精确成型技术 第十讲 压力铸造
压力铸造特点
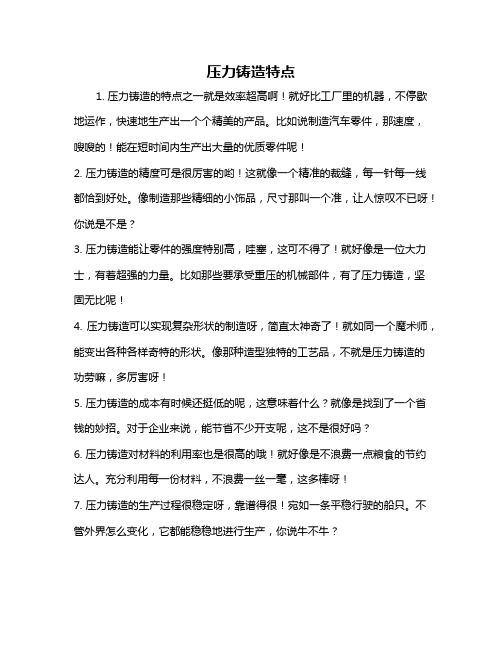
压力铸造特点
1. 压力铸造的特点之一就是效率超高啊!就好比工厂里的机器,不停歇地运作,快速地生产出一个个精美的产品。
比如说制造汽车零件,那速度,嗖嗖的!能在短时间内生产出大量的优质零件呢!
2. 压力铸造的精度可是很厉害的哟!这就像一个精准的裁缝,每一针每一线都恰到好处。
像制造那些精细的小饰品,尺寸那叫一个准,让人惊叹不已呀!你说是不是?
3. 压力铸造能让零件的强度特别高,哇塞,这可不得了!就好像是一位大力士,有着超强的力量。
比如那些要承受重压的机械部件,有了压力铸造,坚固无比呢!
4. 压力铸造可以实现复杂形状的制造呀,简直太神奇了!就如同一个魔术师,能变出各种各样奇特的形状。
像那种造型独特的工艺品,不就是压力铸造的功劳嘛,多厉害呀!
5. 压力铸造的成本有时候还挺低的呢,这意味着什么?就像是找到了一个省钱的妙招。
对于企业来说,能节省不少开支呢,这不是很好吗?
6. 压力铸造对材料的利用率也是很高的哦!就好像是不浪费一点粮食的节约达人。
充分利用每一份材料,不浪费一丝一毫,这多棒呀!
7. 压力铸造的生产过程很稳定呀,靠谱得很!宛如一条平稳行驶的船只。
不管外界怎么变化,它都能稳稳地进行生产,你说牛不牛?
8. 压力铸造确实有着好多独特又很棒的特点,它在制造业中可是有着重要的地位呢!能大大提高生产效率和产品质量,真的是不可或缺的呀!
我的观点结论:压力铸造凭借其诸多出色的特点,在各个领域都发挥着重要作用,给生产带来了极大的便利和进步。
压力铸造的基本概念和过程
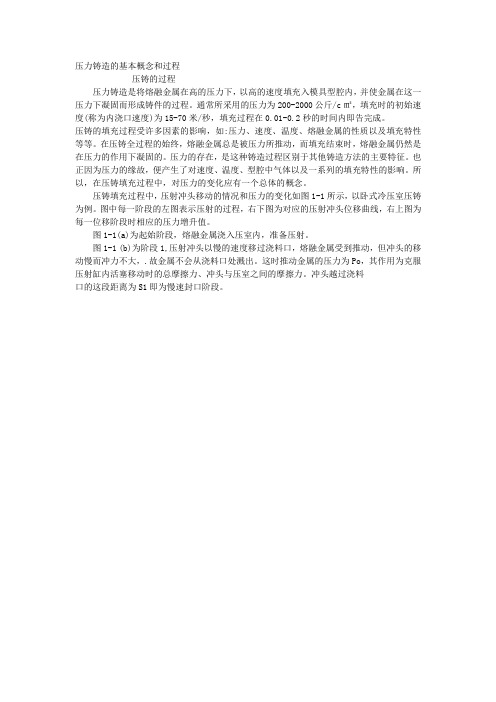
压力铸造的基本概念和过程压铸的过程压力铸造是将熔融金属在高的压力下,以高的速度填充入模具型腔内,并使金属在这一压力下凝固而形成铸件的过程。
通常所采用的压力为200-2000公斤/c㎡,填充时的初始速度(称为内浇口速度)为15-70米/秒,填充过程在0.01-0.2秒的时间内即告完成。
压铸的填充过程受许多因素的影响,如:压力、速度、温度、熔融金属的性质以及填充特性等等。
在压铸全过程的始终,熔融金属总是被压力所推动,而填充结束时,熔融金属仍然是在压力的作用下凝固的。
压力的存在,是这种铸造过程区别于其他铸造方法的主要特征。
也正因为压力的缘故,便产生了对速度、温度、型腔中气体以及一系列的填充特性的影响。
所以,在压铸填充过程中,对压力的变化应有一个总体的概念。
压铸填充过程中,压射冲头移动的情况和压力的变化如图1-1所示,以卧式冷压室压铸为例。
图中每一阶段的左图表示压射的过程,右下图为对应的压射冲头位移曲线,右上图为每一位移阶段时相应的压力增升值。
图1-1(a)为起始阶段,熔融金属浇入压室内,准备压射。
图1-1 (b)为阶段1,压射冲头以慢的速度移过浇料口,熔融金属受到推动,但冲头的移动慢而冲力不大,.故金属不会从浇料口处溅出。
