客车内饰护板技术条件
内饰立柱护板设计指南

立柱护板设计指南编制:校对:审核:批准:1、简要说明一般轿车有A、B、C三个立柱,有的结构还有D柱,如更复杂则依次类推。
立柱护板固定在汽车侧围立柱内板上,主要具有内部美化装饰,乘员保护等功能。
1.1 立柱护板材料的性能我公司现有车型立柱护板的材料有:PP5和PP6(A11、A15), PP-T20 (B11), PP-T15和PP-T20(S11)和PP+EPDM-T20(B14)和PP/PE (T11), 还有麻纤维材料,PP-T15和PP5一般都用在下护板上。
需要根据汽车的档次和护板造型结构的需要,制定合理的材料种类和成品标准,护板设计人员需要考虑材料的硬度、强度、韧性等的性能。
我公司现有这方面的标准有Q/SQR.04.137(PP+T20和PP+EPDM-T20),其他的标准有待进一步完善。
和其它内饰件产品一样,立柱护板满足内饰件统一的成品性能要求,燃烧特性(GB8410),耐光色牢度(QBV.06.1303),气味试验(QBV.06.3900),甲醛含量(QBV.06.3925),冷凝成份,有机化合物等。
1.2 立柱护板的工艺常见立柱护板有注塑工艺和注塑件表面包覆面料工艺。
还有压铸成型的麻纤维材料的立柱护板。
立柱护板包布工艺:注塑-表面喷胶-覆布-切割-修边1.3成本构成成本主要由设计费用、原材料费用、模具和工装,检具等开发费用构成,三种工艺对比而言,麻纤维压铸和注塑成型价格差不多,但包布工艺需要增加约1.5倍的价格。
1.4 立柱护板的结构立柱护板一般都是采用背面设计安装座,通过塑料固定卡子和车身内板安装孔固定在一起,对于C柱和D 柱连接在一起的大立柱护板(如T11车C柱护板),背面设计塑料加强卡片用弹簧钢片固定在车身孔上,同时还采用自攻螺钉和膨胀螺钉固定。
也可才有内部填充网状物的结构方式增加强度和韧性。
下图是B14立柱护板的简图:主要包括:A柱上、下护板,三角窗装饰面板、B柱上、下护板,C柱上护板、D柱上护板,安全带调整滑板、前后门门槛踏板、门槛压板。
J013_车门内护板设计规范标准
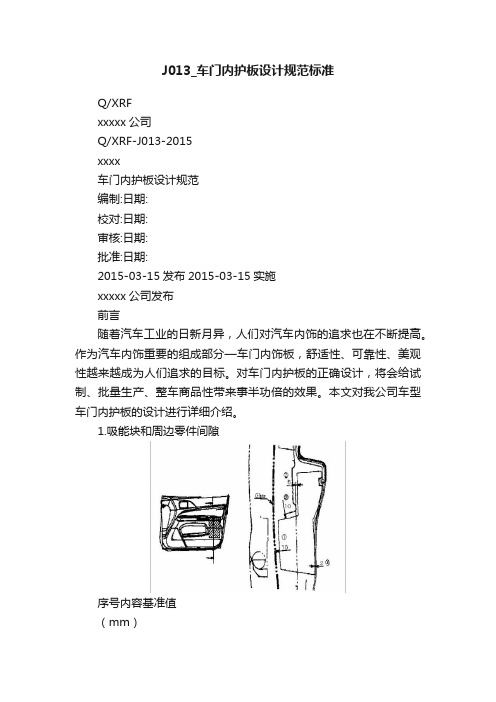
J013_车门内护板设计规范标准Q/XRFxxxxx公司Q/XRF-J013-2015xxxx车门内护板设计规范编制:日期:校对:日期:审核:日期:批准:日期:2015-03-15发布2015-03-15实施xxxxx公司发布前言随着汽车工业的日新月异,人们对汽车内饰的追求也在不断提高。
作为汽车内饰重要的组成部分—车门内饰板,舒适性、可靠性、美观性越来越成为人们追求的目标。
对车门内护板的正确设计,将会给试制、批量生产、整车商品性带来事半功倍的效果。
本文对我公司车型车门内护板的设计进行详细介绍。
1.吸能块和周边零件间隙序号内容基准值(mm)1 与车窗玻璃的间隙102 与车门内板便面的间隙 53 与车门内板孔的间隙104 与车门内饰的间隙 22.内扣手的设定标准3.M/W 调节器手柄设定标准序号内容基准值(mm )参考 1 I/S 扣手长度<685 最大限度760mm 2 从OPONING 开始的位置>480 最小限度420mm3 竖立把手开始位置 120~1404 扣手盖板周围间隙(前后方向)2 5 扣手盖板周围搭接量 1 6 扣手盖板周围间隙(上下方向)3 7扣手盖板周围间隙(上下方向)24.