常减压蒸馏装置生产原理
汽油的常减压蒸馏工艺原理

汽油的常减压蒸馏工艺原理
汽油的常减压蒸馏是一种常用的石油精制工艺,通过不同沸点的分馏油对原油进行分离和精制。
其基本原理如下:
1. 原油加热:将原油通过加热设备加热至一定温度,通常为300-400摄氏度,以使其成为可蒸馏的状态。
2. 进行蒸馏:加热后的原油进入常减压蒸馏塔,该塔内部装有多个分馏塔板。
塔内的温度逐渐降低,塔顶部温度最高,塔底部温度最低。
3. 分离:原油在塔内流动时,由于不同组分的沸点不同,各组分会根据其沸点升高的顺序,从塔底部往塔顶部分离出来。
常见的顺序为:重油、柴油、煤沥青、润滑油、重烯烃、轻烯烃、汽油。
4. 收集:在塔顶部装有冷凝器,将由蒸汽转化成液体的组分冷凝收集。
其中,汽油是最轻的组分,最先冷凝,被收集。
5. 分析和调整:收集到的汽油还需要进行化验和调整,以满足不同等级的汽油要求。
包括调整辛烷值、硫含量、加氢处理等。
通过不断的汽油常减压蒸馏工艺,可以从原油中得到高质量的汽油产品,以满足市场对汽油的需求。
常减压蒸馏原理
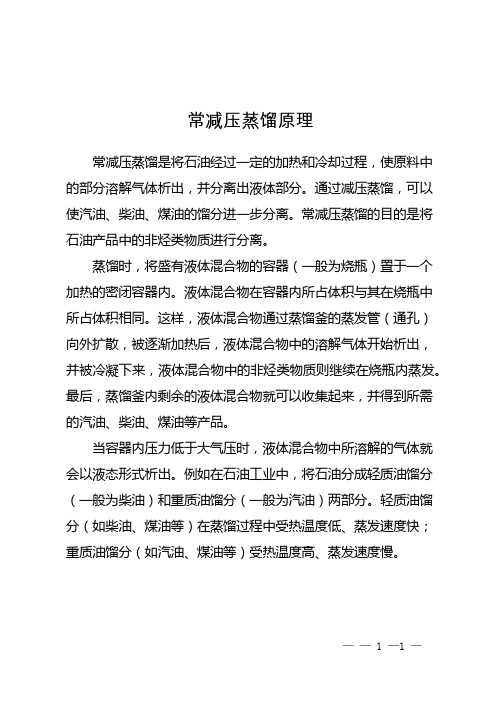
常减压蒸馏原理
常减压蒸馏是将石油经过一定的加热和冷却过程,使原料中的部分溶解气体析出,并分离出液体部分。
通过减压蒸馏,可以使汽油、柴油、煤油的馏分进一步分离。
常减压蒸馏的目的是将石油产品中的非烃类物质进行分离。
蒸馏时,将盛有液体混合物的容器(一般为烧瓶)置于一个加热的密闭容器内。
液体混合物在容器内所占体积与其在烧瓶中所占体积相同。
这样,液体混合物通过蒸馏釜的蒸发管(通孔)向外扩散,被逐渐加热后,液体混合物中的溶解气体开始析出,并被冷凝下来,液体混合物中的非烃类物质则继续在烧瓶内蒸发。
最后,蒸馏釜内剩余的液体混合物就可以收集起来,并得到所需的汽油、柴油、煤油等产品。
当容器内压力低于大气压时,液体混合物中所溶解的气体就会以液态形式析出。
例如在石油工业中,将石油分成轻质油馏分(一般为柴油)和重质油馏分(一般为汽油)两部分。
轻质油馏分(如柴油、煤油等)在蒸馏过程中受热温度低、蒸发速度快;重质油馏分(如汽油、煤油等)受热温度高、蒸发速度慢。
—— 1 —1 —。
减压蒸馏装置及原理
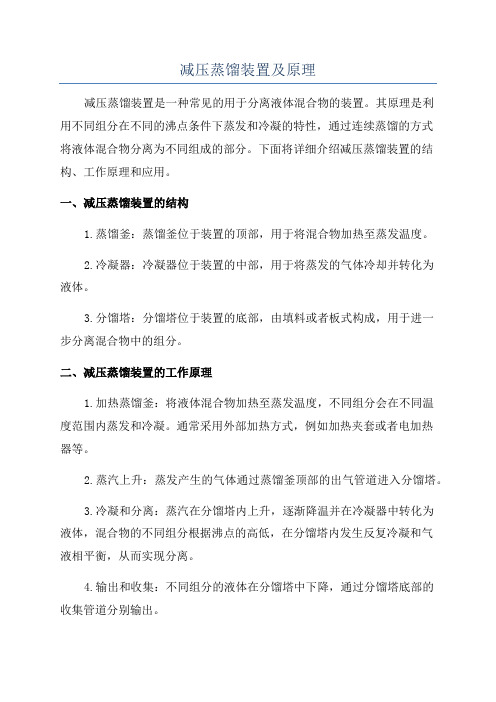
减压蒸馏装置及原理减压蒸馏装置是一种常见的用于分离液体混合物的装置。
其原理是利用不同组分在不同的沸点条件下蒸发和冷凝的特性,通过连续蒸馏的方式将液体混合物分离为不同组成的部分。
下面将详细介绍减压蒸馏装置的结构、工作原理和应用。
一、减压蒸馏装置的结构1.蒸馏釜:蒸馏釜位于装置的顶部,用于将混合物加热至蒸发温度。
2.冷凝器:冷凝器位于装置的中部,用于将蒸发的气体冷却并转化为液体。
3.分馏塔:分馏塔位于装置的底部,由填料或者板式构成,用于进一步分离混合物中的组分。
