常减压蒸馏装置生产原理
减压蒸馏装置及原理
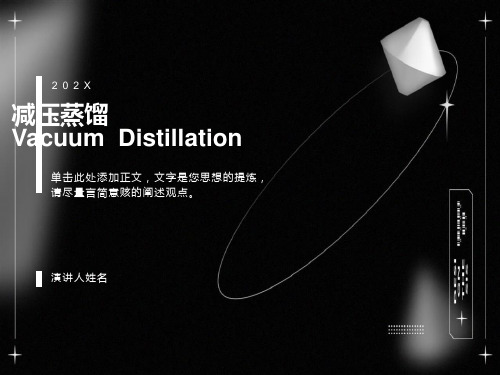
主要试剂的物理常数
乙酰乙酸乙酯 (CH3COCH2COOC2H5) b.p. 180.4℃ nD20 1.4192
四、装置图
克氏
蒸馏头
五、实验操作步骤
折射定律
减压蒸馏装置的密闭性
烧瓶中被提纯物的加入量:50mL烧瓶,20mL样品
二通活塞打开和关闭的时间
2、减压下的沸点 (1)通常液体的沸点是指其表面的蒸气压等于外界大气压时 的温度; (2)液体沸腾时温度是与外界的压力相关的,即外界压力降 低沸点也降低; (3)利用外界压力和液体沸点之间的关系,将液体置于一可 减压的装置中,随体系压力的减小,液体沸腾的温度即 可降低,这种在较低压力下进行蒸馏的操作被称为减压 蒸馏。
减压蒸馏 Vacuum Distillation
202X
单击此处添加正文,文字是您思想的提炼, 请尽量言简意赅的阐述观点。
演讲人姓名
实验目的与要求
掌握减压蒸馏的原理
学会减压蒸馏的规范操作
学会用经验曲线估算被提纯物的沸点
二、实验原理
1、减压蒸馏适用对象 在常压蒸馏时未达沸点即已受热分解、氧化或聚合的物质
3、减压下沸点的估算 (1)经验曲线 (2)近似计算
欲观察沸点
标准大气压时沸点
压力(真空度)
真空度
举例:已知被提纯物在标准大气压下的沸点为180℃, 计算在体系的压力为-0.095MPa时,该物质的近似沸点。
1、换算单位
2、计算真空度
3、用经验曲线查找近似沸点
约为90℃
毛细管上夹子的松紧
整个操作的先后顺序
停止操作的顺序
比较估算值和观察值的差别
记录有关产物的所有原始数据,计算回收率
六、注意
常减压蒸馏装置简述
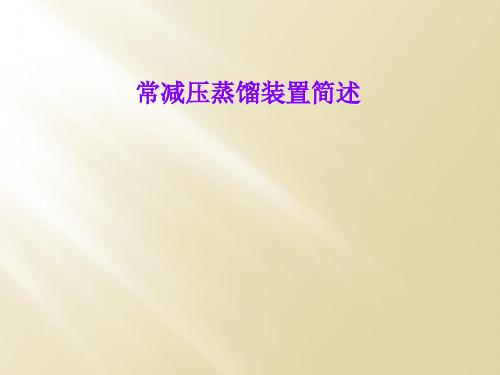
硫在原油馏分中分布一般是随馏分沸程的升高而增加, 大部分的硫集中在重馏分和渣油中。
直馏轻组分中有机硫有硫醇、硫醚以及少量二硫化物 和噻吩,硫醇硫含量占其总硫含量的40%~50%。中 间馏分中主要是硫醚类和噻吩类。
装置的原料(原油)
原油中的氧元素都是以有机化合物的形式存在。 可分为酸性氧化物和中性氧化物。酸性氧化物 包括环烷酸、芳香酸、脂肪酸以及酚类,总称 石油酸。
但世界各地所产原油从外观到性质都有不同程 度的差异。绝大多数原油都是黑色的,但也有 暗黑、暗绿、暗褐色的 。
从凝点来看有很大差异,我国沈北混合原油高 达54℃,而新疆克拉玛依原油则低于-50℃。
装置的原料(原油)
组成原油的主要元素是碳、氢、硫、氮、氧, 其中碳的含量占83.0%~87.0%,氢含量占 11.0%~14.0%,两者合计达95%以上。
装置的产品
我国车用汽油质量标准规定了10%馏出温度不 高于70℃。
