粉末冶金注射成形技术简介
粉末注塑和粉末冶金工艺介绍
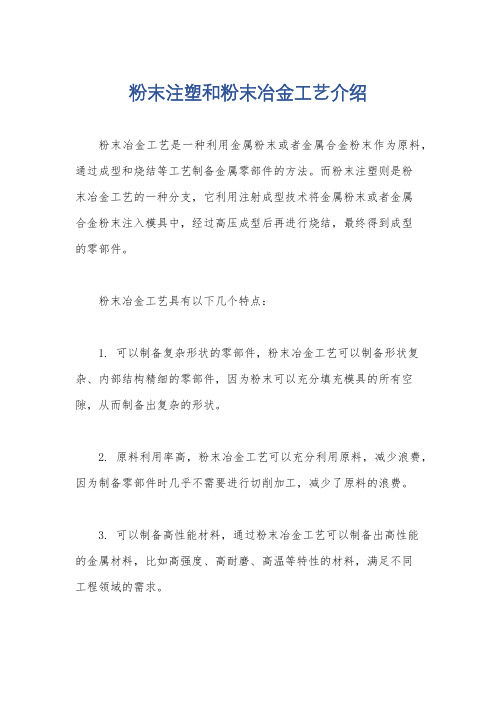
粉末注塑和粉末冶金工艺介绍
粉末冶金工艺是一种利用金属粉末或者金属合金粉末作为原料,通过成型和烧结等工艺制备金属零部件的方法。
而粉末注塑则是粉
末冶金工艺的一种分支,它利用注射成型技术将金属粉末或者金属
合金粉末注入模具中,经过高压成型后再进行烧结,最终得到成型
的零部件。
粉末冶金工艺具有以下几个特点:
1. 可以制备复杂形状的零部件,粉末冶金工艺可以制备形状复杂、内部结构精细的零部件,因为粉末可以充分填充模具的所有空隙,从而制备出复杂的形状。
2. 原料利用率高,粉末冶金工艺可以充分利用原料,减少浪费,因为制备零部件时几乎不需要进行切削加工,减少了原料的浪费。
3. 可以制备高性能材料,通过粉末冶金工艺可以制备出高性能
的金属材料,比如高强度、高耐磨、高温等特性的材料,满足不同
工程领域的需求。
粉末注塑作为粉末冶金工艺的一种应用,具有以下特点:
1. 成本低,相比传统的金属加工工艺,粉末注塑可以减少原材
料浪费和加工成本,从而降低零部件的制造成本。
2. 生产效率高,粉末注塑可以批量生产零部件,提高生产效率,适用于大规模生产。
3. 可以制备复杂形状的零部件,粉末注塑技术可以制备出复杂
形状的零部件,满足不同工程领域对零部件形状的需求。
总的来说,粉末冶金工艺和粉末注塑技术在制备金属零部件方
面具有独特的优势,可以满足不同领域对于零部件性能和形状的需求,有着广泛的应用前景。
金属粉末注射成型技术

技术应用领域
1.计算机及其辅助设施:如打印机零件、磁芯、撞针轴销、驱动零件; 2.工具:如钻头、刀头、喷嘴、枪钻、螺旋铣刀、冲头、套筒、扳手、电工工具,手工具等; 3.家用器具:如表壳、表链、电动牙刷、剪刀、风扇、高尔夫球头、珠宝链环、圆珠笔卡箍、刃具刀头等零 部件; 4.医疗机械用零件:如牙矫形架、剪刀、镊子; 5.军用零件:导弹尾翼、枪支零件、弹头、药型罩、引信用零件; 6.电器用零件:电子封装,微型马达、电子零件、传感器件; 7.机械用零件:如松棉机、纺织机、卷边机、办公机械等; 8.汽车船舶用零件:如离合器内环、拔叉套、分配器套、汽门导管、同步毂、安全气囊件等。
技术简介
其基本工艺过程是:首先将固体粉末与有机粘结剂均匀混练,经制粒后在加热塑化状态下(~150℃)用注射 成形机注入模腔内固化成形,然后用化学或热分解的方法将成形坯中的粘结剂脱除,最后经烧结致密化得到最终 产品。与传统工艺相比,具有精度高、组织均匀、性能优异,生产成本低等特点,其产品广泛应用于电子信息工 程、生物医疗器械、办公设备、汽车、机械、五金、体育器械、钟表业、兵器及航空航天等工业领域。因此,国 际上普遍认为该技术的发展将会导致零部件成形与加工技术的一场革命,被誉为“当今最热门的零部件成形技术” 和“21世纪的成形技术”。
金属粉末注射成型技术
将现代塑料注射成型技术引入粉末冶金领域而形成的新 型粉末冶金近净形成型技术
01 技术简介
目录
02 历史与现状
03 术应用领域
06 未来发展方向
金属粉末注射成型技术(Metal Powder Injection Molding Technology,简称MIM)是将现代塑料注射成型 技术引入粉末冶金领域而形成的一门新型粉末冶金近净形成型技术。
金属粉末的注射成型

具有极高的表面积和活性,能够提高 材料的力学性能和电磁性能,为金属 粉末注射成型的发展提供了新的方向 。
