水玻璃熔模铸造介绍
水玻璃铸造

水玻璃铸造1. 概述水玻璃铸造是一种常见的金属铸造技术,也被称为硅酸钠铸造。
通过使用水玻璃(硅酸钠)作为粘结剂,将骨料与金属颗粒结合在一起,形成一个可铸造的模具。
这种铸造方法广泛应用于工业制造中,包括汽车、机械和航空航天等行业。
2. 水玻璃铸造的工艺步骤水玻璃铸造的过程可以分为以下几个步骤:2.1. 制备模具首先,根据需求设计和制造模具。
模具可以采用硅胶、金属或其他材料制成,以确保模具的精确度和耐用性。
2.2. 准备骨料骨料是水玻璃铸造中的重要组成部分,它可以是石英砂、氧化铝、石膏等材料。
根据具体的铸造要求,选择不同的骨料进行混合。
2.3. 涂抹水玻璃将水玻璃与适量的水混合,并使用刷子将混合物均匀地涂抹在模具表面。
水玻璃的涂抹层应具有一定的厚度,以确保模具的强度和耐用性。
2.4. 添加骨料将预先准备好的骨料均匀地撒在涂抹水玻璃的模具上。
骨料的厚度和数量应根据具体的铸造要求加以调整。
2.5. 铸造金属将要铸造的金属熔化,并将熔融金属缓慢地倒入模具中。
在铸造过程中,注意控制金属的温度和倒注速度,以确保铸件的质量和形状。
2.6. 冷却和处理待金属冷却后,将模具打开,取出铸件。
铸件将会稍微变形,需要进行后续的研磨和处理,以达到客户要求的尺寸和表面质量。
3. 水玻璃铸造的优势和应用水玻璃铸造具有以下几个优势:•成本低:模具制造和骨料的成本相对较低,可大幅降低铸造成本;•高精度:水玻璃铸造能够制造出高精度和复杂的铸件,满足不同行业的需求;•环保:与其他一些铸造方法相比,水玻璃铸造过程中产生的废气和废水较少。
水玻璃铸造广泛应用于各个行业,包括:•汽车制造:发动机零部件、底盘配件等;•机械制造:齿轮、轴承等;•航空航天:飞机引擎零部件、航天器结构件等。
4. 总结水玻璃铸造是一种常见且在工业制造中广泛应用的金属铸造技术。
通过将水玻璃作为粘结剂,骨料与金属颗粒结合在一起,形成可铸造的模具。
水玻璃铸造具有成本低、高精度和环保等优势,并被广泛应用于汽车、机械和航空航天等行业。
水玻璃型壳熔模铸造制壳工艺过程控制

水玻璃型壳熔模铸造制壳工艺过程控制作者:董丽华来源:《中国科技纵横》2018年第21期摘要:近年来,随着中国的铸造业发展迅速。
其中由于熔模铸造可以做到少切削,不切削,复杂件成型率高,生产工艺水平越来越高,其市场也越来越大。
而大部分的铸件生产任然采用的是水玻璃工艺,这种工艺最大的问题就是不稳定性,所以对水玻璃制壳质量控制要求和生产管理要点的讨论就显得很有必要。
实践证明,通过加强关键工序的控制和质量因素的综合控制,产品质量和成品率会有了显著的提高。
关键词:水玻璃;熔模铸造;制壳;工艺;控制中图分类号:TG249.5 文献标识码:A 文章编号:1671-2064(2018)21-0086-02由于水玻璃粘结剂的价格低廉,制壳周期短,因此在我国广泛采用水玻璃工艺精密铸造。
但是,与传统砂型铸造相比,水玻璃壳型铸造成本高,工艺复杂,生产周期长。
型壳是影响铸件质量的重要因素之一。
如何控制其质量具有重要意义。
本文结合生产实践,对壳的原材料控制和管理和制壳工艺的改善,改善型壳强度及稳定性,从而提高铸件质量及其成品率。
1 原材料的选择与控制1.1 水玻璃硅酸钠的水溶液俗称水玻璃,南方一般被称为水玻璃,北方一般被称为泡化碱。
硅酸钠的形态可分为液体、固体和水淬三种形态。
