01 CRH高速动车组轮对探伤体系
动车组构成动车组编号各部位名称功能
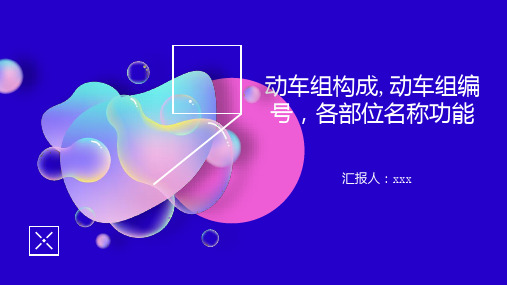
车门和车窗是动车组的进出 通道,它们必须能够快速、 安全地开启和关闭。此外, 车窗还必须能够提供良好的 视野,并能够阻挡风雨和噪
音
座椅和内部装饰
座椅和内部装饰为乘客提供 了一个舒适的环境。座椅通 常采用符合人体工程学的设 计,以提供最大的舒适度。 内部装饰则包括地毯、墙壁、 天花板和灯光等元素,以营 造一个温馨、舒适的环境
动车组构成,动车组编 号,各部位名称功能
汇报人:xxx
-
1
动车组构成
2
动车组编号
3
动车组各部位名称及功能
PART 1
动车组构成
动车组构成
01 动车组主要由动车和拖车组成
02 通常,动车组的前部为动车,后 部为拖车
03 在更复杂的动车组中,可能还包含 有控制车和供电车等特殊车辆
PART 2
动车组编号
获取新闻等
··· ···
-
谢谢您的 ·观看·
BUSINESS TRIP PROJECT PLAN
汇报人:XXX
汇报时间:XXXXX
··· ···
动车组编号
动车组的编号通常由一系列字母和数字组成, 可以提供关于动车组的类型、制造商、运行线
路等重要信息
例如,中国的动车组编号通常以CRH开头,然 后是一个字母序列,表示不同的车型和制造商,
最后是5个数字,表示具体的车号
பைடு நூலகம்ART 3
动车组各部位名称及功能
动车组各部位名称及功能
车体:车体是动车 组的基础结构,负 责承载乘客、司机 以及所有的设备和 系统。车体通常采 用铝合金或高强度 钢制造,以减轻重 量并提高耐久性
转向架:转向架是 动车组的行走机构 ,负责支撑车体并 引导车辆沿轨道行 驶。它由一系列的 轴承、轮对、弹簧 和减震器组成,以 确保列车在高速行 驶时的稳定性和舒 适性
空心轴探伤

动车组空心车轴超声波探伤规程1 适用范围本规程适用于与谐系列(以下简称CRH系列)动车组空心车轴检修时以中心孔内壁为探测面的超声波探伤检查。
2 术语2、1 探伤螺距空心车轴超声波探伤时探头在螺旋扫查过程中同一角度相邻两次扫查轨迹之间的轴向距离。
2、2 探伤系统信噪比基准缺陷超声信号幅度与超声波探伤设备显示的最大背景噪声幅度之比。
2、3 对比试样轴带有已知缺陷用于校验空心车轴探伤设备灵敏度与验证扫查区域系统可靠性的测试用空心车轴。
2、4 落轮探伤落轮探伤就是指轮对(轮轴)从转向架卸下后,对空心车轴进行的超声波探伤检查。
2、5 在线探伤在线探伤就是指对处于装车状态的空心车轴进行的超声波探伤检查。
3 探测规定3、1 在线探伤周期在线探伤周期见表1:- 3 -3、2 空心车轴超声波探伤对C RH2A/B/E、CRH2C 一阶段动车组空心车轴超声波检测时,须采用横波斜探头对横向表面缺陷进行探测;其她车型须采用横波斜探头对横向表面缺陷进行探测, 采用双晶片聚焦纵波探头或直探头对车轴内部缺陷进行探测。
3、3 动车组颠覆或脱轨时,须对全列轮对的空心车轴按3、2 条规定进行超声波探伤检查。
4 质量保证4、1 动车组空心车轴超声波探伤的质量保证期: 在正常运用的情况下,动车组空心车轴超声波探伤检查的质量保证期为表1中规定的运行里程上限(本次探伤作业完成后,上一次质量保证期终止计算)。
4、2 在超声波探伤质量保证期内,发生因漏探导致的事故时,由动车组空心车轴探伤单位负责。
