2MW华渝变桨介绍
风电变桨介绍

2.4变桨轴承基本维护 2.4变桨轴承基本维护
1.检查变桨轴承表面清洁度。 1.检查变桨轴承表面清洁度。 2.检查变桨轴承表面防腐涂层。 2.检查变桨轴承表面防腐涂层。 3.检查变桨轴承齿面情况。 3.检查变桨轴承齿面情况。 4.变桨轴承螺栓的紧固。 4.变桨轴承螺栓的紧固。 5.变桨轴承润滑。 5.变桨轴承润滑。
维护周期 (脂) 优选润滑剂 (油)
维护周期( 维护周期(油)
4.雷电保护装置 4.雷电保护装置
4.1安装位置 4.1安装位置
雷电保护装置在变桨装置中的具体位置见图1 雷电保护装置在变桨装置中的具体位置见图1, 在大齿圈下方偏左一个螺栓孔的位置装第一个保 护爪,然后120等分安装另外两个雷电保护爪。 护爪,然后120等分安装另外两个雷电保护爪。
华锐风电科技有限公司
风力发电机组培训教材 变桨部分
1.变桨控制系统简介 1.变桨控制系统简介
变桨控制系统包括三个主要部件,驱动装置 -电机,齿轮箱和变桨轴承。从额定功率起,通 过控制系统将叶片以精细的变桨角度向顺桨方向 转动,实现风机的功率控制。如果一个驱动器发 生故障,另两个驱动器可以安全地使风机停机。
2.5变桨系统工作环境 2.5变桨系统工作环境
安装地点 工作寿命 环境温度范围 机舱内温度范围 工作过程中环境温度范围 露天环境要求 相对湿度 内陆和沿海地区 20年 20年 -35°C 到 +45°C 35° +45° -35°C 到 +55°C 35° +55° -35°C 到 +55°C 35° +55° 腐蚀性,盐雾,流砂 在+40°C时为5% 到 95%, +40° 时为5% 95%, 露点
电机连接 工作时间
变桨工作原理
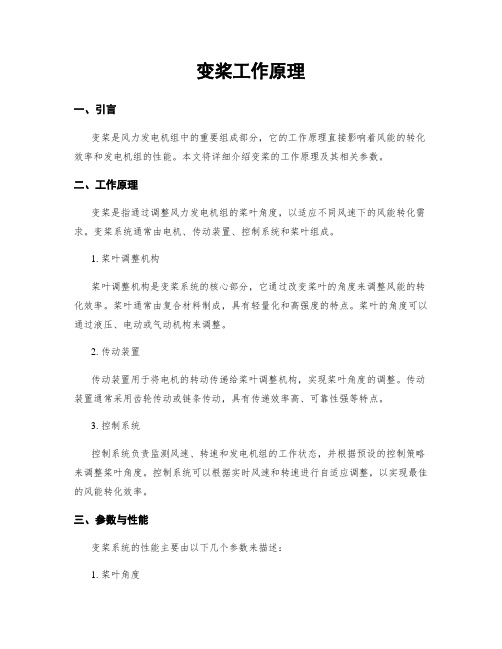
变桨工作原理一、引言变桨是风力发电机组中的重要组成部分,它的工作原理直接影响着风能的转化效率和发电机组的性能。
本文将详细介绍变桨的工作原理及其相关参数。
二、工作原理变桨是指通过调整风力发电机组的桨叶角度,以适应不同风速下的风能转化需求。
变桨系统通常由电机、传动装置、控制系统和桨叶组成。
1. 桨叶调整机构桨叶调整机构是变桨系统的核心部分,它通过改变桨叶的角度来调整风能的转化效率。
桨叶通常由复合材料制成,具有轻量化和高强度的特点。
桨叶的角度可以通过液压、电动或气动机构来调整。
2. 传动装置传动装置用于将电机的转动传递给桨叶调整机构,实现桨叶角度的调整。
传动装置通常采用齿轮传动或链条传动,具有传递效率高、可靠性强等特点。
3. 控制系统控制系统负责监测风速、转速和发电机组的工作状态,并根据预设的控制策略来调整桨叶角度。
控制系统可以根据实时风速和转速进行自适应调整,以实现最佳的风能转化效率。
