铸造行业应用
铸造技术的发展现状与前景探究

铸造技术的发展现状与前景探究铸造技术是一种古老的制造工艺,经过数千年的发展,它已经成为现代工业中不可或缺的一部分。
随着科技的进步和工业化的发展,铸造技术也在不断地创新和完善。
本文将探讨铸造技术的发展现状和前景,并分析其在未来的应用前景。
一、铸造技术的发展现状1. 传统铸造技术的完善传统的铸造技术主要包括砂型铸造、金属型铸造和压力铸造等。
这些传统的铸造方法已经经过数百年的发展与完善,在工艺技术、设备设施和质量控制方面都有了很大的提升。
采用计算机辅助设计和模拟分析技术,可以使产品的质量和生产效率得到显著提高;而高强度、高耐磨的新型铸造材料的应用,也使得铸件的耐用性和性能得到了大幅提升。
2. 数字化铸造技术的应用随着信息技术的快速发展,数字化铸造技术也逐渐成为铸造行业的发展趋势。
数字化铸造技术主要包括数字化设计、数字化仿真和数字化制造等方面。
采用这些技术可以大大减少试制周期,降低开发成本,提高产品的质量和性能。
特别是在航空航天、汽车制造等领域,数字化铸造技术的应用已经成为不可或缺的一部分,为整个行业的发展带来了新的机遇和挑战。
3. 先进铸造材料的研发与应用除了铸造工艺的创新外,先进铸造材料的研发与应用也是铸造技术发展的重要方面。
随着新材料的不断涌现,具有高强度、高温性能和良好耐磨性的铸造材料得到了广泛的应用。
这些材料的使用可以大幅提高铸件的使用寿命和工作性能,促进行业的发展和升级。
4. 自动化、智能化生产技术随着机器人技术和人工智能技术的进步,铸造技术的生产过程也在向自动化、智能化方向发展。
自动化生产线的应用可以提高生产效率,减少人力成本,提高产品质量和一致性。
而智能化技术的应用则可以实现生产过程的实时监控和调整,确保产品的质量和稳定性。
这些技术的应用将会进一步推动铸造技术的发展,并有望成为未来铸造行业的主要发展方向。
二、铸造技术的发展前景1. 高新技术的应用未来铸造技术的发展方向将主要集中在高新技术的应用。
熔模铸造的特点和应用范围

熔模铸造的特点和应用范围1. 熔模铸造简介好嘞,今天咱们来聊聊熔模铸造。
这玩意儿可不是普通的铸造工艺,而是一种高超的技术。
想象一下,就像做蛋糕,先得有模具,熔模铸造就是这个模具的艺术家。
它的基本原理简单粗暴,先把蜡模做出来,然后浇上熔融金属,等金属冷却固化,最后把蜡融掉,嘿,神奇的金属部件就出炉了!听起来是不是挺酷的?2. 熔模铸造的特点2.1 高精度首先,熔模铸造最大的特点就是高精度。
你可以把它想象成在拼拼图,拼得越仔细,最后的图案就越完美。
这种铸造方式能达到非常细致的形状和表面光滑度,简直是“工艺中的工艺”!比如说,汽车零件、航空器组件,都是对精度有着近乎苛刻要求的地方,熔模铸造轻松驾驭。
2.2 复杂形状再来说说它的另一个牛逼之处,那就是能做复杂形状的部件。
