6-6605811-1中文资料
最新en62366-1-中文版

1BS EN 62366-1:20152IEC 62366-1:2015医疗器械3第一部分:医疗器械可用性的应用451.范围67IEC 62366的这一部分规定了制造商分析、指定、开发和评估与安全有8关的医疗设备的可用性的过程。
该可用性工程(人工因素工程)过程允许制造商评估和减轻与正确使用和使用错误相关的风险,即正常使用。
它可用于识910别但不评估或减轻与异常使用相关的风险。
注1:安全是免于不可接受的风险。
使用错误可能会产生不可接受的风1112险,这可能导致直接的身体危害或临床功能的丧失或退化。
13注2:有关可用性工程应用于医疗设备的指南载于IEC 62366-22,该指南不仅涉及安全性,而且涉及与安全无关的可用性方面。
1415如果本国际标准中详细说明的可用性工程流程已得到遵守,则除非有客16观证据相反,否则医疗设备与安全有关的可用性被推定为可以使用。
17注3:这类客观证据可能随后来源于后期生产监视。
182.引用标准119下面的文档的全部或部分被标准的引用到这个文档中并且对于应用是20不可缺少的。
对于有日期的引用,只有引用的版本适用。
对于没有日期的引21用,参考文件的最新版本(包括任何修改)适用。
22注1:规范要求中引用这些参考文件的方式决定了它们的适用范围(全部23或部分)。
24注2:参考资料列于第46页开始的参考书目。
25ISO 14971:2007,医疗器械-医疗器械风险管理的应用263.术语和定义27为了这个文档的目的,术语和定义被提供在ISO14971:2007和下面的应28用中。
术语定义的索引从49页开始。
29303.1非正常使用31故意的有目的的动作或动作有目的的删除,这是与正常应用相反的或亵渎正常应用的,也是超出任何制造商制定的风险控制的用户相关界面的合理方式。
3233例如:为安全起见,不计后果地使用、破坏或故意无视信息是此类行为。
34条目说明1:也见4.1.335条目说明2:未异常使用的有意但错误的操作被视为使用错误的一种类型。
6661HX-XXX-C-EN

INGERSOLL RAND COMPANY LTDP .O. BOX 151 y ONE ARO CENTER y BRYAN, OHIO 43506-0151(800) 276-4658 y FAX (800) 266-7016© 2007CCN 15276603 READ THIS MANUAL CAREFULLY BEFORE INSTALLING,OPERATING OR SERVICING THIS EQUIPMENT.It is the responsibility of the employer to place this information in the hands of the operator. Keep for future reference.OPERATOR’S MANUAL6661HX-XXX-CINCLUDING: OPERATION, INSTALLATION & MAINTENANCERELEASED: 12-18-06REVISED: 6-15-07(REV. 03)1" DIAPHRAGM PUMPCSA CERTIFIED, 1:1 RATIO, METALLICINTENDED FOR USE WITH SWEET NATURAL GASSERVICE KITSRefer to Model Description Chart to match the pump mate-rial options.637118-C for gas section repair (see page 6).637119-C9-C for fl uid section repair (see page 4).PUMP DATAModels . . . . . . . . . . . . . see Model Description Chart for “-XXX”Pump Type . . . . . . . . . Gas Operated Double Diaphragm Material . . . . . . . . . . . . see Model Description Chart Weight . . . . . . . . . . . . . . . . . . . . . . . . . . . . . . 19 lbs (8.62 kgs)Maximum Gas Inlet Pressure . . . . . . . 120 p.s.i.g. (8.3 bar)Maximum Material Inlet Pressure . . . 10 p.s.i.g. (0.69 bar)Maximum Outlet Pressure . . . . . . . . . . 120 p.s.i.g. (8.3 bar)Maximum Flow Rate (flooded inlet) . . . 35 g.p.m. (133 l.p.m.)Displacement / Cycle @ 100 p.s.i.g. . 0.156 gal. (0.59 lit.)Maximum Particle Size . . . . . . . . . . . . . 1/8” dia. (3.2 mm)Maximum Temperature Limits . . . 32° to 125° F (0° to 52° C)Dimensional Data . . . . . . . . . . . . . . . . . . . see page 8Noise Level @ 70 p.s.i., 60 c.p.m. . . . . . . 64.5 db(A)cc The pump sound pressure levels published here have been updated to an Equivalent Continuous Sound Level (L Aeq ) to meet the intent of ANSI S1.13-1971, CAGI-PNEUROP S5.1 using four microphone locations.Figure 1MODEL DESCRIPTION CHART6661 H 0 - 1 C 9 - CCenter Section Material, Fluid Connection H - Aluminum, 1 - 11-1/2 N.P .T.F. - 1Fluid Cap / Manifold Material, Hardware 0 - Aluminum, Carbon Steel Fluid Section Service Kit Selection EXAMPLE: Model #6661H0-1C9-CFluid Section Service Kit # 637119-C9-C6661H0 - 1 X X - C Ball Diaphragm637119 - X X - C Seat Material 1 - Aluminum Diaphragm Material 9 - HytrelBall Material C - Hytrel®Page 2 of 86661HX-XXX-C (en)WARNING EXCESSIVE GAS PRESSURE. Can cause per-sonal injury, pump damage or property damage.Do not exceed the maximum inlet gas pressure asstated on the pump model plate.Be sure material hoses and other components are ableto withstand fl uid pressures developed by this pump.Check all hoses for damage or wear. Be certain dispens-ing device is clean and in proper working condition.WARNING STATIC SPARK. Can cause explosion result-ing in severe injury or death. Ground pump andpumping system.Use the pump ground lug provided. Connect to a 12ga. (minimum) wire (kit is included) to a good earthground source.Sparks can ignite fl ammable material and vapors.The pump must be electrically grounded using thegrounding conductor provided. Improper groundingcan cause improper and dangerous operation.Secure pump, connections and all contact points toavoid vibration and generation of contact or staticspark.Consult local building codes and electrical codes forspecifi c grounding requirements.After grounding, periodically verify continuity ofelectrical path to ground. Test with an ohmmeterfrom each component (e.g., hoses, pump, clamps, con-tainer, spray gun, etc.) to ground to insure continuity.Ohmmeter should show 0.1 ohms or less.Submerse the outlet hose end, dispensing valve ordevice in the material being dispensed if possible.(Avoid free streaming of material being dispensed.)Use hoses incorporating a static wire.Use proper ventilation.Keep infl ammables away from heat, open fl ames andsparks.Keep containers closed when not in use.WARNING Pump exhaust may contain contaminants.Can cause severe injury. Pipe exhaust away from workarea and personnel.The gas outlet of the pump must be vented to a safe lo-cation in accordance with local codes or, in the absenceof local codes, an industry or nationally recognizedcode having jurisdiction over the specifi c installation.Use a grounded 3/8” minimum i.d. hose between thepump and the muffl er.WARNING HAZARDOUS PRESSURE. Can result in seri-ous injury or property damage. Do not service orclean pump, hoses or dispensing valve while the sys-tem is pressurized.Disconnect gas supply line and relieve pressure from the system by opening dispensing valve or device and / or carefully and slowly loosening and removing out-let hose or piping from pump.WARNING injury or property damage. Do not attempt to return a pump to the factory or service center that contains hazardous material. Safe handling practices must comply with local and national laws and safety codey yy y y y y yy y y y yyyyOPERATING AND SAFETY PRECAUTIONSREAD, UNDERSTAND AND FOLLOW THIS INFORMATION TO AVOID INJURY AND PROPERTY DAMAGE.requirements.Obtain Material Safety Data Sheets on all materials from the supplier for proper handling instructions.WARNING minum wetted parts cannot be used with 1,1,1-trichlo-roethane, methylene chloride or other halogenated hydrocarbon solvents which may react and explode.Check pump motor section, fl uid caps, manifolds and all wetted parts to assure compatibility before using with solvents of this type.CAUTION pump wetted parts and the substance being pumped, flushed or recirculated. Chemical compatibility may change with temperature and concentration of the chemical(s) within the substances being pumped, fl ushed or circulated. For specifi c fl uid compatibility, consult the chemical manufacturer.CAUTION mechanical stress only. Certain chemicals will signifi -cantly reduce maximum safe operating temperature. Consult the chemical manufacturer for chemical com-patibility and temperature limits. Refer to PUMP DATA on page 1 of this manual.CAUTION have been trained for safe working practices, under-stand it’s limitations, and wear safety goggles / equip-ment when required.CAUTION port of the piping system. Be certain the system com-ponents are properly supported to prevent stress on the pump parts.Suction and discharge connections should be flex-ible connections (such as hose), not rigid piped, and should be compatible with the substance being pumped.CAUTION Do not allow pump to operate when out of material for long periods of time.Disconnect gas line from pump when system sits idle for long periods of time.CAUTION to assure compatible pressure rating and longest ser-vice life.NOTICE Install the pump in the vertical position. The pump may not prime properly if the balls do not check by gravity upon start-up.NOTICE Re-torque all fasteners before operation. fasteners to loosen. Re-torque all fasteners to insure against fl uid or gas leakage.NOTICE Replacement warning labels are available upon request: “Static Spark” pn \ 93616-1, Diaphragm WARNINGCAUTION y y y y6661HX-XXX-C (en) Page 3 of 8y Loctite® is a registered trademark of Henkel Loctite Corporation y 271™, 262™, 572™ and 577™ are trademarks of Henkel Loctite Corporation y y Hytrel®, Teflon® and Viton® are registered trademarks of the DuPont Company y ARO® is a registered trademark of Ingersoll-Rand Company