沙钢宽厚板5000工艺技术
镰刀弯产生原因及控制措施探讨(精)

镰刀弯产生原因及解决措施探讨杨胜清(江苏沙钢集团沙景宽厚板厂张家港)摘要:针对沙钢5000mm宽厚板厂现场轧制过程中产生镰刀弯的原因进行分析,并结合实际给出解决措施,减少和避免了镰刀弯的现象,保证双边剪的顺利剪切,提高车间综合成材率。
关键词:宽厚板镰刀弯锲形温度对中辊型1.前言目前沙钢5000mm宽厚板厂的轧机功能调试和剪机调试已经结束,本着轧制精品钢材的理念,满足市场需求,船板、管线钢等四切边品种钢轧制比例将大幅度提高,避免和减少轧制过程中的镰刀弯成了提高产量和质量的关键因素之一。
我厂在轧制薄规格(厚度<16 mm) 钢板时,钢板镰刀弯较为严重,经常出现头尾镰刀弯现象。
这对轧制过程的稳定性危害极大,轻则造成边部切损过大、长度短尺,降低成材率和定尺率,重则出现快停、刮框,造成轧废或损害推床等设备,耽误大量的生产时间。
因此,防止轧件镰刀弯显得十分重要。
2.镰刀弯产生原因分析在宽厚板轧制过程中,经常出现镰刀弯现象,即使操作人员在轧制过程中反复调节轧辊两侧倾斜量,但这种调节在某些情况下不是一直有效。
特别是两侧都弯的时候,方向判断困难,容易造成误调节,使镰刀弯加剧。
造成板形不好和尺寸精度变差,这些都严重影响了产品的尺寸精度和质量。
结合我厂宽厚板的生产实际情况,下面主要对薄板轧制时产生镰刀弯的主要因素进行分析:常见的镰刀弯形成原因有: ①坯料楔形;②坯料切斜;③温度分布不均匀的影响; ④轧机两侧刚度存在差异;⑤EGC 和A GC 偏差;⑥推床不对中;⑦轧辊辊形不合理;⑧薄板轧制规程不合理。
以上影响因素不是单一作用在钢板上,一般是多种影响因素同时作用于钢板上。
1.1 坯料楔形的影响由于坯料宽度方向的厚度不均,造成钢板两侧压下量不一样,从而轧机两侧弹跳不一样,使得钢板两侧出口厚度不一致,随着钢板长度的增加,这种现象越来越明显。
这种镰刀弯主要出现在全纵轧的情况下,不易调节。
但实际上,我厂纵轧料少,一般需要进行展宽轧制和延伸轧制,坯料宽度方向的楔形,在展宽阶段经过1-3个道次轧制,其厚度差远小于初始厚度差,基本可以忽略。
宽厚板生产工艺
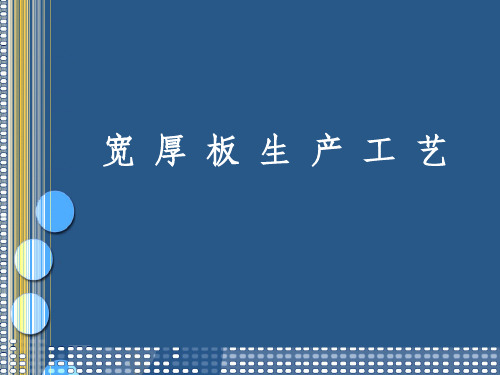
一、粗轧 主体设备包括四辊可逆粗轧机和附着式的立辊,
辅助装置包括高压水除鳞箱、辊道、机架辊、推床等。
高压水除鳞
喷嘴压力:16~18 Mpa 系统压力: 20 Mpa 管数:上、下各2排 水量:约440 m3/h
带立辊轧机的四辊可逆式粗轧机: 立辊轧机:
型式:附着式,上传动 位置:四辊粗轧机入口,与四辊粗轧机中心距4100mm 轧辊规格:Φ900/825×400 mm 轧辊开口度:1300~3800 mm
四辊可逆式粗轧机:
支撑辊: 数量:1套=2辊 辊身直径:2,000/1,800mm 轧机力能参数: 最大轧制压力:≤50000kN 最大轧制速度:5.39m/s(最大辊径) 工作辊最大开口度:330 mm(新辊)
二、精轧 主体设备包括四辊可逆精轧机和ACC设备,辅助装
置包括γ射线仪,辊道,机架辊,推床等。
缩短冶炼周期,提高转炉生产能力。
转炉容量
1*120t(最大为135t)
每炉出钢量
平均为125t
冶炼周期
36~40min
LF炉: LF炉功能: 1)调整钢液温度和均匀钢液成分; 2)脱氧、脱硫; 3)去除钢液中夹杂物提高钢水纯净度; 4)控制夹杂物形态。 设计参数: 公称容量:120t 最大钢水处理量:150t 最小钢水处理量:100t
VD处理功能: 1)脱氢 2)脱氮 3)脱氧、脱硫。 4)脱碳 5)去除钢水中夹杂。 设计参数:公称容量120吨
一座VD炉,双处理工位,年处理能力100万吨
RH炉: RH功能: 1)脱碳 2)脱氢 3)脱氮 4)脱氧 5)去除钢水中夹杂。 设计参数:设计公称容量120吨 一座RH炉,单处理位,双待机位,设计年处理能力60
热分切剪: 最大通过厚度120mm,温度≥550℃时剪切钢板的
5000mm热轧宽厚板四辊可逆式轧机辊系设计可行性方案

5000mm热轧宽厚板四辊可逆式轧机辊系设计可行性方案摘要随着经济社会的发展,特别是战争年代,大型战舰,大型战机的制造需要,对钢材的尺寸要求也越来越大。
