齿轮齿条传动系统的运动学及动力学仿真分析
机械齿轮传动系统的动力学分析与优化

机械齿轮传动系统的动力学分析与优化齿轮传动是一种常见的动力传递机构,具有传递力矩大、传动效率高等优点,在工业生产中得到广泛应用。
但是,由于齿轮传动系统存在着一些固有的问题,如齿轮啮合时的振动和噪音、齿面磨损等,因此对其进行动力学分析和优化是非常重要的。
1. 动力学分析1.1 齿轮啮合的动力学模型齿轮啮合过程中,齿轮之间存在着瞬时的压力、速度和加速度变化。
可以通过建立齿轮啮合的动力学模型来分析其动态特性。
常用的方法包括等效单齿转动法和有限元法。
通过分析齿轮齿面接触应力和应力分布,可以预测系统的振动和噪音水平,为后续的优化提供依据。
1.2 动力学参数的测量和计算为了进行动力学分析,需要测量和计算一些关键参数,如齿轮的啮合刚度、传递误差、滚子轴承的刚度等。
其中,传递误差是影响齿轮传动系统性能的重要因素之一,其大小与齿轮加工质量、啮合配合、齿轮轴向和径向跳动等因素有关。
通过合理的测量方法和计算模型,可以准确地获取这些参数,并对系统进行分析。
2. 动力学优化2.1 齿轮传动系统的振动和噪音控制由于齿轮啮合时的动态特性,齿轮传动系统常常会产生振动和噪音。
为了减小振动和噪音的水平,可以从多个方面进行优化,如合理设计齿形、减小啮合间隙、提高齿轮加工精度等。
此外,也可以采用减振装置,如弹性联轴器、减震器等,来降低系统的振动能量传递。
2.2 传动效率的提高传动效率是衡量齿轮传动系统性能的重要指标之一。
为了提高传动效率,可以从减小传动误差、改善齿轮表面质量、减小传动间隙等方面入手。
此外,合理选择润滑方式和润滑油,也可以有效地降低系统的摩擦和磨损,提高传动效率。
2.3 齿轮传动系统的寿命预测齿轮传动系统的寿命是评估其使用寿命和可靠性的重要指标。
通过综合考虑齿轮的强度、疲劳寿命和磨损等影响因素,可以建立寿命预测模型,对系统进行寿命预测和优化设计。
此外,还可以通过监测齿轮的工作状态和健康状况,进行实时的故障诊断和维护。
3. 总结齿轮传动系统的动力学分析和优化是提高其性能和可靠性的重要手段。
齿轮传动过程中的动力学分析
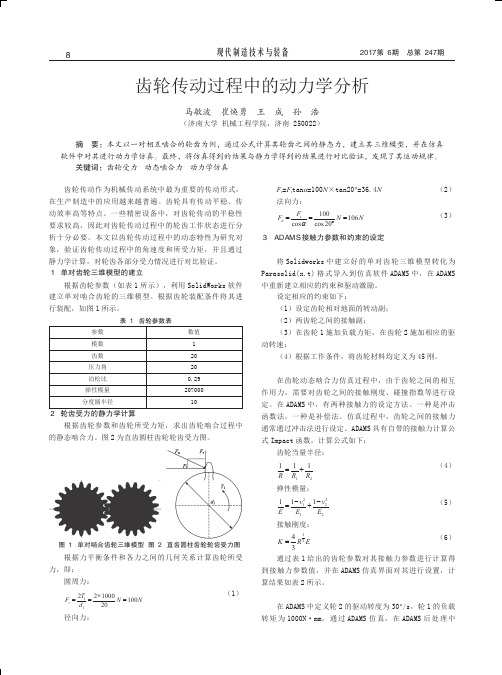
图1 单对啮合齿轮三维模型 图2 直齿圆柱齿轮轮齿受力图根据力平衡条件和各力之间的几何关系计算齿轮所受力,即:圆周力:1122100010020tT F N N d ×=== (1)图3 圆周动态啮合力仿真曲线图4 径向动态啮合力仿真曲线图5 法向动态啮合力仿真曲线通过图6可得出主动轮2所受力矩,而齿轮1负载力矩为1000N·mm。
齿轮2所受力矩根据力的大小围绕1000N·mm波动,所以齿轮在传动过程中所输出力矩并不是一个恒定值,而是会随齿轮动态啮合力大小不断变化。
图6 齿轮2所受力矩仿真曲线图7 齿轮1角速度仿真曲线4 结语首先,根据齿轮传动过程中所受力的大小,由公式计算齿轮的静态啮合力。
其次,利用仿真软件对齿轮实际运动过程中的工况进行动力学仿真,得到实际工况下的动态啮合力和速度图像。
最后,通过得到的动力学图像与静力学条件下计算得到的静态力进行对比验证,并分析了齿轮运动过程中的工况。
