汽车焊装夹具设计—CATIA设计流程论文
关于汽车车身焊装夹具设计探讨

关于汽车车身焊装夹具设计探讨摘要:在汽车车身前期设计中,焊装夹具设计是十分关键的内容,设计质量以及加工工艺能够直接影响汽车车身制造质量。
对此,本文首先对汽车车身焊装夹具的作用及组成进行介绍,然后对汽车焊装夹具设计原则以及具体的设计策略进行详细探究。
关键词:焊装;夹具;设计新时期,汽车已成为人们日常出行中的常用交通工具,通过加强汽车焊接质量控制,有利于提高汽车制造质量,促进汽车行业稳定发展。
汽车焊装夹具会直接影响汽车制造周期以及精度,因此,必须重点关注汽车焊装夹具设计。
一、汽车车身焊装夹具的作用及组成现如今,我国汽车使用量在世界范围内占据首位,国内汽车制造行业面临很多发展机遇和挑战,在汽车生产制造方面,车身质量管控至关重要,而不同车型的车身结构形式比较复杂,在具体的设计过程中构图难度大,在各类因素影响下容易发生变形,同时,车身尺寸还会对汽车结构装配质量以及效率产生较大影响,对此,需加强焊接装配工艺控制。
为了促进汽车车身焊接质量提升,应对焊装夹具进行优化设计,进而实现汽车车身流水线生产,尽量缩短焊接装配所需时间,同时通过提高夹具设计精度,还可保证汽车焊接装配质量和效率。
在汽车车身生产制造中,焊装夹具是十分重要的工具,通过快速定位工作元件,能够保证元件焊装的准确性。
在汽车制造中,在金属结构焊接方面,焊装夹具为十分关键的工具类型,在焊接工艺中可发挥夹持和固定的功能,确保汽车焊接工件的形状以及尺寸能够满足企业前期设计方案要求。
在具体的汽车车身焊接过程中,需充分发挥夹具的辅助作用,尽量减少焊接所需时间。
通常情况下,焊装夹具是由三个元件所组成的,即基础元件、符合标准元件以及外购元件[1]。
二、汽车焊装夹具设计原则在汽车焊装夹具设计中,对于整个设计过程,可分为四个环节,包括定位、夹紧、辅助元件以及夹具空间设计。
在具体的设计过程中,必须严格遵循六点定则,具体而言,需对六个方向自由度进行严格控制。
在对汽车车身六个方向自由度进行限定时,可联合应用孔定位法、面定位法等,确保零件定位准确性。
CATIAV5在汽车白车身焊装与检验夹具设计中的应用
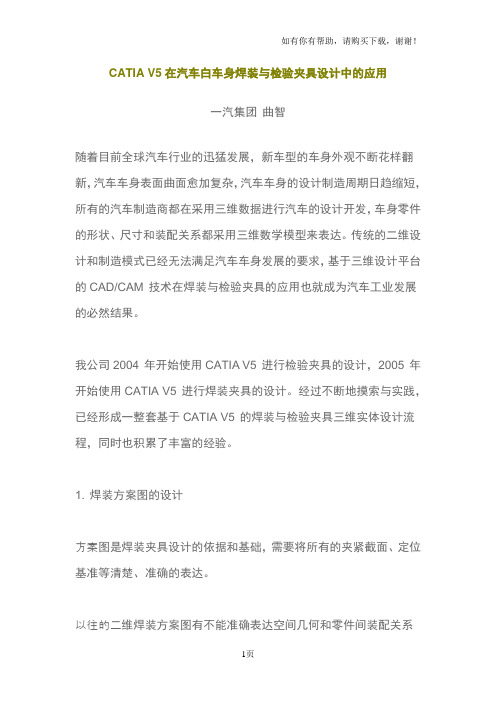
CATIA V5在汽车白车身焊装与检验夹具设计中的应用一汽集团曲智随着目前全球汽车行业的迅猛发展,新车型的车身外观不断花样翻新,汽车车身表面曲面愈加复杂,汽车车身的设计制造周期日趋缩短,所有的汽车制造商都在采用三维数据进行汽车的设计开发,车身零件的形状、尺寸和装配关系都采用三维数学模型来表达。
传统的二维设计和制造模式已经无法满足汽车车身发展的要求,基于三维设计平台的CAD/CAM 技术在焊装与检验夹具的应用也就成为汽车工业发展的必然结果。
我公司2004 年开始使用CATIA V5 进行检验夹具的设计,2005 年开始使用CATIA V5 进行焊装夹具的设计。
经过不断地摸索与实践,已经形成一整套基于CATIA V5 的焊装与检验夹具三维实体设计流程,同时也积累了丰富的经验。
1. 焊装方案图的设计方案图是焊装夹具设计的依据和基础,需要将所有的夹紧截面、定位基准等清楚、准确的表达。
以往的二维焊装方案图有不能准确表达空间几何和零件间装配关系等固有缺点,设计所需信息不全,不能很有效的指导焊装夹具的设计,容易造成后期设计大量修改。