这样就催生了人们对大型轧材的研究与探索。
大型宽厚板应运而生。
在航空母舰,大型水面战舰的制造上对,宽厚板,特别是5米宽厚板的需求是巨大的,由此如雨后春笋般出现的的5m宽厚板轧机的研究与投产更是越来越多。
一个宽厚板生产流水线,包括开坯粗轧机,精轧机,保温坑,冷却装置,切割机等等。
本设计主要只对轧机组进行设计,本设计主要介绍了5000mm热轧宽厚板四辊可逆轧机的轧制力,支承辊与工作辊尺寸,轴承寿命和弯辊装置计算。
本说明书按照设定的最大轧制力和产品规格参数设计计算了5000mm宽厚板轧机的轧辊的尺寸参数,轴承寿命和的基本参数以及校核,选择了轴承结构与类型,轧辊平衡装置也进行了相关设计计算。
其中轧辊尺寸确定是根据来料的规格尺寸确定的。
轧辊轴承的确定根据轧机在轧制过程中的受力状况,工作条件所确定的。
轧制力的计算采用了艾克伦德公式。
关键词:宽厚板;轧机设计;辊系设计;弯辊装置目录摘要 (II)Abstract ................................................................................ 错误!未定义书签。
1 文献综述......................................................................................................... - 1 -1.1 国内 ..................................................................................................... - 1 -1.1.1 国内宽厚板产业先驱——鞍钢股份有限公司.................. - 1 -1.2 国外 ..................................................................................................... - 3 -2 轧辊设计......................................................................................................... - 8 -2.1 轧辊结构与尺寸 ................................................................................ - 8 -2.1.1 轧辊的结构............................................................................. - 8 -2.1.2 轧辊辊身尺寸......................................................................... - 8 -2.1.3 轧辊辊颈尺寸d和l的确定.............................................. - 10 -2.2 轧辊力能参数计算 .......................................................................... - 11 -2.2.1 基本参数............................................................................... - 11 -2.3 轧辊材料选择................................................................................... - 12 -2.4 艾克伦德方法计算轧制时的平均单位压力................................. - 12 -2.4.1 变形阻力............................................................................... - 