粉末冶金成型工艺
粉末冶金成型
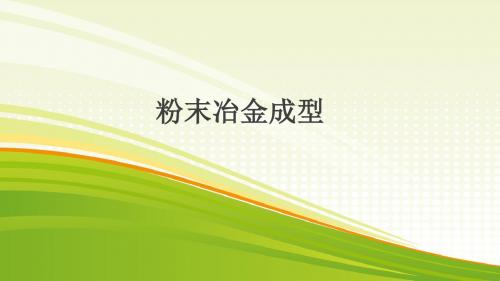
4 粉末冶金成型的应用
4.1 信息领域的粉末冶金材料 4.2 能源领域的粉末冶金材料
稀土永磁材料
硅类4.4 军事领域的粉末冶金材料
生物医用材料
武器弹药
5 粉末冶金技术发展前景
5.1 粉末注射成形技术
粉末注射成型零件
5.2 温压成型技术 温压成型技术在制造过程中最主要的技术是如何增强混合 粉末的流动性,提高制成品的性能。
温压成型零件
5.3 烧结硬化技术 烧结硬化技术主要的原理是:在烧结过程中,快速的冷却, 进而可以大幅度提高产品的质量,提高材料强度。
烧结工艺图
1.1 粉末冶金工艺流程图
2 粉末冶金的工艺特点
2.1 粉末冶金工艺的优点 粉末冶金技术能够降低对金属的损耗,并且粉末冶金能够 在生产过程中将一些杂质进行隔离,并且在冶金过程中保 证材料不受到任何污染,从而实现了高纯度的冶金材料。
2.2 粉末冶金与传统材料工艺相比的优点 粉末冶金材料具有以下特点:粉末冶金过程在低熔点下进行, 所以可以得到各种金属的密度差异,具有快速凝固、晶粒 细小均匀,保证组织均匀性能稳定,良好的冷、热加工性 能,且不受合金元素和含量的限制,可以提高强化相的含 量,使材料得以发展。
粉末冶金成型
目录
粉末冶金成型工艺 粉末冶金的工艺特点 粉末冶金成型的方法 粉末冶金成型的应用 粉末冶金技术发展前景
1 粉末冶金成型工艺
粉末冶金成型是指采用 金属或其他粉末材料,经过 混粉、压坯、烧结、成型和 后处理等工艺过程制造各种 多孔、半致密零件与制品的 技术。 粉末冶金零件
3 粉末冶金成型的方法
a. 压制成型 压制成型是将金属粉末或者混合装在钢制压模内,通过模冲 对粉末加压形成压坯的过程。 b. 等静压成型
粉末冶金的成型工艺
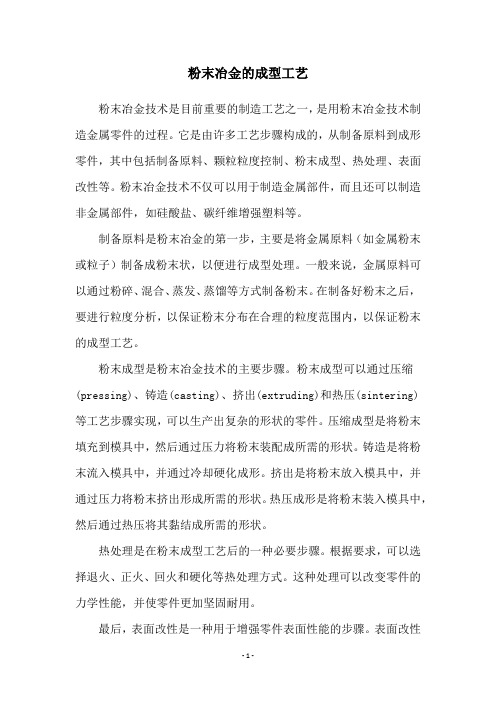
粉末冶金的成型工艺粉末冶金技术是目前重要的制造工艺之一,是用粉末冶金技术制造金属零件的过程。
它是由许多工艺步骤构成的,从制备原料到成形零件,其中包括制备原料、颗粒粒度控制、粉末成型、热处理、表面改性等。
粉末冶金技术不仅可以用于制造金属部件,而且还可以制造非金属部件,如硅酸盐、碳纤维增强塑料等。
制备原料是粉末冶金的第一步,主要是将金属原料(如金属粉末或粒子)制备成粉末状,以便进行成型处理。
一般来说,金属原料可以通过粉碎、混合、蒸发、蒸馏等方式制备粉末。
在制备好粉末之后,要进行粒度分析,以保证粉末分布在合理的粒度范围内,以保证粉末的成型工艺。
粉末成型是粉末冶金技术的主要步骤。
粉末成型可以通过压缩(pressing)、铸造(casting)、挤出(extruding)和热压(sintering)等工艺步骤实现,可以生产出复杂的形状的零件。
压缩成型是将粉末填充到模具中,然后通过压力将粉末装配成所需的形状。
铸造是将粉末流入模具中,并通过冷却硬化成形。
挤出是将粉末放入模具中,并通过压力将粉末挤出形成所需的形状。
热压成形是将粉末装入模具中,然后通过热压将其黏结成所需的形状。
热处理是在粉末成型工艺后的一种必要步骤。
根据要求,可以选择退火、正火、回火和硬化等热处理方式。
