橡胶硫化体系[1]
(知识)橡胶硫化体系概述、硫化过程

(知识)橡胶硫化体系概述、硫化过程橡胶硫化体系概述一、硫化定义硫化是指橡胶的线型大分了链通过化学交联而构成三维网状结构的化学变化过程。
随之胶料的物理性能及其他性能也发发生根本变化。
橡胶分子链在硫化前后的状态如图所示。
橡胶硫化是橡胶生产加工过程中的一个非常重要的阶段,也是最后的一道工序。
这一过程赋予橡胶各种宝贵的物理性能,使橡胶成为广泛应用的工程材料,在许多重要部门和现代尖端科技如交通、能源、航天航空及宇宙开发的各个方面都发挥了重要作用。
二、橡胶硫化体系的发展历程硫化反应是**人Charles Goodyear 于1839年发现的,他将硫黄与橡胶混合加热,能制得性能较好材料。
这一发现是橡胶发展史上最重要的里程碑。
英国人Hancock最早把这一方法用于工业生产,他的朋友Brockeden把这一生产过程称作硫化,直至今天,橡胶工艺科学家仍然沿用这一术语。
1940年又相继发现了树脂硫化和醌肟硫化方法;1943年又发现了硫磺给予体的硫化。
第二次世界以后,又出现了新型硫化体系,如50年代发现的辐射硫化,70年代的脲烷硫化体系和80年代提出的平衡硫化体系等等。
尽管如此,由于硫黄价廉易得,资源丰富,硫化胶性能好,仍是最佳的硫化剂。
经过100多年的研究及发展,已形成几个基本的不同层次的硫黄硫化体系,组成层次表示如下;硫化反应是一个多元组分参与的复杂化学反应过程。
它包含橡胶分子与硫化剂及其他配合剂之间发生的一系列化学反应,在形成网状结构时伴随着发生各种副反应。
其中,橡胶与硫黄的反应占主导地位,它是形成空间网络的基本反应。
一般说来,大多数含有促进剂硫黄硫化的橡胶,大致经历了如下的硫化历程:三、橡胶硫化历程(一)橡胶硫化反应过程(二)硫化历程根据硫化历程分析,可分四个阶段,即焦烧阶段、热硫化阶段、平坦硫化阶段和过硫化阶段。
较为理想的橡胶硫化曲线应满足下列条件: (1)硫化诱导期要足够长.充分保证生产加工的安全性 (2)硫化速度要快,提高生产效率,降低能耗; (3)硫化平坦期要长。
橡胶的硫化体系介绍

橡胶的硫化体系介绍橡胶是一种天然或合成的高分子化合物,具有特殊的弹性和可塑性。
它广泛应用于轮胎、橡胶鞋、管道、密封件等领域。
然而,未经处理的橡胶易老化、自然硬化、热塑性差等缺陷,限制了其使用寿命和性能。
为了克服这些缺陷,橡胶必须进行硫化处理,即向其中引入硫化剂将橡胶分子交联成网状结构,从而增强其硬度、强度、耐磨性和耐化学性等方面的性能。
本文将介绍橡胶硫化体系的基本知识和应用。
1.橡胶的硫化橡胶的硫化是指在适当的温度和压力下,将橡胶与硫化剂反应生成交联链的过程。
硫化剂的作用是将橡胶分子链上的双键和硫醇基之间形成新的硫化键,使其形成硫化链。
随着硫化时间的延长,硫化链交联成网状结构,从而增强了橡胶的强度和硬度。
常见的硫化剂有硫化石灰、含硫羟化合物、代硫酰化合物等。
2.硫化剂的选择选择合适的硫化剂是橡胶硫化体系设计的重要环节。
硫化剂的性质影响着硫化过程的速率和特性。
一般来说,硫化剂的选择应该考虑以下因素:(1) 橡胶的种类和用途。
不同类型的橡胶对硫化剂的适应性不同,在选择硫化剂时应该考虑橡胶本身的特性和使用要求。
(2) 硬度和硫化速率。
