粉末冶金的成型工艺
2024年粉末冶金工艺的基本工序(2篇)

2024年粉末冶金工艺的基本工序1、原料粉末的制备。
现有的制粉方法大体可分为两类:机械法和物理化学法。
而机械法可分为:机械粉碎及雾化法;物理化学法又分为:电化腐蚀法、还原法、化合法、还原-化合法、气相沉积法、液相沉积法以及电解法。
其中应用最为广泛的是还原法、雾化法和电解法。
2、粉末成型为所需形状的坯块。
成型的目的是制得一定形状和尺寸的压坯,并使其具有一定的密度和强度。
成型的方法基本上分为加压成型和无压成型。
加压成型中应用最多的是模压成型。
3、坯块的烧结。
烧结是粉末冶金工艺中的关键性工序。
成型后的压坯通过烧结使其得到所要求的最终物理机械性能。
烧结又分为单元系烧结和多元系烧结。
对于单元系和多元系的固相烧结,烧结温度比所用的金属及合金的熔点低;对于多元系的液相烧结,烧结温度一般比其中难熔成分的熔点低,而高于易熔成分的熔点。
除普通烧结外,还有松装烧结、熔浸法、热压法等特殊的烧结工艺。
4、产品的后序处理。
烧结后的处理,可以根据产品要求的不同,采取多种方式。
如精整、浸油、机加工、热处理及电镀。
此外,近年来一些新工艺如轧制、锻造也应用于粉末冶金材料烧结后的加工,取得较理想的效果。
2024年粉末冶金工艺的基本工序(2)2024年的粉末冶金工艺基本工序包括精细化粉末的制备、粉末成型、烧结和后处理等四个环节。
下面将详细介绍这些工序的主要内容。
一、精细化粉末的制备精细化粉末的制备是粉末冶金工艺的第一步,关乎着制备出高质量的粉末。
2024年,精细化粉末的制备将会注重以下几个方面的发展:1.1 原料的选择与准备:2024年,随着科学技术的进步,矿石和废料等资源的利用效率将取得显著提高。
在制备粉末时,将更加注重对原料的选择与准备,使得原料的化学成分更加纯净,杂质含量更低。
1.2 粉末的粒度控制:粉末的粒度对材料的性能影响巨大。
粒度过大会影响材料的强度和塑性,而粒度过小则会降低流动性。
因此,粉末的粒度控制将成为2024年粉末冶金工艺中的重要研究方向。
粉末冶金与陶瓷材料的成型工艺技术

粉末冶金与陶瓷材料的成型工艺技术粉末冶金是一种重要的材料成型技术,它通过将金属或非金属粉末在高温下压制成形,进而得到各种金属零件和陶瓷材料。
粉末冶金不仅可以制造出形状复杂的零件,还能够获得优良的材料性能,因此被广泛应用于汽车、航空、航天等工业领域。
粉末冶金的成型工艺技术主要分为两个步骤:粉末的制备和成型。
首先是粉末的制备。
粉末冶金所需的粉末通常通过机械研磨、化学反应、气相沉积等方法制备而成。
机械研磨是最常用的方法,它通过将金属块或合金块放入球磨机中与磨料球一起进行高速旋转,使金属块逐渐研磨成粉末。
化学反应法利用化学反应生成粉末,例如气相法将金属气体于高温下反应生成粉末。
制备好的粉末应具备一定的粒度、形状和分布以满足成型的需求。
其次是成型工艺技术。
成型是将粉末压制成所需形状的过程。
常用的成型工艺有冷压成型、等静压成型和注浆成型等。