材料性能与成型工艺的关系
1 2 3
流动性
金属粉末的流动性直接影响注射成型的充模能力 和制件质量,流动性好的粉末有利于提高制件的 光洁度和尺寸精度。
压缩性
金属粉末的压缩性决定了其在模具内的填充密度 和制件的致密度,压缩性好的粉末能够提高制件 的机械性能。
医疗器械领域
制造个性化医疗器械和植入物,满足医疗行业对个性化、高性能 和高安全性的需求。
感谢您的观看
THANKS
注射成型操作
将混合料加热至流动状态,注入 模具中,在压力和温度的作用下, 混合料填充模具并硬化定型。
后处理
脱脂
烧结
通过加热或化学方法将粘结剂从金属粉末 中分解、去除,以获得纯净的金属制品。
将脱脂后的金属粉末制品在高温下进行烧 结,使金属粉末颗粒之间形成冶金结合, 提高制品的强度和性能。
热处理
表面处理
度和复杂度。
新型粘结剂的开发
02
研究新型粘结剂,以提高金属粉末的粘结效果,降低成型难度
和成本。
连续注射成型技术
03
开发连续注射成型技术,实现金属粉末的连续加工,提高生产
效率和降低能耗。
新材料的应用与开发
高性能金属粉末
研究开发高性能金属粉末,如钛合金、镍基高温 合金等,以满足高端制造业的需求。
复合材料的应用
详细描述
粉末流动性问题通常表现为注射压力不足、填充不均匀、成 型时间延长等。为了解决这一问题,可以采用改善粉末粒度 分布、降低粉末含水量和加入润滑剂等方法,以提高粉末的 流动性。
成型精度问题
粉末注射成形
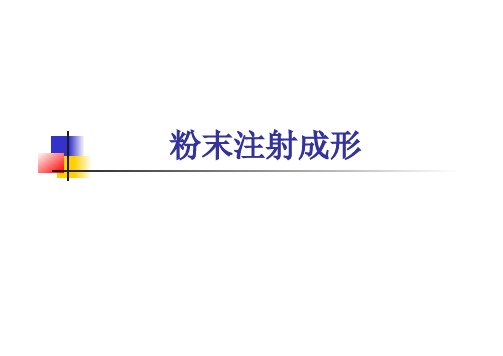
法国Impac技术公司
2001年获得国际粉末冶金大会设计大奖产品
Fe-7%Ni合金Carrier for Rifle(步枪支座)
Fe-7%Ni合金枪机保险栓
美国Parmatech公司
粉末注射成形枪扳机
粉末注射成形枪管套
国际上普遍认为: 该技术的发展将会导 致零部件成形与加工 技术的一场革命,被 誉为“当今最热门的零 部件成形技术”。
美国将该技术列为 对经济繁荣和国家持久 安全起至关重要作用的 “国家关键技术”。
表1 P I M 和精密铸造成形能力的比较
粉末注射成形与传统成形技术的比较
PIM技术的局限
加入大量高分子聚合物作粘结剂为粉末提供流 动性,以保证实现成形复杂形状的零件。粘结 剂的脱除却是一个需要严格控制的长时间过程, 增加了产品的成本。
粉末注射成形
定义:将金属粉末和成形剂制成具有流动 性的膏状物,注入成形机后加温加压的成 形技术。
粉末注射成形(Powder Injection Molding, PIM)是传统粉末冶金技术的基础上,创造 性地结合了塑料工业的注射成形技术而发 展起来的一门新兴的近净成形工艺,
现代塑料注射成形技术 +
金属材料
陶瓷材料
(5)生产成本低 主要表现在: 可以减少甚至消除机加工; 材料利用率高; 生产线建设规模灵活、投资少; 生产线高度自动化。
粉末注射成形技术的特点
近净形、零 部件一体化
高性能
粉末注射成形技术
传统技术,5件组合
应用广泛
高效率 低成本
PIM技术:1件
Today’s Hottest Components Forming Technology
金属粉末注射成型技术(MIM)工艺原理介绍
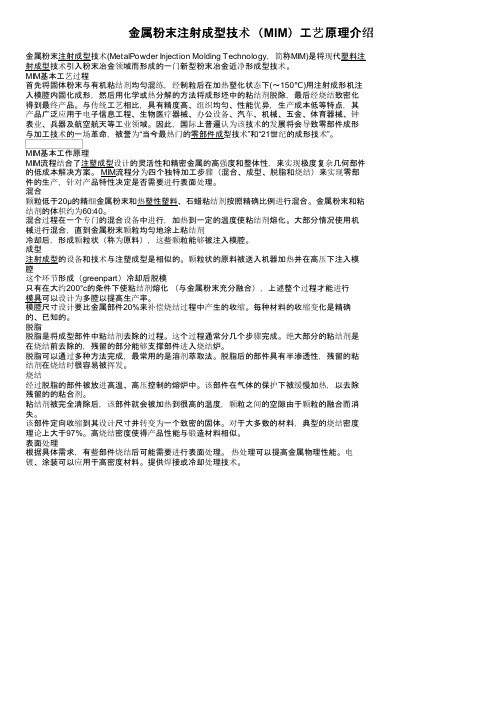