二、减压蒸馏装置的工作原理1.加热蒸馏釜:将液体混合物加热至蒸发温度,不同组分会在不同温度范围内蒸发和冷凝。
通常采用外部加热方式,例如加热夹套或者电加热器等。
2.蒸汽上升:蒸发产生的气体通过蒸馏釜顶部的出气管道进入分馏塔。
3.冷凝和分离:蒸汽在分馏塔内上升,逐渐降温并在冷凝器中转化为液体,混合物的不同组分根据沸点的高低,在分馏塔内发生反复冷凝和气液相平衡,从而实现分离。
4.输出和收集:不同组分的液体在分馏塔中下降,通过分馏塔底部的收集管道分别输出。
三、减压蒸馏装置的应用1.精馏分离:将石油中的原油分离成不同馏分,例如汽油、柴油、液化石油气等。
2.提纯和制备:例如从发酵液中提取酒精,从天然气中提取液态烃等。
3.去除有害组分:例如从水中去除溶解的有机化合物,从废气中去除有毒气体等。
4.回收和再利用:例如从化工废液中回收有用的溶剂,从废气中回收有价值的组分等。
总结:减压蒸馏装置是用于分离液体混合物的一种常见装置,利用不同组分在不同温度下蒸发和冷凝的特性进行分离。
它的结构主要包括蒸馏釜、冷凝器和分馏塔。
减压蒸馏装置广泛应用于化工、石油和制药等领域,用于精馏分离、提纯制备、去除有害组分和回收再利用等方面。
常减压蒸馏装置技术手册

常减压蒸馏装置技术手册第一部分:常减压蒸馏装置概述1.1 常减压蒸馏装置定义常减压蒸馏装置是一种用于液体混合物分离的设备,它通过控制系统压降,使混合物在低温下分馏,从而实现不同组分的分离和提纯。
1.2 常减压蒸馏装置应用领域常减压蒸馏装置广泛应用于化工、制药、食品加工等领域,用于提取精馏、浓缩和分离各种化工原料、药物和食品添加剂等物质。
1.3 常减压蒸馏装置工作原理常减压蒸馏装置利用液体混合物在不同温度下的沸点差异,通过对系统压力的调节,使得混合物在低温下分馏,从而实现不同组分的分离。
通常采用冷凝器冷却分馏出的混合物,再进行收集和提取。
第二部分:常减压蒸馏装置技术参数2.1 常减压蒸馏装置主要参数- 最大工作压力- 最高工作温度- 分离能力- 设备尺寸- 生产能力- 能耗指标- 自动化程度2.2 常减压蒸馏装置技术指标的选择和设计原则- 根据原料性质、产品要求和生产规模确定最大工作压力和最高工作温度;- 根据产品的要求和生产规模确定分离能力和生产能力;- 根据设备场地和生产条件确定设备尺寸和能耗指标;- 根据自动化程度的要求确定控制系统的设计和配置。
第三部分:常减压蒸馏装置设备组成和工作流程3.1 常减压蒸馏装置设备组成- 蒸馏塔- 冷凝器- 分离器- 冷却系统- 加热系统- 控制系统3.2 常减压蒸馏装置工作流程- 原料进料- 加热蒸发- 分馏分离- 冷凝收集- 产品提取- 废料排放第四部分:常减压蒸馏装置操作与维护4.1 常减压蒸馏装置操作注意事项- 严格按照操作规程进行操作;- 定期检查设备运行状态,及时处理异常情况;- 注意安全防护,防止操作人员伤害和事故发生;- 注意原料和产品的储存和处理。