电动控制钮的设定标准序号内容基准值(mm )参考 1 调节器手柄的长度<670 2 从乘坐参考点开始到扣手中心高度>1303 与车门储物盒的距离>1604 与肘靠的距离>90 4与肘靠的距离>60应用参考手册表面高度 5 与仪表板的距离>1306从坐姿的距离参照左图5.肘靠的设定标准序号内容基准值(mm )参考1 对应室内冲击必要条件的场合>2 in 纵面倾斜15°以内 2对应室内内部突出物必要条件的场合>R3.5适合范围清参考上图*1 推荐高度=(0.6+30)+SEAT BACK ANGLE修正值±10上限高度=0.6d+50 下限高度=0.6d1 电动控制钮的长度 625~7252 从把手开始的距离>1403 从把手开始的角度<18 4 前后倾斜角0~10° 前面提升至10° 5左右倾斜角0~5° ARM 表面高度6与内饰表面的距离≥25序号内容基准值(mm)参考1 肘靠上面的高度(H)根据*1计算式从SRP(JM50%)开始2 肘靠长度(SRP的前侧)170±20 SRP(JM50%)3 同上(SRP的后侧)110±20 同上4 ARMREST上面的前后倾斜5~6度5 ARMREST上面的左右倾斜0~5度6 ARMREST上面的宽度>707 室内冲击吸收方式侧面宽度15 θ3<15°6.缝隙间的设定标准序号内容基准值(mm)参考1 与仪表板的缝隙 52 视觉补正上图参考3 与SASH的缝隙 24 与UPPER和LOWER的搭接尺上图参考寸序号内容基准值(mm)参考1 车门内饰与B柱装饰件的间隙 5 水平方向2 车门内饰与B柱装饰件的间隙 5 车副方向3 抽取倾斜角10度54 车门内板的突出部分与内饰的间隔注意:2.从OPNING的缝隙不应该看见车体的颜色7.操作性的设定标准序号内容基准值1 拖拽把盒水平把手区域:R1 <5002 拖拽把盒水平把手区域:R2 >4003 拖拽把盒水平把手区域:R3 <4004 拖拽把盒水平把手区域:R4 <10005 纵把手区域:R1 <5206 纵把手区域:R2 400~5007 纵把手区域:R3 <10008 纵把手高度:H 200~270 9 纵把手区域:R3 68~78度序号内容基准值(mm)参考1 车门内饰与座椅坐垫的缝隙>60 极限值50mm2 车门内饰与储物盒之间的缝西>55 极限值40mm3 门在打开情况下的乘降空间>3004 座椅靠背与扶手的间隙>255 座椅操作杆操作空间>408.扬声器网格的设定标准序号内容基准值(mm)参考1 网格部位的开口率40%2 网格部位的开口率(TWEETER)50% 高音用9.踏板照明的设定标准序号内容基准值(mm)参考1 开启门的可视角度15度2 脚下的可视性(着地点亮光度)3L3 脚下的可视范围上图参考10.乘车性的设定标准序号内容基准值(mm)参考1 从SRP到前车门内饰的距离310~360 极限值290mm2 从SRP到后车门内饰的距离330~380 极限值310mm3 玻璃升降器摇把与膝盖的关系上图参照11.拖拽把手的设定标准序号内容基准值(mm)参考1 把手部位的长度100~1202 把手部位的宽度30~403 手抠(BOX)部位的深度>554 把手部位的粗度:h 25~354 把手部位的粗度:b 20~255 手抠(BOX)部位的角度-8度极限值13度6 拖拽把手的位置50~1507 把手部位的刚性6kg12.