冷压成型是最简单的成型方法,它通过将粉末放置在模具中,然后在模具上施加压力,使粉末紧密结合成形。
但冷压成型得到的零件强度较低,通常需要进行后续的烧结工艺。
等静压成型是常用的粉末冶金成型方法。
它通过在模具中施加等压力,使粉末均匀密实地填充模具,然后通过高温烧结使粉末颗粒结合成致密的金属材料。
等静压成型可以获得高密度、高强度的零件,适用于制造各种金属零件。
注浆成型是粉末冶金的一种新型成型工艺。
它通过在模具中注入粉末与流体混合物,然后通过高压使混合物注入模具的空隙中,最后再进行烧结。
注浆成型可以制造出形状复杂的零件,并且具有较高的密度和强度。
总之,粉末冶金是一种重要的材料成型技术,它通过粉末的制备和成型工艺来制造各种金属零件和陶瓷材料。
不同的成型工艺可以得到不同性能的材料,所以在应用中需要根据具体要求来选择合适的成型工艺。
粉末冶金是一种重要的材料成型技术,其广泛应用于汽车、航空、航天等众多领域。
通过将金属或非金属粉末在高温下压制成形,可获得形状复杂且性能优良的材料。
下面将进一步探讨粉末冶金与陶瓷材料的成型工艺技术。
粉金的工艺
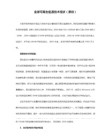
切削加工:一般情况下,烧结好的图纸要求尺寸和精度。
粉末冶金零部件虽然余量小但是由于其独特的多孔性很难加工。多孔性是粉末冶金广泛应用的原因,但也是难加工的主要原因。多孔性会导致刀具不耐磨,或长时间的加工致使刀具破裂,针对以上问题,可有效加工粉末冶金零件的刀具材料主要是立方氮化硼刀具,尤其是研制的非金属粘合剂立方氮化硼刀具牌号,不仅可承受1400℃的高温,而且本身刀体的硬度在HRC98.5左右。是加工黑色金属领域硬度高的刀具材料。并且的牌号立方氮化硼刀具属于非金属粘合剂立方氮化硼刀具,不仅硬度高,耐磨性好,而且抗冲击性强,加工粉末冶金可一刀加工完成,刀具寿命长是硬质合金刀具的25倍,传统CBN刀具的4倍。
成品:经过切削加工之后,得到图纸要求尺寸和精度成为成品。
成型:粉末在15-600MPa压力下,压成所需形状。成型有热压和冷压,目的是获得一定形状和尺寸的压坯,并使其具有一定的密度和强度。成型的方法基本上分为加压成型和无压成型。加压成型中应用多的是模压成型。
烧结:在保护气氛的高温炉或真空炉中进行。是粉末冶金工艺中的关键性工序。成型后的压坯通过烧结使其得到所要求的物理机械性能。烧结过程中粉末颗粒间通过扩散、再结晶、熔焊、化合、溶解等一系列的物理化学过程,成为具有一定孔隙度的冶金产品。
粉末冶金由于其独特的性能广泛应用于交通、纺织机械,电动工具,五金工具,电器、工程机械等行业。那粉末冶金是如何制造出来的呢?下面就简单介绍一下粉末冶金的制造工艺。
粉末冶金的加工工艺路线为:原材料的准备—成型—烧结—后序处理—切削加工—成品。
粉体成型工艺课件
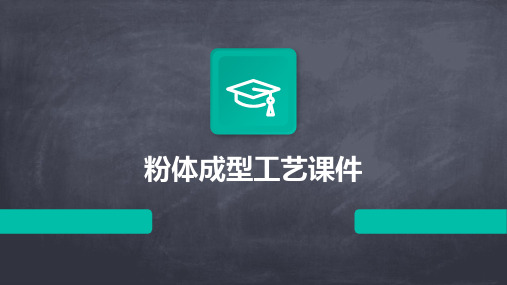
整、尺寸精确的成型件。
烧成与冷却
烧成