硫化剂的种类、含量和硫化条件等因素都会影响硬度和硫化速率,因此选择硫化剂时应该考虑硬度和硫化速率的平衡。
(3) 压力和温度。
硫化剂的选择还应该考虑硫化过程的温度和压力等因素。
(4) 环保和成本。
在选择硫化剂时,还应考虑其环保性和成本因素。
3.橡胶硫化体系的分类橡胶硫化体系主要分为硫磺法和非硫磺法两种。
硫磺法是指使用硫磺作为硫化剂,形成交联链的过程。
硫磺硫化可以在常温下进行,对环境污染小,但硫化速率慢,需要使用促进剂和加热加压等条件来促进硫化。
非硫磺法是指使用非硫磺硫化剂来进行橡胶硫化,如含硫异氰酸酯、含硫醚化合物、含硫羟化合物、代硫酰化合物等。
这些硫化剂可在温和条件下发生反应,硫化速率快,不需要特殊的加热和加压条件,且可降低环境污染。
4.硫化介质的种类硫化介质是指用来促进硫化反应的介质,可以提高反应速率和控制反应条件。
橡胶硫化体系

橡胶硫化体系介绍橡胶硫化体系是指通过加入硫化剂、促进剂和助磺剂等物质,使橡胶分子间发生化学交联反应,形成弹性体的过程。
这个体系在橡胶制品的生产过程中起到了至关重要的作用。
本文将对橡胶硫化体系进行全面、详细、完整且深入地探讨。
硫化剂的作用硫化剂是橡胶硫化体系的核心组成部分,它能够引发橡胶分子间的交联反应。
硫化剂的主要作用有: 1. 引发剂作用:硫化剂能够分解,产生自由基或电离态硫,进而引发橡胶分子的交联反应。
2. 网络形成:硫化剂引发的交联反应使橡胶分子间形成网络结构,增加了橡胶的物理性能,如弹性、耐磨性等。
3. 促进界面反应:硫化剂可以提高橡胶与填料、助剂等其他物质之间的反应活性,增强它们之间的相互作用。
促进剂的作用促进剂常与硫化剂一同使用,它对硫化系统有着重要的调节作用。
促进剂的主要作用有: 1. 提高硫化速度:促进剂能够加快硫化反应的进行,缩短橡胶制品的硫化时间。
2. 改善硫化性能:促进剂能够改善橡胶硫化后的物理性能,如强度、硬度、耐磨性等,使制品具有更好的综合性能。
3. 调节硫化体系:促进剂能够调节硫化体系的活性、稳定性和选择性,提高其适应性和可控性。
助磺剂的作用助磺剂是橡胶硫化体系中的辅助物质,它对硫化反应起到协助作用。
助磺剂的作用主要有: 1. 促进硫化反应:助磺剂与硫化剂共同作用,加速硫化反应的进行,提高交联密度,增强橡胶硫化的效果。
2. 改善反应性能:助磺剂能够调节硫化体系的反应速度、温度敏感性和耐老化性,改善橡胶硫化的性能和稳定性。
硫化体系的选择在实际应用中,选择合适的硫化体系对于橡胶制品的质量和性能至关重要。
硫化体系的选择需要考虑以下几个因素: 1. 橡胶种类:不同种类的橡胶对硫化剂的反应性和选择性有所差异,需要根据橡胶材料的特点进行选择。
2. 硬度要求:不同硫化体系对制品硬度的影响不同,根据制品要求选择合适的硫化体系。
3. 工艺条件:硫化体系的选择还需考虑工艺条件,如硫化温度、硫化时间等。
3橡胶工艺学第二章橡胶的硫化体系
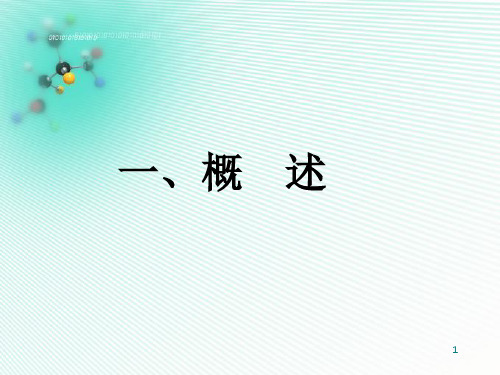
特点:
焦烧时间长,硫化速度快。 适用于合成橡胶的高温快速硫化和厚制
品的硫化。该类促进剂诱导期的长短与 和氨基相连基团的大小数量有关,基团 越大,数量越多,诱导期越长,防焦效 果越好。如DZ>NOBS>CZ。
31
Ⅲ.秋兰姆类:
ห้องสมุดไป่ตู้
结构通式为:
R' S
S
R'