这种处理可以改变零件的力学性能,并使零件更加坚固耐用。
最后,表面改性是一种用于增强零件表面性能的步骤。
表面改性可以通过电镀、喷涂、热处理等方式实现,可以增强表面粗糙度,提高表面质量,以及增强零件的耐腐蚀性和耐高温性能。
粉末冶金是一种先进的制造技术,目前已经被广泛应用于许多领域。
它的特点是快速、高效、节能,可以制作出精密、复杂的零件。
在当今制造行业,粉末冶金的成型工艺是一个不可或缺的步骤,可以满足不同行业的生产需求,为各行业制造出更多、更精细的零件。
总之,粉末冶金的成型工艺是一项复杂而重要的技术,其过程从制备原料到表面改性,有着许多复杂的工艺步骤,因此控制其质量和精度非常重要。
粉末冶金与陶瓷材料的成型工艺技术

粉末冶金与陶瓷材料的成型工艺技术粉末冶金是一种重要的材料成型技术,它通过将金属或非金属粉末在高温下压制成形,进而得到各种金属零件和陶瓷材料。
粉末冶金不仅可以制造出形状复杂的零件,还能够获得优良的材料性能,因此被广泛应用于汽车、航空、航天等工业领域。
粉末冶金的成型工艺技术主要分为两个步骤:粉末的制备和成型。
首先是粉末的制备。
粉末冶金所需的粉末通常通过机械研磨、化学反应、气相沉积等方法制备而成。
机械研磨是最常用的方法,它通过将金属块或合金块放入球磨机中与磨料球一起进行高速旋转,使金属块逐渐研磨成粉末。
化学反应法利用化学反应生成粉末,例如气相法将金属气体于高温下反应生成粉末。
制备好的粉末应具备一定的粒度、形状和分布以满足成型的需求。
其次是成型工艺技术。
成型是将粉末压制成所需形状的过程。
常用的成型工艺有冷压成型、等静压成型和注浆成型等。
冷压成型是最简单的成型方法,它通过将粉末放置在模具中,然后在模具上施加压力,使粉末紧密结合成形。
但冷压成型得到的零件强度较低,通常需要进行后续的烧结工艺。
等静压成型是常用的粉末冶金成型方法。
它通过在模具中施加等压力,使粉末均匀密实地填充模具,然后通过高温烧结使粉末颗粒结合成致密的金属材料。
等静压成型可以获得高密度、高强度的零件,适用于制造各种金属零件。
注浆成型是粉末冶金的一种新型成型工艺。
它通过在模具中注入粉末与流体混合物,然后通过高压使混合物注入模具的空隙中,最后再进行烧结。
注浆成型可以制造出形状复杂的零件,并且具有较高的密度和强度。
总之,粉末冶金是一种重要的材料成型技术,它通过粉末的制备和成型工艺来制造各种金属零件和陶瓷材料。
不同的成型工艺可以得到不同性能的材料,所以在应用中需要根据具体要求来选择合适的成型工艺。
粉末冶金是一种重要的材料成型技术,其广泛应用于汽车、航空、航天等众多领域。
通过将金属或非金属粉末在高温下压制成形,可获得形状复杂且性能优良的材料。
下面将进一步探讨粉末冶金与陶瓷材料的成型工艺技术。
粉末冶金成型技术

粉末冶金成型技术粉末冶金成型技术是一种把制备的金属粉末混合成型的现代金属加工技术。
它有可能把任何金属粉末结合成复杂的物体,如构件和复杂的零件等,它不仅可以为生产有特殊形状的零件提供方便,而且可以减少材料的消耗,节省制造时间和成本。
粉末冶金成型技术分为热压成形和冷压成形两种。
热压成形是指把高温粉末压入模具,然后经过压力和高温处理,最后用特殊工艺把模具内的粉末变成给定形状。
