粉末成型技术
陶瓷粉末成型技术的工艺与控制

国内发展现状:国内陶瓷粉末成型技术的研究和应用已经取得了一定的进展,但与国际先进水平相比仍存在一定 差距。
国外发展现状:国外陶瓷粉末成型技术的研究和应用已经非常成熟,具有较高的技术水平和应用范围。
国内外技术对比:国内外陶瓷粉末成型技术在技术原理、设备结构、工艺流程等方面存在一定的差异,需要根据 具体应用场景进行选择。
设备故障排除:及时排除设备故障,避免影响生产进度和产品质量
温度控制:确保烧结过程中的温度稳定,避免过热或欠热 压力控制:通过调整压力,控制陶瓷粉末的压缩比和密度 时间控制:合理安排各个工艺阶段的时间,确保陶瓷粉末充分成型 气氛控制:保持适宜的烧结气氛,避免氧化或还原反应对产品的影响
质量检测:对陶 瓷粉末成型过程 中的各个环节进 行严格的质量检 测,确保产品质
陶瓷粉末成型技术将不断向高精度、高效率、低成本方向发展 3D打印技术将进一步应用于陶瓷粉末成型领域 智能化、自动化技术将不断应用于陶瓷粉末成型生产过程中 环保、可持续发展将成为陶瓷粉末成型技术的重要发展方向
感谢您的观看
汇报人:
粉末压制成型
凝胶注模成型
喷射成型
注射成型
烧结工艺原理 烧结温度与时间 烧结气氛与压力 烧结过程中的影响因素
烧结工艺:将陶瓷粉末加热至高温,使其致密化并形成坚硬的陶瓷材料 表面处理:对陶瓷表面进行涂层、镀膜等处理,提高其耐磨、耐腐蚀等性能
切割和加工:对烧结后的陶瓷进行切割、磨削等加工,以满足特定形状和尺寸的要求
陶瓷粉末成型技术的 工艺与控制
汇报人:
目录
添加目录标题
陶瓷粉末成型技术概 述
陶瓷粉末成型工艺
陶瓷粉末成型工艺的 控制要素
陶瓷粉末成型技术的 挑战与解决方案
粉末冶金与陶瓷材料的成型工艺技术

粉末冶金与陶瓷材料的成型工艺技术粉末冶金是一种重要的材料成型技术,它通过将金属或非金属粉末在高温下压制成形,进而得到各种金属零件和陶瓷材料。
粉末冶金不仅可以制造出形状复杂的零件,还能够获得优良的材料性能,因此被广泛应用于汽车、航空、航天等工业领域。
粉末冶金的成型工艺技术主要分为两个步骤:粉末的制备和成型。
首先是粉末的制备。
粉末冶金所需的粉末通常通过机械研磨、化学反应、气相沉积等方法制备而成。
机械研磨是最常用的方法,它通过将金属块或合金块放入球磨机中与磨料球一起进行高速旋转,使金属块逐渐研磨成粉末。
化学反应法利用化学反应生成粉末,例如气相法将金属气体于高温下反应生成粉末。
制备好的粉末应具备一定的粒度、形状和分布以满足成型的需求。
其次是成型工艺技术。
成型是将粉末压制成所需形状的过程。
常用的成型工艺有冷压成型、等静压成型和注浆成型等。
冷压成型是最简单的成型方法,它通过将粉末放置在模具中,然后在模具上施加压力,使粉末紧密结合成形。
但冷压成型得到的零件强度较低,通常需要进行后续的烧结工艺。
等静压成型是常用的粉末冶金成型方法。
它通过在模具中施加等压力,使粉末均匀密实地填充模具,然后通过高温烧结使粉末颗粒结合成致密的金属材料。
等静压成型可以获得高密度、高强度的零件,适用于制造各种金属零件。
注浆成型是粉末冶金的一种新型成型工艺。
