压裂液返排处理
返排压裂液处理方法--文献资料
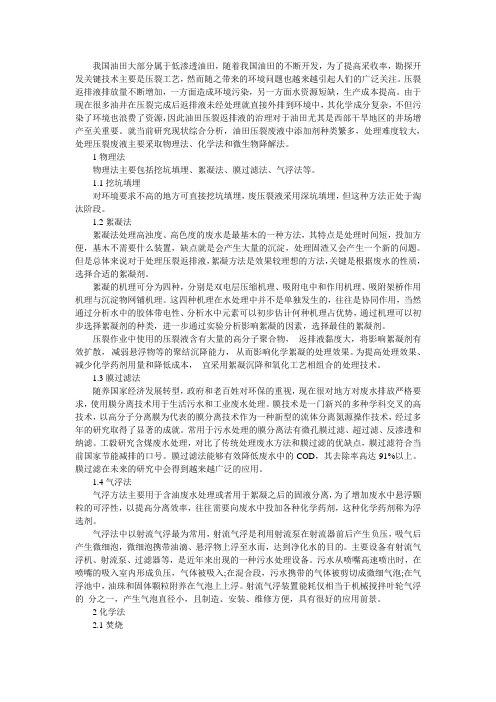
我国油田大部分属于低渗透油田,随着我国油田的不断开发,为了提高采收率,勘探开发关键技术主要是压裂工艺,然而随之带来的环境问题也越来越引起人们的广泛关注。
压裂返排液排放量不断增加,一方面造成环境污染,另一方面水资源短缺,生产成本提高。
由于现在很多油井在压裂完成后返排液未经处理就直接外排到环境中,其化学成分复杂,不但污染了环境也浪费了资源,因此油田压裂返排液的治理对于油田尤其是西部干旱地区的井场增产至关重要。
就当前研究现状综合分析,油田压裂废液中添加剂种类繁多,处理难度较大,处理压裂废液主要采取物理法、化学法和微生物降解法。
1物理法物理法主要包括挖坑填埋、絮凝法、膜过滤法、气浮法等。
1.1挖坑填埋对环境要求不高的地方可直接挖坑填埋,废压裂液采用深坑填埋,但这种方法正处于淘汰阶段。
1.2絮凝法絮凝法处理高浊度、高色度的废水是最基木的一种方法,其特点是处理时间短,投加方便,基木不需要什么装置,缺点就是会产生大量的沉淀,处理固渣又会产生一个新的问题。
但是总体来说对于处理压裂返排液,絮凝方法是效果较理想的方法,关键是根据废水的性质,选择合适的絮凝剂。
絮凝的机理可分为四种,分别是双电层压缩机理、吸附电中和作用机理、吸附架桥作用机理与沉淀物网铺机理。
这四种机理在水处理中并不是单独发生的,往往是协同作用,当然通过分析水中的胶体带电性、分析水中元素可以初步估计何种机理占优势,通过机理可以初步选择絮凝剂的种类,进一步通过实验分析影响絮凝的因素,选择最佳的絮凝剂。
压裂作业中使用的压裂液含有大量的高分子聚合物,返排液黏度大,将影响絮凝剂有效扩散,减弱悬浮物等的聚结沉降能力,从而影响化学絮凝的处理效果。
为提高处理效果、减少化学药剂用量和降低成本,宜采用絮凝沉降和氧化工艺相组合的处理技术。
1.3膜过滤法随养国家经济发展转型,政府和老百姓对环保的重视,现在很对地方对废水排放严格要求,使用膜分离技术用于生活污水和工业废水处理。
膜技术是一门新兴的多种学科交叉的高技术,以高分子分离膜为代表的膜分离技术作为一种新型的流体分离氮源操作技术,经过多年的研究取得了显著的成就。
油田压裂返排液处理技术

油田压裂返排液处理技术1.压裂返排液的产生及存在的问题水基压裂液它具有高黏度、低摩阻、悬砂性好、对地层伤害小等优点现已成为主要压裂液类型。
油井压裂过程中产生的返排压裂废液具有污染物成分复杂、浓度高、黏度大,精品文档,超值下载处理难度大,是油田较难处理污水之一。
如不处理直接进入集输流程,会严重干扰后续流程,严重影响到油田生产,导致设备堵塞、油田下降,环保不达标等诸多问题。
表1 压裂返排液污水性质图1 不同压裂返排水样2.国内常规压裂返排液处理工艺简介2.1 化学氧化-絮凝沉淀-过滤处理工艺采用双氧水、次氯酸钠等强氧化破胶使返排液中的高分子物质氧化分解成小分子物质,降低废液黏度,提高传质效率,增加水处理药剂的分散与分解;絮凝可以改变水中多分散体系表面电性,破坏废液胶体的稳定性,使胶体物质脱稳、聚集;过滤,去除水中不溶或微溶物,脱色除臭。
