先进复合材料主要制造工艺和专用设备
复合材料模具来了,你还在用金属模具吗?

复合材料模具来了,你还在用金属模具吗?先进复合材料以其比强度和比模量高、热膨胀系数小、可设计性好、易于整体成型等一系列突出的优点在航空航天结构上得到了广泛应用, 现已成为航空航天四大结构材料之一。
复合材料在航空航天部门的广泛应用极大地促进了航空航天技术的发展,反过来,也促进了复合材料成型模具技术的进步。
模具是制造复合材料构件的基础,直接影响其最终状态和质量。
复合材料构件的外形、尺寸及与其他构件的配合精度等要靠模具保证,这些都决定了模具在复合材料构件制造过程中起着举足轻重的作用。
1复合材料模具传统复合材料成型模具由金属材料制作,主要原因是金属具有高强度、高刚度、尺寸稳定性好、加工性好,适用于大批量生产等优点。
随着复合材料构件外形准确性和尺寸精度的不断提高,原有金属模具材料的性能已经不能很好地满足高精度成型模具的需要。
在这种背景下,复合材料模具(本文指碳纤维复合材料模具)应运而生,并且得到了迅速发展。
目前,在欧美发达国家的航空航天部门,复合材料模具的应用已经相当普遍。
在国内,除了中航工业哈飞采用复合材料模具比较早、使用比较多之外,其他企业以及航天部门用得还比较少。
但是,随着高性能复合材料航空航天结构件的大量应用,各有关研究院所和企业积极研究和试验使用复合材料模具,因此复合材料模具也很快会成为国内复合材料构件的主要成型模具。
2复合材料模具的主要优点热膨胀性能匹配复合材料模具最大优点是热膨胀系数小,且与复合材料的热膨胀系数比较相匹配,从而可以获得外形准确性和尺寸精度符合设计要求的构件。
为了更深入地认识模具材料的热膨胀性能对复合材料构件质量的影响,首先分析在复合材料构件固化成型过程中,模具与构件之间相互关系发生变化的过程:开始加热时,随着温度的升高,模具受热膨胀,其尺寸跟着增大,这时的构件坯料还是软的,所以它也跟着模具一起增大;继续升温,在树脂体系的凝胶温度下,受热膨胀的模具与构件坯料具有相同的尺寸,这时的树脂体系只有部分固化,性能还比较低;当加热到最后的固化温度时,模具和半固化的构件坯料以各自的热膨胀率膨胀,如果它们的热膨胀率不同,构件中将产生内应力;在保温阶段,构件在已经膨胀到最大尺寸的模具中得到进一步固化;保温结束后,从固化温度开始冷却至室温的过程中,模具和构件都以各自的收缩率收缩。
复合材料技术

航空预浸料- 热压罐工艺复合材料技术应用概况发布时间:2011-11-23 15:34:27先进复合材料自问世以来,由于其轻质、高强、耐疲劳、耐腐蚀等诸多优势,一直在航空材料领域得到重视。
随着近几十年来的发展,尤其是最近10年在大型飞机上井喷式的应用,先进复材料已经证明了其在未来航空领域的重要地位,它在飞机上的用量和应用部位也已经成为衡量飞结构先进性的重要标志之一[1] 如目前代表世界最先进战机的美国F-22 和F-35,其复合材料占机结构重量达到了26%(F-22 机身、机翼、襟翼、垂尾、副翼、口盖、起落架舱门;F-35 机身翼进气道、操纵面、副翼、垂尾),欧洲EF-2000 战机更是达到了35%~40%(机翼、垂尾、方向舵[2] ;民机领域的两大巨头波音和空客,在其最新型的大型客机波音787、A350XWB 机型中,大幅使用复合材料,分别达到50% 和52%[3],在机身主承力结构中,除一些特殊需要外,基本上实现了全复合材料化。
从当前的复合材料应用来看,航空复合材料具备以下几个方面的特点:在材料方面,飞主承力结构应用高韧性复合材料;在工艺方面,呈现出以预浸料- 热压罐工艺为主,积极开发液体成型工艺及其他低成本成型工艺的态势,对复合材料构件的制造综合考虑性能/ 成本因机[4]设计理念的广泛认知,复合材料已逐渐在主承力结构上站稳了脚跟,而且,为了进一步将复合材料的优点充分发挥,飞机结构设计越来越趋向于整体化和大型化。
复合材料在主承力结构上的应用技术是体现航空复合材料水平及应用程度的重要标志。
