滴丸制剂工艺
实验室滴丸剂制备

实验室滴丸剂制备实验室滴丸剂制备是一种常见的药物制备方法,具有许多优点,例如易于控制剂量、稳定性高、方便使用等。
在实验室中,制备滴丸剂需要遵循一定的步骤和注意事项。
一、准备工作在开始制备滴丸剂之前,需要准备好所需的设备和材料,包括:滴丸机、模具、温度计、水浴锅、药物原料、基质、脱模剂等。
确保所有设备已经清洗干净并干燥。
二、选择基质和药物基质是滴丸剂的主要成分之一,它能够与药物混合形成溶液或悬浮液。
在选择基质时,需要考虑其与药物的相容性、稳定性、溶解性和成型性。
常用的基质包括明胶、阿拉伯胶、蜡等。
药物的选择需要根据具体的需求和实验目的来确定。
三、制备滴丸溶液或悬浮液将药物与基质混合,制备成溶液或悬浮液。
在制备过程中,需要注意药物的浓度、混合均匀度以及基质的用量。
可以使用搅拌器或混合器来促进混合。
四、滴丸成型将制备好的滴丸溶液或悬浮液倒入滴丸机中,通过控制温度和滴速,使溶液或悬浮液从喷头滴出,落在冷却液中凝固成滴丸。
在成型过程中,需要注意控制滴速和温度,以确保滴丸的大小和形状一致。
五、脱模和干燥当滴丸在冷却液中凝固后,将其从冷却液中取出,放入脱模剂中浸泡一段时间,以便于将滴丸从模具上脱下。
脱模后,将滴丸放在干燥器中进行干燥,以除去残余的水分和溶剂。
六、质量检测和包装在制备过程中,需要对滴丸进行质量检测,以确保其符合规定的质量标准。
质量检测包括外观检查、重量差异检查、含量测定等。
符合质量标准的滴丸可以进行包装,以便于使用和保存。
通过以上步骤,就可以完成实验室滴丸剂的制备。
需要注意的是,在制备过程中要保持卫生和清洁,避免污染和交叉污染。
同时,需要严格控制温度、湿度和光照等环境因素,以确保药物的稳定性和有效性。
实心滴丸生产机械设备工艺原理
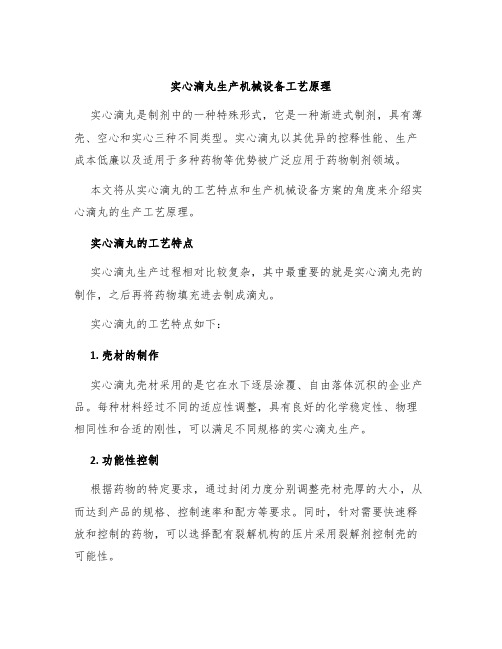
实心滴丸生产机械设备工艺原理实心滴丸是制剂中的一种特殊形式,它是一种渐进式制剂,具有薄壳、空心和实心三种不同类型。
实心滴丸以其优异的控释性能、生产成本低廉以及适用于多种药物等优势被广泛应用于药物制剂领域。
本文将从实心滴丸的工艺特点和生产机械设备方案的角度来介绍实心滴丸的生产工艺原理。
实心滴丸的工艺特点实心滴丸生产过程相对比较复杂,其中最重要的就是实心滴丸壳的制作,之后再将药物填充进去制成滴丸。
实心滴丸的工艺特点如下:1. 壳材的制作实心滴丸壳材采用的是它在水下逐层涂覆、自由落体沉积的企业产品。
每种材料经过不同的适应性调整,具有良好的化学稳定性、物理相同性和合适的刚性,可以满足不同规格的实心滴丸生产。
2. 功能性控制根据药物的特定要求,通过封闭力度分别调整壳材壳厚的大小,从而达到产品的规格、控制速率和配方等要求。
同时,针对需要快速释放和控制的药物,可以选择配有裂解机构的压片采用裂解剂控制壳的可能性。
3. 高品质纯度实心滴丸生产过程采用先进的纯化工艺和材料配方技术,能够保证壳材的物化特性和药物纯度的高品质,最大程度地保留药物的药效,同时降低了不良反应的风险。