这时推动金属的压力为Po,其作用为克服压射缸内活塞移动时的总摩擦力、冲头与压室之间的摩擦力。
冲头越过浇料口的这段距离为S1即为慢速封口阶段。
图1-1压铸填充过程各个阶段P-压射压力;S-压射冲头移动距离t-时间图1-1(C)为阶段2,压射冲头以一定的速度(比阶段1的速度度略快)移动,与这一速度相应的压力增升值达到Pl,熔融金属充满压室的前端和浇道并堆聚于内浇口前沿,但因速度不大,故金属在流动时,浇道中包卷气体只在一个较小的限度以内。
冲头在这一阶段所移动的距离为S2,是为金属堆聚阶段。
在这一阶段的最后瞬间,亦即金属到达内浇口时,由于内浇口的截面在浇口系统(包括压室)各部分的截面中总是最小的,故该处阻力最大,压射压力便因此而增升,其增升值即为达到足以突破内浇口处的阻力为止。
压力铸造

将熔融或半熔融的金属以高速压射入金属铸型内,并在 压力下结晶的铸造方法
01 ห้องสมุดไป่ตู้述
03 工艺流程
目录
02 特点 04 应用
压力铸造是指将熔融或半熔融的金属以高速压射入金属铸型内,并在压力下结晶的铸造方法,简称压铸。常 用压射压力为30~70MPa,充填速度约为0.5~50 m/s,充填时间为0.01~0.2 s。
近些年来,高科技已应用于压铸领域.如采用三级压射机构控制压力、压射速度和型内气体。发展特殊压铸 工艺(如真空压铸、定向引气压铸、充氧压铸等)和应用计算机控制技术,有效地清除气孔,提高铸件致密度,同 时研制新型模具材料和热处理新工艺来延长压型寿命,使黑色金属压铸有了一定进展。
谢谢观看
简述
压力铸造是一种将液态或半固态金属或合金,或含有增强物相的液态金属或合金,在高压下以较高的速度填 充入压铸型的型腔内,并使金属或合金在压力下凝固形成铸件的铸造方法。压铸时常用的压力为4~500MPa,金 属充填速度为0.5—120m/s。因此,高压、高速是压铸法与其他铸造方法的根本区别,也是重要特点。1838年美 国人首次用压力铸造法生产印报的铅字,次年出现压力铸造专利。19世纪60年代以后,压力铸造法得到很大的发 展,不仅能生产锡铅合金压铸件、锌合金压铸件,也能生产铝合金、铜合金和镁合金压铸件。20世纪30年代后又 进行了钢铁压力铸造法的试验。
压力铸造的原理主要是金属液的压射成形原理。通常设定铸造条件是通过压铸机上速度、压力,以及速度的 切换位置来调整的,其他的在压铸型行进行选择。
特点
1、压力铸造的优点 1)生产率高,易于实现机械化和自动化,可以生产形状复杂的薄壁铸件。压铸锌合金最小壁厚仅为0.3mm, 压铸铝合金最小壁厚约为0.5mm,最小铸出孔径为0.7mm。 2)铸件尺寸精度高,表面粗糙度值小。压铸件尺寸公差等级可达CT3~CT6,表面粗糙度一般为Ra0.8~ 3.2μm。 3)压铸件中可嵌铸零件,既节省贵重材料和机加工工时,也替代了部件的装配过程,可以省去装配工序,简 化制造工艺。 2、压力铸造的缺点 1)压铸时液体金属充填速度高,型腔内气体难以完全排除,铸件易出现气孔和裂纹及氧化灾杂物等缺陷,压 铸件通常不能进行热处理。 2)压铸模的结构复杂、制造周期长,成本较高,不适合小批量铸件生产。 3)压铸机造价高、投资大,受到压铸机锁模力及装模尺寸的限制,不适宜生产大型压铸件。
