金属粉末注射成型技术
金属粉末的注射成型

金属粉末的注射成型金属粉末的注射成型,也被称为金属粉末注射成型(Metal Powder Injection Molding,简称MIM),是一种先进的制造技术,将金属粉末与有机物相结合,通过注射成型和烧结工艺,制造出高密度、精确尺寸、复杂形状的金属零件。
在金属粉末注射成型过程中,首先将金属粉末与有机粘结剂和其他添加剂混合均匀,形成金属粉末/有机物混合物。
其次,在高压下,将混合物通过注射机注射到具有细微孔隙和管道的模具中。
模具通常采用两片结构,上模和下模之间形成的形状即为所需制造的零件形状。
注射机将足够的压力用于将混合物推进模具的每一个细微空间,以确保零件形状准确,毛边小。
注射后,模具中的混合物开始固化,形成绿色零件。
最后,通过烧结处理,去除有机物并使金属颗粒结合成整体,形成具有理想密度和力学性能的金属粉末零件。
相对于传统的金属加工方法,金属粉末注射成型具有以下优势:首先,MIM可以制造复杂形状的金属零件,包括薄壁结构、内外复杂曲面和细小结构,满足了一些特殊零件的制造需求。
其次,MIM的材料利用率高,废料少,可以减少原材料和能源的浪费。
此外,零件的尺寸稳定性好,需要的加工工序少,可以降低生产成本。
最重要的是,对于一些其他制造工艺难以实现的金属材料,例如高强度不锈钢、钨合金和钛合金,MIM可以实现高质量的制造。
然而,金属粉末注射成型也存在应用范围的限制。
首先,相对较高的制造成本使得该技术在一些低成本产品上难以应用。
其次,较大的尺寸限制了MIM在制造大尺寸、高精度的零件上的应用。
此外,与其他成型方法相比,MIM的制造周期较长,对行业响应速度要求较高的场景不适用。
尽管如此,金属粉末注射成型技术已经在汽车、电子产品、医疗器械、工具和航空航天等领域得到了广泛的应用。
随着制造技术的进步和材料属性的改进,金属粉末注射成型有望在更多领域发挥其优势,并带来更多创新的解决方案。
MIM技术介绍
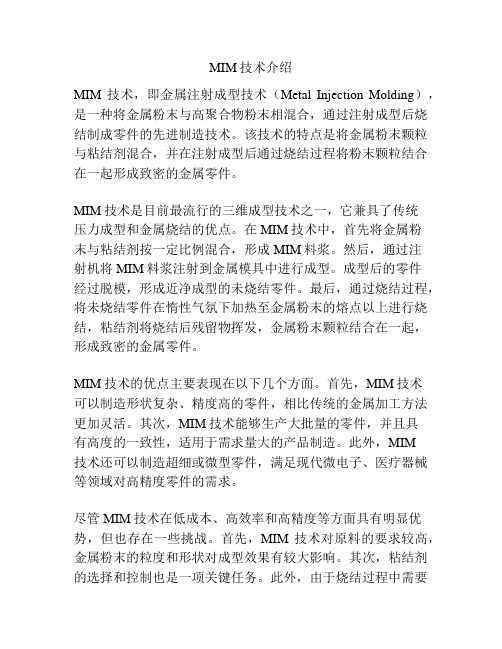
MIM技术介绍MIM技术,即金属注射成型技术(Metal Injection Molding),是一种将金属粉末与高聚合物粉末相混合,通过注射成型后烧结制成零件的先进制造技术。
该技术的特点是将金属粉末颗粒与粘结剂混合,并在注射成型后通过烧结过程将粉末颗粒结合在一起形成致密的金属零件。
MIM技术是目前最流行的三维成型技术之一,它兼具了传统压力成型和金属烧结的优点。
在MIM技术中,首先将金属粉末与粘结剂按一定比例混合,形成MIM料浆。
然后,通过注射机将MIM料浆注射到金属模具中进行成型。
成型后的零件经过脱模,形成近净成型的未烧结零件。
最后,通过烧结过程,将未烧结零件在惰性气氛下加热至金属粉末的熔点以上进行烧结,粘结剂将烧结后残留物挥发,金属粉末颗粒结合在一起,形成致密的金属零件。
MIM技术的优点主要表现在以下几个方面。
首先,MIM技术可以制造形状复杂、精度高的零件,相比传统的金属加工方法更加灵活。
其次,MIM技术能够生产大批量的零件,并且具有高度的一致性,适用于需求量大的产品制造。
此外,MIM技术还可以制造超细或微型零件,满足现代微电子、医疗器械等领域对高精度零件的需求。
尽管MIM技术在低成本、高效率和高精度等方面具有明显优势,但也存在一些挑战。
首先,MIM技术对原料的要求较高,金属粉末的粒度和形状对成型效果有较大影响。
其次,粘结剂的选择和控制也是一项关键任务。