yMAINTENANCECertain ARO “Smart Parts” are indicated which should be available for fast repair and reduction of down time.Provide a clean work surface to protect sensitive internal moving parts from contamination from dirt and foreign matter during service disassembly and reassembly.Keep good records of service activity and include the pump in preventive maintenance program.Service kits are available to service two separate dia-phragm pump functions: 1. GAS SECTION, 2. FLUID SEC-TION. The Fluid Section is divided further to match typical active Material Options.Before disassembling, empty captured material in the outlet manifold by turning the pump upside down to drain material from the pump.FLUID SECTION DISASSEMBLYRemove top manifold(s).Remove (22) balls, (19) “O” rings and (21) seats.Remove (15) fl uid caps.Remove (14) screws, (6) washers, (7) diaphragms and (5) washers.Remove (3) “O” rings. NOTE: Do not scratch or mar the surface of (1) diaphragm rod.FLUID SECTION REASSEMBLYReassemble in reverse order.Clean and inspect all parts. Replace worn or damaged parts with new parts as required.Lubricate (1) diaphragm rod and (2) “O” ring with Key-Lube grease.Use ARO pn 98930-T bullet (installation tool) to aid in in-stallation of (2) “O” ring on (1) diaphragm rod.Be certain (7) diaphragms align properly with (15) fluid caps before making fi nal torque adjustments on bolt and nuts to avoid twisting the diaphragm.Re-check torque settings after pump has been re-started and run a while.y y y yy1.2.3.4.5.y y y y y yWARNINGdamage, personal injury or property damage.Always flush the pump with a solvent compatible withthe material being pumped if the material being pumped is subject to “setting up” when not in use for a period of time.Disconnect the gas supply from the pump if it is to be inactive for a few hours.The outlet material volume is governed not only by the gas supply, but also by the material supply available at the inlet. The material supply tubing should not be too small or restrictive. Be sure not to use hose which might collapse.When the diaphragm pump is used in a forced-feed (fl ooded inlet) situation, it is recommended that a “check valve” be installed at the gas inlet.Secure the diaphragm pump legs to a suitable surface to insure against damage by vibration.y y y y yy yPage 4 of 8 6661HX-XXX-C (en)637119-C9-C fluid section service kits include: Balls (item 22), diaphragms (item 7) plus items 2, 3, 19 and 93706-1 Key-Lube grease (page 6).MATERIAL CODE[A] = Aluminum [B] = Nitrile [C] = Carbon Steel [Co] = Copper [H] = Hytrel [SS] = Stainless Steel [T] = Tefl on® PTFE [V] = Viton®“Smart Parts”, keep these items on hand in addition to the service kit for fast repair and reduction of down time.6661HX-XXX-C (en) Page 5 of 8) TORQUE REQUIREMENTS (NOTE: DO NOT OVERTIGHTEN FASTENERS.(14) Bolt, 25 - 30 ft. lbs (33.9 - 40.7 Nm).(26) Bolt, 120 - 140 in. lbs (13.6 - 15.8 Nm).(29) Nut, 120 - 140 in. lbs (13.6 - 15.8 Nm).LUBRICATION / SEALANTSApply Loctite® 271™ to threads.Apply Key-Lube grease (93706-1) to all “O” rings, “U” cups and matingparts.NOTICE: Radius edge of parts (5 and 6) is against diaphragm.FOR THE GAS MO-TOR SECTION, SEE PAGES 6 & 7.Torque Sequence3275186419 1921212222151626 (26 (1614 (751Figure 229 (62339Cross section view of diaphragm.Fluid sideGas sidePage 6 of 8 6661HX-XXX-C (en)9 Indicates parts included in 637118-C gas section repair kit.MATERIAL CODE[A] = Aluminum [C] = Carbon Steel [SS] = Stainless Steel [B] = Nitrile [D] = Acetal [U] = Polyurethane [Bz] = Bronze[Ny] = Nylon[Z] = ZincGAS MOTOR SECTION SERVICEService is divided into two parts - 1. Pilot Valve, 2. Major Valve.GENERAL SERVICE NOTES:Gas Motor Section service is continued from Fluid Section repair.Inspect and replace old parts with new parts as neces-sary. Look for deep scratches on metallic surfaces, and nicks or cuts in “O” rings.Take precautions to prevent cutting “O” rings upon instal-lation.Lubricate “O” rings with Key-Lube grease.Do not over-tighten fasteners. Refer to torque specifi ca-tion block on view.Re-torque fasteners following restart.PILOT VALVE DISASSEMBLYRemove (104) retaining ring.Remove (123) screws and (122) “O” rings.Remove (118) piston rod, (121) sleeve bushing, (119) “O” rings and (120) spacers from the (101) motor body.Remove (103) sleeve and (102) “O” rings.y y y y y y 1.2.3.4.PILOT VALVE REASSEMBLYReplace two (102) “O” rings, if worn or damaged, and rein-stall (103) sleeve.Install one of the (121) sleeve bushings, (119) “O” rings, (120) spacers and the remaining (121) bushing.Carefully push (118) pilot rod into bushing etc. and retain on each end with the two (122) “O” rings. Retain with (123) screws.Replace (104) retaining rings.MAJOR VALVE DISASSEMBLYRemove (107) legs and (108 and 117) gaskets.On the side opposite the air inlet, push on the inner di-ameter of (111) spool. This will force the (109) piston out. Continue pushing the (111) spool and remove. Check for scratches and gouges.Reach into the gas section (exhaust side) and remove (116) spacer, (115) spacers, (113) “O” rings, (114) “O” rings, (112) washers, etc. Check for damaged “O” rings.MAJOR VALVE REASSEMBLYReplace (112) washer, (114) “O” ring and (113) “O” ring onto (115) spacer and insert etc. NOTE: Be careful to ori-ent spacer legs away from blocking internal ports.Lubricate and carefully insert (111) spool.Install (117) gasket and (107) leg.Lubricate and install (110) packing cup and insert (109) piston into (air inlet side) cavity, the (110) packing cup lips should point outward.Install (108) gasket and replace (107) leg.1.2.3.4.1.2.3.1.2.3.4.5.“Smart Parts”, keep these items on hand in addition to the service kit for fast repair and reduction of down time.108MAJOR VALVE CROSS SECTION DETAIL1136661HX-XXX-C (en) Page 7 of 8Page 8 of 86661HX-XXX-C (en)TROUBLE SHOOTINGProduct discharged from exhaust outlet.Check for diaphragm rupture.Check tightness of (14) diaphragm screw.Gas bubbles in product discharge.Check connections of suction plumbing.Check “O” rings between intake manifold and fluid caps.Check tightness of (14) diaphragm screw.y y y y y Low output volume, erratic fl ow or no fl ow.Check gas supply.Check for plugged outlet hose.Check for kinked (restrictive) outlet material hose.Check for kinked (restrictive) or collapsed inlet material hose.Check for pump cavitation - suction pipe should be sized at least as large as the inlet thread diameter of the pump for proper fl ow if high viscosity fl uids are being pumped. Suction hose must be a non-collapsing type, capable of pulling a high vacuum.Check all joints on the intake manifolds and suction con-nections. These must be gas tight.Inspect the pump for solid objects lodged in the dia-phragm chamber or the seat area.y y y y y y y DIMENSIONAL DATA。
微生物屏障试验 DIN 58953-6_2010 Test report
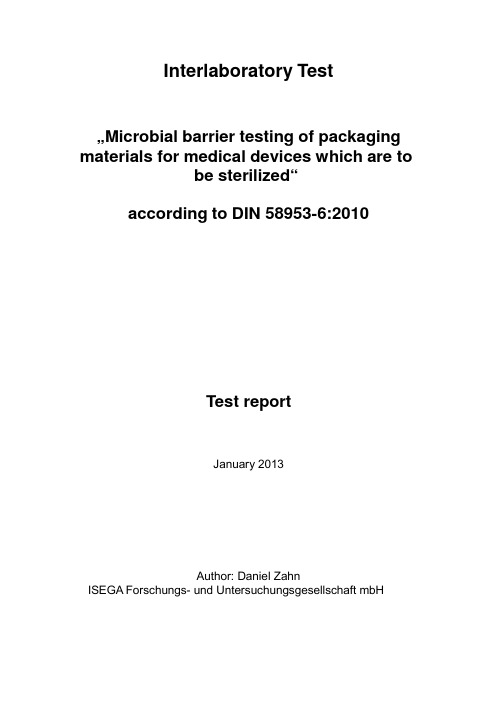
Interlaboratory T est …Microbial barrier testing of packa ging materials for medical devices which are tobe ster ili ze d“according to DIN 58953-6:2010Test re portJanuary 2013Author: Daniel ZahnISEGA Forschungs- und Untersuchungsgesellschaft mbHTest report Page 2 / 15Table of contentsSeite1.General information on the Interlaboratory Test (3)1.1 Organization (3)1.2 Occasion and Objective (3)1.3 Time Schedule (3)1.4 Participants (4)2.Sample material (4)2.1 Sample Description and Execution of the Test (4)2.1.1 Materials for the Analysis of the Germ Proofness under Humidityaccording to DIN 58953-6, section 3 (5)2.1.2 Materials for the Analysis of the Germ Proofness with Air Permeanceaccording to DIN 58953-6, section 4 (5)2.2 Sample Preparation and Despatch (5)2.3 Additional Sample and Re-examination (6)3.Results (6)3.1 Preliminary Remark (6)3.2 Note on the Record of Test Results (6)3.3 Comment on the Statistical Evaluation (6)3.4 Outlier tests (7)3.5 Record of Test Results (7)3.5.1 Record of Test Results Sample F1 (8)3.5.2 Record of Test Results Sample F2 (9)3.5.3 Record of Test Results Sample F3 (10)3.5.4 Record of Test Results Sample L1 (11)3.5.5 Record of Test Results Sample L2 (12)3.5.6 Record of Test Results Sample L3 (13)3.5.7 Record of Test Results Sample L4 (14)4.Overview and Summary (15)Test report Page 3 / 15 1. General Information on the Interlaboratory Test1.1 OrganizationOrganizer of the Interlaboratory Test:Sterile Barrier Association (SBA)Mr. David Harding (director.general@)Pennygate House, St WeonardsHerfordshire HR2 8PT / Great BritainRealization of the Interlaboratory Test:Verein zur Förderung der Forschung und Ausbildung fürFaserstoff- und Verpackungschemie e. V. (VFV)vfv@isega.dePostfach 10 11 0963707 Aschaffenburg / GermanyTechnical support:ISEGA Forschungs- u. Untersuchungsgesellschaft mbHDr. Julia Riedlinger / Mr. Daniel Zahn (info@isega.de)Zeppelinstraße 3 – 563741 Aschaffenburg / Germany1.2 Occasion and ObjectiveIn order to demonstrate compliance with the requirements of the ISO 11607-1:2006 …Packaging for terminally sterilized medical devices -- Part 1: Requirements for materials, sterile barrier systems and packaging systems“ validated test methods are to be preferably utilized.For the confirmation of the microbial barrier properties of porous materials demanded in the ISO 11607-1, the DIN 58953-6:2010 …Sterilization – Sterile supply – Part 6: Microbial barrier testing of packaging materials for medical devices which are to be sterilized“ represents a conclusive method which can be performed without the need for extensive equipment.However, since momentarily no validation data on DIN 58953-6 is at hand concerns emerged that the method may lose importance against validated methods in a revision of the ISO 11607-1 or may even not be considered at all.Within the framework of this interlaboratory test, data on the reproducibility of the results obtained by means of the analysis according to DIN 58953-6 shall be gathered.1.3 Time ScheduleSeptember 2010:The Sterile Barrier Association queried ISEGA Forschungs- und Unter-suchungsgesellschaft about the technical support for the interlaboratory test.For the realization, the Verein zur Förderung der Forschung und Ausbildungfür Faserstoff- und Verpackungschemie e. V. (VFV) was won over.November 2010: Preliminary announcement of the interlaboratory test / Seach for interested laboratoriesTest report Page 4 / 15 January toDecember 2011: Search for suitable sample material / Carrying out of numerous pre-trials on various materialsJanuary 2012:Renewed contact or search for additional interested laboratories, respectively February 2012: Sending out of registration forms / preparation of sample materialMarch 2012: Registration deadline / sample despatchMay / June 2012: Results come in / statistical evaluationJuly 2012: Despatch of samples for the re-examinationSeptember 2012: Results of the re-examination come in / statistical evaluationNovember 2012: Results are sent to the participantsDecember 2012/January 2013: Compilation of the test report1.4 ParticipantsFive different German laboratories participated in the interlaboratory test. In one laboratory, the analyses were performed by two testers working independently so that six valid results overall were received which can be taken into consideration in the evaluation.To ensure an anonymous evaluation of the results, each participant was assigned a laboratory number (laboratory 1 to laboratory 6) in random order, which was disclosed only to the laboratory in question. The complete laboratory number breakdown was known solely by the ISEGA staff supporting the proficiency test.2. Sample Material2.1 Sample Description and Execution of the TestUtmost care in the selection of suitable sample material was taken to include different materials used in the manufacture of packaging for terminally sterilized medical devices.With the help of numerous pre-trials the materials were chosen covering a wide range of results from mostly germ-proof samples to germ permeable materials.Test report Page 5 / 15 2.1.1 Materials for the Analysis of Germ Proofness under Humidity according to DIN 58953-6, section 3:The participants were advised to perform the analysis on the samples according to DIN 58953-6, section 3, and to protocol their findings on the provided result sheets.The only deviation from the norm was that in case of the growth of 1 -5 colony-forming units (in the following abbreviated as CFU) per sample, no re-examination 20 test pieces was performed.2.1.2 Materials for the Analysis of Germ Proofness with Air Permeance according to DIN 58953-6, section 4:The participants were advised to perform the analysis on the samples according to DIN 58953-6, section 4, and to protocol their findings on the provided result sheets.2.2 Sample Preparation and DespatchFor the analysis of the germ proofness under humidity, 10 test pieces in the size of 50 x 50 mm were cut out of each sample and heat-sealed into a sterilization pouch with the side to be tested up.Out of the 10 test pieces, 5 were intended for the testing and one each for the two controls according to DIN 58953-6, sections 3.6.2 and 3.6.3. The rest should remain as replacements (e.g. in case of the dropping of a test piece on the floor etc.).For the analysis of the germ proofness with air permeance, 15 circular test pieces with a diameter of 40 mm were punched out of each sample and heat-sealed into a sterilization pouch with the side to be tested up.Test report Page 6 / 15 Out of the 15 test pieces, 10 were intended for the testing and one each for the two controls according to DIN 58953-6, section 4.9. The rest should remain as replacements (e.g. in case of the dropping of a test piece on the floor etc.).The sterilization pouches with the test pieces were steam-sterilized in an autoclave for 15 minutes at 121 °C and stored in an climatic room at 23 °C and 50 % relative humidity until despatch.2.3 Additional Sample and Re-examinationFor the analysis of the germ proofness under humidity another test round was performed in July / August 2012. For this, an additional sample (sample L4) was sent to the laboratories and analysed (see 2.1.2). The results were considered in the evaluation.For validation or confirmation of non-plausible results, occasional samples for re-examination were sent out to the laboratories. The results of these re-examinations (July / August 2012) were not taken into consideration in the evaluation.3. Results3.1 Preliminary RemarkSince the analysis of germ proofness is designed to be a pass / fail – test, the statistical values and precision data were meant only to serve informative purposes.The evaluation of the materials according to DIN58953-6,sections 3.7and 4.7.6by the laboratories should be the most decisive criterion for the evaluation of reproducibility of the interlaboratory test results. Based on this, the classification of a sample as “sufficiently germ-proof” or “not sufficiently germ-proof” is carried out.3.2 Note on the Record of Test Results:The exact counting of individual CFUs is not possible with the required precision if the values turn out to be very high. Thus, an upper limit of 100 CFU per agar plate or per test pieces, respectively, was defined. Individual values above this limit and values which were stated with “> 100” by the laboratories, are listed as 100 CFU per agar plate or per test piece, respectively, in the evaluation.Test report Page 7 / 153.3 Comment on the Statistical EvaluationThe statistical evaluation was done based on the series of standards DIN ISO 5725-1ff.The arithmetic laboratory mean X i and the laboratory standard deviation s i were calculated from the individual measurement values obtained by the laboratories.The overall mean X of the laboratory means as well as the precision data of the method (reproducibility and repeatability) were determined for each sample3.4 Outlier testsThe Mandel's h-statistics test was utilised as outlier test for differences between the laboratory means of the participants.A laboratory was identified as a “statistical outlier” as soon as an exceedance of Mandel's h test statistic at the 1 % significance level was detected.The respective results of the laboratories identified as outliers were not considered in the statistical evaluation.3.5 