它通过在模具中注入粉末与流体混合物,然后通过高压使混合物注入模具的空隙中,最后再进行烧结。
注浆成型可以制造出形状复杂的零件,并且具有较高的密度和强度。
总之,粉末冶金是一种重要的材料成型技术,它通过粉末的制备和成型工艺来制造各种金属零件和陶瓷材料。
不同的成型工艺可以得到不同性能的材料,所以在应用中需要根据具体要求来选择合适的成型工艺。
粉末冶金是一种重要的材料成型技术,其广泛应用于汽车、航空、航天等众多领域。
通过将金属或非金属粉末在高温下压制成形,可获得形状复杂且性能优良的材料。
下面将进一步探讨粉末冶金与陶瓷材料的成型工艺技术。
粉末冶金成型技术

粉末冶金成型技术粉末冶金成型技术是一种把制备的金属粉末混合成型的现代金属加工技术。
它有可能把任何金属粉末结合成复杂的物体,如构件和复杂的零件等,它不仅可以为生产有特殊形状的零件提供方便,而且可以减少材料的消耗,节省制造时间和成本。
粉末冶金成型技术分为热压成形和冷压成形两种。
热压成形是指把高温粉末压入模具,然后经过压力和高温处理,最后用特殊工艺把模具内的粉末变成给定形状。
冷压成形是指把低温粉末压入模具,然后经过一系列特殊工艺把粉末结合在一起形成一定形状的产品,最后通过高温固化使其变得坚硬。
粉末冶金成型技术不仅可以生产复杂形状的金属零件,而且可以满足生产小批量或单件零件的需求。
典型的应用包括机械零件、航空零件、航天用零件等。
粉末冶金成型技术具有一定的优势,首先,它可以实现复杂零件的加工,这避免了大多数切削加工工艺所面临的技术难题和加工费用的消耗;其次,它可以更有效地实现性能优良的零件,因为贴合技术可以把比普通切削加工技术更少的原料消耗量转变成更多的形状和功能;第三,它还可以在多种金属材料之间制造合金化的零件,并满足不同应用场合的要求。
此外,粉末冶金成型技术还可以在极低温和极高温环境中使用,并可以产生可靠的重复性和准确性,从而提供极低的废品率。
然而,粉末冶金成型技术也存在一些缺点。
正如上文所述,它依赖于模具和高温条件,且受模具形状限制,模具设计和开发费用也较高;对于密度更大的零件,贴合可能较其他方法的成本更高;因为模具的硬度较大,所以它的滑动性能不太好;另外,粉末冶金技术的产品有一定的粗糙性,很难达到高精度要求。
总之,粉末冶金成型技术是一种重要的金属加工技术,可以大大提高零件加工效率并降低成本。
然而,也有一些缺点需要解决,比如模具的高温及耐磨性、模具制造的费用高等,但只要正确使用粉末冶金技术,就能满足企业的实际需求。
陶瓷粉末注射成型技术

陶瓷粉末注射成型技术哎,你听说过陶瓷粉末注射成型技术吗?这玩意儿可真是高科技啊,我最近在研究这个,感觉自己都快成半个专家了。
你知道吗,这技术就是把陶瓷粉末和有机粘结剂混合在一起,然后注射到模具里成型。
听起来简单,但里面的门道可多了去了。
我记得有一次,我和老李在实验室里捣鼓这个,他一边搅拌着那些粉末,一边嘴里念叨着:“这玩意儿要是弄不好,可就全废了。
”我看着他那副认真的样子,忍不住笑出声来:“老李,你这架势,不知道的还以为你在炼丹呢!”他瞪了我一眼,说:“你小子别笑,这可比炼丹难多了。
”那天我们试了好几次,每次出来的成品都不太理想。
要么是密度不够,要么是表面有瑕疵。