氧化-絮凝-过滤是油气田污水处理常用工艺。
在实际应用过程中该工艺也存在一些不足,具体如下:第一、该工艺受温度影响比较大,在低温环境,化学氧化剂反应慢,氧化时间长,需要较长的停留时间,导致氧化反应罐(池)占地大,不易在现场作业,运输困难等。
第二、除油效果不明显,系统对乳化油去除效果不佳,需要添加大量药剂,导致污泥量大,增加污泥处理成本。
第三、过滤器时常堵塞,由于氧化破胶不彻底,污油处理效果不佳,导致过滤器堵塞严重,影响最终出水效果和整套装置处理能力。
2.2 化学氧化-絮凝沉淀-电解氧化-过滤联合处理工艺电解法集氧化还原、絮凝吸附、催化氧化、络合及电沉积等作用于一体,能够使大分子物质分解为小分子物质,降解的物质转变成易降解的物质,是污水深度处理的常用方法。
然而电解技术目前在国内应用情况并不理想,时常存在电极钝化、结垢等问题,时常需要更换电极,处理效果稳定性差,成本高,操作检修频繁。
设备占地大,运输困难,不太适合压裂返排液现场处理要求。
2.3 化学氧化-絮凝磁分离-过滤联合处理工艺该工艺改进了絮凝沉淀工艺,采用高效磁分离机能够减少沉降时间,缩小设备占地面积,相对之前两种工艺有改进之处。
2020年油田压裂返排液处理技术.pptx

表 1 压裂返排液污水性质
图 1 不同压裂返排水样
2. 国内常规压裂返排液处理工艺简介
1. 化学氧化-絮凝沉淀-过滤处理工艺 采用双氧水、次氯酸钠等强氧化破胶使返排液中的高分子物质氧化分解成小 分子物质,降低废液黏度,提高传质效率,增加水处理药剂的分散与分解;絮凝 可以改变水中多分散体系表面电性,破坏废液胶体的稳定性,使胶体物质脱稳、 聚集;过滤,去除水中不溶或微溶物,脱色除臭。氧化-絮凝-过滤是油气田污 水处理常用压裂返排液的产生及存在的问题
压裂工艺是油井增产的一项主要措施 在各油田普遍采用。其中最常用的是 水基压裂液它具有高黏度、低摩阻、悬砂性好、对地层伤害小等优点现已成为主 要压裂液类型。 油井压裂过程中产生的返排压裂废液具有污染物成分复杂、浓度高、黏度大,精
品文档,超值下载
学海无涯
在实际应用过程中该工艺也存在一些不足,具体如下: 第一、 该工艺受温度影响比较大,在低温环境,化学氧化剂反应慢,氧化 时间长,需要较长的停留时间,导致氧化反应罐(池)占地大,不易在现场作业 , 运输困难等。
第二、 除油效果不明显,系统对乳化油去除效果不佳,需要添加大量药剂, 导致污泥量大,增加污泥处理成本。
图 2 现场应用照片
学海无 涯
表 2 压裂返排液处理数据
项目
原水 (mg/L) 产水(mg/L)
Ca2+
661
186
Mg2+
77
9
总铁
27
0.54
含油量
185
3
悬浮物
354
压裂返排液现场处理操作规程(2)

压裂返排液现场处理操作规程(2)压裂返排液现场处理操作规程为了规范压裂返排液现场处理流程,提高工作效率,特规定此操作规范。
一、开工前准备准备好施工所需的各种设备药剂:皮卡、杆泵、流程、方罐、pH 试纸、便携式电位仪、破稳降粘剂、电位调节剂、pH调节剂、预处理剂等。
人员配备:司机一名,操作工1-2名,电工一名。