4. 生产操作简单实心滴丸生产是一种容器内生产法,生产操作相对简单,必要的流动条件很容易通过采用特殊的装置来实现,可同时加工不同规格的实心滴丸,提高生产效率。
实心滴丸的生产机械设备方案实心滴丸生产机械设备方案主要分为壳材生产装置、滴丸制造机和相关的监测质量控制仪器。
1. 壳材生产装置实心滴丸的壳材是实心滴丸过程的核心。
壳材的制作采用的是水下逐层涂覆、自由落体沉积制法。
壳材生产装置主要包括自由落体沉积装置、涂覆装置、清洗设备和烘干装置等。
实心滴丸的壳材生产装置的特点如下:•采用进口高精度伺服电机,控制壳材的厚度和壳的封闭度。
•自动涂层系统,实现涂层的均匀性,降低手动涂层带来的误差。
•利用清洗装置,尽量排除生产过程中的杂质和污染,提高产品的质量。
2. 滴丸制造机滴丸制造机是用于实心滴丸制作过程的核心设备,它主要包括滴丸壳的灌装机、压片机和滚球机。
滴丸剂生产工艺流程

滴丸剂生产工艺流程
《滴丸剂生产工艺流程》
滴丸剂是一种固体制剂,常用于口服给药。
它具有溶解速度快、吸收迅速的特点,因此受到患者和医生的喜爱。
在滴丸剂的生产过程中,需要严格控制每一个环节,以确保最终产品的质量符合标准。
下面是滴丸剂生产工艺流程的简要介绍:
1. 样品接收和质量检测:首先,生产厂家会接收来自原料供应商的样品,并进行严格的质量检测。
只有通过检测的原料才能用于后续的生产工艺。
2. 原料配方:在确定原料质量合格后,生产工艺流程的下一步是进行配方。
根据药品的配方要求,严格按照配方比例将各种原料混合,确保每一批产品的成分均匀。
3. 制粒:接下来,原料将送入制粒机,通过旋转运动和添加适量的粘合剂,制成颗粒状的物料。
4. 压片:将制粒后的物料送入药片压片机,进行压片加工。
这一步是将原料压成规定大小和形状的药片,确保每一片药品的剂量一致。
5. 包衣:压片完成后,药片需要进行包衣处理,以增加药片的稳定性和耐储存性。
6. 包装:最后一步是对包装成品进行检查和包装,确保产品的
外观和质量完好无损。
除了以上流程,滴丸剂的生产还需要在每一个环节进行严格的质量控制和记录。
只有确保每一个步骤都符合标准要求,才能生产出安全、有效的滴丸剂产品。
滴丸剂的制备工艺流程

滴丸剂的制备工艺流程滴丸剂是一种固体制剂,由于药物分散在载体中,便于吞咽和吸收。
以下是滴丸剂的制备工艺流程。
1.准备原料:首先需要准备滴丸剂的活性成分、滴丸剂的载体和辅助材料。
活性成分是需要通过滴丸剂给药的药物,载体一般选择糖或淀粉,辅助材料包括填充剂、分散剂和可溶性导土剂等。
2.筛选原料:将准备好的原料进行筛选,目的是除去杂质和提高药物的纯度。
3.混合:将活性成分和辅助材料按照一定比例混合在一起。
为了保证混合的均匀性,可以使用混合机械或手工混合。
4.制粒:将混合好的药物和辅助材料进行制粒处理。
制粒的目的是使药物颗粒变得更大,并增加表面积,便于吸湿和吸附其他辅助材料。
