砂型铸造模具设计技巧-分型面倒角
模具倒角的技巧
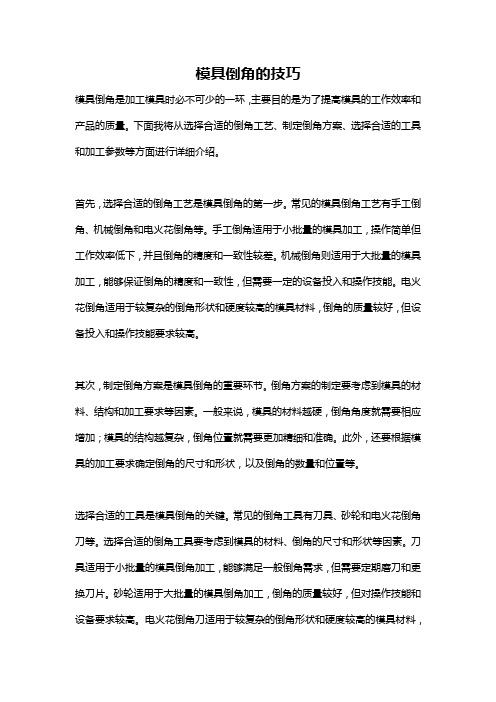
模具倒角的技巧模具倒角是加工模具时必不可少的一环,主要目的是为了提高模具的工作效率和产品的质量。
下面我将从选择合适的倒角工艺、制定倒角方案、选择合适的工具和加工参数等方面进行详细介绍。
首先,选择合适的倒角工艺是模具倒角的第一步。
常见的模具倒角工艺有手工倒角、机械倒角和电火花倒角等。
手工倒角适用于小批量的模具加工,操作简单但工作效率低下,并且倒角的精度和一致性较差。
机械倒角则适用于大批量的模具加工,能够保证倒角的精度和一致性,但需要一定的设备投入和操作技能。
电火花倒角适用于较复杂的倒角形状和硬度较高的模具材料,倒角的质量较好,但设备投入和操作技能要求较高。
其次,制定倒角方案是模具倒角的重要环节。
倒角方案的制定要考虑到模具的材料、结构和加工要求等因素。
一般来说,模具的材料越硬,倒角角度就需要相应增加;模具的结构越复杂,倒角位置就需要更加精细和准确。
此外,还要根据模具的加工要求确定倒角的尺寸和形状,以及倒角的数量和位置等。
选择合适的工具是模具倒角的关键。
常见的倒角工具有刀具、砂轮和电火花倒角刀等。
选择合适的倒角工具要考虑到模具的材料、倒角的尺寸和形状等因素。
刀具适用于小批量的模具倒角加工,能够满足一般倒角需求,但需要定期磨刀和更换刀片。
砂轮适用于大批量的模具倒角加工,倒角的质量较好,但对操作技能和设备要求较高。
电火花倒角刀适用于较复杂的倒角形状和硬度较高的模具材料,倒角的质量较好,但设备投入和操作技能要求较高。
最后,选择合适的加工参数是模具倒角的关键。
加工参数的选择要根据模具的材料和倒角的尺寸来确定。
一般来说,模具材料越硬,加工参数就需要相应增加;倒角的尺寸越大,加工参数就需要相应减小。
此外,还要根据倒角工具的类型和状况来确定加工参数,以确保倒角的质量和效率。
总之,模具倒角是模具加工中的重要环节,选择合适的倒角工艺、制定倒角方案、选择合适的工具和加工参数等是模具倒角的关键。
只有做好这些环节,才能够保证模具倒角的质量和效率,提升模具加工的水平和产品的竞争力。
砂型铸造模具设计及制造分析
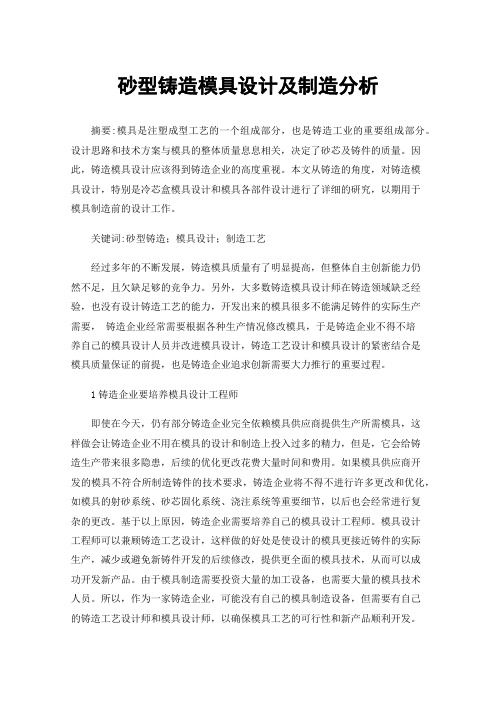
砂型铸造模具设计及制造分析摘要:模具是注塑成型工艺的一个组成部分,也是铸造工业的重要组成部分。
设计思路和技术方案与模具的整体质量息息相关,决定了砂芯及铸件的质量。
因此,铸造模具设计应该得到铸造企业的高度重视。
本文从铸造的角度,对铸造模具设计,特别是冷芯盒模具设计和模具各部件设计进行了详细的研究,以期用于模具制造前的设计工作。
关键词:砂型铸造;模具设计;制造工艺经过多年的不断发展,铸造模具质量有了明显提高,但整体自主创新能力仍然不足,且欠缺足够的竞争力。
