制动器设计
制动器设计-计算说明书

制动器设计-计算说明书三、课程设计过程(一)设计制动器的要求:1、具有良好的制动效能—其评价指标有:制动距离、制动减速度、制动力和制动时间。
2、操纵轻便—即操纵制动系统所需的力不应过大。
对于人力液压制动系最大踏板力不大于(500N )(轿车)和700N (货车),踏板行程货车不大于150mm ,轿车不大于120mm 。
3、制动稳定性好—即制动时,前后车轮制动力分配合理,左右车轮上的制动力矩基本相等,汽车不跑偏、不甩尾;磨损后间隙应能调整!4、制动平顺性好—制动力矩能迅速而平稳的增加,也能迅速而彻底的解除。
5、散热性好—即连续制动好,摩擦片的抗“热衰退”能力要高(指摩擦片抵抗因高温分解变质引起的摩擦系数降低);水湿后恢复能力快。
6、对挂车的制动系,还要求挂车的制动作用略早于主车;挂车自行脱钩时能自动进行应急制动。
(二)制动器设计的计算过程:设计条件:车重2t ,重量分配60%、40%,轮胎型175/75R14,时速70km/h ,最大刹车距离11m 。
1. 汽车所需制动力矩的计算根据已知条件,汽车所需制动力矩:M=G/g ·j ·r k (N ·m ) 206.321j )(v S ?=(m/s 2)式中:r k —轮胎最大半径 (m);S —实际制动距离 (m);v 0 —制动初速度 (km/h)。
217018211 3.6j ??=?=(m/s 2) m=G/g=2000kg查表可知,r k 取0.300m 。
M=G/g ·j ·r k =2000·18·0.300=10800(N ·m )前轮子上的制动器所需提供的制动力矩:M ’=M/2?60%=3240(N ·m )为确保安全起见,取安全系数为 1.20,则M ’’=1.20M ’=3888(N ·m )2. 制动器主要参数的确定(1)制动盘的直径D制动盘直径D 希望尽量大些,这时制动盘的有效半径得以增大,就可以降低制动钳的夹紧力,降低摩擦衬块的单位压力和工作温度。
鼓式制动器设计

鼓式制动器设计
设计说明书:鼓式制动器设计
第一部分:引言
引言部分介绍了鼓式制动器的作用和设计的背景,解释了为何需要设
计新的鼓式制动器,并概述了本文档的结构和目标。
第二部分:设计要求
设计要求部分列出了鼓式制动器设计的主要目标和性能要求。
这些要
求主要包括制动力、制动效率、制动稳定性、耐久性等方面的要求。
同时,还需要考虑到制动器的重量、尺寸、成本等因素。
第三部分:结构设计
结构设计部分包括制动器的整体结构设计和各个部件的详细设计。
其中,整体结构设计需要考虑到制动器的安装位置和方式,以及与车辆其他
部件的配合关系。
各个部件的设计需要考虑到材料的选择、尺寸的确定、
加工工艺等因素。
第四部分:工作原理
工作原理部分详细介绍了鼓式制动器的工作原理。
包括制动器的构成、制动材料的摩擦特性、制动力的产生机制等内容。
同时,还需要考虑到制
动过程中的热量产生和传递机制,以确保制动器的稳定性和耐久性。
第五部分:性能评估
性能评估部分对鼓式制动器的主要性能进行评估。
主要包括制动力、制动效率、制动稳定性、耐久性等方面的测试和分析。