此外,由于烧结过程中需要控制温度和气氛等因素,烧结工艺相对复杂。
因此,MIM技术的成功应用需要综合考虑材料、工艺和设备等多个因素。
总的来说,MIM技术是一种高度灵活、高效率、高精度的金属成型方法,已在汽车、航空航天、电子、医疗器械等领域得到广泛应用。
随着材料科学和制造技术的不断发展,MIM技术将进一步完善和推广,为各个行业提供更多高质量的金属零件。
MIM技术作为一种金属粉末成型技术,具有独特的优势和特点,逐渐成为制造业中不可忽视的一种先进工艺。
2024年金属粉末注射成型(MIM)市场前景分析

金属粉末注射成型(MIM)市场前景分析概述金属粉末注射成型(Metal Injection Molding,简称MIM)是一种通过将金属粉末与聚合物混合,并注射到模具中形成所需形状的金属件的制造工艺。
MIM技术结合了传统的塑料注射成型和金属粉末冶金加工的优势,可以用于生产复杂形状和高精度的金属零件。
本文将对金属粉末注射成型市场的前景进行分析。
市场规模随着制造业的迅猛发展和对高质量金属零件的需求增加,金属粉末注射成型市场正在快速扩大。
根据市场研究公司的数据,2019年全球金属粉末注射成型市场规模达到XX亿美元,预计到2026年将达到XX亿美元。
北美和欧洲是金属粉末注射成型市场的主要地区,但亚太地区的市场份额正在快速增长。
主要应用领域金属粉末注射成型技术在各个行业中得到广泛应用。
其中,汽车工业是金属粉末注射成型市场的主要驱动因素之一。
MIM技术可以用于生产汽车零部件,如发动机组件、传动系统零件和底盘部件等。
此外,电子行业也是金属粉末注射成型的重要市场,用于生产各种电子设备中的金属连接器、传感器和高精密零件。
医疗行业也是金属粉末注射成型的潜在市场,因为MIM零件可以用于生产人工关节、牙科设备和外科手术工具等。
优势和挑战金属粉末注射成型技术具有许多优势。
首先,MIM技术能够生产复杂形状和高精度的金属零件,与传统的加工方法相比具有成本优势。
其次,MIM技术可以在一次注射成型中完成多个零件的生产,提高了生产效率。
此外,金属粉末注射成型技术还可以实现材料的高度可控性,满足客户对材料性能的特殊要求。
然而,金属粉末注射成型技术还面临一些挑战。
首先,MIM设备和模具的投资成本相对较高,对小型企业来说可能是一个限制因素。
其次,金属粉末注射成型过程相对较复杂,需要专业的工艺控制和技术人员的支持。
最后,对于一些大型和厚壁零件的生产,金属粉末注射成型技术可能无法满足要求,需要采用其他加工方法。
发展趋势金属粉末注射成型市场在未来几年有望继续保持较快的增长势头。
金属粉末注射成型
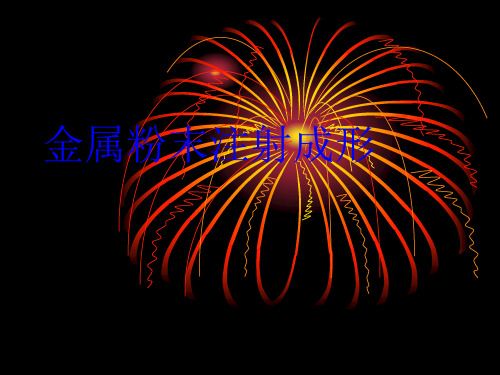
(4)注射速度及注射压力
注射压力大小与注射机种类、物料流动性、模具浇口尺寸、 产品厚度、模具温度及流程等因素有关。 一般注射压力略高于热塑性塑料的注射压力。 保压的作用:使制品冷却收缩时得以补料,尺寸准确,表 面光洁,有利于消除气泡。保压时间一般0.3~2分钟,特厚制 品可达5~10分钟。 注射速度与注射压力、温度、模口尺寸等因素有关。注射 速度慢不利于充模,生产效率低,注射速度过快易混入气泡。 需通过实际实验确定。