另外,大多数铸造模具设计师在铸造领域缺乏经验,也没有设计铸造工艺的能力,开发出来的模具很多不能满足铸件的实际生产需要,铸造企业经常需要根据各种生产情况修改模具,于是铸造企业不得不培养自己的模具设计人员并改进模具设计,铸造工艺设计和模具设计的紧密结合是模具质量保证的前提,也是铸造企业追求创新需要大力推行的重要过程。
1铸造企业要培养模具设计工程师即使在今天,仍有部分铸造企业完全依赖模具供应商提供生产所需模具,这样做会让铸造企业不用在模具的设计和制造上投入过多的精力,但是,它会给铸造生产带来很多隐患,后续的优化更改花费大量时间和费用。
如果模具供应商开发的模具不符合所制造铸件的技术要求,铸造企业将不得不进行许多更改和优化,如模具的射砂系统、砂芯固化系统、浇注系统等重要细节,以后也会经常进行复杂的更改。
基于以上原因,铸造企业需要培养自己的模具设计工程师。
模具设计工程师可以兼顾铸造工艺设计,这样做的好处是使设计的模具更接近铸件的实际生产,减少或避免新铸件开发的后续修改,提供更全面的模具技术,从而可以成功开发新产品。
由于模具制造需要投资大量的加工设备,也需要大量的模具技术人员。
所以,作为一家铸造企业,可能没有自己的模具制造设备,但需要有自己的铸造工艺设计师和模具设计师,以确保模具工艺的可行性和新产品顺利开发。
2铸造工艺设计2.1分型面的选择在砂型铸造中,分型面选择合理可以简化组芯、造型操作,提高生产率,在选择分型面时一般需要考虑以下几个方面:为便于起模,一般分型面应选择在铸件最大截面处,一个截面无法起模时,局部阻碍起模的形状可做成活块,尽可能减少分型面和活块数量。
砂型铸造的方法

工艺参数的设定
(2)起模斜度(拔模斜度、脱模斜度)
便于把模型从砂型中取出,通常在铸件沿拔模方向的 内、外壁上均制有约 1:20的斜度
木模常为 l°~3°;金属模为0.5°~2° 拔模斜度一般不画出,但标注 影响因素:
模样材料
模样高度 造型方法
(3)收缩余量
补偿铸件收缩,在模样上增大的尺寸
5、绘制铸造工艺图
铸造工艺图示例:
例题:名称:连接盘;材料:HT200;生产数量:200件
技术要求:无气孔、缩松、渣眼等铸造缺陷
下
上
1、工艺分析 2、造型方法:手工造型
不铸出 采用型芯
有质量要求
3、浇注位置和分型面
方案1
上
方案2
下
4、加工余量
基本 尺寸 200 端面 120 端面 200 外圆 120 外圆 200 台阶面 加工 基准 120 端面 200 端面 200 端面 200 端面 200 端面 40 该表面距加 工基准尺寸 80 80 顶面 底面 侧面 侧面 端面 底面 MA J H H H H 加工 双面 双面 单面 单面 双面
较厚实的部分应放在分型面附近的上部或侧面
浇注位置的选择