5.包衣:包衣是将制粒后的药物颗粒进行包覆,增加药物的稳定性和口感。
包衣常用的材料有明胶、壳聚糖等。
包衣可以增加颗粒的溶解度,改善口感,并减少药物的因酸碱性质而受到的影响。
6.干燥:将包衣后的药物颗粒进行干燥处理,以去除颗粒表面的水分。
干燥的方法可以采用自然风干或烘干。
7.再包衣:将干燥后的药物颗粒再次进行包衣处理,可以增加稳定性和口感。
8.微粒化/制粉:对于较大颗粒的滴丸剂,可以进行微粒化或制粉,使药物更易吸收和溶解。
9.灭菌:对制备好的滴丸剂进行灭菌处理,以杀灭潜在的微生物。
10.检验:对制备好的滴丸剂进行质量检验,包括外观、颗粒大小、溶解度、水分含量等指标。
11.包装:将检验合格的滴丸剂进行包装,可以采用泡罩、铝箔袋或瓶装等方式。
12.贮存:将包装好的滴丸剂存放在干燥、阴凉和避光的地方,以保持良好的稳定性。
以上是滴丸剂的制备工艺流程,每个步骤都需要严格控制操作条件和质量标准,以确保滴丸剂的质量和疗效。
同时,制备滴丸剂需要依据具体药物和制剂的特点进行调整和优化,以满足临床应用的需要。
丹参滴丸的生产工艺是怎样的?

丹参滴丸的生产工艺是怎样的?丹参滴丸是一种常用的中药制剂,具有舒肝理气、活血化瘀的功效。
它通过采用一定的生产工艺,将丹参这种草本植物进行提取、加工,最终制成丹参滴丸。
下面将对丹参滴丸的生产工艺进行具体介绍。
一、原料采集和准备1. 选择优质丹参为了制作高质量的丹参滴丸,首先需要选择优质的原料丹参。
优质的丹参应该具备植株成熟度高、无虫食病害、颗粒饱满等特点。
2. 清洗和烘干将采集到的丹参进行清洗,去除泥土等杂质。
然后,通过烘干的方式,将丹参晾干,以便后续加工使用。
二、药材炮制1. 炒制丹参将丹参以适当的温度和时间进行炒制,炒制的目的是使丹参的活性成分更易释放出来。
2. 切片将炒制好的丹参进行切片,切片的大小和形状应根据具体制剂的要求进行调整。
三、药材提取1. 选择提取剂根据丹参中活性成分的溶解性,选择适当的溶剂进行提取。
常用的溶剂有水、乙醇等。
2. 提取工艺将切片好的丹参与提取剂进行浸泡和搅拌,使活性成分充分溶解到提取剂中。
然后,将提取液进行浓缩和干燥,得到丹参的提取物。
四、制粒和包衣1. 制粒将丹参的提取物进行制粒,可以使用粉碎、筛分等工艺。
2. 包衣为了方便患者服用,可以对制粒的丹参进行包衣处理。
包衣的材料可以是糖衣、脂肪衣等,以增加药丸的口感和稳定性。
五、干燥和包装1. 干燥将制成的丹参滴丸进行干燥处理,以去除多余的水分,提高质量和保存性。
2. 包装将干燥好的丹参滴丸进行包装,常用的包装材料有铝塑复合膜、硬胶囊等,以保证药物的质量和安全存储。
综上所述,丹参滴丸的生产工艺主要包括原料采集和准备、药材炮制、药材提取、制粒和包衣、干燥和包装等步骤。
通过科学、严谨的生产工艺,能够保证丹参滴丸的药效和品质。
作为一种传统中药制剂,丹参滴丸在临床中具有广泛的应用前景。
同时,我们也应该加强对丹参滴丸的研究和监管,以保证其安全有效的使用。