三、参数与性能变桨系统的性能主要由以下几个参数来描述:1. 桨叶角度桨叶角度是指桨叶相对于风向的角度,它的大小决定了风能的转化效率。
通常情况下,当风速较低时,桨叶角度较大,以捕捉更多的风能;当风速较高时,桨叶角度较小,以减小风力对发电机组的影响。
2. 桨叶调整速度桨叶调整速度是指桨叶角度的变化速度,它的大小直接影响着风能转化的响应速度。
较快的桨叶调整速度可以使发电机组更快地适应风速变化,提高发电效率。
3. 控制精度控制精度是指控制系统对桨叶角度的调整精度。
高精度的控制系统可以更准确地控制桨叶角度,使风能转化效率最大化。
4. 风速范围风速范围是指变桨系统能够适应的风速范围。
通常情况下,变桨系统应能够在较低的风速下启动,并在较高的风速下保持稳定运行。
5. 转速响应转速响应是指发电机组在风速变化时的转速变化速度。
较快的转速响应可以使发电机组更快地适应风速变化,提高发电效率。
四、总结变桨是风力发电机组中的重要组成部分,通过调整桨叶角度来适应不同风速下的风能转化需求。
风力发电机液压变桨系统简介
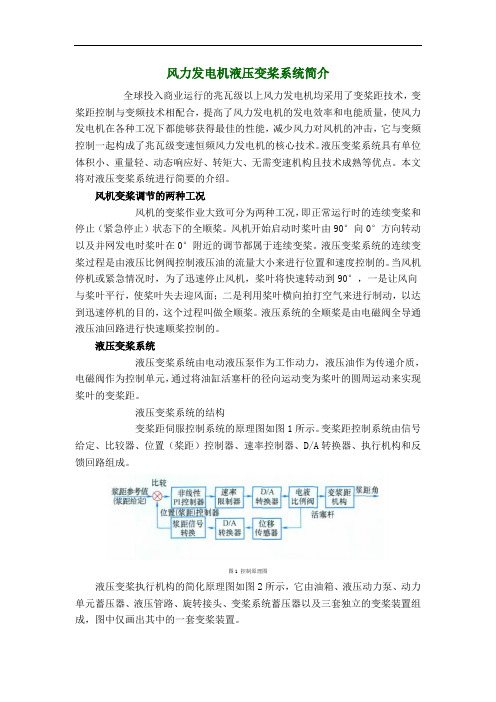
风力发电机液压变桨系统简介全球投入商业运行的兆瓦级以上风力发电机均采用了变桨距技术,变桨距控制与变频技术相配合,提高了风力发电机的发电效率和电能质量,使风力发电机在各种工况下都能够获得最佳的性能,减少风力对风机的冲击,它与变频控制一起构成了兆瓦级变速恒频风力发电机的核心技术。
液压变桨系统具有单位体积小、重量轻、动态响应好、转矩大、无需变速机构且技术成熟等优点。
本文将对液压变桨系统进行简要的介绍。
风机变桨调节的两种工况风机的变桨作业大致可分为两种工况,即正常运行时的连续变桨和停止(紧急停止)状态下的全顺桨。
风机开始启动时桨叶由90°向0°方向转动以及并网发电时桨叶在0°附近的调节都属于连续变桨。
液压变桨系统的连续变桨过程是由液压比例阀控制液压油的流量大小来进行位置和速度控制的。
当风机停机或紧急情况时,为了迅速停止风机,桨叶将快速转动到90°,一是让风向与桨叶平行,使桨叶失去迎风面;二是利用桨叶横向拍打空气来进行制动,以达到迅速停机的目的,这个过程叫做全顺桨。
液压系统的全顺桨是由电磁阀全导通液压油回路进行快速顺桨控制的。
液压变桨系统液压变桨系统由电动液压泵作为工作动力,液压油作为传递介质,电磁阀作为控制单元,通过将油缸活塞杆的径向运动变为桨叶的圆周运动来实现桨叶的变桨距。
液压变桨系统的结构变桨距伺服控制系统的原理图如图1所示。
变桨距控制系统由信号给定、比较器、位置(桨距)控制器、速率控制器、D/A转换器、执行机构和反馈回路组成。
图1 控制原理图液压变桨执行机构的简化原理图如图2所示,它由油箱、液压动力泵、动力单元蓄压器、液压管路、旋转接头、变桨系统蓄压器以及三套独立的变桨装置组成,图中仅画出其中的一套变桨装置。