目前复合材料主承力构件仍是以预浸料- 热压罐工艺为主。
基于此,本文旨在介绍目前与航空预浸料- 热压罐工艺相关的复合材料技术。
主承力结构用预浸料1 高性能复合材料体系“计是主导,材料是基础,工艺是关键”[5]复合材料的制造技术与材料的发展息息相关。
航空预浸料-热压罐工艺高性能复合材料到目前已经历了3个阶段。
第一阶段的复合材料采用通用T300 级碳纤维和未增韧热固性树脂,具有明显的脆性材料特征,主要用于飞机承力较小的结构件。
大型复合材料壁板先进制造技术及应用

大型复合材料壁板先进制造技术及应用李林【摘要】The large and integrative composite panels can not only reduce the plane weight, but also improve the plane performance, simplify assembly. Because of layup complexity in the large-sized co-cured composite part, it is dif-ficult for traditional molding technology and quality is unstable. With the theory of design for manufacture, DFM, and ap-plying the advanced digital manufacture technique to the composite part , it is a good method for solving the large-sized composite panel manufacture.%大型整体化的复合材料壁板会起到较好的减重效果,明显提升飞机的整体效能,简化装配工艺.大尺寸共固化的复合材料制件铺层结构复杂,传统成型工艺难度大,质量稳定性差,组合元件形位尺寸有偏差.随着设计制造一体化(DFM)理念的出现,先进数字化制造技术在复合材料零件制造方面的应用很好地解决了大尺寸复合材料壁板类零件制造的难题.【期刊名称】《航空制造技术》【年(卷),期】2017(000)011【总页数】5页(P105-109)【关键词】设计制造一体化;自动铺带;加热预成型;激光定位组合【作者】李林【作者单位】航空工业沈阳飞机工业(集团)有限公司,沈阳 110850【正文语种】中文相较金属材料,复合材料有较好的比刚度、比强度、耐疲劳、抗冲击、耐腐蚀性能。
铺丝机简介——精选推荐
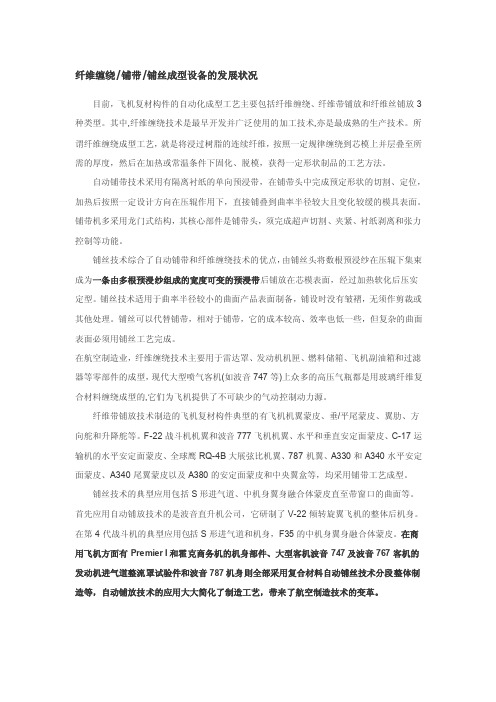
纤维缠绕/铺带/铺丝成型设备的发展状况目前,飞机复材构件的自动化成型工艺主要包括纤维缠绕、纤维带铺放和纤维丝铺放3种类型。
其中,纤维缠绕技术是最早开发并广泛使用的加工技术,亦是最成熟的生产技术。
所谓纤维缠绕成型工艺,就是将浸过树脂的连续纤维,按照一定规律缠绕到芯模上并层叠至所需的厚度,然后在加热或常温条件下固化、脱模,获得一定形状制品的工艺方法。
自动铺带技术采用有隔离衬纸的单向预浸带,在铺带头中完成预定形状的切割、定位,加热后按照一定设计方向在压辊作用下,直接铺叠到曲率半径较大且变化较缓的模具表面。
铺带机多采用龙门式结构,其核心部件是铺带头,须完成超声切割、夹紧、衬纸剥离和张力控制等功能。
铺丝技术综合了自动铺带和纤维缠绕技术的优点,由铺丝头将数根预浸纱在压辊下集束成为一条由多根预浸纱组成的宽度可变的预浸带后铺放在芯模表面,经过加热软化后压实定型。
铺丝技术适用于曲率半径较小的曲面产品表面制备,铺设时没有皱褶,无须作剪裁或其他处理。
铺丝可以代替铺带,相对于铺带,它的成本较高、效率也低一些,但复杂的曲面表面必须用铺丝工艺完成。
在航空制造业,纤维缠绕技术主要用于雷达罩、发动机机匣、燃料储箱、飞机副油箱和过滤器等零部件的成型,现代大型喷气客机(如波音747等)上众多的高压气瓶都是用玻璃纤维复合材料缠绕成型的,它们为飞机提供了不可缺少的气动控制动力源。