简述滴丸的制备工艺流程

简述滴丸的制备工艺流程一、前言滴丸是一种药物剂型,是将药物粉末包裹在糖衣中制成的小球状固体制剂。
滴丸具有口感好、易于咀嚼、易于吞咽等优点,因此广泛应用于医药领域。
下面将详细介绍滴丸的制备工艺流程。
二、原料准备1. 药品原料:根据配方要求称量所需的药品原料,一般需要进行筛选、粉碎和混合等处理。
2. 糖衣原料:根据配方要求称量所需的糖衣原料,一般需要进行溶解、搅拌等处理。
3. 辅助材料:如润滑剂、分散剂等,根据配方要求加入。
4. 溶剂:如水、酒精等,用于溶解糖衣原料和药品原料。
5. 工具设备:包括称量器、混合器、干燥器等。
三、制备步骤1. 药品原料处理:将所需的药品原料按比例称量,并进行筛选、粉碎和混合等处理。
筛选可以去除杂质和不符合要求的颗粒,粉碎可以使药品原料更加细腻,混合可以保证各种药品原料的均匀分布。
2. 糖衣原料处理:将所需的糖衣原料按比例称量,并进行溶解、搅拌等处理。
糖衣原料需要先加入溶剂中进行溶解,然后加热搅拌,使其均匀分散。
3. 药品和糖衣的混合:将药品和糖衣混合在一起,并加入辅助材料。
混合时需要注意控制温度和湿度,以免影响滴丸质量。
4. 滴丸成型:将混合好的药品和糖衣放入滴丸机中进行成型。
滴丸机会将混合好的药品和糖衣放在旋转的盘子上,并通过喷雾器喷出液体使其形成小球状固体制剂。
5. 干燥处理:将成型好的滴丸放入干燥器中进行干燥处理。
干燥时间、温度需要根据具体情况进行调整,以保证滴丸内部干透、外部硬化。
6. 包装:将干燥好的滴丸进行包装,包括瓶装、袋装等。
包装需要注意密封性和防潮性,以保证滴丸的质量和有效期。
四、总结制备滴丸需要进行原料准备、制备步骤等多个环节,每个环节都需要注意控制温度、湿度等因素,以保证滴丸的质量。
同时,还需要根据具体情况进行调整和改进,以提高生产效率和产品质量。
中药滴丸制剂工艺
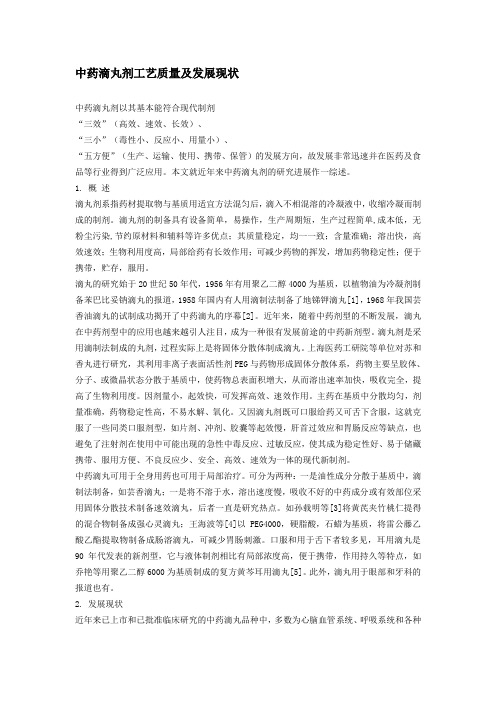
中药滴丸剂工艺质量及发展现状中药滴丸剂以其基本能符合现代制剂“三效”(高效、速效、长效)、“三小”(毒性小、反应小、用量小)、“五方便”(生产、运输、使用、携带、保管)的发展方向,故发展非常迅速并在医药及食品等行业得到广泛应用。
本文就近年来中药滴丸剂的研究进展作一综述。
1. 概述滴丸剂系指药材提取物与基质用适宜方法混匀后,滴入不相混溶的冷凝液中,收缩冷凝而制成的制剂。
滴丸剂的制备具有设备简单,易操作,生产周期短,生产过程简单,成本低,无粉尘污染,节约原材料和辅料等许多优点;其质量稳定,均一一致;含量准确;溶出快,高效速效;生物利用度高,局部给药有长效作用;可减少药物的挥发,增加药物稳定性;便于携带,贮存,服用。
滴丸的研究始于20世纪50年代,1956年有用聚乙二醇4000为基质,以植物油为冷凝剂制备苯巴比妥钠滴丸的报道,1958年国内有人用滴制法制备了地锑钾滴丸[1],1968年我国芸香油滴丸的试制成功揭开了中药滴丸的序幕[2]。