MIM和传统方法的比较: 压铸工艺用在铝和锌合金等熔点低、铸液流动性良好的材料。此工艺的产品因 材料的限制,其强度、耐磨性、耐蚀性均有限度。MIM工艺可以加工的原材料 则较多。注射成型工艺技术利用注射机注射成型产品毛坯,保证物料充分充满 模具型腔(金属液铸造充模较差),也就保证了零件高复杂结构的实现。 粉末锻造是一项重要的发展,已适用于连杆的量产制造。但是一般而言,锻造 过中热处理的成本和模具的寿命还是有问题,仍待进一步解决。 传统机械加工法,近年来靠自动化而提升了其加工能力,在效果和精度上 有极大的进步,但是基本的程序上仍脱不开逐步加工(车削、刨、铣、磨、钻孔、 抛光等)来完成零件形状的方式。机械加工方法的加工精度远优于其他加工方法, 但是因为材料的有效利用率低,且其形状的完成受限于设备与刀具,有些零件 无法用机械加工完成。相反,MIM可以有效利用材料,不受限制,对于小型、 高难度形状的精密零件的制造,MIM工艺比较机械加工而言,其成本较低且效 率高,具有很强的竞争力。 以往在传统加工技术中先作成个别元件再组合成组件的方式,在使用MIM 技术时可以考虑整合成完整的单一零件,大大减少步骤、简化加工程序。 MIM技术并非与传统加工方法竞争,而是弥补传统加工方法在技术上的不足 或无法制作的缺陷。MIM技术可以在传统加工方法制作的零件领域上发挥其特 长。MIM工艺在零部件制造方面所具有的技术优势可成型高度复杂的结构零件。
金属粉末的注射成型

具有极高的表面积和活性,能够提高 材料的力学性能和电磁性能,为金属 粉末注射成型的发展提供了新的方向 。
材料性能与成型工艺的关系
1 2 3
流动性
金属粉末的流动性直接影响注射成型的充模能力 和制件质量,流动性好的粉末有利于提高制件的 光洁度和尺寸精度。
压缩性
金属粉末的压缩性决定了其在模具内的填充密度 和制件的致密度,压缩性好的粉末能够提高制件 的机械性能。
医疗器械领域
制造个性化医疗器械和植入物,满足医疗行业对个性化、高性能 和高安全性的需求。
感谢您的观看
THANKS
注射成型操作
将混合料加热至流动状态,注入 模具中,在压力和温度的作用下, 混合料填充模具并硬化定型。
后处理
脱脂
烧结
通过加热或化学方法将粘结剂从金属粉末 中分解、去除,以获得纯净的金属制品。
将脱脂后的金属粉末制品在高温下进行烧 结,使金属粉末颗粒之间形成冶金结合, 提高制品的强度和性能。
热处理
表面处理
度和复杂度。
新型粘结剂的开发
02
研究新型粘结剂,以提高金属粉末的粘结效果,降低成型难度
和成本。
连续注射成型技术
03
开发连续注射成型技术,实现金属粉末的连续加工,提高生产
效率和降低能耗。
新材料的应用与开发
高性能金属粉末
研究开发高性能金属粉末,如钛合金、镍基高温 合金等,以满足高端制造业的需求。
复合材料的应用
详细描述
粉末流动性问题通常表现为注射压力不足、填充不均匀、成 型时间延长等。为了解决这一问题,可以采用改善粉末粒度 分布、降低粉末含水量和加入润滑剂等方法,以提高粉末的 流动性。
成型精度问题
金属粉末注射成型技术范文

金属粉末注射成型技术范文金属粉末注射成型技术,通常称为金属粉末注射成型(MIM),是一种集金属粉末冶金和塑料注射成型技术于一体的先进制造技术。
它采用了金属粉末与塑料模具注射成型的工艺,利用金属粉末经过混合、注射成型、脱模和烧结等步骤制造出金属部件。
MIM技术具有高精度、高复杂性、高效率和低成本等优势,被广泛应用在汽车、通信、医疗器械等领域。
MIM技术的原理主要包括金属粉末的混合、注射成型、脱模和烧结四个步骤。
首先,将金属粉末与塑料粉末按一定比例混合均匀,获得金属粉末与塑料的混合粉末。
然后,将混合粉末装入注射机中,通过高压注入塑料模具中。
在注射成型过程中,金属粉末与塑料粉末一起被热塑软化,并填充模具的空腔,形成所需的形状。