金属粉末注射成型技术(MIM)工艺原理介绍金属粉末注射成型技术(MetalPowder Injection Molding Technology,简称MIM)是将现代塑料注射成型技术引入粉末冶金领域而形成的一门新型粉末冶金近净形成型技术。
MIM基本工艺过程首先将固体粉末与有机粘结剂均匀混练,经制粒后在加热塑化状态下(~150℃)用注射成形机注入模腔内固化成形,然后用化学或热分解的方法将成形坯中的粘结剂脱除,最后经烧结致密化得到最终产品。
与传统工艺相比,具有精度高、组织均匀、性能优异,生产成本低等特点,其产品广泛应用于电子信息工程、生物医疗器械、办公设备、汽车、机械、五金、体育器械、钟表业、兵器及航空航天等工业领域。
因此,国际上普遍认为该技术的发展将会导致零部件成形与加工技术的一场革命,被誉为“当今最热门的零部件成型技术”和“21世纪的成形技术”。
MIM基本工作原理MIM流程结合了注塑成型设计的灵活性和精密金属的高强度和整体性,来实现极度复杂几何部件的低成本解决方案。
MIM流程分为四个独特加工步骤(混合、成型、脱脂和烧结)来实现零部件的生产,针对产品特性决定是否需要进行表面处理。
混合颗粒低于20µ的精细金属粉末和热塑性塑料、石蜡粘结剂按照精确比例进行混合。
金属粉末和粘结剂的体积约为60:40。
混合过程在一个专门的混合设备中进行,加热到一定的温度使粘结剂熔化。
大部分情况使用机械进行混合,直到金属粉末颗粒均匀地涂上粘结剂冷却后,形成颗粒状(称为原料),这些颗粒能够被注入模腔。
成型注射成型的设备和技术与注塑成型是相似的。
颗粒状的原料被送入机器加热并在高压下注入模腔这个环节形成(greenpart)冷却后脱模只有在大约200°c的条件下使粘结剂熔化(与金属粉末充分融合),上述整个过程才能进行模具可以设计为多腔以提高生产率。
模腔尺寸设计要比金属部件20%来补偿烧结过程中产生的收缩。
每种材料的收缩变化是精确的、已知的。
MIM金属粉末注射成形
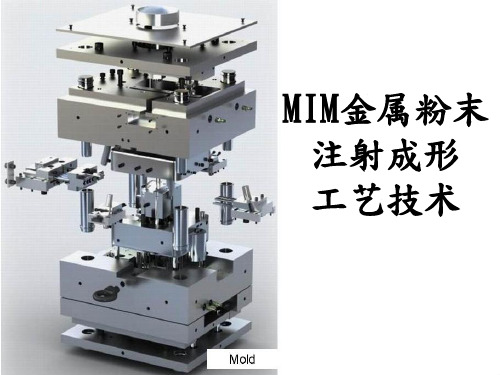
(2)MIM能最大限度制得接近最终形状的零件,尺寸精度较高。
(3)即使是固相烧结,MIM制品的相对密度可达95%以上,其性能可与锻造材料相媲美。特别是动力学性能优良。
流动的载体。因此,粘接剂的选择是整个粉末注射成型的关键。对有机粘接剂要求:①用量少,即用较少的粘接剂 能使混合料产生较好的流变性;②不反应,在去除粘接剂的过程中与金属粉末不起任何化学反应;③易去除,在制 品内不残留碳。
2.2.3 混炼与制粒 混炼时把金属粉末与有机粘接剂均匀掺混在一起,将其流变性调整到适于注射成型状态的作用,混合料的均匀
程度直接影响其流动性,因而影响注射成型工艺参数乃至最终材料的密度及其它性能,注射成型过程中产生的下角 料、废品都可重新破碎、制粒,回收再用。
2.3.4 注射成型
本步工艺过程与塑料注射成型工艺过程在原理上是一致的,其设备条件也基本相同。在注射成型过程中,混合 料在注射机料筒内被加热成具有流变性的塑性物料,并在适当的注射压力下注入模具中,成型出毛坯。注射成型的 毛坯的密度在微观上应均匀一致,从而使制品在烧结过程中均匀收缩。控制注射温度、模具温度、注射压力、保压 时间等成型参数对获得稳定的生坯重量至关重要。要防止注射料中各组分的分离和偏析,否则将导致尺寸失控和畸 变而报废。
3.1.2 MIM与精密铸造的比较