Record of Test ResultsOn the following pages, the records of the test results for each interlaboratory test sample with the statistical evaluation and the evaluation according to DIN 58953-6 are compiled.Test report Page 8 / 153.5.1 Record of Test Results Sample F1Individual Measurement values:Statistical Evaluation:Comment:Laboratory 4, as an outlier, has not been taken into consideration in the statistical Evaluation.Outlier criterion: Mandel's h-statistics (1 % level of significance)Overall mean X:91.0CFU / agar plateRepeatability standard deviation s r:17.9CFU / agar plateReproducibility standard deviation s R:19.8CFU / agar plateRepeatability r:50.0CFU / agar plateRepeatability coefficient of variation:19.6%Reproducibility R:55.5CFU / agar plateReproducibility coefficient of variation:21.8%Evaluation according to DIN 58953-6, Section 3.7:Lab. 1 - 6:Number of CFU > 5, i.e. the material is classified as not sufficiently germ-proof.Conclusion:All of the participants, even the Laboratory 4 which was identified as an outlier, came to the same results and would classify the sample material as “not sufficiently germ-proof”Test report Page 9 / 153.5.2 Record of Test Results Sample F2Individual Measurement values:Statistical Evaluation:Comment:Laboratory 4, as an outlier, has not been taken into consideration in the statistical Evaluation.Outlier criterion: Mandel's h-statistics (1 % level of significance)Overall mean X:0CFU / agar plateRepeatability standard deviation s r:0CFU / agar plateReproducibility standard deviation s R:0CFU / agar plateRepeatability r:0CFU / agar plateRepeatability coefficient of variation:0%Reproducibility R:0CFU / agar plateReproducibility coefficient of variation:0%Evaluation according to DIN 58953-6, Section 3.7:Lab. 1 – 3:Number of CFU = 0, i.e. the material is classified as sufficiently germ-proofLab. 4:Number of CFU ≤ 5, i.e. a re-examination on 20 test pieces would have to be done Lab. 5 – 6:Number of CFU = 0, i.e. the material is classified as sufficiently germ-proofConclusion:All of the participants, except for the Laboratory 4 which was identified as an outlier, came to the same results and would classify the sample material as “sufficiently germ-proof”.Test report Page 10 / 153.5.3 Record of Test Results Sample F3Individual Measurement values:Statistical Evaluation:Overall mean X:30.1CFU / agar plateRepeatability standard deviation s r:17.2CFU / agar plateReproducibility standard deviation s R:30.9CFU / agar plateRepeatability r:48.2CFU / agar plateRepeatability coefficient of variation:57.1%Reproducibility R:86.5CFU / agar plateReproducibility coefficient of variation:103%Evaluation according to DIN 58953-6, Section 3.7:Lab. 1 - 4:Number of CFU > 5, i.e. the material is classified as not sufficiently germ-proof. Lab. 5:Number of CFU = 0, i.e. the material is classified as sufficiently germ-proof. Lab. 6:Number of CFU > 5, i.e. the material is classified as not sufficiently germ-proof.Conclusion:Five of the six participants came to the same result and would classify the sample as “not sufficiently germ-proof”. Only laboratory 5 would classify the sample material as “sufficiently germ-proof”.Test report Page 11 / 153.5.4 Record of Test Results Sample L1Individual Measurement values:Statistical Evaluation:Overall mean X:0.09CFU / test pieceRepeatability standard deviation s r:0.32CFU / test pieceReproducibility standard deviation s R:0.33CFU / test pieceRepeatability r:0.91CFU / test pieceRepeatability coefficient of variation:357%Reproducibility R:0.93CFU / test pieceReproducibility coefficient of variation:366%Evaluation according to DIN 58953-6, Section 4.7:Lab. 1 - 6:Number of CFU < 15, i.e. the material is classified as sufficiently germ-proof.Conclusion:All participants came to the same result and would classify the sample as “sufficiently germ-proof”.Test report Page 12 / 153.5.5 Record of Test Results Sample L2Individual Measurement values:Statistical Evaluation:Overall mean X:0.73CFU / test pieceRepeatability standard deviation s r: 1.10CFU / test pieceReproducibility standard deviation s R: 1.18CFU / test pieceRepeatability r: 3.07CFU / test pieceRepeatability coefficient of variation:151%Reproducibility R: 3.32CFU / test pieceReproducibility coefficient of variation:163%Evaluation according to DIN 58953-6, Section 4.7:Lab. 1:Number of CFU > 15, i.e. the material is classified as not sufficiently germ-proof. Lab. 2 - 6:Number of CFU < 15, i.e. the material is classified as sufficiently germ-proof.Conclusion:Five of the six participants came to the same result and would classify the sample as “sufficiently germ-proof”. Only laboratory 1 exceeds the limit value slightly by 1 CFU, so that the sample would be classified as “not sufficiently germ-proof”.Test report Page 13 / 153.5.6 Record of Test Results Sample L3Individual Measurement values:Statistical Evaluation:Overall mean X:0.36CFU / test pieceRepeatability standard deviation s r: 1.00CFU / test pieceReproducibility standard deviation s R: 1.06CFU / test pieceRepeatability r: 2.79CFU / test pieceRepeatability coefficient of variation:274%Reproducibility R: 2.98CFU / test pieceReproducibility coefficient of variation:293%Evaluation according to DIN 58953-6, Section 4.7:Lab. 1 - 6:Number of CFU < 15, i.e. the material is classified as sufficiently germ-proof.Conclusion:All participants came to the same result and would classify the sample as “sufficiently germ-proof”.Test report Page 14 / 153.5.7 Record of Test Results Sample L4Individual Measurement values:Statistical Evaluation:Overall mean X:35.1CFU / test pieceRepeatability standard deviation s r:18.8CFU / test pieceReproducibility standard deviation s R:42.6CFU / test pieceRepeatability r:52.7CFU / test pieceRepeatability coefficient of variation:53.7%Reproducibility R:119CFU / test pieceReproducibility coefficient of variation:122%Evaluation according to DIN 58953-6, Section 4.7:Lab. 1 - 3:Number of CFU > 15, i.e. the material is classified as not sufficiently germ-proof. Lab. 4:Number of CFU < 15, i.e. the material is classified as sufficiently germ-proof. Lab. 5 - 6:Number of CFU > 15, i.e. the material is classified as not sufficiently germ-proof.Conclusion:Five of the six participants came to the same result and would classify the sample as“not sufficiently germ-proof”.Test report Page 15 / 15 4. Overview and SummarySummary:In case of four of the overall seven tested materials, a 100 % consensus was reached regarding the evaluation as“sufficiently germ-proof”and“not sufficiently germ-proof”according to DIN 58 953-6.As for the other three tested materials, there were always 5 concurrent participants out of 6 (83 %). In each case, only one laboratory would have evaluated the sample differently.It is noteworthy that the materials about the evaluation of which a 100 % consensus was reached were the smooth sterilization papers. The differences with one deviating laboratory each occurred with the slightly less homogeneous materials, such as with the creped paper and the nonwoven materials.。
(完整版)EN62366-1-2015中文版

BS EN 62366-1:2015IEC 62366-1:2015医疗器械第一部分:医疗器械可用性的应用1.范围IEC 62366的这一部分规定了制造商分析、指定、开发和评估与安全有关的医疗设备的可用性的过程。
该可用性工程(人工因素工程)过程允许制造商评估和减轻与正确使用和使用错误相关的风险,即正常使用。
它可用于识别但不评估或减轻与异常使用相关的风险。
注1:安全是免于不可接受的风险。
使用错误可能会产生不可接受的风险,这可能导致直接的身体危害或临床功能的丧失或退化。
注2:有关可用性工程应用于医疗设备的指南载于IEC 62366-22,该指南不仅涉及安全性,而且涉及与安全无关的可用性方面。
如果本国际标准中详细说明的可用性工程流程已得到遵守,则除非有客观证据相反,否则医疗设备与安全有关的可用性被推定为可以使用。
注3:这类客观证据可能随后来源于后期生产监视。
2.引用标准下面的文档的全部或部分被标准的引用到这个文档中并且对于应用是不可缺少的。
对于有日期的引用,只有引用的版本适用。
对于没有日期的引用,参考文件的最新版本(包括任何修改)适用。
注1:规范要求中引用这些参考文件的方式决定了它们的适用范围(全部或部分)。
注2:参考资料列于第46页开始的参考书目。
ISO 14971:2007,医疗器械-医疗器械风险管理的应用3.术语和定义为了这个文档的目的,术语和定义被提供在ISO14971:2007和下面的应用中。
术语定义的索引从49页开始。
3.1非正常使用故意的有目的的动作或动作有目的的删除,这是与正常应用相反的或亵渎正常应用的,也是超出任何制造商制定的风险控制的用户相关界面的合理方式。
例如:为安全起见,不计后果地使用、破坏或故意无视信息是此类行为。
条目说明1:也见4.1.3条目说明2:未异常使用的有意但错误的操作被视为使用错误的一种类型。
条目说明3:非正常使用并不能免除制造商考虑与非用户界面相关的风险控制手段。
lord 公司的水溶液性胶合剂 CHEMLOK 8560D 安全数据表 说明书

