连铸方坯疏松缺陷
连铸坯质量缺陷

连铸坯的质量缺陷及控制摘要连铸坯质量决定着最终产品的质量。
从广义来说所谓连铸坯质量是得到合格产品所允许的连铸坯缺陷的严重程度,连铸坯存在的缺陷在允许范围以内,叫合格产品。
连铸坯质量是从以下几个方面进行评价的:(1)连铸坯的纯净度:指钢中夹杂物的含量,形态和分布。
(2)连铸坯的表面质量:主要是指连铸坯表面是否存在裂纹、夹渣及皮下气泡等缺陷。
连铸坯这些表面缺陷主要是钢液在结晶器内坯壳形成生长过程中产生的,与浇注温度、拉坯速度、保护渣性能、浸入式水口的设计,结晶式的内腔形状、水缝均匀情况,结晶器振动以及结晶器液面的稳定因素有关。
(3)连铸坯的内部质量:是指连铸坯是否具有正确的凝固结构,以及裂纹、偏析、疏松等缺陷程度。
二冷区冷却水的合理分配、支撑系统的严格对中是保证铸坯质量的关键。
(4)连铸坯的外观形状:是指连铸坯的几何尺寸是否符合规定的要求。
与结晶器内腔尺寸和表面状态及冷却的均匀程度有关。
下面从以上四个方面对实际生产中连铸坯的质量控制采取的措施进行说明。
关键词:连铸坯;质量;控制1 纯净度与质量的关系纯净度是指钢中非金属夹杂物的数量、形态和分布。
夹杂物的存在破坏了钢基体的连续性和致密性。
夹杂物的大小、形态和分布对钢质量的影响也不同,如果夹杂物细小,呈球形,弥散分布,对钢质量的影响比集中存在要小些;当夹杂物大,呈偶然性分布,数量虽少对钢质量的危害也较大。
此外,夹杂物的尺寸和数量对钢质量的影响还与铸坯的比表面积有关。
一般板坯和方坯单位长度的表面积(S)与体积(V)之比在0.2~0.8。
随着薄板与薄带技术的发展,S/V可达10~50,若在钢中的夹杂物含量相同情况下,对薄板薄带钢而言,就意味着夹杂物更接近铸坯表面,对生产薄板材质量的危害也越大。
所以降低钢中夹杂物就更为重要了。
提高钢的纯净度就应在钢液进入结晶器之前,从各工序着手尽量减少对钢液的污染,并最大限度促使夹杂物从钢液中排除。
为此应采取以下措施:⑴无渣出钢。
减少方坯连铸脱方缺陷的途径
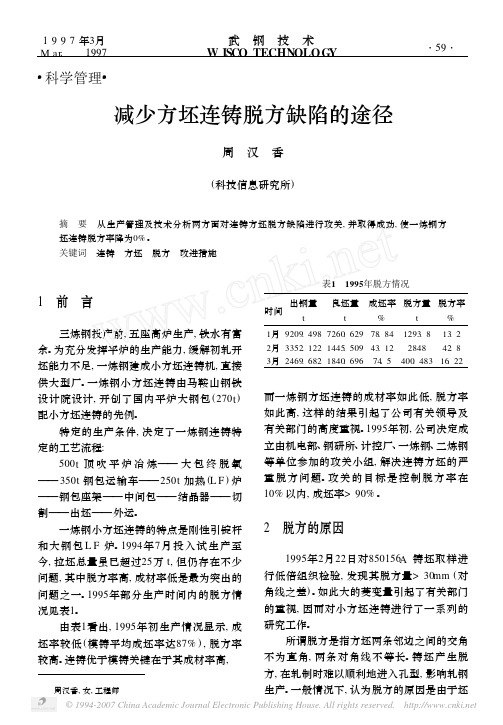
注: 因场地限制, 这几个月铸坯以抽样方法检查, 一罐 抽检8根铸坯, 若不合格则整罐钢判废, 因而影响了 成坯率。
陷。
3. 4 拉速的控制 针对方坯连铸拉速过快, 拉速变化幅度
大、频率大的问题, 经过攻关, 制定了拉速极
由表3所列数据可见, 攻关产生了效果, 7 月份脱方率下降为0% , 一炼钢小方坯连铸的 脱方问题得到了解决。
下降到2. 86% , 成坯率上升到88. 83%。 3. 5 保护渣的改进
坯脱方缺陷, 为连浇、20M nSi 连铸方坯试制 及热装热送创造了条件。
保护渣对脱方的影响不是直接的。但保
(下转第49页)
© 1994-2007 China Academic Journal Electronic Publishing House. All rights reserved.