12 -2.4.2 变形速度............................................................................... - 13 -2.4.3 轧制压力............................................................................... - 14 -2.5 轧辊传动力矩................................................................................... - 15 -2.6 小结 ................................................................................................... - 16 -3 轧辊强度校核 .............................................................................................. - 17 -3.1 影响轧辊强度的因素...................................................................... - 17 -3.2 小结 ................................................................................................... - 21 -4 轧辊轴承....................................................................................................... - 22 -4.1 轴承的选择....................................................................................... - 22 -4.2 轴承寿命计算................................................................................... - 22 -4.3 小结 ................................................................................................... - 24 -5 轧辊弯辊装置 .............................................................................................. - 25 -5.1 液压弯辊装置................................................................................... - 26 - 参考文献 ........................................................................................................... - 28 - 致谢 ........................................................................................................... - 31 -1 文献综述有句话是这么说的:战争年代,工业的发展速度和创新水平都能得到很大的提高。
宝钢 5000mm 宽厚板厂设计资料

t/d
294.4 0.8 5.4 1.4 0.2 7.2 0.4 5.4 0.8 273.7 2463.7 117.3 1055.7 1.0 16.8 243.8 成品库发货的钢 板的最大长度为 25m ,特厚板发 货区发货的钢板 最 大 长 度 为 18m ,两库发货 的钢板的最大宽 度为 4.8m
