常减压蒸馏装置的三环节用能分析
常减压蒸馏装置生产中的问题与解答
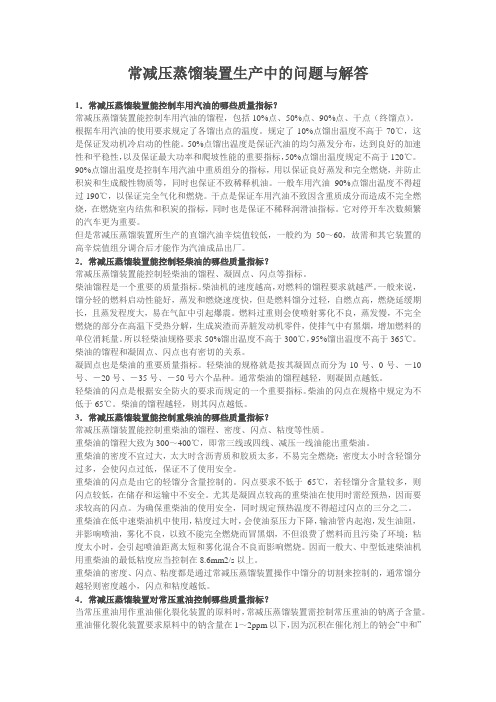
常减压蒸馏装置生产中的问题与解答1.常减压蒸馏装置能控制车用汽油的哪些质量指标?常减压蒸馏装置能控制车用汽油的馏程,包括10%点、50%点、90%点、干点(终馏点)。
根据车用汽油的使用要求规定了各馏出点的温度。
规定了10%点馏出温度不高于70℃,这是保证发动机冷启动的性能。
50%点馏出温度是保证汽油的均匀蒸发分布,达到良好的加速性和平稳性,以及保证最大功率和爬坡性能的重要指标,50%点馏出温度规定不高于120℃。
90%点馏出温度是控制车用汽油中重质组分的指标,用以保证良好蒸发和完全燃烧,并防止积炭和生成酸性物质等,同时也保证不致稀释机油。
一般车用汽油90%点馏出温度不得超过190℃,以保证完全气化和燃烧。
干点是保证车用汽油不致因含重质成分而造成不完全燃烧,在燃烧室内结焦和积炭的指标,同时也是保证不稀释润滑油指标。
它对停开车次数频繁的汽车更为重要。
但是常减压蒸馏装置所生产的直馏汽油辛烷值较低,一般约为50~60,故需和其它装置的高辛烷值组分调合后才能作为汽油成品出厂。
2.常减压蒸馏装置能控制轻柴油的哪些质量指标?常减压蒸馏装置能控制轻柴油的馏程、凝固点、闪点等指标。
柴油馏程是一个重要的质量指标。
柴油机的速度越高,对燃料的馏程要求就越严。
一般来说,馏分轻的燃料启动性能好,蒸发和燃烧速度快,但是燃料馏分过轻,自燃点高,燃烧延缓期长,且蒸发程度大,易在气缸中引起爆震。
燃料过重则会使喷射雾化不良,蒸发慢,不完全燃烧的部分在高温下受热分解,生成炭渣而弄脏发动机零件,使排气中有黑烟,增加燃料的单位消耗量。
所以轻柴油规格要求50%馏出温度不高于300℃,95%馏出温度不高于365℃。
柴油的馏程和凝固点、闪点也有密切的关系。
凝固点也是柴油的重要质量指标。
轻柴油的规格就是按其凝固点而分为10号、0号、-10号、-20号、-35号、-50号六个品种。
通常柴油的馏程越轻,则凝固点越低。
轻柴油的闪点是根据安全防火的要求而规定的一个重要指标。
【常减压工艺流程】常减压工艺流程的原理
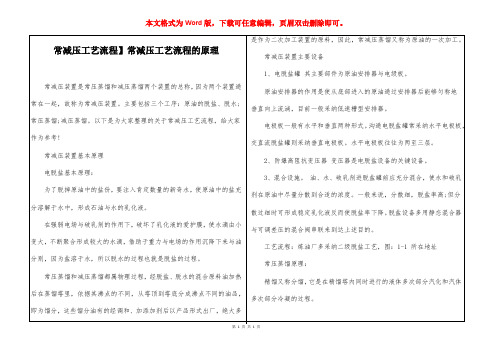
五括钢结构、炉管、炉墙、燃烧器、孔类配件等。
它分为自然通风和强制通风两种方式。前者依靠烟囱本身的抽力,后
第1页共1页
者使用风机。
本文格式为 Word 版,下载可任意编辑,页眉双击删除即可。
过去,绝大多数炉子都采纳自然通风方式,烟囱安装在炉顶。
随着炉子的结构冗杂化,炉内烟气侧阻力增大,加之提高加热炉的热
蒸塔、常压塔、减压塔。
的是管孔式液体分布器和喷淋型液体分布器。
、蒸馏塔的结构:
气体分布器:气体分布器一般应用在汽提蒸汽入塔处,目的是使蒸汽
塔体:塔体是由直圆柱型桶体,高度在 35~40 米左右,材质一般为 匀称分布。
第1页共1页
本文格式为 Word 版,下载可任意编辑,页眉双击删除即可。
破沫 XX:在减压塔进料上方,一般都装有破沫 XX,破沫 XX 由丝 XX
以靠预热燃烧空气来回收,使回收的热量再次返回到炉中
烧时产生的高温火焰与烟气作为热源,加热炉中高速流淌的物料,使其到
是采纳另外的系统回收热量。前者称为空气预热方式,后者通用水回
达后续工艺过程所要求的温度。
收称为废热锅炉方式。
