小方坯连铸机工艺培训课件
连铸机设备PPT幻灯片课件
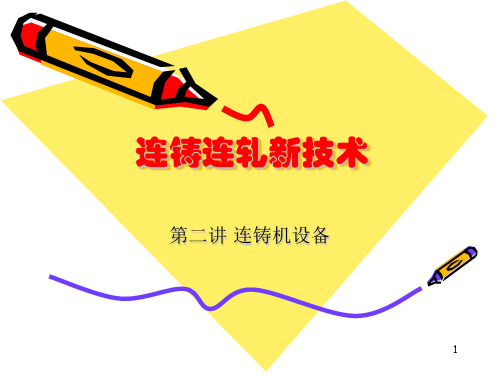
长水口又称保护套管,用于钢包与中间包之间保护 注流不被二次氧化,同时也避免了注流的吸气、飞溅以 及敞开浇注的卷渣问题。
图2-4 长水口保护装置 (a)卡口型;(b)液压型;(c)叉型 1一钢包;2一氩气;3~钢水;4一中间包;5一浇注位置
19
钢包回转台
图2-5 钢包回转台 (a)直臂式;(b)双臂单独升降式;(c)带钢包加盖功能 钢包回转台是现代连铸中应用最普遍的运载和承托钢包进行浇 注的设备,通常设置于钢水接受跨与浇注跨柱列线之间。钢包回转 台能够在转臂上同时承放两个钢包,一个用于浇注,另一个处于待 浇状态。
2
2.1.2 弧形、椭圆形连铸机的表示方法
连铸机的规Leabharlann 表示如下: aRb—c这里:a——机数,若其数为1,则可省略; R——机型为弧形或椭圆形连铸机; b——连铸机的圆弧半径,m;若椭圆形连铸机
为多个半径之乘积,也标志可浇铸坯 的最大厚度; c ——表示拉辊坯辊身长度,mm,它标志着连
铸机可容纳的连铸坯的最大宽度。 B=C-(150~200)mm
1一钢包注流位置;2一中间包水口位置;3一挡渣墙
21
中间包车结构有哪些特点?
中间包车是承载和运送中间包的特殊车辆,根据工艺操作要求,中间包车 必须具备如下功能:
(1)将中间包由预热位置移到浇钢位置上,在浇钢结束后还应移出浇钢位置, 因此中间包车应具有运行功能; 。
(2)在安放中间包时,首先将中间包提起,使水口离开结晶器盖一定高度后 再进入浇钢位置,下降中间包,使水口对准结晶器中心,因此它应具有升降和 微调功能;
内壁之间的滑动摩擦,因此结晶器内壁的材质应有良好的耐磨性和较高的再结晶 温度。 (5)重量要轻,以减少振动时的惯性力。为提高铸坯表面质量,结晶器的振动广 泛采用高频率小振幅,最高已达4 00次/min,在高频振动时惯性力不可忽视, 过大的惯性力不仅影响到结晶器的强度和刚度,进而也影响到结晶器运动轨迹的 精度。
小方坯连铸机工艺培训课件 (2)

精心整理方坯连铸工艺培训课件一、方坯连铸工艺流程简图二、方坯连铸基本参数铸坯断面:150×150mm定尺长度:6~12m(实际最短生产过9.25的,拉速2.1m/min)55Q4.1钢包汇总台4.1钢包回转台功能支承钢包并将满包从受包位旋转到中间罐上方的浇4.2中间罐功能保证连浇;均匀分配钢流到结晶器;促使夹杂物上浮。
结构型式中间罐为梯形带盖式,主要技术参数中间罐最大容量20t钢水液面高度工作液面:800mm主要技术参数烘烤时间180min烘烤温度~1000℃4.5结晶器功能将钢水凝结成型,使浇入其中的钢水快速冷却。
在引锭头拉出结晶器铜管后,凝结的钢水坯壳能承受内部还未凝固的钢水静压力。
结构型式结晶器为套管式,主要由内壁镀铬的三维立体锥度铜管、精密加工成型的整体铜水套、钢结构外壳、上下法兰、卡板及密封件等部分组成。
铜管材质为磷脱氧铜。
主要技术参数铜管长度900mm托架等组成,喷淋管沿弧线纵向布置。
主要技术参数冷却段数3(含喷淋环)喷淋管长度~4.5m喷嘴型号3/8PZ17080QZ5*12PZ8065QZ5*28PZ8047QZ5*284.8导向段功能开浇时引导引锭杆进入结晶器并在浇铸时支承铸坯。