4、3 超出超声波探伤质量保证期,发生因表面缺陷或内部缺陷导致的事故时,由动车组配属管理单位负责。
4、4 因内部缺陷导致的事故,同时由动车组制造单位负责。
5 人员要求5、1 探伤人员5、1、1 从事动车组空心车轴超声波探伤的人员须具有中专或以上学历;视力(包括矫正视力)达到5、0 及以上,非色盲。
5、1、2 动车组空心车轴超声波探伤人员须取得铁道部门无损检测人员鉴定考核委员会颁发的Ⅱ级或Ⅱ级以上级别的超声波探伤技术资格证书,并经过空心车轴超声波探伤岗位操作培训, 考试合格后方能上岗作业。
动车组检修体系

动车组检修体系 Hessen was revised in January 2021中国高速列车(CRH)维修体系1.修制设计基本框架本次引进的三种动车组,其检修体制设计原则基本一致,即:实行定期的计划性预防修;修制框架基本相同,分为预防性检修和事后检修或更正性检修,具体框架如下图示。
2.修程设计基本流程修程设计是不断积累、不断总结、不断提高的过程,通过选择高持久性的系统和部件,统筹考虑制造与使用的各个环节,设计建立经济合理的检修制度,保证动车组运用的安全性和可靠性,同时,最大限度地提高动车组的使用效率。
国外将修程设计视为一项十分重要的前提性的基础工作,形成了一套比较完整的设计流程,一般框架如下图示。
3.修程安排基本情况⑴四方股份生产的动车组①检修周期检修周期设计分两个系列,一类是以走行公里单位,另一类是以时间为单位。
两个系列中以先到检修周期的优先安排检修,一般在运行图中使用率高的按走行以主要系统和部件的检修范围划分,在对应的检修周期下,其检修状态表现系统、空调装置和车钩装置要进行全分解或部分分解检修。
③检修时间和检修材料费用其检修周期的设计是以走行公里为主,以时间为辅。
除每日运行结束后的例行检查外,检修周期的分为四个等级,基本级是“基本性”检修,检修周期为6万公里,第二级是一级大型维修,检修周期是120万公里,第三级是二级大修维修,检修周期是240万公里,第四级是三级大型维修,检修周期是480万公里。
基本性检一级大型二级大型修三级大型维修240万公里480万公里②检修范围以主要系统和部件的检修范围划分,在对应的检修周期下,其检修状态表现制动系统、空调装置和车钩装置要进行全分解或部分分解检修。
⑶BSP公司生产的动车组①检修周期其检修周期的设计是以时间为主,以走行公里为辅,且时间间隔划分比较细致,经过综合分析调整,检修周期大致可以分为五个等级。
②检修范围以主要系统和部件的检修范围划分,在对应的检修周期下,其检修状态表现统、空调装置和车钩装置要进行全分解或部分分解检修。
CRH2A统型动车组三级修轮对轮辋轮辐探伤作业指导书
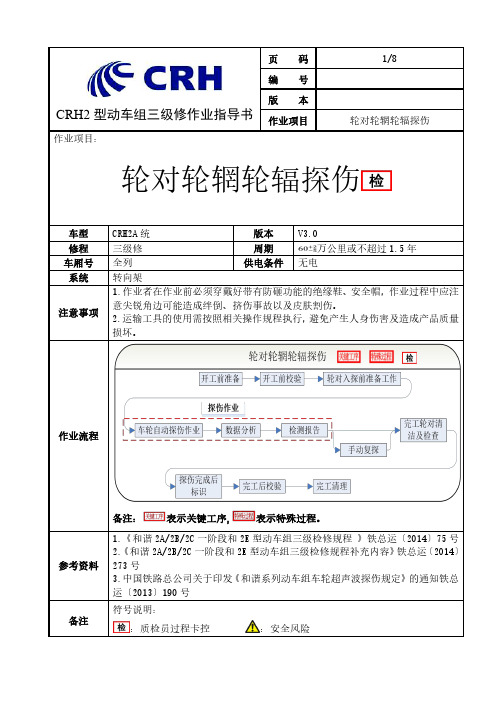
备注
按需 180#及以上
1
页码
4/8
编号
版本
CRH2 型动车组三级修作业指导书 作业项目
轮对轮辋轮辐探伤
序号 1 2
作业项目 校验要求 开工前准备
作业内容、标准及图示 1) 日常性能校验:每班开工前和完工后由探伤工、探伤工长、质检
