连铸方坯的缺陷及其处理
连铸坯缺陷的产生与防止措施 Microsoft Word 文档1

连铸坯裂纹的产生与防止措施连铸坯裂纹的分类 :铸坯表面裂纹包括表面纵裂纹、表面横裂纹、网状裂纹(星裂)、发裂、角部纵裂纹、角部横裂纹等;铸坯内部裂纹包括中间裂纹、角部裂纹、中心线裂纹、三角区裂纹、皮下裂纹、矫直裂纹等。
1.1 铸坯表面裂纹部纵裂纹等几种主要的缺陷形式。
铸坯表面裂纹主要有表面纵裂纹、表面横裂纹、网状裂纹、角部横裂纹、边铸坯表面裂纹是在结晶器内产生的,在二冷段得到扩展。
它会导致轧制板材表面的微细裂纹,影响最终产品的表面质量。
图1为表面裂纹示意图图 1 铸坯表面裂纹示意图1-表面纵裂纹;2-表面横裂纹;3-网状裂纹;4-角部横裂纹;5-边部纵裂纹1.1.1 表面纵裂纹连铸坯表面纵裂纹是指沿着拉坯方向在铸坯表面上发生的裂纹。
它可由工艺因素或设备因素引起。
由工艺因素引起的纵裂,大多出现在铸坯宽面的中央部位,是表面裂纹中最常见的一种裂纹缺陷。
纵裂主要是由于初生坯壳在结晶器内冷却强度不均匀,造成应力的集中,在坯壳相对较薄的地方坯壳厚度不足以承受这种应力,致使坯壳裂开而产生裂纹,并在二冷区得到扩展,形成表面纵裂纹。
图2 图3 图4为表面纵裂纹示意图图2图3 图41.影响连铸坯表面纵裂纹因素:实际生产过程中,主要有以下因素影响连铸坯表面纵裂纹的产生:1) 成品成分及钢水质量(1) 成品钢中碳含量处在亚包晶和包晶反应区时,由于初生坯壳在结晶器弯月面内激冷时收缩较大,容易造成初生坯壳厚薄不均,从而使铸坯发生纵裂纹的倾向增加。
因此,在实际生产中各连铸厂家都尽量控制其成品钢中碳含量,使其避开亚包晶和包晶反应区,从而减少铸坯纵裂纹的发生机率。
(2) 成品钢中硫、磷含量也会影响铸坯纵裂纹的产生。
钢中硫、磷含量增加时,钢的高温强度和塑性明显降低,在应力作用下就容易产生裂纹,因此,在实际生产中各连铸厂家都尽量控制其成品钢中硫、磷含量,尽量控制在0.02%以内。
(3) 钢中微合金如铌、钒等对铸坯纵裂纹的产生也有重要影响,因为微合金而产生的铸坯纵裂纹在铸坯表面上分布不规则,缺陷较短、数量较多。
连铸坯质量缺陷

连铸坯的质量缺陷及控制摘要连铸坯质量决定着最终产品的质量。
从广义来说所谓连铸坯质量是得到合格产品所允许的连铸坯缺陷的严重程度,连铸坯存在的缺陷在允许范围以内,叫合格产品。
连铸坯质量是从以下几个方面进行评价的:(1)连铸坯的纯净度:指钢中夹杂物的含量,形态和分布。
(2)连铸坯的表面质量:主要是指连铸坯表面是否存在裂纹、夹渣及皮下气泡等缺陷。
连铸坯这些表面缺陷主要是钢液在结晶器内坯壳形成生长过程中产生的,与浇注温度、拉坯速度、保护渣性能、浸入式水口的设计,结晶式的内腔形状、水缝均匀情况,结晶器振动以及结晶器液面的稳定因素有关。
(3)连铸坯的内部质量:是指连铸坯是否具有正确的凝固结构,以及裂纹、偏析、疏松等缺陷程度。
