ISO9001-2015不良品处理规范
ISO9001:2015不合格品控制程序

发放部门:□总经理□管理者代表□技术部□品质部□生产部□工程部□采购部□销售部□仓库□财务部□行政人事部□其它(如有请详细填写:)1.目的对不合格品进行严格控制,以防止其非预期使用,确保不合格品不转序、不出公司。
2.范围适用于采购产品、半成品和成品不合格品的控制和处置。
3.职责3.1品质部是不合格品的判定和管理部门,负责对不合格品进行记录、标识、并对一般不合格品进行处置。
3.2重大不合格品由总经理进行评审和处置。
3.3品质部负责不合格品隔离、返修,按评审意见,采取措施,消除已发现的不合格。
4.工作程序4.1不合格品的类型4.1.1重大不合格当出现以下情况之一的为重大不合格:1)成品加工中出现一项产品性能指标不达标。
2)上级归口部门检测中心检测的“检测报告”中综合判定结论为不合格的。
3)产品不合格,由顾客抱怨或退货的。
4.1.2一般不合格成品加工中外观不良的不合格品为一般不合格品。
4.2本公司对不合格品评审后,有以下处置办法:返工或返修、让步接收(需经顾客协商同意)、拒收或报废。
4.3不合格的评审和处置的权限及办法:4.3.1一般不合格由品质部直接进行处置。
并要责任者查找原因,采取措施,防止再发生。
4.3.2重大不合格由总经理评审和处置,组织有关人员,召开质量分析会,填写“不合格品评审单”找出责任人,分析原因,采取有效措施,防止不合格的再发生。
4.4采购产品不合格的控制4.4.1经检验发现供方提供的原辅材料、外购件等采购产品不合格,由检验员记录、标识、隔离、填写“不合格品评审单”。
4.4.2运营部采购与供方联系,将不合格品进行退货处理。
4.5产品实现过程中出现不合格的控制4.5.1检验员发现产品实现过程中出现的不合格品,作好记录标识、隔离,填写“不合格品评审单”,并按本程序4.3条款进行评审和处理。
4.5.2不合格返工、返修后应重新进行检测,并应按规定作好记录。
4.6成品不合格的控制成品检验员发现的不合格品,作好记录、标识、隔离、填写“不合格品评审单”,并按本程序4.3条款进行评审和处置。
ISO9001-2015异常品处理程序

异常品处理程序(ISO9001:2015)1、目的对于的异常做适当的处理,防止异常品流出以及异常再度发生。
2、适用范围发现的所有可以直接或间接影响产品的异常均适用。
3、定义5M1E:人(Man)、机(Machine)、料(Material)、方法(Method)、测量(Measurement)、环境(Environment)异常:所有可能引发产品不良的5M1E的不当因素,都被视为异常4、工作流程4.1 异常发生的时机4.1.1 作业过程中发现作业内容或结果与平时不一样;4.1.2 设备装置或工具的状态与平时不一样;4.1.3 从未发生的不良;4.1.4 设备、治具使用时与平时不一样;4.1.5 同样的不良持续发生时;4.1.6 作业者的操作方法与作业指导书不一样时;4.1.7 5M1E发生变化时4.2 异常发生的处理流程4.2.1 当本规定中4.1的异常发生时,发现者立即向上级班、组长报告,班、组长需要在发现半小时内进行解决。
若班、组长无法解决,需填写“异常报告”,由品质管理部组织各部门进行调查、分析并提出改善对策。
具体流程按照“附件一异常处理流程”处理;4.2.2 当无法解决或异常品已经出货时,由营业部门通知客户协商解决。
4.3 各类异常的管理4.3.1 部品异常时,应立即查清异常品的数量,并记录LOT号,同时将异常品与正常品作区分,妥善保留等待处理;4.3.2 材料异常时退回仓库不良品暂放,并做好标识,并由相关品质人员与相关供应商联络;4.3.3 其他异常直接按照“异常处理流程”处理。
5、相关表单《异常报告单》异常的处理流程资料存档生产停止发现部门提出品质管理部、生产管理部、生产部工厂长。
ISO9001-2015不合格品处理程序(中英文)

不合格品处理程序Management of Nonconforming Product(ISO9001:2015)1.0目的Purpose:本程序对不合格品的标识、隔离、评估、处置、记录提供指引。