近年来,随着中药剂型的不断发展,滴丸在中药剂型中的应用也越来越引人注目,成为一种很有发展前途的中药新剂型。
滴丸剂是采用滴制法制成的丸剂,过程实际上是将固体分散体制成滴丸。
上海医药工研院等单位对苏和香丸进行研究,其利用非离子表面活性剂PEG与药物形成固体分散体系,药物主要呈胶体、分子、或微晶状态分散于基质中,使药物总表面积增大,从而溶出速率加快,吸收完全,提高了生物利用度。
因剂量小,起效快,可发挥高效、速效作用。
主药在基质中分散均匀,剂量准确,药物稳定性高,不易水解、氧化。
又因滴丸剂既可口服给药又可舌下含服,这就克服了一些同类口服剂型,如片剂、冲剂、胶囊等起效慢,肝首过效应和胃肠反应等缺点,也避免了注射剂在使用中可能出现的急性中毒反应、过敏反应,使其成为稳定性好、易于储藏携带、服用方便、不良反应少、安全、高效、速效为一体的现代新制剂。
中药滴丸可用于全身用药也可用于局部治疗。
复方丹参滴丸制备工艺

复方丹参滴丸制备工艺
复方丹参滴丸是一种中药制剂,它由多种天然草药组成,具有消肿止痛、活血化瘀、清热解毒等功效。
其制备工艺主要包括以下几个步骤:
首先,需要准备好所需的原材料,包括丹参、三七、桃仁、甘草、黄芩等多种中草药。
这些原材料需要进行质量检验,确保符合药典规定的标准。
接着,需要对原材料进行处理。
比如,将丹参和三七洗净后晾干,再研成细末;将桃仁去壳后研成细末;将甘草和黄芩煎煮后制成浓缩液等。
然后,需要按照一定的配方将各种原材料混合起来。
混合时需要根据不同的功效要求和药典规定的配比进行精确配比,确保每个成分的含量符合规定。
混合好后,需要将药物研磨成细末,然后进行粘合。
粘合方法有多种,比如采用淀粉、糖浆、蜂蜜等物质进行粘合。
最后,将粘合好的药末制成小丸,并进行包装。
包装时需要采用无菌、密封的方法,确保药物的质量和安全性。
以上就是复方丹参滴丸的制备工艺,每个步骤都需要严格遵守药典规定和操作规程,以确保药物的质量和疗效。
- 1、下载文档前请自行甄别文档内容的完整性,平台不提供额外的编辑、内容补充、找答案等附加服务。
- 2、"仅部分预览"的文档,不可在线预览部分如存在完整性等问题,可反馈申请退款(可完整预览的文档不适用该条件!)。
- 3、如文档侵犯您的权益,请联系客服反馈,我们会尽快为您处理(人工客服工作时间:9:00-18:30)。
第二节
滴丸滴制成型工艺操作
(2)开机操作 ① 打开“电源”开关,接通电源;滴罐及冷却柱处 照明灯点亮。 ② 在控制面板上,设定以下温度:“制冷温度”设 定为1-5℃;“油浴温度”和“滴盘温度”均为40℃。 ③ 按下“制冷”开关,启动制冷系统。 ④ 按下“油泵”开关,启动磁力泵,并调节柜体左 侧面下部的液位调节旋钮,使其冷却剂液位平衡。 ⑤ 按下“滴罐加热”开关,启动加热器为滴罐内的 导热油进行加热。 ⑥ 按下“滴盘加热”开关,启动加热盘为滴盘进行 加热保温。
第二节
滴丸滴制成型工艺操作