4.2 常减压蒸馏装置维护保养- 定期检查设备零部件的磨损和损坏情况,及时更换; - 定期清洁设备内部和外部,防止污染和腐蚀;- 定期对设备进行润滑和保养;- 定期进行设备的技术检测和维修。
第五部分:常减压蒸馏装置发展趋势5.1 常减压蒸馏装置技术发展趋势- 高效节能:采用新型节能材料和技术,提高装置的能效比;- 自动化智能:利用先进的控制系统和机器学习算法,实现设备的自动化操作和智能化管理;- 绿色环保:采用环保材料和技术,减少废气排放和资源浪费。
常减压蒸馏原理

常减压蒸馏原理摘要:常压蒸馏是石油加工的“龙头装置”,后续二次加工装置的原料,及产品都是由常减压蒸馏装置提供。
常减压蒸馏主要是通过精馏过程,在常压和减压的条件下,根据各组分相对挥发度的不同,在塔盘上汽液两相进行逆向接触、传质传热,经过多次汽化和多次冷凝,将原油中的汽、煤、柴馏分切割出来,生产合格的汽油、煤油、柴油及蜡油及渣油等。
(1)由此掌握常减压蒸馏原理对于从事相关工作的人员来说显得尤其重要。
本文先从蒸馏的基本概念和原理说起,然后分别对常压蒸馏、减压蒸馏的原理做一个简要介绍。
关键词:蒸馏、基本概念和原理、常压蒸馏、减压蒸馏一、蒸馏的基本概念和原理1、基本概念1.1饱和蒸汽压任何物质(气态、液态和固态)的分子都在不停的运动,都具有向周围挥发逃逸的本领,液体表面的分子由于挥发,由液态变为气态的现象,我们称之为蒸发。
挥发到周围空间的气相分子由于分子间的作用力以及分子与容器壁之间的作用,使一部分气体分子又返回到液体中,这种现象称之为冷凝。
在某一温度下,当液体的挥发量与它的蒸气冷凝量在同一时间内相等时,那么液体与它液面上的蒸气就建立了一种动态平衡,这种动态平衡称为气液相平衡。
当气液相达到平衡时,液面上的蒸气称为饱和蒸汽,而由此蒸气所产生的压力称为饱和蒸汽压,简称为蒸汽压。
蒸气压的高低表明了液体中的分子离开液面气化或蒸发的能力,蒸气压越高,就说明液体越容易气化。
在炼油工艺中,根据油品的蒸气压数据,可以用来计算平衡状态下烃类气相和液相组成,也可以根据蒸气压进行烃类及其混合物在不同压力下的沸点换算、计算烃类液化条件等。
1.2气液相平衡处于密闭容器中的液体,在一定温度和压力下,当从液面挥发到空间的分子数目与同一时间内从空间返回液体的分子数目相等时,就与液面上的蒸气建立了一种动态平衡,称为气液平衡。
气液平衡是两相传质的极限状态。
气液两相不平衡到平衡的原理,是气化和冷凝、吸收和解吸过程的基础。
例如,蒸馏的最基本过程,就是气液两相充分接触,通过两相组分浓度差和温度差进行传质传热,使系统趋近于动平衡,这样,经过塔板多级接触,就能达到混合物组分的最大限度分离。
减压蒸馏装置原理
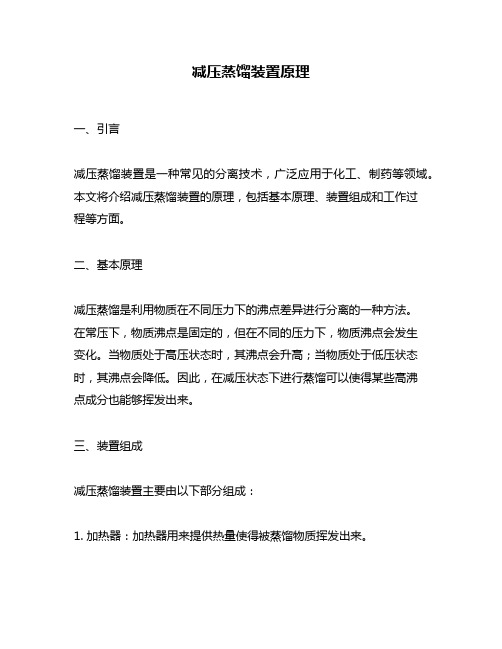
减压蒸馏装置原理一、引言减压蒸馏装置是一种常见的分离技术,广泛应用于化工、制药等领域。
本文将介绍减压蒸馏装置的原理,包括基本原理、装置组成和工作过程等方面。
二、基本原理减压蒸馏是利用物质在不同压力下的沸点差异进行分离的一种方法。