需要设计相应的测试方法和评估标准,以确保设计的鼓式制动器能够满足要求。
第六部分:结论
结论部分对整个设计过程进行总结,评价了设计的鼓式制动器的优缺点,并提出了进一步改进的建议。
同时,还需要总结设计过程中的经验和教训,以便在将来的鼓式制动器设计中能够有所借鉴。
制动器的设计计算

制动器的设计计算制动器是用来减速和停止运动物体的一种装置。
在设计制动器时,需要考虑以下几个因素:制动力的大小、制动距离的要求、制动器材料的选型、热力学效应以及制动器的结构设计等等。
首先,要确定所需的制动力大小。
制动力是指制动器施加在运动物体上的力,它的大小决定了物体的减速度和停止的时间。
根据实际需求和应用场景,可以通过以下公式计算制动力:制动力=质量×减速度其中,质量是指运动物体的质量,减速度是要达到的减速度。
根据这个制动力,可以选择适当的制动器结构和材料。
其次,要确定制动距离的要求。
制动距离是指从开始制动到停止的距离,它的大小决定了制动器制动的效果和占用的空间。
制动距离可以通过以下公式计算:制动距离=初始速度²/(2×减速度)其中,初始速度是运动物体开始制动时的速度,减速度是物体的减速度。
根据这个制动距离,可以调整制动器结构和制动参数的设计。
然后,要选择适当的制动器材料。
制动器材料需要具备一定的强度、硬度和耐磨性,以保证制动效果和使用寿命。
常见的制动器材料包括金属、陶瓷和复合材料等。
选择合适的材料还需要考虑制动温度的影响,因为制动过程中会产生大量的热量,可能导致制动器材料的热膨胀、软化或者燃烧。
最后,要进行制动器的结构设计。
制动器的结构设计包括选择合适的制动器类型(如摩擦制动器、液力制动器和电磁制动器等),确定制动器的安装位置和方式,设计制动器的摩擦面积和接触面形状等。
结构设计需要考虑制动器的尺寸、重量和安装方便性,以保证制动器能够稳定可靠地工作。
在制动器设计的过程中,还需要考虑一些其他的因素,如制动器的可靠性、维修性以及制动器和运动物体之间的适配性。
制动器的设计是一个综合考虑各种因素的过程,需要进行合理的计算和模拟分析,并结合实际的试验验证。
货车前后轮制动器设计

货车的前后轮制动器设计是为了确保货车能够安全、高效地制动,以下是一种常见的设计方案:
1. 前轮制动器:
-使用液压制动系统,通过踏板传递力量给主制动缸。
-主制动缸将压力传递给前轮制动器。
-前轮制动器通常采用盘式制动器,其中包括刹车片、刹车盘和刹车卡钳等部件。
-刹车盘固定在车轮上,当刹车踏板踩下时,刹车卡钳夹紧刹车盘,使刹车片与刹车盘摩擦产生制动力。
2. 后轮制动器:
-后轮制动器通常采用鼓式制动器,其中包括制动鼓、制动鞋和制动缸等部件。
-制动鼓固定在车轮上,当刹车踏板踩下时,制动缸通过连杆或其他机构将力量传递给制动鞋。
-制动鞋与制动鼓接触,产生摩擦力来制动车轮旋转。
此外,货车的制动系统还包括制动液、制动管路和制动助力装置等。
制动液通过制动管路将踏板的压力传递给前后轮制动器,而制动助力装置(如真空助力器或液压助力器)可以增加制动系统的效能。
需要注意的是,以上只是一种常见的设计方案,具体的货车前后轮制动器设计应根据车辆类型、负载重量、行驶条件等因素进行调整和优化。