铸件的重要加工面和主要工作面朝下或侧面:机床导轨是重 要面,浇注时要朝下。这是因为铸件上部凝固速度慢,晶粒 较粗大,易在铸件上部形成砂眼、气孔、渣孔等缺陷。铸件 下部的晶粒细小,组织致密,缺陷少,质量优于上部。机床 床身导轨和铸造锥齿轮的锥面都是主要的工作面,浇注时应 朝下。
余 量 8.5 5.5 7 5.5 7
60孔
孔直径 80
孔径/直径中 大者
同顶 面
J
双面
5.5
砂型铸造模具设计技巧-分型面倒角
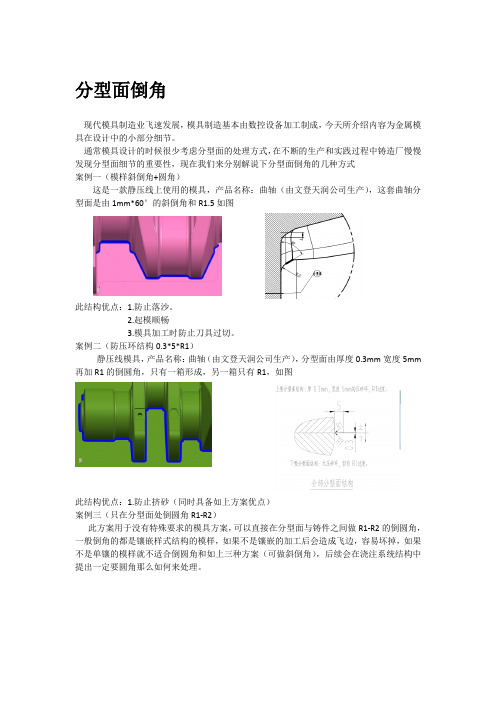
分型面倒角现代模具制造业飞速发展,模具制造基本由数控设备加工制成,今天所介绍内容为金属模具在设计中的小部分细节。
通常模具设计的时候很少考虑分型面的处理方式,在不断的生产和实践过程中铸造厂慢慢发现分型面细节的重要性,现在我们来分别解说下分型面倒角的几种方式案例一(模样斜倒角+圆角)这是一款静压线上使用的模具,产品名称:曲轴(由文登天润公司生产),这套曲轴分型面是由1mm*60°的斜倒角和R1.5如图此结构优点:1.防止落沙。
2.起模顺畅3.模具加工时防止刀具过切。
案例二(防压环结构0.3*5*R1)静压线模具,产品名称:曲轴(由文登天润公司生产),分型面由厚度0.3mm宽度5mm 再加R1的倒圆角,只有一箱形成,另一箱只有R1,如图此结构优点:1.防止挤砂(同时具备如上方案优点)案例三(只在分型面处倒圆角R1-R2)此方案用于没有特殊要求的模具方案,可以直接在分型面与铸件之间做R1-R2的倒圆角,一般倒角的都是镶嵌样式结构的模样,如果不是镶嵌的加工后会造成飞边,容易坏掉,如果不是单镶的模样就不适合倒圆角和如上三种方案(可做斜倒角),后续会在浇注系统结构中提出一定要圆角那么如何来处理。
浇注系统倒角以上介绍的都是模样上的倒角结构,接下来解说下浇注系统的倒角结构由于铸造的各种不定因素及设计方案各种方式不同,会对后期的浇注系统进行调整和翻箱的可能性,对于浇系来说就不适合镶嵌式,这样修改起来会对模具造成不美观及不易修改的不必要麻烦,但是又要保证分型面有圆角,一般来说最重要的是浇注系统根部留有R3-R6的圆角,原因是当铁水进入型腔时候第一时间经过的就是浇注系统,由于冲刷力和高温会造成尖沙部分被冲开,这样掉落的沙子就会流入型腔内造成大量铸件的报废,付出昂贵的损失,那么如何来制作倒圆角呢?请看下图浇注系统倒圆角(冒口)如图所示分型面处是做了0.5mm厚*R6的分型面结构,0.5mm是为了在模具加工时候不易被刀具挂掉,钳工在装配时候不易被磕碰掉,(相对没有厚度的样式来说)但是在安装和加工时候还是要格外细心操作避免损伤,在实际生产过程中根据客户及公司生产能力可做细微调整例如0.3mm*R3结构等等。
铸造砂眼缺陷

铸件的砂眼缺陷是砂型铸造最常见的缺陷之一,在铸件表面或铸件内部有充塞着型砂的孔眼。