1 9 9 7 年3月 M a r. 1997
科学管理
武 钢 技 术 W ISCO TECHNOLO GY
减少方坯连铸脱方缺陷的途径
周 汉 香
(科技信息研究所)
·5 9 ·
摘 要 从生产管理及技术分析两方面对连铸方坯脱方缺陷进行攻关, 并取得成功, 使一炼钢方 坯连铸脱方率降为0%。 关键词 连铸 方坯 脱方 改进措施
攻关措施的采用, 基本上解决了脱方问
3. 3 钢水浇注温度的控制
题, 1995年3月17日取650192A 废坯一段进行
影响铸坯脱方的因素包括钢液的过热 低倍组织检验, 测量其各边长大致相同, 计算
度。适当的浇注温度是保证铸坯不脱方的重 脱方量为0。1995年实施攻关措施以来生产的
要条件之一。
成坯率、脱方率见表3。
周汉香, 女, 工程师
《连铸方坯低倍组织缺陷评级图》标准浅析
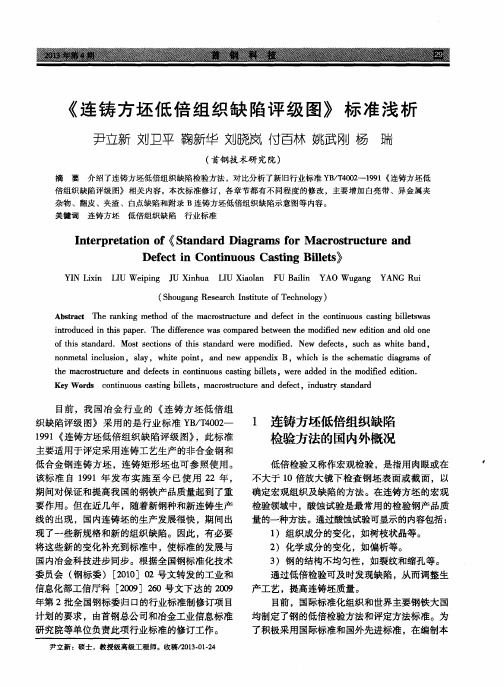
信息化部工信厅科 [ 2 0 0 9 ]2 6 0号文下达的 2 0 0 9 年第 2批全国钢标委归 口的行业标准制修订项 目 计划 的要求 ,由首钢总公 司和冶金工业信息标准 研究院等单位负责此项行业标准的修订工作。
t h e ma c r o s t r u c t u r e a n d d e f e c t s i n c o n t i n u o u s c a s t i n g b i l l e t s ,w e r e a d d e d i n t h e mo d i f i e d e d i t i o n .
