统计过程控制(SPC)在质量管理中的应用
如何运用SPC统计过程控制进行质量控制

如何运用SPC统计过程控制进行质量控制质量控制是制造业中非常重要的环节,它涉及到产品的质量和可靠性,对企业的发展和客户满意度有着直接的影响。
而SPC统计过程控制(Statistical Process Control)是一种常用的质量控制方法,通过对过程中收集到的数据进行统计分析,帮助企业实现质量的稳定和持续改进。
本文将探讨如何运用SPC统计过程控制进行质量控制。
SPC统计过程控制的核心是收集和分析数据。
在质量控制过程中,我们需要收集大量的数据,包括产品的尺寸、重量、颜色等各种指标。
这些数据可以通过传感器、检测设备等手段进行实时采集,并存储在数据库中。
接下来,我们需要对这些数据进行统计分析,以了解过程的变化和稳定性。
在SPC统计过程控制中,常用的统计工具有控制图、直方图、散点图等。
控制图是一种用来监控过程稳定性的图表,可以帮助我们判断过程是否处于控制状态。
常见的控制图有X-bar图、R图、P图等。
通过对控制图的分析,我们可以了解过程的中心线、规格限和过程能力,并及时发现和纠正异常。
除了控制图,直方图也是SPC统计过程控制中常用的工具。
直方图可以帮助我们了解数据的分布情况,判断过程是否符合正态分布。
通过对直方图的分析,我们可以确定过程的偏离程度,并采取相应的措施进行调整。
散点图则可以帮助我们了解两个变量之间的关系,判断其是否存在相关性。
在实际应用中,SPC统计过程控制还可以结合其他质量管理方法,如六西格玛、PDCA循环等,实现质量的持续改进。
六西格玛是一种以减少变异性为目标的质量管理方法,通过对过程进行改进和优化,提高产品的质量和可靠性。
PDCA循环则是一种持续改进的管理方法,通过不断地计划、实施、检查和调整,推动质量的提升。
在运用SPC统计过程控制进行质量控制时,还需要注意以下几点。
首先,要确保数据的准确性和可靠性,避免因为数据采集和处理错误而导致错误的判断和决策。
其次,要及时发现和纠正异常,防止异常扩大和影响产品质量。
基于SPC技术的质量控制体系的研究与应用

基于SPC技术的质量控制体系的研究与应用随着全球化竞争的不断加剧,企业的竞争力已不再仅仅是品牌、市场规模和价格等传统领域的竞争。
如今,质量已经成为衡量企业竞争力的重要指标之一。
因此,实现生产过程中的高质量和稳定性,就显得尤为重要。
而SPC技术的应用可以有效地实现质量控制,大大提高生产效率和企业竞争力。
一、SPC技术的概念与历史SPC(Statistical Process Control),也就是统计过程控制,是对生产过程进行统计分析,以实现质量控制的一种方法。
其核心原理是以统计学方法为工具,掌握生产过程中的相关数据,对生产过程的变化进行控制和改进。
SPC技术最早起源于20世纪20年代,由W.A.Shewhart提出,是美国通用电气公司(GE)最早的实施者之一。
以SPC技术为核心的质量管理理念也随之发展壮大,成为20世纪90年代的主流质量管理思想。
如今,SPC已经广泛应用于不同行业和领域,并得到了大力推广和应用。
二、SPC技术的原理和要素SPC技术的核心原理是监测和控制生产过程中的变量,以减少生产过程的变异性。
通常包括以下要素:1.数据采集:生产过程中要监控的变量需要进行数据采集和记录。
这些数据来源可以是产品的制造过程、生产设备的运行状态、原材料的供应情况等。
企业可以通过人工收集数据或使用软件工具自动收集数据。
在数据采集时,应注意数据的准确性和可靠性。
2.数据分析:在数据采集后,需要进行数据分析。
数据分析是SPC技术的核心,它能够帮助企业识别生产过程中的变异因素,并进行针对性改进。