在金属成型工艺中,压铸和精密铸造是可以成型三维复杂形状的零件,但压铸仅限于低熔点金属,而精密铸造 (IC)限于合金钢、不锈钢、高温合金等高熔点金属及有色金属,对于难熔合金如硬质合金、高密度合金、金属陶 瓷等却无能为力,这是IC的本质局限性,而且IC对于很小、很薄、大批量的零件生产是十分困难或不可行的。IC产 业化已成熟,发展的潜力有限。MIM是新兴的工艺,将挤入IC大批量小零件的市场。
金属粉末冶金注射成型技术
金属粉末冶金注射成型技术金属粉末冶金注射成型技术(Metal Powder Injection Molding,简称MIM)是近年来快速发展起来的一种先进的粉末冶金成形工艺。
它将金属粉末与有机蜡粉通过混合、热塑性制品注射成型、脱蜡、烧结等步骤制作成金属零件。
MIM技术具有成型精度高、加工复杂度高、生产效率高等优点,并且可以制造出形状复杂、尺寸精确的金属零部件,已经在汽车、电子、医疗器械等领域得到广泛应用。
金属粉末冶金注射成型技术的工艺流程主要包括:粉末配方、混合、成型、脱蜡、烧结和后处理。
首先,根据要生产的零件的要求选择合适的金属材料,对金属粉末进行配方,以获得所需的物理和化学性能。
然后,将金属粉末和有机蜡粉混合均匀,形成金属粉末和有机蜡的复合物料。
复合物料经过精密注射成型机注射到塑料型腔中,通过注射压力和模具温度的控制,使金属粉末和有机蜡混合物充分填充型腔,并形成零件的初始形状。
注射成型后,将模具中的零件放入脱蜡设备中进行脱蜡处理。
在脱蜡过程中,通过加热使有机蜡融化和蒸发,从而获得完全密实的金属粉末成型件。
然后,将脱蜡后的零件置入烧结炉中进行烧结处理。
在烧结过程中,通过控制炉内温度和气氛,使金属粉末颗粒相互结合,获得致密的金属零部件。
最后,对烧结后的零件进行后处理,如机械加工、热处理、表面处理等,以获得所需的工程性能和外观质量。
MIM技术的优势主要体现在以下几个方面:首先,MIM技术可以制造出形状复杂、尺寸精确的金属零部件,可以实现传统加工方法难以实现的形状和结构。
其次,MIM技术具有高度的自动化程度,生产效率高,能够大规模、高效率地生产金属零件。
再次,MIM的制造工艺具有较好的重复性和稳定性,能够确保产品的质量和性能的稳定性。
此外,MIM还可以利用强化纤维等增强材料提高零件的力学性能。
当前,MIM技术已经应用于广泛的领域。
在汽车行业,MIM技术可以用于制造汽车的发动机支架、齿轮、离合器等零部件;在电子行业,MIM技术可以用于制造手机、电视等电子产品的外壳、连接器等零部件;在医疗器械领域,MIM技术可以制造手术钳、植入物等高精度、高性能的医疗器械部件。
MIN金属粉末成型介绍
金属粉末注射成形MIM制品
பைடு நூலகம்
笔记本电脑铰链转角
MIM工艺手机类产品
锁配件(锁头.锁舌.按键.复杂异形部件
MIM金属注射成型产品
工艺特点
金属粉末注射成型技术是集塑料成型工艺学、高分子化学、粉末 冶金工艺学和金属材料学等多学科透与交叉的产物,利用模具可 注射成型坯件并通过烧结快速制造高密度、高精度、三维复杂形 状的结构零件,能够快速准确地将设计思想物化为具有一定结构、 功能特性的制品,并可直接批量生产出零件,是制造技术行业一 次新的变革。该工艺技术不仅具有常规粉末冶金工艺工序少、无 切削或少切削、经济效益高等优点,而且克服了传统粉末冶金工 艺制品、材质不均匀、机械性能低、不易成型薄壁、复杂结构件 的缺点,特别适合于大批量生产小型、复杂以及具有特殊要求的 金属零件。工艺流程金属粉末+粘结剂→混炼→注射成形→脱脂 →烧结→后处理 MIM工艺所用金属粉末颗粒尺寸一般在0.5~20μm;从理论 上讲,颗粒越细,比表面积也越大,易于成型和烧结。而传统的 粉末冶金工艺则采用大于40μm的较粗的粉末。 有机胶粘剂作用是粘接金属粉末颗粒,使混合料在注射机料 筒中加热具有流变性和润滑性,也就是说带动粉末流动的载体。 因此,粘接剂的选择是整个粉末注射成型的关键。对有机粘接剂 要求: 1.用量少,用较少的粘接剂能使混合料产生较好的流变性; 2.不反应,在去除粘结剂的过程中与金属粉末不起任何化学 反应; 3.易去除,在制品内不残留。