现在,我们利用CATIA V5 进行方案图的三维设计(如下图),可以准确的表达各类几何关系、装配关系、设计信息(包括坐标轴系,焊点、夹紧截面位置和夹紧方式、产品定位基准和方式、夹具零件的定位元素等),能够有效地指导后期设计,大大减少了方案图和夹具图的错误和修改。
对于主机厂提供的方案图,我们也要将其三维化,目的是一方面初步检查焊装方案的可行性,同时将后期结构设计所需要的设计信息补充完整,以方便后期结构设计加以利用。
2. 焊装与检验夹具设计A、PowerCopy 和User Feature(UDF)的应用我们利用CATIA 的PowerCopy 和UDF 功能,实现了一些标准样式结构的自动化生成。
例如检验夹具设计过程中,有很多位置使用相同的检测方式,这些地方需要设计员做大量的曲面造型工作,而造型过程往往所用的命令、功能乃至步骤都完全一样,只不过是初始输入条件不同,使得造型过程费时费力。
catia作业论文

汽车与发动机CAD/CAE——Catia在汽车工业上的应用以及用Catia画三通管接头摘要:汽车行业是一个高速发展的行业,其竞争日趋激烈。
随着新产品推出的速度越来越快,CAD/CAE在汽车行业的应用越来越多,水平也在逐步提高。
当代汽车开发和制造技术中,涵括了当今各个基础学科和最新科技,实现汽车结构和部件总成的正向设计与制造技术、缩短汽车开发周期、降低成本、减少汽车产品开发风险等因素直接关系到企业的自主创新力。
而Catia是汽车行业中应用最广泛的cad软件,于是我就学习用catia绘制关于汽车方面的零件,并加以解释和标记。
关键词:CAD/CAE; 软件应用;汽车开发;Catia;三通管接头引言CA TIA是法国达索公司的产品开发旗舰解决方案。
作为PLM协同解决方案的一个重要组成部分,它可以帮助制造厂商设计他们未来的产品,并支持从项目前阶段、具体的设计、分析、模拟、组装到维护在内的全部工业设计流程。
1软件概述CA TIA由法国DassaultSystems(达索)公司开发,后被美国IBM公司收购的CA TIA是一个全面的CAD/CAM/CAE/PDM应用系统。
居世领导地位,广泛应用于航空航天、汽车、造船、机械制造、电子\\电器、消费品等行业,它的集成解决方案覆盖所有的产品设计与制造领域,其特有的DMU电子样机模块功能及混合建模技术更是推动着企业竞争力和生产力的提高。
CATIA对产品整个开发过程包括概念设计、详细设计、工程分析、成品定义和制造乃至成品在整个生命周期中的使用和维护。
而且CA TIA能够模拟观察者的视野进入到零件的内部去观察零件,使用者只要输入人的性别、身高等特征,就会出现一个虚拟装配的工人。
2Catia在汽车设计制造中的应用2.1齿轮力齿轮的弯曲应力和接触应力分析:齿轮是汽车发动机和传动系中普遍采用的传动零件。
通过对齿轮齿根弯曲应力和齿面接触应力的分析,优化齿轮结构参数,提高齿轮的承载载力和使用寿命。
浅谈汽车焊装夹具的设计

等要充分考虑其加工工艺性及零部件的通用化和标准化, 便于更换易损件和恢复原设计精度。(5)车身总成的装 焊夹具比较复杂笨重,在制造使用中常需调整样架来进 行调整校正。2.2 装焊定位基准的选
择装夹工件时,使工件在夹具中占有正确位置所采用的 基准,称为定位基准,定位基准的选择正确与否将直接 影响工件的装配精度。2.3 定位方法和定位元件车身装焊 夹具装夹的主要对象是冲压件,由于制
,有手动,气动、液压式等,这些夹紧机构的设计与一 般机床夹具设计大同小异,可参考借鉴。2.5 车身总成装 焊夹具车身总成装焊夹具按其定位方式分为一次性定位 和多次性定位。一次性装配定位的总装