水玻璃可分为钾水玻璃和钠水玻璃。
熔模铸造中一般采用的是钠水玻璃。
水玻璃中二氧化硅和氧化钠(或氧化钾)的摩尔比通常称为模数(M)。
硅酸钠是水分散体系中的无色、浅色透明或半透明粘稠液体。
固体硅酸钠是一种无色和浅色的透明或半透明玻璃。
硅酸钠在的凝固与石灰非常相似。
主要通过碳化、脱水、固化三个工序来实现。
随着二氧化硅含量的增加,游离水蒸发,硅胶脱水成固体SiO2并固化。
由于空气中CO2浓度低,碳化反应和固化过程非常缓慢。
1.2 水玻璃的特性熔模铸造生产时水玻璃应为液态,纯净的水玻璃是一种外观显无色透明的粘滞性溶液,含有杂质时则显青灰色或者淡黄色。
水玻璃溶液显碱性,一般高、中模数的水玻璃的PH值为11~13。
水玻璃在铸造生产中的应用
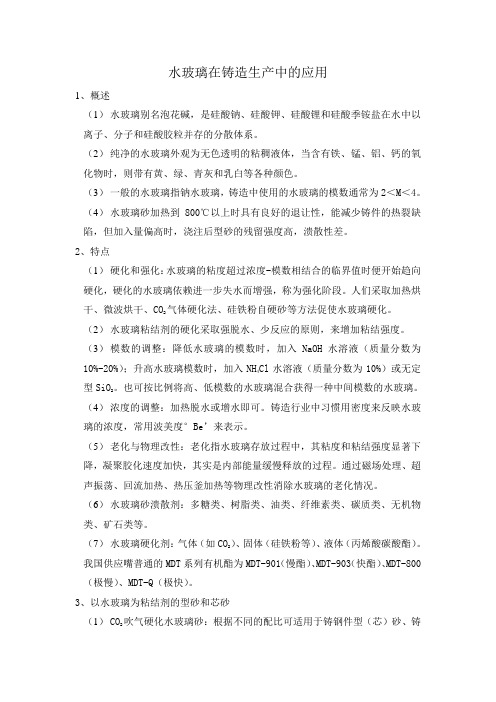
水玻璃在铸造生产中的应用1、概述(1)水玻璃别名泡花碱,是硅酸钠、硅酸钾、硅酸锂和硅酸季铵盐在水中以离子、分子和硅酸胶粒并存的分散体系。
(2)纯净的水玻璃外观为无色透明的粘稠液体,当含有铁、锰、铝、钙的氧化物时,则带有黄、绿、青灰和乳白等各种颜色。
(3)一般的水玻璃指钠水玻璃,铸造中使用的水玻璃的模数通常为2<M<4。
(4)水玻璃砂加热到800℃以上时具有良好的退让性,能减少铸件的热裂缺陷,但加入量偏高时,浇注后型砂的残留强度高,溃散性差。
2、特点(1)硬化和强化:水玻璃的粘度超过浓度-模数相结合的临界值时便开始趋向硬化,硬化的水玻璃依赖进一步失水而增强,称为强化阶段。
人们采取加热烘气体硬化法、硅铁粉自硬砂等方法促使水玻璃硬化。
干、微波烘干、CO2(2)水玻璃粘结剂的硬化采取强脱水、少反应的原则,来增加粘结强度。
(3)模数的调整:降低水玻璃的模数时,加入NaOH水溶液(质量分数为Cl水溶液(质量分数为10%)或无定10%-20%);升高水玻璃模数时,加入NH4。
也可按比例将高、低模数的水玻璃混合获得一种中间模数的水玻璃。
型SiO2(4)浓度的调整:加热脱水或增水即可。
铸造行业中习惯用密度来反映水玻璃的浓度,常用波美度°Be’来表示。
(5)老化与物理改性:老化指水玻璃存放过程中,其粘度和粘结强度显著下降,凝聚胶化速度加快,其实是内部能量缓慢释放的过程。
通过磁场处理、超声振荡、回流加热、热压釜加热等物理改性消除水玻璃的老化情况。
(6)水玻璃砂溃散剂:多糖类、树脂类、油类、纤维素类、碳质类、无机物类、矿石类等。
)、固体(硅铁粉等)、液体(丙烯酸碳酸酯)。
(7)水玻璃硬化剂:气体(如CO2我国供应嘴普通的MDT系列有机酯为MDT-901(慢酯)、MDT-903(快酯)、MDT-800(极慢)、MDT-Q(极快)。
3、以水玻璃为粘结剂的型砂和芯砂吹气硬化水玻璃砂:根据不同的配比可适用于铸钢件型(芯)砂、铸(1)CO2铁件型砂等。
水玻璃熔模铸造介绍

水玻璃熔模铸造介绍变量和公差熔模铸造又称“失蜡铸造”,通常是在蜡模表面涂上数层耐火材料,待其硬化干燥后,将其中的蜡模熔去而制成型壳,再经过焙烧,然后进行浇注,而获得铸件的一种方法。
由于获得的铸件具有较高的尺寸精度和表面光洁度,故又称“熔模精密铸造”。
可用熔模铸造法生产的合金种类有碳素钢、合金钢、耐热合金、不锈钢、精密合金、永磁合金、轴承合金、铜合金、铝合金、钛合金和球墨铸铁等。
熔模铸件的形状一般都比较复杂,铸件上可铸出孔的最小直径可达0.5mm,铸件的最小壁厚为0.3mm。