建议在设计过程中遵循相关的法规和标准,并咨询专业的汽车工程师进行指导。
制动器设计及计算实例汇总
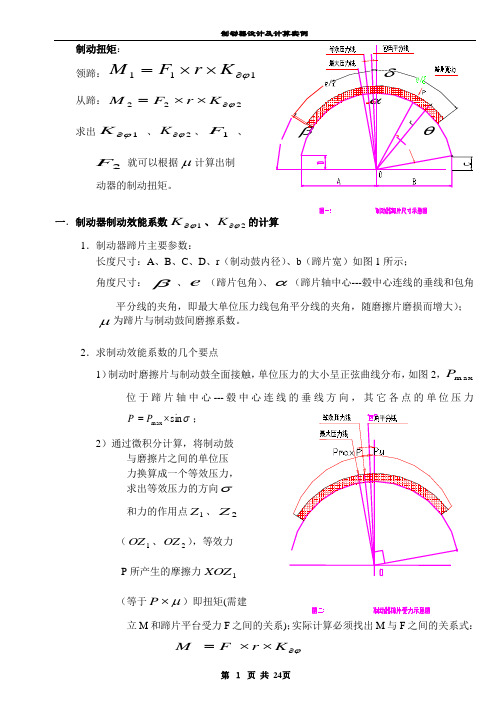
等效压力:
或
方向通过 ,
以上是固定销式求合力的方法(含合力的角度 )
摩擦力矩:
,c为常数;(另外,摩擦力矩T还可以用积分方法求: = )
=
力矩:
由制动器的几何尺寸( 、 )确定。
总等效压力:
由P与输入力F的关系可作图求出(力平衡)
故可得出:
式中BEF为制动器效率因数。
车型
制动鼓
直径
(前桥)
(前桥)
为蹄片与制动鼓间磨擦系数。
2.求制动效能系数的几个要点
1)制动时磨擦片与制动鼓全面接触,单位压力的大小呈正弦曲线分布,如图2, 位于蹄片轴中心---毂中心连线的垂线方向,其它各点的单位压力 ;
2)通过微积分计算,将制动鼓
与磨擦片之间的单位压
力换算成一个等效压力,
求出等效压力的方向
和力的作用点 、
( 、 ),等效力
0.576
0.621
0.574
0.571
0.58
0.568
0.416
0.35
0.292
0.263
0.285
0.286
0.295
摩擦片上最大单位压力位于 角处:
摩擦片上单位压力的分配:
位于与x-x成 角处。
单位压力在x、y方向上分解:
P分解为:
对整个蹄片x-x方向上合力为:
同样y-y方向上合力为:
合力角度
P所产生的摩擦力
(等于 )即扭矩(需建
立M和蹄片平台受力F之间的关系);实际计算必须找出M与F之间的关系式:
3)制动扭矩计算
蹄片受力如图3:
a.三力平衡
领蹄:
从蹄:
b.通过对蹄片受力平衡分析(对L点取力矩)
制动器设计及计算实例
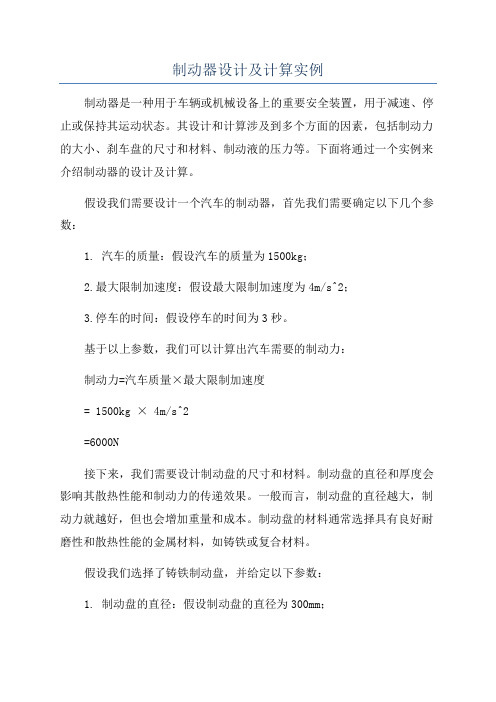
制动器设计及计算实例制动器是一种用于车辆或机械设备上的重要安全装置,用于减速、停止或保持其运动状态。
其设计和计算涉及到多个方面的因素,包括制动力的大小、刹车盘的尺寸和材料、制动液的压力等。
下面将通过一个实例来介绍制动器的设计及计算。
假设我们需要设计一个汽车的制动器,首先我们需要确定以下几个参数:1. 汽车的质量:假设汽车的质量为1500kg;2.最大限制加速度:假设最大限制加速度为4m/s^2;3.停车的时间:假设停车的时间为3秒。
基于以上参数,我们可以计算出汽车需要的制动力:制动力=汽车质量×最大限制加速度= 1500kg × 4m/s^2=6000N接下来,我们需要设计制动盘的尺寸和材料。
制动盘的直径和厚度会影响其散热性能和制动力的传递效果。
一般而言,制动盘的直径越大,制动力就越好,但也会增加重量和成本。
制动盘的材料通常选择具有良好耐磨性和散热性能的金属材料,如铸铁或复合材料。
假设我们选择了铸铁制动盘,并给定以下参数:1. 制动盘的直径:假设制动盘的直径为300mm;2. 制动盘的厚度:假设制动盘的厚度为40mm;根据制动盘的直径和厚度,我们可以计算制动盘的转动惯量:转动惯量=(1/2)×制动盘的质量×(制动盘的直径/2)^2=(1/2)×制动盘的质量×(0.15m)^2根据实际情况,制动盘的质量需要根据制动盘的材料、直径和厚度来选择。