应急设备:干粉灭火器、二氧化碳灭火器各一个(5公斤),3%碳酸氢钠洗液一瓶(500ml),清水一瓶(500ml),京万红烫伤膏一只,绷带、创可贴若干。
(碳酸氢钠洗液,清水主要处理pH调节剂灼伤事故,京万红主要处理一般烫伤事故,创可贴,绷带处理一般刮伤、划伤事故)。
设备到达现场,经专业操作人员连接完设备,开机前,必须全面检查设备有无异常,对转动设备,应确认无卡死现象、漏电现象,管路是否接好,防止漏液现象发生。
施工人员穿戴好防护装备,安全帽,防静电工服,工鞋,防酸手套,口罩(带活性炭芯),护目镜。
若发现有异常情况,及时通知当值技术员、领导,再根据实际情况及时处理。
二、压裂返排液处理标准、流程及注意事项1.现场处理标准(1)pH在6.4-7.5之间(精密试纸5.5-9)。
(2)电位低于219mv(±10%)。
(3)木棍挑挂无拉丝现象(无拉丝现象即为破胶)。
2.处理总体加药流程(1)破稳降粘剂-电位调节剂-pH调节剂-预处理剂(2)如果返排液已破胶,则只添加电位调节剂、pH调节剂、预处理剂,并在罐中沉降除砂,上层清液直接进系统。
(3)如果返排液未破胶,则添加破稳降粘剂至破胶,再添加pH 调节剂、电位调节剂和预处理剂后进罐沉降,过滤后进系统。
3.具体加药流程(1)判断现场有无未使用的配置好的压裂液。
若有则按照1方加入10升液体破稳降粘剂加入,计算加入药剂总量。
若全部都是返排出来的液体则判断返排液是否破胶,如果破胶则执行第(4)步;如果未破胶则按照1方液添加5升液体破稳降粘剂。
(2)破稳降粘剂加药速度根据泵送速度即可(泵每抽1方液即加入1千克固体药剂或者10升液体药剂)。
油田压裂返排废液处理技术方案
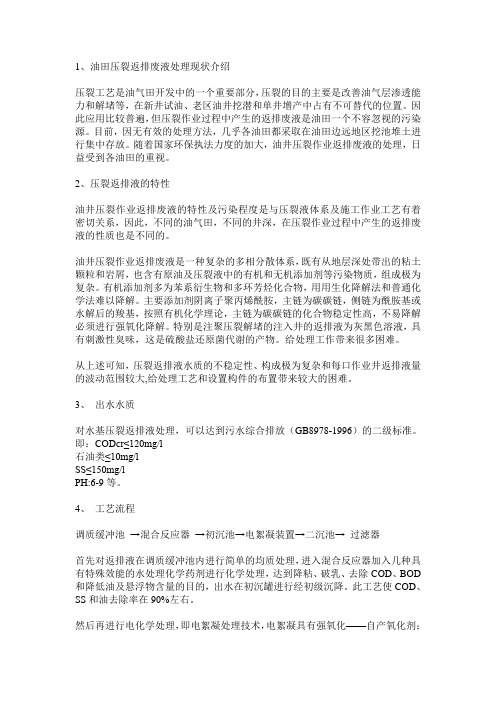
1、油田压裂返排废液处理现状介绍压裂工艺是油气田开发中的一个重要部分,压裂的目的主要是改善油气层渗透能力和解堵等,在新井试油、老区油井挖潜和单井增产中占有不可替代的位置。
因此应用比较普遍,但压裂作业过程中产生的返排废液是油田一个不容忽视的污染源。
目前,因无有效的处理方法,几乎各油田都采取在油田边远地区挖池堆土进行集中存放。
随着国家环保执法力度的加大,油井压裂作业返排废液的处理,日益受到各油田的重视。
2、压裂返排液的特性油井压裂作业返排废液的特性及污染程度是与压裂液体系及施工作业工艺有着密切关系,因此,不同的油气田,不同的井深,在压裂作业过程中产生的返排废液的性质也是不同的。
油井压裂作业返排废液是一种复杂的多相分散体系,既有从地层深处带出的粘土颗粒和岩屑,也含有原油及压裂液中的有机和无机添加剂等污染物质,组成极为复杂。
有机添加剂多为苯系衍生物和多环芳烃化合物,用用生化降解法和普通化学法难以降解。
主要添加剂阴离子聚丙烯酰胺,主链为碳碳链,侧链为酰胺基或水解后的羧基,按照有机化学理论,主链为碳碳链的化合物稳定性高,不易降解必须进行强氧化降解。
特别是注聚压裂解堵的注入井的返排液为灰黑色溶液,具有刺激性臭味,这是硫酸盐还原菌代谢的产物。
给处理工作带来很多困难。
从上述可知,压裂返排液水质的不稳定性、构成极为复杂和每口作业井返排液量的波动范围较大,给处理工艺和设置构件的布置带来较大的困难。