在生产中可将一些原来由几个零件组合而成的部件,通过改变零件的结构,设计成为整体零件而直接由熔模铸造铸出,以节省加工工时和金属材料的消耗,使零件结构更为合理。
熔模铸件的重量大多为零点几十牛(即几十克到几公斤),太重的铸件用熔模铸造法生产较为麻烦,但目前生产大的熔模铸件的重量已达800牛左右。
溶膜铸造是用易熔材料制成模型,然后在模型上涂挂耐火材料,经硬化后,在将模型熔化排出型外,从而获得无分型面的铸型,铸型焙烧后即浇注。
一. 工艺过程:1. 蜡模制作1) 压型:制蜡模的专用模具、钢、铜、铝、切削而成2) 蜡模的压制:石蜡、峰蜡、硬脂酸、松香等,将熔化的蜡料压入压型中,冷凝后取出,修去毛刺,得到蜡模3) 蜡模组装:若干蜡模焊在一个直浇棒上2. 结壳:蜡模涂上涂料、硬化、干燥等1) 浸涂料(石英粉+粘结剂的糊状物)表面光洁2) 撒砂(粗石英砂)的目的:增厚型壳3) 硬化(水玻璃+NH4CL—SIO2)化学硬化3. 脱蜡、焙烧1) 脱蜡:热水或水蒸气2) 焙烧:加热800~1000℃提高型壳强度4. 填砂:浇注1) 填砂:型壳放入铁箱中,周围干砂充填2) 浇注:趁热(600~700℃)进行浇注5. 落砂清理冷却后,破坏型壳,取出铸件,去浇口、毛刺、退火或正火,以便得到所需机械性能1) 铸造精度、光洁度高、且可浇注形状复杂的件2) 能铸造各种合金(型壳是高级耐火材料)3) 单件、小批、大批量生产均可4) 少无切削加工(Ra3.2~1.6um)稍磨5) 材料贵,工艺过程繁杂,生产周期长应用:使用高熔点合金精密铸件的成批、大量生产,形状复杂,难以切削加工的小零件。
铸造用水玻璃及其改性机制

铸造用水玻璃及其改性机制
1水玻璃铸造
水玻璃铸造是一种将熔融的玻璃流体包裹到特殊模具中形成三维造型的制作技术,它具有多种优点:节约用料,获得高质量的产品,设计性强,还拥有低热能消耗和回收废弃玻璃的廉价方式等优势。
在制造建筑玻璃、家具玻璃装饰等工业品时,水玻璃铸造是最常用的方法。
2水玻璃改性
由于传统水玻璃铸造制品易碎,无法满足工业应用的要求,因此,人们采用改性方法,将水玻璃的硬度大大增强。
目前,改性水玻璃的方法多种多样,其中,改性剂有多种,可以根据不同的物理性质和使用环境选择不同的改性剂。
3改性机制
改性水玻璃的机理主要有两方面:一是在玻璃表面形成厚度较大的吸附膜,使表面变硬;二是改变玻璃的结构,使其变得坚韧耐用。
1)吸附膜:通过改性剂与玻璃表面形成吸附膜,使其富含阳离子,形成无机化合物,使表面变硬,从而增强玻璃的韧性。
2)玻璃的结构改变:玻璃的表面吸附了改性剂,形成较多的非晶态小晶粒,成为玻璃网状结构的基本单元,从而有效地提高了玻璃的耐酸碱性、耐腐蚀性和耐热性,增加了玻璃的耐磨性。
4水玻璃的应用
水玻璃的硬度大增,质量更高,从而使其在汽车车窗、空调管道、毒气室管道、油管道等行业得到广泛应用。
此外,水玻璃还可以作为各种装饰玻璃装饰品,如制作玻璃台面、玻璃墙板、玻璃壁灯等,可以用于家居装饰,并可用于室外建筑景观,以增加建筑美观度。
水玻璃铸造件工艺是怎样的

水玻璃铸造件工艺是怎样的前言水玻璃铸造作为一种先进制造技术,可以用于制造一些特殊形状、结构复杂、装配性好的铸造件。
本文将对水玻璃铸造件的工艺流程、特点以及应用进行介绍。
工艺流程模具制作水玻璃铸造的模具一般使用铝合金或者树脂模具。