纤维带铺放技术制造的飞机复材构件典型的有飞机机翼蒙皮、垂/平尾蒙皮、翼肋、方向舵和升降舵等。
F-22战斗机机翼和波音777飞机机翼、水平和垂直安定面蒙皮、C-17运输机的水平安定面蒙皮、全球鹰RQ-4B大展弦比机翼、787机翼、A330和A340水平安定面蒙皮、A340尾翼蒙皮以及A380的安定面蒙皮和中央翼盒等,均采用铺带工艺成型。
铺丝技术的典型应用包括S形进气道、中机身翼身融合体蒙皮直至带窗口的曲面等。
首先应用自动铺放技术的是波音直升机公司,它研制了V-22倾转旋翼飞机的整体后机身。
复合材料工艺详解(共35页)

复合材料(fù hé cái liào)工艺详解——热固与热塑树脂(shùzhī)热固性树脂(shùzhī)成型工艺手糊成型(chéngxíng)工艺(手糊类)手糊成型:用纤维增强材料和树脂胶液在模具上铺覆成型,室温(或加热)、无压(或低压)条件下固化,脱模制成品的工艺方法。
1.原料:①树脂:不饱和聚酯树脂,环氧树脂;②纤维增强材料:玻纤制品(无捻粗纱、短切纤维毡、无捻粗纱布、玻纤细布、单向织物),碳纤维,Kevlar纤维;③辅助材料:稀释剂,填料,色料。
2.工艺过程:2.1 原材料准备2.1.1胶液准备胶液的工艺性主要指胶液粘度和凝胶时间。
①手糊成型的胶液粘度控制在0.2Pa·s~0.8Pa·s之间为宜。
环氧树脂可加入5%~15%(质量比)的邻苯二甲酸二丁酯或环氧丙烷丁基醚等稀释剂进行调控。
②凝胶时间:在一定温度条件下,树脂中加入定量的引发剂、促进剂或固化剂,从粘流态到失去流动性,变成软胶状态的凝胶所需的时间。
手糊作业前必须做凝胶试验。
但是胶液的凝胶时间不等于制品的凝胶时间,制品的凝胶时间不仅与引发剂、促进剂或固化剂有关,还与胶液体积、环境温度与湿度、制品厚度与表面积大小、交联剂蒸发损失、胶液中杂质的混入、填料加入量等有关。
2.1.2增强材料的准备手糊成型所适用增强材料主要是布和毡。
需要注意布的排向,同一铺层的拼接,布的剪裁。
2.1.3胶衣糊准备胶衣树脂的性能指标:外观:颜色均匀,无杂质,粘稠状流体;酸值:10mgKOH/g~15mgKOH/g(树脂);凝胶时间:10min ~15min;触变指数(zhǐshù):5.5~6.5;贮存(zhùcún)时间:25℃ 6个月2.1.4手糊制品厚度(hòudù)与层数计算①手糊制品(zhìpǐn)厚度t:制品(铺层)的厚度;m:材料质量,Kg/m2;k:厚度常数,mm/(Kg·m-2)材料厚度常数k表材料性能玻璃纤维E型 S型 C型聚酯树脂环氧树脂填料-碳酸钙密度(Kg/m3)2.56;2.49;2.45 1.1;1.2;1.3;1.4 1.1;1.3 2.3;2.5;2.9k[mm/(Kg·m-2)]0.391;0.402;0.408 0.909;0.837;0.769;0.714 0.909;0.769 0.435;0.400;0.345②铺层层数计算A:手糊制品总厚度,mm;m f:增强纤维单位面积质量,Kg/m2;kf:增强纤维的厚度常数,mm/(Kg·m-2);kr:树脂基体的厚度常数,mm/(Kg·m-2);c:树脂与增强材料的质量比;n:增强材料铺层层数。
复合材料长桁共固化成型工艺

定期对设备及工具进行保养, 延长其使用寿命。
04 复合材料长桁共固化成型工艺应用案例及效果
应用案例一
• 背景介绍:随着航空工业的发展,飞机制造对材料的要求越来 越高。复合材料因其高强度、轻质、耐腐蚀等优点,在飞机制 造中得到广泛应用。长桁作为飞机结构中的重要构件,其成型 工艺直接影响飞机的性能和安全性。
近年来,复合材料长桁共固化成型工艺不断取得突破,如在制造大型复杂结构件方面的应用、新型预浸料和粘合 剂的开发、以及绿色制造和循环利用等方面的研究。未来,该工艺将继续朝着提高性能、降低成本、提高生产效 率等方向发展。
02 复合材料长桁共固化成型工艺原理及流程
工艺原理
01