夹具是指车身总成的主要装焊工作在一台总装夹具上完 成。组成车身的零件,合件,分总成等依次装到总装夹 具上,进行定位和夹紧,直至车身总成的主要装焊工作 完毕,才从夹具上取下来。这种夹具的特点是
要求(1)对于冲压零件装焊后应具有互换性的车身合件 及总成,应使用车身的各配合部位,特别是孔洞的形状 尺寸符合技术要求。(2)能快速准确地进行装配定位、 夹紧,被焊部位要便于操作,松开夹紧机
构后,焊件能从夹具上方便地卸下,且安全可靠。(3) 在设计夹具时,要注意夹具上的某些零部件出现导电, 绝缘等问题,提高车身的装焊质量。(4)由于车身结构 复杂,因此,对所设计的定位件、夹紧件
身总成的主要装焊工作是在2台以上的不同装焊夹具上完 成的。车身每通过一台总装夹具就要被定位夹紧1次,主 要用于有骨架驾驶室的装焊,如在第一台夹具上完成内 骨架的装简单,数量少,不存在 水,电,气的连接问题,若增加定位夹紧次数,则容易 产生装配误差。3 设计流程分析以某汽车的前地板预总成 工位的某一焊装夹具为例,阐述其焊装夹
作外形复杂且易变形,因此在夹具设计时应考虑用曲面 外形、曲面上经过整形的平台、工件经拉延和弯曲成形 的台阶、经修边的窗口和外部边缘、装配用孔和工艺孔 等部位定位。由于冲压件外形复杂,装夹过程
分析车身焊接夹具的设计规律论文
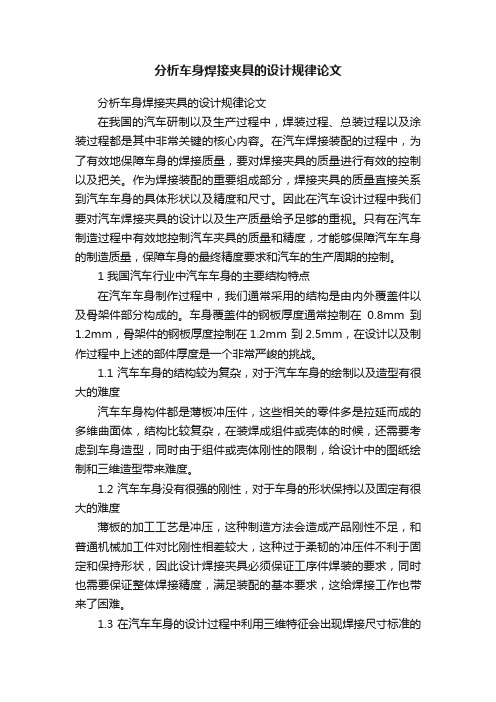
分析车身焊接夹具的设计规律论文分析车身焊接夹具的设计规律论文在我国的汽车研制以及生产过程中,焊装过程、总装过程以及涂装过程都是其中非常关键的核心内容。
在汽车焊接装配的过程中,为了有效地保障车身的焊接质量,要对焊接夹具的质量进行有效的控制以及把关。
作为焊接装配的重要组成部分,焊接夹具的质量直接关系到汽车车身的具体形状以及精度和尺寸。
因此在汽车设计过程中我们要对汽车焊接夹具的设计以及生产质量给予足够的重视。
只有在汽车制造过程中有效地控制汽车夹具的质量和精度,才能够保障汽车车身的制造质量,保障车身的最终精度要求和汽车的生产周期的控制。
1 我国汽车行业中汽车车身的主要结构特点在汽车车身制作过程中,我们通常采用的结构是由内外覆盖件以及骨架件部分构成的。
车身覆盖件的钢板厚度通常控制在0.8mm到1.2mm,骨架件的钢板厚度控制在1.2mm 到2.5mm,在设计以及制作过程中上述的部件厚度是一个非常严峻的挑战。
1.1 汽车车身的结构较为复杂,对于汽车车身的绘制以及造型有很大的难度汽车车身构件都是薄板冲压件,这些相关的零件多是拉延而成的多维曲面体,结构比较复杂,在装焊成组件或壳体的时候,还需要考虑到车身造型,同时由于组件或壳体刚性的限制,给设计中的图纸绘制和三维造型带来难度。
1.2 汽车车身没有很强的刚性,对于车身的形状保持以及固定有很大的难度薄板的加工工艺是冲压,这种制造方法会造成产品刚性不足,和普通机械加工件对比刚性相差较大,这种过于柔韧的冲压件不利于固定和保持形状,因此设计焊接夹具必须保证工序件焊装的要求,同时也需要保证整体焊接精度,满足装配的基本要求,这给焊接工作也带来了困难。
1.3 在汽车车身的设计过程中利用三维特征会出现焊接尺寸标准的问题汽车车身的.焊接具有非常强的三维空间特征,而且三维跨度非常大,这给焊接夹具设计中的尺寸标注带来了一定的困难。
为保证夹具能符合要求,必须对车身进行空间坐标标注,为夹具的空间尺寸特征提供必要的参数。