数据分析可以采用各种统计方法,如均值、标准差、方差等。
3.过程控制:企业通过对数据的分析,可以发现生产过程中存在的问题,并针对性地进行改进。
过程控制是SPC技术的重要部分,它可以使生产过程更加稳定。
4.过程优化:通过SPC技术进行数据分析和过程控制,企业可以发现潜在的问题并进行改进。
这些改进可以是改变生产流程,增加生产设备的容量,或改变产品的设计。
过程控制在质量管理中的应用

过程控制在质量管理中的应用质量管理是一个组织的管理活动,旨在确保产品和服务符合预期的质量标准。
过程控制是质量管理的重要组成部分,它涉及到对所有业务过程进行监控和管理,以确保它们能够按照既定的质量要求运行。
过程控制的应用在质量管理中具有重要的作用。
过程控制能够帮助组织监控和识别潜在的质量问题。
通过对业务过程进行持续的监控,可以及时发现任何潜在的问题或质量偏差,并采取相应的措施进行纠正和改进。
这有助于组织在产品和服务交付之前发现和解决质量问题,避免不符合质量要求的产品和服务流入市场。
过程控制还能够帮助组织实现质量目标和要求。
在质量管理中,组织通常会设定一系列的质量目标和要求,以确保产品和服务的质量达到所期望的水平。
通过对业务过程进行控制和管理,可以确保这些质量目标和要求能够得到满足。
在生产过程中,通过监控和控制每个关键环节的质量,可以确保最终产品能够符合设计要求,并具有一致的品质水平。
过程控制还能够帮助组织改进和优化业务过程。
通过对业务过程进行持续的监控和测量,可以了解各个环节的性能和效果,并找出改进的机会。
通过分析数据和指标,组织可以识别出哪些环节存在问题或瓶颈,并采取措施进行改进。
这有助于组织优化业务过程,提高生产效率和质量水平,降低成本和浪费。
过程控制还能够帮助组织建立和保持质量管理体系。
质量管理体系是一个组织的质量管理框架,包括一系列的政策、程序和规范。
过程控制通过对业务过程的控制和管理,确保组织能够按照质量管理体系的要求进行运作。
它为组织提供了一个指导和规范的框架,帮助组织建立并保持一套可持续的质量管理体系。
在实际应用中,过程控制可以通过多种方式来实现。
可以使用统计过程控制(SPC)来监控和控制关键过程参数的变化,以确保过程在可控范围内运行。
还可以使用六西格玛方法来通过识别和消除质量问题的根本原因,改善和优化业务过程。
还可以使用业务流程管理(BPM)来对业务过程进行建模和分析,以提高过程的效率和质量。
spc质量管理
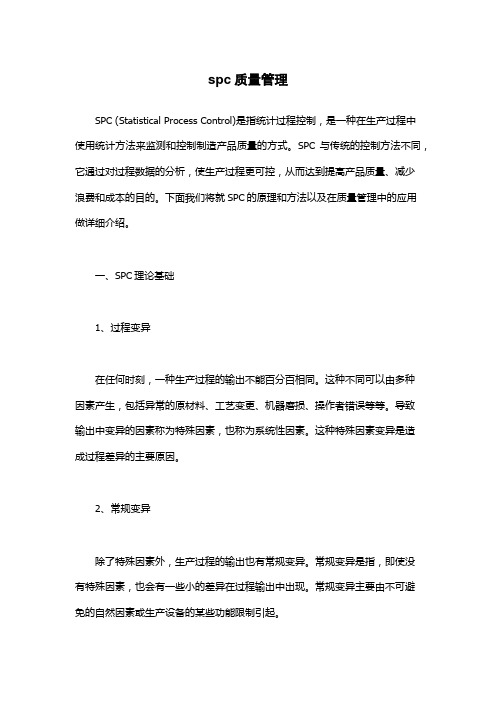
spc质量管理SPC (Statistical Process Control)是指统计过程控制,是一种在生产过程中使用统计方法来监测和控制制造产品质量的方式。
SPC与传统的控制方法不同,它通过对过程数据的分析,使生产过程更可控,从而达到提高产品质量、减少浪费和成本的目的。
下面我们将就SPC的原理和方法以及在质量管理中的应用做详细介绍。
一、SPC理论基础1、过程变异在任何时刻,一种生产过程的输出不能百分百相同。
这种不同可以由多种因素产生,包括异常的原材料、工艺变更、机器磨损、操作者错误等等。
导致输出中变异的因素称为特殊因素,也称为系统性因素。
这种特殊因素变异是造成过程差异的主要原因。
2、常规变异除了特殊因素外,生产过程的输出也有常规变异。
常规变异是指,即使没有特殊因素,也会有一些小的差异在过程输出中出现。
常规变异主要由不可避免的自然因素或生产设备的某些功能限制引起。
3、SPC方法SPC方法的核心是确定过程总体的变异范围,并确定过程中的差异是否在可接受的范围内。
在某些情况下,它可以通过实施统计控制来消除这种变异。