管式加热炉一般由辐射室、对流室、余热回收系统、燃烧及通风系统
燃烧及通风系统:通风系统的作用是把燃烧用空气导入燃烧器,将废
散过细时可形成稳定乳化液反而使脱盐率下降。脱盐设备多用静态混合器
在强弱电场与破乳剂的作用下,破坏了乳化液的爱护膜,使水滴由小 与可调差压的混合阀串联来到达上述目的。
变大,不断聚合形成较大的水滴,借助于重力与电场的作用沉降下来与油
工艺流程:炼油厂多采纳二级脱盐工艺,图:1-1 所在地址
分别,因为盐溶于水,所以脱水的过程也就是脱盐的过程。
常在一起,故称为常减压装置。主要包括三个工序:原油的脱盐、脱水; 垂直向上流淌,目前一般采纳低速槽型安排器。
常减压蒸馏装置与设备分析

随着环保要求的日益严格,常减压蒸馏装置将面临更严峻的节能减排 挑战,需要不断开发和应用低能耗、低排放的新技术和新设备。
06
案例分析与实际操作
常减压蒸馏装置运行案例分析
案例一
装置启动过程中的参数调整
01
02
描述
在装置启动阶段,通过对温度、压力等关键参数的精细 调整,实现装置的平稳启动,提高产品质量的稳定性。
少能源浪费。
低排放技术
03
通过改进工艺流程和操作条件,减少装置废气、废水的排放,
实现绿色、环保生产。
设备自动化与智能化发展
1 2 3
自动化控制系统
常减压蒸馏装置引入先进的自动化控制系统,实 现生产过程的实时监测、自动调节,提高装置的 稳定性和安全性。
智能化诊断与预警
通过引入大数据、人工智能等技术,建立装置故 障诊断和预警模型,实现装置故障的及时发现和 处理,减少生产中断时间。
分析
阐述结焦形成的机理和危害,详细讲解预防措施的原理 和实施方法,提高装置的运行稳定性和寿命。
现场操作演示与实训
演示一
常减压蒸馏装置启动操作
内容
现场展示装置启动的全过程,包括参数设置、设备检查、 启动程序等,使学员全面了解装置启动的要点和注意事项 。
演示二
设备故障应急处理
内容
模拟设备故障场景,展示应急处理的操作流程和技巧,培 养学员应对突发情况的能力和冷静处理问题的心态。
装置的预防性维修与大修计划
预防性维修
根据设备的运行情况和历史故障数据,制定预防性维修计划,对 可能出现故障的部位进行提前维修和更换。
大修计划
根据设备的磨损情况和运行时间,制定大修计划,对装置进行全面 、系统的维修和更新,以确保装置的长周期稳定运行。
减压蒸馏的工作原理和应用
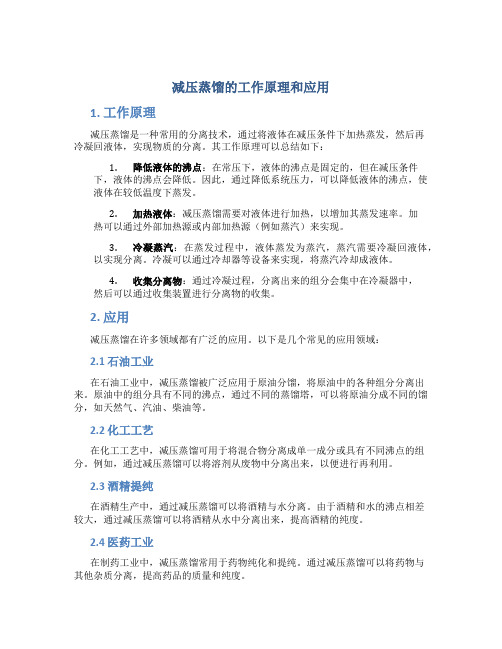
减压蒸馏的工作原理和应用1. 工作原理减压蒸馏是一种常用的分离技术,通过将液体在减压条件下加热蒸发,然后再冷凝回液体,实现物质的分离。
其工作原理可以总结如下:1.降低液体的沸点:在常压下,液体的沸点是固定的,但在减压条件下,液体的沸点会降低。
因此,通过降低系统压力,可以降低液体的沸点,使液体在较低温度下蒸发。
2.加热液体:减压蒸馏需要对液体进行加热,以增加其蒸发速率。
加热可以通过外部加热源或内部加热源(例如蒸汽)来实现。
3.冷凝蒸汽:在蒸发过程中,液体蒸发为蒸汽,蒸汽需要冷凝回液体,以实现分离。
冷凝可以通过冷却器等设备来实现,将蒸汽冷却成液体。
4.收集分离物:通过冷凝过程,分离出来的组分会集中在冷凝器中,然后可以通过收集装置进行分离物的收集。
2. 应用减压蒸馏在许多领域都有广泛的应用。
以下是几个常见的应用领域:2.1 石油工业在石油工业中,减压蒸馏被广泛应用于原油分馏,将原油中的各种组分分离出来。