为了方便计算,假设制动盘的质量为20kg。
转动惯量= (1/2) × 20kg × (0.15m)^2= 0.45kg·m^2接下来,我们需要选择适当的制动液和计算所需的制动液压力。
制动液在制动器中起到传递力和控制制动器放松的作用。
制动液需要具有良好的抗压性、稳定性和耐高温性能。
假设我们选择了常用的DOT4制动液,并给定以下参数:1.制动液的抗压性比:假设制动液的抗压性比为10:1;2.需要的制动力:假设需要的制动力为6000N。
盘式制动器_毕业设计说明书参考

盘式制动器_毕业设计说明书参考(以下是机械设计专业的毕业设计说明书范例,供参考)毕业设计题目:盘式制动器设计一、题目来源及背景盘式制动器是用于汽车、摩托车等机动车辆的制动装置之一,具有制动力矩大、耐磨损、散热快等优点。
本毕业设计项目充分利用机械设计、材料学等方面知识,对盘式制动器的制动器件进行设计。
二、设计要求1. 主要技术指标:(1)制动力矩:大于100 N·m(2)使用寿命:大于2×10⁴次(3)材料:盘式制动器盘采用GCr15;制动蹄采用40Cr;制动片采用半金属材料。
2. 设计思路(1)整体结构设计:盘式制动器的整体结构以制动盘、制动蹄、制动片、制动器液压缸等组成。
其中,制动盘为主动件,制动蹄和制动片为被动件,液压缸提供制动力。
(2)制动盘设计:制动盘是盘式制动器的核心部件,由于需要承受制动力矩,因此采用GCr15高强度材料。
制动盘的直径和厚度由制动力矩、车辆重量等因素决定。
(3)制动片设计:制动片采用半金属材料,能够在制动过程中承受高温、高压。
制动片的表面采用刻花纹路,以增加摩擦面积和摩擦系数。
(4)制动蹄设计:制动蹄采用40Cr合金钢,具有足够的强度和硬度。
制动蹄的设计应考虑制动片与制动盘之间的间隙,以确保能够实现完整制动。
(5)液压缸设计:液压缸的设计应考虑到制动盘的直径和轮轴间隙,能够提供足够的制动力矩。
液压缸的设计也应考虑到防泄漏、稳定等因素。
三、设计过程1. 制动盘设计(1)根据制动力矩、车辆重量等因素确定制动盘的直径和厚度。
(2)采用CAD软件进行3D建模,并进行有限元分析,得出制动盘在制动力矩作用下的应力分布情况和变形情况。
(3)结合分析结果,调整制动盘的厚度和结构。
(4)根据制动盘的设计尺寸和结构参数,进行加工和表面处理,确保制动片和制动盘之间具有充分的接触面积和摩擦力。
2. 制动片设计(1)选择半金属材料作为制动片材料。
根据制动盘的直径和表面处理情况,设计制动片的形状和尺寸。
制动器设计的计算过程
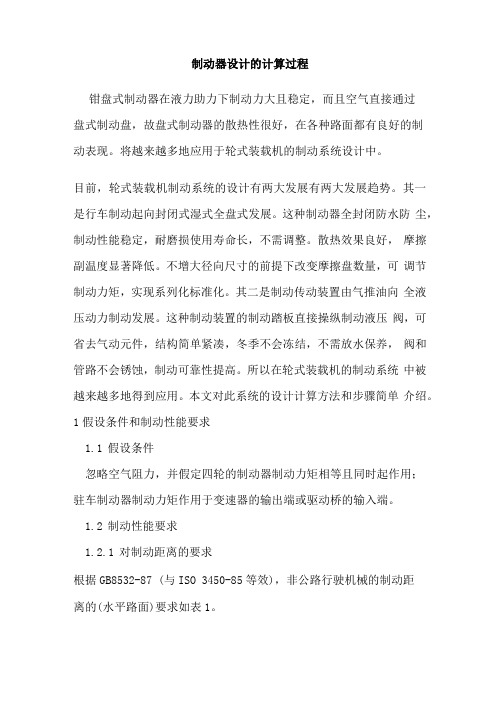
制动器设计的计算过程钳盘式制动器在液力助力下制动力大且稳定,而且空气直接通过盘式制动盘,故盘式制动器的散热性很好,在各种路面都有良好的制动表现。
将越来越多地应用于轮式装载机的制动系统设计中。
目前,轮式装载机制动系统的设计有两大发展有两大发展趋势。
其一是行车制动起向封闭式湿式全盘式发展。
这种制动器全封闭防水防尘,制动性能稳定,耐磨损使用寿命长,不需调整。
散热效果良好,摩擦副温度显著降低。