近净成形技术
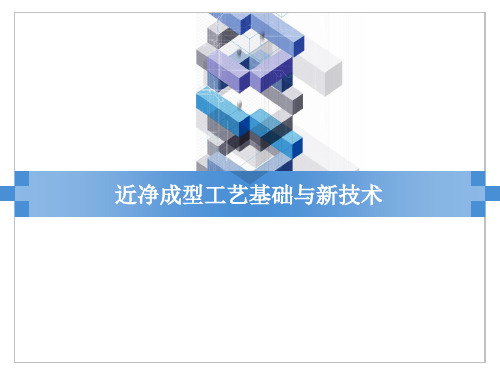
1.1 近净成形概念
近净成形技术是指零件成形后,仅需少量加工 或不再加工,就可用做机械零件的成形技术。它 将新材料、新能源、精密模具技术、计算机技术 自动化技术等多种高新技术融入传统的毛配成形 技术,使之由粗糙成形变为优质、高效、高精度 轻量化、低成本的成形技术。采用近净成形技术 所获得的机械零件具有精确的外形、高的尺寸精 度、形位精度和好的表面粗糙度。[2]
高、质量稳定、劳动条件好等优点,在工业发达国家这种生产线研究和建 设已有几十年历史,并且随着人们对产品个性化的要求,已经出现一些柔 性生产线。
1.3近净成形的发展概况
5.重视生产过程的质量控制,提高质量一致性 国外企业为了保证产品质量一方面加强管理,做好生产全过程的质量
控制,另一方面通过生产过程中的自动化和智能控制以保证近净成形生产 质量稳定,并且开发各种在线检测和无损检测技术和仪器,并且进行了统 计过程控制技术的研究和应用,从而使成形件的质量和精度可靠。上述几 项关键技术我国还有不小差距,也需要尽快掌握,从而保证最终成形件质 量。 6.发展近净成形技术的虚拟制造和网络制造
121精密铸造成形压铸循环过程压铸循环过程清理模具具具具具具具具具具具具具具具具具具具具具具具具具具具具具具具具具具具具具具具具具具具具具具具具具具喷刷涂料料料料料料料料料料料料料料料料料料料料料料料料料料料料料料料料料料料料料料料料料料料料料料料料合模模模模模模模模模模模模模模模模模模模模模模模模模模模模模模模模模模模模模模模模模模模模模模浇注注注注注注注注注注注注注注注注注注注注注注注注注注注注注注注注注注注注注注注注注注注注压射射射射射射射射射射射射射射射射射射射射射射射射射射射射射射射射射射射射射射射凝固固固固固固固固固固固固固固固固固固固固固固固固固固固固固固固固固固固固开模模模模模模模模模模模模模模模模模模模模模模模模模模模模模模模模模顶出出出出出出出出出出出出出出出出出出出出出出出出出出出出出出取出铸件件件件件件件件件件件件件件件件件件件件件件件件件件件全自动压铸循环全自动压铸循环全自动压铸循环全自动压铸循环全自动压铸循环全自动压铸循环全自动压铸循环全自动压铸循环全自动压铸循环全自动压铸循环全自动压铸循环全自动压铸循环全自动压铸循环全自动压铸循环半自动压住循环半自动压住循环半自动压住循环半自动压住循环半自动压住循环半自动压住循环半自动压住循环半自动压住循环半自动压住循环半自动压住循环半自动压住循环半自动压住循环半自动压住循环半自动压住循环半自动压住循环半自动压住循环清理模模模模模模模模模模模模模模模模模模模模模模模模模模模模模模模模模模模模模模模模模模模模模模模模模喷刷涂涂涂涂涂涂涂涂涂涂涂涂涂涂涂涂涂涂涂涂涂涂涂涂涂涂涂涂涂涂涂涂涂涂涂涂涂涂涂涂涂涂涂涂涂涂涂清理理理理理理理理理理理理理理理理理理理理理理理理理理理