老李急得直挠头,我看着他那副模样,心里也跟着着急。
后来我们决定换个思路,调整了一下粘结剂的比例,结果还真成了!看着那件完美的陶瓷制品从模具里取出来,我和老李都乐坏了,差点没抱在一起庆祝。
这技术虽然复杂,但做出来的东西可真是漂亮。
我记得有一次,我们用这技术做了一批陶瓷饰品,拿到市场上卖,结果一下子就被抢光了。
那些顾客都说,这东西既精致又耐用,比那些普通的陶瓷制品强多了。
我听了心里那个美啊,感觉自己这几个月的辛苦没白费。
不过,这技术也有它的局限性。
比如,对材料的要求特别高,稍微有点杂质就会影响成品的质量。
还有,成型后的脱脂和烧结过程也很关键,稍有不慎就可能前功尽弃。
所以,每次做实验的时候,我都特别小心,生怕出什么差错。
有一次,我和老李在实验室里忙活了一整天,结果还是没成功。
我累得瘫坐在椅子上,老李却还在那儿琢磨。
我看着他那副认真的样子,心里突然有种说不出的感动。
这老李,平时看着大大咧咧的,但做起事来还真是一丝不苟。
后来,我们终于找到了问题的关键,调整了一下工艺流程,结果一下子就成功了。
那天晚上,我和老李一起去喝了顿酒,庆祝我们的胜利。
酒桌上,老李拍着我的肩膀说:“小子,咱们这回可算是摸到门道了,以后可得好好干,别辜负了这门技术。
”我听了,心里暖洋洋的,感觉自己肩上的担子更重了。
粉末注射成型技术介绍

粉末注射成型技术介绍粉末注射成形概述:粉末注射成形(Powder Injection Molding,PIM)由金属粉末注射成形(Metal Injection Molding,MIM)与陶瓷粉末注射成形(Ceramics Injection Molding,CIM)两部分组成,它是一种新的金属、陶瓷零部件制备技术,它是将塑料注射成形技术引入到粉末冶金领域而形成的一种全新的零部件加工技术。
MIM的基本工艺步骤是:首先选取符合MIM要求的金属粉末和黏结剂,然后在一定温度下采用适当的方法将粉末和黏结剂混合成均匀的喂料,经制粒后再注射成形,获得成形坯(Green Part),再经过脱脂处理后烧结致密化成为最终成品(White Part)。
粉末注射成形技术的特点:粉末注射成形能像生产塑料制品一样,一次成形生产形状复杂的金属、陶瓷零部件。
该工艺技术利用注射方法,保证物料充满模具型腔,也就保证了零件高复杂结构的实现。
以往在传统加工技术中,对于复杂的零件,通常是先分别制作出单个零件,然后再组装;而在使用PIM技术时,可以考虑整合成完整的单一零件,这样大大减少了生产步骤,简化了加工程序。
1、与传统的机械加工、精密铸造相比,制品内部组织结构更均匀;与传统粉末冶金压制∕烧结相比,产品性能更优异,产品尺寸精度高,表面光洁度好,不必进行再加工或只需少量精加工。
金属注射成形工艺可直接成形薄壁结构件,制品形状已能接近或达到最终产品要求,零件尺寸公差一般保持在±0.10%~±0.30%水平,特别对于降低难以进行机械加工的硬质合金的加工成本、减少贵重金属的加工损失尤其具有重要意义。
2、零部件几何形状的自由度高,制件各部分密度均匀、尺寸精度高,适于制造几何形状复杂、精度密高及具有特殊要求的小型零件(0.2~200g)。