N C Sx C N
R
R
R,R’为烷基,芳基或其它基团
双键 自由基 Or 离子型加成
∵硫化前后双键数目变化不大。
∴反应主要在α-H上反应,以自由基 机理为主。
7
㈡、硫化历程
第一阶段:诱导期,活性剂,促进剂,硫 黄之间相互作用,生成带有多硫促进剂侧 基的橡胶大分子。线型分子,能流动。
第二阶段:交联反应,带有多硫促进剂侧 基的橡胶大分子与橡胶大分子之间发生交 联反应,生成交联键。初期网状分子,已 不能流动。
H, D
NA-22,
CZ
NOBS,
DZ
18
按促进速度分类:
国际上习惯以促进剂M对NR的硫化速度 为标准,以比较促进剂的硫化速度。
慢速级促进剂:H,NA-22 中速级促进剂:D 准速级促进剂:M,DM,CZ,DZ,NOBS 超速级促进剂:TMTD,TMTM 超超速级促进剂:ZDMC,ZDC
英文 简称 ZDM
C ZDC
BZ
PX
基团
R,R’为甲基,M为 锌
R,R’为乙基,M为 锌
R,R’为丁基,M为 锌
R为乙基,R’为苯 基,M为锌
36
特点:
此类促进剂比秋兰姆更活泼。 过渡金属离子使橡胶的不饱和键更易
极化,硫化速度更快,属超超速级酸 性促进剂。 诱导期极短,适用于室温硫化和胶乳 制品的硫化。
橡胶硫化体系详解

硫化是胶料通过生胶分子间交联,形成三维网络结构,制备硫化胶的基本过程。
不同的硫化体系适用于不同的生胶。
橡胶硫化的研究一直在深入持久地进行,研究的目的主要是改进硫化胶的力学性能及其它性能,简化及完善工艺过程,降低硫化时有害物质的释放等等。
下面有针对性地简述当前使用的硫化体系。
不饱和橡胶通常使用如下几类硫化体系。
1.以硫黄,有机二硫化物及多硫化物、噻唑类、二苯胍类,氧化锌及硬脂酸为主的硫化剂。
这是最通用的硫化体系。
但所制得的硫化胶的耐热氧老化性能不高。
2.烷基酚醛树脂。
3.多卤化物(如用于聚丁二烯橡胶、丁苯橡胶及丁腈橡胶的六氯乙烷)、六氯-对二甲苯。
4.双官能试剂[如醌类、二胺类、偶氮及苯基偶氮衍生物(用于丁基橡胶及乙丙橡胶)等。
5.双马来酰亚胺,双丙烯酸酯。
两价金属的丙烯酸酯(甲基丙烯酸酯)、预聚醚丙烯酸酯。
6.用于硫化饱和橡胶的有机过氧化物。
饱和橡胶硫化不同种类的饱和橡胶时,可使用不同的硫化体系。
例如,硫化三元乙丙橡胶时,使用有机过氧化物与不饱和交联试剂,如三烯丙基异氰脲酸酯(硫化剂TAIC)。
硫化硅橡胶时也可使用有机过氧化物。
乙烯基硅橡胶硫化时可在催化剂(Pt)参与条件下进行。
含卤原子橡胶或含功能性基团的橡胶。
聚氯丁二烯橡胶、氯磺化聚乙烯及氯化丁基橡胶等是最常用的含氯橡胶。
硫化氯丁橡胶通常采用ZnO与MgO的并用物,以乙撑硫脲(NA-22)、二硫化秋兰姆、二-邻-甲苯基二胍(促进剂BG)及硫黄作硫化促进剂。
硫化氯磺化聚乙烯时可使用如下硫化体系。
1.氧化铝、氧化铅和氧化镁的并用物,以及氧化镁和季戊四醇酯,以四硫化双五甲撑秋兰姆(促进剂TRA)及促进剂DM作硫化促进剂。
2.六次甲基四胺与己二酸及癸二酸盐及氧化镁。
3.有机胺与环氧化物作用的产物。
以下体系可用于氯化丁基橡胶硫化:1.氧化锌与硬脂酸、氧化镁、秋兰姆及苯并噻唑二硫化物等的并用物;2.乙烯基二硫脲与氧化锌及氧化镁的并用物。
3.多羟基甲基酚醛树脂与氧化锌的并用物。
丁基橡胶硫化体系