结构型式导向段位于喷淋集管组与拉矫机之间,主要由导向辊、支座、侧导辊、压辊及侧导板等组成。
功能开浇时引锭头堵住结晶器下口,把初步凝固的铸坯拉出结晶器,引入拉矫机。
结构型式主要由自适应型引锭头、刚性杆身、链条及联接件、传动系统、导向轮及安全装置所组成。
铸机开浇前,启动存放装置电动机使引锭杆下降至拉矫机内。
引锭结束后,引锭杆运行至存放位置。
主要技术参数引锭杆外弧半径R8m引锭杆长度(弧度)~87°送引锭杆速度1~4.0m/min4.11切前/输送/出坯辊道坯。
主要技术参数行程~20000mm(工作行程)轨距~13000mm轮距/轮径~2100mm/D300mm4.13翻转冷床功能翻转冷却铸坯,防止铸坯变形结构型式冷床为液压传动、步进翻转式。
(ppt版)连铸工艺技术培训课程

律调查的根底上,根据每个钢种所要经过的工艺路线
(lùxiàn)来确定。
第十六页,共七十页。
㈢ 钢水温度控制要点 1、出钢温度控制: ①提高终点温度命中率
②确保从出钢到二次精炼( jīngliàn)站,钢包钢水温度处于目 标范围之内
2、充分发挥钢包精炼的温度与时间的协调作用
3、控制和减少从钢包到中间包的温度损失
(0.5~1.2℃/min〕;
△T5 钢水从钢包注入中间包的温降。
第十页,共七十页。
• 1温、降△T1 钢水从炼钢炉的出钢口流入钢包(gāngbāo)这个过程的 分析:
• 热量损失形式:钢流辐射热损失、对流热损失、钢包吸热 。
• 影响因素:出钢时间、出钢温度及钢包的使用状况。 • 降低热量损失的措施:
③非金属夹杂不易上浮,影响铸坯内在质量。
第六页,共七十页。
第二节 中间包钢水温度(wēndù)的控制
一、浇铸温度(wēndù)确实定 〔浇铸温度也称目标浇铸温度〕:
T浇=TL+△T 式中: TL——液相线温度
△T ——钢水过热度
第七页,共七十页。
1、液相线温度TL
液相线温度,即开始凝固(nínggù)的温度, 就是确定浇铸温度的根底。推荐一个计算 公式:
第五节 连铸过程检测(jiǎn 与自动 cè) 控制
• 一、连铸过程(guòchéng)自动检测
〔一〕中间(zhōngjiān)包钢液温度测定
1、中间包钢液温度的点测
第二十九页,共七十页。
用快速测温头
及数字显示二次 仪测量(cèliáng)温 度。
第三十页,共七十页。
2、中间(zhōngjiān)包钢液温度的连续测定
第四十三页,共七十页。
小方坯连铸机工艺培训课件样本

方坯连铸工艺培训课件一、方坯连铸工艺流程简图二、方坯连铸基本参数铸坯断面: 150×150mm定尺长度: 6~12m( 实际最短生产过9.25的, 拉速2.1m/min) 主要生产钢种: 碳素结构钢、低合金结构钢。
55Q ( 轻轨钢) Q195( 碳素结构钢, 建筑, 结构, 摩托车架)热轧带肋钢筋 HRB335/335E ( 二级) HRB400/400E ( 三级) HRB500/500E ( 四级) Q235 ( 普碳钢, 建筑、化工)三、主要经济技术指标15 铸机设备生产能力1×120万t/a连铸机主要设备性能4.1 钢包汇总台4.1 钢包回转台功能支承钢包并将满包从受包位旋转到中间罐上方的浇铸位。