3、合金化灵活性好,对于过硬、过脆、难以切削的材料或原料铸造时有偏析或污染的零件,可降低制造成本。
粉末冶金成型技术

粉末冶金成型技术Ⅰ、粉末冶金成型技术1、粉末冶金成型技术(Powder Metallurgy)是一种较新的金属制造工艺,它通过将金属粉末或粉体团结成模具内所需形状,从而生产出广泛应用的金属零件。
其原理是金属粉末经高压热压成型而形成零件。
2、粉末冶金成型技术能够制造出具有较高精度、更小体积的零件,是传统金属制造技术无法达到的高精度和大精度的紧凑零件。
同时,由于具有良好的耐磨性,它还可以制造可耐高速摩擦的零件。
3、粉末冶金成型技术使用金属粉末来制造零件,因此可以制造出大规模和复杂零件。
它制造出的产品可以达到更高的均匀度、更高的精度和更强的密度,这些特点比其他技术都有优势。
II、工艺流程1、把金属粉末混合成易流动的糊状物:在粉末冶金成型过程中,首先将金属粉末混合成易流动的糊状物,然后将其成型成所需的各类结构。
2、金属流成型:将调制好的金属流放入到模具中,然后将其投射成型,采用精确的高压成型,以形成模具内期望的形状。
3、表面处理:一些金属零件可能需要再进行表面处理,比如镀铬、电镀和热处理,以满足零件性能的需求,增强其耐蚀性、耐磨性等。
4、热处理:热处理是利用复杂的热处理技术,通过改变零件的温度来改变其组织和性能,以获得期望的性能和表面光洁度。
III、优点1、体积小:由于采用精密模具来进行流体压力成型,可以制造出具有较小体积和精确尺寸的部件;2、准确精度:粉末冶金成型可以根据模具进行长宽比、曲率与折弯处理,以达到较高的精度,组装时也相对容易;3、节能降耗:比传统金属加工手段更加节省能源耗费,而且粉末冶金可以减少冶炼及清理成本,从而降低成本;4、结构复杂:粉末冶金制造的零件可以根据设计形状进行复杂的结构设计,可在一个工件上制造气隙空间及护套,从而更加省时。
IV、缺点1、成本高:粉末冶金技术的设备耗费较高,使得生产成本比其他工艺高很多;2、尺寸大小限制:模具的设计尺寸受生产设备的尺寸限制,影响着大小尺寸和深度尺寸的生产;3、生产周期长:由于加工方法比其他工艺复杂,因此所需的生产周期也变得更长;4、表面光洁度差:因为运用压力成型,而非切削加工,因此物件的表面光洁度不是非常理想。
金属粉末注射成型技术规程
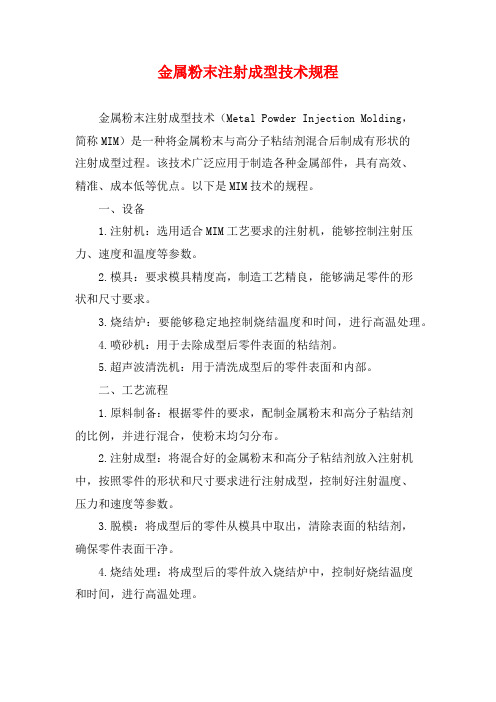
金属粉末注射成型技术规程金属粉末注射成型技术(Metal Powder Injection Molding,简称MIM)是一种将金属粉末与高分子粘结剂混合后制成有形状的注射成型过程。
该技术广泛应用于制造各种金属部件,具有高效、精准、成本低等优点。
以下是MIM技术的规程。
一、设备1.注射机:选用适合MIM工艺要求的注射机,能够控制注射压力、速度和温度等参数。
2.模具:要求模具精度高,制造工艺精良,能够满足零件的形状和尺寸要求。
3.烧结炉:要能够稳定地控制烧结温度和时间,进行高温处理。
4.喷砂机:用于去除成型后零件表面的粘结剂。
5.超声波清洗机:用于清洗成型后的零件表面和内部。
二、工艺流程1.原料制备:根据零件的要求,配制金属粉末和高分子粘结剂的比例,并进行混合,使粉末均匀分布。