我国车用汽油质量标准规定了50%馏出温度不 高于120℃。
我国车用汽油质量标准规定了90%馏出温度不 高于190℃。
我国车用汽油质量标准规定了终馏点馏出温度 不高于205℃。
装置的产品
常减压蒸馏装置能控制喷气燃料的馏程、密度、 冰点、结晶点等性质。
中间馏分如在煤油、柴油馏分中含的C11~C20的正异 构烷烃、带侧链的单环环烷烃、双环及三环环烷烃、 双环芳烃、环烷-芳香的混合烃。
高沸点馏分如润滑油馏分中含C20~C36的正异构烷 烃、环烷烃和芳香烃。环烷烃主要以稠环类为主。
装置的原料(原油)
硫在原油中的存在形态已经确定的有:单质硫、硫化 氢及硫醇、硫醚、二硫化物、噻吩等类型的有机含硫 化合物,此外还有其它类型。
常减压蒸馏原理
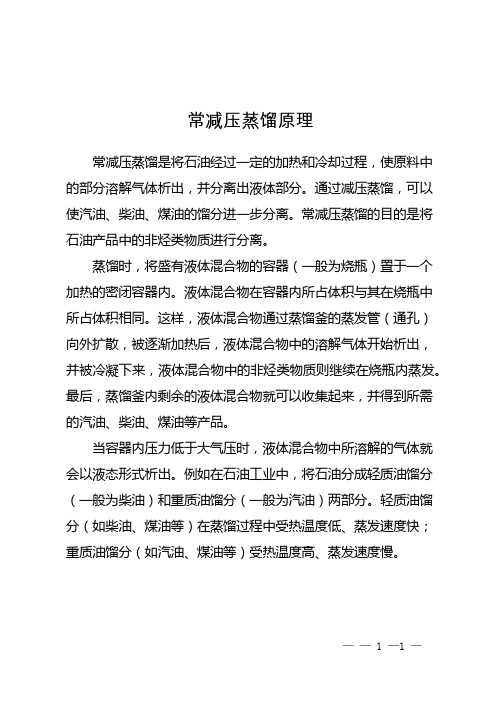
常减压蒸馏原理
常减压蒸馏是将石油经过一定的加热和冷却过程,使原料中的部分溶解气体析出,并分离出液体部分。
通过减压蒸馏,可以使汽油、柴油、煤油的馏分进一步分离。
常减压蒸馏的目的是将石油产品中的非烃类物质进行分离。
蒸馏时,将盛有液体混合物的容器(一般为烧瓶)置于一个加热的密闭容器内。
液体混合物在容器内所占体积与其在烧瓶中所占体积相同。
这样,液体混合物通过蒸馏釜的蒸发管(通孔)向外扩散,被逐渐加热后,液体混合物中的溶解气体开始析出,并被冷凝下来,液体混合物中的非烃类物质则继续在烧瓶内蒸发。
最后,蒸馏釜内剩余的液体混合物就可以收集起来,并得到所需的汽油、柴油、煤油等产品。
当容器内压力低于大气压时,液体混合物中所溶解的气体就会以液态形式析出。
例如在石油工业中,将石油分成轻质油馏分(一般为柴油)和重质油馏分(一般为汽油)两部分。
轻质油馏分(如柴油、煤油等)在蒸馏过程中受热温度低、蒸发速度快;重质油馏分(如汽油、煤油等)受热温度高、蒸发速度慢。
—— 1 —1 —。
减压蒸馏装置及原理
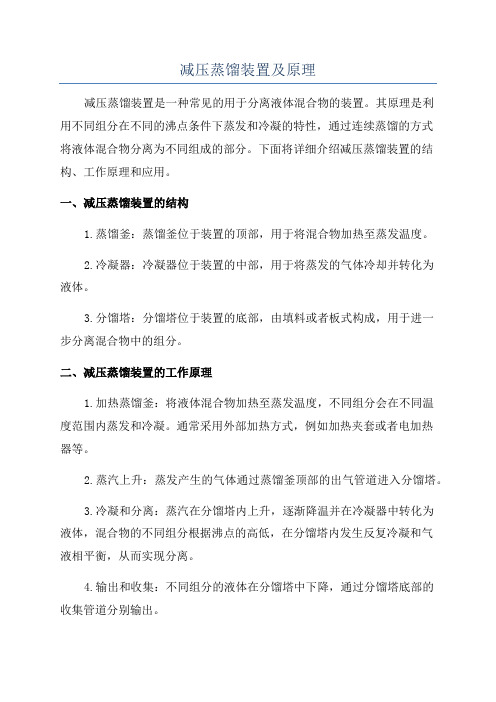
减压蒸馏装置及原理减压蒸馏装置是一种常见的用于分离液体混合物的装置。
其原理是利用不同组分在不同的沸点条件下蒸发和冷凝的特性,通过连续蒸馏的方式将液体混合物分离为不同组成的部分。
下面将详细介绍减压蒸馏装置的结构、工作原理和应用。
一、减压蒸馏装置的结构1.蒸馏釜:蒸馏釜位于装置的顶部,用于将混合物加热至蒸发温度。
2.冷凝器:冷凝器位于装置的中部,用于将蒸发的气体冷却并转化为液体。
3.分馏塔:分馏塔位于装置的底部,由填料或者板式构成,用于进一步分离混合物中的组分。
二、减压蒸馏装置的工作原理1.加热蒸馏釜:将液体混合物加热至蒸发温度,不同组分会在不同温度范围内蒸发和冷凝。
通常采用外部加热方式,例如加热夹套或者电加热器等。
2.蒸汽上升:蒸发产生的气体通过蒸馏釜顶部的出气管道进入分馏塔。