二冷区冷却水的合理分配、支撑系统的严格对中是保证铸坯质量的关键。
(4)连铸坯的外观形状:是指连铸坯的几何尺寸是否符合规定的要求。
与结晶器内腔尺寸和表面状态及冷却的均匀程度有关。
下面从以上四个方面对实际生产中连铸坯的质量控制采取的措施进行说明。
关键词:连铸坯;质量;控制1 纯净度与质量的关系纯净度是指钢中非金属夹杂物的数量、形态和分布。
夹杂物的存在破坏了钢基体的连续性和致密性。
夹杂物的大小、形态和分布对钢质量的影响也不同,如果夹杂物细小,呈球形,弥散分布,对钢质量的影响比集中存在要小些;当夹杂物大,呈偶然性分布,数量虽少对钢质量的危害也较大。
此外,夹杂物的尺寸和数量对钢质量的影响还与铸坯的比表面积有关。
一般板坯和方坯单位长度的表面积(S)与体积(V)之比在0.2~0.8。
随着薄板与薄带技术的发展,S/V可达10~50,若在钢中的夹杂物含量相同情况下,对薄板薄带钢而言,就意味着夹杂物更接近铸坯表面,对生产薄板材质量的危害也越大。
所以降低钢中夹杂物就更为重要了。
提高钢的纯净度就应在钢液进入结晶器之前,从各工序着手尽量减少对钢液的污染,并最大限度促使夹杂物从钢液中排除。
为此应采取以下措施:⑴无渣出钢。
连铸方坯的缺陷及其处理
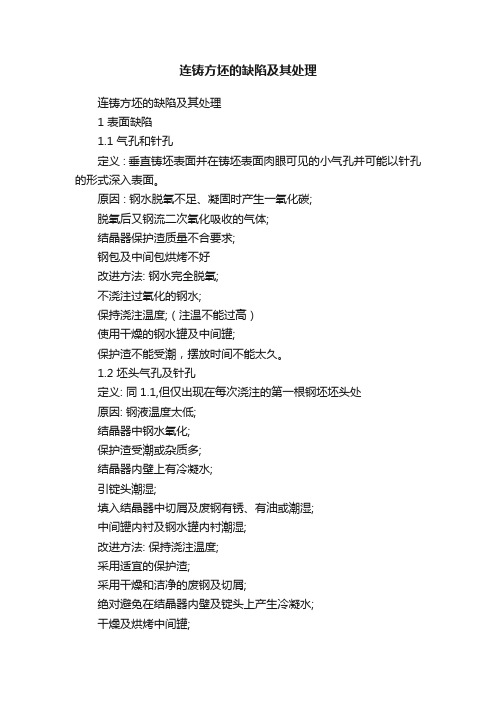
连铸方坯的缺陷及其处理连铸方坯的缺陷及其处理1 表面缺陷1.1 气孔和针孔定义 : 垂直铸坯表面并在铸坯表面肉眼可见的小气孔并可能以针孔的形式深入表面。
原因 : 钢水脱氧不足、凝固时产生一氧化碳;脱氧后又钢流二次氧化吸收的气体;结晶器保护渣质量不合要求;钢包及中间包烘烤不好改进方法: 钢水完全脱氧;不浇注过氧化的钢水;保持浇注温度;(注温不能过高)使用干燥的钢水罐及中间罐;保护渣不能受潮,摆放时间不能太久。
1.2 坯头气孔及针孔定义: 同1.1,但仅出现在每次浇注的第一根钢坯坯头处原因: 钢液温度太低;结晶器中钢水氧化;保护渣受潮或杂质多;结晶器内壁上有冷凝水;引锭头潮湿;填入结晶器中切屑及废钢有锈、有油或潮湿;中间罐内衬及钢水罐内衬潮湿;改进方法: 保持浇注温度;采用适宜的保护渣;采用干燥和洁净的废钢及切屑;绝对避免在结晶器内壁及锭头上产生冷凝水;干燥及烘烤中间罐;1.3 夹渣定义: 表面分布不均匀的夹渣,有时针孔和渣聚集,呈疏松态的外观原因: 由保护渣耐火材料颗粒和钢水氧化产物以及出钢渣等引起,随着钢流带入并被卷至铸坯表面。
改进方法: 用挡渣出钢;采用适宜的保护渣及耐火材料;钢水不能过氧化,注温要合适。
1.4 振动波纹及折叠定义: 在与铸坯轴线垂直方向上,铸坯表面上以均匀间距分布的波纹振痕,在不利的情况下出现折叠。
原因: 浇注速度波动大,使结晶器中钢液面不稳定。
改进方法: 保持均匀的浇注速度,稳定结晶器钢水液面。