结构型式直臂式。
主要由回转臂、回转支承系统、回转台底座、基础框架、传动装置及钢包加盖装置等部分组成。
主要技术参数双臂最大承重 2×125t回转半径 4.9m回转速度 0~1.0r/min回转范围 360度事故回转180度4.2 中间罐功能保证连浇; 均匀分配钢流到结晶器; 促使夹杂物上浮。
结构型式中间罐为梯形带盖式,主要技术参数中间罐最大容量 20t钢水液面高度工作液面: 800mm溢流液面: 900mm4.3 中间罐车功能支承中间罐, 并运载中间罐在烘烤位和浇铸位之间移动。
结构型式半悬挂( 高低腿) 式。
主要由车架、走行机构、横移机构、摆槽、液压升降机构及驱动系统等主要技术参数最大承载重量 60t走行速度 0~20m/min横移行程±50mm升降行程 500mm4.4 中间罐烘烤(干燥)装置资料内容仅供您学习参考,如有不当或者侵权,请联系改正或者删除。
功能加热( 预热) 中间罐, 降低第一包钢水的温降。
结构型式中间罐烘烤(干燥)装置由支座、风机、电液推杆、管件、阀门、烧嘴等组成。
主要技术参数烘烤时间 180 min烘烤温度~1000℃4.5 结晶器。
方坯连铸机设备规程培训(设备概述部分)
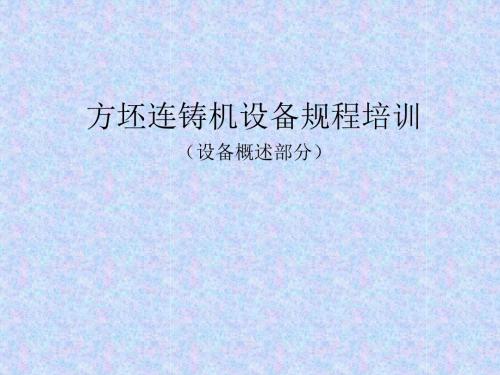
功能及结构
• 液压步进冷床主要由活动齿条、固定齿条、 传动装置、连杆、横梁、支架等组成。液 压动力来自出坯液压站。 • 收集台架由支架、导轨、推头等组成,传 动装置与步进冷床共用。
移坯车
• • • • • • • • 1). 技术参数 结构形式: 双向移坯,行走为齿轮齿条传动 移坯车工作行程: ~22000mm 轨距: ~14250mm 轮距/轮径: 2500mm/400mm 移坯车运行速度: ~18m/min 行走电机功率: 30kW 拨爪升降电液推杆电机: 3kW
功能及结构
中间罐车
• • 1). 技术参数 • 中间罐车型式全悬挂、液压升降式中间罐车数量 四台(四流采用一台车,两两对称布置)载荷能 力75t(罐+盖+钢水+塞棒机构)小车走行方式变 频电机传动(每台车2台电机)电机功率5.5kW/ 台走行速度1~14.8m/min(可调)升降方式液压 传动(每台车两个升降缸)升降行程500毫米横 向微调方式液压传动(每台车两个缸)
出坯辊道及翻钢机
• 1). 技术参数 • 出坯辊道:结构型式四流长辊子,每辊单 独传动辊径×辊身长度315×4750mm辊 面线速度~30 m/min辊子间距~1200mm辊 子数量8×2个传动装置齿轮减速电机(辊 道电机~2.2kW/台)轴承润滑集中干油润 滑
功能及结构
• 出坯辊道将铸坯送到固定挡板,让铸坯停 止。出坯辊道采用长辊子(每四流长辊), 集中传动
方坯连铸机设备规程培训
(设备概述部分)
钢包回转台
• 1). 技术参数 • 结构型式蝶形单臂升降式双臂承重max. 2×200 t回转半径~5.5 m回转速度 0~1.0r/min回转角度360o任意驱动形式正 常-电机;事故-液压马达,电机~30 kW 升降机构液压缸,升降行程800mm,升降 速度1.2 m/min加盖机构升降、回转液压驱 动升降行程:~300 mm旋转角度:~90º 介 质连接电气、液压滑环
连铸工艺培训课件讲解