SPC方法可以有效地降低过程差异,提高产品质量,减少成本,增加可靠性,提高客户满意度。
二、SPC的应用范围SPC方法可以应用于所有类型的制造过程,包括离散、连续、传统目视检验和自动化检验。
以下是SPC可以处理生产过程的举例:•\t安装对象的物理特性:例如长度、宽度、高度、重量、颜色、性质等。
•\t材料特性:例如硬度、强度、韧性、导电性等。
•\t流体特性:例如温度、压力、流量、粘度等。
•\t机器特性:例如速度、功率、电流、温度、气压等。
•\t操作员特性:例如工作时间、工作速度、操作标准等。
三、SPC的主要原理SPC的主要原理是基于过程变异性的持续监测和控制,包括以下步骤:1、控制图建立控制图以时间为横轴,测量数据为纵轴。
每次收集数据时,都将点绘制到控制图上。
然后通过绘制中心线、上界和下界来确定控制限。
SPC在质量管理中的应用研究

SPC在质量管理中的应用研究SPC(Statistical Process Control,统计过程控制)是一种重要的质量管理工具,通过统计学方法监控和控制过程中的变异性,确保产品和服务的质量稳定性。
SPC在质量管理中的应用研究已经成为一个热门话题,吸引了众多研究者的关注和参与。
本文将通过对SPC在质量管理中的应用研究进行综述,探讨其在提高产品质量、降低成本和提升客户满意度等方面的重要作用。
SPC的基本原理是通过数据收集、分析和控制过程变异性,以便及时发现和纠正潜在的质量问题。
SPC主要包括过程能力分析、控制图、假设检验、方差分析等统计方法。
通过对这些方法的应用,企业可以实时监控生产过程中的质量变化,及时采取措施,确保产品符合质量标准。
1.提高产品质量:通过SPC方法对生产过程中的关键参数进行实时监控和分析,可以及时发现生产过程中的异常情况,减少次品率和废品率,提高产品质量。
许多研究表明,通过SPC技术优化生产过程,可以显著提高产品的合格率和稳定性。
2.降低成本:SPC技术可以有效降低生产过程中的变异性,减少废品和次品的产生,提高生产效率,降低生产成本。
经济学研究表明,SPC方法可帮助企业节省大量成本,提高盈利能力。
3.提升客户满意度:高质量的产品和服务是提升客户满意度的关键。
通过SPC技术,企业可以更好地控制产品质量,提供高品质的产品和服务,满足客户需求,提升客户满意度,增强市场竞争力。
4.持续改进:SPC方法不仅可以用于生产过程中的控制,还可以用于质量管理体系的持续改进。
通过对SPC数据的分析,企业可以发现潜在的改进机会,优化生产过程,持续提升产品质量和生产效率。
在SPC在质量管理中的应用研究中,还存在一些问题和挑战,需要进一步探讨和解决。
例如,如何选择合适的监控指标和参数、如何建立有效的SPC体系、如何利用SPC数据进行持续改进等问题都是研究者需要深入研究的方向。
总的来说,SPC在质量管理中的应用研究具有重要的理论和实践价值,对于提高产品质量、降低成本、提升客户满意度等方面都有着积极的作用。
spc质量控制

spc质量控制SPC(统计过程控制)是一种通过统计方法和工具对过程进行监控和管理的质量控制技术。
它旨在实时检测过程中的变异性并采取适当的控制措施,以确保产品或服务的质量稳定性和一致性。
在本文中,将介绍SPC的原理、实施步骤以及其在质量控制中的应用。
一、SPC的原理SPC的核心原理是通过数据收集和分析来了解过程中的变异性。
它基于以下两个假设:1. 过程变异性是正常的:任何过程在生产中都会存在一定的变异性,即使是最优化的过程也不可避免地存在着各种差异。
2. 变异性可以通过统计方法进行衡量和控制:SPC利用统计分析的工具和技术,能够准确地衡量和控制过程中的变异性。