调整振动频率使其与拉速相适应。
1.5 结疤与重皮定义: 铸坯角部和表面上出现的疤痕原因: 由于结晶器内坯壳破裂、钢水渗入到结晶器和铸坯之间的夹缝,以及保护渣结块造成。
改进方法: 保证结晶器具有准确的锥度,当结晶器使用时间过长而磨损会使坯壳过早脱离结晶器内壁而导致坯壳破裂。
1.6 分层: (双浇)定义: 铸坯中间出现分界层原因: 浇注中断又重新开始浇注时,使两次浇注连接出现重接。
改进方法: 浇注过程中不要断流,拉速要相对稳定,不要忽高忽低。
连铸方坯脱方及表面缺陷的成因与对策
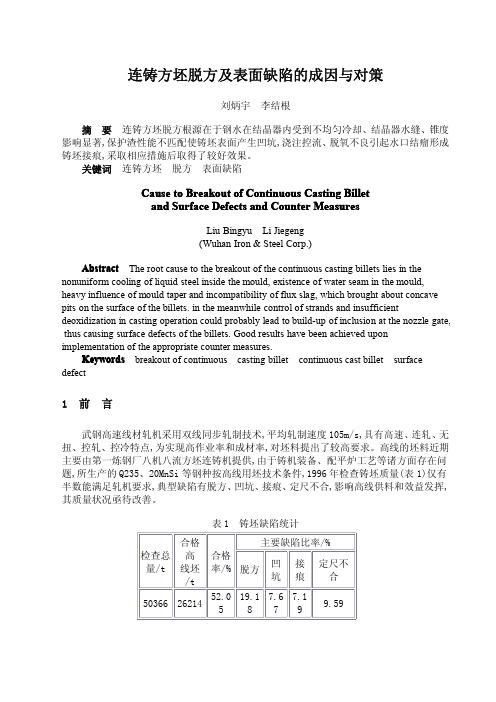
202. 202. 202. 202. 202. 202. 202. 203. 30055550
202. 202. 202. 202. 202. 202. 202. 202. 00060555
表 7 WF—A 理化指标
水缝宽度决定着结晶器的冷却效果,其控制精度有特殊要求,设计技术条件为 5+0.5 0mm 范围,现场抽查实际情况表 5,由于定位方式不当,支撑刚度不够,水套易变形,使水 缝间隙远远超过标准要求,并有冷却死角。水缝超宽,水速达不到设计 6m/s 要求,引起 边界处冷却水间隙沸腾,使铸坯受到不均匀冷却。
流号
表 6 抽查在线铜管尺寸情况/mm 标 准 1号 2号 3号 4号 5号 6号 7号 8号
东
上 口
西
下 口
南
上 口
北
下 口
206.2~ 206.8
204.9~ 205.7
203.2~ 203.8
201.9~ 202.7
206. 205. 205. 205. 205. 206. 206. 206. 05590005
及操作问题。
4 实施措施
4.1 结晶器改进 将螺栓调水缝改为水套与铜管间线接触,端面四周用 5mm×50mm 钢条定位,使水缝
平整光滑,将水套板厚由 5mm 改为 8mm,增加刚度减少变形,可以保证达到技术要求。取 消压盖和中间压板,消除了上水室冷却死角,改进了密封方式。足辊靠四角立柱定位,间 距由立柱上螺栓调节,调整范围 0~30mm,总装配底部增设存放底座,便于吊装找正定位, 受到碰撞时辊距不移位,有利于准确对弧。在同罐次条件下进行新旧结晶器浇铸 Q235 对比(表 8),减少脱方率 6.54%,平均对角线差减小 0.24mm,新结晶器的脱方趋势明显要 小。
连铸坯的缺陷与控制技术
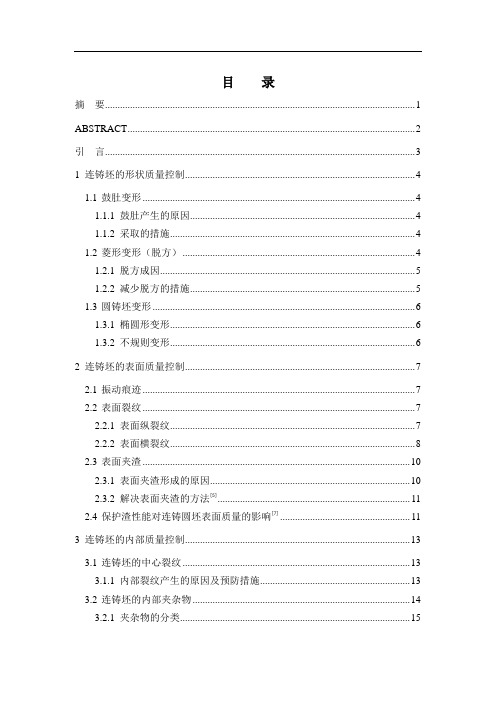