3、出水水质对水基压裂返排液处理,可以达到污水综合排放(GB8978-1996)的二级标准。
即:CODcr≤120mg/l石油类≤10mg/lSS≤150mg/lPH:6-9等。
4、工艺流程调质缓冲池→混合反应器→初沉池→电絮凝装置→二沉池→ 过滤器首先对返排液在调质缓冲池内进行简单的均质处理,进入混合反应器加入几种具有特殊效能的水处理化学药剂进行化学处理,达到降粘、破乳、去除COD、BOD 和降低油及悬浮物含量的目的,出水在初沉罐进行经初级沉降。
《2024年裂缝闭合过程中压裂液返排机理研究与返排控制》范文
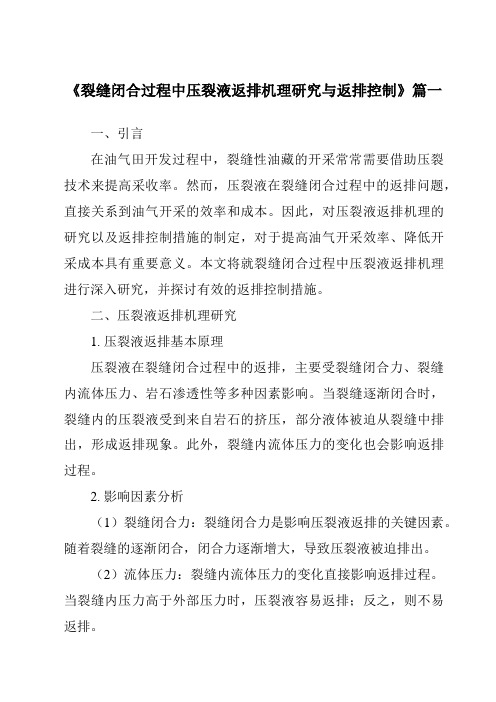
《裂缝闭合过程中压裂液返排机理研究与返排控制》篇一一、引言在油气田开发过程中,裂缝性油藏的开采常常需要借助压裂技术来提高采收率。
然而,压裂液在裂缝闭合过程中的返排问题,直接关系到油气开采的效率和成本。
因此,对压裂液返排机理的研究以及返排控制措施的制定,对于提高油气开采效率、降低开采成本具有重要意义。
本文将就裂缝闭合过程中压裂液返排机理进行深入研究,并探讨有效的返排控制措施。
二、压裂液返排机理研究1. 压裂液返排基本原理压裂液在裂缝闭合过程中的返排,主要受裂缝闭合力、裂缝内流体压力、岩石渗透性等多种因素影响。
当裂缝逐渐闭合时,裂缝内的压裂液受到来自岩石的挤压,部分液体被迫从裂缝中排出,形成返排现象。
此外,裂缝内流体压力的变化也会影响返排过程。
2. 影响因素分析(1)裂缝闭合力:裂缝闭合力是影响压裂液返排的关键因素。
随着裂缝的逐渐闭合,闭合力逐渐增大,导致压裂液被迫排出。
(2)流体压力:裂缝内流体压力的变化直接影响返排过程。
当裂缝内压力高于外部压力时,压裂液容易返排;反之,则不易返排。
(3)岩石渗透性:岩石的渗透性影响压裂液的流动和排出。
渗透性好的岩石有利于压裂液的排出,反之则不利于排液。
三、返排控制措施针对压裂液返排机理的研究,我们可以采取以下措施来控制返排过程:1. 优化压裂液配方通过优化压裂液配方,提高其黏度和降低其表面张力,可以减少压裂液在裂缝中的流失,提高返排效率。
此外,合理选择添加剂可以改善压裂液的流动性能,有助于控制返排过程。
2. 控制注液速度和压力注液速度和压力是影响压裂液返排的重要因素。
适当控制注液速度和压力,使裂缝在合适的时间内闭合,可以减少压裂液的损失,提高返排效率。
同时,实时监测裂缝内流体压力的变化,根据实际情况调整注液参数。
3. 合理选择井身结构和完井方式井身结构和完井方式对压裂液的返排也有重要影响。
根据油藏特点和实际需求,选择合适的井身结构和完井方式,有助于提高压裂液的返排效率。
压裂返排液回用处理
厚德诚信、持续创新、互利共赢! 科力迩,尽环境保护的社会责任,共创碧水蓝天! 压裂返排液回用处理 为了达到环保要求和降低水资源消耗,压裂过程中产生的大量返排液需要进行深度处理后重新利用。
工艺优势:
分离效率高,达到回用要求;
橇装化、可移动装置;
化学药剂量少,油泥量少;
自动化封闭运行,安全环保。
应用范围:
油田压裂返排液;油田酸化返排液
页岩气压裂返排液;废气钻井液处理等。