首先需要将铸造件的3D模型设计完成,并根据其尺寸及目标成型形状制作出实体模型。
此后,在实体模型的基础上,进行模仁制造、模具制造,完成模具的制作。
模具涂覆该工艺常采用一个叫“水玻璃”或“硅酸钠”的组分来涂覆模具表面,然后在经过一定的加热后,在模具内壁形成一层坚硬、不易脱落的薄层。
将模具各分支及与铸件接触面涂覆均匀,以防止在铸造过程中涂层被拱起或断裂。
铸造铸造时先将模具加热至一定温度,然后用水玻璃与固定比例的铸造砂混合均匀,倒入模具中,并在一定时间内震实,将涂覆在模具表面的水玻璃及铸造砂干燥结合,形成坚固的铸造件。
后处理铸造完成后需要进行后处理,主要包括去砂、热处理、机加工等步骤。
在热处理过程中,可以改善铸造件的力学性能和物理性能,提高其强度和耐磨性等指标,而机加工可以进一步加工出更为精细的形状和尺寸。
特点精度高水玻璃铸造件的精度很高,所铸铸件表面光滑,良好的整体性和精准的尺寸,最大限度地保证了铸件的密封性。
安全、环保硅酸钠是一种绿色环保的化学品,故其在水玻璃铸造过程中并不会产生有毒气体和其他污染物,因此是一种安全、环保的铸造法。
复杂件铸造水玻璃铸造可以铸造出形状较为复杂、结构复杂、设计合理、装配性好的、高强度、高耐热、高抗蚀的特种铸造件,适用于船舶、矿山、重工业和冶金等领域。
应用目前,水玻璃铸造技术已广泛应用于各个行业,其中最为常见的即是机械领域的部分零部件生产,例如大型漏斗、球阀、泵体等。
在冶金、制药、化工等领域,水玻璃铸造件也逐渐得到了越来越广泛的应用。
结论水玻璃铸造件工艺流程简单,制造精度高、安全环保、特点明显、应用广泛。
虽然其制造成本较高,但是在一些领域对特殊铸件的制造需求很高时,水玻璃铸造技术依旧具有其重要的应用价值。
熔模铸造简介

熔模铸造简介1.熔模铸造发展概况1.1. 概述熔模铸造又称熔模精密铸造,是一种近净形的液态金属成型工艺,应用该工艺获得的每个铸件都是经多种工序、多种材料、多种技术共同协作综合的结果。
熔模铸造通常是指在易熔材料制成的模样表面包覆若干层耐火材料制成型壳,再将模样熔化排出型壳,从而获得无分型面的铸型,经高温焙烧后即可填砂浇注的铸造方案。
由于模样广泛采用蜡质材料来制造,故常将熔模铸造称为“失蜡铸造”。
1.2. 工艺流程熔模铸造工艺全过程:1.蜡模成型:将蜡料压入金属型腔模具,冷却取出形成蜡模;2.组树:将若干蜡模焊在一根蜡制的浇注系统上,组成蜡模组;3.沾浆:将蜡模组浸入水玻璃和石英粉配置的浆料中;4.硬化壳:将蜡模组放入硬化剂中进行硬化,如此重复数次,直到蜡模表面形成一定厚度的硬化壳;5.熔蜡制壳:将带有硬壳的蜡模组加热,使蜡熔化后从浇口中流出,形成铸型空腔;6.熔炼浇注:将液态金属浇入模壳,形成铸件毛坯;7.清理型壳:待浇注后的产品充分冷却后,使用人工锤击或振动脱壳机使模壳从铸件上分离。
最后,利用切割的方法分离出模组上的铸件产品,得到所需铸件。
2.模料2.1. 模料要求制模材料的性能不单应保证方便地制得尺寸精确和表面光洁度高,强度好,重量轻的熔模,它还应为型壳的制造和获得良好铸件创造条件。
模料一般用蜡料、天然树脂和塑料(合成树脂)配制。
凡主要用蜡料配制的模料称为蜡基模料,它们的熔点较低,为60~70℃;凡主要用天然树脂配制的模料称为树脂基模料,熔点稍高,约70~120℃。