纵把手的设定标准序号内容基准值(mm)参考1 从SRP到把手的距离350±502 角度60~70度3 把手部位的粗度20~254 有效长度>1105 到玻璃升降器摇把的距>90 离6 P/W控制钮间隔的距离>807 从把手区域<52013.储物盒的设定标准序号内容基准值(mm)参考1 宽(尽可能做大)40 地图的厚度+52 高度100 EU:703 长度320 地图长度+104 地图收纳状态上图参照1:加强筋一般布置5~6根,筋厚0.5mm2:在有加强筋区域内可以适当的增加料厚0.3~0.4mmLD DOOR TRIMCOPOLLA DOOR TRIMXD DOOR TRIMRS FACE LIFT DOOR TRIMBL DOOR TRIMGQ DOOR TRIM14.车用密封条操作指南车用3M胶1.概述本操作指南适用于用压敏胶带把橡胶密封条装配到汽车和卡车的操作工艺。
J013车门内护板设计规范_1
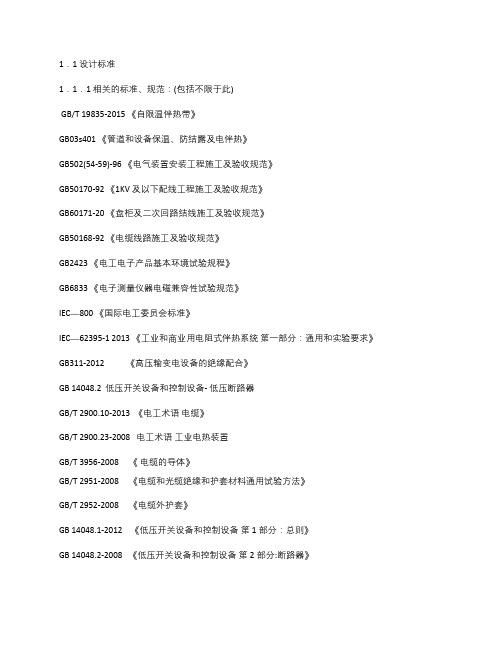
1.1 设计标准1.1.1 相关的标准、规范:(包括不限于此)GB/T 19835-2015 《自限温伴热带》GB03s401 《管道和设备保温、防结露及电伴热》GB502(54-59)-96 《电气装置安装工程施工及验收规范》GB50170-92 《1KV 及以下配线工程施工及验收规范》GB60171-20 《盘柜及二次回路结线施工及验收规范》GB50168-92 《电缆线路施工及验收规范》GB2423 《电工电子产品基本环境试验规程》GB6833 《电子测量仪器电磁兼容性试验规范》IEC—800 《国际电工委员会标准》IEC—62395-1 2013 《工业和商业用电阻式伴热系统第一部分:通用和实验要求》GB311-2012 《高压输变电设备的绝缘配合》GB 14048.2 低压开关设备和控制设备- 低压断路器GB/T 2900.10-2013 《电工术语电缆》GB/T 2900.23-2008 电工术语工业电热装置GB/T 3956-2008 《电缆的导体》GB/T 2951-2008 《电缆和光缆绝缘和护套材料通用试验方法》GB/T 2952-2008 《电缆外护套》GB 14048.1-2012 《低压开关设备和控制设备第1部分:总则》GB 14048.2-2008 《低压开关设备和控制设备第2部分:断路器》GB14048.3-2008 《低压开关设备和控制设备第3部分: 开关、隔离器、隔离开关以及熔断器组合电器》如使用上述以外的标准和规范时,应加以说明。
1.2 管道电伴热设置范围无采暖区域的消防管道和生活给水管道,管道维持温度为 5℃。
1.3 基本要求1.3 . 1电伴热系统供货范围包括发热电缆及附件(不锈钢扎带、高温纤维胶带、温控探头、温度控制器、电源接线盒、两通、三通、尾端等)、并负责安装调试。
投标者应对所投产品的结构、技术特性、制作工艺、相关参数、执行的技术标准给予详细的描述和说明。
汽车内饰零件通用技术条件(塑料件要求)
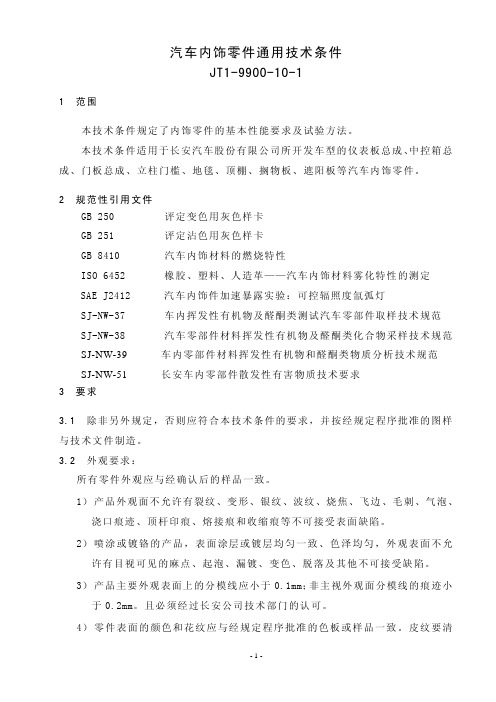