3.冷凝和分离:蒸汽在分馏塔内上升,逐渐降温并在冷凝器中转化为液体,混合物的不同组分根据沸点的高低,在分馏塔内发生反复冷凝和气液相平衡,从而实现分离。
4.输出和收集:不同组分的液体在分馏塔中下降,通过分馏塔底部的收集管道分别输出。
三、减压蒸馏装置的应用1.精馏分离:将石油中的原油分离成不同馏分,例如汽油、柴油、液化石油气等。
2.提纯和制备:例如从发酵液中提取酒精,从天然气中提取液态烃等。
3.去除有害组分:例如从水中去除溶解的有机化合物,从废气中去除有毒气体等。
4.回收和再利用:例如从化工废液中回收有用的溶剂,从废气中回收有价值的组分等。
总结:减压蒸馏装置是用于分离液体混合物的一种常见装置,利用不同组分在不同温度下蒸发和冷凝的特性进行分离。
它的结构主要包括蒸馏釜、冷凝器和分馏塔。
减压蒸馏装置广泛应用于化工、石油和制药等领域,用于精馏分离、提纯制备、去除有害组分和回收再利用等方面。
常减压蒸馏装置常见原料故障分析及处理方法

一、常减压蒸馏装置1.装置简介兰州石化公司550万吨/年常减压装置由中国石化工程建设公司设计,于2009年11月建成投用。
该装置为燃料型常减压装置,以南疆原油、北疆原油、吐哈原油为原料,设计年加工能力为550万吨,年开工时间为8400小时。
装置由电脱盐系统、换热网络系统、常压系统、减压系统、轻烃回收系统、液化气及减顶气的脱硫化氢系统等组成,采用DCS控制。
2.工艺原理常减压蒸馏是在常压状态下和负压状态下,根据原油中各组分的沸点不同,将原油切割成不同馏份。
常减压蒸馏是炼油厂加工原油的第一个工序,常被称之为“龙头”装置。
一般来说,原油经常减压装置加工后,可得到直馏汽油,航空煤油,灯用煤油,轻,重柴油和燃料油等产品,因此,常减压蒸馏装置的生产操作,直接影响着下游二次加工装置和全厂的生产状况。
二、装置出现故障及解决方案1.原油带水故障及处理原油带水的现象:电脱盐跳闸,DCS画面电流电压报警响,脱盐电流指示为零;初馏塔顶压力和塔顶回流罐界位升高,排水量增大;换热器原油压力增大,原油量下降,原油换后温度下降;塔顶回流量增加,塔顶,侧线因雾沫夹带干点变高;严重带水时,使换热器憋压而泄漏,初馏塔顶安全阀跳闸,造成初馏塔冲油,塔底泵抽空等。
原因:原油罐切水不好或者沉降时间短;原油性质不好含水高;有回炼污油时可能带水量大。
解决方案:(1)若是原油带水严重,要切换原油罐,原油停止注水,将脱盐罐的水位放到最低现场开副线加大脱盐罐排水量,并加大破乳剂的注入量。
(2)若是脱盐水位高引起的跳闸,则停止注将脱盐罐水位放到最低,及时送上电。
(3)降低处理量,保证换热器与初馏塔塔压不要超高。
(4)适当提高初馏塔顶温度,停初侧线抽出,不影响常压系统。
(5)注意初顶回流罐界位,加强切水,严防界位过高,回流带水。