比方说,一些形状奇特的艺术品或者高科技的仪器,传统铸造可能会发愁,但熔模铸造可不怕。
就像会魔法一样,蜡模能随心所欲地造型,成品完全符合设计师的想法,简直是一种“想象力与技术结合”的完美体现!3. 熔模铸造的应用范围3.1 航空航天接下来,我们聊聊熔模铸造的应用范围。
这东西用得可广了,首先在航空航天领域那是无人能敌。
飞机、火箭的发动机部件,很多都得靠熔模铸造来实现,没办法,安全第一呀!而且,随着科技的发展,这些部件还得轻、强、耐高温,熔模铸造就能满足这些要求,简直是个超级英雄!3.2 医疗器械再说医疗器械。
想想看,手术刀、植入物,这些东西对精度和材料的要求都非常高,稍微差点可就“麻烦大了”。
熔模铸造在这方面也是大展拳脚,很多高精度的医疗器械部件,都是通过这项技术来制作的。
可以说,熔模铸造不仅仅是个技术活,更是关乎人命的大事,想想都觉得责任重大呢。
4. 小结总的来说,熔模铸造是个神奇的存在,凭借它的高精度和能制造复杂形状的特点,在各个行业里大放异彩。
无论是航天还是医疗,它都能发挥不可替代的作用。
就像一位默默无闻的英雄,在背后默默奉献,却又总能让人心生敬意。
铸造技术的发展现状与前景探究

铸造技术的发展现状与前景探究铸造技术是一种广泛应用的金属加工工艺,其发展对于工业生产具有重要意义。
随着现代制造业的不断发展和需求的不断增加,铸造技术也得到了迅速的发展并取得了较大的成就。
本文将对铸造技术的发展现状进行探究,并展望其未来的发展前景。
一、铸造技术的发展现状1. 传统铸造技术传统铸造技术主要包括砂型铸造、金属型铸造、压力铸造等。
这些技术在工业生产中应用广泛,具有成本低、工艺简单等优点。
但是传统铸造技术也存在一些问题,如生产效率低、能源消耗大、材料利用率低等,不能完全满足现代工业对高质量、高效率、节能环保的需求。
随着科技的不断进步,先进铸造技术不断涌现,如精密铸造技术、数字化铸造技术、快速凝固铸造技术等。
这些新技术在提高铸造件的精度、降低能耗、改善材料利用率等方面具有明显优势。
先进铸造技术也在发展中遇到了一些挑战,例如技术成熟度不高、设备投资大等问题,需要不断进行技术改进和创新。
随着人工智能、大数据、云计算等技术的不断发展,智能化铸造技术也逐渐走进人们的视野。
智能化铸造技术通过智能装备、智能控制系统等手段,实现铸造过程的自动化、智能化,极大地提高了生产效率和产品质量,降低了生产成本。
智能化铸造技术的发展将有效推动铸造行业向数字化、智能化方向转变。
数字化铸造技术是近年来的热门发展方向,它通过数字化建模、仿真分析等手段,对铸造过程进行全面监控和优化。
数字化铸造技术的发展将引领铸造行业向数字化制造方向转变,实现生产智能化、灵活化、高效化。
2. 绿色铸造技术的推广随着环保意识的增强,绿色铸造技术也受到了越来越多的关注。
各种新型的绿色铸造材料和清洁生产技术不断涌现,有力地推动了铸造行业向绿色化转型。