原油中的组分具有不同的沸点,通过不同的蒸馏塔,可以将原油分成不同的馏分,如天然气、汽油、柴油等。
2.2 化工工艺在化工工艺中,减压蒸馏可用于将混合物分离成单一成分或具有不同沸点的组分。
例如,通过减压蒸馏可以将溶剂从废物中分离出来,以便进行再利用。
2.3 酒精提纯在酒精生产中,通过减压蒸馏可以将酒精与水分离。
由于酒精和水的沸点相差较大,通过减压蒸馏可以将酒精从水中分离出来,提高酒精的纯度。
2.4 医药工业在制药工业中,减压蒸馏常用于药物纯化和提纯。
通过减压蒸馏可以将药物与其他杂质分离,提高药品的质量和纯度。
2.5 食品工业在食品工业中,减压蒸馏可用于提取天然香料和食品添加剂。
通过减压蒸馏可以将香料和添加剂从原材料中提取出来,以增加食品的香气和口感。
3. 总结减压蒸馏是一种常用的分离技术,通过降低液体的沸点和冷凝蒸汽,实现物质的分离。
在石油工业、化工工艺、酒精提纯、医药工业和食品工业等领域都有广泛的应用。
减压蒸馏技术在实际应用中,需要根据具体的分离物和工艺条件进行优化和调整,以获得最佳的分离效果和经济效益。
常减压装置用能分析

馏 装 置 为 例 , 用 能 量 系统 “ 环 节 ” 构 理 论 , 装 置 进 行 了 用 能 分 析 . 据 分 析 所 得 结 果 , 论 了 该 常 压 蒸 馏 运 三 结 对 根 讨
装 置 实 现 节 能 的 方 向 , 提 出 了具 体 的节 能 措 施 . 并
关 键 词 : 减 压 ; 耗 ; 环 节 能 量 结 构 ; 量 平衡 常 能 三 能
J 12 1 u. 0 2
文 章 编 号 :1 7 — 9 X( 0 2 0 — 0 90 6 26 1 2 1 )40 4—3
常减 压 装 置 用 能分析
吴 云鹏 , 李 锋
( 州 石化 公 司 炼 油 厂 , 肃 兰州 7 0 6 ) 兰 甘 3 00
摘
要 : 学地分析评价炼油过程用能状况是 炼油 企业实现 节能 的基础. 文 以某炼油 厂 5 5 / 科 本 . Mta常 减 压 蒸
中图分类号 : TE6 4 2 2 . 文 献 标识 码 :A
O 引 言
石 油加工 行 业 即是 能 源 生 产企 业 , 是 能源 也 消耗大 户. 介绍 [ , 国能源 的利 用率 比世 界先 据 】我 ]
3 5 , 不影 响换 热 终 温 的 前 提下 , 分 利 用 低 0℃ 在 充 温位 的物 流加 热 低 温热 媒 水 , 回收 装 置 的低 温 余 热, 降低 能耗. 原油 电脱盐 系统 采用 国内电脱 盐技
用能 状况则 是节 能工 作 的基础 . 笔者 以某炼 油 厂 的常 减压蒸 馏 装置 为 例 , 用 过 程 系统 三 环 节 能 运
量 结 构理论 , 出了能 量 利 用 的 薄弱 环 节 和 装 置 指 的节 能方 向 , 出 了相 应 的节能 措施 . 提
常减压蒸馏能耗分析
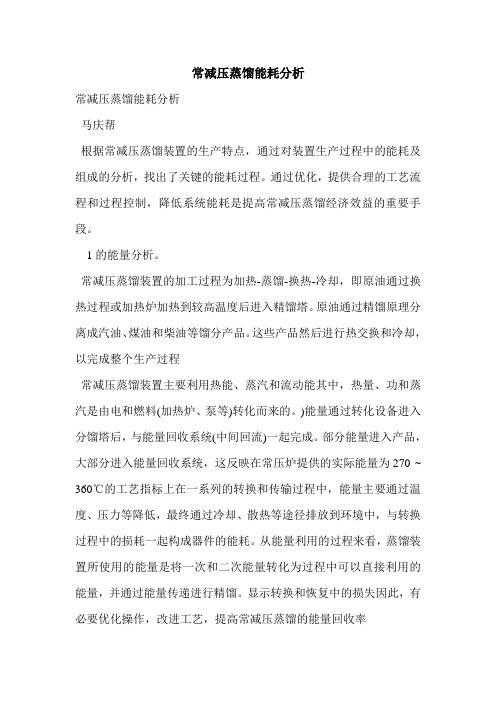
常减压蒸馏能耗分析常减压蒸馏能耗分析马庆帮根据常减压蒸馏装置的生产特点,通过对装置生产过程中的能耗及组成的分析,找出了关键的能耗过程。
通过优化,提供合理的工艺流程和过程控制,降低系统能耗是提高常减压蒸馏经济效益的重要手段。
1的能量分析。