员共同校验系统的性能,检查系统的技术状况、确定探伤灵敏度。 按当班探伤作业计划选择相应的对比试样轴进行校验,并储存校 验时的系统参数,作为探伤时相应的检测参数,并详细填写相关 表格,按要求签章。 2) 季度性能检查:每季度由主管检修(生产)的副段长或总工程师组 织,轮轴专职、设备专职、验收员、质检员、探伤工长、探伤工 和设备维修工共同参加,对设备进行一次全面性能检查,全面检 查系统的状态。详细填写轮辋轮辐超声波探伤设备季度性能检查 记录并共同签章。 1) 检查探伤现场,须干净整洁。 2) 检查设备外观状态良好,设备没有损坏。 1) 按要求对设备进行点检作业。 2) 每班开工前样板轮对校验:按当班探伤作业计划选择相应的样板 轮对进行设备日常校验,并将样板轮对推至探伤机前。(本项作 业至少2人配合完成) 3) 检查轮对踏面情况,要求踏面表面不能存在油污,完成后将轮对 推入“待检”位,并将定位磁块放置在样板轮轮辋外侧面上,靠 探伤设备有感应器一侧。
3) 探伤复检。对探伤数据进行分析,需要进行探伤复检时,点击数
据分析区的【探伤复检】则进入检测控制区域,如下图所示:
复检检测
点击【开始检测】按钮,进行复核数据采集。检测数据处理加载 完成后,在自动打开的“复核分析”界面进行复核判伤检查。(复核 判伤完之后可通过点击数据分析区的【复核数据】,加载探伤复检生 成的文件,进行复核判伤检查)。
超声波全面探伤。检测结束后进行标定、校验结果处理。
浅议动车组空心车轴探伤
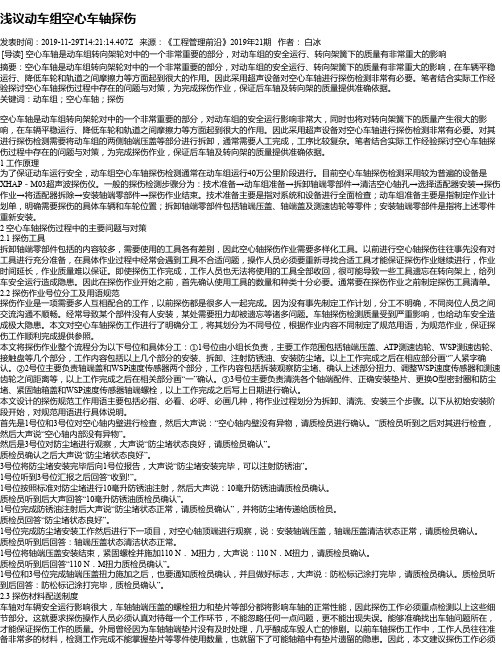
浅议动车组空心车轴探伤发表时间:2019-11-29T14:21:14.407Z 来源:《工程管理前沿》2019年21期作者:白冰[导读] 空心车轴是动车组转向架轮对中的一个非常重要的部分,对动车组的安全运行、转向架簧下的质量有非常重大的影响摘要:空心车轴是动车组转向架轮对中的一个非常重要的部分,对动车组的安全运行、转向架簧下的质量有非常重大的影响,在车辆平稳运行、降低车轮和轨道之间摩擦力等方面起到很大的作用。
因此采用超声设备对空心车轴进行探伤检测非常有必要。
笔者结合实际工作经验探讨空心车轴探伤过程中存在的问题与对策,为完成探伤作业,保证后车轴及转向架的质量提供准确依据。
关键词:动车组;空心车轴;探伤空心车轴是动车组转向架轮对中的一个非常重要的部分,对动车组的安全运行影响非常大,同时也将对转向架簧下的质量产生很大的影响,在车辆平稳运行、降低车轮和轨道之间摩擦力等方面起到很大的作用。
因此采用超声设备对空心车轴进行探伤检测非常有必要。
对其进行探伤检测需要将动车组的两侧轴端压盖等部分进行拆卸,通常需要人工完成,工序比较复杂。
笔者结合实际工作经验探讨空心车轴探伤过程中存在的问题与对策,为完成探伤作业,保证后车轴及转向架的质量提供准确依据。
1 工作原理为了保证动车运行安全,动车组空心车轴探伤检测通常在动车组运行40万公里阶段进行。
目前空心车轴探伤检测采用较为普遍的设备是XHAP-M03超声波探伤仪。
一般的探伤检测步骤分为:技术准备→动车组准备→拆卸轴端零部件→清洁空心轴孔→选择适配器安装→探伤作业→将适配器拆除→安装轴端零部件→探伤作业结束。
技术准备主要是指对系统和设备进行全面检查;动车组准备主要是指制定作业计划单,明确需要探伤的具体车辆和车轮位置;拆卸轴端零部件包括轴端压盖、轴端盖及测速齿轮等零件;安装轴端零部件是指将上述零件重新安装。
2 空心车轴探伤过程中的主要问题与对策2.1 探伤工具拆卸轴端零部件包括的内容较多,需要使用的工具各有差别,因此空心轴探伤作业需要多样化工具。
动车车轮对检测系统分级标准

2.
