炼钢元素的氧化
炼钢 用氧

炼钢用氧
炼钢过程中使用氧气可以提高生产效率和降低成本。
具体来说,氧气在炼钢中的作用主要有以下几个方面:
1. 氧化剂:在炼钢过程中,需要将生铁中的碳和其他杂质氧化掉,以提高钢的纯度。
氧气作为一种强氧化剂,可以加速这个过程,从而缩短炼钢时间。
2. 燃烧剂:在炼钢过程中,需要将生铁加热到高温,以使其融化。
氧气可以作为燃烧剂,与燃料一起燃烧,产生高温火焰,从而加热生铁。
3. 搅拌剂:在炼钢过程中,需要将生铁和其他原料充分混合,以保证钢的质量。
氧气可以作为搅拌剂,通过鼓吹氧气,使生铁和其他原料充分混合,从而提高钢的质量。
4. 提高产量:使用氧气可以提高炼钢的产量。
通过增加氧气的供应,可以提高炉内的燃烧效率,从而增加产量。
总的来说,氧气在炼钢过程中起着非常重要的作用,可以提高生产效率、降低成本、提高钢的质量和产量。
电弧炉炼钢之碳的氧化讲解和计算案例
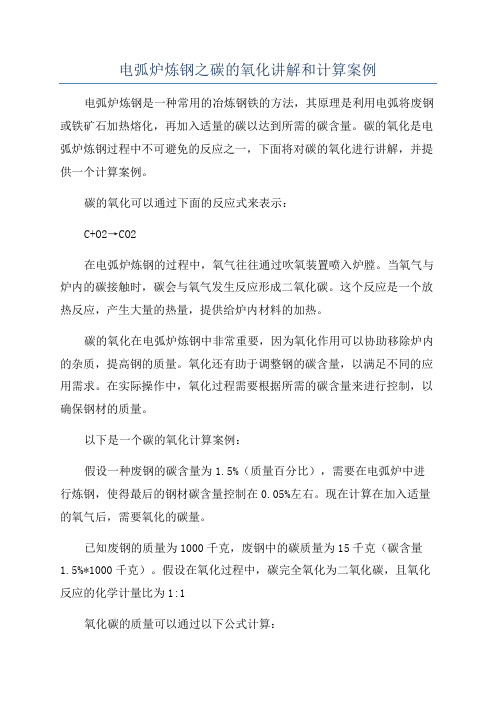
电弧炉炼钢之碳的氧化讲解和计算案例电弧炉炼钢是一种常用的冶炼钢铁的方法,其原理是利用电弧将废钢或铁矿石加热熔化,再加入适量的碳以达到所需的碳含量。
碳的氧化是电弧炉炼钢过程中不可避免的反应之一,下面将对碳的氧化进行讲解,并提供一个计算案例。
碳的氧化可以通过下面的反应式来表示:C+O2→CO2在电弧炉炼钢的过程中,氧气往往通过吹氧装置喷入炉膛。
当氧气与炉内的碳接触时,碳会与氧气发生反应形成二氧化碳。
这个反应是一个放热反应,产生大量的热量,提供给炉内材料的加热。
碳的氧化在电弧炉炼钢中非常重要,因为氧化作用可以协助移除炉内的杂质,提高钢的质量。
氧化还有助于调整钢的碳含量,以满足不同的应用需求。
在实际操作中,氧化过程需要根据所需的碳含量来进行控制,以确保钢材的质量。
以下是一个碳的氧化计算案例:假设一种废钢的碳含量为1.5%(质量百分比),需要在电弧炉中进行炼钢,使得最后的钢材碳含量控制在0.05%左右。
现在计算在加入适量的氧气后,需要氧化的碳量。
已知废钢的质量为1000千克,废钢中的碳质量为15千克(碳含量1.5%*1000千克)。
假设在氧化过程中,碳完全氧化为二氧化碳,且氧化反应的化学计量比为1:1氧化碳的质量可以通过以下公式计算:氧化碳的质量=废钢的质量*碳含量*氧化反应的化学计量比在这个案例中,氧化碳的质量=1000千克*1.5%*1=15千克因此,在达到所需的碳含量0.05%的情况下,需要将15千克的碳完全氧化。
需要注意的是,在实际操作中,碳的氧化往往是一个动态的过程,需要根据不同的钢种和碳含量的要求来进行控制。
同时,电弧炉炼钢的过程中还存在其他的反应和影响,如还原反应和氧吹效率等,这些因素也需要综合考虑,确保炼钢过程的稳定与高效。
炼钢脱碳反应
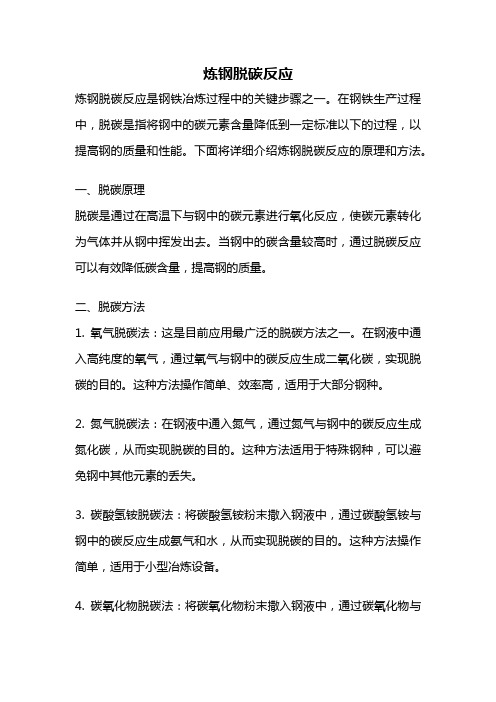