参考文献[1]夏永.基于ADAMS的风电齿轮箱动力学仿真分析[D].大连:大连理工大学,2014.[2]江志祥,朱增宝,季军.基于UG与ADAMS的行星齿轮减速器动力学仿真分析[J].煤矿机械,2013,(6):43-44.[3]张白鸽,岑海堂.基于ADAMS的椭圆齿轮动力学仿真分析[J].机械工程与自动化,2016,(2):98-100.[4]陈涛.风力发电机组齿轮箱传动系统动力学仿真与分析[D].北京:华北电力大学,2015.[5]钱直睿,黄晓燕,李明哲,李东平.多轴齿轮传动系统的动力学仿真分析[J].中国机械工程,2006,(3):241-244.Dynamic Analysis of Gear TransmissionMA Minbo, CUI Huanyong, WANG Cheng, SUN Hao(School of Mechanical Engineering, University of Jinan, Jinan 250022)Abstract: In this paper, a pair of meshing teeth, for example, through the formula to calculate the static force between the teeth, and the establishment of its three-dimensional model, in the simulation software for its dynamic simulation. The results of simulation are compared with those obtained by statics, and the laws of motion are found.Key words:gear force, dynamic meshing force, dynamic simulation。
《2024年齿轮传动系统动力学特性的有限元分析及试验方法研究》范文
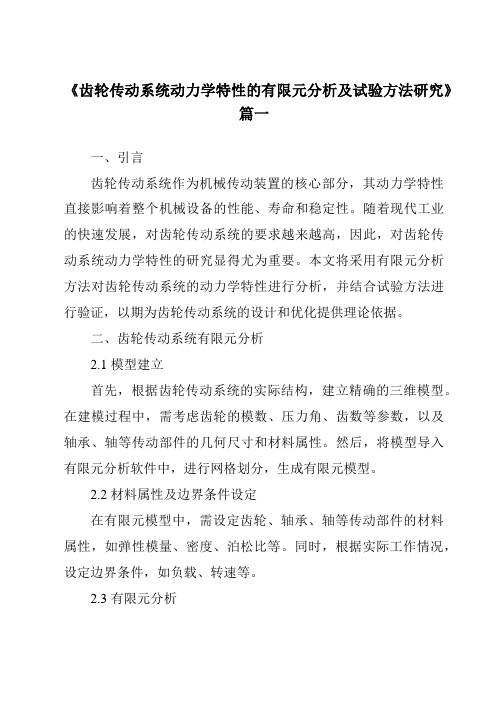
《齿轮传动系统动力学特性的有限元分析及试验方法研究》篇一一、引言齿轮传动系统作为机械传动装置的核心部分,其动力学特性直接影响着整个机械设备的性能、寿命和稳定性。
随着现代工业的快速发展,对齿轮传动系统的要求越来越高,因此,对齿轮传动系统动力学特性的研究显得尤为重要。
本文将采用有限元分析方法对齿轮传动系统的动力学特性进行分析,并结合试验方法进行验证,以期为齿轮传动系统的设计和优化提供理论依据。
二、齿轮传动系统有限元分析2.1 模型建立首先,根据齿轮传动系统的实际结构,建立精确的三维模型。
在建模过程中,需考虑齿轮的模数、压力角、齿数等参数,以及轴承、轴等传动部件的几何尺寸和材料属性。
然后,将模型导入有限元分析软件中,进行网格划分,生成有限元模型。
2.2 材料属性及边界条件设定在有限元模型中,需设定齿轮、轴承、轴等传动部件的材料属性,如弹性模量、密度、泊松比等。
同时,根据实际工作情况,设定边界条件,如负载、转速等。
2.3 有限元分析在设定好材料属性和边界条件后,进行有限元分析。
通过施加动态载荷,模拟齿轮传动系统在实际工作过程中的受力情况,分析齿轮的应力、应变、位移等动力学特性。
三、试验方法研究3.1 试验设备及方案为验证有限元分析结果的准确性,需设计并搭建齿轮传动系统试验平台。
试验平台应包括齿轮、轴承、轴等传动部件,以及测功机、传感器、数据采集系统等测试设备。
试验方案应包括不同转速、负载等工况下的试验内容。
3.2 数据采集与分析在试验过程中,通过传感器实时采集齿轮传动系统的应力、应变、位移等数据。
然后,将采集到的数据导入数据分析软件中,与有限元分析结果进行对比,验证有限元分析的准确性。