⑦ 待油浴温度和滴盘温度均显示达到40℃时,关闭 “滴罐加热”和“滴盘加热”开关,停留10分钟,使导热 油和滴盘温度适当传导后,再将二者温度显示仪调整到所 需温度(如一次性调整到所需温度,加热系统的惯性会使 温度飙升,令原料的稳定性下降)。油浴温度根据原料性 质而定,但应高于70℃;滴盘温度应比油浴温度高5℃, 以防止药液下滴时凝固。
(1)滴罐玻璃罐处与照明灯处温度较高,投料时要 小心操作,慎防烫伤。
(2)药液温度低于70℃时不可启动搅拌机进行搅拌, 否则原料未完全熔融易损坏电机。 (3)搅拌器不允许长期开启,且调节转速不应过高, 一般在60~100转/分钟范围内。
(4)经常留意冷却油液面高度是否适中,通过调节 液位调节旋钮,使冷却油液位平衡。
第二节
滴丸滴制成型工艺操作
② 投料:打开滴罐的加料口,投入已调剂好的原料, 关闭加料口(原料可以是固体粒状、粉末状,或在外部加 热成液体状再投料均可)。 ③ 打开压缩空气阀门,调整压力为0.7MPa。如原料 粘度小可不使用压缩空气。 ④ 当药液温度达到设定温度时,将滴头用开水加热 浸泡5分钟,带手套拧入滴罐下的滴头螺纹上。
滴丸滴制成型工艺操作
1.气压压力显示; 2.制冷温度显示; 3.制冷系统启动开 关; 4.滴罐加热启动开 关; 5.总电源启动开关; 6.气动调节旋钮; 7.搅拌电机速度调 节旋钮; 8.真空调节旋钮; 9.冷却油泵气动开 关; 10.滴盘加热气动开 关; 11.滴盘温度显示; 12.搅拌电机启动开 关; 13.药液温度显示; 14.真空度显示; 15.导热油温度显示
⑧ 正式滴丸后,每小时取丸10粒,用罩绸毛巾抹去 表面冷却油,逐粒称量丸重,根据丸重调整滴速。
第二节
滴丸滴制成型工艺操作
⑨ 收集的滴丸在接丸盘中滤油15分钟,然后装进干 净的脱油用布袋,放入离心机内脱油,启动离心机2~3次, 待离心机完全停止转动后取出布袋。 ⑩ 滴丸脱油后,利用合适规格的大、小筛丸筛,分 离出不合格的大丸和小丸、碎丸,中间粒径的滴丸为正品, 倒入内有干净胶袋的胶桶中,胶桶上挂有物料标志,标明 品名、批号、日期、数量、填写人。
二、实训适用岗位及设备介绍
本工艺操作适用于滴丸工、滴丸质量检查工、工艺员。
第二节
(一)滴丸工
滴丸滴制成型工艺操作
1.工种定义:滴丸工是指将固体或液体药物与基质 加热熔化混匀后,使用规定的设备将药液滴入不相混溶的 冷凝液中,使其收缩冷凝成球状制剂的操作人员。 2.适用范围:滴丸机操作、质量自检
(二)滴丸质量检查工 1.工种定义:滴丸质量检查工是指从事滴丸滴制生 产全过程的各工序质量控制点进行现场监控和对规定的质 量指标进行检查、判定的人员。 2.适用范围:滴丸滴制成型全过程的质量监督(工 艺管理、QA)
第二节
滴丸滴制成型工艺操作
2. 滴丸岗位操作法
(1)生产前准备