This procedure provides the instructions for the identification, quarantine, evaluation, disposition,documentation of non-conformance associated with incoming materials, in-process incoming materials, semi-product, finished product. .2.0范围Scope:适用于本厂所有不合格来料,半成品及成品。
Apply to all non-conforming incoming materials, semi-products and finished products.3.0定义Definition:3.1DXC: DXC的简称:DXC is short for DXC.3.2UAI:特采,也称让步接受。
UAI is short for use as it is, also calling concession.3.3PM/PA: 项目经理/项目助理 Program manager / Program Assistant.3.4QE: 品质工程师 Quality Engineer3.5ME: 制程工程师 Manufacturing Engineer3.6不合格品:不符合既定的品质标准/要求或客户要求的所有来料、半成品、成品。
Nonconforming Product: All incoming materials, WIP, finished products arenon-compliant with established quality standard/requirements or customers’.3.7可疑物品/物料:检验或试验状态标识不明确或没有标识,或储存超过保存期限或由于包装受损等原因可能引起品质变异或降低的物料/半成品/成品。
ISO9001-2015进料检验不合格品处理程序

进料检验不合格品处理程序(ISO9001:2015)1目的制定组件进料检验发现的不合格品的处理办法,确保材料出现不合格时能有效及时的处理。
2范围本办法适用于公司IQC检验范围内所有不合格物料的处理。
3相关文件3.1不合格品控制程序4定义4.1不合格品:所有来料检验发现的不符合质量标准的原物料。
4.2退/换货:将不合格物料全部退回供应商或部分与供应商更换。
4.3特采:不合格物料因客户、生产需求急迫,客户或销售部代表客户同意授权,或投入后不影响产品功能、构造机能、特殊外观要求及应用功能性,不造成人身安全,可满足最终客户使用品质的不合格品做特殊接收的状态,等同让步接收。
4.4厂内挑选:经过协商,由公司相关部门代为厂商全检不合格品,挑选合格品投入生产,不合格品由采购部负责办理退/换货,并由厂商赔偿工时损失。
4.5供应商挑选:由供应商负责按照我司要求对不合格品进行全检(可派人员来我司进行挑选等)。
5职责5.1质量部(IQC):物料的检验及物料不合格的及时反馈。
5.2质量部(PQC):针对特采物料上线使用情况进行跟踪及数据统计。
5.3SQE:不合格物料的评审,联系供应商对已发现的不合格物料进行确认及推动改善。
5.4采购部:不合格物料的评审,联系供应商对不合格物料进行处理。
5.5PMC:物料安全库存的确认;及特采物料上线使用前的信息发布。
5.6工程部:负责对材料的安全性、功能性使用的影响进行评审判定,必要时实施相关实验。
5.7生产部:不合格物料的评审,在线不合格物料的及时提报,配合做好厂内挑选工作,确保合格品投入生产。
5.8仓库:不合格物料的分类存放。
5.9质量部:负责对不合格材料作出最终判定;6环境满足客户要求,符合行业标准7职业健康安全满足客户要求,符合行业标准8管理内容8.1特采原则8.1.1对产品的使用,确定安全性、公害性及功能性的顾虑原则,不致产生客户抱怨事件发生时。
8.1.2对产品功能及产品价值的影响很微小时。
ISO9001-2015废弃品处理规范
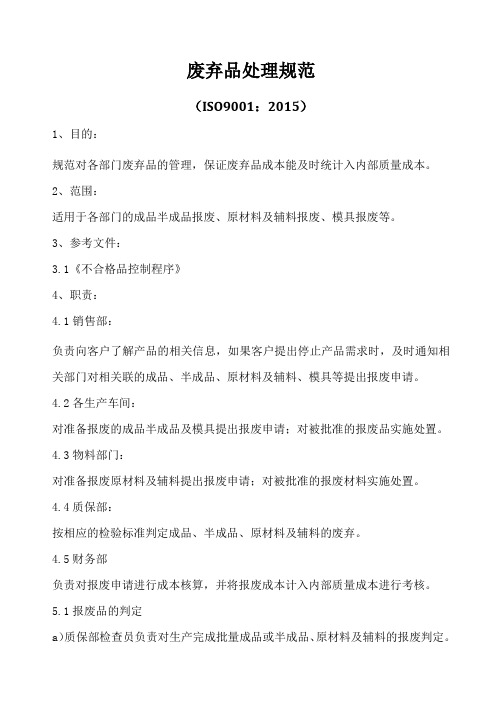