宽厚板轧机及其公辅设施布置在纬三路与一炼钢厂连铸系统及其铁 路之间的场地上。 场地东西向长度约 1110m, 南北向宽度仅 250~280m, 二期工程增加了 1.50hm2 达到了 32.60 占地面积: 一期工程约 31.10hm2; hm2。西侧与拟建的宽厚板坯连铸厂房毗邻,东端以经五路为界,车间 总长度(按行列线计)为 1083m。 根据坯料来向,生产工艺流程按西进东出进行布置,成品分别从纬 三路、经五路输出。与生产工艺联系密切的公辅设施,如变配电、检验 室、循环水处理、空压站及除尘设施等则尽可能靠近用户分别布置在主 厂房两侧;办公楼设置在迎合人群流向的纬三路南侧、主厂房板坯跨和 预留成品库之间。 主厂房南侧通道非常狭窄(仅相当同型厂的 1/3 左右),设计无法 按《宝钢工厂设计统一技术规定》的要求进行常规的管线综合布置。 总图布置详见附图 S90.85-U1。
夏季月平均相对湿度最高值 冬季月平均相对湿度最高值 (3) 风速、风向 夏季平均风速 冬季平均风速 历史最大风速 全年主导风向 夏季主导风向 冬季主导风向 (4) 降雨量 十分钟最大降雨量 一小时最大降雨量 一日最大降雨量 一月最大降雨量 一年最大降雨量 (5) 气压 年平均气压 夏季平均气压 冬季平均气压 (6) 年积雪最大厚度 (7) 土壤冻结深度
5-9
为宽厚板厂服务的新设计道路的技术标准按《宝钢工厂设计统一技 术规定》的要求,选用城市型沥青路面,路面结构及厚度的确定,按《宝 钢道路路面结构标准图(修改版)》选用。 厂区道路,除担负成品运输的车间引道采用 10m 宽道路以外,其他 均为 7m 宽道路。 道路内侧边缘最小转弯半径、 道路最大纵坡等均按 《宝 钢工厂设计统一技术规定》。并根据《宝钢工厂设计统一技术规定》及 宝钢惯例,在主干道以外的道路两侧均不设置人行道及绿化带,故在宽 厚板厂区域内的道路两侧均不设置人行道。 宽厚板厂二期建设时,将在其南侧新建一铁路成品跨,其铁路将连 接在均热炉间前的调 4 东线上,并和工厂站进行联结。所以宽厚板厂二 期铁路成品跨及其铁路运输的建设,将和初轧厂的改造紧密结合起来。 二期新建铁路采用 60kg/m 钢轨,8#道岔,最小曲线半径为 120m。 14.4 绿化 一期工程绿化覆盖率按 20%计算。 二期工程的建筑系数已经达到 74%以上,再加上道路铺砌面积,两 项和的占地率已达到 85%以上, 所以除尽可能在空地和管线带上绿化外, 再采取一些垂直绿化措施,力争使绿化覆盖率达到 15%。 14.5 消防 本工程不单独设置消防站,由公司现有消防力量联防。 14.6 主要技术经济指标 本工程总图运输主要技术经济指标见下表。
宽厚板工艺技术
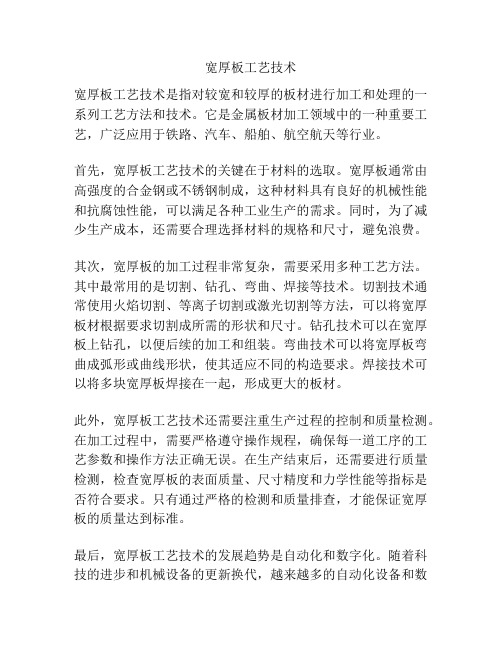
宽厚板工艺技术宽厚板工艺技术是指对较宽和较厚的板材进行加工和处理的一系列工艺方法和技术。
它是金属板材加工领域中的一种重要工艺,广泛应用于铁路、汽车、船舶、航空航天等行业。
首先,宽厚板工艺技术的关键在于材料的选取。
宽厚板通常由高强度的合金钢或不锈钢制成,这种材料具有良好的机械性能和抗腐蚀性能,可以满足各种工业生产的需求。
同时,为了减少生产成本,还需要合理选择材料的规格和尺寸,避免浪费。
其次,宽厚板的加工过程非常复杂,需要采用多种工艺方法。
其中最常用的是切割、钻孔、弯曲、焊接等技术。
切割技术通常使用火焰切割、等离子切割或激光切割等方法,可以将宽厚板材根据要求切割成所需的形状和尺寸。
钻孔技术可以在宽厚板上钻孔,以便后续的加工和组装。
弯曲技术可以将宽厚板弯曲成弧形或曲线形状,使其适应不同的构造要求。
焊接技术可以将多块宽厚板焊接在一起,形成更大的板材。
此外,宽厚板工艺技术还需要注重生产过程的控制和质量检测。
在加工过程中,需要严格遵守操作规程,确保每一道工序的工艺参数和操作方法正确无误。
在生产结束后,还需要进行质量检测,检查宽厚板的表面质量、尺寸精度和力学性能等指标是否符合要求。
只有通过严格的检测和质量排查,才能保证宽厚板的质量达到标准。
最后,宽厚板工艺技术的发展趋势是自动化和数字化。
随着科技的进步和机械设备的更新换代,越来越多的自动化设备和数字化工艺方法被引入到宽厚板加工中。