图2 液压原理图结束语液压变桨系统与电动变桨系统相比,液压传动的单位体积小、重量轻、动态响应好、扭矩大并且无需变速机构,在失电时将蓄压器作为备用动力源对桨叶进行全顺桨作业而无需设计备用电源。
变桨工作原理

变桨工作原理一、概述变桨是风力发电机组中的一个重要组成部分,它通过调整叶片的角度来适应不同风速下的风能转换效率。
本文将详细介绍变桨的工作原理及其关键技术。
二、工作原理1. 变桨系统组成变桨系统主要由叶片、桨毂、液压系统和控制系统组成。
叶片通过连接在桨毂上,桨毂则与主轴相连。
液压系统负责控制桨毂的转动,控制系统则根据风速和发电机组运行状态来调整液压系统的工作。
2. 变桨过程当风速发生变化时,控制系统会根据风速传感器的反馈信号判断当前风速,并根据预设的风速-功率特性曲线来确定最佳叶片角度。
然后,控制系统通过液压系统控制桨毂的转动,使叶片调整到相应的角度。
当风速较低时,叶片角度会增大以增加风能捕捉面积;当风速较高时,叶片角度会减小以减少风阻,保护发电机组。
3. 关键技术(1) 风速传感器:用于实时监测风速,将风速信号传输给控制系统,以便根据风速调整叶片角度。
(2) 液压系统:通过液压油缸控制桨毂的转动,实现叶片角度的调整。
液压系统需要具备高精度、高可靠性和快速响应的特点。
(3) 控制系统:根据风速传感器的反馈信号和预设的风速-功率特性曲线,控制液压系统的工作,实现叶片角度的调整。
(4) 叶片材料:叶片需要具备轻量化、高强度和耐腐蚀的特点,以适应不同的风速环境和气候条件。
三、数据分析根据实际的风力发电场运行数据,可以得出以下结论:1. 变桨系统的优化可以显著提高风力发电机组的发电效率。
通过合理调整叶片角度,可以最大限度地捕捉风能,提高发电机组的利用率。
2. 变桨系统的响应速度对发电效率影响较大。
当风速突然变化时,如果变桨系统响应迟缓,将导致发电机组的发电效率下降。
3. 叶片材料的选择对发电机组的寿命和稳定性有重要影响。
优质的叶片材料可以提高叶片的耐久性,减少维护成本。
四、发展趋势随着风力发电技术的不断发展,变桨系统也在不断创新和改进中。
未来的发展趋势包括:1. 智能化控制:利用先进的传感器和控制算法,实现变桨系统的智能化控制,提高风力发电机组的发电效率和稳定性。
变桨工作原理
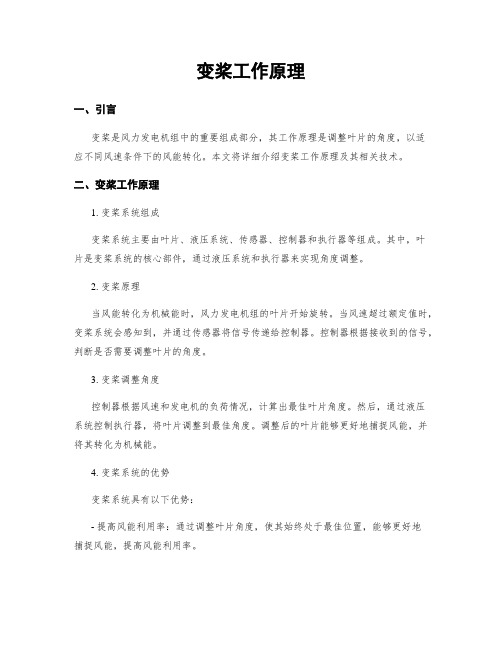
变桨工作原理一、引言变桨是风力发电机组中的重要组成部分,其工作原理是调整叶片的角度,以适应不同风速条件下的风能转化。
本文将详细介绍变桨工作原理及其相关技术。
二、变桨工作原理1. 变桨系统组成变桨系统主要由叶片、液压系统、传感器、控制器和执行器等组成。
其中,叶片是变桨系统的核心部件,通过液压系统和执行器来实现角度调整。