CRH2 型车轮对检测系统分级标准表见表 2
表 2:轮对检测系统 CRH2 型车分级标准表(单位为 mm) CRH 2 型车(LMA) 1级 >27 <6 2级 26-27 6-6.5 3级 <26 >6.5 <1352 或>1355 <1 1-2 >2 >4 <0.3 0.3-0.5 >0.5 一处>20,两处每处>10
>2 >3 >0.25 >30 >25 >0.5
不圆度
4.
CRH5 型车轮对检测系统分级标准表见表 4
表 4:轮对检测系统 CRH5 型车分级标准表(单位为 mm) 车型 分级标准 轮缘厚度 踏面磨耗 轮对内距 同一轮对直径差 同一转向架直径差 擦伤深度 不圆度 <0.3 <0.2 0.3-0.5 0.2-0.5 <1.2 1.2-2.2 1级 >23 <6 CRH 5 型车(XP55) 2级 22-23 6-6.5 3级 <22 >6.5 <1353 或>1354.2 >2.2 同车动轴>5,其他>20 >0.5 >0.5
踏面磨耗 动车轮对 内距 直径>840 直径≤840
<6
或>1356 <1351 或>1356 <1350 或>1356
拖车轮对内距 同一轮对直径差 同一转向架直径差 擦伤深度 擦伤长度 直径>840 直径≤840 <0.2 0.2-0.5 <0.1 0.1-0.25 <1 1-2
车 型 分级标准 轮缘厚度 踏面磨耗 轮对内距 同一轮对直径差 同一转向架直径差 擦伤深度 擦伤长度
《和谐系列动车组空心车轴超声波探伤规程》(2013)100
TG/CL248-2013和谐系列动车组空心车轴超声波探伤规程为统一动车组空心车轴超声波探伤方法,规范探伤作业,确保探伤质量,特制定本规程。
1 适用范围本规程适用于和谐系列(以下简称CRH系列)动车组空心车轴检修时以中心孔内壁为探测面的超声波探伤检查。
2 术语2.1探伤螺距空心车轴超声波探伤时探头在螺旋扫查过程中同一角度相邻两次扫查轨迹之间的轴向距离。
2.2探伤系统信噪比基准缺陷超声信号幅度与超声波探伤设备显示的最大背景噪声幅度之比。
2.3对比试样轴带有已知缺陷用于校验空心车轴探伤设备灵敏度和验证扫查区域系统可靠性的测试用空心车轴。
2.4落轮探伤落轮探伤是指轮对(轮轴)从转向架卸下后,对空心车轴进行的超声波探伤检查。
2.5在线探伤在线探伤是指对处于装车状态的空心车轴进行的超声波探伤检查。
3 探测规定3.1 在线探伤周期在线探伤周期见表1:3.2 空心车轴超声波探伤对CRH2A/B/E、CRH2C一阶段动车组空心车轴超声波检测时,须采用横波斜探头对横向表面缺陷进行探测;其他车型须采用横波斜探头对横向表面缺陷进行探测,采用双晶片聚焦纵波探头或直探头对车轴内部缺陷进行探测。
3.3 动车组颠覆或脱轨时,须对全列轮对的空心车轴按3.2条规定进行超声波探伤检查。
4 质量保证4.1 动车组空心车轴超声波探伤的质量保证期:在正常运用的情况下,动车组空心车轴超声波探伤检查的质量保证期为表1中规定的运行里程上限(本次探伤作业完成后,上一次质量保证期终止计算)。
4.2 在超声波探伤质量保证期内,发生因漏探导致的事故时,由动车组空心车轴探伤单位负责。
4.3 超出超声波探伤质量保证期,发生因表面缺陷或内部缺陷导致的事故时,由动车组配属管理单位负责。
4.4 因内部缺陷导致的事故,同时由动车组制造单位负责。
5 人员要求5.1 探伤人员5.1.1从事动车组空心车轴超声波探伤的人员须具有中专或以上学历;视力(包括矫正视力)达到5.0及以上,非色盲。
CRH1介绍
CRH1B