丁基橡胶硫化体系摘要:1.丁基橡胶硫化体系的概述2.丁基橡胶硫化体系的组成3.丁基橡胶硫化体系的作用4.丁基橡胶硫化体系的发展趋势正文:一、丁基橡胶硫化体系的概述丁基橡胶硫化体系是指在制备丁基橡胶过程中,通过加入硫化剂和其他辅助材料,使丁基橡胶具有良好的韧性、强度、耐磨性和耐高温性能的一种技术。
硫化体系对于丁基橡胶的性能至关重要,直接影响到丁基橡胶制品的使用寿命和可靠性。
二、丁基橡胶硫化体系的组成丁基橡胶硫化体系主要由以下几部分组成:1.丁基橡胶:丁基橡胶是一种合成橡胶,具有优良的耐热性、耐老化性和耐化学品性能。
2.硫化剂:硫化剂是丁基橡胶硫化体系中最关键的部分,它能够使丁基橡胶分子间产生交联,提高橡胶的韧性和强度。
常用的硫化剂有硫磺、加速剂和促进剂等。
3.填充剂:填充剂可以改善丁基橡胶的加工性能和制品的性能,如增加硬度、耐磨性和耐高温性能等。
常用的填充剂有碳黑、硅烷等。
4.增塑剂:增塑剂能够提高丁基橡胶的柔韧性和可塑性,使其更容易加工成各种形状。
常用的增塑剂有酯类、醚类等。
5.防老剂:防老剂能够延缓丁基橡胶制品的老化过程,延长使用寿命。
常用的防老剂有抗氧化剂、紫外线吸收剂等。
三、丁基橡胶硫化体系的作用丁基橡胶硫化体系的主要作用有以下几点:1.提高丁基橡胶的韧性和强度:通过硫化剂的作用,使丁基橡胶分子间产生交联,形成稳定的三维结构,从而提高韧性和强度。
2.改善丁基橡胶的加工性能:通过添加填充剂、增塑剂等辅助材料,改善丁基橡胶的加工性能,使其更容易加工成各种形状和尺寸的制品。
3.提高丁基橡胶制品的耐热性、耐磨性和耐老化性:通过选择合适的硫化剂、填充剂等材料,提高丁基橡胶制品在使用过程中的耐热性、耐磨性和耐老化性。
四、丁基橡胶硫化体系的发展趋势随着科技的不断发展,丁基橡胶硫化体系也在不断改进和优化,主要发展趋势有以下几点:1.硫化剂的环保化:随着人们对环境保护意识的增强,硫化剂的环保化成为丁基橡胶硫化体系发展的重要方向,如采用无硫硫化剂或低硫硫化剂等。
橡胶制品的硫化过程及对应曲线图

橡胶制品的硫化过程及对应曲线图
橡胶硫化过程:
完整的硫化体系主要有硫化剂、活化剂、促进剂组成
诱导阶段:先是硫磺、促进剂、活化剂的相互作用,是氧化锌在胶料中溶解度增加,活化促进剂,是促进剂与硫磺之间反应生成一种活性更大的中间产物。
对应硫化曲线→焦烧阶段:操作焦烧时间、剩余焦烧时间。
它的长短关系到生产加工安全性,决定于胶料配方成分,主要受促进剂的影响。
操作焦烧时间:橡胶加工过程中由于热积累效应所消耗掉的焦烧时间。
剩余焦烧时间:胶料在模型中加热保持流动性的时间。
交联阶段:可交联的自由基(或离子)与橡胶分子链产生反应,生成交联键对应硫化曲线→热硫化阶段:时间长短决定于温度和胶料配方。
温度越高,促进剂用量越多,硫化速度也越快。
曲线的斜率大小代表硫化反应速度,斜率越大,硫化反应速率
越快,生产效率越高。
网络形成阶段:此阶段的前期,交联反应已趋形成,初始阶段的交联键发生短化、重排和裂解反应,最后网络趋于稳定,获得网络相对稳定的硫化胶。
对应硫化曲线→平坦硫化阶段:网络形成的前期,交联反应已基本完成,继而发生交联键的重排、裂解等反应,胶料强力曲线出现平坦期,平坦硫化时间取决于胶料配方。
对应硫化曲线→过硫化阶段:网络形成的后期,存在着交联的重排,由于此时主要是交联键及键段的热裂解反应,因此胶料的弹力性能显著下降。