汽车内饰零件通用技术条件JT1-9900-10-11 范围本技术条件规定了内饰零件的基本性能要求及试验方法。
本技术条件适用于长安汽车股份有限公司所开发车型的仪表板总成、中控箱总成、门板总成、立柱门槛、地毯、顶棚、搁物板、遮阳板等汽车内饰零件。
2 规范性引用文件GB 250 评定变色用灰色样卡GB 251 评定沾色用灰色样卡GB 8410 汽车内饰材料的燃烧特性ISO 6452 橡胶、塑料、人造革——汽车内饰材料雾化特性的测定SAE J2412 汽车内饰件加速暴露实验:可控辐照度氙弧灯SJ-NW-37 车内挥发性有机物及醛酮类测试汽车零部件取样技术规范SJ-NW-38 汽车零部件材料挥发性有机物及醛酮类化合物采样技术规范 SJ-NW-39 车内零部件材料挥发性有机物和醛酮类物质分析技术规范SJ-NW-51 长安车内零部件散发性有害物质技术要求3 要求3.1 除非另外规定,否则应符合本技术条件的要求,并按经规定程序批准的图样与技术文件制造。
3.2 外观要求:所有零件外观应与经确认后的样品一致。
1)产品外观面不允许有裂纹、变形、银纹、波纹、烧焦、飞边、毛刺、气泡、浇口痕迹、顶杆印痕、熔接痕和收缩痕等不可接受表面缺陷。
2)喷涂或镀铬的产品,表面涂层或镀层均匀一致、色泽均匀,外观表面不允许有目视可见的麻点、起泡、漏镀、变色、脱落及其他不可接受缺陷。
3)产品主要外观表面上的分模线应小于0.1mm;非主视外观面分模线的痕迹小于0.2mm。
且必须经过长安公司技术部门的认可。
4)零件表面的颜色和花纹应与经规定程序批准的色板或样品一致。
皮纹要清晰、色泽均匀,皮纹类型、纹理方向、纹理深度以及皮纹范围应与长安公司所要求的一致,由于因脱模方向引起的非主要表面皮纹深度变化要均匀,不允许出现皮纹拉伤。
3.3 性能要求序号试验项目性能要求试验方法3.3.1 阻燃性满足GB 8410的要求4.13.3.2 耐辐照高温性(仅针对仪表板上本体、搁物板及安装于仪表板、搁物板水平表面上的零件,要求与仪表板一起进行试验)试验过程中及试验后,产品不得出现可见颜色或光泽变化、裂纹、难闻气味、分层、起泡、收缩、翘曲变形、增塑剂析出、皱褶、卷边等缺陷及其他任何影响正常使用的缺陷。
客车内饰板常见装配方式分析

客车内顶板常见装配方式分析摘要:通过对现有客车整车内顶板常见装配方式的介绍,分析装配过程中操作方法及质量控制关键点关键词:客车内顶板装配方式质量控制随着长春整车的发展,内饰顶板的装配方式多样化增多,现需要将内饰顶板装配方式做整理分析汇总来进一步提高产品质量和生产效率。
一、客车顶板固定方法客车内顶板根据表面材质可分为硬质护面结构和软质护面结构。
软质护面结构又可分为分块式表面附革和整体式两种。
硬质护面多采用胶合板或纤维板。
在结构上采用分块式,即按照板材规格(整幅2440x1220mm采购),在提高材料利用率的前提下将护面分成若干块,块与块之间在车身骨架上搭接并用压条固定,最大优点是便于装配和更换,目前代表车型为12米公交车750。
软质护面中的整体连续内饰顶板多为蜂窝板+PUR发泡+PVC革,外购件定尺采购,来料不需要加工,直接装配,目前代表车型为10.5米团体车89Z;软质护面中分块式表面附革顶板指底层材质为分段式胶合板安装,然后表面附革,目前代表车型为8.6米团体车88Z。
对于不同结构的内饰护板,所采取的安装工艺也不相同。