冷压成形是指把低温粉末压入模具,然后经过一系列特殊工艺把粉末结合在一起形成一定形状的产品,最后通过高温固化使其变得坚硬。
粉末冶金成型技术不仅可以生产复杂形状的金属零件,而且可以满足生产小批量或单件零件的需求。
典型的应用包括机械零件、航空零件、航天用零件等。
粉末冶金成型技术具有一定的优势,首先,它可以实现复杂零件的加工,这避免了大多数切削加工工艺所面临的技术难题和加工费用的消耗;其次,它可以更有效地实现性能优良的零件,因为贴合技术可以把比普通切削加工技术更少的原料消耗量转变成更多的形状和功能;第三,它还可以在多种金属材料之间制造合金化的零件,并满足不同应用场合的要求。
此外,粉末冶金成型技术还可以在极低温和极高温环境中使用,并可以产生可靠的重复性和准确性,从而提供极低的废品率。
然而,粉末冶金成型技术也存在一些缺点。
正如上文所述,它依赖于模具和高温条件,且受模具形状限制,模具设计和开发费用也较高;对于密度更大的零件,贴合可能较其他方法的成本更高;因为模具的硬度较大,所以它的滑动性能不太好;另外,粉末冶金技术的产品有一定的粗糙性,很难达到高精度要求。
总之,粉末冶金成型技术是一种重要的金属加工技术,可以大大提高零件加工效率并降低成本。
然而,也有一些缺点需要解决,比如模具的高温及耐磨性、模具制造的费用高等,但只要正确使用粉末冶金技术,就能满足企业的实际需求。
粉末冶金工艺的基本工序(三篇)
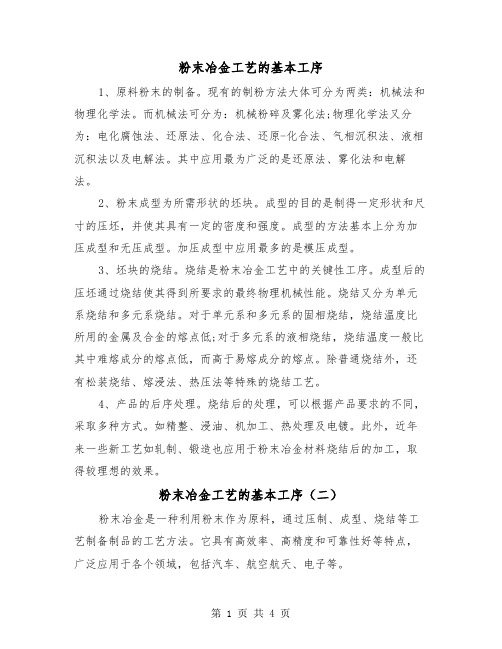
粉末冶金工艺的基本工序1、原料粉末的制备。
现有的制粉方法大体可分为两类:机械法和物理化学法。
而机械法可分为:机械粉碎及雾化法;物理化学法又分为:电化腐蚀法、还原法、化合法、还原-化合法、气相沉积法、液相沉积法以及电解法。
其中应用最为广泛的是还原法、雾化法和电解法。
2、粉末成型为所需形状的坯块。
成型的目的是制得一定形状和尺寸的压坯,并使其具有一定的密度和强度。
成型的方法基本上分为加压成型和无压成型。
加压成型中应用最多的是模压成型。
3、坯块的烧结。
烧结是粉末冶金工艺中的关键性工序。
成型后的压坯通过烧结使其得到所要求的最终物理机械性能。
烧结又分为单元系烧结和多元系烧结。
对于单元系和多元系的固相烧结,烧结温度比所用的金属及合金的熔点低;对于多元系的液相烧结,烧结温度一般比其中难熔成分的熔点低,而高于易熔成分的熔点。
除普通烧结外,还有松装烧结、熔浸法、热压法等特殊的烧结工艺。
4、产品的后序处理。
烧结后的处理,可以根据产品要求的不同,采取多种方式。
如精整、浸油、机加工、热处理及电镀。
此外,近年来一些新工艺如轧制、锻造也应用于粉末冶金材料烧结后的加工,取得较理想的效果。
粉末冶金工艺的基本工序(二)粉末冶金是一种利用粉末作为原料,通过压制、成型、烧结等工艺制备制品的工艺方法。
它具有高效率、高精度和可靠性好等特点,广泛应用于各个领域,包括汽车、航空航天、电子等。
粉末冶金工艺的基本工序包括粉末选料、混合、成型、烧结等。
首先是粉末选料。
粉末冶金工艺中所用的粉末要求颗粒细小、纯度高、形状均匀。
常见的粉末材料包括金属、陶瓷和合金等。
粉末选料的过程中需要考虑到材料的物理化学性质,并进行相应的测试和分析。
接下来是粉末的混合。