-。
橡胶中dcp硫化体系的作用_解释说明以及概述

橡胶中dcp硫化体系的作用解释说明以及概述1. 引言1.1 概述橡胶作为一种重要的材料,在工程和日常生活中有广泛的应用。
为了提高橡胶的性能和满足特定需求,研究人员一直在寻找适当的添加剂和新的硫化体系。
dcp (二苯基二异丙基氧化锆)硫化体系是近年来在橡胶领域中受到广泛关注的一种。
它被证明可以有效改善橡胶的物理性能、耐热性和耐老化性等方面。
1.2 文章结构本文将对橡胶中dcp硫化体系的作用进行详细解释和说明。
首先,我们将简要介绍dcp硫化体系的基本原理和作用机理。
然后,我们将论述该硫化体系在橡胶材料中的具体应用,并分析其对橡胶物理性能改善的影响。
最后,我们将探讨该硫化体系对橡胶耐热性、耐老化性等方面的影响,并总结其在橡胶领域中的作用和意义。
1.3 目的本文旨在全面了解并解释橡胶中dcp硫化体系的作用,并阐述其在橡胶领域中的应用前景和发展方向。
通过对该硫化体系的深入研究,我们可以更好地理解它对橡胶性能的影响,为橡胶工业提供技术支持和指导。
同时,通过展望未来的研究方向和应用前景,我们可以为相关领域的科学家和工程师提供一些建议和启示。
2. 橡胶中dcp硫化体系的作用2.1 dcp硫化体系简介橡胶是一种重要的弹性材料,用于制造各种制品,例如轮胎、密封件和鞋底等。
而硫化是橡胶加工中常用的一种方法,其中dcp(二氧化二己基三苯基膦硫酸钼)是一种广泛使用的硫化剂。
dcp硫化体系由dcp硫化剂及其辅助物质组成,能够在适当的温度和时间下促使橡胶分子间形成交联结构,从而提高橡胶制品的物理性能。
2.2 dcp硫化体系的作用机制dcp硫化剂在橡胶中起到催化剂的作用。
它能够通过与橡胶中的双键进行反应,将双键之间形成交联结构。
当dcp加入到橡胶中后,在适当的温度下发生热分解,生成自由基,并与橡胶中存在的双键进行反应。
这些自由基会引发链式反应,将相邻分子连接起来形成交联网状结构,从而增加了橡胶材料的强度和硬度。
此外,dcp硫化剂还可以通过氧化作用,将部分橡胶链上的疏松结构形成更为紧密的网络结构,从而提高橡胶制品的耐磨性、耐油性和耐老化性。
- 1、下载文档前请自行甄别文档内容的完整性,平台不提供额外的编辑、内容补充、找答案等附加服务。
- 2、"仅部分预览"的文档,不可在线预览部分如存在完整性等问题,可反馈申请退款(可完整预览的文档不适用该条件!)。
- 3、如文档侵犯您的权益,请联系客服反馈,我们会尽快为您处理(人工客服工作时间:9:00-18:30)。
硫化是胶料通过生胶分子间交联,形成三维网络结构,制备硫化胶的基本过程。
不同的硫化体系适用于不同的生胶。
尽管阐述弹性体硫化的文献数量众多,但有关橡胶硫化的研究仍在深入持久地进行。
研究的目的主要是改进硫化胶的力学性能及其它性能,简化及完善工艺过程,降低硫化时有害物质的释放等等。
为了评估近年来的有关硫化的新的见解,首先有针对性地简述当前使用的硫化体系。
传统的硫化体系一、不饱和橡胶通常使用如下几类硫化体系。
1.以硫黄,有机二硫化物及多硫化物、噻唑类、二苯胍类,氧化锌及硬脂酸为主的硫化剂。
这是最通用的硫化体系。
但所制得的硫化胶的耐热氧老化性能不高。
2.烷基酚醛树脂。