炼钢脱碳反应炼钢脱碳反应是钢铁冶炼过程中的关键步骤之一。
在钢铁生产过程中,脱碳是指将钢中的碳元素含量降低到一定标准以下的过程,以提高钢的质量和性能。
下面将详细介绍炼钢脱碳反应的原理和方法。
一、脱碳原理脱碳是通过在高温下与钢中的碳元素进行氧化反应,使碳元素转化为气体并从钢中挥发出去。
当钢中的碳含量较高时,通过脱碳反应可以有效降低碳含量,提高钢的质量。
二、脱碳方法1. 氧气脱碳法:这是目前应用最广泛的脱碳方法之一。
在钢液中通入高纯度的氧气,通过氧气与钢中的碳反应生成二氧化碳,实现脱碳的目的。
这种方法操作简单、效率高,适用于大部分钢种。
2. 氮气脱碳法:在钢液中通入氮气,通过氮气与钢中的碳反应生成氮化碳,从而实现脱碳的目的。
这种方法适用于特殊钢种,可以避免钢中其他元素的丢失。
3. 碳酸氢铵脱碳法:将碳酸氢铵粉末撒入钢液中,通过碳酸氢铵与钢中的碳反应生成氨气和水,从而实现脱碳的目的。
这种方法操作简单,适用于小型冶炼设备。
4. 碳氧化物脱碳法:将碳氧化物粉末撒入钢液中,通过碳氧化物与钢中的碳反应生成二氧化碳,从而实现脱碳的目的。
这种方法操作简单,但适用范围较窄。
三、脱碳反应的影响因素1. 温度:脱碳反应通常在高温下进行,温度的升高可以加快反应速率,提高脱碳效果。
2. 反应时间:反应时间的延长可以增加脱碳反应的充分程度,提高脱碳效果。
3. 气氛:脱碳反应需要在氧化性或还原性气氛中进行,不同的钢种需要选择适合的气氛。
4. 搅拌方式:搅拌可以使钢液更加均匀,有利于脱碳反应的进行。
四、脱碳反应的应用脱碳反应广泛应用于钢铁冶炼过程中。
通过控制脱碳反应的条件和方法,可以使钢的碳含量达到要求,从而提高钢的质量和性能。
脱碳反应还可以调整钢的成分,使其达到特定的用途要求。
炼钢脱碳反应是钢铁冶炼过程中至关重要的步骤。
通过选择合适的脱碳方法和条件,可以有效降低钢中的碳含量,提高钢的质量和性能。
在钢铁生产中,脱碳反应是不可或缺的环节,对于保证钢的质量和性能具有重要意义。
5、炼钢基本反应资料
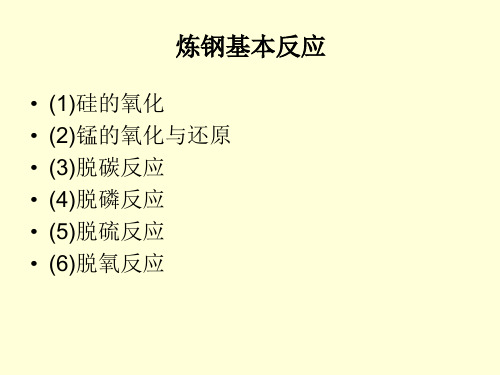
2[P]+5(FeO)=(P2O5)+5[Fe](界面反应) △G°=-209327+40.3
T J/mol
3(FeO)+(P2O5)=(3FeO.P2O5) (熔渣反应)
(3FeO.P2O5)+n(CaO)=(nCaO.P2O5)+3(FeO) (熔渣反应)
[C]+[O]={CO}(熔池粗糙表面反应) △G°=-22364-39.63T J/mol
[C]+1/2{O2}={CO}(氧射流冲击区,直接氧化反应) △G°=136900-43.51T J/mol
(3)脱碳反应
铁水中溶解的碳和氧反应式:
[C]+[O]={CO}
△G°=-22364-39.63T J/mol
[P]/(P)的传质;