同时,通过分析试验数据,可以了解齿轮传动系统在实际工作过程中的动力学特性。
四、结果与讨论4.1 结果展示通过有限元分析和试验方法的研究,我们可以得到齿轮传动系统在不同工况下的动力学特性,包括应力、应变、位移等参数的变化规律。
齿条齿轮转向系统动态仿真分析
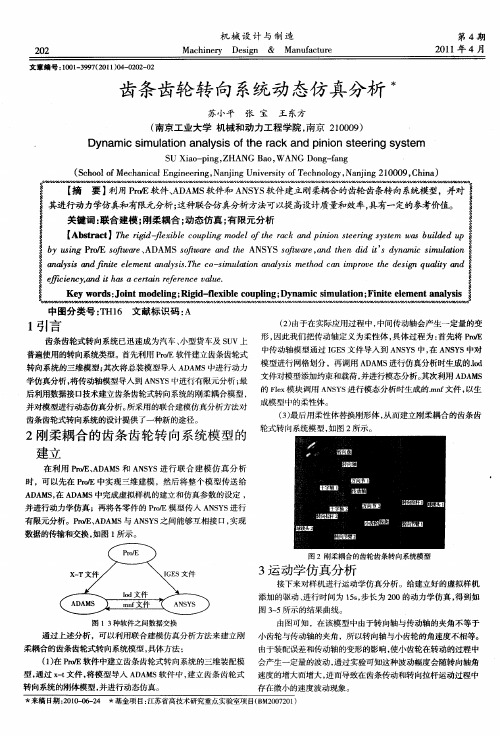
添加的驱动 、 进行时 间为 1 s步长为 20的动力学仿真, 5, 0 得到如
图 35所示 的结果 曲线 。 ~
图 13 种软件之间数据交换
由图可知,在该模型 中由于转向轴与传动轴的夹角不等于 由于装配误差和传动轴的变形的影响 , 使小齿轮在转动的过程中
【 摘
要】 利用Pd 软件、 D M 软件和 A S S rE AA S N Y 软件建立刚柔耦合的齿轮齿条转向系统模型, 并对
其进行动力学 仿真和有限元分析; 这种联合仿真分析方法可以 提高设计质量和效率, 具有一定的参考价值。 关键 词 : 联合建模 ; 刚柔耦合 ; 动态仿真 ; 限元分析 有
S Xio p n ZHANG o, ANG n - a g U a - i g, Ba W Do g f n
( col f ca ia E g e r gN nigU i r t o eh o g , aj g2 0 0 , hn ) S h o o h ncl ni ei , a j nv sy f cn l y N ni 10 9 C ia Me n n n e i T o n
普遍使用的转向系统类型。首先利用 Po rE软件建立齿条齿轮式 /
D MS 1 o 转 向系统 的三 维模 型 ; 次将 总装 模 型导 入 A A S中进 行 动 力 模型进行网格划分 ,再调用 A A 进行仿真分析时生成 的.d 其 D M 文件对模型添加约束和载荷 , 并进行模态分析。 其次利用 A A D MS 学仿真分析 , 将传动轴模型导人到 A S S中进行有限元分析; NY 最 的 Fe 模 块 调 用 A S S进行 模 态 分析 时 生 成 的 .i" l x NY m d文件 , 以生 后利用数据接口技术建立齿条齿轮式转 向系统的刚柔耦合模型 , 成模 型 中的柔 性 体 。 并对模型进行动态仿真分析。 所采用的联合建 齿条齿轮式转向系统的设计提供 了一种新 的途径 。 轮式 转 向 系统模 型 , 图 2所 示 。 如
高速精密齿轮传动装置的动力学仿真与优化设计
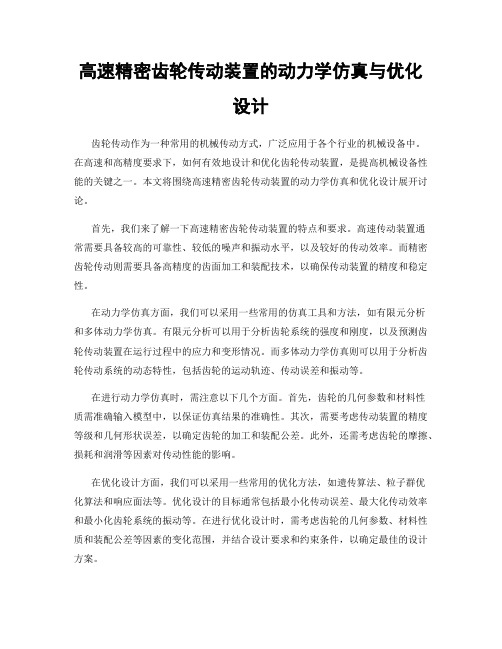
高速精密齿轮传动装置的动力学仿真与优化设计齿轮传动作为一种常用的机械传动方式,广泛应用于各个行业的机械设备中。
在高速和高精度要求下,如何有效地设计和优化齿轮传动装置,是提高机械设备性能的关键之一。
本文将围绕高速精密齿轮传动装置的动力学仿真和优化设计展开讨论。
首先,我们来了解一下高速精密齿轮传动装置的特点和要求。
高速传动装置通常需要具备较高的可靠性、较低的噪声和振动水平,以及较好的传动效率。
而精密齿轮传动则需要具备高精度的齿面加工和装配技术,以确保传动装置的精度和稳定性。
在动力学仿真方面,我们可以采用一些常用的仿真工具和方法,如有限元分析和多体动力学仿真。
有限元分析可以用于分析齿轮系统的强度和刚度,以及预测齿轮传动装置在运行过程中的应力和变形情况。
而多体动力学仿真则可以用于分析齿轮传动系统的动态特性,包括齿轮的运动轨迹、传动误差和振动等。
在进行动力学仿真时,需注意以下几个方面。