生产铸件的过程中,砂眼问题时有发生,严重时可直接导致报废。
根据砂眼出现的位置,可分为表面砂眼和内部砂眼。
由于砂型或砂芯脱落产生,使铸件产生多肉或缺肉。
型腔掉砂时铸件多肉,砂粒掉入型腔时铸件缺肉。
根据砂眼出现的位置,可分为表面砂眼和内部砂眼。
对于铸件表面的砂眼,用肉眼外观检查即可识别;对于铸件内部的砂眼,要用超声或者射线探伤进行检验。
要想防止砂眼的产生那么就要分析铸件砂眼形成的原因。
一、铸造砂眼缺陷的特征在铸件表面或铸件内部有充塞着型砂的孔眼。
由于砂型或砂芯脱落产生,使铸件产生多肉或缺肉。
型腔掉砂时铸件多肉,砂粒掉入型腔时铸件缺肉。
典型案例:二、发现方法外观检查、机械加工、抛丸清理、超声、射线或磁力探伤可以发现。
三、产生的原因分析1、浇口位置不合适,如直对砂芯;或浇口太小,铁水冲击力太大,冲坏局部砂型(冲砂)。
冲砂在铸件被冲部位留有明显的冲刷痕迹和砂眼。
2、由于模具设计不合理,未留(留的不足)分型负数(分型面处太清根);合模时发生挤砂。
砂型未修好;铸件拐角处未捣实;铸件分型落差太大,造型线生产时射砂不满或型冲压不实。
3、湿型在浇铸前停留时间太长,使砂型尖角部分干燥而脱落,产生掉砂。
4、造型和合箱时浮砂未吹净,浇注后在铸件表面形成砂眼。
5、型砂配制不符合工艺(湿压强度太低)要求。
型砂中灰分太大(灰分可提高湿压强度,但不提高湿拉强度)。
6、型砂或芯砂表面强度不够。
7、造好的型浇口未盖,外来砂粒掉入型内。
8、砂箱套间隙太大,合箱时错箱,碰掉砂粒。
9、造型线设备在脱型和推型时振动太快,推型不稳造成错型而碰掉砂。
10、砂芯分型面处毛刺未清净,合箱时疵掉砂,掉入型腔。
11、砂温太高,在传送过程中水分挥发,使型砂强度降低。
12、气候干燥,加快了水分的蒸发,型砂强度太低。
13、粘结材料质量不好,降低了型砂性能。
14、生产线用弹簧浇口杯配合间隙太大,弹簧弹性不够,造成有效长度不够,形成浇口和模型接触段有间隙,射砂后有小的砂隔层,浇注时冲入型内。
砂型铸造分型面的确定原则.2

金属工艺学重点知识答案1.砂型铸造分型面的确定原则1).为了起模方便,分型面一般选在铸件的最大截面上,但注意不要使模样在砂型内过高。
2).尽量将铸件的重要加工面或大部分加工面和加工基准面放在同一个砂型中,而且尽可能放在下型,以便保证铸件尺寸的精确度。
3).为了简化操作过程,保证铸件尺寸精度,应尽量减少分型面的数目,减少活块的数目。
4).分型面应尽量采用平直面5)。
应尽量减少砂芯的数目2.影响金属可锻造性的因素1.化学成分;2.金属组织;3.变形温度;4.变形速度;5.应力状态3.焊接检验的方法1.外观检验;2.无损检验;3.焊接成品强度检验;4.致密性检验3.主运动和进给运动的区别、联系在机床上,转速最高,运动最快的运动称为主运动,进给运动是使工件切削层材料相进投入切割,从而加工出完整表面所需的运动. 由此可以看出,在平面磨床上,主运动是砂轮的高速旋转,进给运动是工作台的移动和砂轮的向下进给,在外圆磨上,主运动是砂轮的高速旋转,进给运动是砂轮的径向移动与工件的旋转。