绿色铸造技术的发展将有效解决传统铸造技术存在的环境污染和资源浪费等问题。
3. 智能化铸造技术的应用铸造技术发展现状良好,同时面临的挑战和机遇也在不断增加。
只有不断进行技术创新和提高,才能更好地满足现代制造业对高质量、高效率、节能环保的需求,铸造技术必将迎来更加美好的未来。
铸造生产工艺的应用
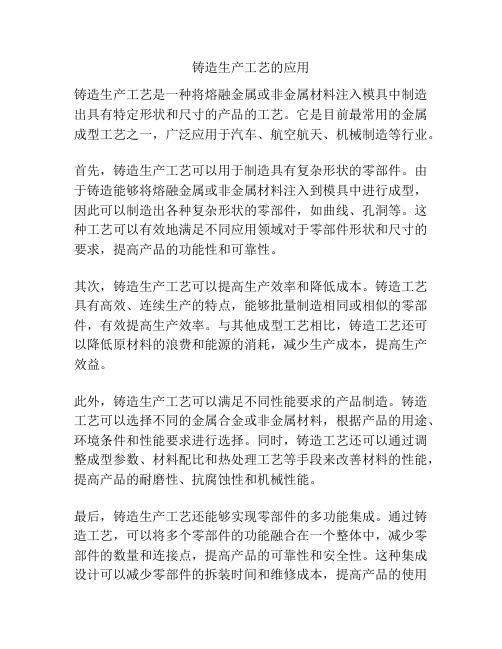
铸造生产工艺的应用
铸造生产工艺是一种将熔融金属或非金属材料注入模具中制造出具有特定形状和尺寸的产品的工艺。
它是目前最常用的金属成型工艺之一,广泛应用于汽车、航空航天、机械制造等行业。
首先,铸造生产工艺可以用于制造具有复杂形状的零部件。
由于铸造能够将熔融金属或非金属材料注入到模具中进行成型,因此可以制造出各种复杂形状的零部件,如曲线、孔洞等。
这种工艺可以有效地满足不同应用领域对于零部件形状和尺寸的要求,提高产品的功能性和可靠性。
其次,铸造生产工艺可以提高生产效率和降低成本。
铸造工艺具有高效、连续生产的特点,能够批量制造相同或相似的零部件,有效提高生产效率。
与其他成型工艺相比,铸造工艺还可以降低原材料的浪费和能源的消耗,减少生产成本,提高生产效益。
此外,铸造生产工艺可以满足不同性能要求的产品制造。
铸造工艺可以选择不同的金属合金或非金属材料,根据产品的用途、环境条件和性能要求进行选择。
同时,铸造工艺还可以通过调整成型参数、材料配比和热处理工艺等手段来改善材料的性能,提高产品的耐磨性、抗腐蚀性和机械性能。
最后,铸造生产工艺还能够实现零部件的多功能集成。
通过铸造工艺,可以将多个零部件的功能融合在一个整体中,减少零部件的数量和连接点,提高产品的可靠性和安全性。
这种集成设计可以减少零部件的拆装时间和维修成本,提高产品的使用
效率和经济效益。
综上所述,铸造生产工艺具有广泛的应用前景。
在现代工业生产中,铸造工艺已经成为制造各类零部件和装备的主要工艺之一。
随着科技的发展和工艺的改进,铸造工艺将进一步提高产品的质量和性能,满足不断变化的市场需求。
铸造技术创新及其应用实践总结
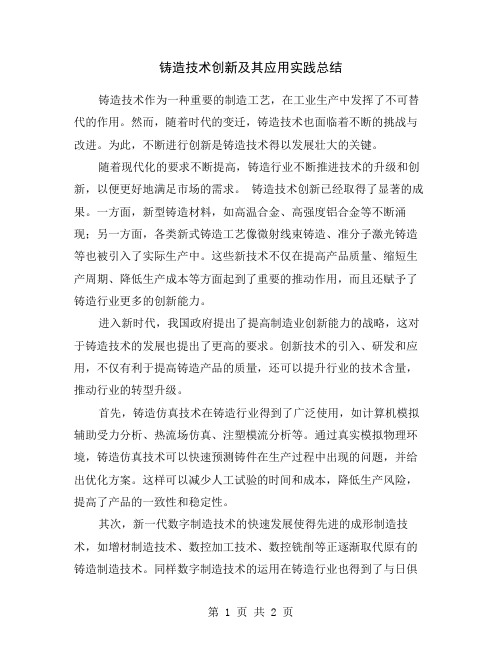
铸造技术创新及其应用实践总结铸造技术作为一种重要的制造工艺,在工业生产中发挥了不可替代的作用。
然而,随着时代的变迁,铸造技术也面临着不断的挑战与改进。
为此,不断进行创新是铸造技术得以发展壮大的关键。
随着现代化的要求不断提高,铸造行业不断推进技术的升级和创新,以便更好地满足市场的需求。
铸造技术创新已经取得了显著的成果。
一方面,新型铸造材料,如高温合金、高强度铝合金等不断涌现;另一方面,各类新式铸造工艺像微射线束铸造、准分子激光铸造等也被引入了实际生产中。
这些新技术不仅在提高产品质量、缩短生产周期、降低生产成本等方面起到了重要的推动作用,而且还赋予了铸造行业更多的创新能力。