浅谈汽车焊接夹具的结构设计
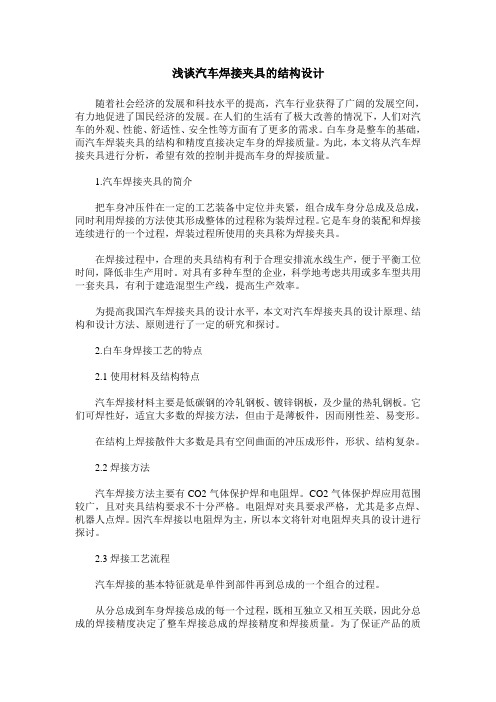
浅谈汽车焊接夹具的结构设计随着社会经济的发展和科技水平的提高,汽车行业获得了广阔的发展空间,有力地促进了国民经济的发展。
在人们的生活有了极大改善的情况下,人们对汽车的外观、性能、舒适性、安全性等方面有了更多的需求。
白车身是整车的基础,而汽车焊装夹具的结构和精度直接决定车身的焊接质量。
为此,本文将从汽车焊接夹具进行分析,希望有效的控制并提高车身的焊接质量。
1.汽车焊接夹具的简介把车身冲压件在一定的工艺装备中定位并夹紧,组合成车身分总成及总成,同时利用焊接的方法使其形成整体的过程称为装焊过程。
它是车身的装配和焊接连续进行的一个过程,焊装过程所使用的夹具称为焊接夹具。
在焊接过程中,合理的夹具结构有利于合理安排流水线生产,便于平衡工位时间,降低非生产用时。
对具有多种车型的企业,科学地考虑共用或多车型共用一套夹具,有利于建造混型生产线,提高生产效率。
为提高我国汽车焊接夹具的设计水平,本文对汽车焊接夹具的设计原理、结构和设计方法、原则进行了一定的研究和探讨。
2.白车身焊接工艺的特点2.1使用材料及结构特点汽车焊接材料主要是低碳钢的冷轧钢板、镀锌钢板,及少量的热轧钢板。
它们可焊性好,适宜大多数的焊接方法,但由于是薄板件,因而刚性差、易变形。
在结构上焊接散件大多数是具有空间曲面的冲压成形件,形状、结构复杂。
2.2焊接方法汽车焊接方法主要有CO2气体保护焊和电阻焊。
CO2气体保护焊应用范围较广,且对夹具结构要求不十分严格。
电阻焊对夹具要求严格,尤其是多点焊、机器人点焊。
因汽车焊接以电阻焊为主,所以本文将针对电阻焊夹具的设计进行探讨。
2.3焊接工艺流程汽车焊接的基本特征就是单件到部件再到总成的一个组合的过程。
从分总成到车身焊接总成的每一个过程,既相互独立又相互关联,因此分总成的焊接精度决定了整车焊接总成的焊接精度和焊接质量。
为了保证产品的质量,这就要求从单件到总成的各个焊接工序采用统一的定位基准。
在整车出现质量问题时便于质量问题原因的分析,便于整改和控制。
基于CATIA的汽车车身焊装夹具设计
属J : f I : 十 , J ; 汁 制造1 ' 1 9 f
钎. J 1 纳 i I 休1 4
的结 构 、, l i 广 : 条什 干 l 际 求 米 I l I "没汁 ‘ 州州 造 , J : C A - r l A的J j = l I l 火 没汁 . i I r 以缩 n 汁删 J 9 】 . 扔 样. r I = 改【 I I l I = l f i l l 1 , 摊I } I } 汁效 l
1 夹具设计前期 准备工作
1 . 1 整理分 析 客户提 供 的数据
』 ’ , 捉供 J 的 I 艺艾 件 ( 包折 I : J l l O i J 、 点[ 冬 I 、 I t , f 、 J MC P l 冬 1 等) . ㈨I 1还 I l f 会j = 址 供数十 l l 、 定化 俯息 ・ 和 钳的十 ¨ 火f 。 息 、I ) 一 内 数十 I l 达 r J M的符利 儿f f J J 火系 i 殳 汁价 、 ,I 上 ・ l t J ’ 受 儿个I 冬什 ,
火系 ̄ t l ' f , l 熟 悉数卡 ; ! 址 没汁 必j I 的 + 个必 ’ 条件 ,