目录摘要 (1)ABSTRACT (2)引言 (3)1 连铸坯的形状质量控制 (4)1.1鼓肚变形 (4)1.1.1 鼓肚产生的原因 (4)1.1.2 采取的措施 (4)1.2菱形变形(脱方) (4)1.2.1 脱方成因 (5)1.2.2 减少脱方的措施 (5)1.3圆铸坯变形 (6)1.3.1 椭圆形变形 (6)1.3.2 不规则变形 (6)2 连铸坯的表面质量控制 (7)2.1振动痕迹 (7)2.2表面裂纹 (7)2.2.1 表面纵裂纹 (7)2.2.2 表面横裂纹 (8)2.3表面夹渣 (10)2.3.1 表面夹渣形成的原因 (10)2.3.2 解决表面夹渣的方法[5] (11)2.4保护渣性能对连铸圆坯表面质量的影响[7] (11)3 连铸坯的内部质量控制 (13)3.1连铸坯的中心裂纹 (13)3.1.1内部裂纹产生的原因及预防措施 (13)3.2连铸坯的内部夹杂物 (14)3.2.1夹杂物的分类 (15)3.2.2 夹杂物的来源[9] (15)3.2.3 连铸坯中夹杂物的控制方法[10] (16)结论 (18)致谢 (19)参考文献 (20)摘要连铸坯质量决定着最终产品的质量。
从广义来说所谓的连铸坯质量是得到严格产品所允许范围以内,叫合格产品。
连铸坯质量是从一下几个方面进行评价的:1. 连铸坯的外观形状:是指连铸坯的几何尺寸是否符合规定的要求。
与结晶器内腔尺寸和表面状态及冷却的均匀程度有关。
2. 连铸坯的表面质量:主要是指连铸坯表面是否存在裂纹,夹渣等缺陷。
连铸坯这些表面缺陷主要是钢液在结晶器内坯壳形成生长过程中产生的,与浇注温度,拉坯速度,保护渣性能,浸入式水口的设计,结晶式的内腔形状,水缝均匀情况,结晶器振动以及结晶器液面的稳定因素有关。
3. 连铸坯的内部质量:是指连铸坯是否具有正确的凝固结构,以及裂纹,偏析,疏松等缺陷程度。
二冷区冷却水的合理分配,支撑系统的严格对中是保证铸坯质量的关键。
连铸板坯和方坯表面缺陷的分析与判定

在钢板、板卷、棒材、型钢上的裂纹和其他等缺陷,大多源于板坯和方坯上的缺陷。
大多数钢厂面临的最大挑战是缺乏如何判定、检查这些缺陷及相应地采取何种对策。
令人遗憾的是,目前很多钢厂在遇到表面缺陷问题时所做的一些措施并不恰当,甚至没有对板坯和方坯进行检测分析便作出相应的判定和措施。
1.板坯和方坯的表面缺陷类型板坯和方坯上的所有表面缺陷几乎可以被分成五大类,并且在世界上大多数铸机上它们的发生位置基本上也是可以预测的。
基于经验,按照发生概率的大小顺序列出了五大类缺陷,即针状气孔/疏松、裂纹、深度振痕、不良清理、结晶器壁污染和刮伤等。
依据加热炉的氧化条件,可以确定板坯和方坯表面缺陷的临界深度,从而判定缺陷是否最终会成为板材、板卷或棒材上的轧制表面缺陷。
大部分加热炉操作会导致1%~2%厚度的铸坯氧化成氧化铁皮。
如果铸坯的厚度为220mm,就意味着在加热过程中会造成2.2mm~4.4mm的厚度损失。
这个厚度损失同样会传递到表面缺陷。
如果铸坯表面缺陷的深度小于铸坯厚度的1%~2%,那么这些缺陷将在加热过程中消除。
而那些比成为氧化铁的1%~2%厚度更深的缺陷,最终会造成轧材的表面缺陷。