(一)顶板左右侧面固定方式有两种:a.卡接式(图一) b.压接式(图二)a.卡接式连接即顶板的左右两侧通过卡入相邻型材槽内固定,要求卡入深度≮卡槽深度-2mm。
b.压接式连接即顶板的左右两侧通过扣式压条底座和顶盖固定,式压条用自攻钉固定到安装位。
(二)顶板前后端面固定方式有两种:c.卡接式(图三) d.压接式(形状同图二) (三)顶板之间连接方式分为两种:e.卡接式(图四) f.压接式(形状同图二)二、硬质护面顶板装配方法具体介绍(一)顶板固定方式全为卡接式(ace组合)安装方法1.1在木工房将顶板按照产品要求下料修形并开出安全天窗、空调回风口等尺寸位置,要求切口平直,周边无毛刺,对于圆形孔位要用正确的开孔器开孔,开孔后不得划伤表面(铝扣板开孔后表面平整,不得有凹坑等)卡接式顶板下料时长度和宽度尺寸不能过小,要求装配后卡入滑槽深度符合要求。
客车封板、地板、隔音降噪设计规范

• 4.5、板簧位置、气簧位置、减震器连接位置开检修口,发动机油泵 位置开检修口,尽量使用现有的检修门(盖)。
• 设计原则,优先使用检修门,其次使用检修盖;
• 4.6、 踏步封板设计要满足《客车结构安全要求》,内容如下:
• 4.6.1、 乘客门及车内乘客踏步的最大高度、最小高度(车身降低系 统不工作)及最小深度见(表1)及(图6)。
1
2
4 3
• 1.2.3、测试结果:
• 2、车外噪音篇
• 由于俄罗斯认证门槛越来越高,对于车型整车性能要求越来越高,对 于车外噪音一项,采用Henkel吸音材料用在UC2认证样车上,以下是 方案:
• 1)发动机舱增加NA120S吸音泡沫材料;
• 2)发动机底部增加下档板,且下档板加装DH20隔音片和NA120S 吸音材料
• 4.6.5、 其他踏步处,每级踏步可以延伸到相邻踏步的垂直投影区最 多100 mm,且下级踏步的投影应至少保留200mm深度的自由表面见 (表2)和(图6)。所有踏步外边缘的设计应最大程度降低乘客绊倒 的风险且有明显的颜色标记。
图6
• 4.5.7、 踏步的尺寸应满足:在每级踏步上放置(表2)给出的对应矩 形时,矩形超出踏步部分的面积不得大于5%。双引道门处的踏步, 其每一半应分别满足此要求。
客车封板、地板、隔音降噪设计
一、封板
• 1、封板分类:封板按照装配位置不同,可分为:地板封板、仓封板、 轮罩封板等。
• 2、封板设计依据:封板的设计需要参照车身室车身地板骨架总成及 各分总成图纸。
• 3、封板设计的具体流程:总布置指定设计任务书,系统相关底盘系 统提供相关系统布置图、相关系统检修位置、跳动尺寸、管线孔等, 提供给车身室,封板设计人员提前与车身设计工程师协调易于封板装 配的骨架结构,车身设计工程师设计整车骨架总成图,封板设计工程 师根据完善后的图纸设计封板。
汽车内饰件国家标准
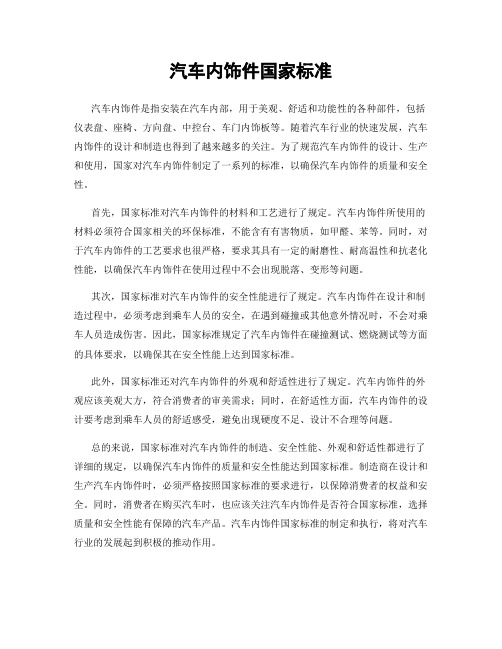
汽车内饰件国家标准汽车内饰件是指安装在汽车内部,用于美观、舒适和功能性的各种部件,包括仪表盘、座椅、方向盘、中控台、车门内饰板等。
随着汽车行业的快速发展,汽车内饰件的设计和制造也得到了越来越多的关注。
为了规范汽车内饰件的设计、生产和使用,国家对汽车内饰件制定了一系列的标准,以确保汽车内饰件的质量和安全性。
首先,国家标准对汽车内饰件的材料和工艺进行了规定。
