理减少库存,并将库存量限制在合理的范围内。
3.运输浪费:运输浪费包括物料在生产、仓库和供应链中的多次搬运。
减少运输浪费的方法包括优化生产布局,减少生产线上的传送带长度,提高运输设备的效率,以及优化仓储管理和运输路线规划。
4.过度加工浪费:过度加工浪费指超过产品规格或顾客需求的加工。
减少过度加工浪费的方法包括明确产品规格和顾客需求,设立合理的加工标准,避免不必要的加工步骤和环节,以及提高员工技能和意识。
5.等待浪费:等待浪费指产品或工作在生产或供应链中等待的时间延误。
减少等待浪费的方法包括优化生产调度和物流流程,减少生产环节的停机时间和设备故障,以及提高生产和供应链的反应能力。
6.移动浪费:移动浪费指不必要的物料和人员移动。
减少移动浪费的方法包括优化工作布局,减少不必要的移动距离,提高物料存放和工具的易取性,以及改善工作环境和工作条件。
7.不必要的工艺浪费:不必要的工艺浪费指在生产过程中的不必要步骤和工艺。
消除不必要的工艺浪费的方法包括分析生产环节,识别和优化不必要的工艺和步骤,以及减少生产过程中的冗余操作。
8.缺陷浪费:缺陷浪费包括产品质量问题和返工造成的资源和时间浪费。
减少缺陷浪费的方法包括实施质量管理和质量控制措施,提高生产工艺和设备质量,以及设立合理的质量标准和检查流程。
总结起来,消除浪费需要从多个层面入手,包括优化生产流程、改善供应链管理、提高员工技能和意识、加强质量控制等。
工厂精益生产之八大浪费
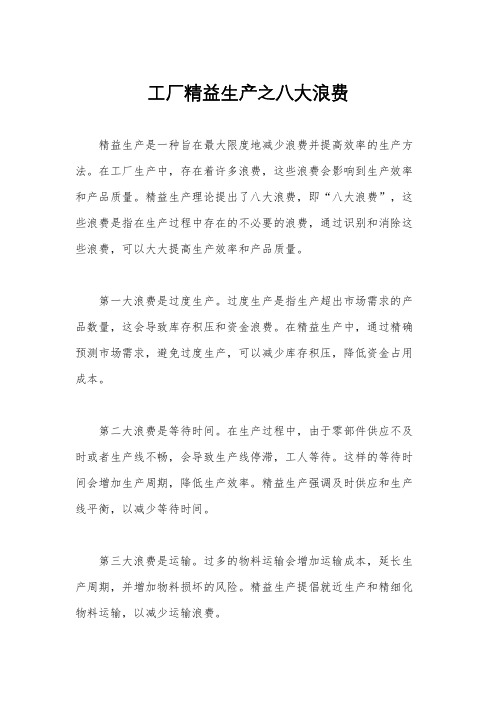
工厂精益生产之八大浪费精益生产是一种旨在最大限度地减少浪费并提高效率的生产方法。
在工厂生产中,存在着许多浪费,这些浪费会影响到生产效率和产品质量。
精益生产理论提出了八大浪费,即“八大浪费”,这些浪费是指在生产过程中存在的不必要的浪费,通过识别和消除这些浪费,可以大大提高生产效率和产品质量。
第一大浪费是过度生产。
过度生产是指生产超出市场需求的产品数量,这会导致库存积压和资金浪费。
在精益生产中,通过精确预测市场需求,避免过度生产,可以减少库存积压,降低资金占用成本。
第二大浪费是等待时间。
在生产过程中,由于零部件供应不及时或者生产线不畅,会导致生产线停滞,工人等待。
这样的等待时间会增加生产周期,降低生产效率。
精益生产强调及时供应和生产线平衡,以减少等待时间。
第三大浪费是运输。
过多的物料运输会增加运输成本,延长生产周期,并增加物料损坏的风险。
精益生产提倡就近生产和精细化物料运输,以减少运输浪费。
第四大浪费是过度加工。
过度加工是指对产品进行超出需求的加工,这会增加生产成本,降低生产效率。
精益生产强调精确理解市场需求,避免过度加工,以提高生产效率。
第五大浪费是库存。
过多的库存会增加资金占用成本,并增加库存积压的风险。
精益生产强调“用时生产”和“精准库存”,以减少库存浪费。
第六大浪费是不合格品。
不合格品会增加返工成本,并影响产品质量和客户满意度。
精益生产强调质量控制和持续改进,以减少不合格品浪费。
第七大浪费是人员运动。
不必要的人员运动会增加生产成本,并降低生产效率。
精益生产强调生产线布局和工作流程优化,以减少人员运动浪费。
第八大浪费是设计不当。