USA SAFETY DATA SHEET1. CHEMICAL PRODUCT AND COMPANY IDENTIFICATIONProduct name:CHEMLOK 8560DProduct Use/Class: Aqueous AdhesiveLORD Corporation111 LORD DriveCary, NC 27511-7923 USATelephone: 814 868-3180Non-Transportation Emergency: 814 763-2345Chemtrec 24 Hr Transportation Emergency No.800 424-9300 (Outside Continental U.S. 703 527-3887)EFFECTIVE DATE: 06/30/20212. HAZARDS IDENTIFICATIONGHS CLASSIFICATION:Serious eye damage/eye irritation Category 2ASkin sensitization Category 1ACarcinogenicity Category 2Specific target organ systemic toxicity (single exposure) Category 2 blood systemSpecific target organ systemic toxicity (single exposure) Category 1 Respiratory system, Systemic toxicity Specific target organ systemic toxicity (repeated exposure) Category 2 blood systemSpecific target organ systemic toxicity (repeated exposure) Category 1 LungsHazardous to the aquatic environment - acute hazard Category 2Hazardous to the aquatic environment - chronic hazard Category 2GHS LABEL ELEMENTS:Symbol(s)Signal WordD ANGERHazard StatementsCauses serious eye irritation.May cause an allergic skin reaction.Suspected of causing cancer.May cause damage to organs.(blood system)Causes damage to organs.(Respiratory system, Systemic toxicity)May cause damage to organs through prolonged or repeated exposure.(blood system)Causes damage to organs through prolonged or repeated exposure.(Lungs)Toxic to aquatic life.Toxic to aquatic life with long lasting effects.Precautionary StatementsPreventionObtain special instructions before use.Do not handle until all safety precautions have been read and understood.Wear protective gloves/eye protection/face protection.Use personal protective equipment as required.Do not breathe dust/fume/gas/mist/vapors/spray.Wash thoroughly after handling.300000005458Do not eat, drink or smoke when using this product.Contaminated work clothing should not be allowed out of the workplace.Avoid release to the environment.ResponseGet medical advice/attention if you feel unwell.IF exposed: Call a POISON CENTER or doctor/physician.Specific treatment (see supplemental first aid instructions on this label).IF ON SKIN: Wash with plenty of soap and water.If skin irritation or rash occurs: Get medical advice/attention.IF IN EYES: Rinse cautiously with water for several minutes. Remove contact lenses, if present and easy to do.Continue rinsing.If eye irritation persists: Get medical advice/attention.Wash contaminated clothing before reuse.Collect spillage.StorageStore locked up.Disposal:Dispose of contents/container in accordance with waste/disposal laws and regulations of your country or particular locality.Other Hazards:This product contains component(s) which have the following warnings; however based on the GHS classification criteria of your country or locale, the product mixture may be outside the respective category(s).Acute: In elevated-temperature applications, product may release vapors that may produce cyanosis in the absence of sufficient ventilation or adequate respiratory protection. May be harmful if swallowed. Ingestion is not an expected route of entry in industrial or commercial uses. This product contains a residual amount of a chemical substance that may cause an allergic skin and/or respiratory reaction.Causes mild skin irritation.Chronic: Prolonged or repeated contact may result in dermatitis. The nitrogen substituted aromatic in this product gave positive results for mutagenicity in an Ames Assay study while two other mutagenicity studies proved negative.IARC has identified the proprietary curative in this product as an "animal suspected" carcinogen, Group 3, which downgrades a previous NCI report of it as an "animal positive" carcinogen. IARC has designated carbon black as Group 2B - inadequate evidence for carcinogenicity in humans, but sufficient evidence in experimental animals. In 2006 IARC reaffirmed its 1995 finding that there is "inadequate evidence" from human health studies to assesswhether carbon black causes cancer in humans. Further, epidemiological evidence from well-conductedinvestigations has shown no causative link between carbon black exposure and the risk of malignant or non-malignant respiratory disease in humans.withheld.The above Nonylphenol ethoxylate compound is listed by ECHA as an SVHC.FIRST AID - EYE CONTACT: Flush eyes immediately with large amount of water for at least 15 minutes holding eyelids open while flushing. Get prompt medical attention.FIRST AID - SKIN CONTACT: Flush contaminated skin with large amounts of water while removing contaminated clothing. Wash affected skin areas with soap and water. Get medical attention if symptoms occur.FIRST AID - INHALATION: Move person to fresh air. Restore and support continued breathing. If breathing is difficult, give oxygen. Get immediate medical attention.FIRST AID - INGESTION: If swallowed, do not induce vomiting. Call a physician or poison control center immediately for further instructions. Never give anything by mouth if victim is rapidly losing consciousness, unconscious or convulsing.SUITABLE EXTINGUISHING MEDIA: Carbon Dioxide, Dry Chemical, Foam, Water FogUNSUITABLE EXTINGUISHING MEDIA: Not determined for this product.SPECIFIC HAZARDS POSSIBLY ARISING FROM THE CHEMICAL: Keep containers tightly closed. Closed containers may rupture when exposed to extreme heat. Use water spray to keep fire exposed containers cool. WARNING: Due to the combustible nature of the dried film of this product and the potential for smoldering or fire, the accumulation and buildup of the dried film on spray booth walls and floors, spindles, fixtures and other surfaces should be avoided, and any buildup should be removed. Keep the dried film accumulations away from sparks, friction, impact, high heat (>235 F/>112 C) or other sources of ignition. These conditions could cause the dried film to ignite very readily and quickly, and the resulting smoldering or fire may be difficult to extinguish. During removal of accumulation/buildup of this product, take precautions to avoid heat, friction and impact during the cleaning process. Use paint stripper, brass brush, or plastic scraper for cleaning. In the event of smoldering or a fire involving the dried product, Cold Fire®** fire suppressing agent is preferred as the extinguishing medium. If Cold Fire® is not available, use water spray as the extinguishing medium. Take efforts to ensure that these agents reach the base of the smoldering or fire. Parker-LORD Corporation will not be responsible for personal injuries, property damage or any other damages arising from the accumulation (buildup, cleaning/removal or any related smoldering or fire) resulting from the use of this product. Refer to the Chemlok® Safe Handling Guide for additional information. **NOTE: Parker-LORD Corporation has determined Cold Fire® fire suppressing agent to be effective in extinguishing fires involving dried Chemlok® adhesives. Parker-LORD does not recommend any particular equipment or system for use in delivering or applying Cold Fire® products. Customer is responsible for determining that Cold Fire® products and any delivery equipment or system is appropriate and effective for customer's specific needs. During a fire, irritating and/or toxic gases and particulate may be generated by thermal decomposition or combustion.SPECIAL PROTECTIVE EQUIPMENT AND PRECAUTIONS FOR FIRE-FIGHTERS: Wear full firefighting protective clothing, including self-contained breathing apparatus (SCBA). If water is used, fog nozzles are preferable.PERSONAL PRECAUTIONS, PROTECTIVE EQUIPMENT AND EMERGENCY PROCEDURES: Avoid breathing vapors. Avoid contact. Use appropriate respiratory protection for large spills or spills in confined area.ENVIRONMENTAL PRECAUTIONS: Do not contaminate bodies of water, waterways, or ditches, with chemical or used container.METHODS AND MATERIALS FOR CONTAINMENT AND CLEANUP: Notify appropriate authorities if necessary. Contain and remove with inert absorbent material. Avoid contact. Keep non-essential personnel away from spill area. Before attempting cleanup, refer to hazard caution information in other sections of the SDS form.HANDLING: Keep closure tight and container upright to prevent leakage. Avoid