废弃品处理规范(ISO9001:2015)1、目的:规范对各部门废弃品的管理,保证废弃品成本能及时统计入内部质量成本。
2、范围:适用于各部门的成品半成品报废、原材料及辅料报废、模具报废等。
3、参考文件:3.1《不合格品控制程序》4、职责:4.1销售部:负责向客户了解产品的相关信息,如果客户提出停止产品需求时,及时通知相关部门对相关联的成品、半成品、原材料及辅料、模具等提出报废申请。
4.2各生产车间:对准备报废的成品半成品及模具提出报废申请;对被批准的报废品实施处置。
4.3物料部门:对准备报废原材料及辅料提出报废申请;对被批准的报废材料实施处置。
4.4质保部:按相应的检验标准判定成品、半成品、原材料及辅料的废弃。
4.5财务部负责对报废申请进行成本核算,并将报废成本计入内部质量成本进行考核。
5.1报废品的判定a)质保部检查员负责对生产完成批量成品或半成品、原材料及辅料的报废判定。
b)生产部门负责本部门内生产过程中产品及所使用模具的报废判定。
5.2报废申请提出5.2.1批量成品或半成品报废经检查员判定NG,并且无法进行特采、返修、分选等处置的批量产品,由责任部门填写MP007-05《报废申请单》,统计申请报废产品名称及数量。
5.2.2生产过程中产品的报废生产过程中操作者自检发现的NG品,且无法进行特采、返修、分选等处置时,需由生产部门填写《报废申请单》,申请报废。
5.2.3修理、调试过程中产品的报废a)冲压调试、修理模具时连续生产的数量超过1K时,需填写报废申请,不得自行废弃。
b)热处理调试设备时使用的产品数量超过2K时,需填写报废申请,不得自行废弃。
5.2.4原材料及辅料的报废经检查员判定NG,且不属于供应商原因,无法进行退货、特采、分选等处置的原材料及辅料,需由物料部填写《报废申请单》申请报废。
5.2.5模具报废冲压车间提出模具的《报废申请单》。
5.2.6各部门每周一对前一周需要申请报废的成品半成品、原材料及辅料、模具等提出《报废申请单》,如遇休息日可顺延。
ISO9001-2015异常处理规范

异常处理规范(ISO9001:2015)1.目的为了减少异常情况的发生,为了能更规范的处理异常,从而减少异常的处理时间而制订本规定。
2.适用范围本规定适用于全公司经营活动中出现所有异常情况,并填写各相关记录的要求。
3.定义和规定:3.1定义:异常就是指与正常不一样、与普通状态不一样;异常为不符合规定的情况,质量异常为连续发生小批量不符合规定产品。
3.2异常的分类:生产异常、品质异常、自然灾害及其他异常。
3.2.1生产异常:(1).生产计划的异常:因生产计划临时变更或安排失误等导致的异常(2).物料计划的异常:因物料供应不及(断料),物料品质问题等导致的异常.(3).设计工艺异常:因产品设计或其他技术问题而导致的生产异常(4).设备异常::因设备故障、设备不足、工装器具不足或水,电、气等原因而导致的异常(5).人员不足:因公司产能扩大或减员所致的人力不足造成的生产异常。
3.2.2品质异常:(1).原材料的异常:在材料进厂时发现的异常(2).制品的异常:产品生产中发现的异常(3).成品的异常:产品全工序完成后发现的异常3.2.3自然灾害洪涝、地震等不可抗拒的自然灾害导致的异常:3.3异常造成的原因及预防措施3.3.1生产计划的异常原因:计划排错、计划漏下、计划量与产能不匹配措施:定期对计划表进行查看、核对;要看懂安排表,预知生产何时比较紧张,提前做跟踪。
3.3.2物料计划的异常原因:外购/协没按时回来、原材材没到措施:提前跟进订单,多提醒相应的采购3.3.3设计工艺的异常原因:业务不够专业,建议给客户错的工艺;工艺中较难克服的图案措施:提升业务专业知识,掌握相应设计软件的基础操作;对自己无法判断的订单,发给工艺组帮忙确认。
3.3.4设备异常:原因:偶发性的设备故障,与机台保养、矫正、维护有关措施:定期做好机台保养;规范机台操作。
4.作业程序4.1如果生产出现设备异常造成阻产,当班班长应判断故障的严重性,如果事态严重则马上通知设备员,或者20分钟内仍无法排除故障的也应马上通知设备部。
ISO9001-2015报废品管理规范A0