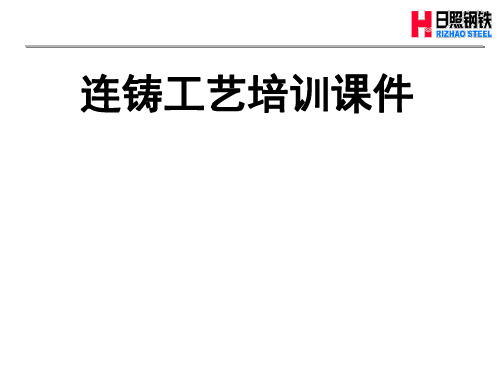
2.2、连铸的优越性
a、简化生产工序,缩 短工艺流程 b、提高综合成材率 c、降低能耗 e、易于实现机械自动化 f、扩大钢种,提高产品质量
弧形连铸机的几个重要参数
台数:凡是共用一个钢包同时浇注一流或 多流铸坯的一套连铸设备,称为一台连铸 机。 机数:具有独立的传动系统和工作系统, 当其他组出事故时仍照常工作的一组设备 称为一个机组。一台连铸机可由一机或多 多机组成。 流数:每台连铸机所能同时浇注铸坯的总 根数称为连铸机流数。
2007年4月1日原炼钢厂分设成立第一炼钢厂。目前,第一炼钢厂要生产优质碳素钢、冷 镦钢、焊接用钢、预应力钢棒、建筑用钢、船板用低合金高强度钢等,牌号标准有国标以外 的日标、欧标、英标、美标和韩标等。已经具备年产550万吨钢以上的生产能力。
1.2 炼钢工艺概述
1.2 炼钢工艺概述
炼钢厂的任务
铁水罐 混铁炉
Vmax=(Km/δmin)2 Lm 式中 Vmax—最大拉坯速度,m/min;
Lm —结晶器有效长度,mm; Km —结晶器内钢液凝固系数,mm/min1/2;结 晶器凝固系数可用经验公式Km=37.5/D0.11估算。 δmin—最大坯壳厚度,mm。
圆弧半径 用经验公式确定基本圆弧半径,也是连
t
最大拉坯速度
限制拉坯速度的因素主要是铸坯出结晶
器下口坯壳的安全厚度(最小坯壳厚度)。
对于小断面铸坯壳安全厚度为8~10mm;大
断面铸坯坯壳安全厚度不小于15mm。
根据凝固定律:δ=K凝
或
δ=K凝
t
L vC
式中 K凝—凝固系数,mm/min1/2;铸坯综合凝固系 数K凝为24~30 mm/min1/2。为保险起见,板坯 K凝取值较小,碳素钢K凝取28 mm/min1/2 ,弱钢冷 却钢种K凝取24~25mm/min1/2。 最大拉坯速度:
(四)连铸工艺与操作课件.ppt

三、连铸生产工艺
上引锭杆 开浇 启车拉矫 脱引锭杆 切割 钢包更换 中间包更换
精品
停车
1.上引锭杆
油缸驱动→引 锭杆放到中间轨道→ 送入拉矫机引锭杆经 二冷段→入结晶器上 100-150mm→ 反 向 至结晶器下口 150mm 处 → 拉 矫 机 引锭杆夹紧定位→完 成安装操作.
精品
2.开 浇
连铸连轧新技术
第二讲 连铸工艺与操作
精品
主要内容
一、概 述 二、生产模拟 三、生产工艺 四、连铸设备 五、工艺参数
精品
一、概 述 1.连铸的发展概况 2.连铸机的特点 3.连铸机的机型
精品
1.连铸的发展概况
连续铸钢(连铸)是将钢水通过连铸机直接铸成钢坯 ,从而取代模铸和初轧开坯的一种钢铁生产先进 工艺。世界各国都以连铸比(连铸坯产量占钢总产 量比例)的高低来衡量钢铁工业生产结构优化的程 度和技术水平的高低。连铸的好处在于节能和提 高金属收得率。
精品
弧型连铸机:
设备高度明显下降,能够 适应提高拉速和加大断面的要 求
又分为:
直弧型连铸机:
采用直结晶器从结晶器下 保留2m直线段,然后为弧型段, 铸坯由直变弯,最后通过拉矫机 将弧形坯矫直; 优点:夹杂物易上浮,且比立弯式 高度低;
全弧型连铸机:
铸坯的运动轨迹是一条弧 线.结晶器,二冷段全为弧型,拉 矫机、切割机和出坯系统布置 在水平线上.