2. 变桨原理当风能转化为机械能时,风力发电机组的叶片开始旋转。
当风速超过额定值时,变桨系统会感知到,并通过传感器将信号传递给控制器。
控制器根据接收到的信号,判断是否需要调整叶片的角度。
3. 变桨调整角度控制器根据风速和发电机的负荷情况,计算出最佳叶片角度。
然后,通过液压系统控制执行器,将叶片调整到最佳角度。
调整后的叶片能够更好地捕捉风能,并将其转化为机械能。
4. 变桨系统的优势变桨系统具有以下优势:- 提高风能利用率:通过调整叶片角度,使其始终处于最佳位置,能够更好地捕捉风能,提高风能利用率。
- 保护风力发电机组:在风速过高或过低时,通过调整叶片角度,可以避免过载或过速运行,保护风力发电机组的安全运行。
- 调整叶片角度的灵活性:变桨系统可以根据风速的变化,实时调整叶片角度,以适应不同的风能转化需求。
三、变桨技术发展趋势1. 智能化控制技术随着科技的不断进步,智能化控制技术在变桨系统中得到了广泛应用。
通过引入人工智能和大数据分析等技术,可以实现对风速、发电机负荷等参数的实时监测和预测,从而更精确地调整叶片角度,提高发电效率。
2. 液压系统改进传统的液压系统存在能耗高、噪音大等问题。
未来的发展趋势是采用更高效、更节能的液压系统,以降低能源消耗和环境污染。
3. 变桨材料创新目前,变桨系统中常用的叶片材料主要是玻璃纤维复合材料和碳纤维复合材料。
未来的发展趋势是研发更轻、更坚固的材料,以提高叶片的耐久性和风能转化效率。
4. 多桨设计传统的风力发电机组一般采用三桨设计,但随着技术的发展,多桨设计也逐渐受到关注。
风机控制系统-变桨

4
工作原理
控制时一般都以发电机额定功率或转子转速为界,即当发电机输出功率(转
速)低于额定值时,进行变速恒频控制,最大捕获风能;而当输出功率(转 速)高于额定值时,进行变桨距控制,维持发电机功率在额定值附近。要实 现真正的独立变桨,输入变量包括桨叶节距角变化和风速,以及每个桨叶受力 等,实现多变量控制。
1、驱动故障 2、接触器故障 3、编码器溢出 4、通讯故障 5……
4、带照明灯、手机、对讲机
5……
18
问题讨论
1、变桨同步误差过大;(机械问题,反馈问题)
2、驱动器超温;(自然环境、电气环境) 3、电机超温;(电机本身、负载桨的构成-电动变桨
系统组成: 驱动器、电机、编码器、减速机、限位开关。
优点:组合灵活、技术成熟、环境适应能力强、防沙尘、腐蚀
缺点:容量增加时电机体积变大
8
工作原理
液压变桨 变桨距伺服控制系统的原理图如图1所示。变桨距控制系统由信 号给定、比较器、位置(桨距)控制器、速率控制器、D/A转换器、 执行机构和反馈回路组成。
风机控制系统
—— 变桨部分
目录
什么是变桨 变桨的类型
变桨的构成
变桨系统的工作原理 变桨各部件介绍 原理图示意 故障处理 问题讨论
1
变桨的概念
什么是变桨系统?