熔模铸造对模料的要求:1.热物理性能①熔点:模料的熔点及凝固温度区间应适中,熔点一般在50~80 ℃范围为宜,模料的凝固温度一般选择在5~10 ℃,以便配制模料、制模及脱蜡工艺的进行。
②热稳定性:热稳定性是指当温度升高时,模料抗软化变形的能力。
蜡基模料的热稳定性常以软点来表示,它是以标准悬臂试样加热保温2 h的变形量(挠度)达2 mm时的温度作为软化点,模料软化点一般应比制模车间的温度高10 ℃以上为宜。
熔模铸造水玻璃型壳质量控制

熔模铸造水玻璃型壳质量控制许晓兰,高明轩,陈学敏(霍州煤电集团机电修配分公司,山西霍州031400)摘 要:全过程论述了铸造水玻璃型壳的质量控制要点。
实践证明,通过对型壳质量影响因素的综合控制,使铸件的质量有了明显的提高。
关键词:铸造;水玻璃;型壳;质量中图分类号:T Q171 文献标识码:A 文章编号:1008-8725(2003)10-0084-021 水玻璃粘结剂的质量控制(1)水玻璃种类的选择:市场供应的水玻璃有两种,一种是纯碱与石英粉在1300~1400℃温度下反应得到的,杂质含量少,性能稳定;另一种是采用芒硝生产,杂质含量较高。
通常第一种方法生产的水玻璃较适合熔模铸造选用。
(2)水玻璃模数(M)、密度(ρ),控制M取决于S iO2和Na2O的相对含量,而ρ的高低又决定着S iO2的含量。
M和ρ直接影响型壳的表面强度、常温强度、高温强度及残留强度。
在我厂生产中,控制面层涂料水玻璃的M=3.0~3.2,ρ=1.27~1.29。
加固层M=3.0~3.2,ρ=1.30~1.34。
当M和ρ不符合要求时,用酸或碱来调整M,用水或高密度的水玻璃调整ρ,使用效果良好,既保证了壳体的各种常温、高温性能,又有较低的溃散强度。
在实际生产中,水玻璃的假模数对型壳高温强度的影响很大。
当M>310时,水玻璃存放时间越长粘度越大。
由于水玻璃中有游离的S iO2存在,储存一定时间后,S iO2沉积在容器的底部,导致水玻璃模数下降,严重影响型壳的高温强度。
这主要是由于生产厂制做水玻璃时,S iO2和Na2O不是以化合态存在,或者为了提高模数,加入细石英粉造成的。
所以,在使用过程中,为了防止游离S iO2存在使模数高的假象,当水玻璃卸车时化验一次,存放24h后再化验一次。
以保证型壳的质量。
对于沉积于容器底部的杂质,必须在一定时间内予以清理,一般容量在15~20t的储罐,每二年要清理一次。
2 粉料粒度分布对型壳质量的影响与控制生产中,较粗的粉料(手感)所制得的涂料沉淀快,流杯粘度大,工艺稳定性差,生产出的铸件表面粗糙。
- 1、下载文档前请自行甄别文档内容的完整性,平台不提供额外的编辑、内容补充、找答案等附加服务。
- 2、"仅部分预览"的文档,不可在线预览部分如存在完整性等问题,可反馈申请退款(可完整预览的文档不适用该条件!)。
- 3、如文档侵犯您的权益,请联系客服反馈,我们会尽快为您处理(人工客服工作时间:9:00-18:30)。
水玻璃熔模铸造介绍变量和公差熔模铸造又称“失蜡铸造”,通常是在蜡模表面涂上数层耐火材料,待其硬化干燥后,将其中的蜡模熔去而制成型壳,再经过焙烧,然后进行浇注,而获得铸件的一种方法。
由于获得的铸件具有较高的尺寸精度和表面光洁度,故又称“熔模精密铸造”。
可用熔模铸造法生产的合金种类有碳素钢、合金钢、耐热合金、不锈钢、精密合金、永磁合金、轴承合金、铜合金、铝合金、钛合金和球墨铸铁等。