2.注射成型:将混合好的金属粉末和高分子粘结剂放入注射机中,按照零件的形状和尺寸要求进行注射成型,控制好注射温度、压力和速度等参数。
3.脱模:将成型后的零件从模具中取出,清除表面的粘结剂,确保零件表面干净。
4.烧结处理:将成型后的零件放入烧结炉中,控制好烧结温度和时间,进行高温处理。
5.机械加工、表面处理:将烧结后的零件进行机械加工和表面处理,使零件达到要求的尺寸和表面粗糙度要求。
6.检验、包装:对成品进行检验,合格后进行包装。
三、质量控制1.原料质量控制:保证金属粉末和高分子粘结剂的质量符合规定要求,严格管控原料供应商。
2.工艺参数控制:精细控制注射温度、压力和速度等参数,保证零件的成型质量。
3.产品检验:对成品进行尺寸、外观等方面的检验,并严格把关。
4.持续改进:根据生产实际情况,不断优化工艺流程,提高生产效率和产品质量。
四、安全生产1.操作人员应接受严格的培训和考核,熟练掌握操作技能和注意安全规定。
2.设备维护保养应按时按方法进行。
3.操作过程中,严格遵守操作规程和安全规定,确保人身和设备安全。
以上就是金属粉末注射成型技术规程,通过规范化的操作流程和严格的品质控制,可以达到生产出高品质、高精度的金属零件的目的。
CIM陶瓷粉末注射成型技术ppt课件

脱脂工艺
• 脱脂是通过加热及其它物理方法将成型体内的有机 物排除并产生少量烧结的过程。与配料、成型、烧 结及陶瓷部件的后加工过程相比,脱脂是注射成型 中最困难和最重要的因素。脱脂过程不正确的工艺 方式和参数使产品收缩不一致,导致变形、开裂、 应力和夹杂。脱脂对其后烧结也很重要,在脱脂过 程中产生的裂纹和变形不能通过烧结来弥补。粘结 剂和脱脂是联系在一起的,粘结剂决定脱脂方式。 目前的脱脂工艺除了传统的热脱脂、溶剂脱脂外, 还有最近几年发展起来的催化脱脂以及水基萃取脱 脂.
陶瓷粉末注射成型技术应用
随着CIM技术的快速发展,其已在一些方面得到了应用 • 瑞士三分之一的手表表壳采用CIM技术生产,材料是称永不磨损的
陶瓷材料氧化锆 • 日本已将内孔直径为0.015mm的氧化锆光纤接头实现产业化,每年
垄断了全球数亿美元的市场 • 美国已实现氧化锆理发推剪的生产和发动机中氮化硅零部件的应用
CIM中几种常见的粘结剂组成
近年来国际上各种陶瓷粉末注射成型中经常用到的较典型的粘结剂,从表中可以
看出,CIM中用粘结剂体系还主要属于热塑性多组分体系。
CIM混料制备
• 混料是粉末和粘结剂的混合物。在整个注射成型的工艺中,粉末和 聚合物粘结剂混合物的制备是最重要的步骤之一。工艺要求混料具 有良好的均匀性、良好的流变特性,以及好的脱脂特征。只有这三 个方面都照顾到的粉末注射系统才是一个成功的体系。
• 粉末注射成型源于20世纪20年代的一种热压铸成型技术,当时已用于生产汽车 火花塞等产品。
• 20世纪50年代,用环氧树脂作粘结剂试制了大量的硬质合金、难熔金属、陶瓷 等,预示着此技术在应用中的地位。但因理论欠缺,加之制粉、成型和烧结等 技术存在一系列不足,离应用的距离还比较远。
- 1、下载文档前请自行甄别文档内容的完整性,平台不提供额外的编辑、内容补充、找答案等附加服务。