4.锻压的基本生产方式1.扎制;2.挤压;3.拉拔;4自由锻;5模锻;6.冲压5.机械零件的失效形式、表面损伤包括1.变形失效;断裂失效;表面损失失效;变形失效:弹性变形失效、塑性变形失效断裂失效:延性断裂、低应力脆性断裂、疲劳断裂、蠕变断裂表面损失失效包括:1.磨损;2.解除疲劳;3.腐蚀6.铸造收缩三个阶段;简述影响收缩的主要原因1.液态收缩;2.凝固收缩;3.固态收缩影响收缩的主要原因:化学成分、浇注温度、铸件结构、铸型条件等。
7.焊接分类方法1.熔焊;2.压焊;3.钎焊8.切削物理现象积屑瘤、切削力、切削热、刀具磨损9.预防焊接变形措施1.反变形法;2.加裕量法;3.刚性固定法;4.合理安排焊接次序;5.强制冷却法;6.焊前预热简答题:1.锻压的基本生产方式1.扎制;2.挤压;3.拉拔;4自由锻;5模锻;6.冲压2.焊接检验的方法1.外观检验;2.无损检验;3.焊接成品强度检验;4.致密性检验3.毛坯制造工艺合理选择的因素1.零件的材料、形状及尺寸的影响;2.生产类型的影响;3.毛坯制造方法的工艺特点的影响;4.毛坯工艺技术的发展4.刀具切削运动中主运动和合运动的区别和联系主运动是切屑被切下所需要的基本运动,是形成机床切屑速度或消耗主要动力的切削运动,其形式有旋转运动和直线往复运动两种;进给运动是使刀具连续切下金属层所需要的运动,通常它的速度较低,消耗动力较少,其形式也有两种:旋转和直线,5.欠定位和超定位的定义欠定位:是指工件在某个方向上影响加工精度的自由度没有限制超定位:是指工件在某个方向上的自由度被两个以上定位元件重复限制6.写机械零件的加工工艺路线C620-1 卧式车床主轴箱中滑动齿轮(机床齿轮选材)工艺路线:下料——锻造——正火——组加工——调质——精加工——齿轮高频淬火及回火——精磨解放牌汽车一速齿轮(载重汽车的变速齿轮)工艺路线:下料——模锻——正火——机械粗、半精加工——渗碳淬火、低温回火——喷丸——校正花键孔——磨齿7.制定轴类零件的加工工艺过程磨床主轴工艺路线:下料——锻造——退火——粗加工——调质处理——精加工——表面淬火——粗磨——低温人工时效——精磨阶梯轴工艺过程(生产数量较少)工序号工序内容地点(设备)1 车端面,钻中心孔车床2 车外圆、切槽、倒角车床3 铣键槽、去毛刺铣床4 磨外圆磨床及阶梯轴工艺过程(生产数量较多)工序号工序内容地点(设备)1 铣端面,钻中心孔组合机床2 车小段外圆,切槽及倒角车床3 车大段外圆,切槽及倒角车床4 铣键槽铣床5 去毛刺钳工台6 磨外圆磨床课后答案1.简述浇注位置的确定原则1).一般情况下,铸件浇注位置的上面比下面铸造缺陷多,所以应将铸件的重要加工面或主要受力面等要求较高的部分放到下面;若有困难,则可放在侧面或斜面2).应有利于铸型的填充和型腔中气体的排出,所以,薄壁铸件应将薄而大的平面放到下面或侧立、倾斜,以防止出现浇不足或冷隔等缺陷3)。