熔模铸件的形状一般都比较复杂,铸件上可铸出孔的最小直径可达0.5mm,铸件的最小壁厚为0.3mm。
在生产中可将一些原来由几个零件组合而成的部件,通过改变零件的结构,设计成为整体零件而直接由熔模铸造铸出,以节省加工工时和金属材料的消耗,使零件结构更为合理。
熔模铸件的重量大多为零点几十牛(即几十克到几公斤),太重的铸件用熔模铸造法生产较为麻烦,但目前生产大的熔模铸件的重量已达800牛左右。
溶膜铸造是用易熔材料制成模型,然后在模型上涂挂耐火材料,经硬化后,在将模型熔化排出型外,从而获得无分型面的铸型,铸型焙烧后即浇注。
一. 工艺过程:1. 蜡模制作1) 压型:制蜡模的专用模具、钢、铜、铝、切削而成2) 蜡模的压制:石蜡、峰蜡、硬脂酸、松香等,将熔化的蜡料压入压型中,冷凝后取出,修去毛刺,得到蜡模3) 蜡模组装:若干蜡模焊在一个直浇棒上2. 结壳:蜡模涂上涂料、硬化、干燥等1) 浸涂料(石英粉+粘结剂的糊状物)表面光洁2) 撒砂(粗石英砂)的目的:增厚型壳3) 硬化(水玻璃+NH4CL—SIO2)化学硬化3. 脱蜡、焙烧1) 脱蜡:热水或水蒸气2) 焙烧:加热800~1000℃提高型壳强度4. 填砂:浇注1) 填砂:型壳放入铁箱中,周围干砂充填2) 浇注:趁热(600~700℃)进行浇注5. 落砂清理冷却后,破坏型壳,取出铸件,去浇口、毛刺、退火或正火,以便得到所需机械性能1) 铸造精度、光洁度高、且可浇注形状复杂的件2) 能铸造各种合金(型壳是高级耐火材料)3) 单件、小批、大批量生产均可4) 少无切削加工(Ra3.2~1.6um)稍磨5) 材料贵,工艺过程繁杂,生产周期长应用:使用高熔点合金精密铸件的成批、大量生产,形状复杂,难以切削加工的小零件。
如:汽轮机叶片、工艺品用以浇注铸件的钢。
铸造合金的一种。
铸钢分为铸造碳钢、铸造低合金钢和铸造特种钢3类。
二. 铸钢工艺:①铸造碳钢。
以碳为主要合金元素并含有少量其他元素的铸钢。
含碳小于0.2%的为铸造低碳钢,含碳0.2%~0.5%的为铸造中碳钢,含碳大于0.5%的为铸造高碳钢。
随着含碳量的增加,铸造碳钢的强度增大,硬度提高。
铸造碳钢具有较高的强度、塑性和韧性,成本较低,在重型机械中用于制造承受大负荷的零件,如轧钢机机架、水压机底座等;在铁路车辆上用于制造受力大又承受冲击的零件如摇枕、侧架、车轮和车钩等。
②铸造低合金钢。
含有锰、铬、铜等合金元素的铸钢。
合金元素总量一般小于5%,具有较大的冲击韧性,并能通过热处理获得更好的机械性能。
铸造低合金钢比碳钢具有较优的使用性能,能减小零件质量,提高使用寿命。
③铸造特种钢。
为适应特殊需要而炼制的合金铸钢,品种繁多,通常含有一种或多种的高量合金元素,以获得某种特殊性能。
例如,含锰11%~14%的高锰钢能耐冲击磨损,多用于矿山机械、工程机械的耐磨零件;以铬或铬镍为主要合金元素的各种不锈钢,用于在有腐蚀或650℃以上高温条件下工作的零件,如化工用阀体、泵、容器或大容量电站的汽轮机壳体等。
三. 铸钢的质量与质量要求铸造生产中,“质量”包含两个方面的内容:一是产品质量,即铸件满足用户要求的程度,也就是适用性;二是工程质量,即制造铸件的生产过程对产品质量的保证程度。
两者有相关性,但又不是一个概念。
评定产品质量,最基本的判据是设计者对其结构和功能的要求,如铸件需经机械加工及热处理,则还应包括这些后续工序对铸件毛坯的要求,如定位基准、工艺孔、为防止热处理变形而加的工艺补正量或拉肋等。