连轧为代 表,钢厂向紧凑化发展。
精品
2、 21世纪钢铁工业发展趋势
(1) 产品更加纯洁化 (2) 生产工艺更加高效低耗 (3) 生产过程对环境更加友好
精品
•
连铸液体金属是19世纪提出的。最初只能用
于浇铸低熔点的有色金属。1933年现代连铸之父
连铸ppt-6-7

图3.1.水结晶冷却曲线 水结晶冷却曲线 1—水理论结晶曲线; 水理论结晶曲线; 2—水实际结晶曲线 水理论结晶曲线 水实际结晶曲线
(2)形核、长大(动力学条件) )形核、长大(动力学条件) 形核过程 A.均质形核,又称自发形核 液态金属中存在很多与固态金属结构相似、体积很小、 液态金属中存在很多与固态金属结构相似、体积很小、近程 有序排列的原子集团,在很大的过冷度(通常 通常∆T=(0.15~ 有序排列的原子集团,在很大的过冷度 通常 ~ 0.20)Tl, 实验室测定纯铁 实验室测定纯铁∆T=0.16Tl=295℃。)条件下,这些 条件下, ℃ 条件下 原子集团变成规则排列,并稳定下来而成为晶核,这一过程 原子集团变成规则排列,并稳定下来而成为晶核, 即为均质形核。 即为均质形核。 B.非均质形核,又称非自发形核,也称异质形核 又称非自发形核, 在金属液相中已存在的固相质点和表面不光滑的器壁均可作 为形成核心的“依托”而发展成初始晶核。 为形成核心的“依托”而发展成初始晶核。非均质形核需要 的过冷度则很小,只要过冷度到20℃就能形成晶核。 的过冷度则很小,只要过冷度到 ℃就能形成晶核。 钢液内部含有熔点不同的杂质, 钢液内部含有熔点不同的杂质,因此钢液的结晶主要为非均 质形核。
4.铸坯凝固冷却过程分为四个阶段: .铸坯凝固冷却过程分为四个阶段: 1)钢液在结晶器中快速冷却,形成薄的坯壳,坯壳与结晶 )钢液在结晶器中快速冷却,形成薄的坯壳, 器壁紧密接触,此时冷却较快,铸坯表面温度明显下降; 器壁紧密接触,此时冷却较快,铸坯表面温度明显下降; 2)随着凝固壳增厚,铸坯收缩,坯壳与结晶器壁间产生气 )随着凝固壳增厚,铸坯收缩, 隙,铸坯冷却速度减慢; 铸坯冷却速度减慢; 3)铸坯从结晶器中拉出,在二冷区受到强烈的喷水冷却, )铸坯从结晶器中拉出,在二冷区受到强烈的喷水冷却, 中心逐渐凝固; 中心逐渐凝固; 4)铸坯在空气中较缓慢的冷却,铸坯中心的热量传导给外 )铸坯在空气中较缓慢的冷却, 层使铸坯外层变热,表面温度回升。 层使铸坯外形成的细小等轴晶的基础上, 在已形成的细小等轴晶的基础上, 一些在散热方向上具有优先成长 方位的晶体将继续长大。 方位的晶体将继续长大。如果在 结晶前沿液相中成分过冷很大, 结晶前沿液相中成分过冷很大, 则晶体呈树枝状发展, 则晶体呈树枝状发展,从而形成 了大体上平行于散热方向的树枝 晶集合组织(柱状晶)。 晶集合组织(柱状晶)。
- 1、下载文档前请自行甄别文档内容的完整性,平台不提供额外的编辑、内容补充、找答案等附加服务。
- 2、"仅部分预览"的文档,不可在线预览部分如存在完整性等问题,可反馈申请退款(可完整预览的文档不适用该条件!)。
- 3、如文档侵犯您的权益,请联系客服反馈,我们会尽快为您处理(人工客服工作时间:9:00-18:30)。
小方坯连铸机工艺培训课件Document number:PBGCG-0857-BTDO-0089-PTT1998方坯连铸工艺培训课件一、方坯连铸工艺流程简图二、方坯连铸基本参数铸坯断面: 150×150mm定尺长度: 6~12m(实际最短生产过的,拉速min)主要生产钢种:碳素结构钢、低合金结构钢。