在常压下,物质沸点是固定的,但在不同的压力下,物质沸点会发生变化。
当物质处于高压状态时,其沸点会升高;当物质处于低压状态时,其沸点会降低。
因此,在减压状态下进行蒸馏可以使得某些高沸点成分也能够挥发出来。
三、装置组成减压蒸馏装置主要由以下部分组成:1. 加热器:加热器用来提供热量使得被蒸馏物质挥发出来。
2. 蒸发器:蒸发器是被蒸馏物质所在的容器,在加热作用下被蒸馏物质挥发出来。
3. 冷凝器:冷凝器是将蒸发出来的物质冷却成液体的设备,通常使用水进行冷却。
4. 减压系统:减压系统包括真空泵、减压计等设备,用于控制蒸发器内部的压力。
5. 收集瓶:收集瓶用于收集分离出来的物质。
四、工作过程减压蒸馏装置的工作过程如下:1. 将被蒸馏物质加入到蒸发器中,并关闭密封盖。
2. 开启加热器,提供热量使得被蒸馏物质挥发出来。
3. 开启真空泵,将蒸发器内部的气体抽出,降低内部压力。
4. 被蒸馏物质在低压状态下挥发出来,并进入冷凝器进行冷却。
5. 冷却后的液体流入收集瓶中,分离出所需物质。
6. 根据需要调整真空泵等设备以控制内部压力和温度,以达到最佳分离效果。
五、总结本文介绍了减压蒸馏装置的基本原理、装置组成和工作过程等方面。
减压蒸馏是一种常见的分离技术,可以用于分离高沸点成分或者提高某些物质的纯度。
在实际应用中,需要根据具体情况调整设备参数以达到最佳效果。
常减压装置的原理
常减压装置的原理常减压装置是一种常用的安全阀装置,广泛应用于各种工业设备和系统中,旨在控制和调节系统内部的压力,以确保设备运行的安全性和稳定性。
本文将介绍常减压装置的原理及其在工业领域中的应用。
一、常减压装置的原理常减压装置是一种通过调节介质流体的流量来实现压力调节的装置。
它的原理基于流体动力学和泄压原理。
1. 流体动力学原理常减压装置中的介质流体在流动过程中,会受到管道或设备内部的阻力和摩擦力的影响,形成压力损失。
根据伯努利方程,流体在管道中的速度增加,压力将会降低。
常减压装置通过合理设计流道和缩径的方式,增加介质的流速,从而降低系统的压力。
2. 泄压原理常减压装置中的泄压机构是实现压力调节的关键部件。
它通常由弹簧、活塞、阀芯等组成。
当系统内部的压力超过设定的压力值时,泄压机构会自动打开,释放部分介质流体,从而降低系统的压力。
当压力下降到设定范围内时,泄压机构会关闭,保持系统的压力在一定范围内。
二、常减压装置的应用常减压装置广泛应用于各种工业设备和系统中,用于控制和调节系统的压力,保证设备运行的安全性和稳定性。
以下是常减压装置在几个典型应用领域中的具体应用。
1. 石油化工领域在石油化工生产过程中,常减压装置被用于控制和调节各种介质(如气体、液体)的压力。
它可以应用于炼油装置、化工反应器、压缩机、蒸馏塔等设备中,确保这些设备在正常工作压力范围内运行,避免压力过高引发事故。
2. 能源领域在能源领域中,常减压装置被广泛应用于发电厂、锅炉系统等设备中。