分类
热处理 调湿处理
(1)热处理
热处理的实质:迫使冻结的分子链松弛,凝固的大 分子链段转向无规位置,消除部分内应力,提高结晶度, 稳定结晶结构,提高弹性模量,降低断裂延伸率。
(2)调湿处理
将刚脱模的制品放入水中,与空气隔绝、防止氧化。 调湿条件:90~110℃ 4h
粉末注射成型技术介绍
粉末注射成型技术介绍粉末注射成形概述:粉末注射成形(Powder Injection Molding,PIM)由金属粉末注射成形(Metal Injection Molding,MIM)与陶瓷粉末注射成形(Ceramics Injection Molding,CIM)两部分组成,它是一种新的金属、陶瓷零部件制备技术,它是将塑料注射成形技术引入到粉末冶金领域而形成的一种全新的零部件加工技术。
MIM的基本工艺步骤是:首先选取符合MIM要求的金属粉末和黏结剂,然后在一定温度下采用适当的方法将粉末和黏结剂混合成均匀的喂料,经制粒后再注射成形,获得成形坯(Green Part),再经过脱脂处理后烧结致密化成为最终成品(White Part)。
粉末注射成形技术的特点:粉末注射成形能像生产塑料制品一样,一次成形生产形状复杂的金属、陶瓷零部件。
该工艺技术利用注射方法,保证物料充满模具型腔,也就保证了零件高复杂结构的实现。
以往在传统加工技术中,对于复杂的零件,通常是先分别制作出单个零件,然后再组装;而在使用PIM技术时,可以考虑整合成完整的单一零件,这样大大减少了生产步骤,简化了加工程序。
1、与传统的机械加工、精密铸造相比,制品内部组织结构更均匀;与传统粉末冶金压制∕烧结相比,产品性能更优异,产品尺寸精度高,表面光洁度好,不必进行再加工或只需少量精加工。
金属注射成形工艺可直接成形薄壁结构件,制品形状已能接近或达到最终产品要求,零件尺寸公差一般保持在±0.10%~±0.30%水平,特别对于降低难以进行机械加工的硬质合金的加工成本、减少贵重金属的加工损失尤其具有重要意义。
2、零部件几何形状的自由度高,制件各部分密度均匀、尺寸精度高,适于制造几何形状复杂、精度密高及具有特殊要求的小型零件(0.2~200g)。
3、合金化灵活性好,对于过硬、过脆、难以切削的材料或原料铸造时有偏析或污染的零件,可降低制造成本。
金属粉末注射成型
案例四:电子产品制造
总结词
微型化、高精度、轻量化
详细描述
金属粉末注射成型在电子产品制造中发挥着重要作用,尤其 在微型化、高精度和轻量化方面具有显著优势。例如,用于 制造手机、平板电脑等消费电子产品的金属结构件和连接件 等。
05
结论
金属粉末注射成型的重要性和应用前景
金属粉末注射成型是一种重要的金属加 工技术,具有高精度、高效率、低成本 等优点,广泛应用于汽车、航空航天、
未来发展方向
新材料研究与应用
随着新材料技术的不断发展,未来将有更 多具有优异性能的金属粉末应用于金属粉
末注射成型工艺。Βιβλιοθήκη 环保与可持续发展随着环保意识的提高,未来金属粉末注射 成型将更加注重环保和可持续发展,减少