常减压蒸馏装置的加工过程为加热-蒸馏-换热-冷却,即原油通过换热过程或加热炉加热到较高温度后进入精馏塔。
原油通过精馏原理分离成汽油、煤油和柴油等馏分产品。
这些产品然后进行热交换和冷却,以完成整个生产过程常减压蒸馏装置主要利用热能、蒸汽和流动能其中,热量、功和蒸汽是由电和燃料(加热炉、泵等)转化而来的。
)能量通过转化设备进入分馏塔后,与能量回收系统(中间回流)一起完成。
部分能量进入产品,大部分进入能量回收系统,这反映在常压炉提供的实际能量为270 ~ 360℃的工艺指标上在一系列的转换和传输过程中,能量主要通过温度、压力等降低,最终通过冷却、散热等途径排放到环境中,与转换过程中的损耗一起构成器件的能耗。
从能量利用的过程来看,蒸馏装置所使用的能量是将一次和二次能量转化为过程中可以直接利用的能量,并通过能量传递进行精馏。
显示转换和恢复中的损失因此,有必要优化操作,改进工艺,提高常减压蒸馏的能量回收率2。
分析和优化,节能降耗。
优化操作,降低总工艺能量蒸馏是蒸馏装置工艺能耗的核心。
能耗的多少取决于原油中总馏出物的比例和产品质量的要求。
然而,影响总提取率和产品质量的关键因素是超汽化率和中段热提取率1.1,超汽化率。
从传统的节能观点来看,过汽化率越低,越节能。
从生产操作的角度来看,一般认为过汽化率越高;轻油的产量越高;产品质量越好实践表明,常压塔过汽化率的合理经验值为2% ~ 4%1.2产品质量生产中的产品质量控制不容忽视;要求太高,不仅降低了产品的收率,而且浪费了高温下的热量回收。
特别是对于第二和第三蒸馏管线,产品的分配不仅要考虑产量最大化,还要考虑节能。
因此,优化操作,实施“卡边”操作,提高成品率,已经成为一种可以接受的、降低成本的合理操作方法。
常减压蒸馏装置与设备分析ppt

2
3
常减压蒸馏装置的能耗主要包括加热炉能耗、机械能耗、电能耗等。
能耗组成
常减压蒸馏装置的能耗较大,其中加热炉能耗占比最大,其次是机械能耗和电能耗。
能耗特点
常减压蒸馏装置的能耗受到多种因素的影响,如原油性质、加工负荷、操作条件等。
能耗影响因素
03
排放标准
常减压蒸馏装置的有害物质排放应符合国家和地方的相关排放标准。
常减压蒸馏设备的种类与用途
常减压蒸馏装置与设备的现状
目前常减压蒸馏装置已经比较成熟,各种设备的设计和制造已经比较完善,能够实现高效的分离和热交换。
常减压蒸馏装置与设备的发展趋势
随着技术的不断进步,常减压蒸馏装置也在不断升级改造,设备更加高效、节能、环保,智能化程度也越来越高。
常减压蒸馏装置与设备的现状及发展趋势
选用原则
选用常减压蒸馏装置的主要设备时,需要考虑以下原则:适用性原则——根据装置的规模、原料性质、产品质量等因素选用适合的设备;可靠性原则——选用质量稳定可靠、性能优良的设备;经济性原则——选用价格合理、使用寿命长、能耗低的设备;环保性原则——选用符合环保要求的设备,减少污染排放。
主要设备的性能特点及选用原则
常减压蒸馏装置的组成
常减压蒸馏是将原油加热到一定温度后,通过一系列的塔器和冷换设备进行分离,得到不同沸点的馏分。
常减压蒸馏装置的工作原理
常减压蒸馏装置的组成及工作原理
常减压蒸馏设备的种类
常减压蒸馏设备包括各种类型的塔器、加热炉、冷换设备、机泵等。
常减压蒸馏设备的用途
不同设备在常减压蒸馏过程中起着不同的作用,如塔器用于分离馏分,加热炉提供热量,冷换设备进行热交换等。
设备的安装与调试技术要求
质量控制