- 2、"仅部分预览"的文档,不可在线预览部分如存在完整性等问题,可反馈申请退款(可完整预览的文档不适用该条件!)。
- 3、如文档侵犯您的权益,请联系客服反馈,我们会尽快为您处理(人工客服工作时间:9:00-18:30)。
▪ 润滑剂 ▪↓粉末颗粒与模壁间的摩擦 ▪改善压坯密度分布不均匀 ▪影响被压制工件的表面质量 ▪降低模具的使用寿命
▪ 粉末压制用的润滑剂 ▪硬脂酸 ▪硬脂酸锌 ▪工业润滑蜡 ▪二硫化钼、石墨粉、硫磺粉也 可起润滑作用
▪ 润滑方式:
▪粉末内润滑 ▪润滑剂直接加入粉末中 ▪铁基粉末:润滑剂含量提高0.1%,坯件的 无孔隙密度下降0.05g/cm3
▪ 颗粒间的结合强度 ▪ 颗粒表面的粗糙度 ▪ 颗粒形状 ▪ 颗粒表面洁净程度 ▪ 压制压力 ▪ 颗粒的塑性
▪ 颗粒间接触面积 ▪ 即颗粒间的邻接度 contiguity ▪ 颗粒的显微硬度 ▪ 粒度组成 ▪ 颗粒间的相互填充程度 ▪ 压制压力 ▪ 颗粒形状
▪ 外在因素:残余应力大小
▪压坯密度分布的均匀性 ▪粉末的填充均匀性 ▪粉末压坯的弹性后效 ▪模具设计的合理性 ▪过高的压制压力
挤压成型
末
燒結初期
燒結中期
燒結末期之表面
燒結後之破斷面
▪压力作用下,松散状态→拱桥效应的破坏 (位移→颗粒重排)+颗粒塑性变形→孔隙 体积收缩→致密化
▪ 拱桥效应 bridge effect ▪颗粒间由于摩擦力的作用而相互搭架形成 拱桥孔洞的现象
▪ 影响因素
▪与粉末松装密度、流动性存在一定联系 ▪颗粒形状 ▪粒度及其组成 ▪颗粒表面粗糙度 ▪颗粒比重(含致密程度)
▪与坯件的弹性模量,残留应 变量即弹性后效及其与模壁 之间的摩擦系数直接相关
润滑(摩擦系数)对脱模力的影响
2 压坯密度分布均匀性及控制
▪ 压坯密度分布不均匀的后果
▪不能正常实现成形,如出现分层,断裂,掉边角 等 ▪烧结收缩不均匀,导致变形
▪ 因素
▪高径比H/D ▪↑H/D,ρ↓,dρ/dX ↑ ▪当H/D→∞,压坯的下部粉末无法成形
▪浸铜 ▪密度大于95%,但表面较粗糙,形状、成 分设计有限,成本高
▪ 液相烧结 ▪密度可达93%,变形较大,零件精度低, 尺寸控制困难,成分设计有限
▪ 粉末锻造 ▪全致密,但尺寸精度低,形状受限,成本 昂贵
成型方式
▪ 非模压成形 ▪ 模压成形
▪冷、热等静压 ▪注射成形 ▪粉末挤压 ▪粉末轧制 ▪粉浆浇注 ▪喷射成形 ▪爆炸成形
轿车部件
电动工具与汽车部件
齿轮保持架(Ford)
汽车发动机用粉末烧结钢零件
汽车变速器系统用粉末烧结钢件
P/F连杆
不锈钢注射成形件
▪ 成形和烧结过程
▪ 控制粉末冶金材料及其部件的微观结构 ▪ 主宰着粉末材料及其部件的应用
粉末成形
powder shaping or forming
▪ 成形:成型是将松散的粉体加工成具有一定 尺寸、形状以及一定密度和强度的坯块。 ▪粉末颗粒间的结合力为机械啮合力或范德 华力
压坯密分布
Z
X
结论
在没有润滑剂的情况下,模壁摩擦 力的压力损失很大,可达60~90%。 由于压力沿压模轴向分布不均,造 成压坯的密度不均匀现象。加入润 滑剂能够改善这一现象。