例如,自动切割机可以替代传统的手工切割,提高生产效率和精度;数字化控制系统可以实现加工过程的自动监控和远程操控,减少人力投入和生产周期。
这些新技术的应用,将进一步提升宽厚板工艺技术的水平和竞争力。
总之,宽厚板工艺技术是一项重要的金属板材加工技术,应用广泛且发展迅速。
它需要选择合适的材料,采用多种工艺方法进行加工,注重生产过程的控制和质量检测,并且面临着自动化和数字化的发展趋势。
只有不断创新和进步,才能不断提高宽厚板工艺技术的水平,为工业生产提供更好的支持。
宽厚板的加热、轧制和冷却技术

2一 0 取样贯 2 一扮线装! 2 一 1 2 冷娇机
图 3 德 国迪林根厚板厂工艺图
本也开始建立了发m优势。之后, 一些新工艺技 术、 控制系统和装备得到了开发与应用, 其中宽厚 板轧制新技术主要有 1高尺寸精度轧制技术。如r ) 射线测厚仪、 立 辊轧边机、 A 液压 WC系统、 工作辊移动( S + WR ) 强力弯辊( B 、 WR )成对交叉辊轧机(C 和连续可 P) 变凸度轧机(V ) 皮 C C等一术的应用, 提高了厚板尺寸 控制精度; 2平面形状控制伎术。如 M S ) A 平面形状控制 法、 狗骨轧制法及T P F 技术在日 芬兰、 本、 英国、 瑞 典等宽厚板轧机上得列了应用; 3控轧控冷技术。T C 工艺已成为宽厚板 ) MP 生产的主导工艺, 采用此技术生产的钢板已占3% 0 - 0 其板坯加热溢度为90 1 I, 5%, 5 一1 C 出炉温 5 0 度低于常规 轧制, 但混差小于 3'。此外, 0 C 宽厚板 生产品种多、 用途广、 现格大, 因而国外宽厚板生产 已 经普遍由 计算机进行 设定、 控制。
1 . x . 15 7 2 4
千叶厚板厂
全箱式炉型
8 3 0 3 . x . 5
加古川厚 h ’ / v
炉型
9 0 1 1 0 7 15 1
‘ ik声波探伤(/) _ 一 J 一 o A V_
热矫直、标记轧制批号 一 卜 一一
成检w 、扎,板志试打- , 品查 面尺 . 标 样印一 a r 品
L卜 部 查 试 打 冷 _外 松 、 样 印
一争 人工超声波探伤 ( , 供货状态) 一 1 一
最终检查伏 面、板形尺寸和标心
- il线装置 一 , - t ,
我国中厚板轧机生产技术概述
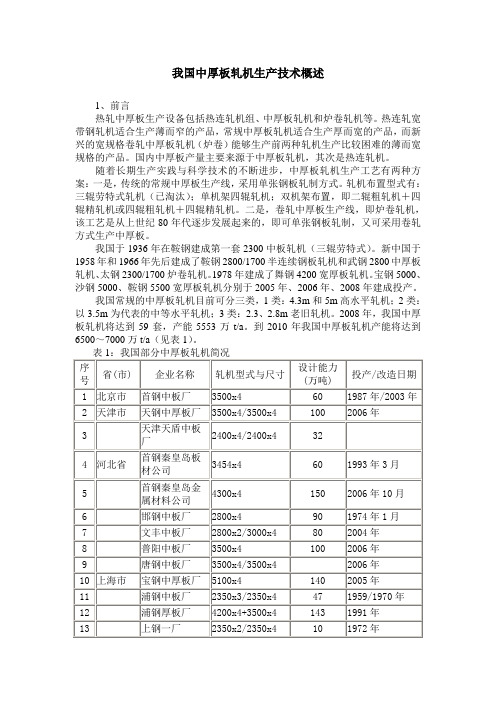
我国中厚板轧机生产技术概述1、前言热轧中厚板生产设备包括热连轧机组、中厚板轧机和炉卷轧机等。
热连轧宽带钢轧机适合生产薄而窄的产品,常规中厚板轧机适合生产厚而宽的产品,而新兴的宽规格卷轧中厚板轧机(炉卷)能够生产前两种轧机生产比较困难的薄而宽规格的产品。
国内中厚板产量主要来源于中厚板轧机,其次是热连轧机。
随着长期生产实践与科学技术的不断进步,中厚板轧机生产工艺有两种方案:一是,传统的常规中厚板生产线,采用单张钢板轧制方式。
轧机布置型式有:三辊劳特式轧机(已淘汰);单机架四辊轧机;双机架布置,即二辊粗轧机+四辊精轧机或四辊粗轧机+四辊精轧机。
二是,卷轧中厚板生产线,即炉卷轧机,该工艺是从上世纪80年代逐步发展起来的,即可单张钢板轧制,又可采用卷轧方式生产中厚板。
我国于1936年在鞍钢建成第一套2300中板轧机(三辊劳特式)。
新中国于1958年和1966年先后建成了鞍钢2800/1700半连续钢板轧机和武钢2800中厚板轧机、太钢2300/1700炉卷轧机。
1978年建成了舞钢4200宽厚板轧机。
宝钢5000、沙钢5000、鞍钢5500宽厚板轧机分别于2005年、2006年、2008年建成投产。
我国常规的中厚板轧机目前可分三类,1类:4.3m和5m高水平轧机;2类:以3.5m为代表的中等水平轧机;3类:2.3、2.8m老旧轧机。
2008年,我国中厚板轧机将达到59套,产能5553万t/a。
到2010年我国中厚板轧机产能将达到6500~7000万t/a(见表1)。
热轧中厚板生产工艺流程:a)坯料准备工艺流程:选择坯料(种类、尺寸)—坯料清理—坯料检验—合格坯料。
b)加热工艺流程:装炉—加热(控制加热时间、温度、速度和炉内气氛)—出炉。
c)轧制工艺流程:除鳞—粗轧—精轧。
d)精整工艺流程:矫直—冷却—表面检查—缺陷清理—剪切→(抛丸处理或热处理)→检验—标记—入库。