石油炼制中常减压装置的节能分析

石油炼制中常减压装置的节能分析节能是石油炼制过程中的重要环节,随着能源问题的日益突出,节能成为了石油炼制行业发展的关键。
常减压装置作为石油炼制过程中的一个重要设备,其节能优化也是炼油企业努力的方向。
本文将从常减压装置的工艺流程及设备特点出发,分析其节能优化的方法和措施。
常减压装置是石油炼制过程中的一个重要环节,主要用于分离原油中的不同组分。
其工艺流程一般包括加热、常减压和冷凝三个阶段。
在加热阶段,原油被加热至一定温度,以提高其蒸发性;在常减压阶段,原油被进一步加热,使其在较低的压力下蒸发,从而实现分离;在冷凝阶段,蒸发出的油气被冷凝成液态,进一步分离出不同组分的油品。
常减压装置的节能优化主要可以从以下几个方面入手。
首先是加热阶段的节能优化。
加热过程中,可以采用先进的加热设备,如传热效率高的换热器;对进入加热器的原油进行预热,以减轻加热器的负荷;对加热器进行热能回收,将废热用于加热其他流体等,从而提高能源利用效率。
其次是常减压阶段的节能优化。
常减压装置一般采用多级减压设备,通过逐级降低压力,使原油在不同温度下蒸发,实现组分的分离。
在常减压过程中,可以采用适当的温度和压力,使蒸汽压力和冷凝温度得到优化,从而减少能量损耗。
常减压设备的密封性能也是影响能源利用的重要因素,通过对密封系统的改进,减少泄漏,进一步提高能源利用效率。
最后是冷凝阶段的节能优化。
常减压装置在冷凝阶段,将蒸发出的油气冷凝成液态,通过冷凝器进行冷凝。
在冷凝过程中,可以采用高效的冷凝设备,如换热器等,以提高冷凝效率;对冷凝器的水冷方式进行优化,如采用冷却塔等,减少能源消耗。
除了上述几个方面外,常减压装置的节能优化还可以从运营管理层面入手。
可以制定合理的运行方案,如减少停工次数,降低设备启停的能耗;加强人员培训,提高操作人员的技术水平和管理能力,减少人为因素对能源消耗的影响;定期检修设备,保证设备的正常运行,减少能源损耗等。
常减压装置的节能优化需要从多个方面入手,包括工艺流程的优化、设备的改进以及运营管理的提升。
- 1、下载文档前请自行甄别文档内容的完整性,平台不提供额外的编辑、内容补充、找答案等附加服务。
- 2、"仅部分预览"的文档,不可在线预览部分如存在完整性等问题,可反馈申请退款(可完整预览的文档不适用该条件!)。
- 3、如文档侵犯您的权益,请联系客服反馈,我们会尽快为您处理(人工客服工作时间:9:00-18:30)。
2003年6月石油学报(石油加工)ACTAPETROLEISINICA(PETROLEUMPROCESSINGSECTION)第19卷第3期文章编号:1001—8719(2003)03—0053—05常减压蒸馏装置的“三环节"用能分析ENERGYANALYSIS0FATMoSPHERICANDVACUUMDISTILLATIONUNITBASEDONTHREE-LINKMETHoD李志强,侯凯锋,严淳LIZhi—qiang,HOUKai—feng,YANChun(中国石化工程建设公司,北京100011)(SINOPECEngzneeringIncorporation,BeOing100011,China)摘要:科学地分析评价炼油过程用能状况是节能工作的基础。
笔者以某炼油厂常减压蒸馏装置为例,运用过程系统三环节能量结构理论,依据热力学第一定律和热力学第二定律进行了装置的能量平衡和炯平衡计算及分析,并根据分析结果指出了装置的节能方向,提出了节能措施。
