熔模铸造水玻璃工艺
水玻璃精铸工艺流程

水玻璃精铸工艺流程Water glass precision casting process, also known as investment casting, is a complex and intricate manufacturing method that has been used for centuries to produce high-quality metal parts. This process involves creating a wax pattern, investing the pattern in a ceramic shell, melting out the wax, and then pouring molten metal into the shell to create the final casting.水玻璃精铸工艺流程,也被称为投资铸造,是一种复杂而精密的制造方法,几个世纪以来一直被用来生产高质量的金属零件。
这个过程涉及到制作蜡模,把模型投入陶瓷壳内,熔掉蜡模,然后将熔化的金属倒入壳内,形成最终的铸件。
One of the key advantages of the water glass precision casting process is its ability to produce highly detailed and complex parts with excellent surface finish. This makes it an ideal method for producing components with intricate geometries or fine details, such as turbine blades, jewelry, or medical implants.水玻璃精铸工艺流程的一个关键优点是它能够生产具有极高细节和复杂度的零件,并且具有优良的表面光洁度。
水玻璃铸造

水玻璃铸造1. 概述水玻璃铸造是一种常见的金属铸造技术,也被称为硅酸钠铸造。
通过使用水玻璃(硅酸钠)作为粘结剂,将骨料与金属颗粒结合在一起,形成一个可铸造的模具。
这种铸造方法广泛应用于工业制造中,包括汽车、机械和航空航天等行业。
2. 水玻璃铸造的工艺步骤水玻璃铸造的过程可以分为以下几个步骤:2.1. 制备模具首先,根据需求设计和制造模具。
模具可以采用硅胶、金属或其他材料制成,以确保模具的精确度和耐用性。
2.2. 准备骨料骨料是水玻璃铸造中的重要组成部分,它可以是石英砂、氧化铝、石膏等材料。
根据具体的铸造要求,选择不同的骨料进行混合。
2.3. 涂抹水玻璃将水玻璃与适量的水混合,并使用刷子将混合物均匀地涂抹在模具表面。
水玻璃的涂抹层应具有一定的厚度,以确保模具的强度和耐用性。
2.4. 添加骨料将预先准备好的骨料均匀地撒在涂抹水玻璃的模具上。
骨料的厚度和数量应根据具体的铸造要求加以调整。
2.5. 铸造金属将要铸造的金属熔化,并将熔融金属缓慢地倒入模具中。
在铸造过程中,注意控制金属的温度和倒注速度,以确保铸件的质量和形状。
2.6. 冷却和处理待金属冷却后,将模具打开,取出铸件。
铸件将会稍微变形,需要进行后续的研磨和处理,以达到客户要求的尺寸和表面质量。