首先,齿轮的几何参数和材料性质需准确输入模型中,以保证仿真结果的准确性。
其次,需要考虑传动装置的精度等级和几何形状误差,以确定齿轮的加工和装配公差。
此外,还需考虑齿轮的摩擦、损耗和润滑等因素对传动性能的影响。
在优化设计方面,我们可以采用一些常用的优化方法,如遗传算法、粒子群优化算法和响应面法等。
优化设计的目标通常包括最小化传动误差、最大化传动效率和最小化齿轮系统的振动等。
在进行优化设计时,需考虑齿轮的几何参数、材料性质和装配公差等因素的变化范围,并结合设计要求和约束条件,以确定最佳的设计方案。
在进行动力学仿真和优化设计时,我们还需关注以下几个关键问题。
首先,需要对齿轮传动系统的工作条件和运行环境进行充分的分析和评估,以确定仿真和优化设计的基准和目标。
其次,需要建立合理的数学模型和仿真方案,以保证仿真结果的准确性和可靠性。
此外,还需考虑齿轮传动与其他部件的耦合效应和相互作用,以综合考虑整个系统的动力学性能。
总之,高速精密齿轮传动装置的动力学仿真和优化设计是提高机械设备性能的关键之一。
齿轮传动系统的动力学仿真分析

齿轮传动系统的动力学仿真分析摘要:本文对建立好的整体机械系统的虚拟样机模型进行运动学和动力学的仿真分析,通过仿真分析,可以方便地得出齿轮传动系统在特定负载和特定工况下的转矩,速度,加速度,接触力等,仿真分析后,可以确定各个齿轮之间传递的力和力矩,为零件的有限元分析提供基础。
关键词:传动系统动力学仿真 adams 虚拟样机中图分类号:th132 文献标识码:a 文章编号:1007-9416(2011)12-0207-01随着计算机图形学技术的迅速发展,系统仿真方法论和计算机仿真软件设计技术在交互性、生动性、直观性等方面取得了较大进展,它是以计算机和仿真系统软件为工具,对现实系统或未来系统进行动态实验仿真研究的理论和方法。
运动学仿真就是对已经添加了拓扑关系的运动系统,定义其驱动方式和驱动参数的数值,分析其系统其他零部件在驱动条件下的运动参数,如速度,加速度,角速度,角加速度等。
对仿真结果进行分析的基础上,验证所建立模型的正确性,并得出结论。
本文中所用的动力学仿真软件是adams软件。
adams软件使用交互式图形环境和零件库、约束库、力库,创建完全参数化的机械系统几何模型,其求解器采用多刚体系统动力学理论中的拉格郎日方程方法,建立系统动力学方程,对虚拟机械系统进行静力学、运动学和动力学分析,输出位移、速度、加速度和反作用力曲线。
adams软件的仿真可用于预测机械系统的性能、运动范围、碰撞检测、峰值载荷以及计算有限元的输入载荷等。
虚拟样机就是在adams软件中建的样机模型。
1、运动参数的设置先在造型软件ug中将齿轮传动系统造型好,如下图所示。
在已经设置好运动副的齿轮传动系统的第一级齿轮轴上绕地的旋转副上给传动系统添加一个角速度驱动。
然后进行仿真。
在进行仿真的过程中,单位时间内仿真步数越多,步长越短,越能真实反映系统的真实结果,但缺点是仿真时间也随之变长,占用的系统空间也就越大。
所以应该在兼顾仿真真实性与所需物理资源和仿真时间的基础上,选择一个合适的仿真时间和仿真的步长。
差速器齿轮机构的运动学及动力学分析
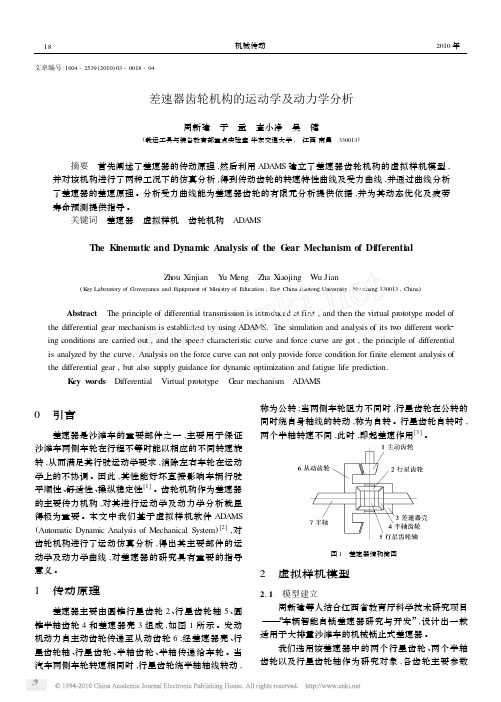
称为公转 ; 当两侧车轮阻力不同时 ,行星齿轮在公转的 同时绕自身轴线的转动 ,称为自转 。行星齿轮自转时 , 两个半轴转速不同 ,此时 ,即起差速作用[3 ] 。
图1 差速器结构简图
2 虚拟样机模型
2. 1 模型建立
1 传动原理