1)针状气孔/疏松在所有铸机上,针状气孔/疏松几乎都是常见的,也是最容易被忽略的铸坯缺陷。
如果钢中的气体得不到合理控制,就会在板坯和方坯表面上产生针状气孔/疏松。
当凝固率达到90%而气体总压力Ar+H2+N2+CO+CO2>1atm时,针状气孔/疏松就会在板坯和方坯表面上形成。
找出表面和皮下针状气孔/疏松的形成原因并不困难。
在实际生产中,皮下通常是指表面以下10mm的深度。
根据经验,针状气孔/疏松是影响钢板、板卷表面质量的最突出问题。
举一个板坯上的针状气孔/疏松的例子,钢种是V和Nb复合微合金化的A572Gr50结构钢,含0.15%C,在铸坯上角部出现针状气孔/疏松,导致14.3mm厚的成材的上边部出现缺陷。
该板坯进行了展宽轧制以满足板宽尺寸的需要。
211172579_连铸方坯的常见表面缺陷及控制

管理及其他M anagement and other连铸方坯的常见表面缺陷及控制康旭辉摘要:连铸方坯表面的质量直接影响材料轧制后成品的质量,而近年来,我国部分企业在连铸方坯生产的过程中,存在诸多的表面缺陷问题,不能确保生产的质量和效果。
基于此,本文分析连铸方坯常见表面缺陷问题,提出几点表面缺陷控制的建议和措施,旨在为增强连铸方坯的表面质量提供帮助。
关键词:连铸方坯;常见表面缺陷;控制全面掌握方坯缺陷的类型、形成机理和消除途径是方坯质量控制的关键。
目前,国内外钢铁企业在钢坯质量控制方面取得了可喜的成绩,并获得了大量的生产数据和实际操作经验。
全面提高方坯质量,对提高连铸方坯成品率、改善钢材质量、节能降耗、降低成本具有重要意义。
连铸钢属于直接浇注钢水的工艺。
它的出现从根本上改变了主导了一个世纪的钢锭开坯过程。
液态金属连铸钢的概念早在19世纪中叶就被提出。
1840年,美国的销售商获得了连铸铅管的专利。
1846年,转炉的发明者贝塞默使用水冷旋转双辊连铸机生产锡箔、铅板和玻璃板。
1872年,David提出了移动式结晶器连铸的概念。
1886年~1889年,提出了立式连铸机的设计方案。
1921年,皮尔逊提出了结晶器振动的概念,即结晶器振动使板坯和结晶器之间连续的相对运动。
1933年,连铸的先驱德国准噶斯人建造了第一台1700t/月振动结晶器立式连铸机。
20世纪30年代,第一个成功铸造铜铝合金的有色金属连铸应用于生产。
目前,部分企业在连铸方坯生产的过程中,方坯表面的质量波动幅度很高,存在脱方缺陷、凹陷,缺陷和渣沟缺陷等,不能确保整体结构表面质量符合标准要求,对特钢产品生产质量造成一定的危害,因此,在连铸方坯实际生产的过程中需结合具体表面缺陷问题的发生原因与实际情况,采用有效的措施进行控制,确保连铸方坯表面质量符合标准规范,为特钢产品高质量生产夯实基础。