(6)初馏塔顶出重整料或者乙烯原料时,可将油品转入不合格汽油罐,当原油水分下降后,再恢复正常。
(7)若原油带水十分严重时,应及时降量,降温熄火改循环,停止塔底汽提,做到不超温,不超压,安全环保受控,待带水好转后再逐步恢复正常操作。
常减压蒸馏原理

常减压蒸馏原理摘要:常压蒸馏是石油加工的“龙头装置”,后续二次加工装置的原料,及产品都是由常减压蒸馏装置提供。
常减压蒸馏主要是通过精馏过程,在常压和减压的条件下,根据各组分相对挥发度的不同,在塔盘上汽液两相进行逆向接触、传质传热,经过多次汽化和多次冷凝,将原油中的汽、煤、柴馏分切割出来,生产合格的汽油、煤油、柴油及蜡油及渣油等。
(1)由此掌握常减压蒸馏原理对于从事相关工作的人员来说显得尤其重要。
本文先从蒸馏的基本概念和原理说起,然后分别对常压蒸馏、减压蒸馏的原理做一个简要介绍。
关键词:蒸馏、基本概念和原理、常压蒸馏、减压蒸馏一、蒸馏的基本概念和原理1、基本概念1.1饱和蒸汽压任何物质(气态、液态和固态)的分子都在不停的运动,都具有向周围挥发逃逸的本领,液体表面的分子由于挥发,由液态变为气态的现象,我们称之为蒸发。
挥发到周围空间的气相分子由于分子间的作用力以及分子与容器壁之间的作用,使一部分气体分子又返回到液体中,这种现象称之为冷凝。
在某一温度下,当液体的挥发量与它的蒸气冷凝量在同一时间内相等时,那么液体与它液面上的蒸气就建立了一种动态平衡,这种动态平衡称为气液相平衡。
当气液相达到平衡时,液面上的蒸气称为饱和蒸汽,而由此蒸气所产生的压力称为饱和蒸汽压,简称为蒸汽压。
蒸气压的高低表明了液体中的分子离开液面气化或蒸发的能力,蒸气压越高,就说明液体越容易气化。
在炼油工艺中,根据油品的蒸气压数据,可以用来计算平衡状态下烃类气相和液相组成,也可以根据蒸气压进行烃类及其混合物在不同压力下的沸点换算、计算烃类液化条件等。
1.2气液相平衡处于密闭容器中的液体,在一定温度和压力下,当从液面挥发到空间的分子数目与同一时间内从空间返回液体的分子数目相等时,就与液面上的蒸气建立了一种动态平衡,称为气液平衡。
气液平衡是两相传质的极限状态。
气液两相不平衡到平衡的原理,是气化和冷凝、吸收和解吸过程的基础。
例如,蒸馏的最基本过程,就是气液两相充分接触,通过两相组分浓度差和温度差进行传质传热,使系统趋近于动平衡,这样,经过塔板多级接触,就能达到混合物组分的最大限度分离。
减压蒸馏装置原理
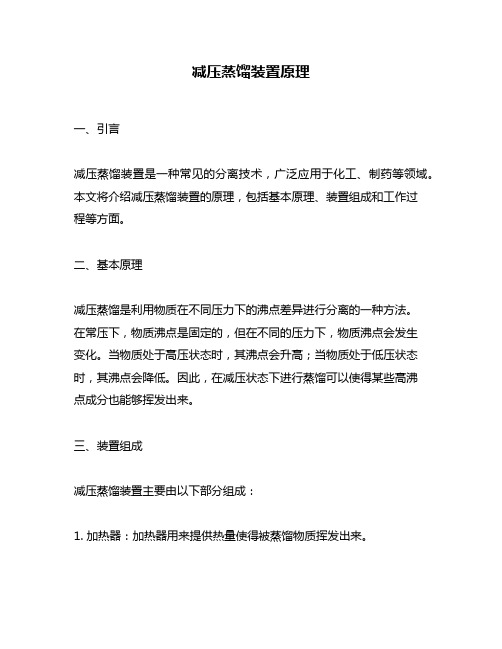
减压蒸馏装置原理一、引言减压蒸馏装置是一种常见的分离技术,广泛应用于化工、制药等领域。
本文将介绍减压蒸馏装置的原理,包括基本原理、装置组成和工作过程等方面。
二、基本原理减压蒸馏是利用物质在不同压力下的沸点差异进行分离的一种方法。