设计不当会导致生产过程中出现问题,增加生产成本和生产周期。
精益生产强调产品设计和生产工艺的协同优化,以减少设计不当浪费。
在实践中,工厂可以通过精益生产的方法,识别并消除这八大浪费,从而提高生产效率,降低生产成本,提高产品质量。
精益生产并不是一蹴而就的过程,需要持续改进和全员参与,但通过不懈努力,工厂一定能够取得显著的成效。
生产中的八大浪费

生产中的八大浪费1.不良、修理的浪费:所谓不良、修理的浪费,指的是由于工厂内出现不良品,需要进行处置的时间、人力、物力上的浪费,以及由此造成的相关损失。
这类浪费具体包括:材料的损失、不良品变成废品;设备、人员和工时的损失;额外的修复、鉴别、追加检查的损失;有时需要降价处理产品,或者由于耽误出货而导致工厂信誉的下降。
2.加工的浪费加工的浪费也叫过分加工的浪费,主要包含两层含义:第一是多余的加工和过分精确的加工,例如实际加工精度过高造成资源浪费;第二是需要多余的作业时间和辅助设备,还要增加生产用电、气压、油等能源的浪费,另外还增加了管理的工时。
3.动作的浪费动作的浪费现象在很多企业的生产线中都存在,常见的动作浪费主要有以下12种:两手空闲、单手空闲、作业动作突然停止、作业动作过大、左右手交换、步行过多、转身的角度太大,移动中变换“状态”、不明技巧、伸背动作、弯腰动作以及重复动作和不必要的动作等,这些动作的浪费造成了时间和体力上的不必要消耗。
4.搬运的浪费搬运是一种不产生附加价值的动作,而不产生价值的工作都属于浪费。
搬运的浪费具体表现为放置、堆积、移动、整列等动作浪费,由此而带来物品移动所需空间的浪费、时间的浪费和人力工具的占用等不良后果。
5.库存的浪费由于库存很多,将故障、不良品、缺勤、计划外停机、计划有误、调整时间过长、品质不一致、能力不平衡等问题全部掩盖住了。
6.制造过多或过早的浪费制造过多或过早,提前用掉了生产费用,不但没有好处,还隐藏了由于等待所带来的浪费,失去了持续改善的机会。
有些企业由于生产能力比较强大,为了不浪费生产能力而不中断生产,增加了在制品,使得制品周期变短、空间变大,还增加了搬运、堆积的浪费。
此外,制造过多或过早,会带来庞大的库存量,利息负担增加,不可避免地增加了贬值的风险。
7.等待的浪费由于生产原料供应中断、作业不平衡和生产计划安排不当等原因造成的无事可做的等待,被称为等待的浪费。
精益生产八大浪费记忆口诀
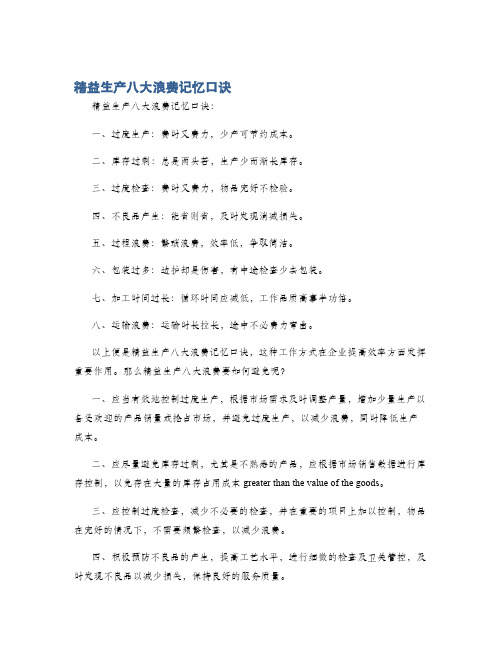
精益生产八大浪费记忆口诀精益生产八大浪费记忆口诀:一、过度生产:费时又费力,少产可节约成本。
二、库存过剩:总是两头苦,生产少而渐长库存。
三、过度检查:费时又费力,物品完好不检验。
四、不良品产生:能省则省,及时发现消减损失。
五、过程浪费:繁琐浪费,效率低,争取简洁。
六、包装过多:边护却是伤害,有中途检查少去包装。
七、加工时间过长:循环时间应减低,工作品质高事半功倍。
八、运输浪费:运输时长拉长,途中不必费力弯曲。
以上便是精益生产八大浪费记忆口诀,这种工作方式在企业提高效率方面发挥重要作用。
那么精益生产八大浪费要如何避免呢?一、应当有效地控制过度生产,根据市场需求及时调整产量,增加少量生产以备受欢迎的产品销量或抢占市场,并避免过度生产,以减少浪费,同时降低生产成本。