1 连铸方坯的常见表面缺陷和发生原因1.1 渣沟缺陷与原因从实际情况而言,连铸方坯表面出现渣沟缺陷问题,轧制以后线材表面出现裂纹缺陷问题的发生存在直接联系,从表面观察可以发现坯件有纵向贯通性的沟状缺陷问题,具体是在连铸方坯的内弧部分分布,很小一部分会在侧弧的位置,采用跟踪性轧制12.5mm绞丝钢实验的方式,可以发现线材的表面存在裂纹问题。
《改善连铸板坯缺陷的轧制工艺》范文

《改善连铸板坯缺陷的轧制工艺》篇一一、引言随着现代工业的快速发展,钢铁行业作为国民经济的重要支柱,其产品质量和生产效率的提升显得尤为重要。
连铸板坯作为钢铁生产中的重要环节,其质量直接影响到后续轧制工艺的效率和产品质量。
因此,如何有效改善连铸板坯的缺陷,优化轧制工艺,成为了业界关注的焦点。
本文旨在探讨连铸板坯的常见缺陷及原因,并分析轧制工艺的改进措施,以提高钢铁产品的质量和生产效率。
二、连铸板坯常见缺陷及原因分析1. 中心裂纹:中心裂纹是连铸板坯的主要缺陷之一,其形成原因主要是板坯凝固过程中的温度梯度和热应力过大。
此外,铸坯的化学成分、夹杂物、铸机振动等因素也会对中心裂纹的产生造成影响。
2. 表面裂纹:表面裂纹主要出现在板坯的表面,其形成原因包括钢水质量、结晶器振动、二次冷却制度等因素。
此外,钢中合金元素和夹杂物的含量也会对表面裂纹的产生造成影响。
3. 夹渣和夹杂物:夹渣和夹杂物主要来源于钢水的精炼过程和浇注过程中的夹杂物。
此外,铸模的质量、涂料的性能以及连铸机的维护保养也会影响夹渣和夹杂物的产生。
三、轧制工艺的改进措施针对上述连铸板坯的常见缺陷,轧制工艺的改进措施主要包括以下几个方面:1. 优化轧制参数:通过合理设定轧制温度、轧制速度、压下量等参数,使轧制过程更加稳定,减少轧制过程中的变形和裂纹等缺陷的产生。
2. 调整轧辊质量:选用高质量的轧辊,提高轧辊的硬度和耐磨性,减少轧制过程中的磨损和振动,从而降低板坯的表面裂纹和内部缺陷。
3. 强化轧前准备:在轧制前对连铸板坯进行充分的预热和除鳞处理,以去除表面的夹杂物和氧化皮,提高板坯的表面质量。
4. 优化冷却制度:根据板坯的化学成分、尺寸和轧制要求,制定合理的冷却制度,控制板坯的冷却速度和温度分布,以减少中心裂纹和表面裂纹的产生。
5. 引入无损检测技术:在轧制过程中引入无损检测技术,如超声波检测、X射线检测等,对板坯进行实时监测,及时发现并处理缺陷,提高产品的良品率。
- 1、下载文档前请自行甄别文档内容的完整性,平台不提供额外的编辑、内容补充、找答案等附加服务。
- 2、"仅部分预览"的文档,不可在线预览部分如存在完整性等问题,可反馈申请退款(可完整预览的文档不适用该条件!)。
- 3、如文档侵犯您的权益,请联系客服反馈,我们会尽快为您处理(人工客服工作时间:9:00-18:30)。
连铸方坯的缺陷及其处理
1 表面缺陷
1.1 气孔和针孔
定义 : 垂直铸坯表面并在铸坯表面肉眼可见的小气孔并可能以针孔的形式深入表面。
原因 : 钢水脱氧不足、凝固时产生一氧化碳;
脱氧后又钢流二次氧化吸收的气体;