skin and eye contact. Wash thoroughly after handling. Do not handle until all safety precautions have been read and understood. Empty containers should not be re-used. Use with adequate ventilation.STORAGE: Store only in well-ventilated areas. Keep from freezing. Keep container closed when not in use.INCOMPATIBILITY: Strong acids, bases, and strong oxidizers.Engineering controls: Sufficient ventilation in pattern and volume should be provided in order to maintain air contaminant levels below recommended exposure limits.PERSONAL PROTECTION MEASURES/EQUIPMENT:RESPIRATORY PROTECTION: Use a NIOSH approved chemical/mechanical filter respirator designed to remove a combination of particulates and organic vapor if occupational limits are exceeded. For emergencysituations, confined space use, or other conditions where exposure limits may be greatly exceeded, use an approved air-supplied respirator. For respirator use observe OSHA regulations (29CFR 1910.134) or use in accordance with applicable laws and regulations of your country or particular locality.SKIN PROTECTION: Use neoprene, nitrile, or rubber gloves to prevent skin contact.EYE PROTECTION: Use safety eyewear including safety glasses with side shields and chemical goggles where splashing may occur.OTHER PROTECTIVE EQUIPMENT: Remove and wash contaminated clothing before reuse.HYGIENIC PRACTICES: Wash hands before eating, smoking, or using toilet facility. Do not smoke in any chemical handling or storage area. Food or beverages should not be consumed anywhere this product is handled or stored. Wash thoroughly after handling.Typical values, not to be used for specification purposes.ODOR: Odorless VAPOR PRESSURE: N.D.APPEARANCE: Green/Black VAPOR DENSITY: Heavier than Air PHYSICAL STATE: Liquid LOWER EXPLOSIVE LIMIT: Not ApplicableUPPER EXPLOSIVE LIMIT: Not ApplicableFLASH POINT:≥ 201 °F, 93 °CSetaflash Closed CupBOILING RANGE: 100 °C EVAPORATION RATE: Slower than n-butyl-acetate AUTOIGNITION TEMPERATURE:N.D.DENSITY: 1.18 g/cm3 (9.83 lb/gal) DECOMPOSITION TEMPERATURE:N.D. VISCOSITY, DYNAMIC: N.D.ODOR THRESHOLD: N.D.VISCOSITY, KINEMATIC: N.D.SOLUBILITY IN H2O: Soluble VOLATILE BY WEIGHT: 52.14 %pH: 6.0VOLATILE BY VOLUME: 61.54 %FREEZE POINT: N.D. VOC CALCULATED: 0.02 lb/gal, 3 g/l COEFFICIENT OF WATER/OILN.D.DISTRIBUTION:LEGEND: N.A. - Not Applicable, N.E. - Not Established, N.D. - Not DeterminedHAZARDOUS POLYMERIZATION: Hazardous polymerization will not occur under normal conditions.STABILITY: Product is stable under normal storage conditions.CONDITIONS TO AVOID: High temperatures.; For dried product issues, refer to Section 5 of the (M)SDS. INCOMPATIBILITY: Strong acids, bases, and strong oxidizers.HAZARDOUS DECOMPOSITION PRODUCTS: Decomposition due to high temperatures or a fire causes the formation of irritating and/or toxic gases, organic vapors or fumes., May contain CO, CO2, oxides of nitrogen, oxides of sulfur, halogenated by-products, Metal oxidesEXPOSURE PATH: Refer to section 2 of this SDS.SYMPTOMS:Refer to section 2 of this SDS.TOXICITY MEASURES:Germ cell mutagenicity: No classification proposedCarcinogenicity: Category 2 - Suspected of causing cancer.Components contributing to classification: Curative.Reproductive toxicity: No classification proposedPERSISTENCE AND DEGRADABILITY:Not determined for this product.BIOACCUMULATIVE: Not determined for this product.MOBILITY IN SOIL: Not determined for this product.OTHER ADVERSE EFFECTS: Not determined for this product.DISPOSAL METHOD: Disposal should be done in accordance with Federal (40CFR Part 261), state and local environmental control regulations. If waste is determined to be hazardous, use licensed hazardous waste transporter and disposal facility. Waste streams, including the dried adhesive residue, resulting from the use of this product should be tested for RCRA characteristics, including ignitability, to determine any applicable waste classifications.US DOT RoadProper Shipping Name: Environmentally hazardous substances, liquid, n.o.s.Hazard Class: 9SECONDARY HAZARD: NoneUN/NA Number: 3082Packing Group: IIIEmergency Response Guide Number: 171For US DOT non-bulk road shipments this material may be classified as NOT REGULATED. For the mostaccurate shipping information, refer to your transportation/compliance department regarding changes inpackage size, mode of shipment or other regulatory descriptors.IATA CargoPROPER SHIPPING NAME: Environmentally hazardous substance, liquid, n.o.s.Hazard Class: 9HAZARD CLASS: NoneUN NUMBER: 3082PACKING GROUP: IIIEMS: 9LIMDGPROPER SHIPPING NAME: Environmentally hazardous substance, liquid, n.o.s.Hazard Class: 9HAZARD CLASS: NoneUN NUMBER: 3082PACKING GROUP: IIIEMS: F-AThe listed transportation classification applies to non-bulk shipments. It does not address regulatory variations due to changes in package size, mode of shipment or other regulatory descriptors. For the most accurate shipping information, refer to your transportation/compliance department.U.S. FEDERAL REGULATIONS: AS FOLLOWS:SARA SECTION 313This product contains the following substances subject to the reporting requirements of Section 313 of Title III of the Superfund Amendment and Reauthorization Act of 1986 and 40 CFR part 372.:Chemical Name CAS Number Weight % Less ThanZinc compound PROPRIETARY10.0%TOXIC SUBSTANCES CONTROL ACT:INVENTORY STATUSThe chemical substances in this product are on the active TSCA Section 8 Inventory or exempt.EXPORT NOTIFICATIONThis product contains the following chemical substances subject to the reporting requirements of TSCA 12(B) if exported from the United States:NoneUnder HazCom 2012 it is optional to continue using the HMIS rating system. It is important to ensure employees have been trained to recognize the different numeric ratings associated with the HazCom 2012 and HMIS schemes.HMIS RATINGS - HEALTH: 2* FLAMMABILITY: 1 PHYSICAL HAZARD: 0* - Indicates a chronic hazard; see Section 2Revision: Company LogoEffective Date: 06/30/2021The information contained herein is, to the best of our knowledge and belief, accurate. However, since the conditions of handling and use are beyond our control, we make no guarantee of results, and assume no liability for damages incurred by use of this material. It is the responsibility of the user to comply with all applicable federal, state and local laws and regulations.。
66158-001资料

66158 SINGLE CHANNEL OPTOCOUPLER DIRECT REPLACEMENT FOR 3C92CMii OPTOELECTRONIC PRODUCTSDIVISIONREVISION B 12/29/00Features:• HighReliability•Base lead eliminated for improved noise immunity • Ruggedpackage•Stability over wide temperature•+500V electrical isolation A pplications:•Eliminate ground loops • Levelshifting• Linereceiver •Switching power supplies • MotorcontrolDESCRIPTIONThe 66158 contains a gallium arsenide infrared LED optically coupled to a silicon planar phototransistor. The optocoupler is built on a TO-46 header. The collector of the phototransistor is electrically connected to the case. This optocoupler is capable of transmitting signals between two galvanic sources. The potential difference between transmitter and receiver should not go over the maximum isolation voltage. The internal base connection has been eliminated for improved noise immunity.ABSOLUTE MAXIMUM RATINGSInput to Output Voltage (500V)Emitter-Collector Voltage (7V)Collector-Emitter Voltage (value applies to emitter-base open-circuited & the input-diode equal to zero) (60V)Reverse Input Voltage (7V)Input Diode Continuous Forward Current at (or below) 65°C Free-Air Temperature (see note 1) .................................50mA Peak Forward Input Current (value applies for tw < 1µs, PRR < 300 pps) .....................................................................500mA Continuous Collector Current............................................................................................................................................50mA Continuous Transistor Power Dissipation at (or below) 25°C Free-Air Temperature (see Note 2)..............................230mW Storage Temperature........................................................................................................................................