不增大径向尺寸的前提下改变摩擦盘数量,可调节制动力矩,实现系列化标准化。
其二是制动传动装置由气推油向全液压动力制动发展。
这种制动装置的制动踏板直接操纵制动液压阀,可省去气动元件,结构简单紧凑,冬季不会冻结,不需放水保养,阀和管路不会锈蚀,制动可靠性提高。
所以在轮式装载机的制动系统中被越来越多地得到应用。
本文对此系统的设计计算方法和步骤简单介绍。
1假设条件和制动性能要求1.1假设条件忽略空气阻力,并假定四轮的制动器制动力矩相等且同时起作用;驻车制动器制动力矩作用于变速器的输出端或驱动桥的输入端。
1.2制动性能要求1.2.1对制动距离的要求根据GB8532-87 (与ISO 3450-85等效),非公路行驶机械的制动距离的(水平路面)要求如表1。
表1非公路行驶机械的制动距离最高车速(km/h)最大质量(kg)行车制动系统的制动距离(m)辅助制动系统的制动距离(m)二32/ 0 W32000 V2/68+(V2/124) . (G/32000) V2/39+ (V2/130). (G/32000)三32000 V2/44 V2/30W32 / 0 W32000 V2/68+(V2/124) . (G/32000) +0.1(32-V) V2/39+ (V2/130) . (G/32000) +0.1(32-V)三32000 V2/44+0.1(32-V) V2/30+0.1(32-V)* V——制动初速度(Km/h) G——整机工作质量(kg)1.2.2对行车系统的性能要求除了满足制动距离要求外,还要求行车制动系统能满足装载机空载在25% (14.0)的坡度上停住。
- 1、下载文档前请自行甄别文档内容的完整性,平台不提供额外的编辑、内容补充、找答案等附加服务。
- 2、"仅部分预览"的文档,不可在线预览部分如存在完整性等问题,可反馈申请退款(可完整预览的文档不适用该条件!)。
- 3、如文档侵犯您的权益,请联系客服反馈,我们会尽快为您处理(人工客服工作时间:9:00-18:30)。
燕山大学专业综合训练说明书题目: CD1轻型货车后制动器设计燕山大学专业综合训练任务书院(系):车辆与能源学院基层教学单位:车辆与交通运输工程系题目CD1轻型货车后制动器设计训练内容和目的1. 熟悉制动系统及鼓式制动器结构;2. 计算制动器制动力分配系数;3. 计算制动器主要结构参数;4. 练习使用绘图软件;5. 学习查阅相关标准。
附主要参数:满载质量:1850kg,前轮至质心距离1391mm;装备质量:1160kg,前轮至质心距离1350mm;质心高:空载695mm,满载750mm;轮胎型号:175/70R14完成任务量1. 确定制动器制动力分配系数;2. 绘制制动器总装图;3. 绘制制动鼓零件图;4. 书写6000字计算说明书。
进度安排第一、二周:熟悉制动器结构、计算制动器制动力分配系数;计算相关结构参数并绘制制动器总装图;第三周:完善总装图,绘制制动鼓零件图;第四周:编写说明书,准备答辩。
参考资料1.《汽车设计》.王望予.机械工业出版社2.《汽车设计》.刘唯信.清华大学出版社指导教师签字基层教学单位主任签字2012年11月29日第1章概述1.1制动器功能汽车制动器是指产生阻碍车辆运动或运动趋势的力(制动力)的部件。