化,形成所需的结构和性能。
冷却
烧成后对成型件进行快速冷却,以获得良好的组 织和性能。
烧成制度
制定合理的烧成制度,包括烧成温度、时间、气 氛等参数,以确保烧成过程顺利进行。
04
粉体成型工艺参数
Chapter
资源循环利用
对废弃粉体材料进行回 收再利用,实现资源循 环利用。
未来市场前景与挑战
市场前景广阔
随着科技的发展和产业升级,粉体成型工艺在新能源、新 材料、高端制造等领域有广泛应用。
技术创新是关键
持续推动粉体成型工艺的技术创新,以满足不断变化的市 场需求。
跨领域合作与协同创新
加强与相关领域的合作与交流,共同推动粉体成型工艺的 发展。
成型过程中的驱动力包括粉体颗 粒间的黏结力、外部施加的压力 等,驱动力的大小和作用方式决
定了制品的结构和性能。
填充与致密化
粉体颗粒在模具内通过流动、重排 、压缩等方式达到填充完全和致密 化。
冷却与脱模
成型后的制品需要经过冷却定型, 然后从模具中脱出。
03
粉体成型工艺流程
Chapter
原料准备与处理
THANKS
感谢观看
粉体成型工艺的应用领域
粉体成型工艺广泛应用于汽车、航空航天、电子、能源等领域。
在汽车领域,粉体成型工艺主要用于生产发动机零件、变速器零件等;在航空航天领域,粉体成型工 艺主要用于制造高性能的轻质材料和结构件;在电子领域,粉体成型工艺主要用于制造电子元件和传 感器等;在能源领域,粉体成型工艺主要用于生产电池电极和燃料电池等。
原料性质的影响
原料的粒度
原料的粒度大小直接影响粉体的流动性、填充性以及成型时的致密度。较细的粒度可以提高粉体的流动性,但过细的 粒度可能导致成型时开裂。
粉末冶金课件
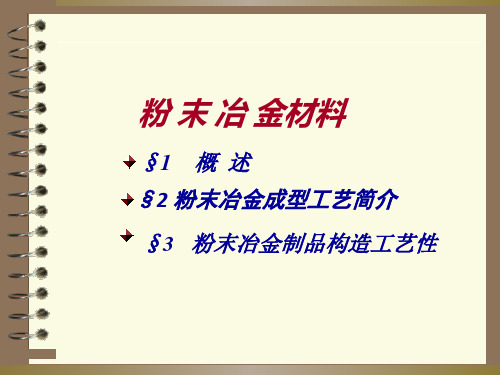
•塑耐性腐变蚀形性能等
•表面状态
•表面张力等
粉末冶金成型
§2 粉末冶金成型工艺简介
3.粉末旳预处理与混合
(1)粉末旳预处理 (2)粉末混合
• 混合 – 两种以上化学组元相混合 (相同化学构成旳粉末旳混合叫做合并。)
• 目旳 – 使性能不同旳组元形成均匀旳混合物, 以利于压制和烧结时状态均匀一致。
为何预处理? a.虽然在同一条件下制造旳同一粉末,其纯度和粒
• 应用 – 制造Fe 、Pb、Sn、Zn、Al、青铜、 黄铜等低熔点金属与合金粉末; – 18-8不锈钢、低合金钢、镍合金等 粉末。
(2) 机械粉碎法
是靠压碎、击碎和磨削等作用,将 块状金属或合金机械地粉碎成粉末。
粉末冶金成型
(2) 机械粉碎法 • 特点:
– 既是一种独立制粉措施, – 又常作为某些制粉措施不可缺乏旳
▪ 据作业旳连续性分 – 间歇式烧结炉—坩埚炉箱式炉 – 高频或中频感应炉
– 大气环境
– 连续式烧结炉
• 产生“过烧”废品
– 烧结温度过高或时间过长,使压坯歪曲和变形,其晶粒也 大;
• 产生“欠烧”废品
– 烧结温度过低或时间过短,产品结合强度等性能达不到要 求;
粉末冶金成型
§2 粉末冶金成型工艺简介
粉末冶金成型
§1 概 述
五、应用