3. 水玻璃铸造的优势和应用水玻璃铸造具有以下几个优势:•成本低:模具制造和骨料的成本相对较低,可大幅降低铸造成本;•高精度:水玻璃铸造能够制造出高精度和复杂的铸件,满足不同行业的需求;•环保:与其他一些铸造方法相比,水玻璃铸造过程中产生的废气和废水较少。
水玻璃铸造广泛应用于各个行业,包括:•汽车制造:发动机零部件、底盘配件等;•机械制造:齿轮、轴承等;•航空航天:飞机引擎零部件、航天器结构件等。
4. 总结水玻璃铸造是一种常见且在工业制造中广泛应用的金属铸造技术。
通过将水玻璃作为粘结剂,骨料与金属颗粒结合在一起,形成可铸造的模具。
水玻璃铸造具有成本低、高精度和环保等优势,并被广泛应用于汽车、机械和航空航天等行业。
水玻璃熔模铸造介绍

水玻璃熔模铸造介绍变量和公差熔模铸造又称“失蜡铸造”,通常是在蜡模表面涂上数层耐火材料,待其硬化干燥后,将其中的蜡模熔去而制成型壳,再经过焙烧,然后进行浇注,而获得铸件的一种方法。
由于获得的铸件具有较高的尺寸精度和表面光洁度,故又称“熔模精密铸造”。
可用熔模铸造法生产的合金种类有碳素钢、合金钢、耐热合金、不锈钢、精密合金、永磁合金、轴承合金、铜合金、铝合金、钛合金和球墨铸铁等。
熔模铸件的形状一般都比较复杂,铸件上可铸出孔的最小直径可达0.5mm,铸件的最小壁厚为0.3mm。
在生产中可将一些原来由几个零件组合而成的部件,通过改变零件的结构,设计成为整体零件而直接由熔模铸造铸出,以节省加工工时和金属材料的消耗,使零件结构更为合理。
熔模铸件的重量大多为零点几十牛(即几十克到几公斤),太重的铸件用熔模铸造法生产较为麻烦,但目前生产大的熔模铸件的重量已达800牛左右。
溶膜铸造是用易熔材料制成模型,然后在模型上涂挂耐火材料,经硬化后,在将模型熔化排出型外,从而获得无分型面的铸型,铸型焙烧后即浇注。
一. 工艺过程:1. 蜡模制作1) 压型:制蜡模的专用模具、钢、铜、铝、切削而成2) 蜡模的压制:石蜡、峰蜡、硬脂酸、松香等,将熔化的蜡料压入压型中,冷凝后取出,修去毛刺,得到蜡模3) 蜡模组装:若干蜡模焊在一个直浇棒上2. 结壳:蜡模涂上涂料、硬化、干燥等1) 浸涂料(石英粉+粘结剂的糊状物)表面光洁2) 撒砂(粗石英砂)的目的:增厚型壳3) 硬化(水玻璃+NH4CL—SIO2)化学硬化3. 脱蜡、焙烧1) 脱蜡:热水或水蒸气2) 焙烧:加热800~1000℃提高型壳强度4. 填砂:浇注1) 填砂:型壳放入铁箱中,周围干砂充填2) 浇注:趁热(600~700℃)进行浇注5. 落砂清理冷却后,破坏型壳,取出铸件,去浇口、毛刺、退火或正火,以便得到所需机械性能1) 铸造精度、光洁度高、且可浇注形状复杂的件2) 能铸造各种合金(型壳是高级耐火材料)3) 单件、小批、大批量生产均可4) 少无切削加工(Ra3.2~1.6um)稍磨5) 材料贵,工艺过程繁杂,生产周期长应用:使用高熔点合金精密铸件的成批、大量生产,形状复杂,难以切削加工的小零件。
水玻璃铸造工艺
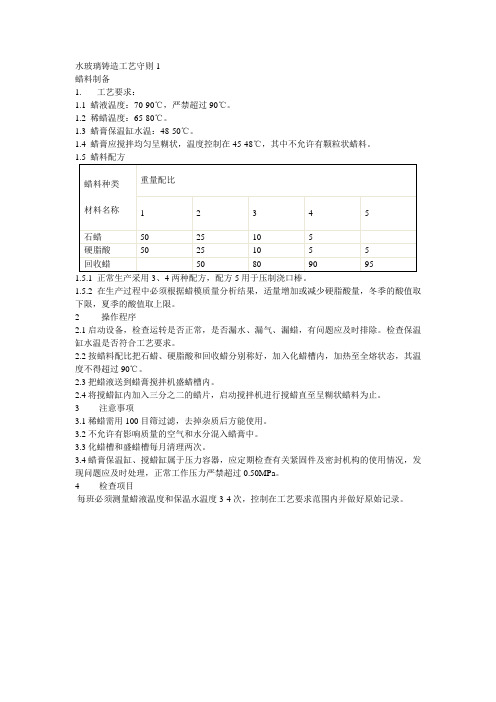
水玻璃铸造工艺守则1蜡料制备1. 工艺要求:1.1 蜡液温度:70-90℃,严禁超过90℃。
1.2 稀蜡温度:65-80℃。
1.3 蜡膏保温缸水温:48-50℃。
1.4 蜡膏应搅拌均匀呈糊状,温度控制在45-48℃,其中不允许有颗粒状蜡料。
1.5.1 正常生产采用3、4两种配方,配方5用于压制浇口棒。