BSP在2007年10月31日再获得铁道部40列16节编组动车 组新订单,合同编号796。其中20列是在CRH1A基础上扩编 至16节车厢的大编组座车高速列车,称为CRH1B,编号为 CRH1-041B~CRH1-060B。全列16节编组中包括10节动车配 6节拖车(10M6T),其中包括3节一等座车,12节二等座车, 1节餐车。最高运营速度为200—250km/h,而车体外观不变。 2009年3月5日,第一列CRH1B型动车组完成了BSP公司内部 的环形线测试,3月8日开始在北京环行铁道试验。CRH1B动 车组在2009年4月起配属上海铁路局,运行上海—南京、上海 南—杭州的城际列车。整批20列CRH1B动车组在2010年4月 交付完毕。2011年发生的动车组列车追尾事故中,D3115车 次的列车就是这种型号。
CRH1动车组组成
CRH1技术参数
编组型式:8辆编组,可两编组连挂运行 动力配置:3个牵引单元,5动3拖,2(2M+1T) + (1M+1T) 车种:一等车、二等车、酒吧坐车合造车 定员(人):670 客室布置:一等车2+2、二等车2+3 最高运营速度(km/h):200 最高试验速度(km/h):250 适应轨距(mm):1435 适应站台高度(mm):500~1200 传动方式:交直交 牵引功率(kW):5500 编组重量及长度:213.5m,420.4t 车体型式:不锈钢 气密性:没有
CRH1A型动车组的原型车是庞巴迪运输为瑞典国家铁路提 供的Regina C2008型。2004年6月,铁道部展开为用于中国 铁路第六次大提速、时速200公里级别的第一轮高速动车组技 术引进招标,中外合资企业青岛四方-庞巴迪-鲍尔铁路运输设 备有限公司(BSP)为中标厂商之一,获得了20列的订单。 2004年10月12日,铁道部与BSP正式签订合同,合同编号790, 铁道部代表签约方为广州铁路(集团)公司。2005年5月30日, 广深铁路股份有限公司决定以25.83亿元人民币的价格向BSP 另外订购20列时速200公里级别动车组,以满足广深铁路第四 线于2008年开通之后的运营需求;同年8月25日,广深铁路公 司董事会通过有关议案。而BSP的40列时速200公里级别动车 组 其 后 最 终 被 定 型 为 CRH1A , 动 车 编 号 为 CRH1001A~CRH1-040A。
高速动车组轮对检修技术分析
高速动车组轮对检修技术分析2身份证号码3身份证号码摘要:轮对作为高速动车组的走行单元,与轨道直接接触。
轮对检修的优劣,将直接影响到动车组的运行安全。
动车组的轮对每运行120万公里就必须拆装检修一次,在进行轮轴压配合时,常常会出现一些不正常的情况,如轮轴压配合表面有划痕、车轮内孔尺寸过大、轮轴和轮座生锈等,这些情况都会对轮对维修的质量和成本产生影响。
本文对上述出现这种异常情况的原因进行了分析,并给出了相应的处理方法。
关键词:高速动车组;轮对检修;技术1.我国高速动车组检修制度我国高速动车组具有高速、运行环境复杂、承载能力大等特点。
在现代维护理论的指导下,按照“规划、预防性、预防性”的原则,划分1—5个等级,构建了我国高速动车组运行维护体系的基本框架。
其中一级和二级属于使用检修,主要是维修和保养;三、四、五级属于高级维修,主要是为了恢复最基本的功能。
同时,还制定了相应的维修规范。
在中国,高速动车组的检修采取的是一种高效的检修模式,它的目标是为了提高动车组的安全性和可靠性,提高动车组的运用效率,减少休车时间,提高检修单位的工作效率,实现修车模式的生产化,并呈现出高度的专业化、集约化、社会化和程序化。
我国高速动车组的维修,应该将目标定位在提高客货运输能力的基础上,提升车辆零部件的运用稳定性,将安全运营作为最重要的目标,努力做到“零故障、零缺陷”,同时还要对国外先进的生产和维修理论、技术和方法进行充分的借鉴,从而保证我国高速动车组车辆的安全高效运营。