二、SPC的实施步骤SPC的实施一般包括以下步骤:1. 确定关键过程参数(KPC):KPC是影响产品或服务质量的重要因素。
通过对生产过程的分析和了解,确定出关键的过程参数。
2. 收集数据:对KPC进行实时数据的收集和记录。
数据可以通过各种手段获取,如传感器、检测仪器等。
3. 统计分析:对收集到的数据进行统计分析,以了解过程中的变异性,并判断其是否在可控范围内。
4. 确定控制限:根据统计分析结果,确定上下限控制限。
控制限用于判断过程是否处于控制状态。
5. 监控过程:实施实时过程监控,及时发现和纠正过程中的异常情况或异常变异。
6. 持续改进:根据监控结果和分析,对过程进行改善,并持续跟踪和改进以确保过程的稳定性和一致性。
三、SPC在质量控制中的应用SPC在质量控制中具有广泛应用,可以用于监控产品的生产过程、服务的提供过程以及供应链中的各个环节。
以下是SPC在质量控制中的几个典型应用场景:1. 控制图的应用:控制图是SPC中最常见和重要的工具,用于监控过程中的变异性并进行相应的处理。
常见的控制图有均值图、范围图等,通过对过程数据的实时监控,能够及时发现并处理过程中的异常情况。
2. 过程能力分析:SPC可以通过对数据的统计分析,评估过程的能力指标,如过程的稳定性、精度和一致性等。
SPC在质量控制中的应用

SPC在质量控制中的应用在现代制造业中,质量控制是确保产品符合标准和要求的关键步骤。
统计过程控制(SPC)是一种通过统计数据分析来监督过程稳定性和产品质量的方法。
SPC的引入可以帮助制造商及时发现和处理生产中的问题,提高产品一致性,降低制造成本,提高客户满意度。
SPC的基本原理SPC依靠收集过程中产生的数据,并使用统计方法来分析这些数据,以确定生产过程是否稳定。
通过收集样本数据并制作控制图,可以监测过程的变化并及时采取措施。
常用的SPC工具包括控制图、直方图、散点图等。
SPC在质量控制中的应用帮助识别过程变化SPC可以帮助生产团队及时发现过程中的变化。
通过监测关键参数的变化,可以快速发现异常情况,并采取纠正措施。
这有助于降低不良品率,提高产品质量。
提高生产效率通过SPC,制造商可以了解生产过程中存在的变化和波动,从而优化生产流程,提高生产效率。
在发现问题后能够及时调整生产参数,减少浪费和重新制造的次数,提高生产效率。
降低制造成本通过SPC的实施,制造商可以减少不良品率,提高产品合格率,从而降低制造成本。
及时发现过程中的问题,可以节省修复成本,减少废品和重新加工的浪费,提高生产效率。
提高产品质量SPC可以帮助制造商及时发现生产过程中可能存在的问题,及时调整生产参数,确保产品质量符合标准要求。
通过持续地监控和改进生产过程,可以提高产品的一致性和稳定性,提升产品质量。
结语SPC作为一种有效的质量控制方法,在现代制造业中发挥着重要作用。
通过统计数据分析和过程监控,制造商可以提高产品质量,降低制造成本,提高生产效率,实现持续改进。
在未来的制造业中,SPC将继续发挥重要作用,推动企业不断提升竞争力。
统计过程控制在质量管理上的应用

统计过程控制在质量管理上的应用李晓潭;林雪梅【摘要】针对当前制造企业在质量管理上普遍存在的弊端,以TFT-LCD生产为例,采用统计过程控制这一成熟的质量管理技术,结合实际生产过程构建出系统构架,设计并实现了数据采集、统计量计算、异常判断、报警处理、参数建模和统计分析等服务,充分验证了统计过程控制在实际生产中的可靠性和实用性。