1.5.2 在生产过程中必须根据蜡模质量分析结果,适量增加或减少硬脂酸量,冬季的酸值取下限,夏季的酸值取上限。
2 操作程序2.1 启动设备,检查运转是否正常,是否漏水、漏气、漏蜡,有问题应及时排除。
检查保温缸水温是否符合工艺要求。
2.2 按蜡料配比把石蜡、硬脂酸和回收蜡分别称好,加入化蜡槽内,加热至全熔状态,其温度不得超过90℃。
2.3 把蜡液送到蜡膏搅拌机盛蜡槽内。
2.4 将搅蜡缸内加入三分之二的蜡片,启动搅拌机进行搅蜡直至呈糊状蜡料为止。
3 注意事项3.1 稀蜡需用100目筛过滤,去掉杂质后方能使用。
3.2 不允许有影响质量的空气和水分混入蜡膏中。
3.3 化蜡槽和盛蜡槽每月清理两次。
3.4 蜡膏保温缸、搅蜡缸属于压力容器,应定期检查有关紧固件及密封机构的使用情况,发现问题应及时处理,正常工作压力严禁超过0.50MPa。
4 检查项目每班必须测量蜡液温度和保温水温度3-4次,控制在工艺要求范围内并做好原始记录。
蜡模制造1 工艺要求1.1 室温:16-28℃(最高不超过30℃)。
1.2 蜡膏压注温度:45~48℃,压力:0.3~0.5 MPa,保压时间:3~10秒。
1.3 压蜡冷却水温,14~24℃,冷却时间:20~100秒。
1.4蜡模冷却水温,14~24℃,冷却时间:10~60min。
1.5蜡模清洗液温度,20~28℃,清洗液中加入0.01% JFC。
1.6 脱模剂:ZF201.1.7蜡模表面光洁度,形状完整,轮廓清洗,尺寸合格,不允许有缩陷,凸包裂纹等缺陷。
2 操作程序2.1 手工制模2.1.1检查压型的分型面、型腔、脱模机构、定位销、紧固件应完整清洁。
水玻璃铸造件工艺是怎样的

水玻璃铸造件工艺是怎样的前言水玻璃铸造作为一种先进制造技术,可以用于制造一些特殊形状、结构复杂、装配性好的铸造件。
本文将对水玻璃铸造件的工艺流程、特点以及应用进行介绍。
工艺流程模具制作水玻璃铸造的模具一般使用铝合金或者树脂模具。
首先需要将铸造件的3D模型设计完成,并根据其尺寸及目标成型形状制作出实体模型。
此后,在实体模型的基础上,进行模仁制造、模具制造,完成模具的制作。
模具涂覆该工艺常采用一个叫“水玻璃”或“硅酸钠”的组分来涂覆模具表面,然后在经过一定的加热后,在模具内壁形成一层坚硬、不易脱落的薄层。
将模具各分支及与铸件接触面涂覆均匀,以防止在铸造过程中涂层被拱起或断裂。
铸造铸造时先将模具加热至一定温度,然后用水玻璃与固定比例的铸造砂混合均匀,倒入模具中,并在一定时间内震实,将涂覆在模具表面的水玻璃及铸造砂干燥结合,形成坚固的铸造件。
后处理铸造完成后需要进行后处理,主要包括去砂、热处理、机加工等步骤。
在热处理过程中,可以改善铸造件的力学性能和物理性能,提高其强度和耐磨性等指标,而机加工可以进一步加工出更为精细的形状和尺寸。
特点精度高水玻璃铸造件的精度很高,所铸铸件表面光滑,良好的整体性和精准的尺寸,最大限度地保证了铸件的密封性。
安全、环保硅酸钠是一种绿色环保的化学品,故其在水玻璃铸造过程中并不会产生有毒气体和其他污染物,因此是一种安全、环保的铸造法。
复杂件铸造水玻璃铸造可以铸造出形状较为复杂、结构复杂、设计合理、装配性好的、高强度、高耐热、高抗蚀的特种铸造件,适用于船舶、矿山、重工业和冶金等领域。
应用目前,水玻璃铸造技术已广泛应用于各个行业,其中最为常见的即是机械领域的部分零部件生产,例如大型漏斗、球阀、泵体等。