轧制是钢板成形阶段,其分为粗轧、精轧两个阶段。
沙钢5000mm宽厚板生产线
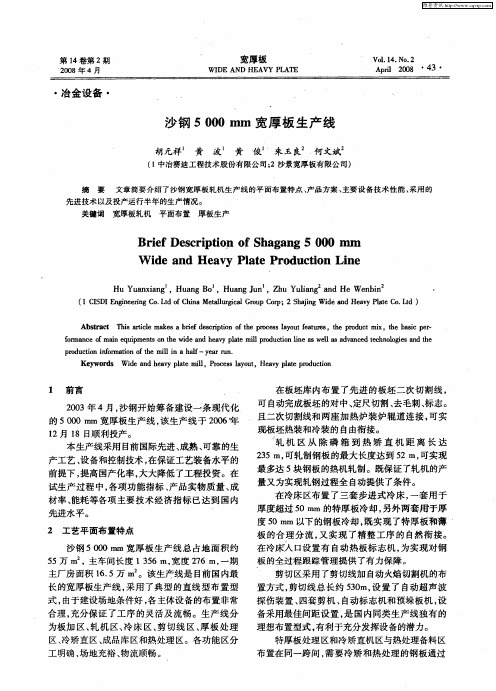
1 前 言
20 0 3年 4月 , 沙钢开始筹备建设一条现代化
的 500m 宽 厚 板生 产 线 , 生 产 线 于 20 0 m 该 06年 1 2月 1 8日顺 利投 产 。
本生产线采用 目前国际先进、 成熟、 可靠 的生 产工艺 、 设备和控制技术 , 在保证工艺装备水平的
前提下 , 提高国产化率, 大大降低了工程投资 。在 试生产过程中, 各项功能指标 、 品实物质量、 产 成
材率 、 能耗等各项主要 技术 经济指标 已达到 国内 先 进水 平 。
2 工 艺平 面布 置特点
沙 钢 500ml宽厚 板 生产 线 总 占地 面积 约 0 i l
5 5万 m 主 车间长 度 13 6m, 度 2 6 m, 期 , 5 宽 பைடு நூலகம் 一
维普资讯
第 1 卷第 2 4 期
20 0 8年 4月
・
宽厚 板
WI E D AND HEAVY P AT L E
V0 . 4 No 2 11 . .
Ap i 2 0 r 0 8 ‘4 ・ l 3
冶金设 备 ・
沙钢 500mm 宽厚 板 生产 线 0
fr a e f i qimet o e ie n ev lt m lpout nl e e d acdtcnl e dte om n eo neup ns nt d dha p e i r co n w l8 avn e h o g sa ma hw a y a l d i l a s l. 8 e o i n h
先进技术 以及投产运行半年 的生 产情 况。
关键词 宽厚板轧机 平面布置 厚 板生 产
Bre s rp i n o h g n 0 l ifDe c i t fS a a g 5 0 0 mi o l
- 1、下载文档前请自行甄别文档内容的完整性,平台不提供额外的编辑、内容补充、找答案等附加服务。
- 2、"仅部分预览"的文档,不可在线预览部分如存在完整性等问题,可反馈申请退款(可完整预览的文档不适用该条件!)。
- 3、如文档侵犯您的权益,请联系客服反馈,我们会尽快为您处理(人工客服工作时间:9:00-18:30)。
沙钢宽厚板工艺技术沈文荣邱松年钱洪建(江苏沙钢集团有限公司)摘要沙钢集团于2006年建成当今中国最现代化宽厚板生产工艺线.采用带工作辊弯辊的Φ1210×5050mm工作辊、带油膜轴承Φ2300×4900mm 支承辊,最大轧制力100MN,最大切断力矩2×4,925kNm,高刚度、液压AGC工作辊弯辊装置轧机及MULPIC 装置满足高强焊接宽厚板高品质和板型要求.亚稳态奥氏体区热机轧制实现晶粒细化,靠中间坯待温时间及未再结晶区γ/α相变较低终轧温度抑制新晶粒成长。
MULPIC装置中加速冷却或直接淬火钢板。
终轧通过MULPIC装置加速冷却使固溶体内保持大量Nb、V、Ti、Mo微合金元素粒子有利γ/α相变、铁素体与贝氏体内沉淀而改善组织性能。
终轧温度低及增加冷却速率有增加沉淀强化和位错密度高强效果。
转变温度取决微合金设计、终轧温度及加速冷却。
精整工序热矫、冷却、切边定尺剪切及冷矫钢板,某些钢板350~400℃间出现剪口应力断裂要堆垛缓冷。
关键词宽厚板轧热机轧制多功能冷却装置相变 UOE板SIS′Wide Heavy Ptate Process TechnologyShen Wenrong Qiu Songnian Qian Hongjian(Shagang Iron & Steel Group ,Suzhou,215625,Jiangsu P.R.C)Abstract In Dec.2006,by S hagang Iron & Steel Group company. Ltd.,SIS,was build latest modernization wide heavy plate operation line. The wide heavy mill is the largest plate mill in China. Main date of the heavy plate mill