(4)脱磷反应
w( P) %
dw[ P]%
LP
A
.
dt
Vm 1 / k m 1 /( K .k s )
w[ P]%
研究表面:
• 氧的传质不是限制环节;
• 界面两侧[P]/(P)的传质为限制性环节。
有利于脱磷反应的动力学条件:
• 增大LP-提高炉渣碱度,增加FetO含量,减低温度等;
J/mol
(SiO2)+(MnO)=MnO.SiO2 (熔渣反应:吹炼初期)
2(CaO)+(MnO.SiO2)=(2CaO.SiO2)+(MnO) (熔渣反应:吹炼中期)
[C]+(MnO)={CO}+[Mn] (熔渣反应:吹炼后期)
(2)锰的氧化与还原
用下式代表Mn在渣-金属间的反应 :
炼钢需要氧气的原因

炼钢需要氧气的原因
炼钢需要氧气的原因是因为氧气具有以下几个重要的作用:
1. 氧化反应:炼钢过程中需要将污染物和杂质从金属中去除,氧气能与这些杂质发生氧化反应,将其转化为氧化物,并在炉渣中排出。
通过氧化反应,可以降低钢中的含硫、含氮等杂质含量,提高钢的纯净度。
2. 改善燃烧条件:在冶炼过程中,燃料通常是煤炭或天然气等有机化合物,它们需要与氧气发生反应才能得到高温,从而提供熔融金属所需的热能。
通过控制氧气的供给量,可以调节燃烧的强度和燃烧产物的组成,从而控制冶炼过程的温度和气氛。
3. 混合气氛控制:氧气可以与其它气体混合,形成特定的气氛,例如氧气与氮气混合可以形成氮气互换气氛,有利于炉内的热交换和保护金属表面;氧气与水蒸气混合可以形成水蒸气互换气氛,有利于炉内的脱氧反应等。
综上所述,氧气在炼钢过程中起到了氧化反应、改善燃烧条件和控制混合气氛的作用,是炼钢过程中不可或缺的重要因素。
炼钢过程钢中氧的控制
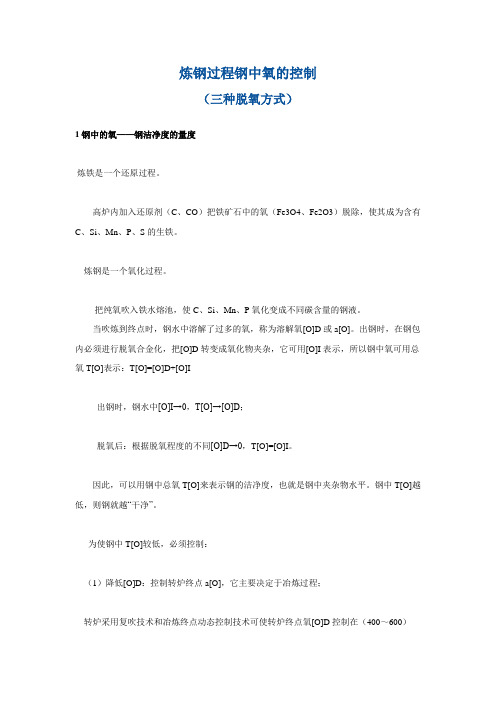
炼钢过程钢中氧的控制(三种脱氧方式)1 钢中的氧——钢洁净度的量度炼铁是一个还原过程。
高炉内加入还原剂(C、CO)把铁矿石中的氧(Fe3O4、Fe2O3)脱除,使其成为含有C、Si、Mn、P、S的生铁。
炼钢是一个氧化过程。
把纯氧吹入铁水熔池,使C、Si、Mn、P氧化变成不同碳含量的钢液。
当吹炼到终点时,钢水中溶解了过多的氧,称为溶解氧[O]D或a[O]。
出钢时,在钢包内必须进行脱氧合金化,把[O]D转变成氧化物夹杂,它可用[O]I表示,所以钢中氧可用总氧T[O]表示:T[O]=[O]D+[O]I出钢时,钢水中[O]I→0,T[O]→[O]D;脱氧后:根据脱氧程度的不同[O]D→0,T[O]=[O]I。
因此,可以用钢中总氧T[O]来表示钢的洁净度,也就是钢中夹杂物水平。
钢中T[O]越低,则钢就越“干净”。
为使钢中T[O]较低,必须控制:(1)降低[O]D:控制转炉终点a[O],它主要决定于冶炼过程;转炉采用复吹技术和冶炼终点动态控制技术可使转炉终点氧[O]D控制在(400~600)×10-6范围。