汽车所用的制动器几乎都是摩擦式的,可分为鼓式和盘式两大类。
鼓式制动器摩擦副中的旋转元件为制动鼓,其工作表面为圆柱面;盘式制动器的旋转元件则为旋转的制动盘,以端面为工作表面。
1.2制动器要求汽车制动系至少应有两套独立的制动装置,即行车制动装置和驻车制动装置。
行车制动是用脚踩下制动踏板操纵车轮制动器来制动全部车轮;而驻车制动则采用手制动杆操纵,且利用专设的中央制动器或利用车轮制动器进行制动。
中央制动器位于变速器之后的传动系中,用于制动变速器的第二轴或传动轴。
此次设计为小型乘用车,轻型客车满载1.85t,设计的是鼓式制动器。
第2章制动力分配2.1参数满载质量:1850kg,前轮至质心距离1391mm;装备质量:1160kg,前轮至质心距离1350mm;质心高:空载695mm,满载750mm;轮胎型号:175/70R142.2法规要求为了保证制动时汽车的方向稳定性和有足够的制动效率,联合国欧洲经济委员会制定的ECE R13制动法规对双轴汽车前、后轮制动器制动力提出了明确的要求。
本次设计的是轻型乘用车,根据法规整理出它的制动效能与利用附着系数的要求如下。
法规规定:对于φ = 0.2 ~ 0.8之间时,要求其制动强度z ≥ 0.1 + 0.85(φ -0.2)车辆在各种装载状态时,前轴利用附着系数曲线应在后轴利用附着系数曲线之上。
但是对于本车而言,制动强度在0.3~ 0.45之间,后轴利用附着系数曲线不超过直线φ = z + 0.05的条件下,允许后轴利用附着系数曲线在前轴利用附着系数曲线的上方。
图2-1 ECE 法规货车的制动力分配2.3具有固定比值的前、后制动器制动力与同步附着系数不少两轴汽车的前、后制动器制动力之比为一固定值。
前制动器制动力与汽车总制动器制动力之比称为制动器制动力分配系数,并以符号β表示,即 β=21μμF F21μμF F =ββ-1 若用2μF = B( 1μF )表示,则2μF = B( 1μF )为一直线,此直线通过坐标原点,且其斜率为tanθ=ββ-1 这条直线称为实际前、后制动器制动力分配线,简称β线。
β线与I 曲线交点处的附着系数为同步附着系数,所对应的制动减速度称为临界减速度。
同步附着系数说明,前、后制动器制动力为固定比值的汽车,只有在同步附着系数路面上制动时才能使前、后车轮同时抱死。
设汽车在同步附着系数路面上制动,此时前、后轮同时抱死,得ββ-1=gg h a h b 00ϕϕ-+,即 0ϕ=gh bL -β (2-1) 当φ<φ0时,β线位于I 曲线的下方,制动时总是前轮先抱死。
当φ=φ0时,制动时前、后轮将同时抱死当φ>φ0时,β线位于I 曲线的上方,制动时总是后轮先抱死。
国外有的文献推荐满载时的同步附着系数:轿车取φ0≥0.6;货车取φ0≥0.5为宜。
在条件允许的情况下应取大些,这样制动稳定性好。