进入新时代,我国政府提出了提高制造业创新能力的战略,这对于铸造技术的发展也提出了更高的要求。
创新技术的引入、研发和应用,不仅有利于提高铸造产品的质量,还可以提升行业的技术含量,推动行业的转型升级。
首先,铸造仿真技术在铸造行业得到了广泛使用,如计算机模拟辅助受力分析、热流场仿真、注塑模流分析等。
通过真实模拟物理环境,铸造仿真技术可以快速预测铸件在生产过程中出现的问题,并给出优化方案。
这样可以减少人工试验的时间和成本,降低生产风险,提高了产品的一致性和稳定性。
其次,新一代数字制造技术的快速发展使得先进的成形制造技术,如增材制造技术、数控加工技术、数控铣削等正逐渐取代原有的铸造制造技术。
同样数字制造技术的运用在铸造行业也得到了与日俱增的应用,打造了智能、高精度、自动化的铸造生产线,提高了生产效率和生产质量。
此外,新型的表面导向制造技术、高能密度表面制备技术、表面纳米处理等新技术也正带动着铸造生产的迈向高效化和高附加值的方向。
表面处理技术在提高产品表面性能、增大材料表面能、加速反应速率等方面具有广泛的应用。
在铸造加工中,表面处理技术特别适用于提高表面粗糙度、硬度和耐磨性,促进产品的耐用度。
总的来说,铸造行业在技术创新与升级过程中,应重视提高创新能力,加速科技创新的步伐,走向高品质产品制造。
压铸技术在铸造行业的应用
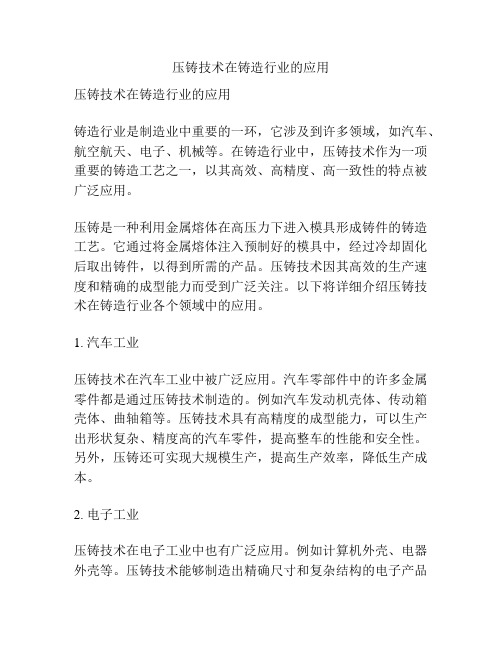
压铸技术在铸造行业的应用压铸技术在铸造行业的应用铸造行业是制造业中重要的一环,它涉及到许多领域,如汽车、航空航天、电子、机械等。
在铸造行业中,压铸技术作为一项重要的铸造工艺之一,以其高效、高精度、高一致性的特点被广泛应用。
压铸是一种利用金属熔体在高压力下进入模具形成铸件的铸造工艺。
它通过将金属熔体注入预制好的模具中,经过冷却固化后取出铸件,以得到所需的产品。
压铸技术因其高效的生产速度和精确的成型能力而受到广泛关注。
以下将详细介绍压铸技术在铸造行业各个领域中的应用。
1. 汽车工业压铸技术在汽车工业中被广泛应用。
汽车零部件中的许多金属零件都是通过压铸技术制造的。
例如汽车发动机壳体、传动箱壳体、曲轴箱等。
压铸技术具有高精度的成型能力,可以生产出形状复杂、精度高的汽车零件,提高整车的性能和安全性。
另外,压铸还可实现大规模生产,提高生产效率,降低生产成本。
2. 电子工业压铸技术在电子工业中也有广泛应用。
例如计算机外壳、电器外壳等。
压铸技术能够制造出精确尺寸和复杂结构的电子产品外壳,保证电子设备的性能和稳定性。
此外,压铸还可以为电子产品提供良好的屏蔽性能,保护内部电路不受外界干扰。
3. 航空航天工业航空航天工业对零件的质量要求非常高,因此压铸技术在该行业中得到了广泛应用。
例如航空发动机零件、飞机座椅支架等。