(2)降低夹杂物的[O]I:控制脱氧、夹杂物形成及夹杂物上浮去除——夹杂物工程概念(Inclusion Engineering)。
随着炉外精炼技术的发展,钢中的总氧含量不断减低,夹杂物越来越少,钢水越来越“干净”,甚至追求“零夹杂物”,钢材性能不断改善。
1970~2000年钢中T[O]演变,由于引入炉外精炼,对于硅镇静钢,T[O]可达(15~20)×10-6,对于铝镇静钢,T[O]可达到<10×10-6。
(3)连铸过程:一是防止经炉外精炼的“干净”的钢水不再污染,二是要进一步净化钢液,使连铸坯中的T[O]达到更低的水平。
钢中T[O]量与产品质量关系举例如下:(1)轴承钢T[O]由30×10-6降到5×10-6,疲劳寿命提高100倍。
(2)钢中T[O]与冷轧板表面质量存在明显的对应关系。
炼钢的氧化亚铁

在炼钢过程中,氧化亚铁(FeO)是一种重要的中间产物,它在高炉中铁矿石还原过程中形成,以及在转炉中过量的生铁与氧气反应生成。
氧化亚铁的存在对钢材质量有不利影响,因为它会导致钢中氧含量升高,从而增加夹杂物和缺陷,影响钢材的机械性能和耐腐蚀性。
为了去除炼钢过程中的氧化亚铁,通常采用以下方法:
1. 脱氧剂的使用:在钢液中加入脱氧剂,如硅铁、锰铁、铝或钙等。
这些脱氧剂与氧化亚铁反应,生成不溶于钢液的氧化物,并以渣的形式从钢液中分离出去。
2. 底吹和顶吹:在转炉炼钢过程中,可以通过底吹或顶吹氧气来氧化氧化亚铁及其他杂质元素,生成的氧化物随炉渣排出。
3. 真空脱气:在二次精炼阶段,通过降低炉内压力来去除溶解在钢液中的气体,包括由氧化亚铁分解产生的气体。
4. 渣洗:利用炉渣对钢液进行洗涤,通过渣与钢液的物理接触,将夹杂物从钢液中分离出去。
5. 电渣重熔:在某些特殊的钢材生产过程中,可以使用电渣重熔法进一步提纯钢液,去除氧化亚铁及其他不希望的元素。
通过以上方法,可以有效减少钢中的氧含量,改善钢材的整体质量。
氧化亚铁的去除是钢铁冶炼中不可缺少的一环,对于生产出高质量的钢材至关重要。
炼钢的反应原理化学方程式
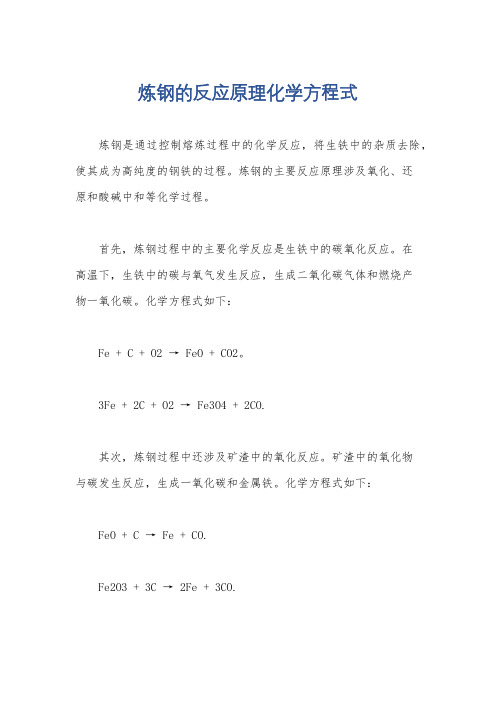
炼钢的反应原理化学方程式
炼钢是通过控制熔炼过程中的化学反应,将生铁中的杂质去除,使其成为高纯度的钢铁的过程。
炼钢的主要反应原理涉及氧化、还
原和酸碱中和等化学过程。
首先,炼钢过程中的主要化学反应是生铁中的碳氧化反应。
在
高温下,生铁中的碳与氧气发生反应,生成二氧化碳气体和燃烧产
物一氧化碳。
化学方程式如下:
Fe + C + O2 → FeO + CO2。
3Fe + 2C + O2 → Fe3O4 + 2CO.
其次,炼钢过程中还涉及矿渣中的氧化反应。
矿渣中的氧化物
与碳发生反应,生成一氧化碳和金属铁。
化学方程式如下:FeO + C → Fe + CO.
Fe2O3 + 3C → 2Fe + 3CO.