压裂反排原液进出水对比图
压裂反排
高效混凝沉淀 CDFU 回用 过滤 CDOF 核心处理工艺。
油田压裂反排液的处理方案
处理返排油田压裂液的研究方案压裂作业返排出的残余压裂液含有胍胶、杀菌剂、石油类及其他添加剂,如不经处理而外排,将对周围环境造成严重污染。
处理压裂废液主要采取物理法、化学法和微生物降解法,物理法主要包括絮凝法、膜过滤法、气浮法等,化学法主要包括氧化法、电解处理法等。
目前针对压裂返排液的新处理技术是絮凝法、氧化法、生物法、吸附法的联合技术,技术的关键问题是如何快速、高效地去除COD。
1.设计依据1.1压裂液的配方压裂液分为水基、油基和多相压裂液三大类,以油作溶剂或作分散介质配成的压裂液是最早采用的压裂液,这主要是它对油(气)层的损害比水基压裂液要轻,它的特性黏度比水基压裂液更具有吸引力。
但油基压裂液成本高,施工上难于处理。
因此现在只用于水敏性强的地层或与水基液接触后渗透率下降的地层,水基压裂液也最常用,约占整个压裂液用量的70%。
油基压裂液主要包括:(1)稠化油压裂液。
它是稠化剂(如脂肪酸铝、磷酸酯盐等)溶于油中配成。
(2)油包水压裂液。
它是一种以油为分散介质,水作分散相,油溶性表面活性剂作乳化剂配成的压裂液。
如以淡水作水相、以柴油作油相,以月桂酰二乙醇作乳化剂,即可配成。
(3)油基泡沫压裂液。
它是以气体(CO2和N2)作分散相,以油作分散介质配成。
水基压裂液一般是水冻胶压裂液,是用交联剂将溶于水的增稠剂高分子进行不完全交联,使具有线性结构的高分子水溶液变成线型和网状体型结构混存的高分子水冻胶,由稠化剂、交联剂、缓冲剂、黏土稳定剂、杀菌剂和助排剂等组成。
多相压裂液由泡沫压裂液等。
泡沫压裂液是一个大量气体分散于少量液体中的均匀分散体系,主要成分有气相、液相、表面活性剂和泡沫稳定剂等其他化学添加剂组成。
不同配方压裂液的返排液处理方法大相径庭,了解压裂液的配方和对返排液的指标分析使得对水处理的方案更加有针对性和高效性。
1.2压裂返排液的水质分析压裂返排液外观呈浅黄色,并伴有强烈的刺激性气味,黏度较大,表面无明显浮油。
压裂返排液处理方案
压裂返排液处理方案
压裂返排液是指通过压裂作业所产生的含有大量固体颗粒、有机物和化学添加剂的废水。
处理压裂返排液需要采取多重技术和方案,以确保废水的安全排放或有效回收利用。
以下是一种常见的压裂返排液处理方案:
1. 溶解气浮:将压裂返排液首先加入溶解气浮槽中,通过加入一定量的药剂和气体,使其中的悬浮物和油脂等污染物从废水中浮出,形成浮渣。
2. 机械过滤:将溶解气浮后的废水进一步通过机械过滤设备,如滤网或滤料,去除较小的颗粒物和悬浮物。
3. 活性炭吸附:将过滤后的废水通过活性炭吸附器,吸附其中有机物质和化学添加剂等溶解性污染物。
4. 生物处理:将吸附后的废水通过生物反应器进行生物降解处理,利用微生物降解有机物质和部分化学添加剂。
5. 深度过滤:将生物处理后的废水进行深度过滤,去除残留的微生物和颗粒物。
6. 杂质去除:通过离子交换等方式去除废水中的重金属离子和其他残留杂质。
7. 监测和排放:对处理过的废水进行监测,确保达到当地环保
标准后,安全进行排放或者回用。