报废品管理规范(ISO9001:2015)1、目的为规范报废品的申报程序,明确各相关部门在报废处置当中的权责范围,有效控制生产性报废物品的流向,使公司财产的安全得到保障,特制作本规定.2、适用范围本规定适合公司的生产性原材料,半成品,生产成品的报废.非生产性的物品报废将根据公司规定另行处理.3、用语定义报废:为防止不良品非预期使用所采取的措施.报废品:指经相关部门人员判定的不能用于预期使用目的的物品.4、权责4.1 仓管部:报废品的区分存放;报废品处理申请单的填写;报废品处理时的发放.4.2 计调部:负责报废申请单的数量确认;报废半成品,产成品分解后良品入库数量的确认;并对报废的全过程进行跟踪.4.3 维修组/生产:负责报废半成品,产成品的分解;分解后损品的废弃,良品的入库等.4.4 品质部:负责报废物品的品质再确认;半成品,产成品分解后良品再入库前的品质确认.4.5 财务部:报废申请单中的报废品金额的计算,记入.4.6 厂办/工程:负责人对报废申请单的审查.4.7 生产副总:报废申请的最终核准.5、规定5.1 报废品来源5.1.1 生产部:生产性物料制程不良的损品(退仓单据上需注明不良原因).5.1.2 货仓部:因我司工程设计、工程更改或制程损失造成一些呆滞物料,已经技术判定不可使用的物料、半成品、或成品确定的需公司内部报废的生产性物料,超过规定期限经品质部确定不可使用的呆滞物料。
5.1.3 工程部:样机解析的损品.5.1.4 品管部:检验、测试、各项实验时领出的原材料、半成品、产成品、在检验、测试、实验完后发生的损品.5.1.5 维修组:返修品的废品;返修领用原材料;返修后的损品.5.1.6 其它:相关部门领出生产性原材料,半成品,产成品后所产生的损品.以上所产生的报废品,除生产部,货仓部的物料需在不良品仓经品质部再确认转入报废品仓外,其它部门的损品可直接入报废品仓(注,开发部领用的原材料为开发新产品使用时,因做成的产成品含技术秘密,其产品破坏后的损品,由开发部自行处理).5.2 报废品申请部门,频次,单据5.2.1 申请部门:计调部或仓库.5.2.2 申请频次:一般要求1次/周(根据产品的实际情况可以每批申请一次),具体根据实际情况安排;另外每月5日前仓库提供上月的报废品清单.5.2.3 申请单据:报废申请单.5.3 报废品审批5.3.1 报废品的审批单据的审核,确认,批准等根据《报废申请单》中内容.5.3.2 对报废品的审批,需经品质部、工程部、计划调度部的负责人会签确认,经生产最高主管及副总经理审核方可生效。
ISO9001-2015不合格品下线处理规范A0

不合格品下线处理规范(ISO9001:2015)1.0目的规范公司内部所有的不合格品(包括隔离品)处理流程,防止不合格品被非预期的使用或交付,合理利用不合格品,降低成本。
2.0范围:公司流水线日常不合格品产生的处理由于原材料原因导致的生产半成品,成品的处理已经在仓库或在生产线的由于工程更改,客户抱怨的需要隔离,返工的成品,半成品已经在仓库或在生产线的由于项目终止需要清理,隔离处置的成品,半成品,原材料客户退回的不良品在仓库贮存时间超过规定周期的3.0责任生产部:负责日常生产过程中不合格品的发现,标识,隔离,反馈,停线,临时解决措施,及返工返修的实施。
改制班:负责组织对日常不合格品进行分解或直接返工。
生产主管:负责监督停线的实施项目部:负责参与评审不合格处置方案工程部:负责停线后分析,参与评审不合格处置方案生产部长:负责停线批准和开线批准及协调机修工程师/主管:负责设备原因引起的停线的原因分析和改进质量部:负责不合格品的确认,标识和返工的监督及返工后的验证和检验。
巡检员:负责对发现不合格品数量统计,标识,开具不合格品报告或停产通知及监督返工过程质量工程师:对停线原因进行分析并提出改进方案质量部长:负责停线批准和开线批准、批量返工的批准及协调物流计划员:负责100PCS以上的批量不良返工的生产计划安排。
IQC:负责对改制后的物料的检验和确认仓库:对改制物料的入库接收和发放及隔离不合格品的管理总经理:批量不合格品的停线和开线批准及协调和支持4.0定义日常不合格品:在生产线发生的,由于原材料,工艺,操作,设备等原因产生的非批量不符合客户要求的半成品和成品。