【期刊名称】《制造业自动化》【年(卷),期】2016(038)008【总页数】8页(P5-12)【关键词】统计过程控制;控制图;判异准则;质量特性数据【作者】李晓潭;林雪梅【作者单位】北京京东方显示技术有限公司,北京 100176;北京京东方显示技术有限公司,北京 100176【正文语种】中文【中图分类】TP249在工业4.0的大环境下,制造企业正在经历一次深刻的变革,其核心是现代信息技术与制造业的深度融合[1]。
当前国内制造企业普遍把统计过程控制(Statistical Process Control,SPC)作为质量管理的重要手段。
这是休哈特博士(W.A.Shewhart)1924年在美国贝尔实验室首次提出的一种质量控制技术。
经过多年的发展,现在ISO 9000质量管理体系特别注重过程控制和统计技术的应用,六西格玛管理也把统计过程控制作为控制阶段的主要工具之一[2,3]。
在进行数据收集和统计分析上,多数制造企业采用人工测量和记录关键质量特性数据,再通过JMP、MINITAB等软件来衡量产品批次的质量情况。
这样做法存在如下弊端:手工记录作业强度大、效率低、准确性无法保证,而且做事后分析,时间严重滞后,一旦出现质量问题,会导致产品过多损耗[4,5]。
同时,使用现有的软件无法与实际生产相集成,仅能作为静态的数据处理分析工具,不能动态地对生产过程进行干预或进行质量问题的层层追溯[6]。
鉴于此,本文以薄膜晶体管液晶显示器(thin-film transistor liquid crystal display,TFT-LCD)生产为例,针对其质量控制点,设计并开发了基于制造执行系统(Manufacturing Execution System,MES)的统计过程控制系统。
- 1、下载文档前请自行甄别文档内容的完整性,平台不提供额外的编辑、内容补充、找答案等附加服务。
- 2、"仅部分预览"的文档,不可在线预览部分如存在完整性等问题,可反馈申请退款(可完整预览的文档不适用该条件!)。
- 3、如文档侵犯您的权益,请联系客服反馈,我们会尽快为您处理(人工客服工作时间:9:00-18:30)。
统计过程控制(SPC)在质量管理中的应用作者:张蕾
来源:《科学导报·学术》2020年第19期
摘 ;要:本文分析研究了SPC的统计原理以及使用方法,结合本公司的产品--- 超白压延光伏玻璃的质量管控,着重介绍了生产过程中钢化颗粒度(`X-R Chart)控制图的建立技术,阐述了SPC统计过程控制在玻璃质量管控中的作用。
关键词:SPC;管控图;过程控制
1 SPC统计原理和控制图实施方法
1.1 SPC
SPC是英文Statistical Process Control的字首简称,即统计过程控制。
SPC是一种借助数理统计方法的过程控制工具,它对生产过程大量数据进行分析评价,根据反馈信息及时发现系统性因素出现的征兆,并采取措施消除其影响,使过程维持在仅受随机性因素影响的受控状态,达到控制质量的目的。
一个产品如果以它对顾客的符合度做为评断的标准,则它必须是由一个稳定而可重复运作的过程所生产的,亦即过程必须具有在生产目标值的些微变动内的生产能力。
统计过程控制(SPC)是使生产过程稳定和降低产品变异性以改善过程能力的数据统计分析方法。
产品质量的统计观点认为,过程的质量在各种影响因素的制约下,呈现波动性(变异性),但过程质量的波动并非漫无边际,在一定范围内,过程质量的波动呈现统计规律性。
1.2 实施SPC
统计过程控制的第一项工作为收集品质特性数据。
统计过程控制的第二项工作为评估、分析品质特性数据。
产品的品质特性值包括产品目标值和误差,误差包括可控误差和偶然误差。
在任何生产过程中,无论设计或维护是多么的好,总有某些天生或自然的误差存在。
这种自然的误差或背景干扰是由许多微小、必定的不可控制的原因所累积影响行成的,这被称作偶然误差。