差速器主要由圆锥行星齿轮 2 、 行星齿轮轴 5 、 圆 锥半轴齿轮 4 和差速器壳 3 组成 , 如图 1 所示 。发动 机动力自主动齿轮传递至从动齿轮 6 ,经差速器壳 、 行 星齿轮轴 、 行星齿轮 、 半轴齿轮 、 半轴传递给车轮 。当 汽车两侧车轮转速相同时 ,行星齿轮绕半轴轴线转动 ,
表1 差速器齿轮主要参数 半轴齿轮 齿数 模数/ mm 齿宽/ mm
) 压力角/ (°
Hertz 碰撞理论 [ 5 ] 可知
2 δ= a =
R
9 P2 16 RE2
1 3
( 1)
则可得撞击时接触法向力 P 和变形δ的关系为 δ2 P= K
4 1 R2 E 3 1
R1
3
( 2)
式中 , 接触刚度 K 取决于撞击物体材料和结构形状
22 . 50 52 . 5 56 . 31 31 . 55 2 . 03 4 . 288 61 . 18 48 . 57 4 . 14 2 . 08 3 . 57 2 . 688 41 . 43 28 . 82 5 . 76 3 . 78
节圆直径/ mm
) 节锥角/ (°
式 ( 1) 和式 ( 3) 中的 R 是个变量 , 这里 R1 、 R2 分别 采用 两 齿 轮 的 节 圆 处 半 径 , 计 算 得 k = 5 . 71 ×
摘要 首先阐述了差速器的传动原理 ,然后利用 ADAMS 建立了差速器齿轮机构的虚拟样机模型 , 并对该机构进行了两种工况下的仿真分析 ,得到传动齿轮的转速特性曲线及受力曲线 ,并通过曲线分析 了差速器的差速原理 。分析受力曲线能为差速器齿轮的有限元分析提供依据 ,并为其动态优化及疲劳 寿命预测提供指导 。 关键词 差速器 虚拟样机 齿轮机构 ADAMS
机械设计中的齿轮系统动力学分析
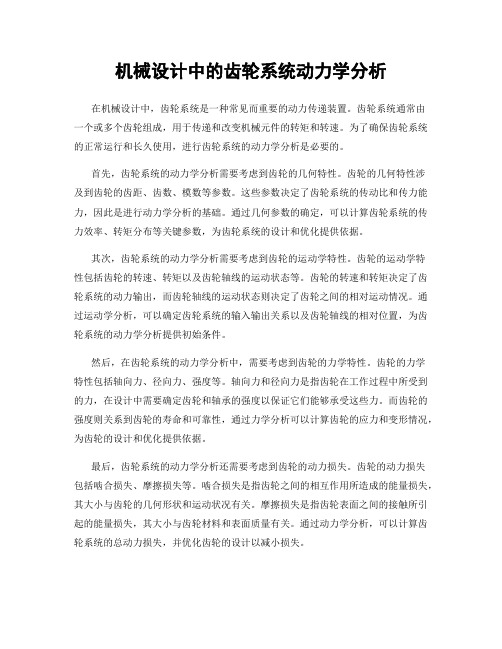
机械设计中的齿轮系统动力学分析在机械设计中,齿轮系统是一种常见而重要的动力传递装置。
齿轮系统通常由一个或多个齿轮组成,用于传递和改变机械元件的转矩和转速。
为了确保齿轮系统的正常运行和长久使用,进行齿轮系统的动力学分析是必要的。
首先,齿轮系统的动力学分析需要考虑到齿轮的几何特性。
齿轮的几何特性涉及到齿轮的齿距、齿数、模数等参数。
这些参数决定了齿轮系统的传动比和传力能力,因此是进行动力学分析的基础。
通过几何参数的确定,可以计算齿轮系统的传力效率、转矩分布等关键参数,为齿轮系统的设计和优化提供依据。
其次,齿轮系统的动力学分析需要考虑到齿轮的运动学特性。
齿轮的运动学特性包括齿轮的转速、转矩以及齿轮轴线的运动状态等。
齿轮的转速和转矩决定了齿轮系统的动力输出,而齿轮轴线的运动状态则决定了齿轮之间的相对运动情况。
通过运动学分析,可以确定齿轮系统的输入输出关系以及齿轮轴线的相对位置,为齿轮系统的动力学分析提供初始条件。
然后,在齿轮系统的动力学分析中,需要考虑到齿轮的力学特性。
齿轮的力学特性包括轴向力、径向力、强度等。
轴向力和径向力是指齿轮在工作过程中所受到的力,在设计中需要确定齿轮和轴承的强度以保证它们能够承受这些力。
而齿轮的强度则关系到齿轮的寿命和可靠性,通过力学分析可以计算齿轮的应力和变形情况,为齿轮的设计和优化提供依据。
最后,齿轮系统的动力学分析还需要考虑到齿轮的动力损失。
齿轮的动力损失包括啮合损失、摩擦损失等。
啮合损失是指齿轮之间的相互作用所造成的能量损失,其大小与齿轮的几何形状和运动状况有关。
摩擦损失是指齿轮表面之间的接触所引起的能量损失,其大小与齿轮材料和表面质量有关。