2 ) 焊点 i , f 以 7 子 焊点 数模 的f ,榆 J 介 性. J i 选择 十 ¨ 的 枪 3 )MC P『 冬 1 址定 义 必J 定f
基于 C A T I A的汽车 车身焊装 夹具设计
冯 明 佳
( 吉林农 此 科技 学院 机 械工桃 学院。 吉林 古林 1 3 2 I ( 1 I ) 摘要 : ' y ( 1 1 l 址f e 1 I 的 5 什之 - . l J 制造胍j I { = 址抛 『 f ( 1 怵啦 J n l r ( r 的核心 分 . 址 i l l 1 1 披 I 汁f f { j 骤. j i …i 汁r i l l ( 1 9 i I { 意
基于CATIA VBA二次开发汽车焊装夹具智能设计系统的技术方案V1.0
基于CATIA VBA二次开发汽车焊装夹具智能设计系统的技术方案一.绪论随着市场竞争日益激烈,制造业中起着重要作用的人工夹具设计已经不能满足生产的需要,有着高效快捷特点的计算机辅助夹具设计(CAFD)应运而生。
计算机辅助夹具设计经历了不同的发展阶段,技术日趋成熟并且正在逐步应用到生产实际之中,起到缩短生产周期、提高设计质量、降低生产成本、提高设计和生成效率等等多方面的作用。
1.1项目的研究背景和意义随着世界经济飞速发展和市场的全球化,制造业空前激烈发展。
传统的制造技术已经不能适应经济的高速发展,也不能满足多样性的要求,为了改进传统的制造技术,提高生产效率,使企业在竞争中获胜,对工艺装备的柔性化提出了迫切的要求。
计算机辅助夹具设计技术就是在上述背景下产生的,即利用计算机辅助人工进行夹具设计的一种先进制造技术。
最初的CAFD系统是交互式设计界面,可以完成相对复杂的夹具设计任务,在一定程度上节省了设计绘图和修改的时间。
随着计算机水平的提高和各种理论的成熟,在基于成组技术和知识工程的基础上CAFD带有一定的智能性,提高了夹具设计自动化程度。
目前的CAFD 系统正在朝着以实际生产应用为导向的计算机辅助夹具设计上发展,使其更具智能化和自动化。
最终,带来工程设计速度加快和节约设计成本两方面的益处,改善汽车焊装夹具建模过程,减少夹具设计所需的经验,使设计过程便捷省力,使设计过程更加灵活。
1.1.1项目的研究背景在现代汽车生产中,焊装夹具是必不可少的工具。
它们用于保持汽车零部件在正确的位置并确保焊接的准确性和一致性。
然而,传统的焊装夹具设计方法存在许多不足之处,如设计效率低下、重复劳动等。
因此,开发一种基于CATIA VBA的二次开发汽车焊装夹具智能设计系统具有重要的研究意义。
1.1.2项目的研究意义通过开发智能设计系统,可以提高焊装夹具的设计效率和精确度。
智能设计系统可以利用计算机的案例推理和规则推理技术,根据之前的经验和规则来生成夹具设计方案,减少设计师的重复工作。
汽车车身焊装夹具设计
汽车车身焊装夹具设计摘要:汽车车身通过冲压、焊装、涂装、总装配制造而成。
车身在焊装过程中要使用多点定位夹紧的专用夹具来保证各零件在焊接处的正确位置。
因为汽车工业的快速发展,大大提高了制造车身水平。
制造车身质量决定了整个车身的品质,而车身装焊设计中焊装线设计是重要组成部分,在设计的时候要充分的了解到产品的功能,认识产品的精确参数,方便在现实应用中增加安全性与实用性。
焊装夹具设计是不是合理,最后唯有通过生产实践检验,才可以证明是合格与优秀的,而在设计以前,一定要做到精益求精,使损失减少,创造出与时代需求相符的产品。