55Q (轻轨钢)Q195(碳素结构钢,建筑,结构,摩托车架)热轧带肋钢筋 HRB335/335E (二级)HRB400/400E (三级)HRB500/500E (四级) Q235 (普碳钢,建筑、化工)三、主要经济技术指标15 铸机设备生产能力1×120万t/a连铸机主要设备性能钢包汇总台钢包回转台功能支承钢包并将满包从受包位旋转到中间罐上方的浇铸位。
结构型式直臂式。
主要由回转臂、回转支承系统、回转台底座、基础框架、传动装置及钢包加盖装置等部分组成。
主要技术参数双臂最大承重 2×125t回转半径回转速度 0~min回转范围 360度事故回转 180度中间罐功能保证连浇;均匀分配钢流到结晶器;促使夹杂物上浮。
结构型式中间罐为梯形带盖式,主要技术参数中间罐最大容量 20t钢水液面高度工作液面:800mm溢流液面:900mm中间罐车功能支承中间罐,并运载中间罐在烘烤位和浇铸位之间移动。
结构型式半悬挂(高低腿)式。
主要由车架、走行机构、横移机构、摆槽、液压升降机构及驱动系统等主要技术参数最大承载重量 60t走行速度 0~20m/min横移行程±50mm升降行程 500mm中间罐烘烤(干燥)装置功能加热(预热)中间罐,降低第一包钢水的温降。
结构型式中间罐烘烤(干燥)装置由支座、风机、电液推杆、管件、阀门、烧嘴等组成。
主要技术参数烘烤时间 180 min烘烤温度~1000℃结晶器功能将钢水凝结成型,使浇入其中的钢水快速冷却。
在引锭头拉出结晶器铜管后,凝结的钢水坯壳能承受内部还未凝固的钢水静压力。
结构型式结晶器为套管式,主要由内壁镀铬的三维立体锥度铜管、精密加工成型的整体铜水套、钢结构外壳、上下法兰、卡板及密封件等部分组成。
铜管材质为磷脱氧铜。
主要技术参数铜管长度 900mm水缝 4mm水压~水量~2200 l/min结晶器振动装置功能支承结晶器并使其沿弧线方向上下振动,防止钢水凝固时与结晶器铜管内壁粘结。
结构型式采用板簧导向刚性支撑式。
主要由固定座、振动架、连杆、传动装置及润滑系统等部分组成。
主要技术参数振幅±3~4mm振动频率 35~333次/min振动负荷 25 kN喷淋集管组功能对出结晶器的初生铸坯进行二次冷却。
结构型式主要由不锈钢喷淋管、活接头、不锈钢喷嘴及托架等组成, 喷淋管沿弧线纵向布置。
主要技术参数冷却段数 3(含喷淋环)喷淋管长度~喷嘴型号 3/8PZ17080QZ5*12PZ8065QZ5*28PZ8047QZ5*28导向段功能开浇时引导引锭杆进入结晶器并在浇铸时支承铸坯。
结构型式导向段位于喷淋集管组与拉矫机之间,主要由导向辊、支座、侧导辊、压辊及侧导板等组成。
主要技术参数导向辊数 3导向辊直径 200 mm拉矫机(自同步连续矫直拉矫机)功能开浇时送引锭杆进入结晶器、拉坯并对铸坯进行矫直。
结构型式主要由拉坯辊、脱坯矫直辊、机架、底座、传动系统及液压系统等组成。
辊子为合金锻钢。
上下拉坯辊开口度大小及脱坯动作的完成由液压系统实现。
电动机通过长轴和减速机传动,远离热源。
机架及辊子内部通水冷却。
主要技术参数最大拉坯速度 min(送引锭)驱动辊数量 3引锭杆及引锭杆存放装置功能开浇时引锭头堵住结晶器下口,把初步凝固的铸坯拉出结晶器,引入拉矫机。
结构型式主要由自适应型引锭头、刚性杆身、链条及联接件、传动系统、导向轮及安全装置所组成。