3.多卤化物(如用于聚丁二烯橡胶、丁苯橡胶及丁腈橡胶的六氯乙烷)、六氯-对二甲苯。
4.双官能试剂[如醌类、二胺类、偶氮及苯基偶氮衍生物(用于丁基橡胶及乙丙橡胶)等]。
5.双马来酰亚胺,双丙烯酸酯。
两价金属的丙烯酸酯(甲基丙烯酸酯)、预聚醚丙烯酸酯。
6.用于硫化饱和橡胶的有机过氧化物。
二、饱和橡胶硫化不同种类的饱和橡胶时,可使用不同的硫化体系。
例如,硫化三元乙丙橡胶时,使用有机过氧化物与不饱和交联试剂,如三烯丙基异氰脲酸酯(硫化剂TAIC)。
三、硫化硅橡胶时也可使用有机过氧化物。
乙烯基硅橡胶硫化时可在催化剂(Pt)参与条件下进行。
四、含卤原子橡胶或含功能性基团的橡胶聚氯丁二烯橡胶、氯磺化聚乙烯及氯化丁基橡胶等是最常用的含氯橡胶。
硫化氯丁橡胶通常采用ZnO与MgO的并用物,以乙撑硫脲(NA-22)、二硫化秋兰姆、二-邻-甲苯基二胍(促进剂BG)及硫黄作硫化促进剂。
五、硫化氯磺化聚乙烯时可使用如下硫化体系。
1.氧化铝、氧化铅和氧化镁的并用物,以及氧化镁和季戊四醇酯,以四硫化双五甲撑秋兰姆(促进剂TRA)及促进剂DM作硫化促进剂。
2.六次甲基四胺与己二酸及癸二酸盐及氧化镁。
3.有机胺与环氧化物作用的产物。
六、以下体系可用于氯化丁基橡胶硫化:1.氧化锌与硬脂酸、氧化镁、秋兰姆及苯并噻唑二硫化物等的并用物;2.乙烯基二硫脲与氧化锌及氧化镁的并用物。
3.多羟基甲基酚醛树脂与氧化锌的并用物。
4.二烷基二硫代氨基甲酸锌。
5.羟基芳香化物(间苯二酚、氢醌等)(在室温下)。
七、硫化羧基橡胶时常使用金属氧化物及过氧化物、多元醇、二元胺及多胺,环氧化物、二异氰酸酯及聚异氰酸酯等。
八、硫化含胺基的橡胶时常用添加氧化锌的硫黄硫化体系、含卤有机物及环氧树脂等。
九、硫化含腈基的橡胶时常用氧化物(如MnO2、Sb2O5)硫化物(如CuS)以及添加硫黄的多胺(对于丙烯酸酯橡胶)。
在无硫化剂时,由于聚合物中具有反应能力的官能团之间发生反应。
在弹性体中也有可能生成化学交联键网络。
例如,在高温下,聚氯乙烯及丁腈橡胶并用胶中即有此种情况发生。
非传统硫化体系近十年来,主要研究内容是硫化过程本身及硫化胶制品在使用过程中的生态问题以及完善硫化工艺、降低焦烧和返原倾向、推广冷硫化等等。
对防止硫化剂特别是硫黄在成品中的喷霜也给予了一定的关注。
通过选择适宜的硫化体系及硫化条件在改进硫化胶及制品性能方面也取得了一些成就。
降低使用硫化体系时的生态危害不饱和橡胶的硫化体系中通常都含有硫黄,故目前正在采取一系列措施,以防止硫黄在称量等过程中的飞扬,如可采用造粒工艺。
通常采用硫黄与二环戊二烯、苯乙烯及其低聚物的共聚物来消除硫黄喷霜。
也有人曾建议过用硫黄与高分子树脂的并用物、硫黄在环烃油中的溶解液、含硫低聚丁二烯、硫黄与5-乙烯-双环[9.2.1]庚-2-烯及四氢化茚等的反应产物。
向硫黄硫化胶中添加N-三氯甲基次磺基对氨基苯磺酸盐可减少喷霜。
乙烯与α-烯烃的共聚物、α-烯烃橡胶以及乙丙橡胶可用含Cl、S或SO2基的双马来酰亚胺衍生物硫化,而不用硫黄硫化。
亚硝基胺的生态危害性是众所周知的。
因此,以二胺为基础的促进剂因会生成挥发性亚硝基胺而具有危险性。
危险性最小的是二苄基二硫代氨基甲酸锌及二硫化二苄基秋兰姆。
次磺酰胺类以及二硫化四甲基秋兰姆及其它低烷基秋兰姆类促进剂可限量(0.4-0.5%)使用。