生产过程中的废弃物和能耗。
智能化与自动化
通过引入先进的传感器、控制系统和人工 智能技术,实现金属粉末注射成型的智能 化和自动化,提高生产效率和产品质量。
探索金属粉末注射成型与其他 先进制造技术的结合,实现优 势互补,提高整体制造水平。
ABCD
加强新材料的研发和应用, 以满足市场需求和推动产 业升级。
加强国际合作和技术交流,引 进先进技术和理念,推动金属 粉末注射成型技术的全球发展 。
THANK YOU
型产品。
1970年代
随着粘结剂喷射和脱脂技术的 发展,金属粉末注射成型技术
逐渐成熟。
1980年代至今
金属粉末注射成型技术不断发 展和完善,应用领域不断扩大
。
应用领域
电子通讯
如连接器、端子、 线圈架等;
医疗器械
如手术器械、牙科 器械等;
汽车零件
如发动机零件、变 速器零件、刹车系 统零件等;
- 1、下载文档前请自行甄别文档内容的完整性,平台不提供额外的编辑、内容补充、找答案等附加服务。
- 2、"仅部分预览"的文档,不可在线预览部分如存在完整性等问题,可反馈申请退款(可完整预览的文档不适用该条件!)。
- 3、如文档侵犯您的权益,请联系客服反馈,我们会尽快为您处理(人工客服工作时间:9:00-18:30)。
≈100% 粗晶,偏析
好 受限制
低 高劳动密集
PIM 技术并非与传统加工方法竞争,而是弥补传统加工方法在技术上的不足或某些零件无法制造的缺 陷。
现代 PIM 技术的研究始于 1973 年,Parmatech 公司在美国成立,专门从事 PIM 技术的研究和产品开 发工作,但当时该项技术还鲜为人知,直到 1979 年,该公司两件 PIM 产品在国际粉末冶金大会的产品设 计大赛中获奖后,才开始受到粉末冶金工业界的关注。到 1985 年,美国才向全世界公布这一技术,而在
先达科技
粉末冶金注射成形技术简介
我国实现粉末注射成形技术产业化,并保持一定竞争力的关键是要进一步提高产品尺寸精度和质量稳 定性,需解决以下关键问题:
因原材料特性变化、工艺参数的波动所带来的产品质量不稳定问题。 关键工艺设备国产化和配套问题。 研究粉末注射成形模具和产品的计算机辅助设计、集成制造、工艺过程在线控制技术,缩短模具
项目
PIM
最小孔径
0.4mm
2mm 盲孔最大深度
20mm
最大壁厚
10mm
最小壁厚
<1mm
锐边
可以
小尺寸内、外螺纹
可以
10mm
±0.05mm
50mm
±0.25mm
0.8~1.6μm
95%~98%
细晶,组织均匀
好
不收限制
高
低,科技含量高
精密铸造 2mm 2mm
数十毫米 2mm
受限制 困难 ±0.12mm ±0.5mm
PIM 的基本工艺步骤是:选取符合 PIM 工艺要求的金属或陶瓷粉末和粘结剂,然后在一定温度下将粉 末和粘结剂混合成均匀的喂料,经制粒后,在加热塑化状态下(~150°C)用注射成形机注入模具腔内成 形而获得成形坯(Green Part),再利用化学或热分解方法脱除成形坯内的粘结剂,最后烧结致密化成为最 终成品(White Part)。
极重要 高 均匀 大 较难 较难 容易 高
形状复杂 尺寸受限制
较低 受限制 范围广 较高 简单,费用低 一般 极低 不均匀 固相烧结时不大
好 容易 困难 较低 成本低 孔隙度较高
形状
尺寸精度 表面粗糙度 Ra 密度 显微组织 性能 零件数量 原料成本 劳动力成本
表 3 PIM 和精密铸造成形能力比较