铸机开浇前,启动存放装置电动机使引锭杆下降至拉矫机内。
引锭结束后,引锭杆运行至存放位置。
主要技术参数引锭杆外弧半径 R8m引锭杆长度(弧度) ~87°送引锭杆速度 1~min切前/输送/出坯辊道自动火焰切割机功能按需要的定尺长度切割铸坯(6~)。
结构型式主要由切割摆动装置、同步夹紧装置、框架、切割枪、凸轮机构、无动力返回系统和前后支架等组成。
主要技术参数切割速度~300 mm/min切割同步行程~1700 mm主要介质氧气、焦炉煤气双向移钢机功能将铸坯移至冷床或热送辊道。
结构型式主要由桥架、拨钢装置、运行轨道、车轮装置、缓冲装置、电动机、制动器及减速器等组成。
驱动装置通过桥架上的齿轮和轨道梁上的齿条带动桥架行走,桥架上的拨钢装置移送铸坯。
主要技术参数行程~20000mm(工作行程)轨距~13000mm轮距/轮径~2100mm/D300mm翻转冷床功能翻转冷却铸坯,防止铸坯变形结构型式冷床为液压传动、步进翻转式。
主要由横梁、纵梁、传动梁、前V形齿条、前U型齿条、床体盖板、液压缸、摇架、拉杆等组成。
出坯装置主要由轨道梁、纵梁、同步梁摇臂、拉杆、立柱、推头小车、滑轨、偏心轴等组成。
主要技术参数铸坯长度 8~12 m冷床大小 12×15 m特点液压驱动;由翻传冷床的传动装置通过拉杆、摇臂驱动推头小车进行推钢,将翻转冷床上的铸坯推放在出坯装置上,存放到一定数量后由出坯吊具吊走。
五、连铸坯质量连铸方坯的缺陷一般可分为表面缺陷、内部缺陷和形状缺陷。
表面缺陷包括:表面横裂纹、纵裂纹、星形裂纹、划伤、弯曲、切面不齐、缩孔、气孔等表面纵裂纹定义与外观沿拉坯方向,铸坯表面中心位置附近产生的裂纹,裂纹长10~1500mm,宽~,深<5mm。
在结晶器弯月面区(钢液面下170mm)左右,钢液凝固在固相线以下发生δ→γ转变,导致凝固厚度生产的不均匀性,由于热收缩使坯壳产生应力梯度,在薄弱处产生应力集中,坯壳在表面形成纵向凹陷,从而形成纵向裂纹原因:导致表面纵裂纹指数增加的因素有:(1)钢水成分SP含量高;(2) Mn/S降低;(3)[C]=~%;包晶反应钢δ→γ转变,收缩大,气隙形成,坯壳折皱,结晶器热流不稳定,坯壳厚度生产不均匀性加重;(4)拉速增加;(5)保护渣熔化性能不良、液渣层过厚或过薄导致渣膜厚薄不均,使局部凝固壳过薄。
液渣层厚度<10 mm;(6)结晶器液面波动≥5mm;(7)结晶器热流和冷却(8)结晶器锥度不合适;(7)结晶器钢液流动(9)水口不对中;(10)水口插入深度不合适。
(11)结晶器振动振痕深;表面横向裂纹定义与外观生成于铸坯面部的横向裂纹,简称为表面横裂纹。
与振痕共生,深度2~7mm,长度较短,一般在5~50mm之间,裂纹处常常被FeO覆盖。
产生于结晶器初生坯壳形成振痕的波谷处,振痕越深,则横裂纹越严重原因:(1)钢水成分◆[C]=~%,坯壳厚度生长不均匀性强,振痕深,表面易产生凹陷或横裂纹◆[N]含量高;(2)结晶器振动◆振痕深度增加◆负滑脱时间增加;(3)结晶器液面波动增加;(4)保护渣消耗量低,坯壳易与铜壁发生粘结;(5)二冷强度不合理,铸坯在脆性区矫直;(6)铸坯横向温差大,尤其是角部温度。
星形裂纹裂纹位于铸坯表面常被FeO覆盖,经酸洗后才能被发现,表面裂纹分布无方向性,形貌呈网状,深度可达1~4mm,有的甚至达20mm。
因及危害(1)铜渗漏:在结晶器下部,铜板渣层破裂,发生固/固摩擦接触,Cu局部粘附在坯壳上,Cu的熔点为1040℃,Cu熔化沿奥氏体晶界渗透,晶界被破坏而失去塑性,产生热脆。