可控误差比偶然误差来得大,它通常反映出过程控制中有不可接受的水平,这种误差主要来源于调整机器失当、操作失误和不良的原料三种现象。
在统计过程控制中,我们通常是以一个统计模式来做为判断过程足否为正常的决策基准。
目前最常用的工具为依据统计原理发展出来的控制图。
当决策系统判断过程不稳定时,接下来的工作是探讨造成过程异常的原因,此阶段之工作称为诊断。
诊断的范围包括人员、设备、物料、方法、测量、环境六个方面,从这六个方面分析工序不良产生的异常原因,找出最终影响产品质量的关键因素。
当找出造成过程不稳定的原因后,必须制定一些改善的措施,使得相同问题不再发生。
回馈控制系统之最后一个步骤是依据制定的改善措施,調整过程的可控制因素。
上述步骤需重复进行,以持续改善过程。
统计过程控制
牵涉到产品和过程的控制,但其重点是在品质数据的分析,只有在品质数据显示过程不稳定时,才考虑调整过程的参数。
1.3 控制图
控制图就是一种为了使过程符合控制状态而广泛使用的在线过程控制工具。
控制图也可用来评估过程中的过程能力参数,经由该参数来决定过程能力。
控制图也可提供改善过程的有用信息。
最后,统计过程控制的终极目标就是减少过程的误差,虽无法完全消除误差,但在尽可能减少误差方面,控制图是一有效的工具。
控制图为一图形表示工具,用以显示从样本中量测或计算所得的品质特性。
典型的控制图包含一中心线(CL),用以代表当制程处于统计管制内时品质特性之平均值。
此图同时包含两条水平线,称为上控制界限(UCL)及下控制界限(LCL),控制界限通常设在当过程为控制状态时,几乎所有点都可落在控制界限内。
只要点都在管制界限内,则制程可视为在统计控制内,对过程不须采取任何行动。
但只要一点在控制界限外,则代表过程有变异,此时我们必须找出造成这种变异的原因,并去除此变异。
控制图也有很多种类,分析我司光伏玻璃的缺陷因素,可以采用平均值与全距控制图(`X-R Chart)和过程能力分析图。
对于光伏玻璃来说,钢化颗粒度的管控尤为重要,因此本文着重介绍光伏玻璃钢化颗粒度(`X - R Chart)控制图的建立。
X控制图主要用于观察正态分布的均值的变化,R控制图主要用于观察正态分布分散或变异情况的变化,而`X-R控制图则将二者联合运用,用于观察数值正态分布的变化。
1.4 建立控制图
选择并收集产品生产过程中的品质特性数据。
确定样本大小、抽样频率和抽样方式,用间隔抽样的方法获得数据,并对数据进行处理。
1.4.1 收集并记录数据
在连续的产品生产过程中,收集并记录20~25个样本组的品质特性数据,通常每组样本量n=4~5个,保证控制过程的抽样率为84%~90%。
1.4.2 计算每个子组的均值(`X)和极差(R)
2. 作出控制线
在控制图中作出平均值和极值控制限的控制
线:将平均极差(`R)和过程均值(`X)画成水平实线,各控制限(UCLR,LCLR,UCLX,LCLX)画成水平虚线。
把线标上记号,在初始研究阶段,这些手段称为试验控制限。
3.绘制控制图
当分析用控制图中点子均在控制限之内或排列无缺陷时,表明生产过程稳定、无系统因素影响生产过程,尚不能说明不合格率小于允许值。
因此,在分析用控制图基础上需要绘制控制用控制图。
如图1所示。
相关步骤如下:
(1)消除系统因素。
依据分析用控制图提供的信息判断生产过程是否稳定,即是否有系统因素在起作用。
如果存在系统因素,应设法消除。
(2)重新计算控制限。
剔除分析用控制图中无代表性的数据(如落在界限外点子的数据)后,重新计算中心线和控制限。
(3)确认分布范围位于公差界限之内。
只有当生产过程稳定且产品质量特性值分布范围位于公差界限之内时,才能保证不出现大量不合格品。