汽车内饰件所使用的材料必须符合国家相关的环保标准,不能含有有害物质,如甲醛、苯等。
同时,对于汽车内饰件的工艺要求也很严格,要求其具有一定的耐磨性、耐高温性和抗老化性能,以确保汽车内饰件在使用过程中不会出现脱落、变形等问题。
其次,国家标准对汽车内饰件的安全性能进行了规定。
汽车内饰件在设计和制造过程中,必须考虑到乘车人员的安全,在遇到碰撞或其他意外情况时,不会对乘车人员造成伤害。
因此,国家标准规定了汽车内饰件在碰撞测试、燃烧测试等方面的具体要求,以确保其在安全性能上达到国家标准。
此外,国家标准还对汽车内饰件的外观和舒适性进行了规定。
汽车内饰件的外观应该美观大方,符合消费者的审美需求;同时,在舒适性方面,汽车内饰件的设计要考虑到乘车人员的舒适感受,避免出现硬度不足、设计不合理等问题。
总的来说,国家标准对汽车内饰件的制造、安全性能、外观和舒适性都进行了详细的规定,以确保汽车内饰件的质量和安全性能达到国家标准。
制造商在设计和生产汽车内饰件时,必须严格按照国家标准的要求进行,以保障消费者的权益和安全。
同时,消费者在购买汽车时,也应该关注汽车内饰件是否符合国家标准,选择质量和安全性能有保障的汽车产品。
汽车内饰件国家标准的制定和执行,将对汽车行业的发展起到积极的推动作用。
UIC_844-4

e<0.9mm 10mm 15mm 40mm 60mm
0.9mm≤e<1.3mm 5mm 8mm 25mm 45mm
1.3mm≤e<3mm 3mm 6mm 15mm 12mm 30mm 24mm
3mm≤e<6mm 2mm 3mm 6mm 5mm 9mm 7.5mm
6mm≤e
(1)
(1)
(1)由供货方和购买铁路协议规定。
名义厚度(e) e≤1.2mm ………………………………………………………………… ±0.1 mm 1.2mm<e≤1.5mm ………………………………………………………………… ±0.12mm 1.5mm<e≤ 2 mm ………………………………………………………………… ±0.15mm 2.0 mm<e≤ 3mm ………………………………………………………………… ±0.2 mm 3 mm<e≤ 4 mm ………………………………………………………………… ±0.25mm 4 mm<e≤ 6 mm ………………………………………………………………… ±0.3 mm 6 mm<e ………………………………………………………………………由供货方和铁
依照购买铁路定单或附件中的规定 顺着层压板方向切 250×10×e* 横切 250×10×e* 圆板,直径 130mm ×e, 或 120×120×e* 230×230×e* 120×50×e
*
平坦度
4.1.4.1.4
耐磨性 耐冲击性 耐开裂性 耐划伤性 可成型性
3 3 2 4 4 4 6 6 3 2 1 3 2 3 依照购买铁路说明,若 物说明则依照定单或其 附件中的规定
2
路买方双方协 议规定 另外,任意一块层压板上间距小于 1m 的两点之间的厚度变化不得超过 0.2mm。 2.1.1.3 平坦度 对于 A 类(预制件)和 B 类层压板,其允许的翘曲度应小于或等于以下值:
- 1、下载文档前请自行甄别文档内容的完整性,平台不提供额外的编辑、内容补充、找答案等附加服务。