通过动力学分析,可以计算齿轮系统的总动力损失,并优化齿轮的设计以减小损失。
综上所述,机械设计中的齿轮系统动力学分析是一个综合性的工程问题。
通过考虑齿轮的几何特性、运动学特性、力学特性和动力损失等因素,可以全面了解齿轮系统的工作情况,为齿轮系统的设计和优化提供科学依据。
- 1、下载文档前请自行甄别文档内容的完整性,平台不提供额外的编辑、内容补充、找答案等附加服务。
- 2、"仅部分预览"的文档,不可在线预览部分如存在完整性等问题,可反馈申请退款(可完整预览的文档不适用该条件!)。
- 3、如文档侵犯您的权益,请联系客服反馈,我们会尽快为您处理(人工客服工作时间:9:00-18:30)。
文章引用 : 郭畅, 范英杰, 金成哲. 齿轮齿条传动系统的运动学及动力学仿真分析[J]. 机械工程与技术, 2016, 5(3): 265-271. /10.12677/met.2016.53031
郭畅 等
摘
要
齿轮齿条传动是一种应用范围广泛的传动方式,本文针对油脂工业用浸出器的齿轮齿条传动系统进行了 运动学及动力学仿真。首先应用UG软件对齿轮、齿条零件进行了参数化建模,将其模型导入ADAMS平 台中进行了动力学与运动学仿真,运用齿轮传动弹性动力学对仿真结果进行了分析,得出了齿轮齿条副 传动过程中齿条的速度,加速度,齿轮齿条齿面接触力,齿轮所受扭矩以及齿条振动量,并且分析了仿 真数值产生波动的原因。
yt = rb × sin ( t1 ) + rb × rad ( t1 ) × cos ( t1 )
t =1 t1 = t ∗ 90
t 为 UG 的系统参数。
先使用渐开线方程,式(1)、(2)、(3)、(4)和表 1 所示的参数做出齿轮大端的一个齿形,如图 1 所示。 然后用平移、缩放建立小端齿形,之后采用扫掠建立一个完整的齿廓,之后采用圆周阵列,拉伸等命令 做出完整的齿轮。齿轮如下图 2(a)所示。齿条采用的建模方法是,先建立一个齿廓,之后采用阵列,布 尔求和等命令建立一部分齿条。齿条建模结果如图 2(b)所示。 与其配对的齿条的参数如表 2 所示。
dq e = F _ impact MAX 0, K ( q0 − q ) − C × × STEP ( q, q0 − d ,1, q0 , 0 ) d t
仿真条件 齿轮为主动件,输入转速 1 r/100min,将齿轮齿条设置为刚体,在齿条上添加油料产生的阻力 14,900 N,设置仿真时间为 75 s,步数为 1800 步。根据文献[8]的研究设置接触刚度为 15000,阻尼为 10。
250.0
cm_MEA_V
cgear
150.0
Velocity (mm/sec)
50.0 0.0 -50.0 -150.0 -250.0 15.0 30.0 Time (sec) 45.0 60.0 75.0
-350.0 0.0 Analysis: Last_Run
Figure 4. Rack speed along X axial direction 图 4. 齿条 X 轴方向速度
参数 模数 齿数 压力角 分度圆直径 分锥角 根锥角 锥距 全齿高 轴交角 类型 毫米 整数 度 毫米 度 度 毫米 毫米 度 符号 m z α d2 δ δf R h Σ 值 20 19 20 380 2.905 2.32 3754.81 44 90
连接线 渐开线
齿顶圆 基圆 齿根圆
Figure 1. Big end bevel gear involutes of UG 图 1. 锥齿轮大端渐开线