4.控制图的判断准则
控制图制订后就成为了控制生产的依据,故控制图一定要以处于稳态日过程能力适宜的生产过程为依据来进行设计和计算。
因此,在开始建立控制图时,应先了解该过程是否处于稳态,过程能力是否适宜。
若过程不处于稳态或过程能力不适宜,就需要对过程进行调整,这样反复进行直到过程满足要求为止。
当上述要求满足后,控制图就可移交给车间使用,这时应用的控制图称为控制用控制图。
它的目的是保持生产处于稳态。
当偶尔发生异常后,应采取措施加以消除,使过程恢复稳态。
4.1控制图的分区
将控制图分区是为了便于说明过程的异常情况。
上下控制限分别位于中心线的上、下3σ距离处。
为了说明过程异常的8种方式,将控制图分为6个区,每个区的宽度为1σ,如图12所示。
6个区的标上为A、B、C、C、B、A,两个A区、B区、C区分别在中心线两侧,相对于中心线对称。
如图2所示。
4.2 控制图的判断准则--过程异常的8种模式
过程异常的8种模式又称为“变差的可查明原因的8种模式”。
当控制图上的点子出现过程异常的8种模式时,则判过程异常。
这8种模式分别为:
模式1:1个点落在A区以外;
模式2:连续9点落在中心线同一侧;
模式3:连续6点递增或递减;
模式4:连续14点中相邻点上下交替;
模式5:连续3点中有2点落在中心线同一侧的B区以外;
模式6:连续5点中有4点落在中心线同一侧的C区以外;
模式7:连续15点落在中心线两侧的C区内;
模式8:连续8点落在中心线两侧且无一点落在C区。
掌握这8种异常模式,可以帮助分析人员从计算错误、测量误差、原材料不合格、设备故障、抽样方法不科学、原材料混批等方面找出原因,事前预防,避免批量不量产生,降低质量损失,同时也通过系统的分析為技术改进提供科学依据。
5. SPC在光伏压延玻璃生产过程控制中的应用
光伏玻璃钢化颗粒度数据是衡量光伏玻璃钢化性能的关键指标之一,其计量特性值,适合用基于正态分布、灵敏度高的`X-R计量控制图来做管控,取颗粒度测量数据,然后将数据分成25个分子组,通过计算相关参数做出控制图,参见表3。
确定我司光伏产品生产过程稳定并具备足够的工序能力后,便选定一条钢化生产线收集统计产品钢化颗粒度数据,使用SPC进行数据统计分析。
用相同时间间隔抽取4件生产样本的方法进行数据统计,找出关键因素在生产过程中的变化。
当超出控制限时,说明关键因素在生产中出现不可控,需提醒生产者采取纠正措施,防止不良品的产生。
将其余24组样本的极差与均值分别打点于R图与`X图上,图6和图7看出过程的变异与均值均处于生产稳定状态。
由上述分析可知,在连续生产光伏玻璃中,按样本抽取产品做钢化颗粒度的测量,并按上述计算公式计算,并制作控制图。
通过观察上述控制图中点的波动状况,能及时显示出钢化颗粒度在生产过程中是受控还是失控,从而体现出SPC产品质量预防控制的作用。
6 结束语
运用SPC统计过程控制工具,可以在连续生产过程中,准确分析判断出生产中的可控误差,并提出改善措施进行针对性改善,从而提高质量管理人员对产品质量的把控力度,提高产品质量,如果运用产品在线检测设备自动检测产品质量特性,并自动运用SPC统计过程控制工具进行实时分析,则可以更加及时的发现生产过程的可控误差,及时改善产品质量,较大的提高过程控制能力。
参考文献
[1] ;荆敏.统计过程控制在课堂教学监控中的应用[J].太原城市职业技术学院学报,2013(02):102-103.
[2] ;图布新.质量统计过程控制技术SPC的应用及实现方法[J].科技展望,2016,26(09):141-143.
[3] ;祖晓琳. 基于SPC对C公司产品质量问题的研究[D].内蒙古科技大学,2015.。