压铸技术能够制造出高强度、高耐热、高耐腐蚀的零件,满足航空航天工业对零件性能的要求。
此外,压铸还可以实现零件的一次成型,减少加工工序,提高生产效率。
4. 机械工业压铸技术在机械工业中也有广泛应用。
例如机床床身、工具箱等。
压铸技术能够制造出高强度、高刚性的机械零件,提高机械设备的工作性能和寿命。
此外,压铸还可以生产复杂形状的零件,减少零件的拼接和焊接,提高整体结构的稳定性和可靠性。
5. 精密仪器工业压铸技术在精密仪器工业中也有广泛应用。
例如光学仪器外壳、高精度测量仪器外壳等。
压铸技术能够制造出精确尺寸和复杂结构的仪器外壳,保证仪器的精确度和稳定性。
铸造成形的应用

铸造成形的应用
铸造成形的应用
铸造成形是一种非常古老的金属加工技术,它可以用于制造各类金属零件,例如:金属框架或铁路架,机器零件以及消费品,如家用电器,游乐设施等。
铸造成形有多种,从古老的“月亮”铸造到现代的芯腔铸造,它们都能够满足客户的需求。
铸造是一种通用的金属加工技术,它可以用于制作各类金属产品,如:汽车配件,机械零件,家用电器,游乐设施,空调,建筑部件等。
铸造的优势在于:可以以低成本生产出坚硬耐用的零件,具有较强的负载能力,对塑料或塑料混合物的加工性也比较好,而且还可以快速生产出大批量的零件。
另一方面,铸造成形还可以用于制作大型金属零件,如:桥梁、铁路架及油罐等。
这些大型零件通常需要经过多步复杂的铸造成形工艺,才能最终完成。
铸造成形不仅可以制作大型零件,还可以用于制作较小型零件,甚至可以制作极小的微型零件,如:微型活塞等。
总之,铸造成形是一种重要的金属加工工艺,它可以制作出各类金属零件,在许多行业中都有着广泛的应用。
- 1 -。
五种特种铸造的原理及应用
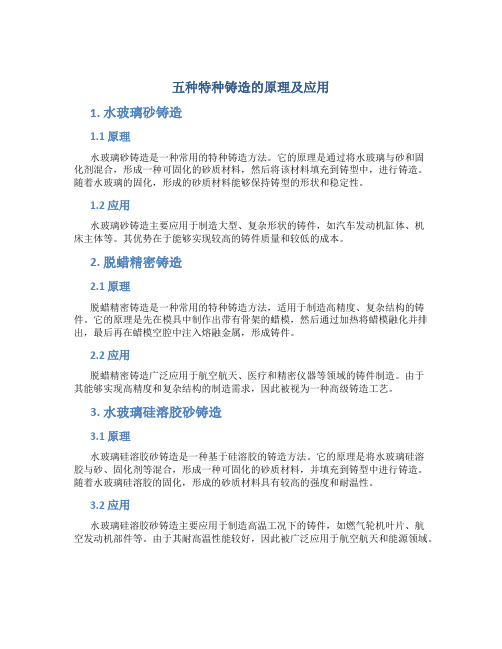
五种特种铸造的原理及应用1. 水玻璃砂铸造1.1 原理水玻璃砂铸造是一种常用的特种铸造方法。
它的原理是通过将水玻璃与砂和固化剂混合,形成一种可固化的砂质材料,然后将该材料填充到铸型中,进行铸造。
随着水玻璃的固化,形成的砂质材料能够保持铸型的形状和稳定性。
1.2 应用水玻璃砂铸造主要应用于制造大型、复杂形状的铸件,如汽车发动机缸体、机床主体等。
其优势在于能够实现较高的铸件质量和较低的成本。
2. 脱蜡精密铸造2.1 原理脱蜡精密铸造是一种常用的特种铸造方法,适用于制造高精度、复杂结构的铸件。
它的原理是先在模具中制作出带有骨架的蜡模,然后通过加热将蜡模融化并排出,最后再在蜡模空腔中注入熔融金属,形成铸件。
2.2 应用脱蜡精密铸造广泛应用于航空航天、医疗和精密仪器等领域的铸件制造。
由于其能够实现高精度和复杂结构的制造需求,因此被视为一种高级铸造工艺。
3. 水玻璃硅溶胶砂铸造3.1 原理水玻璃硅溶胶砂铸造是一种基于硅溶胶的铸造方法。
它的原理是将水玻璃硅溶胶与砂、固化剂等混合,形成一种可固化的砂质材料,并填充到铸型中进行铸造。