注射成型完成后,将模具放入烧结炉中,进行烧结处理。
在高温下,塑料燃烧殆尽,金属粉末颗粒开始发生烧结,并逐渐形成致密的金属部件。
MIM技术具有以下优势,使其成为制造领域的热门技术之一。
首先,MIM技术可以制造出具有高精度和高复杂性的零部件。
相较于传统的冲压和加工工艺,MIM技术可以实现更小尺寸、更精准形状和更复杂结构的部件制造。
其次,MIM技术可以提高生产效率和降低生产成本。
MIM技术可以实现大规模生产,每小时可注射成千上万个零件,大大提高了生产效率。
此外,MIM技术还可以节省材料和资源,减少废品率和二次加工,从而降低了生产成本。
第三,MIM技术可以制造出高性能的金属部件。
通过MIM技术制造的金属部件具有优异的物理和机械性能,如高强度、高硬度和耐磨性等。
因此,MIM技术广泛应用于汽车、通信、医疗器械等领域。
然而,MIM技术也存在着一些挑战和限制。
首先,MIM技术对原材料的要求较高。
金属粉末的粒径、流动性和化学性质等对最终产品的质量和性能有着重要影响。
因此,需要选择合适的金属粉末和混合工艺,以获得理想的成品。
其次,MIM技术的工艺复杂,需要控制好注射成型的温度、压力和时间等参数。
任何细微的变化都可能导致产品质量的下降或失败。
金属粉末注射成型
金属粉末注射成型金属粉末注射成型(Metal Powder Injection Molding,简称MIM)是一种高效、精确和经济的金属加工技术。
它结合了传统的塑料注射成型和金属粉末冶金工艺,可以生产出复杂形状的金属部件。
MIM技术在汽车、医疗、航空航天等行业中得到广泛应用,本文将介绍MIM的工艺原理、材料选择和应用领域。
MIM工艺原理可以分为四个步骤:混合、注射、脱模和烧结。
首先,将金属粉末与聚合物粉末、脱模剂等混合,并将其加热到高温使其熔化。
然后,将熔融的混合物喷射到模具中,形成所需的部件形状。
接下来,通过在高温和高压下使部件凝固,并将其从模具中取出。
最后,在高温下进行烧结,以消除聚合物,并在金属颗粒之间形成冶金结合。
在MIM中,材料选择是关键。
常用的金属材料包括不锈钢、工具钢、硬质合金、钻石等。
不锈钢具有良好的韧性和耐腐蚀性,常用于制造医疗器械、手表零件等高精度部件。
工具钢具有高强度和耐磨性,常用于制造汽车零部件、工具等。
硬质合金具有高硬度和耐磨性,常用于制造切削工具、注射模具等。
钻石是一种具有超硬性和导热性的材料,常用于制造高性能刀具。
MIM技术具有许多优点。
首先,MIM可以生产出复杂形状的部件,减少了后续加工的需要。
其次,MIM可以实现批量生产,提高了生产效率。
再次,MIM可以生产出高密度的部件,具有良好的力学性能和表面质量。
此外,MIM工艺还可以减少材料的浪费,提高了资源利用率。
MIM技术在许多领域中得到了广泛的应用。
在汽车行业中,MIM可以制造各种复杂形状的汽车零部件,如发动机零件、制动系统零件等。
在医疗行业中,MIM可以制造高精度医疗器械,如人工关节、牙科器械等。
在航空航天行业中,MIM可以制造轻量化部件,提高了飞机的燃油效率。
此外,MIM还可以应用于电子、军工等领域。
总之,金属粉末注射成型是一种高效、精确和经济的金属加工技术。
通过在MIM中选择合适的材料和工艺参数,可以生产出各种复杂形状的金属部件,并在汽车、医疗、航空航天等行业中得到广泛应用。
金属粉末注射成型技术规程
金属粉末注射成型技术规程金属粉末注射成型技术(Metal Powder Injection Molding,简称MIM)是一种将金属粉末与高分子粘结剂混合后制成有形状的注射成型过程。