3 复杂形状部件的成形
▪ 密度分布的控制 ▪多台阶零件:恒压缩比
4 压制缺陷的控制
▪ 主要缺陷类型、成因 ▪分层 ▪沿坯件棱边向内部发展的裂纹, 与压制面形成大约45度的界面 ▪弹性后效
▪ 混合方式 ▪干混法:铁基及其它粉末冶金零件的生产
▪湿磨法:硬质合金或含易氧化组份合金的 生产
▪WC与Co粉之间除产生一般的混合均匀 效果,还发生显著的细化效果
▪一般采用工业酒精作为研磨介质
▪ 湿磨的主要优点 ▪有利于环境保护 ▪无粉尘飞扬和减轻噪音 ▪提高破碎效率,有利于粉末 颗粒的细化
▪保护粉末不氧化
▪ 控制方法 ▪适当降低压制压力 ▪复杂件应提高密度分布均匀性
孔隙的消极贡献
▪ 造成应力集中,降低零部件的强度和 韧性
▪ 孔隙降低材料的热导性能,抑制热处 理潜力对
▪ 力学性能改善的贡献:降低缺口敏感 性
▪ 提高铁基P/M零部件密度的技术途径 ▪复压-复烧工艺 ▪密度达92%左右,形状复杂程度有限,成 本较高
§2 压制现象
1 颗粒的位移与变形 1.1 粉末颗粒位移
▪ 位移方式:
▪滑动与转动 ▪颗粒重排列 Particle rearrangement or repacking(restacking)
▪ 影响因素
▪粉末颗粒间内摩擦 ▪表面粗糙度 ▪润滑条件 ▪颗粒的显微硬度 ▪颗粒形状 ▪颗粒间可用于相互填充的空间(孔隙 度) ▪加压速度
②流动性差的粉末:细粉或轻质粉末
▪ 成形剂作用
▪适当增大粉末粒度,减小颗粒间的 摩擦力
▪改善粉末流动性,提高压制性能
▪成形剂材料:橡胶、硬脂酸、石蜡、 SBS 、PEG、PVA等
▪ 选择准则 ▪能赋予待成形坯体以足够的强度 ▪易于排除 ▪成形剂及其分解产物不与粉末发生 反应
▪分解温度范围较宽 ▪分解产物不污染环境
1.2 粉末的变形
▪弹性变形
▪颗粒间的接触应力≤材料弹性极限
▪塑性变形
▪颗粒接触应力≥金属的屈服强度 ▪点接触处局部→面接触处局部→整 体
▪断裂
▪ 受力过程的三个阶段
▪ 第一阶段:粉末颗粒重排,颗粒间的架桥现
象被部分消除且颗粒间的接触程度增加;
▪ 第二阶段:颗粒弹塑性变形,塑性变形的大
小取决于粉末材料的延性。但是,同样的延 性材料在一样的压力下,并不一定得到相同 的坯体密度,还与粉末的压缩性能有关;
▪ 混合均匀程度和效率取决于 ▪粉末颗粒的尺寸及其组成 ▪颗粒形状 ▪待处理粉末组元间比重差异 ▪混合设备的类型 ▪混合工艺
3) 成形剂和润滑剂
成形剂应用于:
①硬质粉末:如硬质合金,陶瓷等 ▪粉末变形抗力很高 ▪难以通过压制所产生的变形而赋予粉末 坯体足够的强度 ▪添加成形剂的方法以提高生坯强度,利 于成形
▪颗粒表面粘附作用(颗粒的磁性、陶瓷 颗粒的静电、液膜存在)
P/M Tungsten Lightbulb Filament: 500 hrs at 2500C
▪ 塑性变形阻力的影响因素
▪颗粒的显微硬度 ▪合金化 ▪酸不溶物 ▪氧化物 ▪原子间作用力 ▪加工硬化速度(晶体结构) ▪颗粒形状 ▪粉末粒度 ▪压制速度
▪ Cold compaction with 100 – 900 MPa to produce a “Green body”.