理理理理理理理理理理理理理理理理理理理理理喷刷刷刷刷刷刷刷刷刷刷刷刷刷刷刷刷刷刷刷刷刷刷刷刷刷刷刷刷刷刷刷刷刷刷刷刷刷刷刷刷刷刷刷刷刷刷清清清清清清清清清清清清清清清清清清清清清清清清清清清清清清清清清清清清清清清清清清清清清清清合合合合合合合合合合合合合合合合合合合合合合合合合合合合合合合合合合合合合合合合合合合合合喷喷喷喷喷喷喷喷喷喷喷喷喷喷喷喷喷喷喷喷喷喷喷喷喷喷喷喷喷喷喷喷喷喷喷喷喷喷喷喷喷喷喷喷喷浇浇浇浇浇浇浇浇浇浇浇浇浇浇浇浇浇浇浇浇浇浇浇浇浇浇浇浇浇浇浇浇浇浇浇浇浇浇浇浇浇浇浇压压压压压压压压压压压压压压压压压压压压压压压压压压压压压压压压压压压压压压凝凝凝凝凝凝凝凝凝凝凝
压力铸造详解
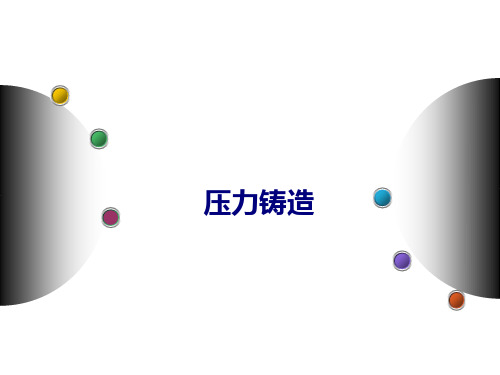
2.3 压铸应用范围和注意点 ① 压铸是实现少无切削加工的精密铸造技术,在汽车、 航空、仪表、 国防等工业部门广泛用于非铁金属的小型、 薄壁、形状复杂件的大批量生产。 ② 铸件壁厚均匀,以3-4mm的壁厚为宜,最大壁厚应小 于8mm,以防止缩孔、缩松等缺陷。 ③ 铸件不宜进行热处理或在高温下工作,以免铸件内气 孔中的气体膨胀而导致铸件变形或断裂。 ④ 由于内部疏松,铸件塑性和韧性差,故它不适合于制 造受冲击的零件。 ⑤ 铸件应尽量避免机械加工,以防内部孔洞外漏。
图3-4立式压铸机压铸过程示意图 1-压射冲头;2-压室;3-金属液;4-定模;5-动模;6-喷嘴;7-型腔; 8-返料冲头;9-余料
3.2.1 立式压铸优点: ①有余料切断、顶出功能; ②空气不易随金属进入压室; ③金属液进入型腔经过转折,压力消耗大。 3.3热室压铸 热室压铸的工作过程如图3-5所示。当压射冲头3上升 时,金属液1通过进口5进入压室4,随着压射冲头下压,液 体金属沿着通道6经喷嘴7填充铸型8;冷却后压射冲头回 升,多余的液体金属回流至压室中,然后打开铸型取出铸 件。
3.压力铸造的种类
根据压力机的不同,压力铸造可分为冷室压铸和热室压 铸两大类型。而按压铸机压力传递方式可分为立式和卧式两 种。冷室压铸机的压室与保温坩埚炉是分开的,压铸时从保 温坩埚中舀取金属液倒入压铸机上的压室后进行压射。而热 室压铸机的压室和保温坩埚连成一体。 3.1卧式冷室压铸 卧式压铸机的压室和压射机构处于水平位置。其工作原 理及过程如图3-1所示。
第Ⅳ阶段为增压阶段,该阶段主要是压射正在凝固的金属 液,是形成的铸件晶粒细小,组织致密;这时压射冲头只做小 位移移动
图3-2 压铸不同阶段压射冲头的压力与运动速度的变化
卧式冷室压铸广泛用于铝合金的压铸。其压铸过程示意图如图3-3。
压力铸造和实型铸造简介

压力铸造和实型铸造简介压力铸造和实型铸造属于特种铸造的范畴。
特种铸造是指除砂型铸造以外的其它铸造方法,如金属型铸造、压力铸造、熔模铸造和离心铸造等等。
这些铸造方法都各有其优越之处,但在应用上也各有其局限性。
2.5.1、压力铸造压力铸造是在高压作用下,将金属液以较高的速度压入高精度的型腔内,力求在压力下快速凝固,以获得优质铸件的高效率铸造方法。