(2)奥氏体晶界玷污:由于结晶器弯月面初生坯壳在张力和静压力的作用下奥氏体晶界裂开,固/液界面富集溶质的液体进入裂纹,加上晶界析出物,污染了晶界成为晶界薄弱点,是产生星状裂纹的起点。
(3)铸坯在运行过程中进一步受到张力作用(鼓肚、不对中、冷却不均匀等),裂纹进一步扩展。
(4)H2过饱和析出:当钢水中[H]>会出现网状裂纹废品,(5)晶间硫化物脆性:奥氏体晶界富集(Fe、Mn)S,熔点980~1000℃,晶界形成硫化物液体薄膜,在外力作用下形成网状裂纹。
表面夹渣定义与外观镶嵌于铸坯表面或皮下的渣疤称为夹渣。
形状不规则,深浅不一,嵌入较浅的夹渣可能被二冷水冲刷掉,在铸坯表面形成凹坑。
原因:(1)结晶器液面急剧波动,造成保护渣卷入并镶嵌于坯壳处。
(2)保护渣性能不良,渣条多,渣条未捞净,卷入并镶嵌于坯壳处。
(3)钢水夹杂物多,流动性不好,中包水口壁上高熔点的大块附着物突然脱落进入结晶器钢水。
夹渣部位坯壳薄,容易破裂导致漏钢;夹渣铸坯轧制后,钢材表面遗传为结疤。
划伤定义与外观沿浇铸方向,在铸坯表面出现连续或断续的沟槽状机械损伤,尤其在铸坯外弧、侧弧出现居多。
原因:(1)铸坯高温强度低。
(2)足辊、二冷段辊子、支座上粘有冷钢(尤其是漏钢造成的冷钢),造成铸坯被冷钢划伤。
(3)二冷段辊子、切前辊、切后辊不能正常运转,造成铸坯被辊子划伤。
(4)铸坯跑偏,被导槽划伤。
(5)拉矫辊表面有异物或不光滑。
脱方定义与外观当方坯横截面上两个对角线长度不相等时称为脱方。
成因及危害原因:(1)结晶器四面水缝厚度不均匀,坯壳冷却不均匀。
(2)结晶器水缝被异物堵塞,坯壳冷却不均匀。
(3)喷嘴堵塞,二冷区铸坯四个面冷却不均匀。
(4)钢水S高鼓肚定义与外观铸坯的凝固壳鼓胀成凸面,主要发生在铸坯的两个侧弧面,凸出最大可达15mm。
成因及危害(1)高温、高拉速。
(2)二冷强度不够,回温太快,凝固壳薄,受到内部钢水静压力的作用,产生鼓肚变形。
(3)拉矫机压下量过大。
弯曲定义与外观铸坯纵向不平直现象称为弯曲。
原因:(1)连铸事故造成卧坯,铸坯在二冷室停留时间过长,温低无法矫直。
(2)浇铸过程中铸坯冷却不均匀。
切面不齐定义与外观铸坯端面切割不平整、切斜严重或表面出现明显的切割沟槽称为切割不良。
成因及危害(1)割枪烧嘴角度安装不当。
(2)割枪的夹紧装置松动或脱落。
(3)燃气压力波动过大。
重接定义与外观铸流经短暂停浇后,中包水口再次开浇造成的铸坯重新连接。
铸坯重接部位渣钢混浇,常有钢筋连接,颜色异常,有明显的结痕。
成因及危害(1)连铸带杆操作。
(2)换浸入式水口。
(3)处理漏钢事故。
(4)结晶器液面波动过大。
缩孔定义与外观在连铸坯横断面中心位置附近出现直径大于3mm的孔洞,称为缩孔。
成因及危害(1)浇注温度高,钢液过热度大。
(2)拉速高。
(3)二次冷却强度控制不当。
(4)电磁搅拌参数不当。
气孔定义与外观位于铸坯表皮以下,直径和长度各在1mm和10mm以上的向柱状晶方向生长的大气泡叫皮下气泡,比气泡小呈密集的小孔叫皮下针孔。
若裸露在外面的叫表面气泡。
成因及危害(1)钢水脱氧不良。
(2)合金料、炉衬、包衬等潮湿,造成钢水中的气体含量高。
(3)塞棒吹氩时,氩气未即时排出残留在钢中。
在加热炉内,铸坯的表面气泡或皮下气泡内表面被氧化而形成脱碳层,轧制后不能焊合而形成表面缺陷。