equipment including Φ1210×5050mm Work roll,Φ2300×4900mm back-up roll, back-up roll oil film bearings and HAGC,10,0000kN maximum rolling force, 2×4925kNm cut-out torque. Work roll bending system ,hydraulic AGC and high elasticity module of mill have to meet plate high quality and shape basic requirement.TMCP, a minimum degree of deformation is carried out in the temperature range of the metal stable austenite, whereby no re-crystallization takes place before the γ/α-transformation, so that the new grain formation is taken over by the transformation reaction. The necessary low finish rolling temperature,require relatively long waiting times before final deformation. For the plate,accelerated cooling or direct hardening velocity controlled by MULPIC equipment.Key W ords heavy plate mill,thermo-mechanical rolling, MULPIC,transformation,UOE1.概况我国目前≤3500mm中板轧机多达30余套,≥3800宽厚板轧机仅宝钢、沙钢、鞍钢、浦钢、舞阳、湘钢及新余7套。
全球16家≥5000mm宽厚板厂,法国1套,中国、美国和德国各2套,俄罗斯4套,日本5套。
沙钢集团于2006年建成5m现代宽厚板生产工艺线如图1所示,辊系采用带WRB的Φ1210×5050mm 工作辊和带油膜轴承Φ2300×4900mm 支承辊,最大轧制力100MN,最大切断力矩2×4925kNm,高刚度、液压AGC工作辊弯辊装置轧机及MULPIC装置。
沙钢建成现代化5m宽厚板厂(表1),提升我国高端特宽厚板生产能力。
满足5~150×900~4900×6000~27000mm高强船板、管线、桥梁、海洋、建筑国民经济单位:m m图1 沙钢宽厚钢板厂平面工艺简图1—步进梁加热炉;2—18MPa除鳞箱; 3—5m宽厚板轧机; 4—立辊轧机; 5—MULPIC装置; 6—9辊热矫;7—2号冷床; 8—1号检验台;9—UST装置;10—切头剪;11—双边剪;12—定尺剪;13—喷号机;14—2号检验台;15—钢板堆垛装置;16—11辊冷矫机;17—3号冷床。
2.工艺布置江苏沙钢集团5m宽厚板厂位于江苏扬子江国际冶金工业园区内,主厂房总长1356m,宽度方向最宽246m,总面积200610m2。
由板坯库、上料跨、加热炉跨、主轧跨、剪切跨、厚板处理中转跨、成品库、磨辊间、主电室组成,预留热处理跨、涂漆线跨。
产品规格5~150×900~4800×~25000mm,最大重量32300kg。
常规轧制、控制轧制及热处理钢板比5:3:2,生产碳素、低合金结构、船板、管线、桥梁、海洋、建筑、锅炉压力容器及机械工程用板,设计年产量180万t/a。
采用5m高刚度轧机、大功率主电机和MULPIC加速冷却装置并扩大精整能力,辊系带HAGC和WRB装置沙钢宽厚板轧机单位轧制力20KN/mm及单位轧制功率4KW/mm,用自动测压、测厚测宽测长仪及板型仪确保自动轧制钢板板型和平直度。
及在线钢板精整和钢板质量跟踪,从加热炉上料辊道至钢板进入成品库止,由计算机物料跟踪系统对板坯、轧件母板及成品子板全线跟踪,确定其确切位置,对相应设备设定和控制,通过全厂L1~L3三级控制系统确保高强船板、锅炉压力容器板、桥梁板和石油管线板的两阶段或三阶段TMCP+ACC/DQ轧制技术要求。