在冶金、制药、化工等领域,水玻璃铸造件也逐渐得到了越来越广泛的应用。
结论水玻璃铸造件工艺流程简单,制造精度高、安全环保、特点明显、应用广泛。
虽然其制造成本较高,但是在一些领域对特殊铸件的制造需求很高时,水玻璃铸造技术依旧具有其重要的应用价值。
熔模铸造工艺流程

一、模具检验。
二、蜡模料搞拌注模——取模型——修型——自检。
三、蜡型焊接——自检。
四、涂料(水玻璃及配比耐火材料+硬化剂)。
五、脱蜡(水温不大于100℃情况下使蜡型变为液体。
取出待用,将
模壳取出转至焙烧序)。
六、将模壳口朝下放入焙烧炉中去水份。
烧至840~880℃左右为
止,保温一小时待用。
七、炉二按要求得钢水及元素配好后,将模壳取出放入砂床中,待
钢水温度达到要求出炉浇注。
八、清砂:将铸件表面耐火材料要求用气铲及手工清净。
便于气割
汽口。
九、气割:将铸件浇口和产品分开,氧气割一无齿锯。
十、检验——修理——打磨。
十一、将检好后产品按大在下小件在上排放在退出炉上。
升温860~880℃为可,保温达4~6小时,检出在自然冷,待产品凉透为止。
十二、转至清砂设备场地,进行抛丸处理。
十三、终检分类——入库。
一、制模检模。
二、注蜡——检蜡型——清洗。
三、组装焊接——自检。
四、涂料——蜡型壳面装耐火材料。
五、脱蜡——回收蜡料下次待用。
六、模壳焙烧——出去水份等。
七、熔化钢水+钢质+钢温浇注。
八、清表面耐火材料。
分类铸件待割浇口。
九、氧气割一无齿锯。
十、初检——整理。
十一、退火处理。
十二、抛丸处理。
十三、终检入库。
水玻璃铸造工艺(3篇)

第1篇一、引言水玻璃铸造工艺是一种传统的铸造方法,它利用水玻璃作为铸造材料,具有熔点低、流动性好、易于脱模等优点。
随着我国铸造工业的不断发展,水玻璃铸造工艺在铸造领域得到了广泛应用。
本文将从水玻璃的制备、铸造工艺流程、质量控制等方面对水玻璃铸造工艺进行详细介绍。
二、水玻璃的制备1. 水玻璃的原料水玻璃的原料主要有硅砂、碱金属氧化物、碱土金属氧化物等。
其中,硅砂是水玻璃的主要成分,其质量直接影响水玻璃的性能。
2. 水玻璃的制备方法(1)熔融法:将硅砂、碱金属氧化物、碱土金属氧化物等原料按照一定比例混合,加热熔融后,加入适量水冷却、固化,得到水玻璃。
(2)水解法:将硅砂、碱金属氧化物、碱土金属氧化物等原料按照一定比例混合,加入适量水,搅拌、加热,使原料水解,得到水玻璃。
(3)沉淀法:将硅砂、碱金属氧化物、碱土金属氧化物等原料按照一定比例混合,加入适量水,搅拌、加热,使原料发生化学反应,生成沉淀,经过过滤、洗涤、干燥等工序,得到水玻璃。
三、水玻璃铸造工艺流程1. 原料准备将硅砂、碱金属氧化物、碱土金属氧化物等原料按照一定比例混合,经过筛选、烘干等工序,确保原料的质量。
2. 水玻璃制备按照一定的工艺参数,将原料进行熔融、水解或沉淀等制备过程,得到符合要求的水玻璃。
3. 模具准备根据铸件形状、尺寸、材料等要求,选择合适的模具。
模具应具有良好的脱模性能、耐磨性和耐腐蚀性。
4. 铸造将水玻璃倒入模具中,进行凝固、硬化。
根据铸件形状、尺寸、材料等要求,选择合适的铸造温度、时间、压力等参数。
5. 脱模在铸件凝固、硬化后,进行脱模操作。
脱模过程中应避免对铸件造成损伤。
6. 后处理对铸件进行打磨、抛光、热处理等后处理工序,提高铸件质量。
四、质量控制1. 原料质量:严格控制原料质量,确保水玻璃的性能稳定。