对于轮胎胶料则常使用促进剂DZ(N,N’-二环已基-2-苯并噻唑次磺酰胺),也可采用二硫化与四苄基秋兰姆双马来酰亚胺的并用物。
不含氮原子的黄原酸衍生物与少量常用促进剂的并用物不会生成亚硝基胺。
以二烷基(C1-5)氧硫磷酰基三硫化物与N-三氯甲基次磺酰基苯基次磺酰胺和二硫化苯并噻唑(促进剂DM)以及二苄基二硫代氨基甲酸锌等的并用物作促进剂也不会生成亚硝基胺。
使用维生素C及维生素E添加剂可降低通用硫化体系中亚硝基胺的生成量。
从生态观点来看,用以1,1’-二硫代双(4-甲基哌嗪)及其它哌嗪的衍生物为主的促进剂取代胺类促进剂是适宜的,将秋兰姆和脲类并用,以及使用含2-15%多噻唑、15-50%双马来酰亚胺,15-45%次磺酰胺及20-55%硫黄的混合物均可减少亚硝基胺的生成。
建议用烷基二硫代磷酸盐作为三元乙丙橡胶的硫化促进剂,此时不会生成亚硝基胺。
用氨或正胺对填料与ZnO进行预处理可阻止生成亚硝基胺。
往聚丁二烯导丁苯橡胶的硫黄硫化并用胶料中加入少量CaO、Ca(OH)2及Ba(OH)2也能阻止生成亚硝基胺。
改进硫化胶的工艺及使用性能近年来,用以改进硫化胶,特别是不饱和橡胶性能的硫化体系的品种显着增加。
不饱和橡胶新型硫化剂建议用邻苯二甲酸及偏苯三酸的Ca、Mg、Zn及其它两价金属盐来硫化羧基橡胶。
含此类金属盐的胶料抗焦烧,其硫化胶的强度可达18MPa。
以Fe(OH)3作促进剂用三乙醇胺可硫化丁二烯、丙烯腈及异丙氧基羰基甲基丙烯酸甲酯的共聚物。
所得硫化胶用于制备耐油和耐苯的制品。
用多功能乙烯酯可使丁腈橡胶交联。
用过氧化物硫化这些橡胶时,常用丙烯酸或二甲基丙烯酸苯酯和萘酯作共硫化剂,所得硫化胶具有耐热性及高耐磨性。
常用季戊四醇四乙烯酯来降低硫化温度。
建议将以乙烯硫脲为基础的新型硫化剂用于硫化丁腈橡胶、丁基橡胶、氯丁橡胶及三元乙丙橡胶。
使用低分子量的酚醛树脂硫化丁腈橡胶可生成互穿网络,从而起到增强作用。
醌单肟(Na、Zn、Al)盐及对醌二肟(Na、Zn)盐可用于硫化顺丁橡胶。
常用乙烯基三甲氧基硅烷来硫化二元乙丙橡胶及三元乙丙橡胶。
在过氧化酚醛低聚物存在下的过氧化物硫化可改进三元乙丙胶的高温性能及物理机械性能。
也可用含过氧基的环氧齐聚物硫化三元乙丙橡胶;此时,炭黑胶料的粘度下降,硫化胶的强度性能得到改善。
烷氧端基聚硅氧烷常用于聚丙烯与三元乙丙共混胶的动态硫化,所得热塑性弹性体具有高耐热性。
新型硫化促进剂羧基丁腈橡胶的硫化是采用硫代磷酸二硫化物与促进剂DM或N-氧化二乙烯-2-苯并噻唑次磺胺并用物。
二甲苯与蒽的二硝基氧化衍生物可将硫化速率提高1-3倍,而硫化温度仅为60-80℃。
(原需140-160℃)所得硫化胶可耐热氧老化。
为了加速羟基丁腈橡胶的硫化,也有使用双(二异丙基)硫代磷酸三硫化物的,可制得增高网络密度的硫化胶。
使用含芳香取代基或双键的苯并咪唑衍生物不仅可以提高丁腈橡胶的耐、热氧老化性能,而且可提高强度及耐动态疲劳性能。
此外还常往丁腈胶料中加入与杂环有共轭双键的苯并咪唑衍生物,从而使橡胶的强度及耐热氧老化性能提高,动态性能得到改善。
往丁腈橡胶CKH-26中加入二磷或多磷酰氢化物,往丁腈橡胶CKH-18中加入有机二硫代磷酸酐可加速硫化并使硫化胶保持稳定。
由六次甲基二胺与硫黄缩聚可制得用于异戊橡胶及丁二烯橡胶的新型聚合物硫化促进剂。