该技术广泛应用于制造各种金属部件,具有高效、精准、成本低等优点。
以下是MIM技术的规程。
一、设备1.注射机:选用适合MIM工艺要求的注射机,能够控制注射压力、速度和温度等参数。
2.模具:要求模具精度高,制造工艺精良,能够满足零件的形状和尺寸要求。
3.烧结炉:要能够稳定地控制烧结温度和时间,进行高温处理。
4.喷砂机:用于去除成型后零件表面的粘结剂。
5.超声波清洗机:用于清洗成型后的零件表面和内部。
二、工艺流程1.原料制备:根据零件的要求,配制金属粉末和高分子粘结剂的比例,并进行混合,使粉末均匀分布。
2.注射成型:将混合好的金属粉末和高分子粘结剂放入注射机中,按照零件的形状和尺寸要求进行注射成型,控制好注射温度、压力和速度等参数。
3.脱模:将成型后的零件从模具中取出,清除表面的粘结剂,确保零件表面干净。
4.烧结处理:将成型后的零件放入烧结炉中,控制好烧结温度和时间,进行高温处理。
5.机械加工、表面处理:将烧结后的零件进行机械加工和表面处理,使零件达到要求的尺寸和表面粗糙度要求。
6.检验、包装:对成品进行检验,合格后进行包装。
三、质量控制1.原料质量控制:保证金属粉末和高分子粘结剂的质量符合规定要求,严格管控原料供应商。
2.工艺参数控制:精细控制注射温度、压力和速度等参数,保证零件的成型质量。
3.产品检验:对成品进行尺寸、外观等方面的检验,并严格把关。
4.持续改进:根据生产实际情况,不断优化工艺流程,提高生产效率和产品质量。
四、安全生产1.操作人员应接受严格的培训和考核,熟练掌握操作技能和注意安全规定。
2.设备维护保养应按时按方法进行。
3.操作过程中,严格遵守操作规程和安全规定,确保人身和设备安全。
以上就是金属粉末注射成型技术规程,通过规范化的操作流程和严格的品质控制,可以达到生产出高品质、高精度的金属零件的目的。
金属粉末冶金注射成型技术
金属粉末冶金注射成型技术金属粉末冶金注射成型技术(Metal Powder Injection Molding,简称MIM)是近年来快速发展起来的一种先进的粉末冶金成形工艺。
它将金属粉末与有机蜡粉通过混合、热塑性制品注射成型、脱蜡、烧结等步骤制作成金属零件。
MIM技术具有成型精度高、加工复杂度高、生产效率高等优点,并且可以制造出形状复杂、尺寸精确的金属零部件,已经在汽车、电子、医疗器械等领域得到广泛应用。
金属粉末冶金注射成型技术的工艺流程主要包括:粉末配方、混合、成型、脱蜡、烧结和后处理。
首先,根据要生产的零件的要求选择合适的金属材料,对金属粉末进行配方,以获得所需的物理和化学性能。
然后,将金属粉末和有机蜡粉混合均匀,形成金属粉末和有机蜡的复合物料。
复合物料经过精密注射成型机注射到塑料型腔中,通过注射压力和模具温度的控制,使金属粉末和有机蜡混合物充分填充型腔,并形成零件的初始形状。
注射成型后,将模具中的零件放入脱蜡设备中进行脱蜡处理。
在脱蜡过程中,通过加热使有机蜡融化和蒸发,从而获得完全密实的金属粉末成型件。
然后,将脱蜡后的零件置入烧结炉中进行烧结处理。
在烧结过程中,通过控制炉内温度和气氛,使金属粉末颗粒相互结合,获得致密的金属零部件。
最后,对烧结后的零件进行后处理,如机械加工、热处理、表面处理等,以获得所需的工程性能和外观质量。
MIM技术的优势主要体现在以下几个方面:首先,MIM技术可以制造出形状复杂、尺寸精确的金属零部件,可以实现传统加工方法难以实现的形状和结构。
其次,MIM技术具有高度的自动化程度,生产效率高,能够大规模、高效率地生产金属零件。