变桨系统是通过传动机构使叶片沿其纵向轴转动,改变气流对叶片攻角的系 统。 为什么大功率风机需要变桨系统? 它控制风力发电机组的叶片节距角可以随风速的大小进行自动调节:在低 风速起动时,桨叶节距可以转到合适的角度,使风轮具有最大的起动力矩; 当风速过高时,通过调整桨叶节距,改变气流对叶片的攻角,从而改变风力 发电机组获得的空气动力转矩,使发电机功率输出保持稳定。当机组故障或
变桨工作原理

变桨工作原理标题:变桨工作原理引言概述:变桨是现代风力发电机组中重要的组成部分,它通过调整叶片的角度来适应不同的风速和风向,从而优化发电效率。
本文将详细介绍变桨的工作原理,包括传动系统、控制系统、叶片角度调整原理、风速和风向检测以及变桨的效益。
一、传动系统1.1 齿轮箱:变桨系统中的齿轮箱负责将风力转换为机械能,并传递给叶片。
齿轮箱通常由多级齿轮组成,通过传动比例来适应不同的风速。
1.2 转子轴:转子轴是连接齿轮箱和叶片的重要部分,它承受着旋转力和扭矩。
转子轴通常采用高强度合金钢材料制造,以确保其耐用性和可靠性。
1.3 联轴器:联轴器连接转子轴和叶片轴,它能够传递转矩并允许叶片在变桨过程中调整角度。
联轴器的设计要考虑到叶片的旋转速度和扭矩传递的平稳性。
二、控制系统2.1 主控制器:主控制器是变桨系统的核心,它负责监测风速、风向和发电机组的运行状态,并根据预设的参数来调整叶片的角度。
主控制器采用先进的算法和传感器技术,以实现高效的风能利用。
2.2 电动机:电动机是控制叶片角度调整的执行器,主控制器通过电动机来实现叶片的旋转。
电动机的选择要考虑到扭矩输出和响应速度,以确保叶片能够及时调整角度。
2.3 传感器:传感器用于监测风速和风向,以提供准确的数据给主控制器。
常用的传感器包括风速传感器和风向传感器,它们能够实时检测风的变化,以便及时调整叶片的角度。
三、叶片角度调整原理3.1 风速检测:主控制器通过风速传感器获取当前的风速数据。
根据风速的大小,主控制器可以判断是否需要调整叶片的角度。
3.2 风向检测:风向传感器用于检测风的方向,主控制器可以根据风向的变化来调整叶片的角度,使其始终面向风的方向。
3.3 叶片角度调整:主控制器根据风速和风向的数据,通过控制电动机来调整叶片的角度。
当风速增大时,叶片的角度会增加,以提供更大的扭矩;当风速减小时,叶片的角度会减小,以避免过载。
四、风速和风向检测4.1 风速传感器:风速传感器通常采用超声波或热线等技术来测量风速。
变桨工作原理

变桨工作原理标题:变桨工作原理引言:变桨是风力发机电组中至关重要的部份,它通过转动桨叶来捕捉风能并将其转化为机械能,进而驱动发机电发电。
本文将详细介绍变桨的工作原理。
一、变桨的基本原理1.1 变桨的定义和作用变桨是指风力发机电组中的桨叶能够根据风速的变化,自动调整角度以最大限度地捕捉风能。
其作用是在不同风速下保持桨叶的最佳运行状态,提高风能的利用效率。
1.2 变桨系统的组成变桨系统由桨叶、主轴、变桨驱动机构和控制系统组成。
桨叶负责捕捉风能,主轴将桨叶的运动传递给发机电,变桨驱动机构负责调整桨叶角度,控制系统则监测风速并相应地调整桨叶角度。
1.3 变桨的工作原理当风速增大时,控制系统会根据传感器的反馈信号判断风速变化,并发出指令调整桨叶角度。
变桨驱动机构根据指令将桨叶转动到合适的角度,以使桨叶能够更好地捕捉风能。
相反,当风速减小时,控制系统会相应地调整桨叶角度,以避免过载运行。
二、变桨的工作原理详解2.1 桨叶的设计和材料选择桨叶的设计要考虑风力的捕捉效率、结构强度和分量等因素。
常用的桨叶材料有复合材料、玻璃钢和碳纤维等,这些材料具有轻质、高强度和耐腐蚀等特点。
2.2 变桨驱动机构的工作原理变桨驱动机构通过机电、减速器和液压装置等组成,当控制系统发出指令时,机电会驱动减速器工作,通过液压装置转动桨叶。