关键词汽车车身;焊装夹具;设计方法制作汽车的精度和汽车车体的生产周期与汽车焊接夹具的要求有关性特别高,在设计的时候我们要非常注意。
所以,确保汽车生产与制造质量的一个重要性程序就是设计与制造汽车焊接夹具,同时,也是需要很多的经验和制造、设计技术的一项工作,增强汽车焊接夹具的研究具备关键意义。
1车身焊装夹具简介焊装夹具基本由底板、支基、气控三部分组成。
焊装夹具用三坐标进行检测。
焊装夹具的常见结构有定位元件和夹紧元件。
定位元件有定位销、定位块。
定位块和定位销座均采用可调式结构,通过调整垫片数量的增减来调整定位块的精确位置。
定位块的定位面、销孔要求热处理后精加工。
夹紧机构有手动、气动两种夹紧方式。
杠杆式定位夹紧单元的基本类型有气缸固定式、双面夹紧机构、手动夹紧气路退回式等模式。
该类型适用于一般夹紧,该模块除了定位块、导向杆之外,其余的零件都是由压板的草图控制。
2焊装夹具的设计要点和常见问题焊装夹具的设计主要考虑焊接质量和人机工程。
为保证焊接质量,应合理确定薄板冲压件焊接搭接顺序,要合理确定定位点和定位方式,焊装夹具在运动过程中无干涉,设计夹紧气路时,考虑焊接完成后是否能取出整体零件。
人机工程能保证操作人员能够舒适、安全地工作,设计时考虑夹具平均操作高度、焊钳类型,基准平台可根据情况安置回转机构。
3车身焊接夹具设计的必要性在设计和制造车身的很多开发程序过程中,特别关键的一个程序就是车身焊接夹具设计,其直接关系着制造出产品的合格率。
汽车焊装夹具设计理论研究
汽车焊装夹具设计理论研究1. 引言1.1 研究背景汽车焊装夹具是在汽车生产过程中必不可少的工具,它承担着固定焊接零部件、保证焊接精度、提高生产效率等重要作用。
随着汽车产业的发展和技术的更新换代,汽车焊装夹具的设计也越来越受到关注。
研究背景:在汽车制造过程中,焊装工艺是其中一个重要环节,焊装质量直接影响到汽车的安全性和性能。
而汽车焊装夹具作为焊装过程中的关键设备,直接影响着焊接部件的精准度和稳定性。
对汽车焊装夹具的设计理论进行深入研究,不仅能够提高焊装质量和效率,还能够满足不断变化的汽车制造需求。
通过对汽车焊装夹具设计理论的研究,可以不断改进现有的设计方法,提高设计的精准度和实用性,为汽车制造业的发展提供更好的支持。
深入探讨汽车焊装夹具设计理论具有重要的理论和实践意义,对于提高汽车制造水平和推动产业发展具有积极的作用。
1.2 研究意义汽车焊装夹具设计在汽车制造中起着至关重要的作用,能够有效提高生产效率、保证焊接质量、降低生产成本。
随着汽车工业的发展,对焊装夹具设计的要求也越来越高,需要不断进行研究和优化。
深入探究汽车焊装夹具设计的理论研究具有重要的实践意义和现实意义。
汽车焊装夹具设计的优化能够提高生产效率,缩短生产周期。
合理设计的焊装夹具能够提高焊接效率,减少生产过程中的等待时间,从而提高汽车制造的整体效率。
汽车焊装夹具设计的优化能够保证焊接质量。
精准的夹具设计能够确保焊接部件的准确定位,保证焊接部位的精准对接,从而提高焊接质量,减少焊接缺陷。
深入研究汽车焊装夹具设计理论,不仅有助于提高汽车生产效率、保证焊接质量,同时也能够降低生产成本,具有重要的意义和价值。
2. 正文2.1 焊装夹具设计的基本原理焊装夹具设计的基本原理是指在汽车生产中,为了保证焊接时的精度和稳定性,需要设计一种特定的夹具来固定工件。
这种夹具通常由钢制成,具有一定的形状和尺寸,能够精确地固定工件并保持焊接位置的稳定性。