除此以外,铸件的表面涂装、包装及按期交货等也是属于产品质量范畴之内的条件。
图样和验收技术条件就是上述各项要求的具体化,是验收产品的判据。
承制方制定生产铸件的工艺,应以下列各项为依据。
(1) 购买方提供的铸件图。
通常有确定铸件的形状、各部尺寸及其公差、定位基准等项。
单件或少量生产时,也可以由购买方提供模样和芯盒,此时,承制方将不对铸件尺寸负责。
(2) 购买方确定的材料规格及适用的标准。
(3) 购买方规定的产品技术条件,如对铸件内部致密性的要求及检测方法、允许的铸造缺陷、对表面粗糙度的要求及表面缺陷的检测方法等。
(4) 购买方和承制方共同商定的其他协议。
提出对铸钢件的质量要求,似乎是购买方享有的特权,可是实际上却是购买方要审慎对待的课题。
不适当地降低质量要求,将影响铸件或机械产品的功能,甚至会招致严重的事故。
不必要地提高质量要求,将使铸件的生产成本增高,对适用性和机械产品的功能则无所一补益。
有时,机械产品中采用成本过高的铸件可能会使整机价格提高而降低竞争能力。
铸造生产是复杂的、多工序的生产过程。
过去,在某些条件较差、人员素质又较低的铸造厂中,对生产中的一些环节往往难以有效地控制,产品的不良率可能相当高,再加以检验手段不完备,不合格铸件漏检而交付购买方的事时有发生的。
在这种情况下,产品设计者往往苦于对铸件的可靠性心中无数,考虑质量要求时,就不免有“要求高点比较保险”的想法。
工作经历较长的人又难免不碰到因铸件质量不好而造成的事故,那就进一步加强了上述想法。
结果,就形成了一种十分矛盾的状况。
一方面是铸造厂难以使铸件质量稳定地保持一个较高的水准;另一方面则是设计者在确定质量要求时往往倾向于宁高毋低。
这种矛盾,只能经由科学技术的进步来加以解决。
随着铸造生产技术水平的不断提高,铸造生产过程中的监控加强了,检测产品质量的手段已建立完善的认证体系。
因而,铸件内在质量和外观质量所能达到的水准正在不断提高,铸件质量的可靠性也有了较好地保证。
情况的变化也导致了供需双方姿态的改变。
保持较高的生产技术水平和使用先进的检测手段,需要较高的投入,这当然要反映在产品的价格上。
于是,质量要求高的铸件和质量要求一般的铸件,价格就有明显的差别。
按当前国际市场的实际情况,尺寸精度高、对外观和内部缺陷限制严格、规定用渗透探伤检查外表面并用射线探伤检查内部质量的铸件、其价格可能数倍、或十几倍于质量要求一般的铸件。
结果,条件较好的承制方,反而希望购买方提出较高、较严的要求,以便充分利用其设施获得较好的效益。
在承制方所能保证的水平越来越高的情况下,购买方在考虑质量要求时越要慎重行事,因为每增加一项要求都意味着铸件的价格会相应提高,提出不必要的要求也是失误,是要付出相应的代价的。
综上可知,质量有两层意思。
首先是满足使用要求,即适用性:其次是在保证适用性的基础上价格最低,即经济性。
四. 碳钢铸件的热处理碳钢铸件通常采用的热处理方式为退火、正火或正火+回火。
这三种热处理方式对铸造碳钢力学性能的影响见图11-19。
经正火处理的铸钢,其力学性能较退火的略高些。
由于组织转变时的过冷度较大,硬度也略高些,切削性能因而也较好。
目前生产中对铸钢件多采用正火方式处理。
含碳量较高,且形状较复杂的碳钢铸件,为消除残余应力和改善韧性,可在正火后进行回火处理。
回火温度以550~650。
C为宜,然后在静止空气中冷却。