关键词:常减压蒸馏;节能;三环节能量结构;能量平衡和炯平衡分析中图分类号:TE01文献标识码:AAbstract:Energy—savinginrefineriesneedstobecarriedoutbasedonthescientificallyenergyanalysisandevaluationoftheprocessingunits.Theatmosphericandvacuumdistillationunitinarefinerywastakenasanexample,itsenergyandexergybalanceswerethenworkedoutthroughcalculationaccordingtothethree—linkmethodforprocessintegrationfollowingtheFirstLawandtheSecondLawofthermodynamics.Theresultswereanalyzed,andthecorrespondingmeasuresforenergy—savingwereproposed.Keywords:atmosphericandvacuumdistillationunit;energy~saving;three—linkenergymethod;energyandexergybalanceanalysis炼油生产过程中为分离出合格的石油产品,需要消耗大量的能量。
因此,能源消耗在原油加工成本中占有很大的比例。
炼油过程的节能不仅可以降低加工成本,而且关系到石油资源的合理利用和企业的经济效益¨J。
与国外先进的炼油厂相比,我国炼油企业的吨油能耗相对较高。
2001年,中国石化股份有限公司所属炼厂平均能耗为77.85kg标油/t原油,与目前世界上大型化复杂炼厂的能耗不大于75kg标油/t原油的先进指标相比,差距较大,节能空间也更大。
因此,加强节能技术的应用,降低炼油过程的能耗,是我国炼油企业降本增效、提高市场竞争力、实现可持续发展的必由之路。
炼油企业的用能水平因生产规模、加工流程、工艺装置的设计、操作和管理水平以及加工原油的品种和自然条件等不同而差别较大。
因此,炼油企业的节能工作必须因厂而异,因装置而异,节能措施要有针对性。
科学地分析评价炼油过程用能状况则是节能工作的基础【2J。
笔者以某炼油厂的常减压蒸馏装置为例,运用过程系统三环节能量结构理论,依据热力学第一定律和热力学第二定律进行了装置的能量平衡和炯平衡计算,并根据计算结果对装置的用能状况进行了分析与评价,指出了能量利用的薄弱环节和装置的节能方向,提出了相应的节能措施。
1三环节能量结构理论炼油生产过程的用能有3个特点:(1)产品分离和合成需要外部供应能量,以热和功两种形式传给收稿日期:2002—07—23通讯联系人:侯凯锋第3期常减压蒸馏装置的“三环节”用能分析55Loss疔ompumpHeatlossLoss仔omfuelgaSHeatlossProcessconsumptionOutputene唱yHeatlossCoolingUnit:MJ/tLossf如mpumpHeatlossLossfbmfuelgasEXergylossProcessconsumptionExe鼢7lOssOutputexe唱yCoolingExe唱ylOssUnit:MJ/tL一…………一…一一一…一…一一.…一一一.J图1装置能流图F唔.1Unitenergyflow图2装置I朋流图F蟾.2Unitexergynow第3期常减压蒸馏装置的“三环节”用能分析573.3能量回收环节的分析(1)由于换热网络采用夹点技术进行了优化,并且采用了部分内波纹外螺纹高效换热器,强化了传热,不仅降低了回收环节的冷却负荷,而且优化了高温/低温物流的匹配,提高了炯效率。