此外,炼钢过程中还包括金属氧化物的还原反应。
金属氧化物在高温下与还原剂(如碳)反应,生成金属和氧化物。
化学方程式如下:
Fe2O3 + 3CO → 2Fe + 3CO2。
最后,炼钢过程中的酸碱中和反应也是至关重要的。
通过向炉中加入石灰石等碱性物质,可以中和矿石中的酸性物质,从而有助于去除硫等杂质。
这些反应不仅有助于去除杂质,还有助于调节炉内的化学平衡。
总的来说,炼钢的反应原理涉及氧化、还原和酸碱中和等多种化学反应,通过这些反应可以有效地去除生铁中的杂质,得到高质量的钢铁产品。
- 1、下载文档前请自行甄别文档内容的完整性,平台不提供额外的编辑、内容补充、找答案等附加服务。
- 2、"仅部分预览"的文档,不可在线预览部分如存在完整性等问题,可反馈申请退款(可完整预览的文档不适用该条件!)。
- 3、如文档侵犯您的权益,请联系客服反馈,我们会尽快为您处理(人工客服工作时间:9:00-18:30)。
【本章学习要点】本章学习炼钢炉渣的来源、组成和作用,钢中元素氧化的规律及铁、硅、锰的氧化情况,硫对钢性能的影响,炉渣脱硫的基本反应和条件,氧在钢中的危害及脱氧的任务,元素的脱氧能力及各种脱氧方法的的特点,钢中气体、夹杂物对钢性能的影响,减少钢中气体和减少钢中夹杂物的途径。
第一节炼钢炉渣一、炉渣的来源、组成和作用1.炉渣的来源炉渣又叫熔渣,是炼钢过程中产生的。
炉渣的主要来源有:1)由造渣材料或炉料带入的物质。
如加入石灰、白云石、萤石等,金属材料中的泥沙或铁锈,也将使炉渣中含有(FeO)、(SiO2)等。
这是炉渣的主要来源。
2)元素的氧化产物。
含铁原料中的部分元素如Si、Mn、P、Fe等氧化后生成的氧化物,如Si02、Mn0、Fe0、P205等。
3)炉衬的侵蚀和剥落材料。
由于高温、化学侵蚀、机械冲刷等方面原因使炉衬剥落,则耐火材料进入渣中。
4)合金元素脱氧产物及炉渣脱硫产物。
如用Al脱氧化生成的(Al2O3),用Si脱氧生成的(SiO2),以及脱硫产物(CaS)等。
2.炉渣的组成化学分析表明,炼钢炉渣的主要成分是:Ca0、Si02、Fe203、Fe0、Mg0、P205、Mn0、CaS等,这些物质在炉渣中能以多种形式存在,除了上面所说的简单分子化合物以外,还能形成复杂的复合化合物,如2Fe0·Si02、2Ca0·Si02、4Ca0·P205等。
3.炉渣的作用炼钢过程中熔渣的主要作用可归纳成如下几点:1)通过调整炉渣的成分、性质和数量,来控制钢液中各元素的氧化还原反应过程,如脱碳、脱磷、脱氧、脱硫等;2)吸收金属液中的非金属夹杂物;3)覆盖在钢液上面,可减少热损失,防止钢液吸收气体;4)能吸收铁的蒸发物,能吸收转炉氧流下的反射铁粒,可稳定电弧炉的电弧;5)冲刷和侵蚀炉衬,好的炉渣能减轻这种不良影响,延长炉衬寿命。
由此可以看出:造好渣是实现炼钢生产优质、高产、低消耗的重要保证。