液压装置的设计要考虑承载能力、响应速度和稳定性等因素。
2.3 控制系统的工作原理控制系统通过风速传感器等设备监测风速,并根据预设的参数和算法判断是否需要调整桨叶角度。
一旦判断需要调整,控制系统会发出指令给变桨驱动机构,实现桨叶角度的调整。
三、变桨的优势和应用3.1 提高风能利用效率变桨系统能够根据风速的变化调整桨叶角度,使其在不同风速下保持最佳运行状态,从而提高风能的利用效率。
3.2 增加风力发机电组的稳定性变桨系统能够根据风速变化及时调整桨叶角度,避免过载运行,增加风力发机电组的稳定性和可靠性。
3.3 减少对环境的影响变桨系统能够根据风速变化调整桨叶角度,使桨叶始终处于最佳角度,减少了风力发机电组对环境的噪音和视觉影响。
- 1、下载文档前请自行甄别文档内容的完整性,平台不提供额外的编辑、内容补充、找答案等附加服务。
- 2、"仅部分预览"的文档,不可在线预览部分如存在完整性等问题,可反馈申请退款(可完整预览的文档不适用该条件!)。
- 3、如文档侵犯您的权益,请联系客服反馈,我们会尽快为您处理(人工客服工作时间:9:00-18:30)。
目录••••••••一、概述 (2)二、主要功能 (2)三、系统组成 (2)四、工作原理 (4)五、系统接口 (13)六、主要零部件 (13)七、系统功能性能指标 (17)八、人机界面操作说明 (20)九、用户车间调试 (30)十、风场调试维护 (35)一、概述HYP2.0-LT型变桨控制系统是重庆华渝电气仪表总厂专门针对中船重工(重庆)海装风电设备有限公司2MW风力发电机组,从国外引进的变桨控制技术,并通过自主国产化研制生产而成。
该变桨系统采用超级电容储能(作为后备电源),使用寿命长,充电时间短,且具有良好的耐低温性能;系统采用75V低压供电,全面提高操作人员和系统元器件的使用安全;系统采用三柜结构,组成简单,占用空间小,安装维护方便;系统采用冷板散热技术,实现柜体全密封设计,防护性能得到全面提升,能在恶劣环境中工作;系统采用模块化设计,线路简单;本系统元器件批量生产,可靠性高;同时保护功能完备,尤其是防雷性能优良。
二、主要功能变桨系统作为风力发电控制系统中重要组成部分,主要完成两项功能:一是根据风力发电机组运行要求控制桨叶变换到设定的角度以达到发电机设定的功率输出;二是根据风力发电机组运行或安全要求驱动桨叶变换到顺桨位置,即桨叶面到达顺风位置,使机组停机。
由于其对于风力发电系统安全性、可靠性起着至关重要的作用,因此理解本系统组成,工作原理等内容,对于正确操作与使用本系统显得尤为重要。
三、系统组成HYP2.0-LT型变桨控制系统见图1。
该系统由三个相对独立的控制单元组成,每个控制单元由控制柜、变桨电机、接近开关、限位开关组成。
每一个控制柜内由超级电容器模组、充电电源、变频驱动器、PLC 控制器及其外围模块以及控制保护线路及其电气元器件组成,详见图2。
图1:HYP2.0-LT型变桨系统图图2:HYP2.0-LT型变桨系统控制柜内部图三个控制单元分别控制三个桨叶,并通过Profibus总线与风力发电机组主控制器相连,成为主控制器的三个独立的Profibus从站,即主控制器可分别对三个控制单元进行控制。
三个控制单元之间相关联的部分是轮毂安全链,即三个控制单元分别给出一个干结点,三个结点串联形成轮毂安全链,详见图3。
我们可以从电气原理上简单理解为本变桨系统是有三个独立的控制单元和一条安全链组成。
其中图3中K1,K2,K3分别对应三个控制柜中的8k3继电器,当变桨系统无断安全链故障时,其8K3将闭合,使得安全链通路接通。
图3:系统组成原理框图四、工作原理本系统工作原理较复杂,但是整个控制方式都是围绕五种工作模式展开,简述这五种工作模式,对于理解工作原理大有裨益。