由表1可见,装置的能量回收利用率为77.14%,炯回收利用率为61.39%,能量和炯的回收利用率都较高。
(2)在待回收的能量中,物流冷却排弃的能量最多,约占18%,但除常二线、减二线和减压渣油的冷却排弃温度较高(分别为163、123和153℃)外,其它侧线产品的冷却排弃温度都在100℃以下,失去了回收利用的价值。
(3)回收过程的不可逆炯损失为主要炯损,约占待回收炯的26%,这部分炯损主要是由高温/f氐温物流换热产生的不可逆炯损,是不可避免的。
由以上分析可知,装置回收环节的能量和炯利用基本实现了优化,可进一步节能的主要方向是回收利用常二线、减二线和减压渣油的余热,降低冷却排弃能。
4结束语(1)过程系统三环节能量结构,将过程用能科学地划分为转换、利用和回收3个环节,为过程系统的节能分析提供了理论模型,有利于对过程系统的用能状况进行全面、科学的计算和分析。
(2)炼油过程的用能分析应综合考虑能量平衡和炯平衡,在降低能量损失的同时,也应注重提高能量的炯利用率,从量和质两方面共同提高炼油装置用能水平。
(3)笔者所列举的常减压装置,其能量和炯的利用率和回收率已达到较高水平,进一步节能的方向是降低某些物流的冷却、排弃能。
参考文献[1]侯祥麟.中国炼油技术[M].北京:中国石化出版社,2001.655—663.[2]冯霄,李勤凌.化工节能原理与技术[M].北京:化学工业出版社,1998.7—10.[3]华贲.工艺过程用能分析及综合[M].北京:中国石化出版社,1989.13—15.[4]李有润.过程系统节能技术[M].北京:中国石化出版社,2001.24—49.[5]S眈600—92,石油化工企业能量平衡方法[S].[6]北京石油设计院.石油化工工艺计算图表[M].北京:烃加工出版社,1985.107—110作者简介:李志强(1940一),男,教授级高级工程师,从事炼油工程设计研究;侯凯锋(1972一),男,工程师,博士,从事化工系统工程及炼油工程设计研究;严淳(1936一),女,高级工程师,从事炼油工艺设计研究。
常减压蒸馏装置的"三环节"用能分析作者:李志强, 侯凯锋, 严淳作者单位:中国石化工程建设公司,北京,100011刊名:石油学报(石油加工)英文刊名:ACTA PETROLEI SINICA(PETROLEUM PROCESSING SECTION)年,卷(期):2003,19(3)引用次数:2次1.侯祥麟中国炼油技术 20012.冯霄.李勤凌化工节能原理与技术 19983.华贲工艺过程用能分析及综合 19894.李有润过程系统节能技术 20015.SH 2600-1992.石油化工企业能量平衡方法6.北京石油设计院石油化工工艺计算图表 19851.期刊论文胡玉臣.Hu Yuchen常减压蒸馏与催化裂化联合装置接口控制方案的优化设计-石油化工自动化2007(4)联合装置间接口的设计,不是一个新的概念,但是一直没有引起设计人员的足够重视,给现场操作,特别是装置开停工操作造成了很多不便,也造成了大量的能源浪费.