复合材料长桁共固化成型工艺是 将两种或两种以上的不同材料通 过共固化工艺结合在一起,形成 一种新型的复合材料。
真空泵
用于在热压罐内形成真空环境 ,帮助材料吸附并排除气泡,
提高成型质量。
搅拌器
用于混合和搅拌复合材料原料 ,确保材料均匀性和一致性。
模具
用于定义复合材料长桁的形状 和尺寸,一般由金属或高强度
塑料制成。
主要工具及用途
热电偶
用于监测热压罐内的温度,确 保温度控制在合适的范围内。
压力传感器
用于监测热压罐内的压力,确 保压力控制在合适的范围内。
质量检测与控制
由于复合材料具有各向异性和非线性等特点,因此其质量 检测与控制技术存在一定难度,需要加强质量检测与控制 技术的研究,提高产品质量和稳定性。
未来发展展望
拓展应用领域
随着复合材料长桁共固化成型工艺的不断完善和发展,其应用领域 将不断拓展,如航空航天、汽车、船舶等领域将得到更广泛的应用 。
1. 铺设增强纤维预浸料;
聚合物基复合材料成型工艺
3. 固化(凝胶-----定型-----熟化)
固化方式
常温固化:温度>15℃ (25~30℃);湿度 ≤80% (15~30℃,8~24h)
加热固化:烘箱、固化炉、模具加热、红外 线加热 (60~80℃,1~2h)
固化度 丙酮萃取法 硬度法(巴氏硬度) >15
4. 脱模:气脱、顶脱、水脱
5. 后处理 修整:除去毛边、飞刺、修补表面及内部缺陷,钻孔 装配:机械连接、胶接 表面涂饰
四、手糊制品缺陷及原因
1. 胶衣起皱、龟裂、变色
原因: 起皱 ①胶衣层太薄;②固化剂不足;③气温太低; ④胶衣层厚度不均;⑤胶衣层固化不足
龟裂 ①胶衣层太厚;②固化时热量过大; ③固化剂用量过多;
变色 ①固化剂用量过多;②胶衣流挂; ③颜色分离;④胶衣层厚度不均
NaBO2 (5~8%) ),80℃溶于水; ⑦低熔点金属58%Bi+42%Sn,熔点135 ℃; ⑧玻璃钢 ⑨金属:钢材、铸铝,不能用铜(铜盐可妨碍树脂固化)
三、模具结构形式
单模 阴模(制品外表面光洁) 阳模(制品内表面光洁)
对合模 制品双面光洁 拼装模(组合模) 大型模具,由小块模具拼装而成
a.阴模示意图
4. 真空袋材料:气球步、橡胶袋、尼龙薄膜 5. 密封材料:胶条、胶带
图4-5 手糊玻璃钢制品举例
➢袋压成型
优点:仅用一个模具,就可得到形状复杂,尺寸较大,质量较好 的制件,也能制造夹层结构件
一、真空袋成型 1. 过程
制品毛坯 真空袋密封
抽真空
固化 制品
2. 特征 1)工艺简单,不需要专用设备;
3)预热和预成型
A. 预热作用:改善工艺性能,提高模压料温度,缩短固 化时间,降低成型压力;
先进复合材料制造及过程控制技术
先进复合材料制造及过程控制技术摘要:基于先进复合材料比强度、比模量高,抗疲劳、耐腐蚀性能好,结构、功能可设计,可整体成型等优异特性,由于复合材料是多组分的各向异性材料,其材料制造和构件成型同步完成,对产品制造缺陷的修复空间狭小,要实现大型复杂结构件的高效、稳定制造,除了要具备性能优异的原材料以外,复合材料构件的制造技术至关重要。
因此,开展先进复合材料结构制造技术研究并实现复合材料制造过程的高水平质量控制,对满足民机适航性和经济性的高标准要求、实现复合材料在民机领域的大规模应用与批产具有重要意义。
关键词:先进复合材料;飞机;制造技术先进复合材料已成为新一代大飞机的主体结构材料,其在飞机上的用量和应用部位已经成为衡量飞机结构先进性的重要标志之一。
随着复合材料在飞机上的应用日益广泛,复合材料产品生产制造过程的质量控制也随之成为研究的热点问题。
一方面,由于航空企业对质量的严格要求决定了作为飞机重要零部件的复合材料产品必须进行严格的生产控制和管理;另一方面,由于复合材料的原材料和生产制造加工成本昂贵,故有必要对生产加工过程进行实时监控,及时发现生产中出现的异常因素,减少或防止不合格品的产生,有效提高企业效益。
一、复合材料复合材料是由两种或两种以上不同性质或不同结构的材料以微观或宏观的形式组合在一起而形成的材料,通常由基体和增强剂两部分构成。