1 压制前粉末料准备 1) 还原退火 reducing and annealing ▪ 作用:
▪降低氧碳含量,提高纯度 ▪消除加工硬化,改善粉末压制性能 ▪粉末钝化 ▪使细粉末适度变粗,或形成氧化薄膜,防止 粉末自燃
侧压系数
▪ 在距上冲为X处的有效外压Px Px=Poexp(-4ξμX/D)
▪ D为模腔内径
▪ 模壁作用在粉末体上的侧压力
和摩擦力也呈现相似的分布
润滑剂对压制的影响
1--用硬脂酸润滑模壁 2、3--用二硫化钼润滑模壁 4--无润滑剂
2 脱模压力(ejection force)
▪ 静脱模力(striping force) ▪ 滑动脱模力(sliding force)
▪模壁润滑 ▪静电喷涂 ▪溶液涂敷
4) 制粒 pelletizing or granulating ▪ 为细小颗粒或硬质粉末而设计 ▪ 应用于:
▪进行自动压制或压制形状较复杂的大 型P/M制品 ▪ 原理
▪借助于聚合物的粘结作用将若干细小 颗粒形成团粒
▪ 好处:
▪减小团粒间的摩擦力 ▪大幅度降低颗粒运动时的摩擦面积
▪ 第三阶段:颗粒断裂。不论是原本脆性的粉
体如陶瓷粉末、还是在压制过程中产生加工 硬化的脆化粉体,都将随着施加压力的增加 发生脆性断裂形成较小的碎块。
▪ 脆性粉末 ▪点接触应力>断裂强度 ▪→断裂
▪ 塑性粉末 ▪点接触应力>屈服强度 ▪→塑性变形 ▪→加工硬化 ▪→脆化→断裂
2 致密化现象
2.1 致密化
2.2 弹性后效 Springback ▪反致密化现象 ▪压坯脱出模腔后尺寸胀大的现象 ▪残留内应力释放的结果
▪ 弹性后效与残留应力相关 ▪压制压力 ▪粉末颗粒的弹性模量
3 压坯强度Green strength
▪ 表征压坯抵抗破坏的能力,即颗粒间 的粘结强度
▪ 影响因素 ▪本征因素 ▪颗粒间的结合强度(机械啮合 mechanical interlocking)和接触 面积
▪ 表征方法
▪抗弯强度或转鼓试验的压坯 重量损失
§3 压坯密度与压制压力间的关系
1 压制过程力的分析
P施加在模腔中的粉末体 ▪ 粉末向周围膨胀→侧压力
Fn(Pn) ▪ 粉末与模壁之间出现相对
运动→摩擦力Ff(Pf) ▪ 下冲头的压力Pb
开始压制
压制结束
P侧 P总 P摩 P总
摩擦系数
▪ 退火温度 ▪高于回复-再结晶温度(0.5-0.6)Tm
▪ 退火气氛 ▪还原性气氛(CO,H2) ▪惰性气氛(N2,Ar) ▪真空
▪ 2) 合批与混合 blending and mixing ▪ 混合
▪将不同成分的粉末混合均匀的过程 ▪ 合批
▪同类粉末(或粉末混合物)混合均匀的过 程
▪ 目的: ▪消除因粉末在运输过程中产生的偏析或 在粉末生产过程中不同批号粉末之间的性 能差异,获得性能均匀的粉末料