2. 齿轮齿条的参数化建模
对渐开线齿轮建立参数化模型,主要是确定齿轮的参数。在表 1 的参数情况下,渐开线与齿根圆不 相交,本文采用了用直线连接的方法。 渐开线方程为:
xt = rb × cos ( t1 ) + rb × rad ( t1 ) × sin ( t1 )
(1) (2) (3) (4)
267
郭畅 等
(a)
(b)
Figure 2. (a) Simulator of wimble gear of UG; (b) UG simulator of rack 图 2. (a) UG 锥齿轮模型;(b) UG 齿条模型
3. ADAMS 运动学以及动力学仿真
在 UG 环境下导出常用的文件格式有 STEP, IGES, DXF, DWG 和 Parasolid 这 5 种常用的格式文件。 本文选用了 Parasolid 格式作为导入 ADAMS 的中间文件。 在齿轮与 ground 间添加旋转副, 齿条与 ground 之间添加直线副,并在齿轮齿条间建立碰撞力。 ADAMS 中共有两类接触力可以选择,本文选择的是基于 Impact 函数的接触力。Impact 使用刚度系 数以及阻尼系数来计算碰撞力。 Impact 函数的表达式为
268
郭畅 等
cgear
MEA_F
40000.0
Force (newton)
30000.0 20000.0 10000.0 0.0 0.0 Analysis: Last_Run 15.0 30.0 45.0 60.0 75.0
Time (sec)
Figure 3. Contact force between gear and rack tooth surface 图 3. 齿轮齿条齿面接触力
The Kinematics and Dynamics Analysis of Gear-Rack Drive System
Chang Guo1, Yingjie Fan2, Chengzhe Jin1
1 2
College of Mechanical, Shenyang Ligong University, Shenyang Liaoning Shenyang Equipment Manufacturing Engineering School, Shenyang Liaoning
Keywords
Gear Transmission, ADAMS, Kinematics, Dynamic
齿轮齿条传动系统的运动学及动力学仿真分析
郭
1 2
畅1,范英杰2,金成哲1
沈阳理工大学机械工程学院,辽宁 沈阳 沈阳市装备制造工程学校,辽宁 沈阳
收稿日期:2016年9月6日;录用日期:2016年9月27日;发布日期:2016年9月30日
4. 仿真结果分析
通过齿轮齿条传动的 ADMAS 运动学和动力学仿真,得到仿真结果如图 3~7 所示。 图 3 齿面接触力呈现周期性波动,波动幅度高达 2500 N 以上。齿面接触力的变化除了对齿轮齿条传 动产生影响,而且还使传动轴受到的扭矩产生了明显的周期性波动。从而影响了减速器以及电动机的运 转平稳性,突然出现的扭矩峰值会加剧电动机的负载。 图 4 反映了齿条质心 X 轴方向的速度波动情况,幅度基本在 0.1 m/s 之内。 图 5 反映了齿轮所受的扭矩,其幅值啮合规律变化。可见其速度、加速度与扭矩都是时变量,其变 化会对传动的平稳性造成破坏,引起附加动应力、振动以及噪声。
2.5E+005 2.0E+005
newton-mm
cgear
MEA_MOM