它的基本特点是高压(5~15OMPa)和高速(5~1O0m /S)。
压力铸造的基本设备是压铸机。
压铸机可分为热室压铸机和冷室压铸机两大类,冷室压铸机又可分为立式和卧式等类型,但它们的工作原理基本相似。
图2-20为卧式冷室压铸机,用高压油驱动,合型力大,充型速度快,生产率高,应用广泛。
图2-20卧式冷室压铸机压铸型是压力铸造生产铸件的模具,主要由动型部分和定型部分两个大部分组成。
定型固定在压铸机的定型座板上,由浇道将压铸机压室与型腔连通。
动型随压铸机的动型座板移动,完成开合型动作。
完整的压铸型组成中包括型体部分、导向装置、抽芯机构、顶出铸件机构、浇注系统、排气和冷却系统等部分。
图2-21是压铸型总体结构示意图。
(l)型体部分型体部分包括定型和动型,在其闭合后构成型腔(有时还要和型芯共同构成型腔)。
(2)导向装置导向装置包括导柱和导套,其作用是使动型按一定方向移动,保证动型和定型在安装及合型时的正确位置。
(3)抽芯机构凡是阻碍铸件从压铸型内取出的成形部分,都必须做成活动的型芯或型块,在开型前或开型后自铸件中取出。
抽出活动型芯的机构称为抽芯机构。
(4)顶出铸件机构顶出机构的作用是开型过程中将铸件顶出铸型,以便取出铸件。
图2-21 压铸型总体结构示意图1-铸件;2-导柱;3-冷却水管;4-定型;5-动型;6-顶杆板;7-顶杆;8-型腔;9-排气槽;10-浇注系统卧式冷室压铸机的压铸过程如图2-22所示。
合型后,液态金属浇入压室2,压射冲头1向前推进,将液态金属经浇道7压入型腔6。
特种铸造之压力铸造

真空压铸镁合金
真空压铸铝件
4.1 铸造在压力下成形特征
但是在此机器上装斜和维护铸型比较麻烦,生产效率较 前两种冷压室压铸机低。
4.1.2 压铸时金属流的特征
压力铸造过程的主要特征就是金属在高压作用下的高速填充型腔。 因此欲掌握压铸件成型实质,主要就应了解压力铸造时金属充型过程中 的所受压力变化,充型时金属的流动形态,以便采取合适的技术措施, 充分运用压铸时金属充型特殊现象的有利方面,避免和克服此现象可能 带来的负面影响,高效地制造出质量符合要求的压铸件。
的致密度。此一增大的压力值一直保持到型内铸件完全凝固。
最终的压力值可为50~500MPa。
2、压铸时金属填充型腔的形态——理论假设
A 弗洛梅尔(Frommer)理论
Frommer 1932
1 当金属流经浇口进入型腔后,仍 保持浇口的断面直向型腔远端的对面型 壁射去;
2 待到达对面型壁厚,在此处的型 腔中聚积,消失了冲击力后,沿型壁在 整个型腔断面上反向移动。型腔中的空 气和随金属六进入型腔的空气依靠金属 液充型时的压力挤出型外: 如果浇口横截面积较小(浇口截面积 f/型腔截面积F>(1/3~1/4))反向流动平 稳,金属液以小的旋转涡流形式移动; 如果浇口截面积较大(f/F<1/3),则 液流速度高,返回流回呈现为强烈的涡 状紊流。
在后续进入型腔金属的补充 下,沿型腔整个断面向正对 浇口的另一端型腔填充,直 至充满型腔。
压力铸造及工艺特点