二、应尽量避免库存过剩,尤其是不熟悉的产品,应根据市场销售数据进行库存控制,以免存在大量的库存占用成本 greater than the value of the goods。
三、应控制过度检查,减少不必要的检查,并在重要的项目上加以控制,物品在完好的情况下,不需要频繁检查,以减少浪费。
四、积极预防不良品的产生,提高工艺水平,进行细微的检查及卫关管控,及时发现不良品以减少损失,保持良好的服务质量。
五、尽量减少过程浪费,提高工作效率,尽量减少在整个生产过程中出现的多余流程,提高效率,降低成本。
六、减少包装过多,如果产品在途中不需要中途检查,应减少包装材料,以减少成本。
七、加工时间应合理,尽可能减少无谓的的加工时间,缩短车间的循环时间,尽可能提高工作效率和品质。
八、努力减少运输浪费,尽量减少物流运输途中出现的弯曲以及勉力以减少运输时长,提高效率降低成本。
通过以上介绍可以看出,精益生产八大浪费的记忆口诀尤其重要,应认真进行推行,以节约成本,提高效率,让企业发展得更快更好。
八大浪费
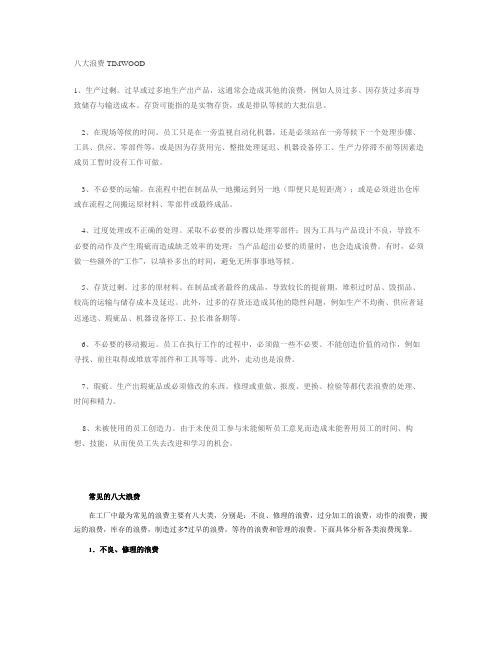
八大浪费TIMWOOD1、生产过剩。
过早或过多地生产出产品,这通常会造成其他的浪费,例如人员过多、因存货过多而导致储存与输送成本。
存货可能指的是实物存货,或是排队等候的大批信息。
2、在现场等候的时间。
员工只是在一旁监视自动化机器,还是必须站在一旁等候下一个处理步骤、工具、供应、零部件等,或是因为存货用完、整批处理延迟、机器设备停工、生产力停滞不前等因素造成员工暂时没有工作可做。
3、不必要的运输。
在流程中把在制品从一地搬运到另一地(即便只是短距离);或是必须进出仓库或在流程之间搬运原材料、零部件或最终成品。
4、过度处理或不正确的处理。
采取不必要的步骤以处理零部件;因为工具与产品设计不良,导致不必要的动作及产生瑕疵而造成缺乏效率的处理;当产品超出必要的质量时,也会造成浪费。
有时,必须做一些额外的“工作”,以填补多出的时间,避免无所事事地等候。
5、存货过剩。
过多的原材料、在制品或者最终的成品,导致较长的提前期,堆积过时品、毁损品、较高的运输与储存成本及延迟。
此外,过多的存货还造成其他的隐性问题,例如生产不均衡、供应者延迟递送、瑕疵品、机器设备停工、拉长准备期等。
6、不必要的移动搬运。
员工在执行工作的过程中,必须做一些不必要、不能创造价值的动作,例如寻找、前往取得或堆放零部件和工具等等。
此外,走动也是浪费。
7、瑕疵。
生产出瑕疵品或必须修改的东西。
修理或重做、报废、更换、检验等都代表浪费的处理、时间和精力。
8、未被使用的员工创造力。
由于未使员工参与未能倾听员工意见而造成未能善用员工的时间、构想、技能,从而使员工失去改进和学习的机会。
常见的八大浪费在工厂中最为常见的浪费主要有八大类,分别是:不良、修理的浪费,过分加工的浪费,动作的浪费,搬运的浪费,库存的浪费,制造过多?过早的浪费,等待的浪费和管理的浪费。
下面具体分析各类浪费现象。
1.不良、修理的浪费所谓不良、修理的浪费,指的是由于工厂内出现不良品,需要进行处置的时间、人力、物力上的浪费,以及由此造成的相关损失。