到目前为止,美国、欧洲、日本等十多个国家和地区有一百多家公司从事该工艺技术的产品开发、研 制与销售工作。日本在竞争上十分积极,并且表现突出,许多大型株式会社均参与 PIM 工业的推广,这些 公司包括有太平洋金属、三菱制钢、川崎制铁、神户制钢、住友矿山、精工--爱普生、大同特殊钢等。目 前日本有 40 多家专业从事 PIM 产业的公司,其 PIM 工业产品的销售总值早已超过欧洲并直追美国。继日 本快速发展之后,中国台湾地区、韩国、新加坡、欧洲和南美的 PIM 产业也雨后春笋般发展起来。其中德 国的 BASF 公司 20 世纪 90 年代开发出来的 Metamold 一步脱脂法是 PIM 产业的一个重大突破,该脱脂方 法的一个重要特点是采用催化剂脱脂,脱脂时不出现液相,避免了 PIM 产品容易发生变形和尺寸精度控制 困难等弱点,大大缩短了脱脂时间,从而降低了成本,并且能生产尺寸较大的 PIM 零部件,是目前应用于 工业生产中最先进的 PIM 脱脂方法。据粉末冶金协会粗略统计和预测,全球 PIM 产品销售额达到 10 亿美 元,到 2010 年将达到 24 亿美元。
中国 PIM 技术的研究始于 20 世纪 80 年代末,先后有钢铁研究总院、北京科技大学、中南大学、北京 有色金属研究总院、北京粉末冶金研究所、广州有色金属研究院等开展了 PIM 技术的研究工作。九五期间, 在国家“863”计划、国家科技攻关计划、国家军工配套科研计划和国家自然科学基金等计划的资助下, 我国突破了 PIM 技术的一些难关,取得了一系列创新性成果,形成小批量的工业生产。近年来,国内 PIM 产业得到迅速发展,国内公司纷纷从国外引进先进的 PIM 设备来提升 PIM 的制造水平及能力,使得我国 的 PIM 技术上了一个新台阶。总体而言,我国 PIM 技术研究起步晚,产业化进程慢,产业规模小,随着 我国经济与社会的快速发展,将会得到充分发展和广泛应用。
表 1 PIM 和其它金属加工方法的比较
项目
加工方法
PIM
传统粉末冶金
精密铸造
机加工
锻造
冲压
零件密度
98%
86%
98%
100%
100%
100%
机械强度
高
低
高
高
高
高
尺寸精度
高
高
高
最高
高
高
表面光洁度
高
中
中
高
低
高
微小化能力
高
中
低
中
低
高
薄壁能力
高
中
中
低
低
高
形状
低
设计宽容度
高
中
中
中
低
低
批量生产能力
先达科技
粉末冶金注射成形技术简介
粉末注射成形能像生产塑料制品一样,一次成形生产形状复杂的金属、陶瓷零部件。 适用于制造几何形状复杂、精密度高及具有特殊要求的小零件(0.2~200g)。 可直接成形薄壁结构件,制品形状接近或达到最终产品要求,尺寸公差一般能保持在±0.10%~±
粉末冶金注射成形技术简介
粉末冶金注射成形技术简介
粉末注射成形(Powder Injection Molding,简写为 PIM)由金属粉末注射成形(Metal Injection Molding, 简写为 MIM)和陶瓷粉末注射成形(Ceramics Injection Molding,简写为 CIM)两部分组成,它是将塑料注 射成形技术引入到粉末冶金领域,利用模具型腔使金属、陶瓷粉末成形,经过去除粘结剂和烧结获得致密 化成品而形成的一种新型金属、陶瓷零部件制备加工技术。