随着水玻璃硅溶胶的固化,形成的砂质材料具有较高的强度和耐温性。
3.2 应用水玻璃硅溶胶砂铸造主要应用于制造高温工况下的铸件,如燃气轮机叶片、航空发动机部件等。
由于其耐高温性能较好,因此被广泛应用于航空航天和能源领域。
4. 压力铸造4.1 原理压力铸造是一种通过将熔融金属注入金属型腔,并施加一定的压力,在一定时间内冷却和凝固的铸造方法。
它的原理是通过压力将熔融金属填充到铸型中,然后通过迅速冷却和凝固来形成铸件。
4.2 应用压力铸造广泛应用于制造轻质合金件,如汽车发动机缸盖、铝合金车轮等。
其优势在于能够实现高产量、高精度和较低的材料浪费。
5. 渗铜铸造5.1 原理渗铜铸造是一种特殊的铸造方法,它的原理是将铜水通过压力注入到铸型中的铜粉或其他带孔材料中,然后通过温度升高和铜的熔化使其浸润和填充到铸型中。
- 1、下载文档前请自行甄别文档内容的完整性,平台不提供额外的编辑、内容补充、找答案等附加服务。
- 2、"仅部分预览"的文档,不可在线预览部分如存在完整性等问题,可反馈申请退款(可完整预览的文档不适用该条件!)。
- 3、如文档侵犯您的权益,请联系客服反馈,我们会尽快为您处理(人工客服工作时间:9:00-18:30)。
喷丸机
喷丸、清理室风量计算方法
3.4 喷丸室室体内气流流向应使产生的粉尘能迅速有效地排除。排出的含尘空气经净化后,应符合GBJ4-73的规
定。
从门洞、观察窗以及缝隙逸散的粉尘,应保证作业场所的粉尘浓度不大于TJ 36-79的规定。
3.5 喷丸室室体的排风量应符合下列要求,并应与保证门洞及缝隙处带尘气流不外逸所求得风量互相校核,取
<8
│
0.30~0.25
──────────────────┼──────────────────
8~20
│
0.25~0.20
──────────────────┼──────────────────
21~100
│
0.20~0.15
──────────────────┼──────────────────
式中:μf──从缝隙处外逸的速度,m/s;
q0──喷嘴耗气量,m^3/s;
x──喷嘴至缝隙的距离,m;
A0──喷嘴截面积,m2。
3.2 抛丸室室体排风量,可参照附 录A按室体容积、抛丸器功率、不 同抛丸室型式和不同清理对象计算。
连续抛丸室按上述方法求得的 排风量,应与保证门洞及缝隙处风 速不小于5m/s所求得的风量互相校 核,取其大值。
注:① 喷嘴直径系指磨损后允许使用的最大直径。 ② 排风量为单个喷嘴的排风量。
抛丸室风量计算方法
抛丸室排风量计算 (参考件)
A.1 抛丸室室体排风量可按室体容积和抛丸器功率按下列计算:
L=a1·a2·(VN)^(1/2)
式中:L──抛丸室室体排风量,m^3/min;
a1──不同型式抛丸室系数;
国产 Nederman
唐纳森
嘉禾瑞丰