① 复核清场情况 a.检查生产场地是否无上一批生产遗留的软胶囊、物料、 生产用具、状态标志等。 b.检查滴丸操作间的门窗、天花、墙壁、地面、地漏、 灯罩、开关外箱、出风口是否已清洁、无浮尘、无油污。 c.检查是否无上一批生产记录及与本批生产无关文件等。 d.检查是否有上一次生产的“清场合格证”,且是否在 有效期内,证上所填写的内容齐全,有QA签字。
如实填写各生产操作记录(表8-1、8-2、8-3、8-4)
第二节
滴丸滴制成型工艺操作
(二)生产工艺及安全管理要点
1.滴丸操作室洁净度按30万级要求。室内相对室外 呈正压。
2.生产场地的地面比较光滑,应随时保持地面清洁, 在行走时动作要轻,跨步不要太大,严禁跑跳,慎防滑倒; 生产过程中使用台级加料前,必须先检查是否有滑动现象, 要慢上慢落,避免因台级滑动或鞋底打滑而摔倒。
第一节
概
述
原料 配制 基质 滴丸 过筛 干燥、整理 药液 滴制 冷却
检验
入库
第二节
一、实训目标
滴丸滴制成型工艺操作
1.掌握滴丸滴制成型岗位操作法
2.掌握滴丸滴制成型工艺管理要点及质量控制要点 3.掌握DWJ-2000型滴丸试验机标准操作规程 4.掌握DWJ-2000型滴丸试验机的清洁及维护、保养标 准操作规程
(5)滴头为较精密部件,必须小心拆装,防止磕碰。
第二节
滴丸滴制成型工艺操作
3. DWJ-2000型滴丸试验机清洁标准操作规程
(1)往滴罐注入80℃以上的饮用水(必要时加入清洁 液),关闭。
(2)打开“搅拌”开关,调节调速旋钮,对滴罐内热 水进行搅拌,提高搅拌器转速,使残留的药液溶于热水中。 (3)在滴头上插上放水胶管,然后打开滴头开关,将 热水从滴头排出。打开滴头开关前,在冷却柱上口处放进接 盘,防止泄漏的热水滴入冷却柱内,影响冷却油的纯度。 (4)重复以上操作,直至滴罐内无药液残留、饮用水 清澈无泡沫,然后用纯化水清洗,最后待滴罐内的水全部流 出为止。用75%乙醇擦拭消毒。
⑧ 当药液温度达到设定温度时,将滴头用开水加热 浸泡5分钟,带手套拧入滴罐下的滴头螺纹上。
⑨ 打开滴罐的加料口,投入已调剂好的原料,关闭 加料口。
第二节
滴丸滴制成型工艺操作
⑩ 打开压缩空气阀门,调整压力为0.7MPa。如原料 粘度小可不使用压缩空气。 ⑾ 启动“搅拌”开关,调节调速旋钮,使搅拌器在 要求的转速下进行工作。 ⑿ 待制冷温度、药液温度和滴盘温度显示达设定值 后,缓慢钮动滴缸上的滴头开关,打开滴头开关,使药液 以一定的速度下滴。 ⒀ 试滴30秒,取样检查滴丸外观是否圆整,去除表 面的冷却油后,称量丸重,根据实际情况及时对冷却温度、 滴头与冷却液面的距离和滴速作出调整,必要时调节面板 上的“气压”或“真空”旋钮(药液粘稠、丸重偏轻时调 “气压”旋钮,药液较稀、丸重偏重时调“真空”旋钮), 直至符合工艺规程为止。
第二节
滴丸滴制成型工艺操作
d.检查滴头开关是否关闭。
e.检查油箱内的液体石蜡是否足够。
f.检查电子秤、电子天平是否计量范围符合要求,清 洁完好,有计量检查合格证,在规定的使用期内,并在使 用前进行校正。 g.接入压缩空气管道。 (2)生产操作 ① 按《滴丸机操作规程》设定“制冷温度”、“油 浴温度”和“滴盘温度”,启动制冷、油泵、滴罐加热、 滴盘加热。