2.车轮、车轴压装配合表面划(拉)伤高速列车轴间干涉过大(超过0.20mm),需采用注油的冷冲方式实现退卸。
在注油退卸的过程中,如果发现车轴轮座和车轮孔表面出现了划(拉)伤,那么就一定要根据有关的维修标准,对划(拉)伤的程度进行检查。
一旦找到划(拉)伤,如果深度超出了维修限度,那么它就必须被按照报废处置。
2.1原因简析车轴轮座和车轮孔划(拉伤)产生的原因有二:一是在压装时产生的划伤。
CRH2C-M2-05-02-001P空心车轴探伤
上海铁路局上海动车客车段发布
前言
本标准由上海动车客车段技术装备科制订
本标准由上海动车客车段总工批准
本标准于20010年6月制定
本标准由上海动车客车段技术装备科张宏起草
岗位作业劳动安全注意事项
1、作业人员在维修作业期间应遵守适用的作业指导书及各种安全规定;必须始终穿着带有橡胶鞋底的绝缘鞋,并穿戴所从事工作要求的防护服和其它与人身安全相关的设施等。
2、在进行动车组检修作业前,必须按规定插设安全防护号志;作业完了必须确认本组作业人员全部离开作业车辆后方准撤除防护。
插撤防护号志要正确传递信号,不得隔位或用对讲机进行传递。
严禁无防护号志检修作业。
3、检修库、临修库配备接触网“有电”、“无电”等安全警示用语,工作人员必须遵照安全警示用语的提示,按作业流程的规定进行作业。
4、应注意尖锐角边可能造成绊倒、挤伤事故以及皮肤割伤。
5、各种电动机械、设备、工具,未安装触电保护器不准使用。
6、电器设备、电线路的安装或变更,必须由专业人员操作,严禁私拉乱接。
7、用于探伤设备的油,以及润滑剂等化学物品,都可能具有腐蚀性
或引起皮肤或肺部刺激,保护好各部皮肤和眼睛。
CRH2C型动车组二级修
(此三维视图为普通轴端)
(a)普通轴端
(c)AG43轴端
图1 动车轮对、AG43轮对及AG37轮对的探伤
附录A 轴箱前盖组装前涂装铬酸锌位置要求。
- 1、下载文档前请自行甄别文档内容的完整性,平台不提供额外的编辑、内容补充、找答案等附加服务。
- 2、"仅部分预览"的文档,不可在线预览部分如存在完整性等问题,可反馈申请退款(可完整预览的文档不适用该条件!)。
- 3、如文档侵犯您的权益,请联系客服反馈,我们会尽快为您处理(人工客服工作时间:9:00-18:30)。
站段局域网
网络终端 网络终端 网络终端
设备间 (数据采集处理)
控制室 (数据分析管理)
CRH动车组轮对探伤技术体系
LY轮对故障动态检测系统-几何尺寸检测
轮对触发
光学 镜头
线光源
图像传感器
CRH动车组轮对探伤技术体系
LY轮对故障动态检测系统-几何尺寸检测
轮缘厚度
踏面磨耗 轮缘厚度 QR值 车轮直径
系统集成度低。
CRH动车组轮对探伤技术体系
LU-移动式轮辋轮辐探伤系统
(2)第二代LU设备
第二代LU设备的原型机来
自于德国设备的UFPE-II,
该设备采用相控阵超声波技 术进行检测。踏面载体采用
机电进探摸式,进探路径固
定,不能柔性适应不同动车 基于PA技术的双踏面载体的LU, 与德国UFPE-II一致 组车底空间。
标准外形曲线
±0.2 ±0.2 ±0.4 ±0.6
mm mm mm mm
偏移量2 踏面磨耗 偏移量1
实际测量外形曲线
轮辋内侧基线
QR值
CRH动车组轮对探伤技术体系
LY轮对故障动态检测系统-几何尺寸检测
工作原理
现场检测
CRH动车组轮对探伤技术体系
LY轮对故障动态检测系统-踏面擦伤检测
接触式 轮缘顶点测量 擦伤测量精度 ±0.2 mmຫໍສະໝຸດ CRH动车组轮对探伤技术体系
LA-固定式轮辋轮辐探伤系统
固定安装在动车检修基 地轮对检修线上,综合 利用UT+PA超声探伤技 术自动检测落轮镟修后
轮对的轮辋轮辐缺陷,
适用于CRH各型动车组 轮对。
CRH动车组轮对探伤技术体系