需要注意的是,不同地区和不同情况下的压裂返排液可能存在一定的差异,因此处理方案可能需要根据具体情况进行调整和优化。
同时,处理过程中需要遵循相关环保法规和标准,并严格控制处理过程中的废弃物和废气排放。
石油工程技术 压裂返排液处理与重复利用技术
压裂返排液处理与重复利用技术1压裂返排液处理技术1.1达标外排为了有效防止生态环境及地下水污染,近几年国家能源局大力推进压裂返排液处理技术研究。
目前,我国压裂返排液外排的水质标准采用的是石油天然气行业标准SY/T5329—2012《碎屑岩油藏注水水质推荐指标及分析方法》和国家标准GB8978—1996《污水综合排放标准》,主要水质指标包括pH值、色度、悬浮物、化学需氧量(COD)、生化需氧量(BOD)、石油类及细菌含量。
处理工艺包括pH 调节、混凝沉淀、油水分离、杀菌及氧化处理等,最后通过清水稀释达到安全排放标准后再进行外排。
由于返排液的复杂性和稳定性,导致处理难度大,成本太高,而且现有的处理工艺都无法去除返排液中的高浓度盐类物质。
虽然各类标准都未对盐类物质作具体要求,但高浓度的盐水排入生态环境会造成许多不良影响。
另外,对于大多数缺水区域,对大量的返排液进行处理后外排也是对水资源的浪费,因此将返排液处理后外排并不是一个好的选择。
1.2处理后回注将压裂返排液经过处理达标后再回注地层,这不仅可以有效解决返排液的排放问题,还能弥补注水开发过程中对用水的需求。
处理后的返排液需达到石油天然气行业标准SY/T5329—2012《碎屑盐油藏注水水质推荐指标及分析方法》的要求方能进行回注,同时还要采取切实可行的措施,防止地层污染。
由于回注水仅对油含量、悬浮物含量及粒径有较严格要求,因此相对于返排液处理后外排,对其处理后再回注不仅可以节省大量水资源,同时也降低处理成本。
然而,由于返排液不仅悬浮物含量高,而且黏度大,性质稳定,必须对其进行氧化、絮凝及过滤等操作后方能达到回注要求,因此需要外运到回注站进行集中处理,而回注站的处理能力一般很难满足大规模返排液处理的要求,且成本高、地下水环境风险不明确。
另外,这种处理方式对返排液中大量残余的稠化剂也是一种浪费。
因此,对返排液进行处理后回注也并非是最佳选择。
1.3处理后重复配制压裂液随着非常规油气资源开采力度加大,压裂用水量和压裂废水急剧增加。
- 1、下载文档前请自行甄别文档内容的完整性,平台不提供额外的编辑、内容补充、找答案等附加服务。
- 2、"仅部分预览"的文档,不可在线预览部分如存在完整性等问题,可反馈申请退款(可完整预览的文档不适用该条件!)。
- 3、如文档侵犯您的权益,请联系客服反馈,我们会尽快为您处理(人工客服工作时间:9:00-18:30)。
11.2 项目实施方案
11.2.1压裂返排液分析
常规压裂施工所采用的压裂液体系,以水基压裂液为主。
压裂施工后所产生的压裂废液主要来源于两个方面:一是施工前后采用活性水洗井作业产生的大量洗井废水;另一个方面就是压裂施工完成后从井筒返排出来的压裂破胶液,返排的压裂废液中含有大量的胍胶、甲醛、石油类及其他各种添加剂,众多添加剂的加入使压裂液具有较高的COD值、高稳定性、高黏度等特点,特别是一些不易净化的亲水性有机添加剂,难以从废水中除去。