当今,复合材料已经与铝、钢、钛一起并列为四大航空结构材料。
复合材料在经历了几个阶段的发展后,实现了从非承力构件、次承力构件到尾翼、机翼与机身等主承力构件的转变。
发生这种转变既是因为飞机性能的需求,同时也是商业和市场竞争的需要。
目前新研制的飞机大都在主结构上采用了复合材料,这大大的提高了结构的一体化程度,减少了零部件的个数,缩短了总装的时间。
另外,复合材料非常好的物理特性和可设计性,再加上目前复合材料生产成本的降低,这促使了航空企业选材从金属材料向复合材料的转变。
当今,随着先进复合材料在军、民用飞机上的应用,复合材料的生产制造成本不断降低,复合材料的应用越来越广泛,不仅在航空航天领域,其他各个领域如航海领域等也越来越多的应用先进复合材料到结构中。
复合材料缠绕成型工艺设备
复合材料缠绕成型工艺设备复合材料缠绕成型是一种常用的制备复合材料制品的工艺方法,该方法通过将纤维材料缠绕在模具上,并结合树脂基体固化形成所需形状。
复合材料缠绕成型工艺设备是用于实现该工艺的专用设备,下面将介绍该设备的主要特点和工作原理。
一、设备特点1.1 自动化程度高:复合材料缠绕成型工艺设备采用先进的自动化控制系统,可以实现整个制造过程的自动化操作,大大提高了生产效率和产品质量。
1.2 精确控制系统:设备配备了精确的控制系统,可以对纤维材料的缠绕角度、张力、速度等进行精确控制,确保制品的质量和性能。
1.3 多功能性:设备可以适应不同形状和尺寸的制品制造,通过更换模具和调整参数,可以满足不同客户的需求。
1.4 节能环保:设备采用先进的节能技术,可以降低能源消耗,减少环境污染。
二、工作原理复合材料缠绕成型工艺设备主要包括纤维材料供给系统、树脂基体供给系统、缠绕机构以及控制系统等组成。
2.1 纤维材料供给系统:纤维材料通常以纱线或带状材料的形式供给,供给系统通过张力控制装置控制纤维材料的张力,保证材料的均匀缠绕。
2.2 树脂基体供给系统:树脂基体通常以液态或半固态形式供给,供给系统通过泵和管路将树脂基体输送到缠绕区域,与纤维材料进行充分混合。
2.3 缠绕机构:缠绕机构是实现纤维材料缠绕的关键部分,它通常由缠绕头、缠绕臂和转动平台等组成。
缠绕头负责将纤维材料沿着设定的轨迹缠绕在模具上,缠绕臂负责控制纤维材料的张力和缠绕角度,转动平台负责使模具进行旋转,以实现整个制造过程。
2.4 控制系统:控制系统用于控制设备的运行和参数调节,通过传感器对纤维材料的张力、树脂基体的流量等进行实时监测和调整,确保制品的质量和性能。
三、应用领域复合材料缠绕成型工艺设备广泛应用于航空航天、汽车、船舶、能源等领域。
在航空航天领域,它被用于制造飞机机翼、机身、推进器等部件;在汽车领域,它被用于制造车身、底盘等部件;在船舶领域,它被用于制造船体和推进器等部件;在能源领域,它被用于制造风力发电叶片、太阳能板等设备。
酚醛树脂及复合材料成型工艺的研究进展
酚醛树脂是最早工业化的合成树脂,已经有100年的历史。
由于它原料易得,合成方便以及树脂固化后性能能满足很多使用要求,因此在模塑料、绝缘材料、涂料、木材粘接等方面得到广泛应用。
近年来,随着人们对安全等要求的提高,具有阻燃、低烟、低毒等特性的酚醛树脂重新引起人们重视,尤其在飞机场、火车站、学校、医院等公共建筑设施及飞机的内部装饰材料等方面的应用越来越多[1]。
与不饱和聚酯树脂相比,酚醛树脂的反应活性低,固化反应放出缩合水,使得固化必须在高温高压条件下进行,长期以来一般只能先浸渍增强材料制作预浸料(布),然后用于模压工艺或缠绕工艺,严重限制了其在复合材料领域的应用。
为了克服酚醛树脂固有的缺陷,进一步提高酚醛树脂的性能,满足高新技术发展的需要,人们对酚醛树脂进行了大量的研究,改进酚醛树腊的韧性、提高力学性能和耐热性能、改善工艺性能成为研究的重点。
近年来国内相继开发出一系列新型酚醛树脂,如硼改性酚醛树脂、烯炔基改性酚醛树脂、氰酸酯化酚醛树脂和开环聚合型酚醛树脂等。