- 1、下载文档前请自行甄别文档内容的完整性,平台不提供额外的编辑、内容补充、找答案等附加服务。
- 2、"仅部分预览"的文档,不可在线预览部分如存在完整性等问题,可反馈申请退款(可完整预览的文档不适用该条件!)。
- 3、如文档侵犯您的权益,请联系客服反馈,我们会尽快为您处理(人工客服工作时间:9:00-18:30)。
前工序過量投入(WIP):工時不平衡﹔Push方式﹔ 看板信息錯誤﹔不是一個流作業﹔工作紀律﹔
例﹕如下圖所示﹐后工程在單位時間內需求1台/次﹐ 提供8台/次﹔
2020/3/24
PCEG DT(II) IE
二. 過生產浪費
(四) 浪費的消除:
過量計划(Schedule)﹕計算機信息集成控制﹔ 准確掌控不良(報廢)率﹔制訂寬放標准和計划校 正機制﹔縮短交付周期(CT﹑批量)﹔
前工序過量投入(WIP)﹕生產線平衡; Pull方 式﹔制訂單次傳送量標准﹔一個流作業﹔作業要 求﹔
交付周期=∑(CT*批量)
2020/3/24
PCEG DT(II) IE更甚﹕未及時轉化→資金周轉→市場反應→企業轉型
貨幣資金 不暢 速度慢
困難
2020/3/24
(企業經營﹕資金運動﹑物質運動﹑信息運動)
PCEG DT(II) IE
二. 過生產浪費
(二) 浪費的表現:
人(Man)﹕整理﹐包裝﹐搬運﹐無功作業
機(Machine)﹕人的動作增加而等待
料(Material)﹕報廢﹐庫存﹐WIP﹐入庫檢查等
2020/3/24
PCEG DT(II) IE
因為不良 品而誕 生…
一. 不良品浪費
(三) 浪費的產生:
供應 制造
來料不良(Incoming)﹕供應商流出不良品﹔ 使用 物流破壞﹔進料檢驗﹑投入檢查或后工序 未發現﹔制程不防呆﹔
制程不良(Process)﹕作業者損壞﹔設備﹑治工具 不防呆﹔制程不防呆﹔
三. 過程浪費
(二) 浪費的表現:
人(Man)﹕無功動作﹐等待 機(Machine)﹕等待(空載),生產力低,成本高 料(Material)﹕耗材﹐成本高 法(Method)﹕不增值﹐過度
2020/3/24
PCEG DT(II) IE
三. 過程浪費
(三) 浪費的產生:
流程(Flow)﹕流程設計﹔Layout﹔參數設定﹔ 制造系統柔性﹔浪費警覺性﹔條件局限性﹔ 強度(Strength)﹕系統穩定性﹔標准﹔
生产过程中八大浪费
2020/3/24
八大浪費介紹
不良品浪費 ❖ 過生產浪費 過程浪費 動作浪費 庫存浪費 移動浪費 不平衡浪費 管理浪費
2020/3/24
PCEG DT(II) IE
一. 不良品浪費
(一) 浪費的定義:
生產過程中,因來料或制程不良,造成的各種 損失, 如:
直接﹕物料報廢、搬運、返工以及后工序的等 待, ……
2020/3/24
PCEG DT(II) IE
四. 動作浪費
(二) 浪費的表現:
人(Man)﹕動作無價值﹔勞動強度大﹔尋找﹔ 機(Machine)﹕等待﹔ 料(Material)﹕易損傷﹔增加客戶不需要的材料; 法(Method)﹕程序復雜;
2020/3/24
PCEG DT(II) IE
四. 動作浪費
法(Method)﹕作業不便﹐拆卸﹐庫存管理 Waitin
g…