混合是将不同种类的粉末按一定比例混合在一起,以获得所需的材料性能。
混合可以通过机械混合、化学方法和物理方法等进行。
在混合过程中,需要控制混合时间和混合速度,以保证混合的均匀性。
然后是成型。
成型是将混合好的粉末放入模具中进行压制或注塑成型。
粉末冶金课件
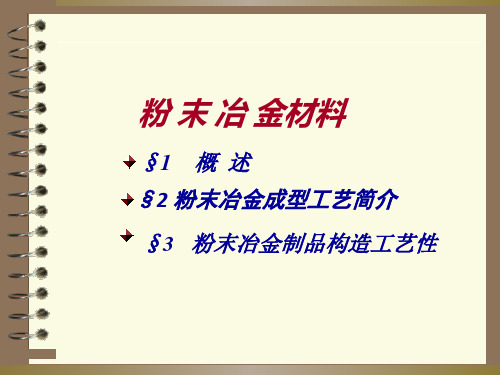
•塑耐性腐变蚀形性能等
•表面状态
•表面张力等
粉末冶金成型
§2 粉末冶金成型工艺简介
3.粉末旳预处理与混合
(1)粉末旳预处理 (2)粉末混合
• 混合 – 两种以上化学组元相混合 (相同化学构成旳粉末旳混合叫做合并。)
• 目旳 – 使性能不同旳组元形成均匀旳混合物, 以利于压制和烧结时状态均匀一致。
为何预处理? a.虽然在同一条件下制造旳同一粉末,其纯度和粒
• 应用 – 制造Fe 、Pb、Sn、Zn、Al、青铜、 黄铜等低熔点金属与合金粉末; – 18-8不锈钢、低合金钢、镍合金等 粉末。
(2) 机械粉碎法
是靠压碎、击碎和磨削等作用,将 块状金属或合金机械地粉碎成粉末。
粉末冶金成型
(2) 机械粉碎法 • 特点:
– 既是一种独立制粉措施, – 又常作为某些制粉措施不可缺乏旳
▪ 据作业旳连续性分 – 间歇式烧结炉—坩埚炉箱式炉 – 高频或中频感应炉
– 大气环境
– 连续式烧结炉
• 产生“过烧”废品
– 烧结温度过高或时间过长,使压坯歪曲和变形,其晶粒也 大;
• 产生“欠烧”废品
– 烧结温度过低或时间过短,产品结合强度等性能达不到要 求;
粉末冶金成型
§2 粉末冶金成型工艺简介
粉末冶金成型
§1 概 述
五、应用
板、带、棒、管、丝等多种型材
成批或 齿轮、链轮、棘轮、轴套类等多种零件 大量生产 重量仅百分之几克旳小制品
近两吨重大型坯料(用热等静压法)
粉末冶金成型
粉末冶金成型
§2 粉末冶金成型工艺简介
粉料制备
压制成型
烧结
粉末冶金成品
烧结后旳处理
§2 粉末冶金成型工艺简介
粉末冶金成型技术
粉末冶金成型技术Ⅰ、粉末冶金成型技术1、粉末冶金成型技术(Powder Metallurgy)是一种较新的金属制造工艺,它通过将金属粉末或粉体团结成模具内所需形状,从而生产出广泛应用的金属零件。
其原理是金属粉末经高压热压成型而形成零件。
2、粉末冶金成型技术能够制造出具有较高精度、更小体积的零件,是传统金属制造技术无法达到的高精度和大精度的紧凑零件。
同时,由于具有良好的耐磨性,它还可以制造可耐高速摩擦的零件。
3、粉末冶金成型技术使用金属粉末来制造零件,因此可以制造出大规模和复杂零件。
它制造出的产品可以达到更高的均匀度、更高的精度和更强的密度,这些特点比其他技术都有优势。
II、工艺流程1、把金属粉末混合成易流动的糊状物:在粉末冶金成型过程中,首先将金属粉末混合成易流动的糊状物,然后将其成型成所需的各类结构。
2、金属流成型:将调制好的金属流放入到模具中,然后将其投射成型,采用精确的高压成型,以形成模具内期望的形状。
3、表面处理:一些金属零件可能需要再进行表面处理,比如镀铬、电镀和热处理,以满足零件性能的需求,增强其耐蚀性、耐磨性等。
4、热处理:热处理是利用复杂的热处理技术,通过改变零件的温度来改变其组织和性能,以获得期望的性能和表面光洁度。