-65°C to +150°C Operating Free-Air Temperature Range..........................................................................................................-55°C to +125°C66158SINGLE CHANNEL OPTOCOUPLER (Direct Replacement for 3C92C)REVISION B 12/29/00ELECTRICAL CHARACTERISTICST A = 25°C unless otherwise specified.PARAMETERSYMBOLMIN TYP MAXUNITSTEST CONDITIONSInput Diode Static Reverse Current I R 1µA V R = 3V Input Diode Static Forward Voltage V F 1.15 1.2V I F = 2mA Input Diode Static Forward Voltage V F 1.31.5V I F = 50mA Reverse Breakdown Voltage B VR 712V I R = 100µA Input Diode CapacitanceC IN25pFV = 0V, f = 1MHzOUTPUT TRANSISTORT A = 25°C unless otherwise specified.PARAMETERSYMBOLMINTYP MAX UNITSTEST CONDITIONSCollector-Emitter Breakdown Voltage V (BR)CEO 50V I C = 1mA, I B = 0, I F = 0Emitter-Collector Breakdown Voltage V (BR)ECO 7VI C = 10µA, I E = 10µA, I F = 0Collector-Emitter Dark CurrentI CEO1I CEO25010nA nAV CE = 50V, I F = 0mA V CE = 5V, I F = 0mACOUPLED CHARACTERISTICST A = 25°C unless otherwise specified.PARAMETERSYMBOLMINTYP MAX UNITSTEST CONDITIONSOn State Collector Current I C(ON)4mAV CE = 5V, I F = 10mA On State Collector CurrentI C(ON)320mA V CE = 0.4V, I F = 10mA On State Collector Current -55°C I C(ON)2mAV CE = 5V, I F = 10mA Collector-Emitter Saturation Voltage V CE(SAT)0.4VI F = 50mA, I C = 10mA Isolation Resistance R ISO 109ΩV IN-OUT = 500VInput to Output Capacitance C IO 2 2.5pFf = 1MHzDelay Time t d 24µs V CE = 5V, I F = 2mA, R L = 100ΩStorage Time t s 0.20.5µs V CE = 5V, I F = 2mA, R L = 100ΩRise Time t r 35µs V CE = 5V, I F = 2mA, R L = 100ΩFall Timet f45µsV CE = 5V, I F = 2mA, R L = 100ΩRECOMMENDED OPERATING CONDITIONS:PARAMETERSYMBOL MIN MAX UNITSInput Current, Low Level I FL 01µAInput Current, High Level I FH 210mA Supply Voltage V CE 550VOperating TemperatureT A-55125°CSELECTION GUIDEPART NUMBER PART DESCRIPTION66158-011Single Channel optocoupler, military operating range (-55° to +125°C)66158-101Single Channel optocoupler, full mil-temp (-55° to +125°C) with 100% device screening 66158-001Single Channel optocoupler, commercial (0° to 70°C)。
6605834-1中文资料

6605834-1 Product DetailsHome | Customer Support | Suppliers | Site Map | Privacy Policy | Browser Support© 2007 Tyco Electronics Corporation All Rights Reserved Searc hHome > Products > By Type > Modular Jacks & Plugs > Product Feature Selector > Product Details6605834-1Active Integrated Magnetic, Stacked (Mag45™)and Power over Ethernet (PoE)Always EU RoHS/ELV Compliant (Statement of Compliance)Product Highlights:l10/100 POE Applicationl Component Type = Single Portl Magnetic Circuit = 7D15l Turns Ratio = 1:1l Power over Ethernet (PoE) Type =Enabled PowerView all Features | Find SimilarProductsCheck Pricing &AvailabilitySearch for ToolingProduct FeatureSelectorContact Us AboutThis ProductQuick LinksDocumentation & Additional InformationProduct Drawings:l1X1 MAG45(TM), MODULAR JACK, 7DN2 SCHEMATIC, 7D15 Po...(TIF, English)Catalog Pages/Data Sheets:l None AvailableProduct Specifications:l Mag45* Modular Jacks With Integrated Magnetics(PDF, English) Application Specifications:l None AvailableInstruction Sheets:l None AvailableCAD Files:l None AvailableList all Documents Additional Information:l Product Line InformationRelated Products:l ToolingProduct Features (Please use the Product Drawing for all design activity)Product Type Features:l Power over Ethernet (PoE) Type = EnabledPowerl Signal Routing Type = Auto MDI/MDIX, NICl PCB Mount Style = Thru Holel Shielded = Yesl Shield Material = BrassMechanical Attachment:l Jack Configuration = 1 x 1Electrical Characteristics:l Component Type = Single Portl Turns Ratio = 1:1l Impedance (?) = 100Termination Related Features:l Bottom Panel Ground Tab = WithoutBody Related Features:l LED = Withl Shield Panel Ground Tabs = Withl Latch Orientation = Inverted -Latch Upl Bottom Shield = Withoutl Shield Plating = Semi-Bright Nickel (Pre-plated) l PCB Tail Length (mm [in]) = 3.30 [0.130] Housing Related Features:l Housing Flammability Rating = UL 94V-0l Housing Material = Thermoplastic Polyester(PET)Configuration Related Features:l Magnetic Circuit = 7D15l Decoupling Capacitor = Withoutl Rear PCB Ground Tab = Withoutl Signal Lead Quantity = 8Industry Standards:l RoHS/ELV Compliance = RoHS compliant, ELVcompliantl Lead Free Solder Processes = Wave soldercapable to 240°C, Wave solder capable to 260°C, Wave solder capable to 265°Cl RoHS/ELV Compliance History = Always wasRoHS compliantIdentification Marking:l Left LED Color (Position #1) = Green -250ohm resistorl Right LED Color (Position #2) = Yellow -250ohm resistorConditions for Usage:l Temperature Rating = Office / Premises (0 ºCto +70 ºC)Operation/Application:l Application = 10/100 POEOther:l Brand = Tyco ElectronicsProvide Website Feedback | Contact Customer Support Products Documentation Resources My Account Customer Support。
伪罗特水溶性抗渗剂技术数据表说明书

The data on this sheet represent typical values. Since application variables are a major factor in product performance, this information should serve only as a general guide. Valspar assumes no obligation or liability for use of this information. UNLESS VALSPAR AGREES OTHERWISE IN WRITING, VALSPAR MAKES NO WARRANTIES, EXPRESS OR IMPLIED, AND DISCLAIMS ALL IMPLIED WARRANTIES INCLUDINGWARRANTIES OF MERCHANTABILITY OR FITNESS FOR A PARTICULAR USE OR FREEDOM FROM PATENT INFRINGEMENT. VALSPAR WILL NOT BE LIABLE FOR ANY SPECIAL, INCIDENTAL OR CONSEQUENTIAL DAMAGES. Your only remedy for any defect in this product is the replacement of the defective product, or a refund of its purchase price, at our option.Version 2: Feb 2011 (supersedes all previous revisions) (Continued on reverse)Waterborne RetarderTECHNICAL DATA SHEETPRODUCT NUMBERYXT0700COMPANION PRODUCTSZenith™ Coatings, stains, and glaze basesDESCRIPTION/USESZenith™ Waterborne Retarder is designed to increase the open time of Zenith™ coatings, stain, and glaze bases where needed. This may be necessary in conditions of high temperature, excessive airmovement, or when applying coatings to very large pieces where longer open time is needed. This product is not designed for thinning purposes and will not affect viscosity at recommended amounts. Zenith™Waterborne Retarder is designed for professional use only. For Wood Substrates Only.PRODUCT ADVANTAGES• HAP’s Free• Formaldehyde Free • Very low odor •Water cleanupAPPLICATION FEATURES• Easy mixing.•Extends the open time of Zenith™ products.PRECAUTIONSThese products are recommended for professional application and are designed for interior use only. Always pre-test the system on your substrate and under your line conditions to verify suitability to the application and to avoid potential need for costly refinishing. Valspar Wood Finishes products aredesigned to protect and enhance the natural beauty of wood, but cannot eliminate natural discoloration or deterioration of wood as it ages. Additional notes:Do not mix with other finishing systems or deviate from these finishing recommendations. Valspar will not be held liable for finish failures resulting from the mixing of products or deviations from finishing recommendations.PHYSICAL PROPERTIES (objective specifications)Viscosity: N/A Weight Solids: 0 Volume Solids: 0%Weight/Gallon: 8.66 lbs/gal¹ Theoretical Coverage: N/A Flash Point: 999ºF Closed CupAir Quality Information: VOC: 8.66 lbs/gal of Product AIM VOC : 1037.7g/l VOC Ratio: N/A VHAP: 0.0 lb VHAP/lb solid-HAP’s Free Photochemically Reactive: NoDry Times (78°F, 50%RH): Air Dry N/AForce DryN/AShelf life: 2 years from the manufacturing datePot Life: N/AApplication Equipment:Use only equipment with plastic, stainless steel, or Teflon coated valves and parts.Recommended tip sizes : N/ANote: All information provided is typical (as formulated) and will not represent exact values for every product. For specific Air Quality Data for each product, VOC reports are available upon request.FINISHING RECOMMENDATIONSGeneral: Surface must be clean and dust