可以用于smc/bmc、rtm、拉挤、喷射、手糊等复合材料成型工艺。
本文结合作者的研究工作,介绍了酚醛树脂的改性研究进展及rtm、拉挤等酚醛复合材料成型工艺的研究应用情况。
1酚醛树脂的改性研究1.1聚乙烯醇缩醛改性酚醛树脂工业上应用得最多的是用聚乙烯醇缩醛改性酚醛树脂,它可提高树脂对玻璃纤维的粘结力,改善酚醛树脂的脆性,增加复合材料的力学强度,降低固化速率从而有利于降低成型压力。
用作改性的酚醛树脂通常是用氨水或氧化镁作催化剂合成的苯酚甲醛树脂。
用作改性的聚乙烯醇缩醛一般为缩丁醛和缩甲乙醛。
使用时一般将其溶于酒精,作为树脂的溶剂。
利用缩醛和酚醛羟甲基反应合成的树脂是1种优良的特种油墨载体树脂。
1.2聚酰胺改性酚醛树脂经聚酰胺改性的酚醛树脂提高了酚醛树脂的冲击韧性和粘结性。
用作改性的聚酰胺是一类羟甲基化聚酰胺,利用羟甲基或活泼氢在合成树脂过程中或在树脂固化过程中发生反应形成化学键而达到改性的目的。
- 1、下载文档前请自行甄别文档内容的完整性,平台不提供额外的编辑、内容补充、找答案等附加服务。
- 2、"仅部分预览"的文档,不可在线预览部分如存在完整性等问题,可反馈申请退款(可完整预览的文档不适用该条件!)。
- 3、如文档侵犯您的权益,请联系客服反馈,我们会尽快为您处理(人工客服工作时间:9:00-18:30)。
先进复合材料主要制造工艺和专用设备中国航空工业第一集团公司科技发展部 郝建伟中国航空工业发展研究中心 陈亚莉先进复合材料具有轻质、高强度、高模量、抗疲劳、耐腐蚀、可设计、成型工艺性好和成本低等特点,是理想的航空结构材料,在航空产品上得到了广泛应用,已成为新一代飞机机体的主体结构材料。
复合材料先进技术的成熟使其性能最优和低成本成为可能,从而大大推动了复合材料在飞机上的应用。
一些大的飞机制造商在飞机设计制造中,正逐步减少传统金属加工的比例,优先发展复合材料制造。
本文旨在介绍在复合材料制造过程中所涉及到的主要工艺和先进专用设备。
复合材料在飞机上的应用随着复合材料制造技术的发展,复合材料在飞机上的用量和应用部位已经成为衡量飞机结构先进性的重要标志之一。
复合材料在飞机上的应用趋势有如下几点:(1)复合材料在飞机上的用量日益增多。
复合材料的用量通常用其所占飞机机体结构重量的百分比来表示,世界上各大航空制造公司在复合材料用量方面都呈现增长的趋势。
最有代表性的是空客公司的A380客机和后续的A350飞机以及波音公司的B787飞机。
A380上复合材料用量约30t。
B787复合材料用量达到50%。
而A350飞机复合材料用量更是达到了创纪录的52%。
复合材料在军机和直升机上的用量也有同样的增长趋势,近几年得到迅速发展的无人机更是将复合材料用量推向更高水平。
(2)应用部位由次承力结构向主承力结构发展。
最初采用复合材料制造的是飞机的舱门、整流罩、安定面等次承力结构。
目前,复合材料已经广泛应用于机身、机翼等主承力结构。
主承载部位大量应用复合材料使飞机的性能得到大幅度提升,由此带来的经济效益非常显著,也推动了复合材料的发展。
(3)在复杂外形结构上的应用愈来愈广泛。
飞机上用复合材料制造的复杂曲面制件也越来越多,如A380和B787飞机上的机身段,球面后压力隔框等,均采用纤维铺放技术和树脂膜渗透(RFI)工艺制造。
(4)复合材料构件的复杂性大幅度增加,大型整体、共固化成型成为主流。
在飞机上大量采用复合材料的最直接的效果是减重,复合材料制件采用共固化、整体成型技术,能够成型大型整体部件,明显减少零件、紧固件和模具的数量,减少零件装配,从而有效地降低制造成本。
(5)复合材料的制造手段和先进专用设备得到迅速发展和广泛应用。
传统的复合材料制造技术自动化程度低,复合材料制件的质量不稳定,分散性大,可靠性差,生产成本居高不下,无法生产大型和复杂的复合材料制件。
飞机结构尺寸的不断增加使大尺寸复合材料制件的制造工艺变得极为重要。