III、优点1、体积小:由于采用精密模具来进行流体压力成型,可以制造出具有较小体积和精确尺寸的部件;2、准确精度:粉末冶金成型可以根据模具进行长宽比、曲率与折弯处理,以达到较高的精度,组装时也相对容易;3、节能降耗:比传统金属加工手段更加节省能源耗费,而且粉末冶金可以减少冶炼及清理成本,从而降低成本;4、结构复杂:粉末冶金制造的零件可以根据设计形状进行复杂的结构设计,可在一个工件上制造气隙空间及护套,从而更加省时。
IV、缺点1、成本高:粉末冶金技术的设备耗费较高,使得生产成本比其他工艺高很多;2、尺寸大小限制:模具的设计尺寸受生产设备的尺寸限制,影响着大小尺寸和深度尺寸的生产;3、生产周期长:由于加工方法比其他工艺复杂,因此所需的生产周期也变得更长;4、表面光洁度差:因为运用压力成型,而非切削加工,因此物件的表面光洁度不是非常理想。
粉末冶金的工艺流程-粉末成形
简介 粉末冶金生产中的基本工序之一,目的是将松散的粉末制成具有预定几何形
状、尺寸、密度和强度的半成品或成品。模压(钢模)成形是粉末冶金生产中采 用最广的成形方法。18世纪下半叶和19世纪上半叶,西班牙、俄国和英国为制造 铂制品,都曾采用了相似的粉末冶金工艺。当时俄国索博列夫斯基 (П.Г.Соболевсκий)使用 的是 钢模 和螺 旋压 机。 英 国的 沃拉 斯顿 (W.H.Wol laston )使 用 压 力 更 大 的 拉 杆 式 压 机 和 纯 度 更 高 的 铂 粉 ,制 得 了 几 乎 没 有 残余孔隙的致密铂材。后来,模压成形方法逐渐完善,并用来制造各种形状的铜 基 含 油 轴 承 等 产 品 。 20世 纪 30年 代 以 来 , 在 粉 末 冶 金 零 件 的 工 业 化 生 产 过 程 中 , 压 机 设 备 、模 具 设 计 等 方 面 不 断 改 进 , 模 压 成 形 方 法 得 到 了 更 大 的 发 展 ,机 械 化 和 自动化已达到较高的程度。为了扩大制品的尺寸和形状范围,特别是为了提高制 品密度和改善密度的均匀性相继出现和发展了多种成形方法。早期出现的有粉末 轧制、冷等静压制、挤压、热压等;50年代以来又出现了热等静压制、热挤压、 热锻等热成形方法。这些方法推动了全致密、高性能粉末金属材料的生产。 主要功能
料 为 金 属( 低 碳 钢 、不 锈 钢 、钛 ),还 可 用 玻 璃 和 陶 瓷 。由 于 温 度 和 等 静 压 力 的 同 时作用,可使许多种难以成形的材料达到或接近理论密度,并且晶粒细小,结构 均匀,各向同性和具有优异的性能。热等静压法最适宜于生产硬质合金、粉末高 温合金、粉末高速钢和金属铍等材料和制品;也可对熔铸制品进行二次处理,消 除气孔和微裂纹;还可用来制造不同材质紧密粘接的多层或复合材料与制品。 粉末锻造
粉末冶金的工艺流程
粉末冶金的工艺流程
粉末冶金工艺流程是指将一定比例的活性金属(称为“基料金属”)和一定比例的被
加工金属(称为“变性金属”)经过粉碎、混合、去除杂质、压制及烧结等操作,而制得
一种具有均匀分布和比较细小的金属粉末而得名。
粉末冶金工艺以金属粉末重熔致密法为
技术基础,以粉末精细的团聚结构和晶粒细小的晶体取向分布为独特特征,用以制备尺寸大、高强度、脆性高、密度高,表面光滑均匀的金属零件,例如复杂正方体的盒体零件和