free with moisture content of 6-8% prior to finishing. Remove all dirt, dust, wax and wood marks. Proper sanding and preparation of the wood is critical to achieving consistent results. New Wood: Finish sand surface (150-180 grit) and remove all sanding dust.Painted or Varnished Wood: Remove all paint or varnish then follow new wood instructions.Before using, mix product by hand, or if using mechanical agitation such as an air mixer or drill, mix at slow to moderate speed until there is no material on the bottom of the container.The Zenith™ product line is packaged ready to use. However, certain conditions of high temperature, excessive air movement, or size of the piece to be sprayed may require a longer open time than normal. Such conditions may warrant the use of Zenith™ Waterborne Retarder. Amounts of addition are specific to each product. Please refer to the following table to maintain regulatory compliance:Zenith™ clear sealer and topcoatsLKF700X series, PKF720X series, PKF750X series, PKS7200: Add 1-5 oz (1-4%) max per gal. Max VOC after recommended addition is 275 g/l or 2.3 lbs per gallon.Zenith™ basecoats and white topcoatsLKW7100, LKN7200, LKW710X series, PKW730X series: Add 1-4 oz (1-3%) max per gal. Max VOC after recommended addition is 275 g/l or 2.3 lbs per gallon.Zenith™ stains and glazesLWS075X series: Add 1-2.5 oz (1-2%) max per gal. Max VOC after recommended addition is 250 g/l or 2.08 lbs per gallon.LWS4750: Add 1-2oz (1-1.5%) max per gal. Max VOC after recommended addition is 250 g/l or 2.08 lbs per gallon. LWS4725: Add 1-2oz (1-1.5%) max per gal. Max VOC after recommended addition is 250 g/l or 2.08 lbs per gallon. LWS1000: Add 4-7oz (3-5%) max per gal. Max VOC after recommended addition is 120 g/per liter of Material.For Zenith products/series not listed-No retarder is recommended.Note: Adding Zenith™ Waterborne Retarder will increase the dry time needed before re-coating. The amount ofextra time needed will depend on ambient conditions and air movement. Make sure products are thoroughly dry before re-coating.Caution: Exceeding recommended amounts may cause severely extended dry times and cause a soft film in the early curing stages.Clean equipment with warm water. If coating has dried, Acetone may be required to remove dried film. Keep container closed when not in use to avoid skinning. Do not transfer contents to other containers for storage or disposal. In case of spillage, absorb with inert material such as sand or kitty litter. Dispose of empty cans or unused portion in accordance with local state and federal regulations.Store in a cool, dry place. DO NOT FREEZE! Product should be stored in temperatures between 50°-110°F. Close all containers after use. Do not store near heat or sparks. Spills should be cleaned up with non-sparking tools. See the product MSDS for complete safety information.Always pre-test the system on your substrate and under your line conditions to verify suitability to the application and avoid potential need for costly refinishing. All dry times listed are as tested under ideal indoor environmental conditions of 78°F (26°C) with relative humidity not exceeding 50%. These products are recommended for use under temperature conditions of 60-100°F (16-38°C) and when relative humidity is below 50% during application and drying time. Low temperatures, poor air circulation or high humidity will extend dry times. Valspar strongly recommends against use of these products if temperatures of air, material, or surface to be coated are below 60°F (16°C) or below the dew point. Abnormal conditions of temperature or humidity may adversely affect product performance. Please contact your authorized Valspar Wood Finishes distributor for additional product use recommendations and finishing guidance.MSDS AND CPDS SHEETS AVAILABLE UPON REQUEST。
- 1、下载文档前请自行甄别文档内容的完整性,平台不提供额外的编辑、内容补充、找答案等附加服务。
- 2、"仅部分预览"的文档,不可在线预览部分如存在完整性等问题,可反馈申请退款(可完整预览的文档不适用该条件!)。
- 3、如文档侵犯您的权益,请联系客服反馈,我们会尽快为您处理(人工客服工作时间:9:00-18:30)。
/TE/bin/TE.Connect?C=1&M=BYPN&TCPN=6-6605811-1&RQPN=6-6605811-1 (4 of 4)27/09/2007 11:05:55 •
q q
6-6605811-1 Product Details - Tyco Electronics
Shielded = Yes Shield Material = Brass
Configuration Related Features: q Magnetic Circuit = 7G01P1 q Decoupling Capacitor = 2KV q Rear PCB Ground Tab = Without
q
Resources
RoHS Compliance & Alternates Cross Reference Products Compare Multiple Products Check Distributor Inventory Find Authorized Distributors
q
My Account
Search Search By: Part Number Sign In | Register (Why Register?)
q
Products
By Type Connectors Electromechanical Components Electronic Modules Fiber Optics Filters Identification Labeling Products Passive Components Power Sources RF & Microwave Products Tooling Products Touch Screen Displays Tubing, Molded and Harnessing Products Wire, Cable and Cable Assemblies List all Product Types
q
q
q
Check Pricing & Availability Search for Tooling Product Feature Selector Contact Us About This Product
Documentation & Additional Information Product Drawings: q 1X1 MAG45(TM), MODULAR JACK, 7G1P1 GIGABIT SCHEMATIC... (PDF, English) Catalog Pages/Data Sheets: q None Available Product Specifications: q Mag45* Modular Jacks With Integrated Magnetics (PDF, English) Application Specifications: q None Available Instruction Sheets: q None Available CAD Files: q None Available List all Documents Additional Information: q Product Line Information Related Products: q Tooling
6-6605811-1 Product Details
/TE/bin/TE.Connect?C=1&M=BYPN&TCPN=6-6605811-1&RQPN=6-6605811-1 (2 of 4)27/09/2007 11:05:55 •
q
Mechanical Attachment: q Jack Configuration = 1 x 1 Electrical Characteristics: q Component Type = Single Port
q q
Signal Lead Quantity = 10
Industry Standards: q RoHS/ELV Compliance = RoHS compliant, ELV compliant
q
Shield Panel Ground Tabs = With Latch Orientation = Inverted - Latch Up Bottom Shield = Without Shield Plating = Semi-Bright Nickel (Pre-plated)
Housing Related Features: q Housing Flammability Rating = UL 94V-0 q Housing Material = Thermoplastic
Quick Links
q
6-6605811-1
Active
Product Highlights: q Gigabit Ethernet Application q Component Type = Single Port q Magnetic Circuit = 7G01P1 q Turns Ratio = 1:1 q 1 x 1 Jack Configuration View all Features
元器件交易网
Integrated Magnetic, Stacked (Mag45™) and Power over Ethernet (PoE)
Always EU RoHS/ELV Compliant (Statement of Compliance)
6-6605811-1 Product Details - Tyco Electronics
q
Turns Ratio = 1:1 Impedance (!&) = 100
q
Lead Free Solder Processes = Wave solder capable to 240°C, Wave solder capable to 260°C, Wave solder capable to 265°C RoHS/ELV Compliance History = Always was RoHS compliant
/TE/bin/TE.Connect?C=1&M=BYPN&TCPN=6-6605811-1&RQPN=6-6605811-1 (3 of 4)27/09/2007 11:05:55 •
元器件交易网
Product Features (Please use the Product Drawing for all design activity) Product Type Features: q Signal Routing Type = Auto MDI/MDIX q PCB Mount Style = Thru Hole
Brand = Transpower
Provide Website Feedback | Contact Customer Support Home | Customer Support | Suppliers | Site Map | Privacy Policy | Browser Support © 2007 Tyco Electronics Corporation All Rights Reserved
/TE/bin/TE.Connect?C=1&M=BYPN&TCPN=6-6605811-1&RQPN=6-6605811-1 (1 of 4)27/09/2007 11:05:55 •
元器件交易网
By Industry Aerospace & Defense Appliance Automotive Communications Computer & Consumer Electronics Industrial & Commercial Instrumentation & Medical Equipment By Brand A to Z
q
6-6605811-1 Product Details - Tyco Electronics
Documentation
Find
Documents & Drawings Find CAD Models SPICE/Electrical Models NAFTA Certificate of Origin White Papers
元器件交易网
Skip to content Corporate Home | Worldwide Electronic Components | Segments | Who We Are
6-6605811-1 Product Details - Tyco Electronics
Termination Related Features: q Bottom Panel Ground Tab = Without Body Related Features: q LED = With
q q q q
Identification Marking: q Left LED Color (Position #1) = Green - 250 ohm resistor q Right LED Color (Position #2) = Green - 250 ohm resistor Conditions for Usage: q Temperature Rating = Office / Premises (0 ºC to +70 ºC) Operation/Application: q Application = Gigabit Ethernet Other: q Insulator = Without