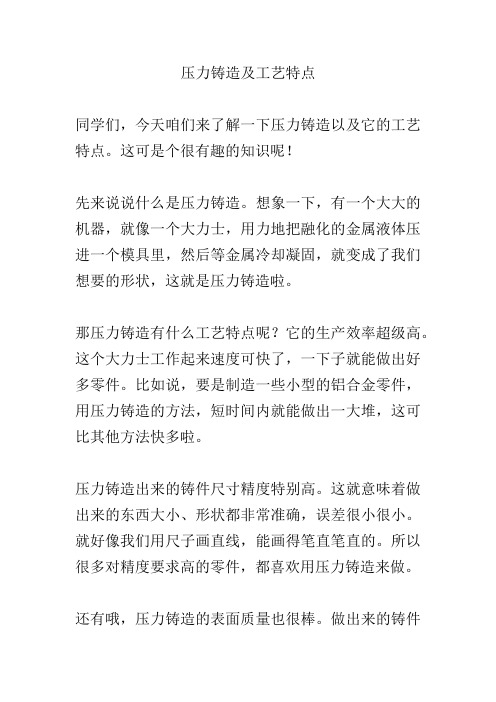
压力铸造及工艺特点同学们,今天咱们来了解一下压力铸造以及它的工艺特点。
这可是个很有趣的知识呢!先来说说什么是压力铸造。
想象一下,有一个大大的机器,就像一个大力士,用力地把融化的金属液体压进一个模具里,然后等金属冷却凝固,就变成了我们想要的形状,这就是压力铸造啦。
那压力铸造有什么工艺特点呢?它的生产效率超级高。
这个大力士工作起来速度可快了,一下子就能做出好多零件。
比如说,要是制造一些小型的铝合金零件,用压力铸造的方法,短时间内就能做出一大堆,这可比其他方法快多啦。
压力铸造出来的铸件尺寸精度特别高。
这就意味着做出来的东西大小、形状都非常准确,误差很小很小。
就好像我们用尺子画直线,能画得笔直笔直的。
所以很多对精度要求高的零件,都喜欢用压力铸造来做。
还有哦,压力铸造的表面质量也很棒。
做出来的铸件表面光滑平整,就像镜子一样。
比如说,一些汽车的零部件,用压力铸造做出来,表面又好看又光滑,质量杠杠的。
但是呢,压力铸造也有一些小缺点。
因为压力很大,模具很容易磨损,所以模具的成本就比较高啦。
而且,不是所有的金属都适合用压力铸造的方法,只有那些能在压力下快速凝固的金属才行。
压力铸造的时候,因为金属液是在高压下快速填充模具的,所以铸件内部容易产生气孔。
这就像我们吹气球,如果吹得太快太猛,气球里可能就会有一些小气泡。
在很多领域都发挥着重要的作用。
比如说,在航空航天领域,那些精密的零件很多都是通过压力铸造做出来的;在电子行业,像手机的外壳、电脑的配件,也经常用到压力铸造。
同学们,现在你们对压力铸造和它的工艺特点是不是有了更清楚的了解啦?希望大家以后在生活中看到相关的产品,能想到今天学到的知识哦!。
- 1、下载文档前请自行甄别文档内容的完整性,平台不提供额外的编辑、内容补充、找答案等附加服务。
- 2、"仅部分预览"的文档,不可在线预览部分如存在完整性等问题,可反馈申请退款(可完整预览的文档不适用该条件!)。
- 3、如文档侵犯您的权益,请联系客服反馈,我们会尽快为您处理(人工客服工作时间:9:00-18:30)。
➢ 不宜小批量生产,其主要原因是压铸型制造成本 高,压铸机生产效率高,小批量生产不经济。
压铸应用范围
➢压铸合金包括锌、铝、镁、铜、铸铁和 铸钢。
➢铸件形尺寸可以从几毫米到1~2m;重 量可以从几克到数十公斤。
➢压铸件应用于汽车、仪表、农业机械、 机床工业、电子工业、国防工业、计算 机、医疗器械、钟表、照相机和日用五 金等几十个行业。
压力铸造优点
➢ 压铸件尺寸精度高,表面粗糙度值低 ➢ 材料利用率高 ➢ 可以制造形状复杂轮廓清晰、薄壁深腔的
金属零件 ➢ 可以嵌铸其他材料的零件 ➢ 压铸件组织致密,具有较高的强度和硬度 ➢ 生产率极高
压力铸造缺点
➢ 液态金属流态不稳定,采用一般压铸法,铸件易 产生气孔,不能进行热处理;
➢ 铸件尺寸受锁模力及装模尺寸的限制。对内凹复 杂的铸件,压铸较为困难;
压铸发展趋势