LU、LA 轮辋轮辐探伤原理
CRH动车组轮对探伤技术体系 轮对探伤设备的运用情况 管理制度
动车组入库线 动态自动检测
2
24万km
轮辋轮辐 全范围探伤
移动式轮辋轮辐 轮对检查线 探伤系统(UFPE) 不需拆卸轮对
3
120万km
轮辋轮辐 全范围探伤
固定式轮辋轮辐 探伤系统(AURA)
轮对检修线 拆卸轮对
CRH动车组轮对探伤技术体系
中国CRH高速动车轮对检查制度
DB无损检测技术部负责人 Hartmut Hintze
自动完成轮辋轮辐缺陷
探伤,适用于CRH各型 动车组轮对。
CRH动车组轮对探伤技术体系
LU-移动式轮辋轮辐探伤系统
(1)第一代LU设备
第一代LU设备的原型机来 自于德国设备的UFPE-I,该 设备采用人工在地沟内手动 定位探头载体;采用常规超 声波技术进行检测。该版本 设备笨重、自动化程度低、 原型机地沟调试 实车测试
定(分别针对动轮与拖轮),所花时间较长,同时由于旋转 等动作会 造成降低标定准确性,影响实车检测缺陷判定;
开放式模组电机,多点控制,故障点多,后期维护难度大。
CRH动车组轮对探伤技术体系
LU-移动式轮辋轮辐探伤系统
(3)第三代LU设备(全路全面应用)
第三代LU设备采用相控阵超声波 技术和机器人定位技术进行检测
CRH动车组轮对探伤技术体系
典型事故案例2:
2008年7月9日,德国ICE3-518号 轮轴断裂脱轨
CRH动车组轮对探伤技术体系
典型事故案例3: 2007年1月14日,兰州铁路局SS7E机车,崩轮事故
辐板沿根部断裂为三个扇形块
崩裂断口金相分析 左一轮违规补焊-辐板最大应力区
CRH动车组轮对探伤技术体系
探伤、高级修分解检测、故障复核确认的动车组轮对检查制度。
LY
LU
LA
CRH动车组轮对探伤技术体系
中国高速动车轮对缺陷检测技术体系
序号 1 检修 层次 日常 动态 检测 定期 在线 检测 定期 落轮 检测 检修 周期 每次入库 18-25万 公里 设备 LY LU LX LHZ-M LA 高级修 LX 检测内容 使用地点
CRH动车组轮对探伤技术体系
LY轮对故障动态检测系统-阵列超声波动态探伤
车轮踏面依次与超声波探头阵列接触,实现车轮一周的超声波探伤
钢轨上组合布置超声直探头和斜探头,检测周向、径向缺陷
CRH动车组轮对探伤技术体系
LY轮对故障动态检测系统
CRH动车组轮对探伤技术体系
LY轮对故障动态检测系统
CRH动车组轮对探伤技术体系
LY轮对故障动态检测系统
CRH动车组轮对探伤技术体系
目
录
1、CRH轮对探伤体系
2、CRH轮对探伤设备-LY 3、CRH轮对探伤设备-LU、LA
CRH动车组轮对探伤技术体系
LU-移动式轮辋轮辐探伤系统
安装在动车运用所、动
车检修基地检查线上, 利用UT和PA超声探伤 技术,通过沿地沟导轨 移动的检测小车,在线
车运用所检查库线上的LU设备,对轮辋轮辐各部位进行周向、
径向、斜向在线深度探伤。
CRH动车组轮对探伤技术体系
高级修分解检测:结合动车组高级修,将轮对从转向架上分解
下来,利用安装在动车段轮对检修线上的LA设备,对轮对轮辋
轮辐各部位进行周向、径向、斜向全方位深度探伤。 故障复核确认:检修探伤过程中如发现轮对缺陷,利用LX设备
2010年11月,铁道部组织召开动车组车轮车轴运用情况交流 会,依据国外动车组轮对探伤管理的经验,结合我国动车组
运用检修管理模式,形成CRH动车组轮对检查制度。
CRH动车组轮对探伤技术体系
CRH轮对探伤技术体系和设备
根据国外动车组轮对探伤管理的相关规定,结合我国动车组
运用检修管理模式,铁道部制定了一级修日常检查、二级修专项
目
录
1、CRH轮对探伤体系
2、CRH轮对探伤设备-LY
3、CRH轮对探伤设备-LU、LA