- 2、"仅部分预览"的文档,不可在线预览部分如存在完整性等问题,可反馈申请退款(可完整预览的文档不适用该条件!)。
- 3、如文档侵犯您的权益,请联系客服反馈,我们会尽快为您处理(人工客服工作时间:9:00-18:30)。
3.4.1 外观应符合表1规定。
表1 外观要求
序号
项目
规 定
1
颜色及皮纹
颜色均匀,无杂色。皮纹符合设计要求。
2
厚度
厚度均匀,厚度偏差为±0.1 mm。
3
翘曲度
展开2 m长其翘曲度应不大于10 mm
4
针孔
在3 m长内小于或等于0.5 mm的孔不应超过一个,大于0.5 mm的针孔不允许有
c)双复仿皮,内侧复合纱布和海绵的PVC仿皮。结构为仿皮+纱布+3mm海绵+纱布。
d)特种复合仿皮,内侧复合无纺布的PVC仿皮。
3.2.2 硬质纤维板与PVC仿皮采用84号胶粘接,周边采用工业用装璜钉联接。
3.2.3 ABS板材、麻粘板与PVC仿皮采用高温辊压粘接。
3.3 性能要求
3.3.1 聚氯乙烯装饰膜与内衬板贴合牢固,表面平整、光洁,无压痕、无褶皱、无裂纹。
GB/T 9846.3 胶合板 第3部分:普通胶合板通用技术条件
GB/T 9846.4 胶合板 第4部分:普通胶合板外观分等技术条件
GB/T 10009 丙烯脯-丁二烯-笨已烯(ABS)塑料挤出板材
GB/T 10111 利用随机数骰子进行随机抽样的方法
GB/T 12626.2硬质纤维板技术要求
GB/T 12626.6硬质纤维板含水率的测定
2 规范性引用文件
下列文件中的条款通过本标准的引用而成为本标准的条款。凡是注日期的引用文件,其随后所有的修改单(不包括勘误的内容)或修订版均不适用于本标准,然而,鼓励根据本标准达成协议的各方研究是否可使用这些文件的最新版本。凡是不注日期的引用文件,其最新版本适用于本标准。
GB 8410 汽车内饰材料的燃烧特性
3.2 内饰护板的材料
3.2.1 内饰护板的基体材料为ABS板、麻粘板、硬质纤维板或胶合板,护板蒙皮材料为聚氯乙烯装饰膜,聚氯乙烯装饰膜采用PVC发泡挤压成型、表面皮纹(PVC仿皮)。PVC仿皮有以下几种型式:
a)无复合仿皮,仿皮内侧无任何复合物的PVC仿皮。
b)单复仿皮,内侧复合单层纱布的PVC仿皮。
5
漏涂
不允许
6
料柱痕
不应有明显的料柱痕
7
气痕
不应有明显的气痕
8
光泽斑
不应有明显的光泽斑
9
附着杂质
不允许有0.6 mm以上杂质,0.3 mm~0.5 mm以上的杂质每平方米不得超过1个
3.4.2 物理机械性能应符合表2规定。
表2 物理机械性能
序号
项 目
指 标
1
拉伸强度,MPa
≥12
2
断裂伸长率,%
≥150
客车内饰护板技术条件
前 言
本标准是根据相关标准,结合本公司客车产品用内饰护板的实际情况,为满足采购、生产和质量检验的需要,保证产品质量而制定的。本标准是对Q/XXA004—2000《客车侧围护板技术条件》的修订。
本标准与Q/XXA004—2000相比在技术内容上主要存在以下差异:
——调整了标准的适用范围,适用于客车内装饰用各类内饰护板。
3.5.3 ABS板板材表面应光滑平整,不允许有影响使用有波纹、亏料痕、划痕、黑点和杂质;不允许有气泡和裂纹。
3.5.4 ABS板物理力学性能应符合表5规定。
表5 物理力学性能
指标项目
指标