➢ 压铸机向系列化、大型化及自动化发展; ➢ 计算机在压铸生产中的应用日益广泛; ➢ 压铸工艺不断采用新技术,开展延长压铸模寿
命研究。
压铸技术有真空压铸、加氧压铸、精速密压铸以及可 溶型芯应用等新工艺。
压铸机简介
压铸机一般分为 冷压室压铸机 和 热压室压铸机 两大类。
冷压室压铸机
➢按其压室结构和布置方式分为卧式压铸 机和立式压铸机(包括全立式压铸机) 两种。
热压室压铸机(简称热室压铸机)
➢压室浸在保温溶化坩埚的液态金属中, 压射部件不直接与机座连接,而是装在 坩埚上面。
➢优点是生产工序简单,效率高;金属消 耗少,工艺稳定。但压室、压射冲头长 期浸在液体金属中,影响使用寿命。并 易增加合金的含铁量。
热压室压铸机压铸过程
1-坩埚 2-进口 3-压室 4-压射冲头 5-液态金属 6-通道 7-喷嘴
《材料精确成形技术》 第十讲
压力铸造技术
在高压作用下,使液态或半液态金属以较 高的速度充填压铸型型腔,并在压力下成 型和凝固而获得铸件的方法,简称压铸。
课程内容
➢压力铸造工艺过程 ➢压力铸造特点 ➢压铸应用范围及发展趋势 ➢压铸机简介 ➢压力铸造工艺简介
压铸生产工艺过程
产品图
铸件成品入库
工艺设计
质量检验
废品、浇注系统
铸型设计
外观检验 及清理
废 品 原材料准备
铸型制造
开型取件
回
炉料配制
炉Leabharlann 料铸型安装压铸成型
合金熔化
铸型预热
浇注
合金液保温
喷刷涂料
合型
压力铸造特点
高压和高速充填是压铸的两大特点。 ➢ 常用的压力是15~100MPa。 ➢ 充填速度约在10~50m/s,有些时候甚至可达
100m/s以上。 ➢ 充填时间很短,一般在0.01~0.2s范围内。
压力铸造的充型特点
层流充填
压力铸造的充型特点
湍流充填
a) 流股撞击型壁 b) 形成涡流
c) 充型
压力铸造的充型特点
弥散式充填
压铸型总体结构示意图
1-铸件 2-导柱 3-冷却水管 4-定型 5-动型 6-顶杆板 7-项杆 8-型腔 9-排气槽 10-浇注系统
辅助系统
溢流槽及尾部排气槽
抽芯机构
立式冷压室压铸机压铸过程
a) 合型浇注 b) 压射 c) 推出余料,开型取件 1-压射冲头 2-浇勺 3-液态金属 4-反料冲头 5-动型 6-静型 7-压室 8-推杆 9-铸件 10-余料 11-浇口套
全立式冷压室压铸机压铸过程
a) 定型与动型 b) 合型压铸 c) 开型 1-压射冲头 2-液态金属 3-压室 4-定型 5-动型 6-型腔 7-余料
➢冷室压铸机的压室与保温炉是分开的。 压铸时,从保温炉中取出液体金属浇入 压室后进行压铸。
冷压室压铸机
冷压室压铸机
热压室压铸机
卧式压铸机压铸过程
a) 合型浇注 b) 压射 c) 开型 d) 顶出铸件 1-动型 2-静型 3-浇勺 4-压室 5-浇注孔 6-推杆 7-铸件 8-余料 9-压射冲头 10-金属液
抽芯机构
思考题
➢ 压力铸造为什么必须有高的金属液流动 速度和高的压力?
➢ 简述压铸型的构造。 ➢ 简述压力铸造技术的优点和缺点。
作业题
➢ 比较冷室压铸机和热室压铸机的优缺点。