在设计夹具时,首先需要考虑工件的形状和尺寸,以确定夹具的结构和尺寸。
- 1、下载文档前请自行甄别文档内容的完整性,平台不提供额外的编辑、内容补充、找答案等附加服务。
- 2、"仅部分预览"的文档,不可在线预览部分如存在完整性等问题,可反馈申请退款(可完整预览的文档不适用该条件!)。
- 3、如文档侵犯您的权益,请联系客服反馈,我们会尽快为您处理(人工客服工作时间:9:00-18:30)。
基于CATIA汽车焊装夹具设计流程
1 Project文档Directory的预备
1.1创建Project Directory
具体位置请向你的System Administrator问询。
其目录结构,如图1.1所示:
图1.1 文档目录结构
1.2 文件名命名规则
u工件:工位代号—UNIT号—零件序号(与相应图纸图号相比,少项目代号)例:FW002L-00-00 ——FW002L工位的GA
FW002L-01-00 —— FW002L工位的U01
FW002L-01-01—— FW002L工位U01的零件01
u标准件:名称与标准件号一致。
但若文件内容更改,文件名也要作相应修改。
u外购件:名称与样本订购编号一致。
气缸后面加“ _ 实际应用行程”
u国标件:国标号_型号例:GB93-87_8 代表弹簧垫圈8
2 CATIA 设计过程中的工作环境
如图2.1所示,设计所涉及的模块包括:
2.1零部件设计
做基本PART 的设计,对某个PART 一般设计和修改时所在的工作状态。
2.2装配件设计
在对PRODUCT 操作和修改时所在的工作状态。
可以完成装配和新建产品和零部件。
2.3草图绘制器
图2.1 CATIA 主要模块
当新建文件时要先画草图再拉伸,当在PART下画草图时自动进入该状态。
按工作台按钮自动退出。
2.4工程图绘制
做二维图时所在的状态。
新建DRAWING时自动进入。
2.5线框和曲面设计/创成式外形设计
是在操作PART时的一种状态,可以和零部件设计状态互换,当一些操作在零部件设计状态下不能完成时可以在该状态下完成。
如画圆、作曲面的有关操作时。
3设计步骤
3.1 新建PRODUCT文件为工位总成
图3.1 新建产品对话框
如图3.1所示,建立新产品。
如图3.2所示,对PRODUCT 操作,右键—属性—产品—零部件号,进行修改,改为工位总成编号,“确定”后保存到工位文件夹下如:…\FW002L 。
3.2加载PANEL
如图3.3所示,在GA 下使用插入“现在组件”
图3.2 修改产品属性
1 选择产品节点
2 修改产品属性
3.3 创建模拟焊点
如图3.4所示,在GA 下使用新建“产品”分别建单元PRODUCT ,用“右键—属性—产品—实体名称/零部件号”重命名为
WELDING-POINTS-ASSEMBLY 和WELDING-POINTS 零件节点。
进入线框和曲面设计/创成式外形设计,WELDING-POINTS 节点,利用“点”和“球”工具创建Φ16球面。
图3.3 装配车身数模
1 选择总装配节点
2 装配现有部件
3.4 插入焊枪
如图3.5所示,插焊枪前一般要在焊点位置做垂直于PNL 面的线,可以在“零部件设计”里操作,如果不行可切换到“线框和曲面设计”里操作。
用 “现在组件”或“具有定位的现在组件”插入焊枪。
并使用中的各个按钮来定位焊枪的位置,或用中的各个按钮来快速定位焊枪的位置。
图3.4 创建模拟焊点
图3.5 创建模拟焊枪
3.5 创建单元PRODUCT.