FS过滤器
FD过滤器
DLMC布袋式过滤器
国产布袋式
FMC200
覆膜滤芯 不覆膜滤芯
覆膜滤芯 DF
不覆膜滤芯
覆膜滤芯 DFO
不覆膜滤芯
覆膜滤芯 DFT
不覆膜滤芯
覆√ √ √ √ √
√
√
√
浇注 √ √ √ √ √
√
√
√
冷却 √ √ √ √ √
>100
│
0.15~0.12
━━━━━━━━━━━━━━━━━━┷━━━━━━━━━━━━━━━━━━
3.5.2 作业人员在喷丸室内操作时,喷丸室的排风量宜以喷嘴的直径和数量确定, 见表2。
表2 ━━━━━━━┯━━━┯━━━┯━━━┯━━━┯━━━┯━━━┯━━━━━ 喷嘴直径,mm │ 7 │ 8 │ 9 │ 10 │ 12 │ 14 │16 ───────┼───┼───┼───┼───┼───┼───┼───── 排风量,m^3/h│ 5000│ 5500 │ 6000 │ 7000 │10000 │13500 │18000 ━━━━━━━┷━━━┷━━━┷━━━┷━━━┷━━━┷━━━┷━━━━━
Nederman FD 扁袋式除尘器
FD7 22/6.00/840(840) FD是过滤器的类型-代表压缩空气反吹 7是滤袋的层数; 22代表滤袋长度2.2m; 6.0代表6个模块(每个模块横向为20
片) 840(840)代表最大安装滤袋个数
和实际安装滤袋个数; 每个滤袋的过滤面积约为:1.5m2; 反吹方式为在线压缩空气脉冲反吹;
不高时选用; A型滤筒每个过滤器面积为6.6m2;L型滤筒每个过滤面积为:4m2;
FS除尘器结构
FS除尘器结构
FS除尘器结构
FS除尘器结构
FD除尘器结构
FD除尘器结构
唐纳森DLMC扁袋脉冲式除尘器
DLMC 2/8/15; DLMC 过滤器类型; 2列数(每列10个滤袋); 8滤袋层数, 2*8为标准单元的个数,16个标准单元; 15 每个标准单元的的过滤面积为15m2; 此除尘器的过滤面积为16*15=240m2 滤料需要根据过滤的材质选择;
去氧化皮
│
1.0
───────────────────┼─────────────────
去粘砂
│
1.2
━━━━━━━━━━━━━━━━━━━┷━━━━━━━━━━━━━━━━━
附录B
压缩空气射流所及缝隙处带尘气流外逸速度计算 (参考件)
压缩空气射流从缝隙处外逸的速度μf按下式计算:
μf=2q0/(x·(A0)^(1/2))
抛丸与喷砂都能对工件起到清整去污的目的,目的为下序作准备,即要 保证下道工序的粗糙度要求,也有的为了要表面的一致性,喷丸对工件 有强化作用,喷砂就不明显了。一般喷丸为小钢球,喷砂为石英砂。按 不同要求,分目数。 精密铸造几乎天天都在用喷砂、抛丸
抛丸机的一些构造
抛头
丸料
在抛丸机领域DISA是行业的领军企业, Nederman的布袋式除尘设备就是从 DISA分离出来的!