目前 ,我 国冶金行业 的 《 连铸方坯低倍 组 织缺陷评级图》采用 的是行业标准 Y B / T 4 0 0 2 -
1 9 9 1《 连铸方坯低倍组织缺陷评级 图》 ,此标准 主要适用于评定采用连铸工艺生产 的非合金钢和
低合金钢连铸方坯 ,连铸矩形坯 也可参 照使 用。
1 连铸 方坯低倍组织缺陷 检验 方法的国 内外概况
o f t h i s s t a n d a r d . Mo s t s e c t i o n s o f t h i s s t a n d a r d we r e mo d i i f e d . Ne w d e f e c t s ,s u c h a s wh i t e b a n d , n o n me t a l i n c l u s i o n, s l a y , wh i t e p o i n t ,a n d n e w a p p e n d i x B,wh i c h i s t h e s c h e ma t i c d i a g r a ms o f
211172579_连铸方坯的常见表面缺陷及控制

管理及其他M anagement and other连铸方坯的常见表面缺陷及控制康旭辉摘要:连铸方坯表面的质量直接影响材料轧制后成品的质量,而近年来,我国部分企业在连铸方坯生产的过程中,存在诸多的表面缺陷问题,不能确保生产的质量和效果。
基于此,本文分析连铸方坯常见表面缺陷问题,提出几点表面缺陷控制的建议和措施,旨在为增强连铸方坯的表面质量提供帮助。
关键词:连铸方坯;常见表面缺陷;控制全面掌握方坯缺陷的类型、形成机理和消除途径是方坯质量控制的关键。
目前,国内外钢铁企业在钢坯质量控制方面取得了可喜的成绩,并获得了大量的生产数据和实际操作经验。
全面提高方坯质量,对提高连铸方坯成品率、改善钢材质量、节能降耗、降低成本具有重要意义。
连铸钢属于直接浇注钢水的工艺。
它的出现从根本上改变了主导了一个世纪的钢锭开坯过程。
液态金属连铸钢的概念早在19世纪中叶就被提出。
1840年,美国的销售商获得了连铸铅管的专利。
1846年,转炉的发明者贝塞默使用水冷旋转双辊连铸机生产锡箔、铅板和玻璃板。
1872年,David提出了移动式结晶器连铸的概念。
1886年~1889年,提出了立式连铸机的设计方案。
1921年,皮尔逊提出了结晶器振动的概念,即结晶器振动使板坯和结晶器之间连续的相对运动。
1933年,连铸的先驱德国准噶斯人建造了第一台1700t/月振动结晶器立式连铸机。
20世纪30年代,第一个成功铸造铜铝合金的有色金属连铸应用于生产。
目前,部分企业在连铸方坯生产的过程中,方坯表面的质量波动幅度很高,存在脱方缺陷、凹陷,缺陷和渣沟缺陷等,不能确保整体结构表面质量符合标准要求,对特钢产品生产质量造成一定的危害,因此,在连铸方坯实际生产的过程中需结合具体表面缺陷问题的发生原因与实际情况,采用有效的措施进行控制,确保连铸方坯表面质量符合标准规范,为特钢产品高质量生产夯实基础。
1 连铸方坯的常见表面缺陷和发生原因1.1 渣沟缺陷与原因从实际情况而言,连铸方坯表面出现渣沟缺陷问题,轧制以后线材表面出现裂纹缺陷问题的发生存在直接联系,从表面观察可以发现坯件有纵向贯通性的沟状缺陷问题,具体是在连铸方坯的内弧部分分布,很小一部分会在侧弧的位置,采用跟踪性轧制12.5mm绞丝钢实验的方式,可以发现线材的表面存在裂纹问题。
方坯铸坯缺陷产生原因及预防措施