環(Environment)﹕存放區﹐搬運
…
2020/3/24
WIP=Work In Process
PCEG DT(II) IE
二. 過生產浪費
(三) 浪費的產生:
過量計划(Schedule)﹕信息不准﹔計划錯誤﹔計 划失當﹔信息傳遞不暢﹔制程反應速度慢﹔
PCEG DT(II) IE
四. 動作浪費
(一) 浪費的定義:
生產作業時調整位置﹑翻轉產品﹑取 放工具物料等不必要的動作浪費﹐如﹕
直接﹕動作浪費﹑時間等待﹑容易損傷產品﹑ 更甚﹕操作時間長→生產率低→成本高
勞動強度增加
滿意度低
2020/3/24
PCEG DT(II) IE
(如例)
不必要裝PE袋 不必要的分開
制程不良(Process)﹕及時指正﹔培訓技能﹔設 備﹑治工具﹑工藝流程防呆﹔
使用者破壞(User)﹕及時提醒﹔醒目標示﹔培 訓﹔教導﹔
2020/3/24
PCEG DT(II) IE
二. 過生產浪費
(一) 浪費的定義:
前工程之投入量﹐超過后工程單位時間內之 需求量﹐而造成的浪費﹐如﹕
直接﹕搬運﹐堆積﹐庫存﹐超過終點需求而造成 的拆卸﹑報廢等……
更甚﹕質量不穩定→客戶抱怨→顧客忠誠↓﹑ 庫存↑ →采購(供應)計划紊亂……
2020/3/24
PCEG DT(II) IE
一. 不良品浪費
(二) 浪費的表現:
人(Man)﹕搬運﹐重工﹐維修﹐更換﹐等待 機(Machine)﹕等待或空載 料(Material)﹕報廢﹐退換﹐庫存 法(Method)﹕拆卸﹐分析﹐判斷 環(Environment)﹕存放區﹐搬運﹐維修區
(三) 浪費的產生:
操作不經濟(Handling)﹕動作不精簡﹔動作多余 設計不合理(Design)﹕可同時完成但未同時﹔
2020/3/24
PCEG DT(II) IE
三. 過程浪費
(四) 浪費的產消除:
流程(Flow)﹕簡化生產流程﹔提高系統柔性﹔ 改變工作台面布置﹑擺放方式﹑參數設定﹔ “縮短距離﹑減少阻力﹑簡化程序﹑精減過程” 強度(Strength)﹕系統穩定性﹔制訂強度標 准﹔明確操作要求﹔制程防呆……
2020/3/24
1) 兩點間距離寬﹔
始 始 末末
2) 机器行程大; 起子轉速慢﹐程式運行時間長
3) 動作的過程(距離﹑阻力﹑復雜程度)
4) 材料強度過剩﹕如螺絲長度,用不必要的耗 材(膠水、膠帶等)﹔
5) 操作強度過剩﹕多余的習慣動作(如清潔等 重復性動作)。
(如圖)
2020/3/24
PCEG DT(II) IE
三. 過程浪費
(一) 浪費的定義:
作業的流程過多﹑過長﹑重復﹐或強度過 剩﹑Over design 等造成的浪費﹐如﹕
直接﹕動作浪費﹔等待﹔材料浪費﹔設備生產力 低﹑折舊成本高……(如例所示)
更甚﹕交付周期增長→資金周轉慢 →損失潛在顧客
2020/3/24
PCEG DT(II) IE
過程浪費的例子:
使用者破壞(User)﹕未提醒﹔未按要求﹔人為破 壞﹔不小心損壞﹔設計不防呆﹔
2020/3/24
PCEG DT(II) IE
一. 不良品浪費
(四) 浪費的消除:
SQM﹑供 應商輔導
來料不良(Incoming)﹕及時制止﹔供應商改善 (制程﹑品管系統﹑包裝物流)﹔進料品質控制﹔ 提醒投入者注意﹔制程防止不良流出﹔