因此实际生产中常讲:炼钢就是炼渣。
二、炉渣的化学性质和物理性质熔渣的化学性质主要是指熔渣的碱度、氧化性和还原性。
熔渣的物理性质主要是指炉渣的熔点和黏度。
为了准确描述反应物和产物所处的环境,规定用“[]”表示其中的物质在金属液中,“()”表示在渣液中,“{}”表示在气相中。
1.炉渣的化学性质(1)熔渣的碱度炉渣中常见的氧化物有酸、碱性之分,其分类如下:碱度是指炉渣中碱性氧化物与酸性氧化物浓度的比值,用“R”来表示。
碱度是判断熔渣碱性强弱的指标。
去磷、去硫以及防止金属液吸收气体等都和熔渣的碱度有关,因此碱度是影响渣、钢反应的重要因素。
由于熔渣中Ca0和Si02的数量最多,约为渣量的60%以上,所以在熔渣含磷不高时,常以Ca0与Si02浓度之比表示熔渣的碱度,即:R若炉渣中含磷量较高,也可以表示为:R根据碱度高低,熔渣可分为三类:1)R<1酸性渣2)R=1中性渣R<1.5低碱度渣3)R>1碱性渣R=1.8~2.2中碱度渣R>2.5高碱度渣(2)熔渣的氧化性炉渣的氧化性是指熔渣所具备的氧化能力的大小。
它对炼钢过程中的成渣速度、去磷、去硫、喷溅、金属收得率和终点钢水含氧量等均有重大影响。
根据炉渣的分子理论,Fe0能同时存在于渣—钢之中,并在渣—钢之间建立一种平衡(FeO)/[FeO],所以一般认为渣中的氧是通过Fe0传递到钢液中的。
因而熔渣中的FeO含量便可代表熔渣所具备的氧化能力的大小,即熔渣的氧化性通常用渣中氧化亚铁总量乏(Fe0)表示。
渣中氧化铁含量即渣的氧化性,它对熔渣的反应能力及物理性能有重要的影响。
转炉熔渣Fe0过低,造渣困难,炉渣的反应能力低。
熔渣Fe0过高,又会造成喷溅,增加金属损失及炉衬侵蚀。
因此,渣中氧化铁的含量应适当,在转炉冶炼过程中,一般控制在10%~20%为好。
(3)熔渣的还原性熔渣的还原性和氧化性是炉渣的同一种化学性质的两种不同说法。
在碱性电弧炉还原期操作中,要求炉渣具有高碱度、低氧化性、流动性好的特点,以达到钢液脱氧、去硫和减少合金元素烧损的目的。
所以应降低渣中的Fe0,提高渣的还原性。
电弧炉还原期出钢时,一般要求渣中的Fe0质量分数应小于0.5%,以满足出钢时对渣还原性的要求。
2.熔渣的物理性质(1)熔渣的黏度黏度是表示熔渣内部各部分质点间移动时的内摩擦力的大小。
黏度的单位是泊(P),1P=0.1Pa·S(帕·秒)。
黏度与流动性正好相反,黏度低则流动性好。
冶炼时,若熔渣的黏度过大,则物质在钢液及熔渣之间的传递缓慢,不利于炼钢反应的迅速进行;但若黏度过小,又会加剧炉衬的侵蚀。
所以在炼钢时,希望获得适当黏度的炉渣。
影响熔渣黏度的主要因素是熔渣成分和温度。
凡是能降低炉渣熔点的成分均可以改善熔渣的流动性,降低渣的黏度;熔池温度越高,渣的黏度越小,流动性越好。
实际操作中,黏度的调节主要是靠控制渣中的Fe0、碱度和加入萤石等来实现的。