Nederman DF扁筒式除尘器
DF 40 、80、120、 160滤筒式除尘器; DF为扁筒式除尘器的型号; 40为一个模块数量;每增加一个模块,加一个40
,单组滤筒最大可以加到4个模块,也就是160; 每个模块6片滤芯,每个滤芯过滤面积为72m2,
Nederman FS 扁袋式除尘器
台车式、转台式
│
2.5~3.5
────────────────────┼────────────────
通过式
│
3.5~5.0
────────────────────┼────────────────
吊挂式
│
3.0~4.0
────────────────────┼────────────────
滚筒式、履带式
除尘器保温和加热装置 ; 橡胶粉的粉尘---加装灭火系统及观察窗; 大风量粉尘、及火花---加旋风除尘器; 少量粉尘----用滤筒式除尘器可以室内排放;
系统工作原理图
过滤器过滤风速选择
对于FD、FS、DLMV、或者其他国产布袋式过滤器我们滤芯的过滤 风速一般选择1.5m/s左右的过滤风速;可以根据粉尘量酌情调整;
其大值。
3.5.1 作业人员在喷丸室外操作时,喷丸室的排风量宜按室体容积断面(与气流垂直)
0.12--
0.30m/s计算,见表1。
表1
━━━━━━━━━━━━━━━━━━┯━━━━━━━━━━━━━━━━━━
喷丸室室体容积
│
断面风速
m^3
│
m/s
──────────────────┼──────────────────
炉子上面需要有较好的炉罩才能达到比较好的收尘效果,英达和ABP公司都 有能力加工自己的炉罩,并且能达到不错的收烟效果;Nederman公司能 独立加工炉罩,并且能和很多电炉厂家配合,但是炉罩价格偏高,所以一般 炉罩都有电炉厂家自带;改造项目可能需要配备炉罩;
冷却线
粉尘量适中; 含水汽; 温度较低;
门打开后,滤芯更换比较简单,拉动手柄即可;
能过滤5g/m3以下浓度的粉尘,
每个门2排,即2个A或 者2个L
FMC200工作原理
注意2处的进风挡板设计
在线灰方式:压差清灰、定时清 灰
离线轻灰方式:多种设置
FMC各种过滤器的名称
FMC的滤芯种类
CA100:聚酯制成的标准滤芯普通过滤器,可以过滤细尘和粗尘物质,当过滤效果要求
浇注和扒渣工位
温度微高; 粉尘成份问题; 实际工作相对频率低; 可能含水汽;
喷砂、喷丸、抛丸除尘
粉尘量大; 含橡胶粉; 温度较低; 注意粉尘类型; 注意丸料、沙料种类;
抛丸、喷丸、喷砂的区别;
1,丸与砂 丸一般是球形一类没有棱角的颗粒.如钢丝切丸等; 砂是指有棱角的砂粒,如棕刚玉、白刚玉、河砂等。 2,喷与抛 喷是以压缩空气作为动力将砂料或丸料喷到材料表面,达到清除和一定 的粗糙度。 抛是将丸料以高速旋转时产生的离心力的方法,冲击材料表面,达到清 除和一定的粗糙度
对于DFT、DFO、 FMC 、JDF、或者其他滤筒式过滤器的过滤风 速我们选择过滤风速一般过滤在0.5-0.8m/s之间;切记当选择滤 筒式除尘器式,一定要在过滤器的前面尽量加上一个旋风除尘器,以 降低粉尘浓度,使得进入过滤器的粉尘浓度在其承受范围之内;
铸造行业设备应用领域对照一览表
型号
Nederman 唐纳森
√
√
√
喷丸 √ √ √ √ √ √ √
√
√
√
打磨清 理 √ √ √ √ √ √ √ √ √ √ √ √ √ √
砂处理 √ √ √ √ √
√
√
√
造型线 √ √ √ √ √
√
√
√
注意:“√”为可以采用此类过滤器;
唐纳森DFO圆筒系列除尘器
DFO X-Y DFO是椭圆形滤筒 X代表滤筒层数,x最大到4; Y代表滤筒数量; 每个椭圆形滤筒的过滤面积是17.66m2; 普通滤芯为Cellulex滤芯; 覆膜滤芯为Ultra-WEB滤芯; 清灰方式为脉冲清灰;
a2──不同清理对象系数;
V──室体容积,m^3;
N──抛丸器总功率,kW。
当喷抛联合工作时,上述风量应增加50%~80%。
A.2 不同型式抛丸室系数可按表A1选用。
表A1
━━━━━━━━━━━━━━━━━━━━┯━━━━━━━━━━━━━━━━
抛丸室形式
│
系数,a1
────────────────────┼────────────────
行业应用图表
各区域产生粉尘类型的特点—炉子
高温 可能含有锌粉 可能含油 抽风量有限制,不能过大,也不能过小; 熔炼、倾倒、保温等各个时候所需的风量不一样; 烟气浓度大;