在常压下,物质沸点是固定的,但在不同的压力下,物质沸点会发生变化。
当物质处于高压状态时,其沸点会升高;当物质处于低压状态时,其沸点会降低。
因此,在减压状态下进行蒸馏可以使得某些高沸点成分也能够挥发出来。
三、装置组成减压蒸馏装置主要由以下部分组成:1. 加热器:加热器用来提供热量使得被蒸馏物质挥发出来。
2. 蒸发器:蒸发器是被蒸馏物质所在的容器,在加热作用下被蒸馏物质挥发出来。
3. 冷凝器:冷凝器是将蒸发出来的物质冷却成液体的设备,通常使用水进行冷却。
4. 减压系统:减压系统包括真空泵、减压计等设备,用于控制蒸发器内部的压力。
5. 收集瓶:收集瓶用于收集分离出来的物质。
四、工作过程减压蒸馏装置的工作过程如下:1. 将被蒸馏物质加入到蒸发器中,并关闭密封盖。
2. 开启加热器,提供热量使得被蒸馏物质挥发出来。
3. 开启真空泵,将蒸发器内部的气体抽出,降低内部压力。
4. 被蒸馏物质在低压状态下挥发出来,并进入冷凝器进行冷却。
5. 冷却后的液体流入收集瓶中,分离出所需物质。
6. 根据需要调整真空泵等设备以控制内部压力和温度,以达到最佳分离效果。
五、总结本文介绍了减压蒸馏装置的基本原理、装置组成和工作过程等方面。
减压蒸馏是一种常见的分离技术,可以用于分离高沸点成分或者提高某些物质的纯度。
在实际应用中,需要根据具体情况调整设备参数以达到最佳效果。
常减压蒸馏原理

图 4—1 原油塔示意图 8.石油蒸馏提馏塔采取了哪些不同的提馏方式? 提馏段的主要作用是把塔底或侧线产品中的轻馏分蒸出,从而改善产 品的分割、并能满足某些产品对闪点的要求。 石油蒸他塔多数的提烟段都采取水蒸汽汽提的方法,因此习惯地把提馏 段称为汽提段或汽提塔.其主要原理是通入过热水蒸汽、在提馏段的堆板上与 油品接触,降低了油气分压而使披提馏的油品中的轻馏分汽化、从而达到提馏 的目的。炼厂过热水蒸汽容易取得而且常压塔、减压塔底以及下部侧线的温度 很高,如果采用重沸器很难找到合适的热源。故而水蒸汽汽提得到了广泛的应 用。 近年来常压塔上部侧线采用再沸提馏的方式日益增加,这种做法是基于 以下考虑: ①侧线产品汽提时,产品中会溶解徽量水分,会使航空煤油的冰点或灯 用煤油的浊点上升.采用再沸器进行提馏,可以免除这个弊病。 ②水的分子量较油品分于量小得多,故少量的水蒸汽具有很大的体积, 相当于同样重量的煤油或轻柴油馏分蒸汽体积的十倍。在相当大的程度上加大 了塔的汽相负荷。用再沸器代替侧线汽提有利于提高蒸馏塔的处理能力。 ③水蒸汽的冷凝潜热很大,侧线再沸提馏有助于降低塔顶冷凝器的热负 荷、降低能耗,并且减少含油污水的生成量。 此外有个别炼厂采用干式减压蒸馏来生产润滑油时,侧线抽出物在汽提 塔内用减压闪蒸拔出其中较轻馏分的办法来进行提馏。 9.什么叫回流比?它的大小、对精馏操作有何影晌?