表1 国内外宽厚板厂轧机性能比较由沙钢集团宏发炼钢厂3号连铸机供给板坯,经二次切割精整后,连续加热炉加热,出炉板坯高压水除鳞后,进4辊5m可逆轧机轧制,根据要求进行ACC/DQ冷却后热矫直。
>50mm钢板进3号冷床冷却,厚板处理区堆冷至室温,经翻板检查、火焰切割、标志后吊至指定区域堆放、发货;≤50mm钢板进入2号冷床(若需可下线)冷却,经检查、切头、切尾、分段、切边/剖分、定尺、标志、堆存、发货。
需冷矫钢板送冷矫直机矫直后至成品跨堆存、发货。
3.1 加热3.1.1原料上料根据成品钢板规格、钢级及机时产量,选用220~320×1580~2515×2700~4600mm连铸板坯尺寸。
板坯由沙钢集团宏发炼钢厂提供3号连铸机板坯经轨道车连接,少量经由汽车运输送抵宽厚板厂1A —1B跨与1B―1C跨板坯库。
无缺陷合格板坯进板坯库前将板坯数据输入宽厚板厂,由70t钳吊将轨道车上板坯逐块卸到指定垛位或直接上料。
倍尺坯移送机运到二次切割线受料辊道对中、测长,运到切割辊道将倍尺坯火焰切割一切为二或切为三。
逐块去除头尾毛刺、标志后被运送到卸料辊道。
根据轧制计划顺序,由45t钳吊可同时吊运1~3块板坯,将1C―1D和1D―1E跨板坯吊至堆垛台。
上料推钢机将板坯推到加热炉上料辊道,经测长、称重,送入加热炉加热连铸坯热送热装采用轨道车运输,二次切割线与加热炉上料辊道用板坯运输链连接,缩短上料时间、减少板坯温降。
3.1.2 加热炉8段步进梁式加热炉具备坯料温度预报与热态跟踪、最佳炉温设定、动态空燃比设定、在线热平衡计算、炉压的前馈控制及耽误策略,装钢机端部上料和出钢机端部出料。
焦炉煤气为燃料,上、下供热滚轮斜台面全液压驱动。
两套步进机械双升降平移,单排或双排装料;箱型多区供热,分区控制各段温度适应热坯和冷坯热坯交替装炉加热小时产量变化;高背化耐热垫块和千鸟型布置减少板坯底部黑印;水梁及立柱双层绝热,高效保温材料复合炉衬,最大限度回收显热;高效空气预热器预热空气至550℃减少热耗,最大标定和小时产量分别为245和300t/h,热装率达60~70%。
加热炉236个烧嘴,上部为平焰和侧向烧嘴,下部为侧烧嘴,80和110m3/h平焰烧嘴各有60和72个;400、450和500m3/h侧烧嘴分别为28、48和28个。
风量助燃风机70000m3/h,风压13KPa,1450r/min;现场有炉压测量差压变送器、压力变送器、流量控制器、液位控制器、压力控制器,带黑度补偿板坯高温计、炉内残氧分析仪和NOx分析仪表,各段煤气和高温空气控制阀及煤气总管调节阀。
在步进式加热炉焦炉煤气为燃料,端部上料和出料。
板坯加热至1100~1200℃,对TMCP控制轧制微合金钢可降至1050~1080℃加热温度和加热时间应保证Nb、V、Ti微合金奥氏体固溶和奥氏体晶粒均匀。
钢板加热温度、加热速度、加热时间等工艺参数及炉温制度、炉内气氛、炉压均由计算机设定、控制。
3.2 轧制采用高压水除鳞箱;高精度、高刚度、高功率、大转矩厚板轧机、立辊轧机;MULPIC加速冷却装置和4重9辊热矫机。
3.2.1 高压水除鳞箱高压水除鳞箱有上下各两排喷嘴出口水压18MPa,上部喷嘴垂直可调,喷射与轧件法线成15°。
经高压水除去出炉板坯表面氧化铁皮。
3.2.2 立辊轧机Φ1000×600mm立辊轧机配有液压宽度控制系统(AWC)和轧制头尾部分短行程控制(SSC),控制轧件平面形状和宽度尺寸精度及钢板头尾部形状,轧制头尾部短行程控制对板坯矩形化能使轧件延伸道次全长宽度均匀偏差最小。
对轧件施以侧压立辊轧制减少轧件边部折叠和改善边部质量,提高成材率。
3.2.3 宽厚板轧机采用4KW/mm的Φ1210×5050/Φ2300×4900mm宽厚板轧机,其单位轧制力20KN/mm,单位轧制功率4KW/mm,适用于常规、TCR或TMR“纵—横—纵”或“横—纵—横”成形、展宽和延伸3阶段方式轧制成所需钢级和规格的宽厚板。
普通宽厚板用常规轧制工艺。
经推床对中后,板坯进入4辊可逆轧机进行轧制,先进行1~2道次成形轧制,机前或机后旋转辊道上轧件旋转90°后展宽轧制,轧至成品毛边宽度后再转90°延伸轧制,直至达到设定的成品厚度。