总的来说,压裂废液具有以下特点:
(1)成分复杂。
返排液主要成分是胍胶和高分子聚合物等,其次是SRB菌、硫化物、硼酸根、铁离子和钙镁离子等,总铁、硼含量都很高。
(2)处理难度大。
悬浮物是常规含油污水处理中最难达标的项目,压裂返排液组分的复杂性及其性质的独特性决定了其处理难度更大。
(3)处理后要求比较高。
处理后的液体不仅粘度色度要达标,里面的钙镁离子、铁离子、和硼酸根离子均要去除,否则会影响后续配制压裂液的各项性能。
11.1 国内外研究现状
由于压裂废液具有粘度大、稳定性好、COD高等特点,环保达标处理难度较大。
国外对压裂废液的处理主要是回收利用。
根据国外报道的技术资料看,他们对压裂废液的处理技术和工艺相对简单,一般采用固液分离、碱化、化学絮凝、氧化、过滤等几个组合步骤,处理后的水用于钻井泥浆、水基压裂液、固井水泥浆等配制用水。
这种处理方式不仅降低了处理压裂废液的费用支出,而且还减少了污染物的排放。
国内对早些压裂废液的处理主要采取以下一些方法:
(1)废液池储存:将施工作业中产生的压裂废液储存在专门的废液池中,采用自然蒸发的方式干化,最后直接填埋。
这种处理方式不仅耗时长,而且填埋的污泥块仍然会渗滤出油、重金属、醛、酚等污染物,存在严重的二次污染。
(2)焚烧:这种方式虽然可以在一定程度上控制污染物的排放,但仍然会造成大气污染。
(3)回注:将压裂废液收集,集中进行絮凝、氧化等预处理,然后按照一定比例与采油污水掺混进行再处理,处理后的水质达标后用作回注用水。
就当前研究现状综合分析,处理压裂液返排液回注回注工艺,国内大多数油田采用自然沉降—混凝—过滤的“老三段”式常规处理工艺。
传统处理工艺面临着很多问题,比如沉淀时间长,处理能力低下,净化药剂投加量过大,造成处理后的液体中含盐量的增加,絮凝沉淀后的污泥量过大增加运输成本。
11.2 工艺原理
我公司根据以上难点和问题以及现场施工特点发明了一套最新的压裂液返排液处理工艺。
我公司计划采取絮凝沉淀-固液分离-深度过滤的处理工艺,为压裂返排液高效处理提供一套有效的解决方案。
主要技术特点:
(1)系统设备:采用撬装式设计,操作方便、操作过程连续化、操作管理方便、运行成本低。
(2)絮凝沉淀:采用高效复合混凝剂、絮凝剂提高处理效率。
(3)过滤:经过两个阶段过滤除杂,高效彻底。
(4)深度过滤:膜过滤深度过滤,最终效果有保障。
絮凝沉淀
向废水中投如一定量的混凝剂、絮凝剂,在适当的条件下形成絮体和水相的非均相混合体系,利用重力作用,实现絮体和水相的分离,从而达到去除污染物的目的。
通过絮凝,压裂废液中的高分子单体、高分子残渣得以去除,因此COD值大幅度降低。
一般来说,通过优选絮凝剂及助凝剂种类、优化絮凝剂加量、调节絮凝条件,能够使压裂废液的COD去除率达到40~70%。
絮凝法不仅能降低压裂废液的COD值,而且还能有效降低压裂废液的含油量、悬浮物含量、浊度等。
采用新型化学处理剂,大大降低絮凝时间,提高絮凝效率。
采用新型化学处理剂后,在10分钟的絮凝沉降时间后,其处理的结果可以达到传统化学处理剂处理效果的90%以上。