再次,MIM的制造工艺具有较好的重复性和稳定性,能够确保产品的质量和性能的稳定性。
此外,MIM还可以利用强化纤维等增强材料提高零件的力学性能。
当前,MIM技术已经应用于广泛的领域。
在汽车行业,MIM技术可以用于制造汽车的发动机支架、齿轮、离合器等零部件;在电子行业,MIM技术可以用于制造手机、电视等电子产品的外壳、连接器等零部件;在医疗器械领域,MIM技术可以制造手术钳、植入物等高精度、高性能的医疗器械部件。
金属粉末注射成型工艺及研究进展
金属粉末注射成型工艺及研究进展金属粉末注射成型(Metal Powder Injection Molding)是一种将金属粉末与有机增塑剂混合,并经过成型、脱脂与烧结等工艺步骤得到高密度的金属制品的先进制造技术。
自20世纪60年代开始发展以来,金属粉末注射成型技术在汽车、航空航天、医疗器械等领域得到了广泛应用。
本文将着重介绍金属粉末注射成型工艺的基本原理和研究进展。
一、基本原理金属粉末注射成型工艺主要包括以下几个步骤:原料制备、混合、注射成型、脱脂与烧结。
1. 原料制备在金属粉末注射成型过程中,合适的原料对成品制品的性能和质量起着决定性的作用。
通常,金属粉末的粒径要细小,分布要均匀,并具备良好的流动性。
为了提高金属粉末的流动性,往往需要通过表面处理、添加润滑剂等方法进行改性。
2. 混合在混合过程中,金属粉末与有机增塑剂按一定比例进行混合,并通过机械作用使其均匀分散。
混合的目的是为了使金属粉末与增塑剂形成均匀的糊状混合物,便于后续注射成型工艺的进行。
3. 注射成型注射成型是金属粉末注射成型工艺的核心步骤。
通过将混合物注射进注射机的模具腔中,并在一定的压力和温度下进行填充与压实,使其形成所需形状的绿体。
注射成型的优势在于可以制造出复杂且精密的金属件,且生产效率较高。
4. 脱脂与烧结脱脂与烧结是为了最终获得高密度的金属制品。
脱脂过程中,通过热处理将有机增塑剂从绿体中除去,获得无机绿体。
而烧结过程则是将无机绿体在高温下进行热处理,使金属粉末颗粒相互结合,形成致密的金属零件。
二、研究进展金属粉末注射成型技术在近年来获得了许多关注,在工艺、材料以及设备等方面取得了一系列的研究进展。
1. 工艺优化为了提高金属粉末注射成型工艺的效率和品质,研究者们进行了大量的工艺优化研究。
例如,通过调整注射成型参数、优化模具结构以及改变绿体预烧工艺等,可以有效改善成品的性能和质量。
2. 材料开发金属粉末注射成型所使用的金属粉末涉及多种材料,如不锈钢、钴基合金、铁基合金等。
- 1、下载文档前请自行甄别文档内容的完整性,平台不提供额外的编辑、内容补充、找答案等附加服务。
- 2、"仅部分预览"的文档,不可在线预览部分如存在完整性等问题,可反馈申请退款(可完整预览的文档不适用该条件!)。
- 3、如文档侵犯您的权益,请联系客服反馈,我们会尽快为您处理(人工客服工作时间:9:00-18:30)。
编订:__________________
单位:__________________
时间:__________________
金属粉末注射成型技术
Deploy The Objectives, Requirements And Methods To Make The Personnel In The Organization Operate According To The Established Standards And Reach The Expected Level.