2. 水玻璃制备:按照一定的工艺参数,确保水玻璃的制备质量。
3. 模具质量:选择合适的模具,确保模具的脱模性能、耐磨性和耐腐蚀性。
熔模铸造水玻璃应满足技术要求.pptx

铜合金铸件铸造技术课程
熔模铸造水玻璃应满足技术要求
制作人:杨兵兵
陕西工业职业技术学院
熔模铸造水玻璃应满足技术要求
粘结剂的基本特点 水玻璃密度相关知识 模数与密度之间对照表
铜合金铸件铸造技术课程
粘结剂的基本特点
制造型壳用的耐火涂料由粉粒状耐火材料和粘结剂配制而成,因此 粘结剂应能满足以下要求:
1.用它配制的涂料应有良好的涂挂性、渗透性及保存性;与模料不 起化学反应,不互相溶解,能复制出熔模精确的轮廓,且型壳内腔表面 要光滑。
2.能使粉状和粒状耐火材料牢固地粘结在一起,使型壳在室温、焙 烧、浇注高温合金液时具有足够的强度,硬化时简便快速,在高温下还 应具有良好的化学稳定性。
铜合金铸件铸造技术课程
宽范围内变化,工业上应用水玻璃 M=0.5~4,当M>2时,液体内就有胶体的Si02存在。
通常水玻璃模数M<2.6的低模数水玻璃在熔模精密铸造中不能用于 制作型壳,因此,水玻璃原材料进厂时应满足表1技术要求。
铜合金铸件铸造技术课程
表1 水玻璃原材料(进场)技术要求
铜合金铸件铸造技术课程
制壳用水玻璃要求
表2 制型壳水玻璃技术要求
铜合金铸件铸造技术课程
THANKS FOR YOUR WATCHING
谢谢您的观看
铜合金铸件铸造技术课程
- 1、下载文档前请自行甄别文档内容的完整性,平台不提供额外的编辑、内容补充、找答案等附加服务。
- 2、"仅部分预览"的文档,不可在线预览部分如存在完整性等问题,可反馈申请退款(可完整预览的文档不适用该条件!)。
- 3、如文档侵犯您的权益,请联系客服反馈,我们会尽快为您处理(人工客服工作时间:9:00-18:30)。
技术管理文件水玻璃铸造工艺守则
蜡料制备
1. 工艺要求:
1.1 蜡液温度:70-90℃,严禁超过90℃。
1.2 稀蜡温度:65-80℃。
1.3 蜡膏保温缸水温:48-50℃。
1.4 蜡膏应搅拌均匀呈糊状,温度控制在45-48℃,其中不允许有颗
粒状蜡料。
1.5 蜡料配方
蜡料种类材料名称
重量配比
12345
石蜡5025105
硬脂酸50251055
回收蜡50809095
1.5.1 正常生产采用3、4两种配方,配方5用于压制浇口棒。
1.5.2 在生产过程中必须根据蜡模质量分析结果,适量增加或减少硬
脂酸量,冬季的酸值取下限,夏季的酸值取上限。
2 操作程序
2.1 启动设备,检查运转是否正常,是否漏水、漏气、漏蜡,有问题应
及时排除。
检查保温缸水温是否符合工艺要求。
2.2 按蜡料配比把石蜡、硬脂酸和回收蜡分别称好,加入化蜡槽内,加
热至全熔状态,其温度不得超过90℃。
2.3 把蜡液送到蜡膏搅拌机盛蜡槽内。
2.4 将搅蜡缸内加入三分之二的蜡片,启动搅拌机进行搅蜡直至呈糊状
蜡料为止。
3注意事项
3.1 稀蜡需用100目筛过滤,去掉杂质后方能使用。
3.2 不允许有影响质量的空气和水分混入蜡膏中。
3.3 化蜡槽和盛蜡槽每月清理两次。
3.4 蜡膏保温缸、搅蜡缸属于压力容器,应定期检查有关紧固件及密封
机构的使用情况,发现问题应及时处理,正常工作压力严禁超过
0.50MPa。
4检查项目
每班必须测量蜡液温度和保温水温度3-4次,控制在工艺要求范围内并做好原始记录。