2.4理想的前、后制动器制动力分配曲线地面法向反作用力为)(1g Z zh b LGF +=)(2g Z zh a L G F -=前后轮同时抱死时ϕμG F F Xb ==,此时)()(21g Z g Z h a LGF h b L GF ϕϕ-=+=.......................(2-9) 前后轮同时抱死时:前、后轮制动器制动力之和等于附着力,并且前、后轮制动器制动力分别等于各自的附着力,即121122u u u z u z F F GF F F F ϕϕϕ+=⎧⎪=⎨⎪=⎩将(2-9)式代入上式,得1212u u u g u g F F G F b h F a h ϕϕϕ+=⎧⎪+⎨=⎪-⎩,消去变量ϕ,得221141(2)2g u u u g g h L G Gb F b F F h G h ⎡⎤=+-+⎢⎥⎢⎥⎣⎦由此式可作出I 曲线图2-4 β线与I 曲线2.5利用附着系数与制动效率利用附着系数就是在某一制动强度z 下,不发生任何车轮抱死所要求的最小路面附着系数φi ,其定义为ZiXbii F F =ϕ。
其中,F Xbi 为对应于制动强度z ,汽车对第i 轴产生的地面制动力;F Zi 为制动强度为z 时,地面对第i 轴的法向反力;φi 为第i 轴对应于制动强度z 的利用附着系数。
显然,利用附着系数越接近制动强度,地面的附着条件发挥得越充分,汽车制动力分配的合理程度越高。
2.5.1前轴的利用附着系数设汽车前轮刚要抱死或前、后轮同时抱死时产生的减速度为dtdu=zg ,则 1μF =1Xb F =βg G dtdu=βGz 而)(1g Z zh b L G F += 故f ϕ=11Z Xb F F =)(1g zh b Lz +β (2-3) 同时,由(2-1)式得 β=Lh b g0ϕ+ (2-2), 又前轮刚抱死时,f ϕ=φ,由(2-2)式得当φ<0ϕ时,z = gh b b )(0ϕϕϕ-+ (2-5)2.5.2后轴的利用附着系数2Xb F =(1-β)g G dtdu=(1-β)Gz ,而2Z F =)(g zh a L G -,故)(1)1(22g Z Xb r zh a LzF F --==βϕ (2-4),又前轮刚抱死时,r ϕ=φ, 由(2-4)式得当φ>0ϕ时,z = gh a a )(0ϕϕϕ-+ (2-6)2.5.3利用附着系数曲线此次设计,首先在φ = 0.2 ~ 0.8的不同路面上,取定不同的β值,由(2-1)式算出空载与满载时的同步附着系数0ϕ作出利用附着系数与制动强度的关系曲线,与制动法规对比,看是否满足法规要求。
通过EXCEL 作图,找到合适的β值为0.71,此时 满载0ϕ=gh b L -β=27000.711301750⨯-=0.821空载0ϕ=gh b L -β=27000.7113500.816695⨯-=利用Excel 作图绘制利用附着系数与制动强度的关系曲线如下图2-2 利用附着系数与制动强度的关系曲线从图中可看出,当β值取为0.71时,前轴的利用附着着系数曲线全在后轴利用附着系数曲线上方,前轴的利用附着系数均在法规0.070.85f z φ+=下符合法规要求,后轴均在0.05r Z φ=+下面,说明后轴的利用附着系数也均符合要求,综合说明β=0.71的制动力分配时合理的。
当客车在地面附着系数为0.2~0.8的路面上制动时不会出现后轮先抱死的情况,符合安全要求,说明制动力分配合理。