Word格式 / 完整 / 可编辑
文件编号:KG-AO-3132-56 金属粉末注射成型技术
使用备注:本文档可用在日常工作场景,通过对目的、要求、方式、方法、进度等进行具体、周密的部署,从而使得组织内人员按照既定标准、规范的要求进行操作,使日常工作或活动达到预期的水平。
下载后就可自由编辑。
金属粉末注射成型技术(Metal Powder Injection Molding,简称MIM)是将现代塑料喷射成形技术引入粉末冶金领域而形成的一门新型粉末冶金近净形成形技术。
其基本工艺过程是:首先将固体粉末与有机粘结剂均匀混练,经制粒后在加热塑化状态下(~150℃)用喷射成形机注入模腔内固化成形,然后用化学或热分解的方法将成形坯中的粘结剂脱除,最后经烧结致密化得到最终产品。
与传统工艺相比,具有精度高、组织均匀、性能优异,生产成本低等特点,其产品广泛应用于电子信息工程、生物医疗器械、办公设备、汽车、机械、五金、体育器械、钟表业、兵器及航空航天等工业领域。
因此,国际上普遍认为该技术的发展将会导致零部件成形与加工技术的一场革命,被誉为“当今最热门的零部件成形技术”和“21
世纪的成形技术”。
美国加州Parmatech公司于1973年发明,八十年代初欧洲许多国家以及日本也都投入极大精力开始研究该技术,并得到迅速推广。
特别是八十年代中期,这项技术实现产业化以来更获得突飞猛进的发展,每年都以惊人的速度递增。
到目前为止,美国、西欧、日本等十多个国家和地区有一百多家公司从事该工艺技术的产品开发、研制与销售工作。
日本在竞争上十分积极,并且表现突出,许多大型株式会社均参与MIM 工业的推广,这些公司包括有太平洋金属、三菱制钢、川崎制铁、神户制钢、住友矿山、精工--爱普生、大同特殊钢等。
目前日本有四十多家专业从事MIM产业的公司,其MIM工业产品的销售总值早已超过欧洲并直追美国。
到目前为止,全球已有百余家公司从事该项技术的产品开发、研制与销售工作,MIM技术也因此成为新型制造业中最为活跃的前沿技术领域,被世界冶金行业的开拓性技术,代表着粉末冶金技术发展的主方向MIM技术。
金属粉末喷射成型技术是集塑料成型工艺学、高分子化学、粉末冶金工艺学和金属材料学等多学科透与交叉的产物,利用模具可喷射成型坯件并通过烧结快速制造高密度、高精度、三维复杂形状的结构零件,能够快速准确地将设计思想物化为具有一定结构、功能特性的制品,并可直接批量生产出零件,是制造技术行业一次新的变革。
该工艺技术不仅具有常规粉末冶金工艺工序少、无切削或少切削、经济效益高等优点,而且克服了传统粉末冶金工艺制品、材质不均匀、机械性能低、不易成型薄壁、复杂结构的缺点,特别适合于大批量生产小型、复杂以及具有特殊要求的金属零件。
工艺流程粘结剂→混炼→喷射成形→脱脂→烧结→后处理
粉末金属粉末
MIM工艺所用金属粉末颗粒尺寸一般在0.5~20μm;从理论上讲,颗粒越细,比表面积也越大,易于成型和烧结。
而传统的粉末冶金工艺则采用大于40μm 的较粗的粉末。
有机胶粘剂作用是粘接金属粉末颗粒,
使混合料在喷射机料筒中加热具有流变性和润滑性,也就是说带动粉末流动的载体。
因此,粘接剂的选择是整个粉末的载体。
因此,粘拉选择是整个粉末喷射成型的关键。
对有机粘接剂要求:
1.用量少,用较少的粘接剂能使混合料产生较好的流变性;
2.不反应,在去除粘接剂的过程中与金属粉末不起任何化学反应;
3.易去除,在制品内不残留碳。
混料把金属粉末与有机粘接剂均匀掺混在一起,使各种原料成为喷射成型用混合料。
混合料的均匀程度直接影响其流动性,因而影响喷射成型工艺参数,以至最终材料的密度及其它性能。
喷射成形本步工艺过程与塑料喷射成型工艺过程在原理上是一致的,其设备条件也基本相同。
在喷射成型过程中,混合料在喷射机料筒内被加热成具有流变性的塑性物料,并在适当的喷射压力下注入模具中,成型出毛坯。
喷射成型的毛坯的微观上应均匀一致,从而使制品在烧结过程中均匀收缩。
萃取成
型毛坯在烧结前必须去除毛坯内所含有的有机粘接剂,该过程称为萃取。
萃取工艺必须保证粘接剂从毛坯的不同部位沿着颗料之间的微小通道逐渐地排出,而不降低毛坯的强度。
粘结剂的排除速率一般遵循扩散方程。
烧结烧结能使多孔的脱脂毛坯收缩至密化成为具有一定组织和性能的制品。
尽管制品的性能与烧结前的许多工艺因素有关,但在许多情况下,烧结工艺对最终制品的金相组织和性能有着很大、甚至决定性的影响。
后处理对于尺寸要求较为精密的零件,需要进行必要的后处理。
这工序与常规金属制品的热处理工序相同。
MIM工艺的特点MIM工艺与其它加工工艺的对比
MIM使用的原料粉末粒径在2-15μm,而传统粉末冶金的原粉粉末粒径大多在50-100μm。
MIM工艺的成品密度高,原因是使用微细粉末。
MIM工艺具有传统粉末冶金工艺的优点,而形状上自由度高是传统粉末冶金所不能达到的。
传统粉末冶金限于模具的强度和填充密度,形状大多为二维圆柱型.传统的精密铸造脱
燥工艺为一种制作复杂形状产品极有效的技术,近年使用陶心辅助可以完成狭缝、深孔穴的成品,但是碍于陶心的强度,以及铸液的流动性的限制,该工艺仍有某些技术上的困难。
一般而言,此工艺制造大、中型零件较为合适,小型而复杂形状的零件则以MIM工艺较为合适。
比较项目制造工艺MIM工艺传统粉末冶金工艺粉末粒径(μm)2-1550-100相对密度(%)95-9880-85产品重量(g)小于或等于400克10-数百产品形状三维复杂形状二维简单形状机械性能优劣MIM制程和传统粉末冶金法的比较压铸工艺用在铝和锌合金等熔点低、铸液流动性良好的材料。
此工艺的产品因材料的限制,其强度、耐磨性、耐蚀性均有限度。
MIM工艺可以加工的原材料较多。
精密铸造工艺,虽然在近年来其产品的精度和复杂度均提高,但仍比不上脱蜡工艺和MIM工艺,粉末锻造是一项重要的发展,已适用于连杆的量产制造。
但是一般而言,锻造的工程中热处理的成本和模具的寿命还是有问题,仍待进一步解决.传统机械加工法、
近来靠自动化而提升其加工能力,在效果和精度上有极大的进步,但是基本的程序上仍脱不开逐步加工(车削、刨、铣、磨、钻孔、抛光等)来完成零件形状的方式。
机械加工方法的加工精度远优于其他加工方法,但是因为材料的有效利用率低,且其形状的完成受限于设备与刀具、有些零件无法用机械加工完成。
相反,MIM可以有效利用材料,不受限制,对于小型、高难度形状的精密零件的制造,MIM工艺比较机械加工而言,其成本较低且效率高,具有很强的竞争力.MIM技术并非与传统加工方法竞争,而是弥补传统加工方法在技术上的不足或无法制作的缺陷。
MIM技术可以在传统加工方法制作的零件领域上发挥其特长。
MIM工艺在零部件制造方面所具有的技术优势可成型高度复杂结构的结构零件
喷射成型工艺技术利用喷射机喷射成型产品毛坯,保证物料充分充满模具型腔,也就保证了零件高复杂结构的实现。
以往在传统加工技术中先作成个别元件再组合成组件的方式,在使用MIM技术时可以考虑整。