如图3.6所示,用“右键—属性—产品—实体名称/零部件号”重命名,并逐个激活后保存到UNIT文件夹。
图3.6 创建夹具单元产品装配树
3.6 UNIT 单元装配建模设计
3.6.1创建断面线
1创建UNIT 断面及装配草图零件。
如图3.7所示,在各单元下分别使用新建“零部件”建各单件PART ,用“右键—属性—产品—实体名称/零部件号”重命名,如FW002L-01-SECTION 。
激活此零件节点,进入零件设计,根据MCP 夹具UNIT 位置,创建位置轴系和断面位置处的平面对象。
用“轴系统”插入本单元设计所需的坐标系。
在“轴系统定义”对话框中“源”的选项框里用“右键—坐标”输入所需相对坐标原点的值,在“X 轴、Y 轴、Z 轴”的选项框里分别用“右键—旋转”输入所需坐标转动的角度就可行到所需相对坐标系。
2创建UNIT 断面
如图3.8所示,用“插入->线框->相交曲线”创建断面线。
图3.7 创建断面位置平面
1 创建轴系
2 创建断面位置平面
3创建UNIT 断面装配草图
如图3.9所示,点击“草图编辑器”中的“草图”,然后选取所建草图所在的基准面,将自动进入“草图绘制器”状态。
使用“轮廓”里的各命令画出所需草图的轮廓,用“操作”里的各命令修饰、修剪所画的草图,用“约束”里的各命令给所画的草图加上约束,其中未约束的部分显示白色,已约束的部分显示绿色,过约束的部分显示红色。
如在作草图的过程中转动过视图则可通过点击“视图”里的“法线视图”使视图从新摆正。
完毕后点击“工作台”里的“退出工作台”将自动退出“草图绘制器”状态,重新进进“零部件设计”模式。
图3.8 创建断面
3.6.2 创建UNIT 单元中加工零件 1 复制粘贴总装配草图到单个零件
图3.10 创建夹具单元UNIT 零件
图3.9 创建装配草图
1 创建草图
2 绘制草图
如图3.10所示,在各单元下分别使用新建“零部件”建各单件PART ,用“右键—>属性—>产品—>实体名称/零部件号”重命名,并逐个击活后保存到UNIT 文件夹。
如图3.11所示,复制装配草图到零件。
单个工位的建模思路和顺序和用UG 设计是一样的,单个激活保存是因为如果不单个激活保存会默认保存到你第一次保存的文件夹里,或者用“文件->保存管理”进行单个零件保存。
2 单个零件设计
如图3.12所示,拉伸实体。
使用“基于草图的特征”里的“凸台”进行拉伸,自动默认是“凸台定义”里的“轮廓/曲面—选择”,直接选取所作的草图,在“长度”对话框里输入要拉伸的厚度,点击“更多”使用“第二限制”里的“长度”,可以得到反向拉伸的厚度。
用“修饰特征”对拉伸体修饰。
图3.11 链接装配草图到零件
1 选择装配草图,并复制
2 内部粘贴草图到零件
3修剪型面
如图3.13所示,点击“基于曲面的特征”里的“分割”,选取用于切割型面的面,箭头方向为切割后实体保留部分。
当型面要偏置时使用“厚曲面”进行偏置。
当选取的面不能剖切时可将操作模式切换到“线框和曲面设计”或者“形状”里的“创成式外型设计”,将面编辑后使用。
图3.12 创建零件过程
4 选择轮廓线
1 凸台特征对话框
2 选择轮廓定义
3 选择子元素
5 添加修饰特征
6 设计结果
3.6.3装配标准件和外购件
如图3.14和3.15所示,将单元激活进入“装配件设计”状态,用 “现在组件”或“具有定位的现在组件”插入外购件和标准件,并使用中的各个按钮来精确定位标准件和外购件的位置。
图3.13 修剪定位块和压块零件型面
1 提取操作对话框
2 提取曲面
3 分割特征对话框
4 修剪结果
3.6.4定位销单元设计
图3.15 夹具单元UNIT 设计结果
视图→命令集→平移或旋转
图3.14 装配模块工具条和命令
定位销单元设计可分为三种情况: l 固定定位销 l 移动定位销 l 旋转定位销
除了固定定位销,移动定位销和旋转定位销都可在夹具单元基础上进行设计。
设计方法步骤:
1首先确定定位销的空间位置
如图3.16,提取曲面到截面零件,并创建定位孔轴线,用来装配定位销,然后设计连接支架和销支架。
2根据装配好的定位销设计销支架
如果是固定定位销,根据销支架设计或装配安装支架。
图3.16 定位销单元设计过程
1 提取曲面到断面位置零件
2 创建定位孔轴线
3 装配定位销
4 连接支架和销支架设计。