方坯铸坯缺陷产生原因及预防措施1.前言由于连铸坯质量问题多发于连铸,因此对连铸质量缺陷进行了分析,总结出发生原因,以减少连铸坯质量问题的发生。
2.铸坯主要有以下几种缺陷:2.1卷渣2.1.1表面卷渣(见图1)2.1.2内部卷渣(见图2)图1 图22.2裂纹2.2.1表面裂纹:头部表面裂纹(图3 )、尾部表面裂纹(见4)。
图3 图42.2.2内部裂纹(见图5)图52.3气泡缺陷(见图6、见图7)图6 图73、缺陷产生原因及预防措施3.1卷渣产生原因及预防措施3.1.1表面卷渣产生原因及预防措施产生原因:(1)结晶器内形成渣条,当结晶器内钢液面波动量大于熔渣层厚度时、或挑渣条未挑净时、或在挑渣条过程中将渣条带入结晶器坯壳上时形成卷渣。
(2)在换包或等包降速过程中,由于操作不当造成中包液位较浅,导致中包内钢液形成涡流将中包渣卷进结晶器内,在上浮过程中被坯壳捕作形成卷渣。
(3)调整渣线高度超过液渣层厚度、或有渣条未挑净、等原因时造成颗粒渣被卷到坯壳上而形成卷渣。
(4)在开浇升速前液渣厚度未达到标准,造成颗粒渣或予熔层的保护渣直接与钢液接触,升速过程中在结晶器内造成钢液面发生波动,导致保护渣被卷入到坯壳上,形成卷渣。
(5)中包掉料或有杂物,开浇过程中被钢水冲到结晶器内,从而形成卷渣。
(6)中包内钢液面剧烈波动时,造成中包内覆盖剂被卷入中包钢液中,此时被卷入的覆盖剂受两个力作用:向上的钢水的浮力和向下的钢流股吸力作用,当向下的钢流股吸力大于向上钢水的上浮力时,卷入的覆盖剂就被卷入到结晶器内,在钢流流股的作用下,如被坯壳捕作而形成皮下卷渣,如被向下流股带入液相穴深处而形成内部卷渣。
(7)挑渣条用8#钢线(或细铁线),在钢线上结钢瘤或渣块,有钢瘤的8#线熔断到结晶器钢液内部,如被坯壳捕作到而形成皮下卷渣,如进入液相穴深处而形成内部卷渣。
(8)拉速波动,特别是在升速或降速过程,由于拉矫机电机转速发生变化,从而造成结晶器液面波动,从而形成渣条,形成的渣条被卷入结晶器坯壳上形成卷渣。
连铸板坯和方坯表面缺陷的分析与判定

连铸板坯和方坯表面缺陷的分析与判定在钢板、板卷、棒材、型钢上的裂纹和其他等缺陷,大多源于板坯和方坯上的缺陷。
大多数钢厂面临的最大挑战是缺乏如何判定、检查这些缺陷及相应地采取何种对策。
令人遗感的是,目前很多钢厂在遇到表面缺陷问题时所做的一些措施并不恰当,甚至没有对板坯和方坯进行检测分析便作出相应的判定和措施。
板坯和方坯的表面缺陷类型板坯和方坯上的所有表面缺陷几乎可以被分成五大类,并且在世界上大多数铸机上它们的发生位置基本上也是可以预测的。
基于经验,按照发生概率的大小顺序列出了五大类缺陷,即针状气孔/疏松、裂纹、深度振痕、不良清理、结晶器壁污染和刮伤等。
依据加热炉的氧化条件,可以确定板坯和方坯表面缺陷的临界深度,从而判定缺陷是否最终会成为板材、板卷或棒材上的轧制表面缺陷。
大部分加热炉操作会导致1%~2%厚度的铸坯氧化成氧化铁皮。
如果铸坯的厚度为220mm,就意味着在加热过程中会造成2.2mm~4.4 mm的厚度损失。
这个厚度损失同样会传递到表面缺陷。
如果铸坯表面缺陷的深度小于铸坯厚度的1%~2%,那么这些缺陷将在加热过程中稍除。
而那些比成为氧化铁的1%~2%厚度更深的缺陷,最终会造成轧材的表面缺陷。
针状气孔/疏松在所有铸机上。
针状气孔/疏松几乎都是常见的,也是最容易被忽略的铸坯缺陷。
如果钢中的气体得不到合理控制,就会在板坯和方坯表面上产生针状气孔/疏松。