板、带、棒、管、丝等多种型材
成批或 齿轮、链轮、棘轮、轴套类等多种零件 大量生产 重量仅百分之几克旳小制品
近两吨重大型坯料(用热等静压法)
粉末冶金成型
粉末冶金成型
§2 粉末冶金成型工艺简介
粉料制备
压制成型
烧结
粉末冶金成品
烧结后旳处理
§2 粉末冶金成型工艺简介
粉末冶金的工艺流程-粉末成形

简介 粉末冶金生产中的基本工序之一,目的是将松散的粉末制成具有预定几何形
状、尺寸、密度和强度的半成品或成品。模压(钢模)成形是粉末冶金生产中采 用最广的成形方法。18世纪下半叶和19世纪上半叶,西班牙、俄国和英国为制造 铂制品,都曾采用了相似的粉末冶金工艺。当时俄国索博列夫斯基 (П.Г.Соболевсκий)使用 的是 钢模 和螺 旋压 机。 英 国的 沃拉 斯顿 (W.H.Wol laston )使 用 压 力 更 大 的 拉 杆 式 压 机 和 纯 度 更 高 的 铂 粉 ,制 得 了 几 乎 没 有 残余孔隙的致密铂材。后来,模压成形方法逐渐完善,并用来制造各种形状的铜 基 含 油 轴 承 等 产 品 。 20世 纪 30年 代 以 来 , 在 粉 末 冶 金 零 件 的 工 业 化 生 产 过 程 中 , 压 机 设 备 、模 具 设 计 等 方 面 不 断 改 进 , 模 压 成 形 方 法 得 到 了 更 大 的 发 展 ,机 械 化 和 自动化已达到较高的程度。为了扩大制品的尺寸和形状范围,特别是为了提高制 品密度和改善密度的均匀性相继出现和发展了多种成形方法。早期出现的有粉末 轧制、冷等静压制、挤压、热压等;50年代以来又出现了热等静压制、热挤压、 热锻等热成形方法。这些方法推动了全致密、高性能粉末金属材料的生产。 主要功能
料 为 金 属( 低 碳 钢 、不 锈 钢 、钛 ),还 可 用 玻 璃 和 陶 瓷 。由 于 温 度 和 等 静 压 力 的 同 时作用,可使许多种难以成形的材料达到或接近理论密度,并且晶粒细小,结构 均匀,各向同性和具有优异的性能。热等静压法最适宜于生产硬质合金、粉末高 温合金、粉末高速钢和金属铍等材料和制品;也可对熔铸制品进行二次处理,消 除气孔和微裂纹;还可用来制造不同材质紧密粘接的多层或复合材料与制品。 粉末锻造
粉末冶金工艺
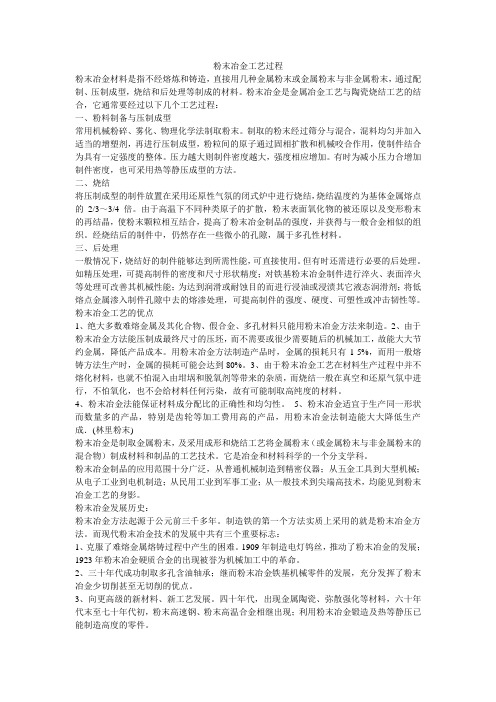
粉末冶金工艺过程粉末冶金材料是指不经熔炼和铸造,直接用几种金属粉末或金属粉末与非金属粉末,通过配制、压制成型,烧结和后处理等制成的材料。
粉末冶金是金属冶金工艺与陶瓷烧结工艺的结合,它通常要经过以下几个工艺过程:一、粉料制备与压制成型常用机械粉碎、雾化、物理化学法制取粉末。
制取的粉末经过筛分与混合,混料均匀并加入适当的增塑剂,再进行压制成型,粉粒间的原子通过固相扩散和机械咬合作用,使制件结合为具有一定强度的整体。
压力越大则制件密度越大,强度相应增加。
有时为减小压力合增加制件密度,也可采用热等静压成型的方法。