它可以控制和调节供水和蒸汽的压力,确保发电设备的安全运行和效率。
3. 化学工程领域在化学工程领域中,常减压装置被用于控制和调节各种化学反应系统中的压力。
通过合理设置常减压装置,可以避免反应系统内部压力过高,导致反应过程失控或发生事故。
4. 汽车制造领域在汽车制造领域中,常减压装置常用于汽车发动机和气囊系统中。
它可以根据发动机的工作状态,及时调节发动机内部的压力,提高燃烧效率和动力输出。
常减压蒸馏装置与设备
常减压蒸馏装置与设备简介常减压蒸馏装置与设备是一种用于分离和提纯化工原料的技术装置。
通过控制系统压力,使被蒸馏物质在较低的温度下蒸发,从而达到提纯的目的。
这种装置在石油化工、化学工程、生物工程等领域得到广泛应用。
工作原理常减压蒸馏装置与设备的工作原理基于液体的沸点受压力影响的特性。
在常减压蒸馏装置中,被蒸馏物质首先进入蒸馏塔底部的加热器,通过加热器的加热作用,使被蒸馏物质蒸发。
蒸发的气体从蒸馏塔底部进入蒸馏塔中,与下降的液体相接触,进行传质传热。
蒸馏塔的压力是通过控制系统来实现的,通过减小蒸馏塔压力,降低被蒸馏物质的沸点,从而使其在相对较低的温度下蒸发。
在蒸馏塔顶部设置了冷凝器,冷凝器中通过循环的冷却剂使蒸发的被蒸馏物质重新液化。
液化后的物质被收集,即得到最终纯净的分离物质。
同时,未被蒸发的馏出液通过回流器回流至蒸馏塔中,继续进行分离。
设备组成常减压蒸馏装置与设备主要由以下部分组成:1. 蒸馏塔蒸馏塔是整个装置的核心部分,由塔底、塔体和塔顶三部分组成。
塔底设置有加热器,用于加热被蒸馏物质。
塔体用于传质传热,塔顶设置有冷凝器。
2. 加热器加热器用于将被蒸馏物质加热至蒸发温度。
加热器的加热方式可以根据具体需求选择,常见的有蒸汽加热和电加热两种方式。
3. 冷凝器冷凝器用于将蒸发的被蒸馏物质重新液化。
冷凝器中通过循环的冷却剂使蒸发物质得到冷凝。
冷凝后的物质被收集,即得到纯净的分离物质。
4. 控制系统控制系统用于控制整个装置的压力和温度。
通过调节蒸馏塔内部的压力,以及加热器的加热功率,达到控制蒸馏过程的目的。
5. 回流器回流器将未被蒸发的馏出液回流至蒸馏塔中,继续进行分离。
回流器的设计和操作对装置的分离效果有着重要影响。
应用领域常减压蒸馏装置与设备在石油化工、化学工程、生物工程等领域得到广泛应用。
它可以用于提纯石油化工原料中的杂质,制备高纯度的化工产品。
在药物合成过程中,可用于去除不纯物质,提高产品的纯度。
炼油厂常减压蒸馏装置生产原理 ppt课件
2007年8月23日
炼油厂常减压蒸馏装置生产原理
工艺原理及概述 工艺流程简介 原料来源及产品走向 装置的技术改造 装置的能量消耗 装置的物料平衡 常减压装置的技术发展方向 装置生产受控管理开展情况
二套常减压工艺简介
2
炼油厂常减压蒸馏装置生产原理
常减压蒸馏是原油加工的第一道工序 装置是根据原油中各组份的沸点(挥发度)不同用加热的方
二套常减压工艺简介
4
炼油厂常减压蒸馏装置生产原理