K
i 1
c
I
xi 1
露点方程是代表气体混合物组成与操作温度、压力条件关系的数学表 达式,其算式如下:
K
i 1
c
yi
i
1
其中 xi、yi、分别代表 i 组份在液相或气相的摩尔分率,C 代表系 统中的组分数目。 5.什么叫挥发度和相对挥发度? 液体混合物中任一组分汽化倾向的大小可以用挥发度 vi 来表示,其 数值是相平衡常数与压力的乘积,即: vi = Ki·P = (yi/xi)P 对于理想体系 Ki=(P i0 /P),液体泡合物中 i 组分的挥发度显然就等 于它的饱和蒸汽压,即 vi=P i0 。 相对挥发度是指系统中、任一组分 i 与对比组分 j 挥发度之比值、即
- 1、下载文档前请自行甄别文档内容的完整性,平台不提供额外的编辑、内容补充、找答案等附加服务。
- 2、"仅部分预览"的文档,不可在线预览部分如存在完整性等问题,可反馈申请退款(可完整预览的文档不适用该条件!)。
- 3、如文档侵犯您的权益,请联系客服反馈,我们会尽快为您处理(人工客服工作时间:9:00-18:30)。
常压炉,减压炉共用一台预热器
该空气预热器布置在地面
可使空气入炉温度达到190℃
炉子热效率达89.75%
设有空气鼓风机及烟气引风机各一台
16
二套常减压工艺简介
工艺流程简介加热炉烟气余热回收系统
为防止温度过低引起空气预热器露点腐蚀,使空气先经热油 式空气预热器(空预-1)加热到40℃,空预-1以常二线作加热热 源。
减三线走602/3去调合进410、413、414、406、409、411罐, 还可走18/3#、29/3#、35/3#线。 减四线走603/3去调合进402、408罐,还可走18/3# 、 29/3# 、
35/3#线。
减五线经87单元去重催装置,还可走18/3# 、 29/3#线。 热渣油去二重催,焦化做原料、另外专线去动力站做燃料。
常减压蒸馏是原油加工的第一道工序 装置是根据原油中各组份的沸点(挥发度)不同用加热的方 法从原油中分离出各种石油馏份
常压蒸馏蒸馏出低沸点的汽油、煤油、柴油等组份
常压渣油在避免裂解的较低温度下进行分馏,分离出润滑油 料、催化料等二次加工原料,剩下减压渣油。 本装置的减压塔,经过两次大型的改造,现在为全填料减压 塔,塔顶采用预冷凝和两级蒸汽喷射器抽真空,全塔压降 3.0KPa。
不足由装置外补给 采用常一中段回流做热源发生压力为0.4MPa的蒸汽
经过加热炉(炉-2)过热到≮360℃
各塔供汽提用
不足由装置外补充供给
本装置发生蒸汽所需的除氧水,在本装置内自设除氧站。
14
二套常减压工艺简介
工艺流程简介装置外输热系统概述
为了进一步回收装置内各侧线油品的低温余热,初馏塔顶及 常四线,减压二,四线及减压渣油等物流都设有采暖水热交换 器
二套常减压工艺简介
10
工艺流程简介航煤脱硫醇系统概述
装置生产的航煤馏分按3号航煤规格设计 航煤馏分硫醇性硫含量在12-20ppm之间,因此需要经过脱硫 醇工序
装置采用国内已成熟的13X铜分子筛氧化脱硫醇工艺
航煤馏分温度130℃、空速为3时-1下,通入少量空气进行氧 化脱硫醇
为使产品消光值达到要求,还需经过脱色罐脱色(罐内装有
常三线出装置 吹 扫 常压炉 电脱盐罐 泵11 吹 扫 泵12 进塔4 常四线出装置 泵10