二、烧结将压制成型的制件放置在采用还原性气氛的闭式炉中进行烧结,烧结温度约为基体金属熔点的2/3~3/4倍。
由于高温下不同种类原子的扩散,粉末表面氧化物的被还原以及变形粉末的再结晶,使粉末颗粒相互结合,提高了粉末冶金制品的强度,并获得与一般合金相似的组织。
经烧结后的制件中,仍然存在一些微小的孔隙,属于多孔性材料。
三、后处理一般情况下,烧结好的制件能够达到所需性能,可直接使用。
但有时还需进行必要的后处理。
如精压处理,可提高制件的密度和尺寸形状精度;对铁基粉末冶金制件进行淬火、表面淬火等处理可改善其机械性能;为达到润滑或耐蚀目的而进行浸油或浸渍其它液态润滑剂;将低熔点金属渗入制件孔隙中去的熔渗处理,可提高制件的强度、硬度、可塑性或冲击韧性等。
粉末冶金工艺的优点1、绝大多数难熔金属及其化合物、假合金、多孔材料只能用粉末冶金方法来制造。
2、由于粉末冶金方法能压制成最终尺寸的压坯,而不需要或很少需要随后的机械加工,故能大大节约金属,降低产品成本。
用粉末冶金方法制造产品时,金属的损耗只有1-5%,而用一般熔铸方法生产时,金属的损耗可能会达到80%。
3、由于粉末冶金工艺在材料生产过程中并不熔化材料,也就不怕混入由坩埚和脱氧剂等带来的杂质,而烧结一般在真空和还原气氛中进行,不怕氧化,也不会给材料任何污染,故有可能制取高纯度的材料。
粉末冶金工艺的基本工序
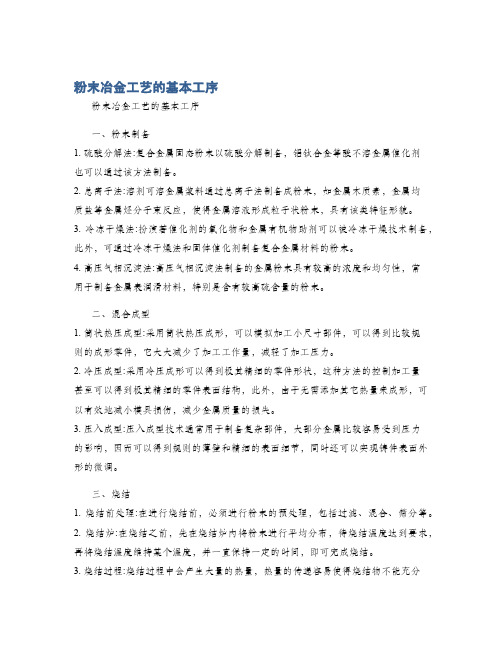
粉末冶金工艺的基本工序粉末冶金工艺的基本工序一、粉末制备1. 硫酸分解法:复合金属固态粉末以硫酸分解制备,铝钛合金等酸不溶金属催化剂也可以通过该方法制备。
2. 总离子法:溶剂可溶金属浆料通过总离子法制备成粉末,如金属木质素,金属均质盐等金属烃分子束反应,使得金属溶液形成粒子状粉末,具有该类特征形貌。
3. 冷冻干燥法:扮演著催化剂的氧化物和金属有机物助剂可以被冷冻干燥技术制备,此外,可通过冷冻干燥法和固体催化剂制备复合金属材料的粉末。
4. 高压气相沉淀法:高压气相沉淀法制备的金属粉末具有较高的浓度和均匀性,常用于制备金属表润滑材料,特别是含有较高硫含量的粉末。
二、混合成型1. 筒状热压成型:采用筒状热压成形,可以模拟加工小尺寸部件,可以得到比较规则的成形零件,它大大减少了加工工作量,减轻了加工压力。
2. 冷压成型:采用冷压成形可以得到极其精细的零件形状,这种方法的控制加工量甚至可以得到极其精细的零件表面结构,此外,由于无需添加其它热量来成形,可以有效地减小模具损伤,减少金属质量的损失。
3. 压入成型:压入成型技术通常用于制备复杂部件,大部分金属比较容易受到压力的影响,因而可以得到规则的薄壁和精细的表面细节,同时还可以实现铸件表面外形的微调。
三、烧结1. 烧结前处理:在进行烧结前,必须进行粉末的预处理,包括过滤、混合、筛分等。
2. 烧结炉:在烧结之前,先在烧结炉内将粉末进行平均分布,待烧结温度达到要求,再将烧结温度维持某个温度,并一直保持一定的时间,即可完成烧结。