装置主要有以下几部分组成 电脱盐系统 初馏和常压系统 航煤脱硫醇系统 减压分馏系统 水除氧及蒸汽发生系统 加热炉烟气余热回收系统。
二套常减压工艺简介
5
炼油厂常减压蒸馏装置生产原理
原油电脱盐就是在一定温度下,破乳剂,注水、混合、电场 等因素综合作用下,原油中小水滴聚结成大水滴,靠油水密 度差而将原油中水和溶解在其中的盐同时分离的过程。
的分离,以减少雾沫夹带。 进料段以下为汽提段直径Φ3.5米 汽提段以下为抽出斗直径Φ2.8米以尽量减少渣油在高温区的
停留时间,减少裂解的不凝气数量。
二套常减压工艺简介
13
炼油厂常减压蒸馏装置生产原理
采用减一中段回流及 减四线、减五线做热源发生压力为 1.0MPa的蒸汽。经加热炉(炉-2)过热到250℃ 供本装置真空喷射器和加热炉燃料油雾化用 不足由装置外补给
抽出,经过四路换热到304℃左右后,被常压炉加 热到370 ℃左右出来进入常压塔第四层上方,经过
常压塔精馏后,塔顶油汽经过冷凝冷却后的汽油一 部分打入塔顶,一部分作为常顶汽油出装置,不凝 气到常压炉烧掉。然后从上到下侧线依次馏出常一 线、常二线、常三线,常四线直接被抽出。
二套常减压工艺简介
常减压蒸馏原理范文
常减压蒸馏原理范文
常减压蒸馏的工作原理是将原油通过加热器加热到一定温度,然后进
入蒸馏塔。
蒸馏塔内部按照升温逐层设有一系列馏分收集装置,每个层次
都有不同的设计压力和温度。
在这些收集装置中,原油会逐渐冷却并蒸发,生成上游收集装置中的较轻石油组分和下游收集装置中的较重石油组分。
常减压蒸馏的原理是通过降低操作压力,从而降低蒸发石油组分的沸点,实现沸点范围内的组分分离。
在蒸馏塔中,通过不同层次的加热和冷却,使得原油在塔内的温度和压力逐渐升高。
当原油进入蒸馏塔顶部的高
温区域时,由于蒸发温度已经高于原油的沸点,顶部会产生大量的轻质组
分蒸气。
这些蒸气通过冷凝回流器冷却成液体,进一步分离出来。
在蒸馏塔内,不同组分的沸点差异会导致油品分离。
较轻组分会向着
高温和低压的方向流动,而较重组分则相对停留在靠近塔底部的较低温度
和高压区域。
常减压蒸馏中的较重组分可以直接用作燃料油,而较轻组分
则可用于提取液化石油气或进行进一步处理。
常减压蒸馏的原理基于分子间的吸引力和相互作用力。
不同组分的沸
点与其分子量、分子间的吸引力以及相互作用力有关。
分子量较小、相互
作用力较弱的组分,往往具有较低的沸点;而分子量较大、相互作用力较
强的组分,沸点则较高。
总结来说,常减压蒸馏是通过控制操作压力和温度,利用不同石油组
分的沸点差异,在蒸馏塔内实现组分的分离。
该工艺的原理基于分子间相
互作用力和分子量的差异。
常减压蒸馏是一种常用的工艺,广泛应用于石
油行业中的石油分离和提纯。
- 1、下载文档前请自行甄别文档内容的完整性,平台不提供额外的编辑、内容补充、找答案等附加服务。
- 2、"仅部分预览"的文档,不可在线预览部分如存在完整性等问题,可反馈申请退款(可完整预览的文档不适用该条件!)。