近年来,出现了各种各样的自动化程度较高的制造技术,如纤维铺放、树脂膜转移成型/渗透成型、电子束固化等技术。
随之研制并得以工业化应用的先进、高效、低成本专用设备也层出不穷,如三维编织机、全自动铺带设备和丝束铺放设备等。
这些高效自动化设备显著提高了复合材料生产效率和制件内部质量,降低了成本,使复合材料性能最优化和低成本并存成为可能。
复合材料制造工艺及主要设备复合材料成型是一个比较复杂的过程。
随着各种新工艺、新技术的涌现,复合材料制造工艺已成为复合材料加工制造的关键,涵盖的技术面广、技术含量高,涉及的成本份额占总成本的80%以上。
根据用途、批量、市场等要求的不同,航空航天用复合材料产品的成型工艺采用了手工铺层、半自动成型、全自动成型以及液体成型等技术。
下面就生产中主要涉及的工艺方法和主要设备加以重点说明。
(1)手工铺层。
目前,手工铺层仍是被广泛使用的传统成型方法,甚至像B-2轰炸机以及一些通用飞机的制造也采用了大量的手工铺层工序。
因为这些产品的定货量往往是一位数,而质量要求很高。
手工铺贴方法的优点是可使蒙皮厚度有大的变化,进行局部加强,嵌入接头用的金属加强片,形成加强筋和蜂窝夹芯区等。
目前,手工铺层使用了许多专用设备来控制和保证铺层的质量,如复合材料预浸料自动剪裁下料系统和铺层激光定位系统等,即采用专门的数控切割设备来进行预浸料和辅助材料的平面切割,从而将依赖于样板的制造过程转变为可根据复合材料设计软件产生的数据文件进行全面运作的制造过程。
手工铺层的缺点是要求铺层人员有很高的技艺和施工经验,手工铺贴费工费时,因此效率低、成本高(占总成本的1/4),难以适应大批量生产和大型复杂复合材料制件的生产要求。
因此,在60年代初,在手工铺层复合材料实施几年之后,就开发了自动铺带(ATL)技术。
即使在美国,人工铺带也仍然采用,这是美国 Liberty Aerospace的工人正在操作(2)自动铺带(ATL)。
自动铺带技术采用有隔离衬纸的单向预浸带,其裁剪、定位、铺叠、辊压均采用数控技术自动完成,由自动铺带机实现。
多轴龙门式机械臂完成铺带位置的自动控制,铺带头上装有预浸带输送和切割系统,根据待铺放工件边界轮廓自动完成预浸带的铺放和特定形状位置的切割。
预浸带在加热状态时,在压辊的压力作用下铺叠到模具表面。
自动铺带机根据铺放制件的几何特征可分为平面铺带和曲面铺带两类。
随着自动铺带设备、编程、计算机软件、铺带技术以及材料的进一步发展,自动铺带的效率变得更高,性能更可靠,操作性更友好。
与手工相比,先进铺带技术可降低制造成本的30%~50%,可成型超大尺寸和形状复杂的复合材料制件,而且质量稳定,缩短了铺层及装配时间,工件近净成型,切削加工及原材料耗费减少。
目前,最先进的第五代铺带机是带有双超声切割刀和缝隙光学探测器的十轴铺带机,铺带宽度最大可达到300mm,生产效率可达到手工铺叠的数十倍。
自动铺带机要成型复杂双曲率型面,需采用窄带,工作效率会降低,而一台铺带机的价格需要3~5百万美元,成本太高。
由此,Hercules率先开发了自动丝束铺放(ATP)设备。
(3)自动丝束铺放(ATP)。
自动丝束铺放技术结合了自动铺带和纤维缠绕技术的优点,铺束头把缠绕技术所用的不同预浸纱束独立输送和铺带技术所用的压实、切割、重送功能结合在一起,由铺束头将数根预浸纱束在压辊下集束成为一条宽度可变的预浸带,然后铺放在芯模表面,铺放过程中加热软化预浸纱束并压实定型。
与自动铺带相比,自动铺丝束技术可以成型更复杂的结构件,材料消耗率低,是自动化制造技术的顶峰,ATP设备对复合材料的重要性相当于铣床对金属材料结构的重要性。
它是介于自动缠绕与自动铺带之间的一种铺层方法,特别适于复杂构件的制造。
自动铺放技术的基础是铺放机的设计与开发。
以美国辛辛那提机床公司Viper纤维铺放机系统为例。
Viper纤维铺放系统将缠绕、特型铺带及计算机控制结合起来,自动生产需要大量手工铺层的复杂零件,从而缩短铺层及装配时间,由于工件近净成型,切削加工及原材料耗费减少。