第二节
滴丸滴制成型工艺操作
(三)滴丸制备设备简介
DWJ—2000型滴丸试验机(图8-1、图8-2)是采用机 电一体化紧密组合方式,集动态滴制收集系统、循环制冷 系统、电气控制系统与一体。
三、实训设备
DWJ-2000型滴丸试验机
第二节
1.搅拌器; 2.柜体; 3.升降装置; 4.液位调节 手柄; 5.冷却油泵; 6.放油阀; 7.放油阀; 8.接油盘; 9.制冷系统; 10.油箱阀; 11.油箱; 12.出料斗; 13.出料管; 14.冷却柱; 15.滴制滴头; 16.滴制速度 手柄; 17.导热油; 18.药液; 19.加料口; 20.搅拌电机;
⑾ 连续生产时,当滴罐内药液滴制完毕时,关闭滴 头开关,将“气压”和“真空”旋钮调整到最小位置,然 后按②~⑩项进行下一循环操作。
第二节
(3)生产结束
滴丸滴制成型工艺操作
① 关闭滴头开关。
② 将“气压”和“真空”旋钮调整到最小位置,关 闭面板上的“制冷”、“油泵”开关。 ③ 将盛装正品滴丸的胶桶放于暂存间。 ④ 收集产生的废丸,如工艺允许,可循环再用于生 产;否则用胶袋盛装,称重并记录数量,放于指定地点, 作废弃物处理。 ⑤ 清洁与清场
3.放入离心机的物料要均匀放入缸体内,装入物料 不可过满,加盖并上紧后方可启动,不可边转边加物料; 出料时必须等其完全停止转动后方可打开盖。
第二节
滴丸滴制成型工艺操作
(三)质量控制关键点 1.滴丸外形(是否圆整、有无粘连、拖尾) 2.滴丸丸重 3.溶散时限 (四)DWJ-2000型滴丸试验机使用规程 1. DWJ-2000型滴丸试验机标准操作规程 (1)开机前准备工作 ① 检查滴头开关是否关闭。 ② 检查制冷、搅拌、油泵、滴罐加热、滴盘加热开 关是否关闭,气压、真空、调速旋钮是否调整到最小位置。 ③ 检查设备内冷却石蜡油是否足够,如不足应及时 补充。
第二节
滴丸滴制成型工艺操作
a.连续生产同一品种时,在规定的清洁周期设备按 《滴丸机清洁规程》进行清洁、生产环境按《300 000级 洁净区清洁规程》进行清洁;非连续生产时,在最后一批 生产结束后按以上要求进行清洁。
b.每批生产结束后按《滴丸间清场规程》进行清场, 并填写清场记录。
⑥ 将本批生产的“清场合格证”、“中间产品递交 许可证”、“准产证”贴在批生产记录规定位置上。 ⑦ 复查本批的批生产记录,检查是否有错漏记。 (4)记录
滴丸制备工艺操作
第八章
滴丸制备工艺操作
第一节 第二节
概
述
滴丸滴制成型工艺操作
第三节
综合实训
第一节
概
述
滴丸系指固体、液体药物或药材提取物与基质加热熔 化混匀后,滴入不相混溶的冷凝液中,收缩冷凝而成的制 剂。选择适宜的基质与冷凝剂十分重要,常用水溶性基质 有聚乙二醇6000、聚乙二醇4000、硬脂酸钠等,脂肪性基 质有硬脂酸、单硬脂酸甘油酯等。 一般生产流程如下: 注:虚线框内代表30万级或以上洁净生产区域 物料: 工序: 检验: 入库: