汽车焊装生产线多车型混合生产
白车身焊装工艺规划问题解决思路及方法

文/广州汽车集团乘用车有限公司 徐文康白车身焊装工艺规划问题解决思路及方法作者简介:徐文康(1984-),男,焊接工艺工程师,目前从事白车身焊装工艺开发的工作,主要负责焊装同步工程,焊装工艺规划,焊装工艺工装导入,量产前工艺问题解决及节拍达成。
摘要:白车身焊装工艺规划过程中需要解决很多问题,这些问题囊括了焊接品质、成本控制、 节拍保证、标准化生产、安全生产保证五个方面(QCDMS)。
本文详细介绍了这五个方面可能遇到的常规问题,有针对性地分析了这些问题,并提出问题解决的思路及方法,为工艺人员提供参考。
关键词白车身;焊接;工艺: 白车身焊装工艺规划是焊装工艺导入前期对车间作业人员、生产设备、生产物料、工艺路线及生产线进行合理配置,以达成高品质、低成本、高效率、高标准、更安全地生产白车身的目的。
前期规划做的越充分,后期工作开展越顺利,风险更小,并且大大缩短达成量产的时间。
工艺规划是白车身焊装工艺导入前期一项复杂的系统工程,此时白车身设计基本定型,需要结合现有生产条件对车身数据作全面分析以及工艺仿真,期间可能会遇到各种工艺问题,关键是如何做出合理的对策。
工艺问题可能影响焊接品质、成本控制、节拍保证、标准化生产、安全生产保证五个方面,合理的对策首先必须满足高品质的要求,虽然品质是第一要素,但是其他方面同样需重视,而且要进行层层检讨,有问题分别作对策以及实施,对实施效果进行仿真或验证。
下面从这五个方面入手,充分阐述其思路及方法。
1 焊接品质 工艺规划跟品质是息息相关的,不合理的焊接工艺可能导致焊接出错或产生焊接缺陷,甚至造成工件损坏。
为节约白车身焊装生产线投入,一条生产线将生产好几款车型,而每种车型的白车身又包含了两种以上的派生,从而导致派生零件之间焊点数量及焊点位置的差异,如果没有对这些差异做出正确的区分,则很容易造成焊接出错。
焊接出错是白车身焊接过程中较为严重的品质问题,如果不及时发现加以制止,有可能造成批量不良,还会带来严重的生产损失,甚至造成零件报废。
焊装车间主焊线柔性化改造
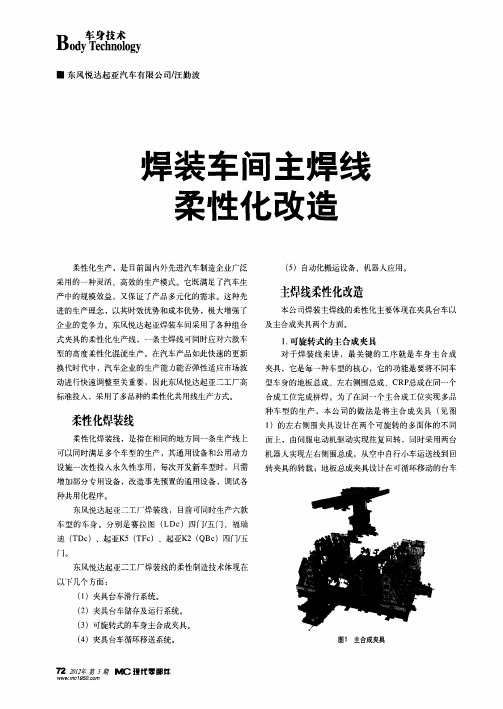
图 主焊线台车夹具 2
式实现 最大混流 。在 实际生产过程 中 ,可以通 过增加不 同类型 台车的数量 来实现主线 的柔性化生产 ,但投资成 本大 ,并 且在实 际生 产过程 中需要 事先对车 型和台车进
图3 D 车型 @U I T c NT 对应的车身断面
当然 ,主焊 线的柔性化改造也 不仅 仅是 上述两个方 面 ,还 包括搬运 系统 的改造 、多车种 吊具 的改造、机器
()自动化搬运设备、机器人应用。 5
主焊线柔性化改造
本公司焊 装主焊线 的柔性化 主要体现在夹具 台车以 及主合成夹具两个方面 。
企业的竞争力。东风悦达起亚焊装车间采用了各种组合
式夹具的 柔性 化生产线 ,一条主焊 线可同时应对六款车 型的高度 柔性化混 流生产 。在汽车产 品如此快速的更新 换代时代 中,汽车企业的生产能 力能否弹性适应市场 波
合成 工位 完成拼焊 。为 了在同一个主 合成 工位实现多 品
柔性化焊装线
柔性 化焊装线 ,是指在相 同的地方 同一条生 产线上 可以 同时满 足多个车型的生产 , 通用设备和公用动 力 其
种车型的生产 ,本公司的做法是将主合成夹具 ( 见图
1 )的左右侧 围夹具 设计在 两个可旋 转 的多面体 的不 同 面上 ,由伺服 电动机 驱动实现往 复回转 ,同时采用两 台 机 器人实现左右侧 围总 成 ,从空 中 自 小车运送线到 回 行 转夹 具的转载 ; 地板 总成夹具设计在 可循环移动 的台车
UNI T。
吊具上。这几组夹具通过P C L 程序控制后实现车身的准
确定位 合成 ,再 由1台机器人共 同完成相关 工位的焊接 2 操作 。其 多面体的 回转面数量是根 据生产纲领 和车种数 量来确定 的 ,本 公司 目前有一 个四面 回转体结 构 ,生产 六款车型 (D 4 、T c F 、Q 4 ),另92 1年 L c/ D 、T c B / 5 5 602 新增加 的车型需要增加 另一组 四面 回转体结构 ,来对应 新增加的一款车 型 ( D )。 Y c
车身车间又称为焊装车间

车身车间又称为焊装车间,生产的是整个汽车零部件的载体——白车身。
车身是以钢制结构件构成的整车支撑部件,其制造成本约占汽车总成本的40% 左右,焊接质量优劣对整车质量起着决定性作用。
车身通常由300〜600个形状复杂的冲压件及标准件,在70〜100个工位上以快节奏焊接而成,辅以少量的焊接、胶接和螺接,焊点多达4000〜6000个。
车身车间机运线规划的重点是将工艺设备、输送设备、通道走廊和设备全生命周期等一系列因素有机协调,得出最佳方案,在满足生产要求的前提下,尽量减少物流搬运量和搬运时间,提高柔性化生产能力。
机运线的先进程度直接决定制造水平的高低,目前上汽乘用车结合多个工厂规划实际情况,已经基本实现了以柔性化、多车型混合焊接为目标的高度自动化、机器人取代人工的生产线规划技术,达到了国际先进水平。
方案规划机运线的方案规划和车间的工艺流程设计是一个并行的过程,方案规划以特定的工艺流程为前提,同时不同的机运线布局设计又反过来影响工艺流程的设计。
上汽某工厂的车身车间采用工艺流程原则来进行布局设计,车身各个零部件按加工工艺顺序流经不同的工位,不仅能够达到特定的高生产节拍,同时可以给生产提供最大限度的制造柔性。
在方案规划阶段,需要通过部门交流、历史资料和规划目标等来确定机运线的输入,根据输入因地制宜地规划最适合的方案。
输入主要分为两类:第一类是与工艺相关的输入,如产品的变更、节拍要求变化、存储区大小的需求以及车型生产配比调整等;第二类是与国家标准和工厂规范相关的输入,如各类设备的国家标准、整车的通过性、机运技术规范和设备的选型标准等。
工艺输入中最典型和常见的是工艺变更以及工艺能力不足提出的需求。
1.工艺变更提出的需求上汽某车身车间共线生产A 和B 两种车型,B 车型侧围分为侧围外板和内板,需要在拼合侧围和车顶板后才能拼合侧围外板,因此B车型需要有内总拼和总拼两次总拼;而A车型侧围内板和外板可在侧围分拼完成拼合,因此完成内总拼后可直接进行补焊。
车身装配焊接生产线

车身装配焊接生产线引言车身装配焊接生产线是汽车制造过程中的关键环节之一。
它涉及到车身的组装和焊接工序,直接影响到汽车的质量和效率。
本文将介绍车身装配焊接生产线的工作流程、设备和关键技术。
基本工作流程车身装配焊接生产线的基本工作流程包括以下几个步骤:1.车身零部件供应:车身零部件是车身装配焊接的基本组成部分,供应商将零部件送至生产线。
2.车身装配:在装配区域,工人将车身零部件按照装配顺序进行组装。
这包括安装车身框架、车身面板、车身底盘等。
装配过程中需要使用各种设备和工具,如螺丝刀、气动压机等。
3.焊接工序:在焊接区域,车身的各个零部件会通过焊接技术进行连接。
常用的焊接方法包括气体焊接、电弧焊接等。
焊接工序需要使用焊接设备和辅助设备,如焊接机器人、焊接工作台等。
4.质检和修正:焊接完成后,车身会通过质检线进行检查。
检查包括焊接缺陷、尺寸偏差、外观等方面。
如果发现问题,需要对车身进行修正,确保其质量达到标准要求。
5.上涂料和烤漆:车身经过质检合格后,会进入涂料区域。
在这里,工人会给车身上涂底漆、面漆、清漆等。
然后将车身送至烤漆室,进行加热和固化,以确保漆面质量和耐久性。
6.装配附件:在装配线上,还需要安装一些附件,如车灯、门把手、车身贴纸等。
这些附件的安装需要工人进行手工操作,确保符合设计要求。
7.最终装配和检验:车身装配完毕后,会进行最终的检验,包括车身外观、内饰、灯光等方面。
通过检验后,车身会被送至下一工序或最终组装线。
设备和技术车身装配焊接生产线涉及到一系列设备和关键技术,以下是常用的设备和技术:•焊接机器人:焊接机器人是车身焊接生产线的核心设备之一。
它可以实现自动化焊接,提高焊接质量和效率。
通过使用焊接机器人,可以减少人为因素的影响,提高生产线的稳定性和一致性。
•自动测量系统:为了确保车身装配的精度和一致性,常常使用自动测量系统。
这些系统可以对车身的尺寸、位移、角度等进行测量和分析,及时发现装配差异,并进行修正。
探讨焊装自动化生产线规划

探讨焊装自动化生产线规划摘要:随着人们经济实力的不断提升,对汽车的需求也越来越大,使用汽车的频率也越来越高,同时随着汽车领域的不断发展,人们对汽车也有了越来越多的需求,汽车的样式功能等也越来越趋于多样化。
本文围绕着汽车焊装自动化生产线展开了分析和探讨,对其优点进行了介绍,分析了生产线规划的具体要求,阐述了汽车焊装自动化生产线的规划布局,以期给相关从业人员提供参考。
关键词:焊装;自动化;生产线;规划对于汽车制造业而言,面对人们对不同车型的喜爱和需求,生产的汽车种类越来越多样,开始朝着车型丰富但产量小的方向发展。
焊接自动化生产线能够满足不同车型的生产需求,能够有效提高生产效率,使汽车生产线上各项工艺环节的设备都能得到有效利用,同时还使生产过程的自动化大大提升,有效节约车间用地面积。
一、焊装自动化生产线的优势汽车焊装自动化生产线有着其独特的优势,能够提升各项资源和设备的利用率,使焊接更加精准高质,生产效率有效提升,能够根据能够满足不同车型生产需要。
和传统的生产线相比,更加符合当前对当前汽车的生产需求。
二、焊装自动化生产线技术工艺规划要求(一)确定生产目标焊装自动化生产线规划最首要的任务是要明确生产目标。
生产目标主要包括预计生产目标和远期生产目标,前者需要根据所需生产的车型类别和车辆数量来进行明确,后者则是为后续生产线的复制和延伸做准备的。
(二)确定工作制度工作制度和生产效率之间的关系非常密切,如果每天的工作时长按照8小时计算,中途休息时间按1小时计算,每周按5个工作日计算,倒班制度按照四班三倒来计算,便可算出每年焊装自动化生产线的工作时间为(8-1) x3 x245=5145h。
(三)确定生产能力生产能力是根据上述两项内容得出的,即将生产目标除以生产时长得到生产能力。
如果设定的生产目标为a台,那么生产能力必须要大于等于a÷5145,才能保障生产目标得以完成。
(四)设计原则设计过程中必须要保障成本合理、物流合理,同时各个模块要分工明确,要保障生产线的自动化程度满足实际需要。
白车身焊装生产线输送方式的应用及比较

车辆工程技术53车辆技术 汽车焊装生产线是汽车白车身全部成形工位的总称,其由车身总成线与多条分总成线构成,每一条总成线或分总成线又由多种焊装工构成。
每一个工位均由部分定位夹具、供水供气构成。
线间、工位间通过搬运机、机器人等搬送设备实现上下料与零部件的传送工作,以此来确保生产线中各项工作的连续性。
汽车焊装生产线主要包含了地板总成线、侧围总成线、车身合成线以及车身装配完成线。
因此,焊装生产线能否实现高速柔性化,其输送设备方式就显得尤为重要。
1 往复杆输送系统 往复杆的输送系统通常安设在夹具的平台之上,与夹具共同构成了焊装生产线。
往复杆输送系统通常由升降机构、同步机构、运动机构、定位机构、电控系统、平衡助力机构等组成。
依照不同的标准分级,往复杆输送线能够进行不同的分类,分类的方式可以以安装形式进行,主要分为空中往复杆输送与地面腹杆输送线;依照往复杆输送线梭结构进行分类,可以分为双往复杆树洞与单往复杆输送线;依照往复杆输送形式进行分类,可以分为水平往复杆输送线与升降往复杆输送线;依照往复杆输送线的举升机构进行分类,可以分为独立升降往复杆输送线与同步升降往复杆输送线[1]。
往复杆输送系统的工作原理主要是通过伺服变频电机带动齿轮与齿条来进行一段距离的往复运动;其举升、降低运动为达到一工位之后落下,能够便于夹具进行夹紧工作,在焊接结束之后,顶升能够促使工件离开夹具,进而使得工件与夹具不会互相干涉,便于输送工作[2]。
往复杆输送系统的主要特点在于机构简单、机械化程度较高、输送定位精度高,而缺点则是设备投资较大、输送机结构较为复杂、输送车型的柔性较差。
2 滑撬输送系统 滑撬输送系统属于白车身焊装车间中应用最为广泛的一种输送设备,多用于车身总成线工序间的输送、调整线输送、焊装车间空中储运线车身储存输送。
这种输送系统主要由滑撬、普通输送滚床、升降输送滚床、旋转滚床、垂直升降机以及电控系统所构成。
滑撬输送系统的主要优点为自动化程度高,能够用于多种批量生产的生产线上,同时其能够在一条生产线中进行间歇、连续输送,以此能够实现生产线中的联线输送,能够将下车身总成线、车身总成焊装线、调整线、车身储运线联系为一个整体,更加便于实现一个车间多车型生产线之间的联线,能够将不同车型的下车身总成线、车身主线独立布置[3],共同构建补焊线、调整线,更加容易实现生产线的分期投入,且输送速度较快、定位精度较高。
汽车自动化焊装车间规划

汽车自动化焊装车间规划摘要:汽车焊接车间规划,首先是由生产纲领、生产体制、工艺流程和装配工时,确定车间工艺布局及走向。
在车间规划时使用的工艺流程,是标准工艺流程,该流程是与生产的具体汽车品种不直接相关的,是具有指导性质的流程,其可以指导某一大类汽车的生产,如承载式车身汽车或非承载式车身汽车。
承载式车身汽车底盘装配标准工艺流程,可描述如下。
其规定了一定的流程,制动管燃油管需最先装配,前、后保险杆总成和车轮需最后装配。
装配工艺流程的建立,是基于经验的长期积累,同时考虑了未来的发展形成的。
标准工艺流程并不是一成不变的,而是随着新技术、新工艺的应用而不断更新的。
关键词:汽车自动化;焊装车间;规划设计1 焊装线技术必要性和优势目前,汽车厂生产现状大趋势:多品种车型并行、小批量生产增多、产品生命周期缩短、生产线建设周期缩短、机器人逐渐替代人工、智能化信息化订单式生产增多等。
亟待解决的需求与矛盾:工业用地资源紧张,用于焊装生产的厂房已建设并固化,现有厂房无法满足不断新增的车型。
如某热销车型焊装线产能满足不了订单需求,人工焊接工位过多,同时又存在其它订单少的单一自动线大量机器人、焊接设备等资源闲置浪费;后续又会继续增加车型投入生产,对应工装和焊接设备在不断的投入,单一车型产量小,设备及产线利用率极低。
故需分期建设能多车型混线生产的高自动化、高柔性、高产能的车身焊装生产线,以满足当前及后续多车型生产需求。
其优势如下:1.1 设备及产线利用率高降低后续重复性投入汽车行业竞争的加剧与客户需求的提升,车型需不断的推陈出新和更新换代,焊装线已由单一品种大量生产方式向多品种批量柔性生产方式转变。
产线占地面积集中,空间利用率提高。
利用自动化柔性线,通过实现通用设备的共用而实现一次投入。
可以有效的避免多次设备重复投入造成的资源浪费,设备重复利用率提高。
唯一的缺点是首次投入中耗资较大。
1.2 焊接质量及焊接精准度提高焊接工程规模以及工程的复杂性在不断发展,进而对焊接质量提出了较为严格的要求。
KUKA焊装线柔性化改造设计讲解
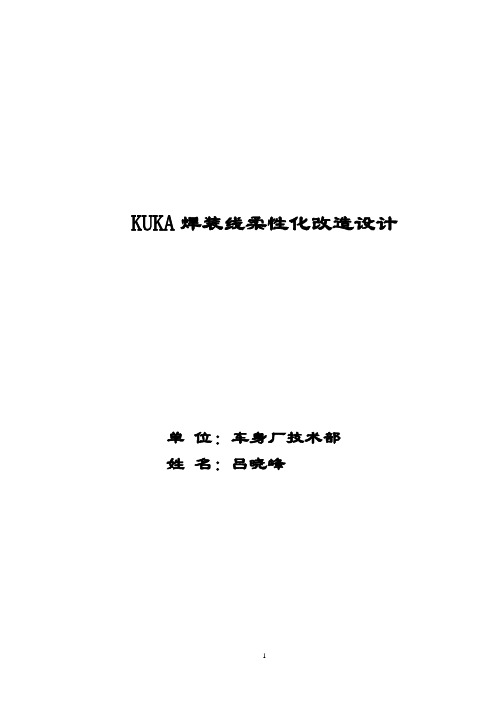
KUKA焊装线柔性化改造设计单位:车身厂技术部姓名:吕晓峰KUKA焊装线柔性化改造设计摘要: 本文通过对多品种平头车驾驶室产品的结构分析,结合KUKA 焊装线的结构特点,简述进口焊装线柔性化改造的工艺设计过程,并对实施过程中的难点进行了分析,阐述了解决的方法,为今后类似的改造设计提供一些参考意见。
关键词:KUKA线、工艺分析、统一基准、平移机构、模拟分析、并行实施。
概述随着汽车市场竞争的加剧,客户对汽车产品的需求越来越多样化。
汽车生产厂为适应这一市场变化,产品也由以往的大批量少品种,逐步转向多品种的柔性化生产。
这对焊装生产线的柔性化多品种生产能力的要求也就越来越高。
我厂于九四年从德国库卡公司(KUKA)引进了一条具有九十年代国际先进水平的焊装生产线,该生产线具有设备先进、工艺性好、自动化率高、夹具定位准确、安全性能好等特点。
按当时的设计要求,该生产线能生产宽、窄两种系列的平头卧铺车驾驶室。
根据总公司对市场的调查,内饰空间大的驾驶室产品将越来越受市场欢迎。
为抓住这一市场要求,公司决定在我厂生产高顶加长的平头卧铺车驾驶室。
能将如此先进、复杂的焊装线使用好、维护好已很不容易,改造它实现多品种混流生产就更不容易,风险也很大。
改造KUKA线实现多品种混流生产已成为能否实现EQ4160系列车型的关键项目之一,为此公司将此项目列为本年度公司的重点项目。
为确立和实现这个目标,我厂领导与工程技术人员做了大量的调查、研究与论证工作,采取了产品设计、工艺方案、现场调试安装并行实施的方式,解决了许多技术难题,在短短的半年时间里,不仅实现了KUKA焊装线能混流生产宽窄、高矮、长短车型的平头卧铺驾驶室的能力,而且还保留了原来的工艺性好、自动化率高、夹具定位准确等优点。
因为本次改造的难点是产品设计和工艺方案的确定,所以本文将主要对以上两个方面做一些介绍和说明。
一、原KUKA焊装线工艺过程简介1.工艺参数KUKA焊装线由六个工位的地板线和十二个工位的总装线两部分组成,工位间距5m,生产纲领为4.5万辆/年,生产节拍为4.672分/辆。
- 1、下载文档前请自行甄别文档内容的完整性,平台不提供额外的编辑、内容补充、找答案等附加服务。
- 2、"仅部分预览"的文档,不可在线预览部分如存在完整性等问题,可反馈申请退款(可完整预览的文档不适用该条件!)。
- 3、如文档侵犯您的权益,请联系客服反馈,我们会尽快为您处理(人工客服工作时间:9:00-18:30)。
一、前言随着我国经济的蓬勃发展,人民生活水平的提高,汽车越来越多地进入了家庭。
人们购买力的提高,也刺激了汽车消费的迅猛增长。
汽车生产企业面对瞬息万变的市场,对产品的市场销售难以准确预测,因此汽车企业的生产能力能否弹性地适应市场波动进行快速调整,显得至关重要。
汽车市场的竞争点越来越集中在产品的更新换代上,面对如此快速的产品更新,汽车行业过去采用的那种大批量单车种专用线的生产模式已不太适应当前发展的要求。
因此多品种的柔性化共用线生产方式也就越来越多地应用在汽车生产中,尤其对于汽车焊装生产这一复杂的专业化制造过程来说,如何实现“柔性化”又是汽车柔性化生产关键。
二、焊装生产线的作用及分类装焊生产的主要任务就是完成车身(也称为白车身,Body in white)的制造,对于轿车来说,车身焊装线一般是由地板总成线、左右侧围总成线、CRP(仪表台横梁+顶盖+后行李仓托架)线和门盖总成线、车身装配调整线等组成。
而各分总成又由很多合件、组件及零件(大多为冲压件)组成,当今由于汽车主机厂考虑到起初的开发投资、日后的生产物流、品质管理等因素,这些分总成线一般都建在主机厂附近的配套厂,采用即时直供方式为主机厂焊装线服务。
所谓专有化焊装线,也称之为单一化焊装生产线,就是该焊装线只能为单一车型提供生产,若再开发新车种生产时,就必须异地或迁移现有焊装线后重新建设焊装线,因此,厂房、设备及公用动力设施重复投资造成浪费,人员流动生产效率低。
而柔性化焊装线,是指在相同的地方同一条生产线上可以同时满足多个车种的生产,其通用设备和公用动力设施一次性投入永久性享用,每次开发新车型时,只需增加部分专用设备;改造事先预置的通用设备;调试各种共用化程序。
因此,避免了重复投资造成的浪费,而且缩短了技改时间,但起初的一次性投资相对会较大。
三、柔性化焊装线然而,这种柔性焊装线它究竟是如何实现多车种混线生产的呢?下面就以东风悦达起亚2工厂焊装线为例来说明柔性制造技术在焊装生产线上的应用,东风悦达起亚 2工厂焊装线,是依据30万台,年纲领设计的,厂房面积33600平方米,分二个阶段投入实施,目前第一阶段15万台,年的能力已经建成并投产,可以同时生产3个车型的车身。
1、夹具台车滑行系统所谓夹具台车滑行系统,就是将不同车型的专用夹具设计于台车上,而台车又安装于类似火车轨道的呈“甲”字型排布、可产生强大电磁力的滑行底座上,夹具台车在滑行线上受到电磁引力作用后可选择性地循环高速滑行。
另外,利用伺服马达驱动可旋转的夹具台车切换装置,实现不同车种的专用夹具台车进行空载,满载切换。
专用夹具台车是依据现场的生产管理系统(G-MES)的指令车型结合设备PLC控制程序进行自动调用,夹具上钣金件的投料是由人工或机器人来完成;但焊接作业全部由机械手自动完成,拼接后分总成件再由机械手取料并送人下道工序。
因此,这种柔性方式可实现为了满足不同消费者的多品种、高品质、低成本的车身焊接和装配要求。
(其基本结构如图1所示)图1 夹具台车滑行系统2、夹具台车储存及运行系统所谓夹具台车储存及运行系统,首先要说明的是该系统是一个综合的运行系统,它由生产作业运行系统、夹具台车空中储存及选择切换系统、夹具台车升降转换系统等组成。
其中,生产作业运行系统的功能是完成工艺规定的作业内容,其结构是:夹具台车设置在带有往复杆的“一”字型双轨道底座上,通过伺服马达驱动往复杆拖动夹具台车前进,到位后往复杆返回,如此循环往复。
台车储存及切换系统的功能是将夹具按车种进行归类存放,然后再依据生产需要有选择性地调用出来,为了节省生产区域面积,该系统通常都设置在生产线的正上方的空中平台上,其结构是:在空中平台上按“四”字型设置带驱动电机的滚床,夹具台车在滚床上储存,在滚床的两端设有可横向移动的台车载运装置,实现台车的车型选择。
台车升降转换系统的功能是将工作完成后空的台车上载到空中平台的储存区、同时将从储存区选择出的空台车下载至生产线上。
(其基本结构如图2所示)一、前言随着我国经济的蓬勃发展,人民生活水平的提高,汽车越来越多地进入了家庭。
人们购买力的提高,也刺激了汽车消费的迅猛增长。
汽车生产企业面对瞬息万变的市场,对产品的市场销售难以准确预测,因此汽车企业的生产能力能否弹性地适应市场波动进行快速调整,显得至关重要。
汽车市场的竞争点越来越集中在产品的更新换代上,面对如此快速的产品更新,汽车行业过去采用的那种大批量单车种专用线的生产模式已不太适应当前发展的要求。
因此多品种的柔性化共用线生产方式也就越来越多地应用在汽车生产中,尤其对于汽车焊装生产这一复杂的专业化制造过程来说,如何实现“柔性化”又是汽车柔性化生产关键。
二、焊装生产线的作用及分类装焊生产的主要任务就是完成车身(也称为白车身,Body in white)的制造,对于轿车来说,车身焊装线一般是由地板总成线、左右侧围总成线、CRP(仪表台横梁+顶盖+后行李仓托架)线和门盖总成线、车身装配调整线等组成。
而各分总成又由很多合件、组件及零件(大多为冲压件)组成,当今由于汽车主机厂考虑到起初的开发投资、日后的生产物流、品质管理等因素,这些分总成线一般都建在主机厂附近的配套厂,采用即时直供方式为主机厂焊装线服务。
所谓专有化焊装线,也称之为单一化焊装生产线,就是该焊装线只能为单一车型提供生产,若再开发新车种生产时,就必须异地或迁移现有焊装线后重新建设焊装线,因此,厂房、设备及公用动力设施重复投资造成浪费,人员流动生产效率低。
而柔性化焊装线,是指在相同的地方同一条生产线上可以同时满足多个车种的生产,其通用设备和公用动力设施一次性投入永久性享用,每次开发新车型时,只需增加部分专用设备;改造事先预置的通用设备;调试各种共用化程序。
因此,避免了重复投资造成的浪费,而且缩短了技改时间,但起初的一次性投资相对会较大。
三、柔性化焊装线然而,这种柔性焊装线它究竟是如何实现多车种混线生产的呢?下面就以东风悦达起亚2工厂焊装线为例来说明柔性制造技术在焊装生产线上的应用,东风悦达起亚 2工厂焊装线,是依据30万台,年纲领设计的,厂房面积33600平方米,分二个阶段投入实施,目前第一阶段15万台,年的能力已经建成并投产,可以同时生产3个车型的车身。
1、夹具台车滑行系统所谓夹具台车滑行系统,就是将不同车型的专用夹具设计于台车上,而台车又安装于类似火车轨道的呈“甲”字型排布、可产生强大电磁力的滑行底座上,夹具台车在滑行线上受到电磁引力作用后可选择性地循环高速滑行。
另外,利用伺服马达驱动可旋转的夹具台车切换装置,实现不同车种的专用夹具台车进行空载,满载切换。
专用夹具台车是依据现场的生产管理系统(G-MES)的指令车型结合设备PLC控制程序进行自动调用,夹具上钣金件的投料是由人工或机器人来完成;但焊接作业全部由机械手自动完成,拼接后分总成件再由机械手取料并送人下道工序。
因此,这种柔性方式可实现为了满足不同消费者的多品种、高品质、低成本的车身焊接和装配要求。
(其基本结构如图1所示)图1 夹具台车滑行系统2、夹具台车储存及运行系统所谓夹具台车储存及运行系统,首先要说明的是该系统是一个综合的运行系统,它由生产作业运行系统、夹具台车空中储存及选择切换系统、夹具台车升降转换系统等组成。
其中,生产作业运行系统的功能是完成工艺规定的作业内容,其结构是:夹具台车设置在带有往复杆的“一”字型双轨道底座上,通过伺服马达驱动往复杆拖动夹具台车前进,到位后往复杆返回,如此循环往复。
台车储存及切换系统的功能是将夹具按车种进行归类存放,然后再依据生产需要有选择性地调用出来,为了节省生产区域面积,该系统通常都设置在生产线的正上方的空中平台上,其结构是:在空中平台上按“四”字型设置带驱动电机的滚床,夹具台车在滚床上储存,在滚床的两端设有可横向移动的台车载运装置,实现台车的车型选择。
台车升降转换系统的功能是将工作完成后空的台车上载到空中平台的储存区、同时将从储存区选择出的空台车下载至生产线上。
(其基本结构如图2所示)图2 夹具台车储存及运行系统、可旋转式的车身主合成夹具对于焊装线来讲,最关键的工序就是车身主合成夹具,它是每一种车型的核心,它的功能是要将不同车型车身的地板总成、左右侧围总成、CRP总成在同一个合成工位完成拼焊。
所以,为了在同一个主合成工位实现多品种车型的生产,本公司的做法是:将主合成夹具的左右侧围夹具设计在2个可旋转的多面体的不同面上,由伺服马达驱动实现往复回转,同时采用2台机器人实现左右侧围总成从空中自行小车运送线到回转夹具的转载;地板总成夹具设计在可循环移动的台车上;CRP总成夹具设计在可循环移送的空中自行小车的吊具上,这几组夹具通过PLC程序控制后实现车身的准确定位合成。
再由12台机器人共同完成该全成工位的焊接操作。
其多面体的回转面数量是根据生产纲领和车种数量来确定的,本公司目前1阶段(15万台,年、3车种)是选用的四面回转体结构,另外预留了2阶段需增设的另一组四面回转体安装位置。
(其基本结构如图3所示)图3 可旋转式的车身主全成夹具4、夹具台车循环移送系统夹具车台车循环移送系统比较适合于车身地板总成及车体总成的补焊线,该系统的结构是:若干个通用性台车分别设置于呈“回”排布的双轨道支承底座上,但台车上的所有车身定位支承均采用小型4面回转体结构,台车的移送结构与以上介绍的生产作业运行系统相同。
为了充分利用“回”形中间部分物流通道,在长度方向的两端空中设置平台,并且设置4组台车升降装置,实现空载,满载台车的转运。
目前在主焊线中使用这种台车的主要优点是:①利用台车搬送较容易在主焊线上实现多车种共线,原则上讲只要台车能装载何种车型,其就能通过主焊线进行生产;②台车搬送不会影响车体生产品质,不像其他搬送设备在搬送时的冲击对车体有不良的影响;③在车型更新时,设备重复利用率高;④台车可直接作为补焊站的定位夹具使用,来满足生产需要;⑤根据台车之编码能够较容易地实现车型的在线追踪。
(其基本结构如图4所示)图4 夹具台车循环移送系统但主焊线上的台车在实际应用时应注意如下几点:①台车结构在设计上应注意通用性,结构力求简单,尽可能轻量化;②台车在各工序到位时,应采用机械锁紧机构进行定位,并重点保证能满足机械手自动焊接时的位置精度要求;③在有精度特别要求的工位,车体位置不能单纯利用台车的定位,而应采用固定式夹具进行准确定位,以确保车体拼装质量;④在台车控制上应避免采用动力线等管路拖拽的形式。
5、自动化搬运设备、机器人应用为了实现焊装线的柔性化,各分总成线之间的物料传送多采用自动化搬运设备一空中自行性移送小车系统(EMS)、物料上下载装置。
运行轨道采用高强度铝合金材料,电力、通信采用滑触式,其自行小车运行平稳、噪音小;并在运行轨道的两端分别设置取放工件有升降机。