2.6制动效率曲线制动效率定义为车轮不锁死的最大制动强度与车轮和地面间附着系数的比值,亦即车轮将要抱死时的制动强度z 与被利用的附着系数之比。
前轴制动效率为//f f f g zb LE h Lϕβϕ==-.................................................(2-7) 后轴制动效率为/(1)/r rr g za LE h Lϕβϕ==-+..............................................(2-8)通过Excel 作图绘制出制动效率曲线如下图2-3 前、后制动效率曲线在上图中可以看到满载和空载时后轴的制动效率均交于空载和满载时的同步附着系数,在0.8后,即在0.2-0.8的路面上行驶时总是前轮先抱死,符合安全要求。
第3章鼓式制动器的结构型式及选择鼓式制动器可分为以下几种:图3-1鼓式制动器简图(a)领从蹄式(用凸轮张开);(b)领从蹄式(用制动轮缸张开);(c)双领蹄式(非双向,平衡式);(d)双向双领蹄式;(e)单向增力式;(f)双向増力式鼓式制动器根据其结构都不同,又分为:双向自增力蹄式制动器、双领蹄式制动器、领从蹄式制动器、双从蹄式制动器。
其制动效能依次降低,最低是盘式制动器。
领丛蹄式制动器的效能和效能稳定性,在各式制动器中居中游:前进、倒退行驶的制动效果不变;结构简单,成本低;便于附装驻车制动驱动机构;调整蹄片与制动鼓之间的间隙工作容易。
但领丛蹄式制动器也有两蹄片上的单位压力不等(在两蹄上摩擦衬片面积相同的条件下),故两蹄片磨损不均匀,寿命不同的特点。
此外,因只有一个轮缸,两蹄必须在同一驱动回路作用下工作。
本次设计的是轻型乘用车后轮鼓式制动器,对制动强度要求不高,并且为了节约成本决定采用领从蹄式鼓式制动器。
第4章制动器结构参数确定4.1制动鼓直径D在输入力OF一定时,制动鼓内径D越大,则制动力矩越大,且散热能力也越强。
但D的增大受轮辋内径限制,制动鼓与轮辋之间应保持足够的间隙,通常要求该间隙不小于20~30mm,否则不仅制动鼓散热条件太差,而且轮辋受热后可能损坏轮胎。
制动鼓应有足够的壁厚,用来保证有较大的刚度和热容量,以减少制动时的温度。
制动鼓的直径小,刚度就大,并有利于保证制动鼓的加工精度。
制动鼓直径与轮辋直径之比/rD D的范围如下:乘用车/rD D=0.64-0.74商用车/rD D=0.70-0.83制动鼓内径尺寸应参考专业标准QC/T309—1999《制动鼓工作直径及制动蹄片宽度尺寸系列》。
轿车制动鼓内径一般比轮辋外径小125mm-150mm,载货汽车和客车的制动鼓内径一般比轮辋外径小80mm-100mm,设计时亦可按轮辋直径初步确定制动鼓内径(见表4-1)。
表4-1 制动鼓最大内径轮辋直径/in 12 13 14 15 16 20制动鼓最大内径/mm轿车180 200 240 260 -- -- 货车、客车220 240 260 300 320 420本次设计轮胎规格70R16 ,其中70为轮胎名义断面宽度,16为轮辋名义直径(in ),1 in=25.4mm轮辋直径16英寸,则轮辋直径r D =14×25.4mm=355.6mm 。