模具倒角设计规范

模具倒⾓设计规范模具倒C⾓设计规范⼀.C4类⑴NC加⼯的零件,结构⼯程师不需设计倒⾓,由准备车间按照标准规范加⼯到位。
此类倒⾓主要从模具外观考虑,不参于模具的成型、锁紧、动作等功能。
该类倒按表1 取值:此类零件主要有以下⼏种①定位圈类②很规则的形状,如码模块,⽀撑块等③尼龙保护块类④油缸平键类⑤油缸⽌转块类⑥油缸接头类⑦U型块类⑧⾏程开关垫板类⑨⾏程开关撞块类⑩压线板类11.⽀撑柱类12.⽅导柱类13.集⽔器类14.插穿保护块类15.⾮标的耐磨板,承压板等16.锁模⽚类17.特制螺钉18.导套压板类19.推板导套压板类20.吊模块21.导滑块类22.垫⽚/压板类备注:⼯程师设计的倒⾓⼤⼩符合表1中所述的尺⼨,⼯程师就不需要在图形上设计倒⾓,准备车间按照表1取值倒⾓。
如果有特殊情况不符合,⼯程师需要在3D图形上设计倒⾓,零件图上明确标准。
⑵有⼀部分需NC加⼯的C4类零件,⼯程师需要在3D图形上设计上,NC按照3D图形加⼯到位。
此类零件主要有以下⼏种1.形状⽐较复杂,⼩圆台,斜⾯准备⽆法加⼯的,如下图所⽰⑶.需要线割的零件,⼯程师需要在3D图形上设计上,线割完成后,转⼊准备车间,由准备⼯序加⼯倒⾓。
如⽅斜顶、⼩镶块排料等。
备注:如果⼯程师设计的倒⾓符合符合上⾯的标准⼆.模板类⑴.标准件建腔的,⽤lem软件都能检测到,研究所按照http://192.168.63.10:8880/jiedian/PTA030.htm将标准件建腔体更新到位,⼯程师直接⽤标准件建腔即可。
⼯程师发图之前,必须⽤lem软件检测⼀遍,所有⽹站上标准的型孔lem软件必须识别。
⑵.⾮标准建腔的,⼯程师需要在3D图形上设计上,NC按照3D图形加⼯到位。
1.各模板外凌边、孔必须倒⾓,倒⾓尺⼨要⼀致,根据模架⼤⼩,以1.5*45°~3*45°为宜。
属于此类情况的⼯程师不需要在3D图形上设计倒⾓。
客户特殊要求的,超出此范围的,需要⼯程师在3D图形上设计上,NC加⼯到位。
铸造件倒角标准
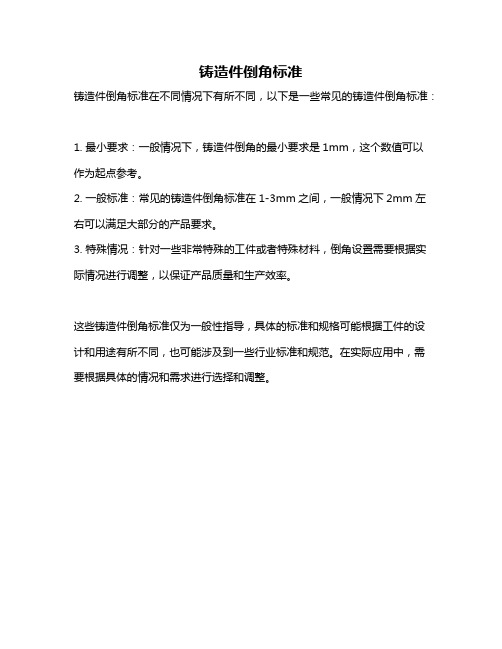
铸造件倒角标准
铸造件倒角标准在不同情况下有所不同,以下是一些常见的铸造件倒角标准:
1. 最小要求:一般情况下,铸造件倒角的最小要求是1mm,这个数值可以作为起点参考。
2. 一般标准:常见的铸造件倒角标准在1-3mm之间,一般情况下2mm左右可以满足大部分的产品要求。
3. 特殊情况:针对一些非常特殊的工件或者特殊材料,倒角设置需要根据实际情况进行调整,以保证产品质量和生产效率。