与传统工艺相比,PIM 技术具有精度高、组织均匀、性能优异、生产成本低等特点,其产品广泛应用 于电子信息工程、生物医疗器械、办公设备、汽车、机械、五金、体育器械、钟表业、兵器及航空航天等 工业领域,是小型复杂零部件成形与加工技术的一场革命,被誉为“当今最热门的零部件成形技术”和“21 世纪的成形技术”。
高
高
中
中-高
高
高
材质适应性
高
高
中-高
高
中
中
供货能力
高
高
中
低
低
高
项目 粉末原料
混料 成形
表 2 PIM 和传统粉末冶金的工艺和性能比较
PIM
传统粉末冶金 P/M
粒度
<20μm
<150μm
工艺
探索改进合适工艺
成熟
数量
批量
大批量
成本
低
高
工序重要性
很重要
一般
混料设备
未定型
有,通用
混料时间
长,加热
短,室温
粘结剂数量
量多,组成复杂
量少,组成简单
设备投资
较低
高
模具
复杂,磨损小
简单,磨损
先达科技
粉末冶金注射成形技术简介
生产率
生坯形状
生坯重量
成本
工艺
脱脂
工序重要性
成本
收缩
收缩率
烧结
尺寸控制 碳含量控制
达到高密度
力学性能
最大优势
产品最大缺点
高 不受限制 小,受限制
低 复杂,费用高
制造和产品试制周期,提高生产工艺过程控制的可靠性。 通过引进、消化、吸收国外先进设备,为关键工艺设备的国产化提供设计和制造依据。 开发新的材料体系和新的气/固界面催化反应脱脂技术,扩大粉末注射成形技术的应用领域。
先达科技
先达科技
粉末冶金注射成形技术简介 这期间美国国内的 PIM 技术得以成熟并迅速发展形成产业化。该项技术向世界披露后得到世界各国政府、 学术界、企业界的广泛重视,并投入了大量的人力、物力和财力予以研究开发。美国政府先后拨款数百万 美元,在伦塞尔理工学院(Rensselaer Polytechnic Institute)开展 PIM 技术基础理论和应用基础的研究工作。 之后,又在宾州大学(Pennsylvania State University)建立了 PIM 专业实验基地,并成立了全美 PIM 协会, 每年定期举办专门的国际研讨会,以促进该项技术的发展。目前,该协会已吸收了许多国外单位和专家参 加,而发展成为一个国际性的学术组织。进入 20 世纪 90 年代,随着 PIM 工艺进一步改进,新材料、新工 艺不断涌现,PIM 技术产业化发展非常迅猛。日本 1991 年 PIM 产品销售额为 27 亿日元,1992 年猛增到 46 亿日元,2000 年达到了 130 亿日元。德国 1993 年 PIM 产品销售额比 1992 年增长了 5 倍。瑞士中高档 手表的表壳和表带 70%用 PIM 工艺制造。美国政府已将该项技术列为美国经济繁荣和国家持久安全起至关 重要作用的“国家关键技术”。为了保持美国在该项技术研究与开发方面的优势,1999 年 6 月美国国家自然 科学基金会和宾州政府联合支持在宾州大学建立了烧结材料工程研究中心,PIM 技术是该中心重点研究的 领域之一。
0.30%水平。 对于过硬、过脆、难以切削的材料,或原料铸造时有偏析或污染的零件,可降低制造成本。 与传统的机械加工、精密铸造相比,制品内部组织结构更均匀;与传统粉末冶金压制烧结相比,产品
性能更优异,尺寸精度高,表面光洁度好(表面粗糙度可达 Ra0.80~1.6μm),不必进行再加工或只 需少量精加工。 制品的相对密度可达 95%~98%,可进行渗碳、淬火、回火等热处理。 原材料利用率高,生产自动化程度高,工艺简单,可连续大批量规模化生产。生产过程无污染,为清 洁生产工艺。 制品微观组织均匀,产品密度、强度、硬度、韧性、塑性等力学性能高。