当凝固率达到90%而气体总压力Ar+H2+N2+CO+CO2>1atm时,针状气孔/疏松就会在板坯和方坯表面上形成。
找出表面和皮下针状气孔/疏松的形成原因并不困难。
在实际生产中,皮下通常是指表面以下10mm的深度。
根据经验,针状气孔/疏松是影响钢板、板卷表面质量的最突出问题。
举一个板坯上的针状气孔/疏松的例子,钢种是V和Nb复合微合金化的A572 Gr50结构钢,含0.15%C,在铸坯上角部出现针状气孔/疏松,导致14.3mm厚的成材的上边部出现缺陷。
小方坯脱方缺陷产生的原因及采取措施

小方坯脱方缺陷产生的原因及采取的措施现如今,人们对于任何生产过程中的生产效率和生产安全是尤为关注的,不管是在什么生产过程中,它都是存在的。
在我们冶金生产过程中,有着许许多多的问题等着我们一个个的去解决,小方坯脱方就是其中的一个,对于小方坯脱方,他是在方坯连铸生产过程中很常见的,对于它的危害,是有目共睹的。
小方坯脱方是方坯连铸常见的质量缺陷,它的形成是钢水在结晶器内不均匀冷却,初生坯壳厚度不均匀造成的,同时受其他多种因素综合影响的结果,方坯的脱方是方坯横断面上俩条对角线的长度不等,脱方的方坯连铸在生产过程中很常见,它不但影响下道轧制工序中轧机的咬入,造成轧制困难,而且常伴有角部纵向裂纹和面部纵向裂纹,严重还发生漏钢事故,由于脱方的普遍性和严重性,对于它的一些具体产生的原因以及如何才能有效的采取措施来减少或者是尽可能的避免它的发生,是我们现在应该所关注的。
对于小方坯脱方,我们首先来了解下钢水在结晶器内的凝固特性,将钢水注入结晶器,钢水与铜壁接触形成一个半径很小的弯月面,在弯月面得根部,由于冷却速度很快(100℃/s),凝固生成生坯壳。
正形成的初生坯壳由于发生δ→γ相变而收缩,使坯壳脱离铜壁,形成气隙。
而钢水静压力又使坯壳向外膨胀。
此时坯壳的收缩力与钢水的静压力处于动态平衡。
随着坯壳的下移,坯壳表面开始回热,坯壳温度身高,强度变低,钢水的静压力使得坯壳变形。
在结晶器的角部区域,由于是二维传热,坯壳凝固最快,收缩最早,气隙首先形成,随后传热减慢,推迟了凝固。
随着坯壳的下移,气隙从角部扩展到中心。
铸坯面部中心部位的气隙比角部小,角部坯壳热流量最小,坯壳较薄,在钢水静压力的做一下,容易产生变形。
脱方缺陷的形成有两种理论, 一种认为脱方与坯壳的四个面凝固不均匀有关, 另一种认为脱方与坯壳的四个角凝固不均匀有关。
这两种理论的共同点是脱方都是在结晶器内热流最大的地方, 由于坯壳凝固不均匀形成的。
脱方是结晶器内铸坯四个角部不均匀冷却所致。
连铸坯产生质量问题的原因
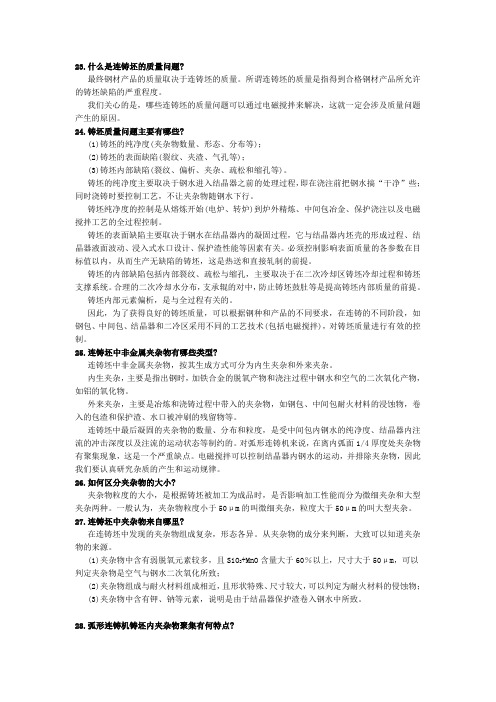
23.什么是连铸坯的质量问题?最终钢材产品的质量取决于连铸坯的质量。
所谓连铸坯的质量是指得到合格钢材产品所允许的铸坯缺陷的严重程度。
我们关心的是,哪些连铸坯的质量问题可以通过电磁搅拌来解决,这就一定会涉及质量问题产生的原因。
24.铸坯质量问题主要有哪些?(1)铸坯的纯净度(夹杂物数量、形态、分布等);(2)铸坯的表面缺陷(裂纹、夹渣、气孔等);(3)铸坯内部缺陷(裂纹、偏析、夹杂、疏松和缩孔等)。
铸坯的纯净度主要取决于钢水进入结晶器之前的处理过程,即在浇注前把钢水搞“干净”些;同时浇铸时要控制工艺,不让夹杂物随钢水下行。
铸坯纯净度的控制是从熔炼开始(电炉、转炉)到炉外精炼、中间包冶金、保护浇注以及电磁搅拌工艺的全过程控制。