原油 排 污 泵-1/1、2 高压瓦斯进装置阀
吹扫蒸汽 排污
减压炉
泵-2/1、2
泵-3/1、2
二套常减压工艺简介
18
工艺流程简介减压系统流程图
二套常减压装置减压系统
1.0MPa专线蒸汽 排空 减顶回流
小放空
在闪蒸段处设置导流板
增设一台减五线换热器(E-53)和初底油换热 新增4台蓝式过滤器用于过滤减一、二中返塔油中的杂质
25
二套常减压工艺简介
装置的技术改造减压塔改造工艺数据
塔段号 塔内径(mm) 填料类型 填料高度 堆积密度 压力降(计算) 温度
二套常减压工艺简介
1 5000 矩鞍环 2000 239.6 0.545 55
至常压炉真空火嘴
容 6 减顶油与常压二侧线合走 减一专线出 减一线出装置
塔5
减二线出装置
减三线出装置 减压塔
减压炉来
减四线出装置
减五线出装置 减五专线 冷渣油出装置 排污 热渣油去 动力站 热渣油38#线
扫线
泵16 泵21
泵17
泵18
泵19
泵20
热渣油去二重
二套常减压工艺简介
19
原料来源及产品走向原料来源
原油由大庆油田东油库、东二库和南Ⅱ-Ⅰ油库供给,东油 库入我厂原油线,管线公称直径250mm,管线长13km,管线 内存油550t,最大输油量可达9000t/d;南Ⅱ-Ⅰ油库入我厂原
油线公称直径250mm,11.9km,管线内存油500t,最大输油
量可达7500t/d,两条原油线最大可输送原油16500t/d。两条 输油线由东、南油库直接入我厂原油中间罐或输入原油稳定
进料段以下为汽提段直径Φ3.5米
汽提段以下为抽出斗直径Φ2.8米以尽量减少渣油在高温区的 停留时间,减少裂解的不凝气数量。
二套常减压工艺简介
13
工艺流程简介蒸汽发生及水除氧系统概述
采用减一中段回流及 减四线、减五线做热源发生压力为 1.0MPa的蒸汽。经加热炉(炉-2)过热到250℃ 供本装置真空喷射器和加热炉燃料油雾化用
侧线(减二、减三、减四)
二套常减压工艺简介
12
工艺流程简介减压分馏系统概述
为了确保减压四线油质量,在进料段和减四线抽出层之间, 设有一个净洗段,用净洗段流下的内回流做洗涤油,冷凝下 的油作为减五线抽出,送去作催化裂化原料。
进料段处塔径放大到10米以进一步降低空速
在进料处的塔内部设有水平敷设的环型导流板,使汽液顺利 的分离,以减少雾沫夹带。
二套常减压工艺简介
3
工艺原理及概述装置概况
本装置是由中国石化总公司北京设计院设计
设计能力为每年加工350万吨大庆原油,年开工时间 为8000小时。
装置为润滑油型常减压蒸馏装置
全装置共有设备232台,占地面积17100m2
1989年4月破土动工,于1991年7月投产
装置生产常一线做为航空煤油要求符合3号航煤标准
7
二套常减压工艺简介
装置流程概述
其中常压塔设有一个顶回流,两个中段回流(常一中、 常二中),常底油经过泵-3/1.2 抽出到减压炉加热到 395℃左右后进入减压塔第四层上方,减压塔底吹入蒸 汽。减顶设有两级抽真空系统,减顶油汽经过一级予冷 器和一级抽空器和二级予冷器及二级抽空器,不凝气到 常压炉烧掉,冷却下来的油水经减顶油水分液罐(容-6) 分出的油经泵送出装置,减压塔沿塔壁至上而下依次馏 出减一线、减二线、减三线、减四线、减五线,各侧线 (除减五线)经过气提塔在由各泵抽出到各换热器进行 换热,冷却最后送出装置,减压塔经过泵-21/1.2 抽出。 经过两路换热,一部分热料去重催、焦化,另一部分经 过冷却做冷渣送出装置。