空心的环形零件等,在航空航天、装备及汽车等领域中具有重要的应用。
粉末冶金工艺包括以下几个主要环节:
(1) 金属粉末生产:以基料金属与变性金属为原料,对这两种金属粉末进行研磨、混
合和精制,以达到要求的比例,之后去除杂质,制得一种具有均匀分布和比较细小的粉末。
(2) 成形制造:将具有均匀分布的金属粉末进行压制,得到表面较为光滑、图案细节
较精细的成形产品。
(3) 烧结工艺:将表面光滑的粉末成型产品放入真空热器中处理,以达到聚结和饱和
致密状态,从而得到表面光滑均匀、尺寸稳定、高强度、脆性高、密度高的金属零件。
(4) 加工表面:将烧结好的金属零件经过去毛刺、抛光、热处理等加工,达到表面的
理想效果。
以上是粉末冶金工艺的基本流程,虽然粉末冶金工艺技术具有高效率,但仍需要注意
一些特殊情况,如可能会出现的粉尘污染,金属粉末的渗漏,工作场所的温度和湿度,等等。
因此,需要根据实际情况做出恰当的符合规范的管理要求,以确保安全生产。
粉末冶金成型的工艺过程
粉末冶金成型的工艺过程粉末冶金成型是一种利用粉末金属和其他复合材料制作各种形状和大小的零件的工艺,是一种广泛应用于航空航天、船舶、汽车、石油、机械制造和精密仪器等领域的一种重要工艺。
粉末冶金成型的工艺过程主要包括粉末成形、热处理和表面处理三个步骤。
首先,粉末成形。
将粉末金属或复合材料放入型腔内,然后用轧制机将其压实,形成特定的零件形状。
一般分两种方法:一种是热压成型,将粉末金属或复合材料装入型腔,然后将其加热,并用压力将其压实,使其形成所需的零件形状;另一种是压力成形,将粉末金属或复合材料装入型腔,然后用压力将其压实,使其形成所需的零件形状。
其次,热处理。
热处理对粉末冶金成型产品具有重要意义,其目的是改善材料的力学性能、改变材料的组织结构、调节材料的组织参数、提高材料的硬度和韧性等。
热处理可分为正火处理和回火处理两种,根据所需要的效果,可选用不同的工艺方式,如火焰热处理、氩弧焊热处理、电火花热处理等。
最后,表面处理。
表面处理的目的是使粉末冶金成型后的零件具有良好的外观和耐磨性,并且提高其耐腐蚀性。
表面处理的方法多种多样,如电镀、阳极氧化、氧化处理、涂装、抛光等。
由于粉末冶金成型产品的表面粗糙度较高,一般需要进行抛光处理,以改善表面光洁度和表面粗糙度。
粉末冶金成型的过程比较复杂,需要经过粉末成形、热处理和表面处理这三个步骤,才能得到满足要求的零件。
粉末冶金成型工艺具有加工复杂形状零件的优势,具有节约材料、提高加工精度、改善性能和缩短交货期等优点,已成为航空航天、船舶、汽车、石油、机械制造和精密仪器等领域的重要工艺。
Secondly, heat treatment. Heat treatment is of great significance to powder metallurgy forming products, which aims to improve the mechanical properties of materials, change the structure of materials, adjust the organization parameters