- 3、如文档侵犯您的权益,请联系客服反馈,我们会尽快为您处理(人工客服工作时间:9:00-18:30)。
3.0KPa。
二套常减压工艺简介
3
工艺原理及概述装置概况
本装置是由中国石化总公司北京设计院设计 设计能力为每年加工350万吨大庆原油,年开工时间
为8000小时。 装置为润滑油型常减压蒸馏装置 全装置共有设备232台,占地面积17100m2 1989年4月破土动工,于1991年7月投产 装置生产常一线做为航空煤油要求符合3号航煤标准
抽出,经过四路换热到304℃左右后,被常压炉加 热到370 ℃左右出来进入常压塔第四层上方,经过
常压塔精馏后,塔顶油汽经过冷凝冷却后的汽油一 部分打入塔顶,一部分作为常顶汽油出装置,不凝 气到常压炉烧掉。然后从上到下侧线依次馏出常一 线、常二线、常三线,常四线直接被抽出。
二套常减压工艺简介
7
装置流程程简介电脱盐系统概述
设计电脱盐温度定为120℃,注水量为5%(占原油),注入
破乳剂的浓度-2%,注入量20ppm (占原油),为了降低能
耗,装置采用容-6脱水作为部分电脱盐注水,今年还尝试使 用硫磺酸性水代替除盐水作为电脱盐注水,并且能够保证脱 后含盐在5mg/l以下。
采用常一中段回流做热源发生压力为0.4MPa的蒸汽 经过加热炉(炉-2)过热到≮360℃ 各塔供汽提用 不足由装置外补充供给
本装置发生蒸汽所需的除氧水,在本装置内自设除氧站。
二套常减压工艺简介
二套常减压工艺简介
10
工艺流程简介航煤脱硫醇系统概述
装置生产的航煤馏分按3号航煤规格设计 航煤馏分硫醇性硫含量在12-20ppm之间,因此需要经过脱硫
醇工序 装置采用国内已成熟的13X铜分子筛氧化脱硫醇工艺 航煤馏分温度130℃、空速为3时-1下,通入少量空气进行氧
化脱硫醇 为使产品消光值达到要求,还需经过脱色罐脱色(罐内装有
其中常压塔设有一个顶回流,两个中段回流(常一中、 常二中),常底油经过泵-3/1.2 抽出到减压炉加热到
395℃左右后进入减压塔第四层上方,减压塔底吹入蒸
汽。减顶设有两级抽真空系统,减顶油汽经过一级予冷 器和一级抽空器和二级予冷器及二级抽空器,不凝气到 常压炉烧掉,冷却下来的油水经减顶油水分液罐(容-6) 分出的油经泵送出装置,减压塔沿塔壁至上而下依次馏 出减一线、减二线、减三线、减四线、减五线,各侧线 (除减五线)经过气提塔在由各泵抽出到各换热器进行 换热,冷却最后送出装置,减压塔经过泵-21/1.2 抽出。 经过两路换热,一部分热料去重催、焦化,另一部分经 过冷却做冷渣送出装置。
二套常减压装置工艺简介
大庆石化公司炼油厂常减压二车间 2007年8月23日
主要内容
工艺原理及概述 工艺流程简介 原料来源及产品走向 装置的技术改造 装置的能量消耗 装置的物料平衡 常减压装置的技术发展方向 装置生产受控管理开展情况
二套常减压工艺简介
2
工艺原理及概述工艺原理
二套常减压工艺简介
9