二套常减压工艺简介
9
工艺流程简介初馏、常压分馏系统概述
初馏塔直径Φ3.2米,内装18层浮阀塔盘,开有一个侧线 初馏塔抽出4%(占原油)直接送入常压塔,可以减少常压炉 的热负荷
常压塔直径上部为Φ3.8米,下部为Φ4.8米,内装47层浮阀塔
盘,及一个供常二中换热的填料段 常二中取热段采用环矩鞍和隔栅填料解决
活性炭) 产品经玻璃毛过滤器和陶瓷过滤器过滤之后送出装置。
11
二套常减压工艺简介
工艺流程简介减压分馏系统概述
本装置的减压塔,是按湿式操作设计,在塔底通入水蒸汽以 降低油气分压,塔顶真空度控制不小于93.5kpa 塔顶部油气冷凝段直径为5.0米,内部装有2米高环矩鞍填
油气冷凝段以下是分馏段,直径Φ8.2米,抽出三个润滑油料
2 8200 规整填料 1000 120 0.209 202.1
3 8200 规整填料 2200 150 1.236 244.4
4 8200 规整填料 1000 120 0.634 266.5
5 8200 规整填料 2600 150 3.574 286.5
6 8200 规整填料 3400 150 3.191 323.3
二套常减压装置工艺简介
大庆石化公司炼油厂常减压二车间 2007年8月23日
主要内容
工艺原理及概述 工艺流程简介 原料来源及产品走向 装置的技术改造 装置的能量消耗 装置的物料平衡 常减压装置的技术发展方向 装置生产受控管理开展情况
二套常减压工艺简介
2
工艺原理及概述工艺原理
装置的技术改造减压塔改全填料
目的提高装置润滑油料的质量和收率 将精馏段原网孔塔盘及原有规整填料拆除,更换成清华大学 SP系列规整填料
将原有的动力式液体分配器更换成重力式液体分配器
原有的矩鞍环填料利旧,减一及减五线集油箱利旧 提馏段将原有的F1浮阀塔盘更换成清华大学的ADV浮阀塔盘
二套常减压工艺简介
27
装置的技术改造减压深拔的策略
29/3#、35/3#、501/3#线。
常四线走18/3#、29/3#线。 减一线经87单元去重催装置,还可走18/3#、35/3#、501/3#
线。
减二线走601/3去调合进410-416罐,还可走18/3#29/3#、 35/3#线。
二套常减压工艺简介
22
原料来源及产品走向产品去向
8二套Biblioteka 减压工艺简介工艺流程简介电脱盐系统概述
设计电脱盐温度定为120℃,注水量为5%(占原油),注入 破乳剂的浓度-2%,注入量20ppm (占原油),为了降低能 耗,装置采用容-6脱水作为部分电脱盐注水,今年还尝试使
用硫磺酸性水代替除盐水作为电脱盐注水,并且能够保证脱
后含盐在5mg/l以下。
二套常减压工艺简介
17
工艺流程简介常压系统流程图
二套常减压装置常压及加热炉系统
初顶汽油470/3#线 紧急放空线
低压瓦斯至原稳装置
容 容2 容3 脱水地漏管
4
容
5 常顶汽油10/3#线
吹 扫
泵8
常一12#线出装置
吹 扫 塔 1 脱水地漏入 下水井 常压塔
塔 3
常一73#线出装置 泵9 常二线出装置
万米罐储存,经8/3#管线由东向西进入装置内泵-1/1.2处。