此种硫化促进剂具有宽域的硫化平坦区,可使硫化胶的物理机械性能得到改善。
异戊二烯橡胶CKH-3及丁腈橡胶CKH-26常采用烷基三乙基氨溴化物作共硫化剂,此时,CKH-26硫化胶的强度可从4.5MPa提高到6.8MPa。
建议采用以脂肪芳香酸和脂肪族酸或醇为基础的酯类和2-(2’,4’-二硝基苯基)硫代苯并噻唑新型硫化剂,其分解诱导期在160℃时为140-165min。
为了提高不饱和橡胶的硫化速率,常常添加第二促进剂,如丁醛与苯胺的缩合物等。
硫化天然橡胶与丁苯橡胶的并用胶时,在使用秋兰姆的同时,还并用1-苯基-2,4-二缩二脲。
可用2-(2,4-二硝基苯基)硫醇基苯并噻唑与第二促进剂硫化天然橡胶。
所得硫化胶的性能与用2-苯并噻唑-N-硫代码啉硫化的相似为了提高天然橡胶的耐疲劳寿命常往该促进剂中加入酰胺基磷酸酯低聚物。
在1,3-丁二烯和2-乙烯吡啶共聚物存在条件下,天然橡胶的硫化速率加快,同时,硫化胶的强度增高。
丁二烯橡胶和丁腈橡胶的硫化速率也可用此种方法提高,且焦烧倾向降低。
往三元乙丙橡胶中加入水杨基亚胺铜及苯胺的衍生物可使硫化速率提高0.2-0.5倍。
同时,硫化胶强度提高,耐多次形变疲劳性能及耐热性改善。
使用脂肪酸的磷酸盐化烷基酰胺可提高丁苯硫化胶的强度(1倍)。
如在硫黄中加入二烷基二硫代磷酸钠及多季铵盐,则在硫化异戊橡胶时有协同效应,硫化胶强度达23.6MPa。
天然橡胶和丁苯橡胶的新型硫化剂是2-间二氮苯次磺酰胺。
与一般次磷酰胺促进剂相比,它们可使硫化速率提高得更快、硫化程度更高及诱导期更长。
丁基橡胶在热水中的“冷”硫化除使用二枯基过氧化物外,还可添加醌醚。
在60℃时硫化时间为9d,在95℃下则分别为12h和3h。
降低焦烧速率的新方法近十年来,为了降低焦烧速率,使用了许多新型化合物。
四苄基二硫化秋兰姆与次磺酰胺的并用物以及2-吡嗪次磺酰胺对大多数用硫黄硫化的橡胶有效。
对于丁苯橡胶与丁二烯橡胶的并用胶,建议使用四甲基异丁基一硫化秋兰姆。
对丁腈橡胶与一元乙丙橡胶的并用胶建议使用二甲基丙烯酸锌。
丁腈橡胶和异戊橡胶用过氧化物硫化时使用酚噻嗪极其有效,而硫化三元乙丙橡胶时有效的是酚噻嗪及2,6-二-特丁基-甲酚。
降低返原性建议使用二乙基磷酸的衍生物来降低返原性。
此外,还可使用六次甲基双(硫代硫酸)钠、五氯-β-羟基乙基二硫化物、双(柠檬酰胺)与三十碳六烯的并用物、二苯基二硫代磷酸盐(Ni、Sn、Zn)、1-苯基-及1,5-二苯基-2,4-二硫脲与N-环己基苯并噻唑次磺酰胺的并用物等。
使用含0.1%至0.25%的双(2,5-多硫代-1,3,4-噻二嗪、0.5%至0.3%双(马来酰亚胺)及0.5%至3%次磺酸胺的并用物也很有效。
使用含硫黄及烯烃基的烷氧端基硅烷硫化剂则没有反原现象。
使用脂肪酸锌和芳香酸锌盐的并用物不仅可以减轻返原,而且还可以改进硫化胶的动态性能。
加入1,3双(柠檬亚氨甲基)苯不仅可以减轻返原,同时还可提高硫化胶的抗撕裂性及强度。
使用硫黄硫化活性剂的新途径通常将ZnO(3-5质量份)与硬脂酸(1份)加以组合作为硫黄硫化的活性剂。
目前使用各种方法来降低氧化锌的用量,甚至取代氧化锌。
例如,将促进剂M与促进剂TT和ZnO、硬脂酸的并用物加热至100-105℃可使橡胶中ZnO含量降低至2质量份。