1.5E+005 100000.0 50000.0 0.0 0.0 50.0 Analysis: Last_Run 100.0 150.0 Time (sec) 200.0 250.0 300.0
Figure 5. Moment of gear centroid 图 5. 齿轮质心处的转矩
d1 da df rb
值(公式) 20 19 20 2.905 130 2.2∗m m∗z
m ∗ ( z + 2 ∗ cos (α ) ) m ∗ ( z − 2.4 ∗ cos (α ) )
d1 ∗ cos (α ) 2
Table 2. Parameter simulator of rack 表 2. 齿条参数
Open Access
Abstract
Rack and gear drive is a kind of widely used transmission mode. In this paper, the kinematics and dynamics simulation of the gear rack and pinion drive system of the oil industry was carried out. Firstly, the gear and rack are parameterized modeln the model are imported into ADAMS for dynamic and kinematics simulation, and analyzed by the rack and gear transmission elastic dynamics. The speed and acceleration of rack, the contact force between rack and gear, torque on the gear, and vibration amplitude of rack are obtained.
关键词
齿轮传动,ADAMS,运动学,动力学
1. 引言
我国油脂工业使用的浸出器主要是固定底平转浸出器。其中比较关键的系统就是传动系统,在传动 系统中齿轮齿条副是影响使用寿命,传动平稳性的主要因素。 近些年来,许多国内外学者对这个问题进行了深入而富有成效的研究。任福深、马若虚[1]两人利用 能量法,建立拉格朗日方程,对齿轮齿条钻机的起升系统进行多体动力学分析;徐长航、苑思敏[2]等人 研究了工程上比较关注的应急状况下,复杂工况下小齿轮及整个系统的动力学特性;A. Fernández,M. Iglesias,A. de-Juan,P [3]等人建立了非线性动力学模型,分析了齿轮传动机构的动态特性及其对齿轮传 动的影响并考虑了齿轮、轴承的误差并分析了模型的振动规律。M. Amarnath,Sang-Kwon Lee [4]用实验 的方法提供了一种基于摩擦和振动评估齿轮磨损的方法,并在分析中考虑了润滑的影响。 Sha Wei , JingshanZha [5]等人基于基于 Chebyshev 区间法考虑了转动惯量、 扭转刚度等不确定变量并建立了扭转振 动模型。周旭辉,疏舒等人[6] [7]建立了齿轮齿条的三维模型,并用 ADAMS 进行了齿面接触力,小齿轮 速度等一系列动力学、运动学特性。研究了本文基于齿轮弹性动力学理论并结合运动学和动力学仿真分 析软件,对齿轮齿条传动系统进行了建模及运动学和动力学的仿真计算,并结合计算结果分析了齿轮齿 条传动的运动学以及动力学特征。