沃特公司制造波音787的23%的机身,其中包括5.8m×7m的47段及4.3m×4.6m的48段,采用了来自辛辛那提公司的自动铺放机Viper6000。
制造时,将东丽的3900系碳/环氧无纬带铺叠在大的筒形旋转模具上,模具由互锁的芯轴组成,筒形件铺成后放在23.2m×9.1m 的、世界上体积最大的热压罐中固化。
目前,自动丝束铺放机已可铺放窄带及宽带丝束。
预浸丝束/带的机器人自动铺放已成为高性能纤维增强复合材料结构的一种强力高效技术。
它是机电装备技术、CAD/CAM软件技术和材料工艺技术的综合集成,包括:自动铺放装备技术、预浸丝束/带切割技术、铺放CAD技术、铺放CAM技术、预浸丝束/带技术、自动铺放工艺技术、铺放质量控制、模具技术、成本分析及控制和一体化协同数字化设计技术等,具有高效率、高质量、高重复性和低成本等优点。
Viper6000大型ATP机,代表了当今自动丝束铺放最高水平(4)热压罐固化成型。
热压罐固化成型是航空航天复合材料结构件传统的制造工艺,它有产品重复性好、纤维体积含量高、孔隙率低或无孔隙、力学性能可靠等优点。
热压罐固化的缺点主要是耗能高以及运行成本高等。
而目前大型复合材料构件必需在大型或超大型热压罐内固化,以保证制件的内部质量,因此热压罐的三维尺寸也在不断加大,以适应大尺寸复合材料制件的加工要求。
目前,热压罐都采用先进的加热控温系统和计算机控制系统,能够有效地保证在罐内工作区域的温度分布均匀,保证复合材料制件的内部质量和批次稳定性,如准确的树脂含量、低或无空隙率和无内部其他缺陷。
这也是热压罐一直沿用至今的主要原因。
(5)复合材料液体成型。
复合材料液体成型已是十分普及的工艺,它是以树脂转移成型(RTM)为主体,包括各种派生的RTM技术,大约有25~30种之多,其中,RTM、真空辅助RTM(VARTM)、真空辅助树脂注射成型(VARI)、树脂膜熔浸成型(RFI)和树脂浸渍成形(SCRIMP)被称为RTM的5大主要成型工艺,也是目前应用最多的RTM工艺。
RTM的优点是成品的损伤容限高,可成型精度高、孔隙率小的复杂构件及大型整体件。
RTM成型的关键是,要有适当的增强预形件以及适当黏度的树脂或树脂膜。
RTM要求树脂在注射温度下的黏度值低,第一代环氧树脂的粘度要求在500cps(0.5Pa·s)以下,以前对于较大尺寸的构件要求树脂黏度低于250cps(0.25Pa·s),RTM工艺的主要设备是各种树脂注射机和整体密闭型模具。
随着新型增强材料结构的不断创新,编织技术和预成形体技术与RTM技术相结合,形成了新的工艺发展和应用方向。
如采用三维编织技术将增强材料预制成3D结构,然后再与RTM工艺复合,也可将纤维织物通过缝纫或粘结的方法,直接预制成制件形状,再采用RTM工艺成型复合材料。
例如,EADS军用飞机公司为B787后机身段制造的后压力隔框,它是一个半球形的整体隔框,插在增压的机身47段及非增压的48段及尾段之间,它是用VARTM制造的,尺寸大约为4.3m×4.6m,波音787是首架具有复合材料后压力隔框的飞机。
该隔框的制造得益于Cytec公司的树脂熔渗膜系统。
韧化的复合材料有顶级阻燃/烟/毒性能,可以取消防火层,从而比传统的树脂熔渗法制得的结构轻。
而波音787机身的大部分隔框则采用了碳纤维树脂膜熔渗RFI技术制造,复合材料隔框用碳纤维复合材料抗剪箍连接在机身蒙皮上,由于设计及成本上的原因,少数部位仍采用钛合金及铝合金隔框。
(6)隔膜成型。
隔膜成型原是一种为热塑性复合材料开发的成型工艺,后发现用于热固性复合材料具有很广泛的用途。
它具有成型过程中纤维不易滑动、不易产生皱褶的特殊功效,非常适用于加工大型飞机机翼前梁的C 形截面。
在近年推出的A400M等大型飞机前梁C形截面中,已广泛采用了这种工艺方法。
为成型出C形截面,预形件从铺带机上卸下送到由英国Aeroform 公司提供的热包膜成型机设备上成型。
为便于抽真空,预形件应夹在两个由俄亥俄州的杜邦电子技术公司提供的Kapton聚酰亚胺薄膜之间。