结晶器保护渣质量不合要求;
钢包及中间包烘烤不好
改进方法: 钢水完全脱氧;
不浇注过氧化的钢水;
保持浇注温度;(注温不能过高)
使用干燥的钢水罐及中间罐;
保护渣不能受潮,摆放时间不能太久。
1.2 坯头气孔及针孔
定义: 同1.1,但仅出现在每次浇注的第一根钢坯坯头处
原因: 钢液温度太低;
结晶器中钢水氧化;
保护渣受潮或杂质多;
结晶器内壁上有冷凝水;
引锭头潮湿;
填入结晶器中切屑及废钢有锈、有油或潮湿;
中间罐内衬及钢水罐内衬潮湿;
改进方法: 保持浇注温度;
采用适宜的保护渣;
采用干燥和洁净的废钢及切屑;
绝对避免在结晶器内壁及锭头上产生冷凝水;
干燥及烘烤中间罐;
1.3 夹渣
定义: 表面分布不均匀的夹渣,有时针孔和渣聚集,呈疏松态的外观
原因: 由保护渣耐火材料颗粒和钢水氧化产物以及出钢渣等引起,随着钢流带入并被卷至铸坯表面。
改进方法: 用挡渣出钢;
采用适宜的保护渣及耐火材料;
钢水不能过氧化,注温要合适。
1.4 振动波纹及折叠
定义: 在与铸坯轴线垂直方向上,铸坯表面上以均匀间距分布的波纹振痕,在不利的情况下出现折叠。
原因: 浇注速度波动大,使结晶器中钢液面不稳定。
改进方法: 保持均匀的浇注速度,稳定结晶器钢水液面。
调整振动频率使其与拉速相适应。
1.5 结疤与重皮
定义: 铸坯角部和表面上出现的疤痕
原因: 由于结晶器内坯壳破裂、钢水渗入到结晶器和铸坯之间的夹缝,以及保护渣结块造成。
改进方法: 保证结晶器具有准确的锥度,当结晶器使用时间过长而磨损会使坯壳过早脱离结晶器内壁而导致坯壳破裂。
1.6 分层: (双浇)
定义: 铸坯中间出现分界层
原因: 浇注中断又重新开始浇注时,使两次浇注连接出现重接。
改进方法: 浇注过程中不要断流,拉速要相对稳定,不要忽高忽低。
1.7 纵裂
定义: 分布在铸坯角部的纵向裂纹, 角部纵裂常是拉漏的预兆。
原因: 针孔、气泡及夹杂;
结晶器内坯壳不均匀冷却;
由于铜结晶器中和足辊上有沟槽,缺口,渣子等而引起裂纹;
结晶器壁磨损或单面磨损使该处坯壳提前脱离结晶器壁;
浇注速度过高或浇注温度过高,坯壳厚度薄;
足辊对位不准;
二次冷却水不均匀;
拉矫机处铸坯扭曲;
钢水成份,特别是含碳高(裂纹倾向性大)和硫、磷含量高的钢。
改进方法: 经常检查结晶器铜管内壁,按规定更换报废;
检查二冷水要分布均匀,喷嘴不能堵塞;
注温注速要按规定,不能忽高忽低;
经常用弧板检查结晶器与二冷段对弧;
检查拉矫机上下辊对中情况;
对碳、硫偏高的钢种要适当减小拉速,减小二冷水。
2 内部缺陷
一部分内部缺陷是凝固条件引起的,连铸坯的凝固组织一般包括三个区域;边缘等轴细晶粒区,柱状树枝晶结晶区,中心等轴晶区,伴随结晶过程而产生的内部缺陷包括:
气孔及皮下气泡
偏析
内裂
夹杂
2.1 气孔及皮下气泡