CRH动车组轮对探伤技术体系
LY轮对故障动态检测系统-功能组成
功能:几何尺寸、踏面擦伤、轮辋深层次探伤
CRH动车组轮对探伤技术体系
LY轮对故障动态检测系统-功能组成
路局网络 网络终端 车号 外形 擦伤 探伤
检测结果 超限数据 综合分析报告
CRH动车组轮对探伤技术体系
动车组轮对检查制度:一级修日常检查、二级修专项探伤、 高级修分解检测、故障复核确认 一级修日常检查:动车组每运行4000公里或2天后进动车所一 级修时,利用安装在进所线路上的LY设备对轮对进行动态检
测,轮对几何尺寸、轮对踏面故障、探测轮辋深层次重大缺
陷。 二级修专项探伤:动车组每运行18-25万公里,利用安装在动
对轮辋缺陷进行复核、定位,并跟踪缺陷发展情况。
通过以上措施对动车组的车轮实行严格检查,在规定的检查 周期内控制动车组轮对缺陷风险。
典型事故案例1:
1998年6月16日 德国ICE1-884号 轮对故障导致列车颠覆
CRH动车组轮对探伤技术体系
典型事故案例2: 2008年7月9日,德国ICE3-518号,轮轴断裂导致列车脱轨
刚驶离科隆中心车站前往杜塞尔多夫,< 30km/h,第一节车的一根车轴 断裂脱轨。列车刚驶离车站,250名乘客均通过站台疏散,无伤亡。
不能检测辐板孔以下缺陷。
CRH动车组轮对探伤技术体系
LU-移动式轮辋轮辐探伤系统
(1)第一代LU设备:原型机主要缺点如下,
采用人工在地沟内手动定位探头载体,设备笨重,自动化程 度低,同时无法适应中国各型动车组车底空间;
超声技术落后:常规超声技术,探头载体庞大,不能检测辐
板孔以下缺陷,同时不能适应负载的车底空间; 不能兼容CRH各型动车组轮辋轮辐探伤;
CRH动车组轮对探伤技术体系
目
录
1、CRH轮对探伤体系 2、CRH轮对探伤设备-LY
3、CRH轮对探伤设备-LU、LA
CRH动车组轮对探伤技术体系
1 国外典型轮对事故
典型事故案例1: 1998年6月16日 德国ICE1-884号 轮对故障导致列车颠覆
德国近50年来最大的灾难事故,造成101人死亡
CRH动车组轮对探伤技术体系
。采用智能机器人结构,定位重
复精度高,能够适应各型动车组 车底空间,超声布局更合理,同
一套探头载体兼容各型动车组轮
LU设备在国内动车所运用情况 辋轮辐探伤。
CRH动车组轮对探伤技术体系
LU-移动式轮辋轮辐探伤系统
(3)第三代LU设备
针对前两代LU设备的缺点,进行改进后,第三代LU设备优点如下所示: 智能机器人可进行柔性定位,能够适应各型动车组车底空间; 智能机器人系统具备防撞保护功能,避免载体与车底碰撞; 超声布局更合理:完全按照我国CRH动车组车轮缺陷发生部位及 类型进行针对性升级改进; 同一套探头载体兼容各型动车组轮辋轮辐探伤;设备性能稳定; 对现场近20万条轮对探伤,探伤波幅稳定性好,检修维护方便; 有效探测出1100多例缺陷,切实保障车轮安全。
CRH动车组轮对探伤技术体系
LU-移动式轮辋轮辐探伤系统
(2)第二代LU设备,主要缺点如下:
踏面载体采用机电进探模式,不能柔性适应不同动车组车底空间; 探头定位均采用接近传感器方式,不能适应不同轮型幅板结构; 设备采用双侧载体,按照“铁总运【2013】190 中国铁路总公司关于印
发《和谐号动车组车轮超声波探伤规定》的通知”规定,进行 二次标
英国
意大利 西班牙
—
★ — ★ ★ —
—
— —
7
8 9
比利时
俄罗斯 韩国
—
★ ★
—
— —
CRH动车组轮对探伤技术体系 德铁ICE列车轮对检测技术体系
序 号 检测 层次 检测 周期 检测内容 配置设备 特 点
1
日常 每天低速 动态 入库时 检测 定期 在线 检测 定期 落轮 检测
尺寸擦伤 径向裂纹
轮对动态探伤系统 (AUROPA)