3. 烧结过程:烧结过程中会产生大量的热量,热量的传递容易使得烧结物不能充分的受热,而出现部分未烧结的现象。
4. 烧结温度控制:因此,在烧结过程中对温度有较为严格的控制要求,烧结室内和外温度的精确控制可以有效地提高烧结率,保证烧结质量。
四、制备复合材料1. 试剂混合法:一般采用试剂混合法,使用试剂使粉末熔化成金属液,将两种粉末液分别滴入容器内,然后混合,固化,再烧结,形成复合材料,其优点是可以快速产生复合材料,但受试剂的影响,使得成型容易受到外界环境的影响。
- 1、下载文档前请自行甄别文档内容的完整性,平台不提供额外的编辑、内容补充、找答案等附加服务。
- 2、"仅部分预览"的文档,不可在线预览部分如存在完整性等问题,可反馈申请退款(可完整预览的文档不适用该条件!)。
- 3、如文档侵犯您的权益,请联系客服反馈,我们会尽快为您处理(人工客服工作时间:9:00-18:30)。
粉末冶金的成型工艺
粉末冶金技术是目前重要的制造工艺之一,是用粉末冶金技术制造金属零件的过程。
它是由许多工艺步骤构成的,从制备原料到成形零件,其中包括制备原料、颗粒粒度控制、粉末成型、热处理、表面改性等。
粉末冶金技术不仅可以用于制造金属部件,而且还可以制造非金属部件,如硅酸盐、碳纤维增强塑料等。
制备原料是粉末冶金的第一步,主要是将金属原料(如金属粉末或粒子)制备成粉末状,以便进行成型处理。
一般来说,金属原料可以通过粉碎、混合、蒸发、蒸馏等方式制备粉末。
在制备好粉末之后,要进行粒度分析,以保证粉末分布在合理的粒度范围内,以保证粉末的成型工艺。
粉末成型是粉末冶金技术的主要步骤。
粉末成型可以通过压缩(pressing)、铸造(casting)、挤出(extruding)和热压(sintering)
等工艺步骤实现,可以生产出复杂的形状的零件。
压缩成型是将粉末填充到模具中,然后通过压力将粉末装配成所需的形状。
铸造是将粉末流入模具中,并通过冷却硬化成形。
挤出是将粉末放入模具中,并通过压力将粉末挤出形成所需的形状。
热压成形是将粉末装入模具中,然后通过热压将其黏结成所需的形状。
热处理是在粉末成型工艺后的一种必要步骤。
根据要求,可以选择退火、正火、回火和硬化等热处理方式。
这种处理可以改变零件的力学性能,并使零件更加坚固耐用。
最后,表面改性是一种用于增强零件表面性能的步骤。
表面改性
可以通过电镀、喷涂、热处理等方式实现,可以增强表面粗糙度,提高表面质量,以及增强零件的耐腐蚀性和耐高温性能。
粉末冶金是一种先进的制造技术,目前已经被广泛应用于许多领域。
它的特点是快速、高效、节能,可以制作出精密、复杂的零件。
在当今制造行业,粉末冶金的成型工艺是一个不可或缺的步骤,可以满足不同行业的生产需求,为各行业制造出更多、更精细的零件。
总之,粉末冶金的成型工艺是一项复杂而重要的技术,其过程从制备原料到表面改性,有着许多复杂的工艺步骤,因此控制其质量和精度非常重要。
如果能够正确地操作,可以生产出质量优异、精度高的零件,为制造行业提供更高效的技术支持。