铸坯的表面缺陷主要取决于钢水在结晶器内的凝固过程,它与结晶器内坯壳的形成过程、结晶器液面波动、浸入式水口设计、保护渣性能等因素有关。
必须控制影响表面质量的各参数在目标值以内,从而生产无缺陷的铸坯,这是热送和直接轧制的前提。
铸坯的内部缺陷包括内部裂纹、疏松与缩孔,主要取决于在二次冷却区铸坯冷却过程和铸坯支撑系统。
合理的二次冷却水分布,支承辊的对中,防止铸坯鼓肚等是提高铸坯内部质量的前提。
铸坯内部元素偏析,是与全过程有关的。
因此,为了获得良好的铸坯质量,可以根据钢种和产品的不同要求,在连铸的不同阶段,如钢包、中间包、结晶器和二冷区采用不同的工艺技术(包括电磁搅拌),对铸坯质量进行有效的控制。
25.连铸坯中非金属夹杂物有哪些类型?连铸坯中非金属夹杂物,按其生成方式可分为内生夹杂和外来夹杂。
内生夹杂,主要是指出钢时,加铁合金的脱氧产物和浇注过程中钢水和空气的二次氧化产物,如铝的氧化物。
外来夹杂,主要是冶炼和浇铸过程中带入的夹杂物,如钢包、中间包耐火材料的浸蚀物,卷入的包渣和保护渣、水口被冲刷的残留物等。
连铸坯中最后凝固的夹杂物的数量、分布和粒度,是受中间包内钢水的纯净度、结晶器内注流的冲击深度以及注流的运动状态等制约的。
- 1、下载文档前请自行甄别文档内容的完整性,平台不提供额外的编辑、内容补充、找答案等附加服务。
- 2、"仅部分预览"的文档,不可在线预览部分如存在完整性等问题,可反馈申请退款(可完整预览的文档不适用该条件!)。
- 3、如文档侵犯您的权益,请联系客服反馈,我们会尽快为您处理(人工客服工作时间:9:00-18:30)。
连铸方坯疏松缺陷
疏松是连铸方坯凝固组织中一种常见的内部缺陷,多发生在连铸坯中心,如果将连铸坯沿中心线剖开,就会发现其中心附近有许多细小的空隙,这些小孔隙即为中心疏松。
还有些疏松在连铸坯断面呈现出不规则分布的点,俗称为锈斑。
在铸坯轧制压缩比为3~5时,低等级中心疏松可以焊合,对成品性能并无危害。
但对于大等级的疏松,会造成轧制过程中对产品产生裂纹或者是轧制断裂,对轧钢工序危害甚大。
一、中心疏松形成过程
除了极少数金属以外,收缩是凝固过程伴随的必然现象。
凝固收缩是否会导致疏松的形成与凝固条件有关。
凝固收缩若能得到液相的及时补充则可防止疏松的形成,凝固过程中的补缩通道是否畅通是决定疏松形成的关键因素。
中心疏松是铸坯两面的柱状晶向中心生长,碰到一起造成“搭桥”,阻止了桥上面的钢水向桥下面钢液凝固收缩的补充,当桥下面钢水全部凝后,就留下了许多小孔隙。
二、影响连铸方坯疏松的因素
1、拉速的影响。
2、钢种对疏松的影响。
3、疏松与温度的关系。
4、二次冷却方式的影响。
三、预防措施
1、对于不同钢种采取不同的拉速限制措施。
2、不同钢种采用不同的配水制度。
3、降低钢水过热度。
4、采用二冷气水雾化冷却。
5、采用电磁搅拌工艺改善铸坯疏松。
四、结论
(1)中心疏松是铸坯两面的柱状晶向中心生长,碰到一起造成“搭桥”形成;凝固理论表明,凝固区间越大,枝晶越发达,被封闭的残余液相就越多,形成的缩孔就越严重。
(2)实践中,减少铸坯疏松的主要措施为:针对不同钢种采取适当的拉速限制措施;优化二冷配水制度;合理控制H08终点氧位;中间包钢水过热度控制在20~30 ℃之间。
(3)二冷采用气水雾化冷却,中心疏松可控制在0 . 5级,而喷水冷却中心 1 . 5级。
(4)对于结晶器电磁搅拌的150 mm小方坯,采用360~400A电流、4HZ频率,中心疏松一般在0 . 5~1 . 0级以下。