(一)工作模式1.自动运行模式当风速在12~25m/s时,即大于额定风速小于切出风速时,风力发电机组为了达到相对恒定的额定输出功率,需变换桨叶角度以获取相对恒定的风能,使发电机转速保持相对恒定。
变桨系统将根据风力发电机组主控制器指令,完成控制桨叶变换到设定角度的任务。
2.正常停机模式风电机组自动运行时,其处于自身运行需要或风场电力调度需要的停机为正常停机,变桨系统将根据主控制器指令控制桨叶回到89°顺桨位置,即桨叶面到达顺风位置。
3.紧急停机模式风电机组因紧急故障,比如主控、变流器或变桨系统本身故障,变桨系统将紧急顺桨。
如果是变桨系统以外的故障将顺桨到89°位置,如果是变桨系统本身故障则要根据是否能够判断桨叶位置来决定顺桨位置,如能判断位置则顺桨到89°,若不能则会直接撞击96°限位开关后停止。
其是否能够判断桨叶位置,主要是以编码器信号为主要依据,如果编码器信号正常,则称为能够判断桨叶位置,否则为不能判断。
4.维护模式即手动模式,在面向控制柜的左侧或下部有一个维护操作盒,内有电源开关、手动/自动转换开关、向前/向后开关、强制手动转换开关、电源和运行指示灯以及调试串口接口,详见图4。
手动自动的转换由机舱控制柜上的手动使能开关或变桨控制柜操作盒中的手动/自动转换开关控制,维护人员进入轮毂前须将机舱控制柜上的手动使能开关转动到手动位置,然后锁定主轴进入轮毂,进入轮毂后必须首先将控制柜操作盒中的手动/自动转换开关转换到手动位置。
变桨系统在维护模式下,轮毂外将无法操作变桨系统,从而保证轮毂内操作人员的安全。
在维护模式下,可以开启手动向前/向后开关,控制桨叶前进或后退。
手动控制一个桨叶的前提条件是:其他两个桨叶必须都在大于85°位置。
电源开关调试串口手动/自动开关向前/向后开关运行指示灯电源指示灯图4:操作盒5.强制手动模式当正常的手动模式受到限制无法转动桨叶,比如在对桨叶的零位时,可以利用本套系统特有的强制手动功能,将操作盒内的强制手动开关打开,开启向前/向后开关,桨叶将无条件转动。
(二)系统供电原理本系统有多种供电电压模式,对于其如何转化,如何供配电等,下图5给出了详尽描述。
图5:系统供电原理图在图中,三相400V电源经过主开关1Q1进入智能充电电源1G1、1G2,电源对系统后备电源超级电容2C1端电压进行实时检测,输出一略高于超级电容端电压的电源电压,在电容即将充满前,输出电流为一恒定电流,大约25~28A,两个电源并联输出50~56A,即将充满时,充电电流逐渐减小,直到充满75V后关闭输出。
当超级电容端电压放电到低于70V时,充电电源则重新启动充电,直到75V,如此反复充放电,形成智能充电电源正常的工作过程。
当系统载荷超过正常载荷,将导致超级电容加速放电,端电压下降到70V以下,则充电电源将与后备电源一起同时向外供电,尽力维持直流母线电压稳定在70~75V区间,以满足系统在各种工况下的能量需求。
连接在直流母线上的两个DC/DC模块为系统提供两路稳定的24V直流电源,一路专供PLC控制器使用,另一路为其余所有电路包括外围电路供电。
所以,直流母线的稳定是整个变桨系统正常工作的基础。
(三)系统控制原理,见图6。
图6:系统控制原理框图风力发电机组主控制器通过profibus通讯将速度、位置值发送给变桨系统PLC控制器,PLC控制器将速度信号解算为驱动器所需要的频率信号,通过CAN通讯发送给驱动器,驱动器驱动电机以给定的速度转动。
电机上安装的增量+绝对值编码器将速度信号反馈给驱动器以形成速度闭环控制、同时将位置信号反馈给PLC,PLC根据位置信号确定电机是否转动到指定位置,然后向驱动器发出相应的速度信号。
(四)安全保护原理1.本系统在轮毂内外都设置了手动/自动转换开关,任意一处转为手动系统都将进入手动状态,在手动状态下桨叶将根据操作人员的需求动作而不受主控制器控制,并且系统设定同一时间只允许一个桨叶离开顺桨位置,从而保证了风电机组在手动维护时的安全。