(2)熔渣的熔点熔渣是多元组成物,成分复杂,当它由固相转变成液相时,是逐渐进行的,不存在明显的熔点,其熔化过程有一个温度范围。
通常熔渣的熔点是指炉渣完全转变成均匀液体状态时的温度。
不同的氧化物和复合氧化物的熔点是不同的,炉渣中各种氧化物的熔点见表8—1。
表8—1炉渣中各种氧化物的熔点炉渣中最常见的氧化物大部分都有很高的熔点。
炼钢温度下,这些氧化物很难熔化。
但实际上,它们相互作用生成了各种复杂化合物,这些化合物的熔点低于原氧化物的熔点,从而降低了熔渣的熔点。
降低炉渣熔点的主要措施是:加入一定的助熔剂,如矿石(Fe203)、萤石(CaF2)等,以便形成低熔点的多元系化合物。
第二节铁、硅、锰的氧化在炼钢过程中,氧供入金属熔池后,元素随即开始氧化。
无论是氧气顶吹转炉或是其它炼钢方法,元素的氧化速度可以不同,但都是按一定的次序进行的。
一般地讲,硅、锰最先被大量氧化,而碳随后被迅速氧化,磷的氧化基本上可与碳同时进行。
元素氧化具有不同次序的原因,是由于各元素与氧的亲和力不同,与氧亲和力强的元素可以夺取更多的氧,首先开始大量氧化;反之,与氧亲和力弱的元素则夺得较小的氧,它的氧化就慢些。
1、当温度T<1400℃时,元素的氧化顺序是:Si Mn C P Fe2、当1400℃<T<1530℃时元素的氧化顺序是:Si C Mn P Fe3、当T>1530℃时,元素的氧化顺序是:C Si Mn P Fe铁和氧的亲和力小于Si、Mn、P与氧的亲和力,但由于金属液中铁的浓度最大,质量分数为90%以上,所以铁最先被氧化,生成大量的Fe0,并通过Fe0使其与氧亲和力大的Si、Mn、P 等被迅速氧化。
在转炉中,Si、Mn、P、Fe在冶炼初期的大量氧化,使熔池温度迅速上升,为碳的迅速氧化提供了有利条件;同时也对炉渣的碱度和流动性等产生了较大的影响。
一、铁的氧化铁的氧化反应是一个极其重要的氧化反应,它是其他元素进行氧化反应的基础。
向金属液供氧的方式有两种:一是直接供氧,即吹入氧气;二是间接供氧,且加入矿石。
因此铁的氧化方式也有两种:直接氧化和间接氧化。
直接氧化是指钢液中的元素直接和氧分子进行接触,而被氧化的反应,如:间接氧化反应是指金属液中的元素直接和氧原子或Fe0接触而被氧化的反应,如:[Fe]+[O]=[FeO](放热)铁被氧化后,其反应产物Fe0一部分进入炉渣,一部分继续存留在金属液中,并在金属液—熔渣之间建立动态平衡,它应服从分配定律,即在一定温度下,为一常数,称为氧在炉渣和金属液中的分配系数。
二、硅的氧化1.硅的氧化反应式在碱性炼钢法中,Si的氧化对成渣过程、炉衬的侵蚀等都有重要的影响。
理论上Si的氧化反应也有直接氧化和间接氧化之分,但实际上,金属液中的Si、Mn 元素很难直接与气态氧反应,所以金属液中Si、Mn、P元素的氧化均以间接氧化反应为主。
硅的间接氧化反应式如下:Si的氧化产物只溶于渣,不溶于钢液。