这些铸造件倒角标准仅为一般性指导,具体的标准和规格可能根据工件的设计和用途有所不同,也可能涉及到一些行业标准和规范。
在实际应用中,需要根据具体的情况和需求进行选择和调整。
- 1、下载文档前请自行甄别文档内容的完整性,平台不提供额外的编辑、内容补充、找答案等附加服务。
- 2、"仅部分预览"的文档,不可在线预览部分如存在完整性等问题,可反馈申请退款(可完整预览的文档不适用该条件!)。
- 3、如文档侵犯您的权益,请联系客服反馈,我们会尽快为您处理(人工客服工作时间:9:00-18:30)。
分型面倒角
现代模具制造业飞速发展,模具制造基本由数控设备加工制成,今天所介绍内容为金属模具在设计中的小部分细节。
通常模具设计的时候很少考虑分型面的处理方式,在不断的生产和实践过程中铸造厂慢慢发现分型面细节的重要性,现在我们来分别解说下分型面倒角的几种方式
案例一(模样斜倒角+圆角)
这是一款静压线上使用的模具,产品名称:曲轴(由文登天润公司生产),这套曲轴分型面是由1mm*60°的斜倒角和R1.5如图
此结构优点:1.防止落沙。
2.起模顺畅
3.模具加工时防止刀具过切。
案例二(防压环结构0.3*5*R1)
静压线模具,产品名称:曲轴(由文登天润公司生产),分型面由厚度0.3mm宽度5mm 再加R1的倒圆角,只有一箱形成,另一箱只有R1,如图
此结构优点:1.防止挤砂(同时具备如上方案优点)
案例三(只在分型面处倒圆角R1-R2)
此方案用于没有特殊要求的模具方案,可以直接在分型面与铸件之间做R1-R2的倒圆角,一般倒角的都是镶嵌样式结构的模样,如果不是镶嵌的加工后会造成飞边,容易坏掉,如果不是单镶的模样就不适合倒圆角和如上三种方案(可做斜倒角),后续会在浇注系统结构中提出一定要圆角那么如何来处理。
浇注系统倒角
以上介绍的都是模样上的倒角结构,接下来解说下浇注系统的倒角结构
由于铸造的各种不定因素及设计方案各种方式不同,会对后期的浇注系统进行调整和翻箱的可能性,对于浇系来说就不适合镶嵌式,这样修改起来会对模具造成不美观及不易修改的不必要麻烦,但是又要保证分型面有圆角,一般来说最重要的是浇注系统根部留有R3-R6的圆角,原因是当铁水进入型腔时候第一时间经过的就是浇注系统,由于冲刷力和高温会造成尖沙部分被冲开,这样掉落的沙子就会流入型腔内造成大量铸件的报废,付出昂贵的损失,那么如何来制作倒圆角呢?请看下图
浇注系统倒圆角(冒口)
如图所示分型面处是做了0.5mm厚*R6的分型面结构,0.5mm是为了在模具加工时候不易被刀具挂掉,钳工在装配时候不易被磕碰掉,(相对没有厚度的样式来说)但是在安装和加工时候还是要格外细心操作避免损伤,在实际生产过程中根据客户及公司生产能力可做细微调整例如0.3mm*R3结构等等。
(除了冒口.横浇道,内浇道都可以做如上结构)。