根据设计经验,结合生产实际,详细论述了常减压蒸馏与催化裂化热联合装置接口控制方案的优化设计,对上下游热联合装置的设计和生产操作具有指导意义.2.期刊论文赵莹燃气脉冲射流吹灰系统在加热炉上的应用-节能与环保2005(11)介绍燃气脉冲射流吹灰系统的构成、工作原理、安装操作及其在辽河石化分公司南常减压蒸馏装置的应用情况.实际应用表明,该系统有很好的吹灰效果,能够有效提高加热效率,达到了节能耗的目的.3.学位论文王芳常减压装置灵活加工换热网络的优化设计2004在实际生产过程中,原油供应具有一定的不确定性,不同阶段供应的原油性质很可能具有明显差异.由于加工流程(特别是换热网络流程)的限制,一般一套常减压装置只能加工一种或几种性质相近的掺炼原油.因此研究如何通过换热流程的优化设计以提高常减压装置的加工灵活性,具有重大的现实意义.该文围绕这一主题,基于一工程实例:某常减压车间正常情况下加工高硫高酸重质原油(以下简称为高硫高酸原油),但在其他常减压车间大检修期间,为保证其他工段的原料供应,需改为加工沙特阿拉伯轻质原油(以下简称为沙轻原油),本着"以加工高硫高酸原油为主,兼顾加工沙轻原油"的原则,主要开展了以下工作:1.过对已有换热网络优化技术的分析总结和长期实践摸索,提出了常减压装置灵活加工不同种原油时换热网络优化设计的分层研究策略,针对研究策略的不同层次,借助相应的软件和技术进行换热网络的优化研究.2.依据提出的研究策略,通过各工况的过程模拟、换热网络的最优合成、最优分析、模拟以及换热器优化设计与核算等工作,分别对年加工300万吨高硫高酸原油和年加工200万吨沙轻原油两种工况的换热网络作了相应研究,提出了切实可行的改造方案,各工况间只需通过简单切换就可实现装置灵活加工两种原油的能力.3.所得方案改造工程量小,基本上维持了装置现状,现有设备全部利旧,只需新增换热器5台,新增换热面积1,825m2.两种工况下原油换后终温均显著提高,高硫高酸原油换后终温可达31 5℃,沙轻原油换后终温可达300℃.4.期刊论文池琳.严錞.Chi Lin.Yan Chun千万吨级常减压蒸馏装置换热网络的优化设计-石油化工设计2008,25(4)分析了10Mt/a常减压蒸馏装置换热网络的设计实例,介绍了大型化装置换热网络的设计经验,提出了通过优化换热网络来提高装置的用能水平和挖掘节能潜力以达到降低常减压蒸馏装置能耗的目的.5.期刊论文杨鸿剑.封子文.丁智刚.王海生.林浩.地木拉提夹点节能及其换热网络综合应用探讨-新疆石油学院学报2004,16(4)换热网络的优化设计一直是化工系统工程最活跃的研究领域.阐述了夹点技术工程设计的基本原理、工程要求与热力学分析方法,并对某常减压蒸馏装置换热网络进行优化设计,结果表明换热网络的热回收率得到显著提高,达到较好的节能效果.6.会议论文戴厚良.侯凯锋.严(錞)能量"三环节"理论在装置扩能改造中的应用2002扬子石化公司炼油厂第一套常减压蒸馏装置扩散改造中,使用了多项节能技术以实现能量的优化利用.本文以标定数据为基础,运用能量"三环节"理论对该装置的用能状况进行了计算和分析,从能量利用角度对装置的扩能改造效果进行了评价,并为装置的进一步优化能量利用提出了相应措施.7.学位论文丁晓明常减压蒸馏装置换热网络的模拟优化2009能源是人类物质活动的基础。