拉伸屈服应力(纵、横),MPa
≥32
冲击强度(纵、横),J/m
≥88.0
球压痕硬度,N/mm2
≥65.0
维卡软化温度,℃
≥90
温度变形率,%
≤0.5
3.5.5 麻粘板外观质量要求:
不允许有水渍、污点、斑纹、粘痕、压痕、分层、鼓泡、裂开痕、边角松软等缺陷
3.5.6 麻粘板物理力学性能应符合表6规定
表6 物理力学性能
指标项目
指标要求
密度, g/cm2
>2000~2600
——增加了PVC内饰仿皮的技术要求。
——增加了ABS板复合PVC内饰仿皮的性能要求。
客车内饰护板技条件
1 范围
本标准规定了客车用内饰护板的技术要求、试验方法、检验规则、标志,包装、运输与贮存。
本标准适用于本公司客车产品用ABS板、麻粘板及硬质纤维板和胶合板复合聚氯乙烯装饰膜内饰护板(以下简称内饰护板)。
≥10
伸长率,%
≥120
12
耐候性
在-45 ℃~80 ℃范围内温度变化,表面不出现开裂或脆化
13
剥离负荷
≥15或不能剥离
3.4.3 PVC仿皮的燃烧特性应符合GB 8410的规定。
3.5 内饰护板基体材料性能要求。
3.5.1 硬质纤维板的外观质量应符合表3规定。
表3 外观质量
缺陷名称
计量方法
允许限度
3
直角撕裂强度,kN/m
≥40
4
尺寸变化率,% (纵/横)
≤8.0/≤2.0
5
加热损失率,%
≤2.0
6
耐摩擦色牢度,级
≥4
7
压花保持性
花纹清晰
8
耐光性,级
≥3
9
光泽度(60°),光泽单位
≤4.0
表2(续) 物理机械性能
序号
项 目
指 标
10
单位面料重量,kg/m2
0.6~0.8
11
热老化性能
拉伸强度,MPa
特级
一级
二级
三级
水渍
占板面积百分比,%
不允许有
≤2
≤20
≤40
污点
直径,mm
不允许有
≤15
≤30,小于15不计
每平方米个数,个/m2
≤2
≤2
斑纹
占板面积百分比,%
不允许有
≤5
粘痕
占板面积百分比,%
不允许有
≤1
压痕
深度或高度,mm
不允许有
≤0.4
≤0.6
每个压痕面积,mm
≤20
≤400
任意每平方米个数,个/mm
≤2
≤2
分层、鼓泡、裂痕、水湿炭化、边角松软
——
不允许
3.5.2 硬质纤维板物理力学性能应符合表4规定。
表4 物理力学性能
指标项目
特级
一 级
二 级
三 级
密度, g/cm
>0.80
静曲强度,MPa
≥49.0
≥39.0
≥29.0
≥20.0
吸水率,%
≤15.0
≤20.0
≤30.0
≤35.0
含水率,%
3.0~10.0
3.3.2ABS板材与PVC仿皮成型内饰件在空气温度-40℃~+70℃,空气湿度≥50%,正常使用条件下,三年内不应出现开裂、脱层、气泡等现象。
3.3.3 麻毡与PVC仿皮压制成型件应进行防潮处理,在空气湿度≥50%,碱性(海滨城市),正常使用条件下,三年内不得脱皮、起泡、分层等现象。
3.3.4 有害气体释放量应符合相关企业标准的要求。
GB/T 12626.7硬质纤维板密度的测定
GB/T 12626.8硬质纤维板吸水率的测定
GB/T12626.9硬质纤维板静曲强度的测定
QB/T 2028 软聚氯乙烯装饰膜(片)
Q/XXB102 车辆产品零部件可追溯性标识规定
3 技术要求
3.1 内饰护板应按照经规定程序批准的图样和技术文件制造,并符合本标准要求。