2.自动运行时,只要桨叶处于顺桨位置,对风电机组而言就是安全的。
本系统从以下三个方面保证了桨叶回到安全位置,即顺桨位置:a.当风电机组发生变桨系统以外的紧急故障,变桨系统将首先收到来自主控的安全保护信号,执行主控指令紧急顺桨。
b.当变桨系统本身发生故障时,将首先切断轮毂安全链,告知主控系统整个风电机组需紧急停机,同时自身紧急顺桨,并通过profibus通讯将故障信息发送给主控。
c.当变桨系统本身发生故障且无法控制驱动器或驱动器外围故障时,驱动器自身将驱动桨叶向顺桨方向转动直至撞击96°限位开关而停止。
3.本系统中,驱动器的可靠性对整个风电机组的安全保证作用是至关重要的。
本系统选用原装进口低压交流伺服驱动器,该驱动器原用于电动汽车上,后被引用到风电变桨系统中,获得了极大的成功。
该驱动器经过了风场长时间大批量的实际运行考核,故障率极低。
该驱动器在设计上考虑了充足的裕量,能够适应风电机组实际运行中的各种复杂工况。
对于直流70-80V的电压输入,都能工作良好,而且自身保护功能完善,对外围以及自身故障的处理及时合理,可靠性很高,从根本上保证了风电机组的运行安全。
4.低电压穿越功能是国家电网对风力发电机组也是对变桨系统的基本要求,这是电网安全的需要。
本系统从设计原理上决定了其低电压穿越性能是原蓄电池系统所无法比拟的,因为它的直流母线上挂载有大容量的储能设备超级电容。
如果电机不带负载,电网即使断电1小时,本系统同样可以在超级电容放电的情况下正常工作;即使电机带有负载,在额定负载条件下也可以运行近20S,完全能够支撑三次顺桨,大大超过了低电压穿越标准所要求的时间。
(五)位置校对原理本变桨系统没有冗余编码器,桨叶角度的校对是依靠安装在3°和88°位置的两个接近开关实现的。
在3°和88°接近开关机械安装牢固后,调试人员需要对这两个位置进行检测标定,并将这两个位置的最终检测位置值和编码器的实际值保存到PLC的掉电保持单元中。
在实际运行时,桨叶每次经过这两个位置,控制器都会将这个位置的角度值和编码器值与原保存的值进行比较,如果误差超过设定值,系统将报故障停机。
(六)系统电气原理图如下:1023456789图7:系统外部接线图五、系统接口(一)变桨系统与主控系统接口关系,见表1。
表1:变桨系统与主控系统接口关系表(二)变桨系统与集中润滑的接口关系变桨系统为集中润滑提供一路24V直流电源,集中润滑将自身故障信号反馈给变桨系统,变桨系统通过通讯发送给主控。
六、主要零部件(一)主电源,见图8。
主电源模块是系统的能量来源,采用两个单相AC/DC模块并联的方式使用,每个模块的输出功率为75V×25A,其主要作用是为超级电容充电和维持直流母线电压的相对稳定,以及为辅助电源提供输入和在系统超负荷运行时与超级电容一起为伺服机构提供能量,并通过CAN接口向控制器传送自身状态、故障信息。
图8:主电源模块(二)超级电容器组,见图9。
超级电容器组是系统的后备电源,电容容量为75V94F,最长充电时间为150S,在系统断电以后,可以提供至少三次顺桨的能量。
图9:超级电容器组(三)变频驱动器,见图10。
变频驱动器是系统的核心关键部件,额定输出功率6.5kW,最大输出电流超过400A。
通过CAN总线与PLC控制器进行数据交换,接收执行PLC控制器的电源、刹车、主接触器使能和速度等指令,同时接收编码器信号并解算为实际运行速度后送给PLC控制器。
变频驱动器最重要的作用是在各种情况下(手动维护、自动运行、系统故障)都能可靠地驱动电机带动桨叶运转到指定位置。
图10:变频驱动器(四)变桨电机,见图11。
变桨电机是系统的执行部件,额定功率为6.0KW,额定转矩为40Nm,最大转矩达120Nm,工作电压是交流三相33V,工作电流165A。
附带电磁制动器、温度传感器、编码器。
图11:变桨电机(五)辅助电源,见图12。