定义: 分布在由激冷层至定向树枝晶区之间的过渡带内,主要以细孔形式出现。
原因: 由于铸坯内钢液吸收了气体,由于上浮作用,在外弧侧较少而内弧侧较多。
改进方法: 同1.1及1.2
2.2 中心偏析中心疏松
定义: 中心偏析是铸坯核心区偏析元素聚集, 这可从硫印上看出。
原因: 浇注速度过高;
浇注温度过高;
冷却过强;
钢中夹杂物多;
改进方法: 保持规定的浇注速度、浇注温度及成份;
适当的二次冷却;铸坯的疏松程度随二冷水量的增加而增大,
因此二冷水量应保持适度,这也是避免冷却时开裂的收缩裂纹的
先决条件
2.3 内裂(偏析裂纹)
连铸坯的内部裂纹常常出现在铸坯内部的薄弱点上,它是由以下原因产
生的:
---当铸坯中心尚处于液态时,承受很大的负荷而引起裂纹。
裂纹被富集偏
析元素的钢水所填充,因此,称此类裂纹为偏析裂纹。
从裂纹的形成原因,可将它们划分为:
由冷却引起的收缩裂纹;
变形裂纹;
对角线裂纹;
应当指出: 不可能给各种引起裂纹的原因间划出精确的界限,缺陷常为两种或两种以上的原因所造成。
(1) 由冷却引起的收缩裂纹
定义: 在铸坯心部和表面附近的裂纹,它往往分布于边缘与心部之间。
原因: 一次及二次冷却过强或不均匀,特别是浇注裂纹敏感性强的钢。
改进方法: 保证按规定的冷却制度配水;
一次及二次冷却水均匀且分布良好;此外,对纵裂纹所采取的措施原则上也
适用于此。
(2) 弯曲、矫直和加压产生的裂纹
定义: 裂纹与铸坯纵向轴成直角,垂直于拉矫机轴线分布。
原因: 在铸坯还有液芯的情况下,向铸坯加压,弯曲或矫直铸坯引起的。
它也可能是由于结晶器与二冷段未对准,使铸坯在拉出时产生变
形引起的。
改进方法: 同1.7"纵裂"一节
(3) 变形裂纹
定义、原因、消除均同上
(4) 对角线裂纹
定义: 对角线裂纹沿两个相邻的凝固界面结晶相交处分布
原因: 结晶器中或二次冷却不均匀,往往与菱形变形结伴产生。
改进方法: 减少菱形变形,见3.1节
检查喷水冷却
减少拉矫机压力
2.4 夹杂物
定义: 与2.2节"中心偏析"所述相类同
原因: 钢中元素铁、锰、硅、铝等与氧、氮、硫相结合形成夹杂物或耐火材料等带入的外来夹杂物。
改进方法: 只浇注完全脱氧,无过氧化的钢水;
不超过的最大S、P含量
采用合适的耐火材料,保护渣及中包涂料。
3 形状缺陷
3.1 菱形变形
定义: 铸坯断面呈菱形歪斜
在浇注小断面铸坯时,铸坯在结晶器内易出现轻度的菱形歪斜,而在二冷区加剧。
原因: 浇注温度太高;
足辊未精确对准;
喷水室内喷水不均匀;
铜结晶器锥度不够或磨损过度;
结晶器未对准;
改进方法: 保持规定的注温及注速;
精确调准足辊;
检查喷水冷却;
替换磨损的结晶器;
3.2 纵向凹陷:
定义: 槽形纵向凹陷
原因: 在铸坯角部附近的纵向凹陷表明该处存在有外部裂纹或内部裂纹。
其产生原因与纵裂相似
改进方法: 同1.7节"纵裂"。