批量不合格品:生产线制造过程中发现的在同一失效模式的,所涉及到的数量超过100PCS的成品或半成品称为批量不合格品。
料废:原材料不良而造成的不合格品报废。
工废:制造过程不良而造成的不合格品报废。
5.0过程:本程序文件包括以下程序模块:1)生产线连续不合格停线处理流程;2)掉落品、设备模具调试状态下生产的产品、不合格原材料和成品、半成品处理流程;3)返工流程;4)报废处理流程;5)改制流程。
- 1、下载文档前请自行甄别文档内容的完整性,平台不提供额外的编辑、内容补充、找答案等附加服务。
- 2、"仅部分预览"的文档,不可在线预览部分如存在完整性等问题,可反馈申请退款(可完整预览的文档不适用该条件!)。
- 3、如文档侵犯您的权益,请联系客服反馈,我们会尽快为您处理(人工客服工作时间:9:00-18:30)。
不良品处理规范
(ISO9001:2015)
1.目的Intent
确保不合格品的返工、返修、报废的过程得到有效的控制,保证产品符合标准和减少损失。
2. 适用范围Application
适用于客户退货不合格品以及生产过程产生的不符合质量要求的零部件/半成品/成品的返工/返修作业(外包产品参照外协加工的方式处理)。
包括以下三种情况:
2.1客户退回需返工返修的产品
2.2 成品库中需返工返修的产品
2.3生产过程中的半成品,经品质判定不符合品质标准
3. 定义及术语Definition and term
3.1 返修:使不合格产品满足预期用途而对其采取的措施;
3.2 返工:使不合格产品达到规定要求而对其采取的措施;
3.3 报废:为避免不合格产品原有的预期用途而对其采取的措施。
4.职责与权限Function and Purview
4.1 质量部
负责组织不合格品产生的原因调查,下达<返工返修通知单>,协同生产技术部
制订返工返修方案,对返工返修过程产品质量进行监控,以及返工后零件的质量检查判定,和对后续改善对策的确认。
4.2.生产部
负责<程序记录卡>的记录,不合格品的筛选和返工返修方案的实施,返工返修的产品和区域标识,提出返工返修不合格物料处置申请;返工返修完成后,汇总统计返工返修工时和所耗费物料,报告质量部和财务部。
4.3.生产技术部
负责根据不合格品产生原因和质量标准,制订返工返修方案和<作业指导书>,并跟进方案实施过程。
4.4.物料计划部
负责下达返工返修<生产计划>,主导供应商来料不良的退货和返工返修。
4.5 市场部
负责与客户沟通和协调退货状况,并出具客户退货清单,明确客户处理要求。
4.6 财务部
负责核算返工返修的质量成本。
5.作业内容Operation content
5.1 在制品的返工返修作业
5.1.1 IPQC和IQC在检验过程中,发现在制品未达到品质要求时,检验员首先将不合格批贴上不合格标签进行标识,并在<程序记录卡>上盖不合格品章,开
具<不合格品处理单>,连同不良样品及时交由QE和生产主管确认。
5.1.2 生产主管安排将不合格批及时移入不合格品区域进行隔离。
5.1.3 QE对检验员开具的<不合格品处理单>,组织生产部、模具部和生产技术部进行不合格批的原因分析和不合格品的审理,确定不合格批处理方案(返工/返修/报废/特采)。
5.1.4返工返修
5.1.4.1 生产技术部根据QC开的<返工返修通知单>和质量标准,制订返工返修流程和<作业指导书>。
5.1.4.2物料计划部根据<返工返修通知单>下达不合格批返工返修<生产计划>。
5.1.4.3 按照返工返修流程和<生产计划>实施返工返修:
a.不合格的原因属于内部生产造成,生产部根据<返工返修计划>和<返工返修作业指导书>,填写返工返修<程序记录卡>,组织安排进行返工返修作业。
b.不合格的原因属于供应商造成,SQE负责与供应商确认产品问题点和质量标准,物料计划部根据<返工返修计划>和<返工返修通知单>组织退货。
原则上不允许供应商在SOB现场返工返修。
特殊情况需在SOB返工返修时,由物料计划部组织供应商进行返工返修作业,填写返工返修<程序记录卡>,并交QC检验。
5.1.4.4 质量部根据制订的返工返修方案对返工返修过程进行监控,并根据质量标准进行返工检验,保证返工返修产品满足质量要求。