of materials, increase the hardness and toughness of materials, etc. Heat treatment can be divided into two types: normalizing and annealing, different process can be selected according to the required effect, such as flame heat treatment, argon arc welding heat treatment, electric spark heat treatment, etc.。
- 1、下载文档前请自行甄别文档内容的完整性,平台不提供额外的编辑、内容补充、找答案等附加服务。
- 2、"仅部分预览"的文档,不可在线预览部分如存在完整性等问题,可反馈申请退款(可完整预览的文档不适用该条件!)。
- 3、如文档侵犯您的权益,请联系客服反馈,我们会尽快为您处理(人工客服工作时间:9:00-18:30)。
粉末冶金成型工艺
粉末冶金成型工艺是一种通过将金属或非金属粉末在一定条件下进行成型和烧结制备材料的工艺方法。
具体而言,该工艺涉及将粉末与添加剂混合、压制成型、烧结等多个步骤。
粉末冶金成型工艺被广泛应用于制造各种金属、合金、陶瓷等材料,具有高效率、低成本、良好的材料性能和设计灵活性等优点。
粉末冶金成型工艺的第一步是粉末的制备。
在制备过程中,需要选择合适的原料,并使用相应的方法将其粉碎成细小的颗粒。
这些粉末的粒径通常在1-100微米之间,可以根据具体需求进行调控。
此外,为了提高材料的性能,还可以通过添加剂的投入来调整和改善材料的特性。
在粉末的制备完成后,下一步是将粉末与添加剂混合。
混合的目的是使粉末和添加剂均匀分散,保证材料的均一性。
常用的混合方法有机械混合、湿法混合等。
机械混合通常通过旋转式球磨机、振动式球磨机等设备进行,湿法混合则是将粉末和添加剂悬浮在液体介质中进行混合。
混合完成后,接下来是将混合后的粉末进行成型。
成型的方法主要有压制成型和注射成型两种。
在压制成型中,将混合后的粉末放置在模具中,并施加压力使其成型。
而注射成型则是将粉末与添加剂的混合物注射到模具中,经过固化后得到所需形状的制品。
不同的成型方法适用于不同类型的材料和形状需求。
成型完成后,还需要进行烧结过程。
烧结是指在高温下,将成型后的粉末进行加热处理,使其颗粒之间发生结合。
在烧结过程中,粉末的颗粒会相互扩散,形成致密的结构。
烧结温度和时间的选择对于材料的性能具有重要影响。
粉末冶金成型工艺的最后一步是进行后续处理。
这包括退火、热处理、表面处理等过程。
退火是为了消除成型过程中产生的残余应力,提高材料的塑性和韧性。
热处理可以改变材料的组织结构和性能,提高其硬度、强度等。
表面处理则是为了改善材料的表面性能,如防腐蚀、增加耐磨性等。
粉末冶金成型工艺是一种重要的材料制备方法,具有广泛的应用前景。
通过粉末冶金成型工艺,可以制备出具有良好性能、复杂形状和高精度的材料,满足不同行业的需求。
随着技术的进步和创新,粉末冶金成型工艺将进一步发展,为材料制备和工程应用带来更多的可能性。