工艺流程简介初馏、常压分馏系统概述
初馏塔直径Φ3.2米,内装18层浮阀塔盘,开有一个侧线 初馏塔抽出4%(占原油)直接送入常压塔,可以减少常压炉
的热负荷 常压塔直径上部为Φ3.8米,下部为Φ4.8米,内装47层浮阀塔
盘,及一个供常二中换热的填料段 常二中取热段采用环矩鞍和隔栅填料解决
由于大庆原油含盐量较低,本装置采用了一级电脱盐,但是 随着原油的逐渐重质化、劣质化,原油脱前含盐量已经是设 计值的一倍 。
二套常减压工艺简介
6
装置流程概述
原油泵-1/1.2 抽87单元11#、12#罐的原油,到装置 内经过两路换热,到电脱盐罐经过脱盐,脱后原油 从容-1出来经过四路换热后进入塔-1,经过闪蒸, 塔-1顶出重整料,不凝气经换-52加热后去原油稳定, 当原油稳定停工时去炉-1烧掉。塔-1 底油经泵-2/1.2
二套常减压工艺简介
4
工艺流程简介装置组成部分
装置主要有以下几部分组成 电脱盐系统 初馏和常压系统 航煤脱硫醇系统 减压分馏系统 水除氧及蒸汽发生系统 加热炉烟气余热回收系统。
二套常减压工艺简介
5
工艺流程简介电脱盐原理
原油电脱盐就是在一定温度下,破乳剂,注水、混合、电场 等因素综合作用下,原油中小水滴聚结成大水滴,靠油水密 度差而将原油中水和溶解在其中的盐同时分离的过程。
常减压蒸馏是原油加工的第一道工序 装置是根据原油中各组份的沸点(挥发度)不同用加热的方
法从原油中分离出各种石油馏份
常压蒸馏蒸馏出低沸点的汽油、煤油、柴油等组份 常压渣油在避免裂解的较低温度下进行分馏,分离出润滑油
料、催化料等二次加工原料,剩下减压渣油。
本装置的减压塔,经过两次大型的改造,现在为全填料减压 塔,塔顶采用预冷凝和两级蒸汽喷射器抽真空,全塔压降
的分离,以减少雾沫夹带。 进料段以下为汽提段直径Φ3.5米 汽提段以下为抽出斗直径Φ2.8米以尽量减少渣油在高温区的
停留时间,减少裂解的不凝气数量。
二套常减压工艺简介
13
工艺流程简介蒸汽发生及水除氧系统概述
采用减一中段回流及 减四线、减五线做热源发生压力为 1.0MPa的蒸汽。经加热炉(炉-2)过热到250℃ 供本装置真空喷射器和加热炉燃料油雾化用 不足由装置外补给
侧线(减二、减三、减四)
二套常减压工艺简介
12
工艺流程简介减压分馏系统概述
为了确保减压四线油质量,在进料段和减四线抽出层之间, 设有一个净洗段,用净洗段流下的内回流做洗涤油,冷凝下 的油作为减五线抽出,送去作催化裂化原料。
进料段处塔径放大到10米以进一步降低空速 在进料处的塔内部设有水平敷设的环型导流板,使汽液顺利
活性炭) 产品经玻璃毛过滤器和陶瓷过滤器过滤之后送出装置。
二套常减压工艺简介
11
工艺流程简介减压分馏系统概述
本装置的减压塔,是按湿式操作设计,在塔底通入水蒸汽以 降低油气分压,塔顶真空度控制不小于93.5kpa
塔顶部油气冷凝段直径为5.0米,内部装有2米高环矩鞍填 油气冷凝段以下是分馏段,直径Φ8.2米,抽出三个润滑油料