2.Si氧化反应的主要特点Si氧化反应的主要特点如下:1)由于Si与氧的亲和力很强,所以在冶炼初期,金属液中的Si便已基本氧化完毕。
例如:转炉吹氧3min后,Si基本上全被氧化。
同时,由于Si的氧化产物Si02,在炉渣中完全被碱性氧化物如Ca0等结合,无法被还原出来,因此硅的氧化是十分完全彻底的,最后只有微量的硅残留在钢液中。
2)Si氧化反应是一个强烈的放热反应,低温有利于Si氧化反应的迅速进行。
Si是转炉吹炼过程中重要的发热元素。
目前在转炉生产中,为了减少渣量,降低热损失,并提高金属收得率,已在广泛推广使用低Si铁水(叫[Si]<0.3%),由降低铁水[Si]所失去的部分化学热,正在靠其他方法来解决,如提高铁水温度等。
三、锰的氧化1.Mn的间接氧化反应式[Mn]+(FeO)=(MnO)+(Fe)放热[Mn]+[FeO]=(MnO)+[Fe]放热Mn的氧化产物只溶于渣,不溶于钢液。
2.Mn氧化的特点Mn氧化有以下特点:1)Mn的氧化反应是放热反应,低温有利于Mn的氧化,故Mn的氧化主要在冶炼前期进行。
2)由于氧化产物Mn0是碱性氧化物,故碱性渣中不利于Mn的氧化。
因此Mn不可能向Si 那样完全被氧化。
3)当熔池温度升高后,Mn的氧化反应会逆向进行,发生Mn的还原,即产生“回锰”现象,使钢液中的“余锰”增加。
第二节碳的氧化碳的氧化反应是贯穿整个炼钢过程的一个最重要的反应,它是完成诸多炼钢任务的一个重要手段。
一、碳的氧化反应1.氧气流股与金属液间的C—O反应该反应放出大量的热,是转炉炼钢的重要热源。
在转炉炼钢的氧流冲击区及电炉、平炉炼钢采用氧管插入钢液吹氧脱碳时,氧气流股直接作用于钢液,均会发生此类反应。
脱碳示意图分别如图8—1和图8—2所示。
流股中的气体氧{02}与钢液中的碳原子[C]直接接触,反应生成气体产物一氧化碳{CO},脱碳速度受供氧强度的直接影响,供氧强度越大,脱碳速度越快。
图8—1熔池吹氧示意图(吹氧脱碳操作)图8—2氧气顶吹转炉氧射流与熔池相互作用示意图2.金属熔池内部的C—O反应[C]+[FeO]={CO}+[Fe]+7600J该反应为弱放热反应,温度降低有利于反应的进行。
在转炉和电炉炼钢吹氧脱碳时,气体氧{02}会使金属熔池内铁原子[Fe]大量氧化成[FeO],金属液中的[C]与[FeO]接触反应,从而起到间接脱碳的作用。
3.金属液与渣液界面的C—O反应在转炉泡沫渣和采用矿石脱碳的电炉渣内均含有大量的(Fe0),渣中的(FeO)通过渣—钢接触界面向钢液中扩散,然后与钢液中的碳原子反应生成一氧化碳气体。
反应式如下:[C]+(FeO)={CO}+[Fe]-75100J所谓泡沫渣是转炉炼钢吹氧脱碳时钢液—熔渣—炉气三相物质混合乳化而形成的乳浊液。
在泡沫渣中,钢液被粉碎成很细小的小液滴,使钢—渣的接触界面积大大增加,这是泡沫渣中脱碳速度很快的原因。