表11-3 不同处理剂的效果对比
固液分离
絮凝沉淀后的液体通过过滤装置进行固液分离。
过滤分为两个阶段,先经过小目数的过滤网去除肉眼可见的固态悬浮物,后经过大目数的过滤网过滤微小絮凝物,经过这两步过滤后的处理液可以达到肉眼看上去非常清澈,物理性质跟水一样的效果。
深度过滤
沉淀分离产生的液相通过深度过滤装置进一步降低液相中的COD值、铁、硼酸根离子的含量。
深度过滤选用非对称膜。
此种膜管壁密布微孔,在压力作用下,原料液在膜管内或膜外侧流动,小分子物质(或液体)透过膜,大分子物质(或固体)被膜截留,从而达到分离、浓缩、纯化和环保等目的。
此种膜具有分离效率高、效果稳定、化学稳定性好、耐酸碱、耐有机溶剂、耐菌、耐高温、抗污染、机械强度高、再生性能好、分离过程简单、能耗低、操作维护简便、使用寿命长等众多优势。
经过深度过滤处理后的液相,达到国家排放标准(GB8978-1996)二级标准。
处理后污水可回用重新配置压裂液。
11.2.4 工艺流程
本方案主要工艺是采用先进的絮凝剂,经过絮凝沉降、固液分离、深度过滤等工序,过程简单实用且破胶除油效果显著。
之后选用高效的处理药剂,将固相进行无害化处理,处理后固相浸出液指标达到验收标准;液相经过深度过滤处理后,现场试验检测满足重新配液要求。
图11-1 处理工艺流程图
施工方案
➢作业前准备
1)返排液处理作业准备
通过与客户协调,公司技术支持人员于开工前7天左右进行现场勘查并完成现场实验。
2)安全技术培训
公司安排作业人员,项目经理1名,技术负责人1名,现场工程师人员10名(1人兼任电工,资质齐全),值班车司机等,所有项目人员都应资质齐全,完成技术、操作人员QHSE培训。
开工前设备维护期间,完成操作人员安全操作培训,并建立员工的培训记录。
3)设备搬迁和现场人员动员
待甲方下发开工动员通知单后,本项目现场人员要提前抵达作业现场,通知公司有关部门准备板车和吊车,将设备和药剂等从公司乌审旗基地搬迁到压裂酸化作业现场。
4)安装调试与试运行
设备进场后,技术管理人员确定装置停放位置,并依据设备调试方案,指导操作人员进行设备安装调试。
药剂到达现场后,存放到易于施工的高地,做到上盖下垫。
➢施工作业工序
1)传输-均质调节系统:
用物料输送系统将井下压裂酸化后返出的液体输送到均质调节系统中,进行均质调节,用泵提升至下一个流程。
2)加药混合破胶-离心分离系统
用气动泵提升返排液的同时按比例投加加破胶剂和絮凝剂,经混合反应设备充分反应后的液体进入均质调节系统处理,进行充分破胶絮凝,破胶后的液体泵入高速离心机,离心分离产生的固相进入固相接收罐,接收后使用螺旋输送机提升至加药混拌设备,进行无害化处理。
离心分离后的液相进入下一步流程。
3)集成超微气泡-混合氧化反应系统
离心分离后的液相进入储罐储存,经过泵提升至超微气泡反应混合装置,同
时加入氧化剂,超微气泡能够缩短氧化反应时间,同时能够解决超滤膜污染的问题,延长超滤膜的使用寿命,充分氧化反应后进入下一步流程。
4)浸没式超滤系统
混合反应后的液相进入浸没式超滤系统进行深度处理,超滤出水到达《污水综合排放标准》GB8978-1996的标准,满足回收配置压裂液的要求。