碳的质量分数在0.35%以上的铸造碳钢件也可采用调质(淬火+高温回火)处理,以改善其综合力学性能。
小型碳钢铸件可由铸态直接进行调质处理;大型或形状复杂的碳钢铸件,则宜在正火处理后再进行调质处理。
五. 铸件热处理工艺铸钢件的热处理由加热、保温和冷却三个阶段组成。
其工艺参数的确定,均以保证产品质量和节约成本为依据。
图11—2给出了铸钢件几种热处理规范示意图。
1. 加热加热是热处理过程中能耗最大的工序。
加热过程的主要技术是选择适当的加热方式、加热速率及装料方式。
(1) 加热速率:对于一般中小型铸钢件,可以不限制加热速率,采用炉子的最大功率加热。
采用热炉装炉可极大地缩短加热时间和生产周期。
实际上快速加热条件下,铸件表面与心部之间无显著的温度滞后(见图ll—3)。
而缓慢加热将导致生产效率降低、能耗增大以及造成铸件表面严重氧化和脱碳。
但对于一些形状结构复杂、壁厚较大、在加热中易生产较大的热应力而导致变形或开裂的铸件,则应控制加热速率。
一般可以采取低温慢速加热(600。
C以下)或在低、中温区停留一、二次等工艺方法,在高温区仍可以采用快速加热升温。
(2) 加热方式:铸钢件加热方式有辐射加热、盐浴加热和感应加热等。
加热方式的选择原则是快速均匀、便于控制及高效低成本。
一般应考虑铸件的结构尺寸、化学成分、热处理工艺和质量要求等。
(3) 装料方式:铸件在炉内的堆放方式应予以足够的重视。
基本原则是,充分利用有效空间、确保均匀受热条件并防止铸件变形。
2.保温铸钢件奥氏体化保温温度应根据铸钢的化学成分和要求的性能选定。
一般比类同成分的锻钢件略高些(高20。
C左右)。
对亚共析钢铸件,以碳化物能较快地溶入奥氏体,并兼顾奥氏体能保持细晶粒为原则,一般在Ac。
温度以上30~50。
c。
正火的温度比退火或淬火的稍高些。
过共析钢铸件正火时应加热到Ac。
温度以上。
淬火时则在Ac。
温度以下和Ac。
温度以上,避免残余奥氏体量过多。
对于晶粒长大倾向显著的铸钢(如锰钢),淬火保温温度宜取下限。
厚截面铸件的奥氏体化保温温度通常取上限。
铸钢件热处理保温时间的确定应考虑两个方面因素:一是使铸件表面与心部温度均匀一致;二是组织均匀化。
因此保温停留时间主要取决于铸件的导热性能、断面壁厚及合金元素等因素。
一般合金钢铸件比碳钢铸件需更长的保温时间,铸件壁厚通常是估计保温时间的主要依据。
根据经验,每25mm壁厚保温lh。
大于25ram 者,每增加25ram延长保温时间lh。
对于回火处理、时效处理时的保温时间,应考虑热处理的目的、保温温度及元素扩散速度等因素,其保温时间应比正火或淬火时的保温时间长,一般为正火或淬火时保温时间的l.5~2倍。
3. 冷却铸钢件在保温后可采取不同的速率冷却完成钢中相的转变,以获得所要求的金相组织,并达到规定的性能指标。
一般说来,加大冷却速率有利于获得良好的组织状态并细化晶粒,从而提高钢的力学性能。
但太大的冷却速度容易使铸件产生较大的应力,对于结构复杂的铸件可能导致变形或开裂。
回火保温后的冷却方式,一般并元特别严格的要求,只是对一些有回火脆性敏感的低合金铸钢,回火保温后的冷却特别重要,宜采用快冷方式,以便尽快通过回火脆性区,避免降低铸钢的韧性。
铸钢件热处理冷却介质常用的有空气、油、水、盐水及熔盐等。
六. 铸造生产关键技术参数问题液态金属通过冷却凝固最终获得合格的、满足各种使用要求的铸件。