数控机床宏程序编程技巧实例
数控机床宏程序编程的技巧和实例
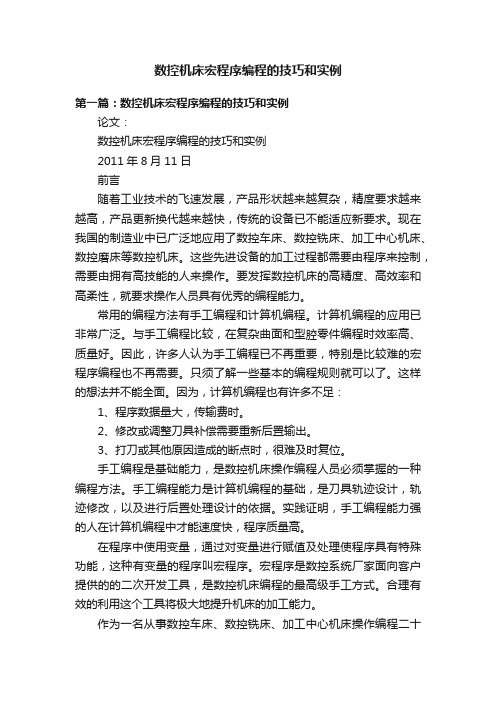
数控机床宏程序编程的技巧和实例第一篇:数控机床宏程序编程的技巧和实例论文:数控机床宏程序编程的技巧和实例2011年8月11日前言随着工业技术的飞速发展,产品形状越来越复杂,精度要求越来越高,产品更新换代越来越快,传统的设备已不能适应新要求。
现在我国的制造业中已广泛地应用了数控车床、数控铣床、加工中心机床、数控磨床等数控机床。
这些先进设备的加工过程都需要由程序来控制,需要由拥有高技能的人来操作。
要发挥数控机床的高精度、高效率和高柔性,就要求操作人员具有优秀的编程能力。
常用的编程方法有手工编程和计算机编程。
计算机编程的应用已非常广泛。
与手工编程比较,在复杂曲面和型腔零件编程时效率高、质量好。
因此,许多人认为手工编程已不再重要,特别是比较难的宏程序编程也不再需要。
只须了解一些基本的编程规则就可以了。
这样的想法并不能全面。
因为,计算机编程也有许多不足:1、程序数据量大,传输费时。
2、修改或调整刀具补偿需要重新后置输出。
3、打刀或其他原因造成的断点时,很难及时复位。
手工编程是基础能力,是数控机床操作编程人员必须掌握的一种编程方法。
手工编程能力是计算机编程的基础,是刀具轨迹设计,轨迹修改,以及进行后置处理设计的依据。
实践证明,手工编程能力强的人在计算机编程中才能速度快,程序质量高。
在程序中使用变量,通过对变量进行赋值及处理使程序具有特殊功能,这种有变量的程序叫宏程序。
宏程序是数控系统厂家面向客户提供的的二次开发工具,是数控机床编程的最高级手工方式。
合理有效的利用这个工具将极大地提升机床的加工能力。
作为一名从事数控车床、数控铣床、加工中心机床操作编程二十多年的技师,在平时的工作中,常常用宏程序来解决生产中的难题,因此对宏程序的编程使用积累了一些经验。
在传授指导徒弟和与同事探讨中,总结了许多学习编制宏程序应注意的要点。
有关宏编程的基础知识在许多书籍中讲过,我们在这里主要通过实例从编制技巧、要点上和大家讨论。
一、非圆曲面类的宏程序的编程技巧1、非圆曲面可以分为两类;(1)、方程曲面,是可以用方程描述其零件轮廓的曲面的。
加工中心宏程序编程实例与技巧方法

加工中心宏程序编程实例与技巧方法宏程序编程实例:假设需要对一个工件进行钻孔、镗孔和攻丝三个工艺步骤。
通过宏程序编程,可以将这三个步骤整合到一个宏程序中,实现自动化加工。
1.钻孔:首先,在宏程序中定义钻孔工艺参数,包括刀具类型、切削速度和进给速度等。
然后,使用钻孔刀具对工件进行钻孔操作,即通过设定好的参数进行切削。
2.镗孔:在钻孔结束后,切换到镗孔刀具。
同样,在宏程序中定义镗孔工艺参数,如刀具类型、切削速度和进给速度等。
使用镗孔刀具对钻孔后的孔进行进一步加工,确保孔的尺寸和精度。
3.攻丝:最后,切换到攻丝刀具。
在宏程序中定义攻丝工艺参数,包括切削速度和进给速度等。
使用攻丝刀具对孔进行攻丝操作,即切削螺纹。
通过将以上三个步骤整合到一个宏程序中,可以实现自动化的加工过程,提高加工效率和精度。
宏程序编程技巧方法:1.合理规划加工顺序:在编写宏程序时,需要根据工艺要求合理规划加工顺序。
例如,在上述实例中,需要先进行钻孔再进行镗孔,否则会对刀具和工件造成损坏。
2.制定合适的工艺参数:在宏程序中定义工艺参数时,需要根据具体的加工材料和刀具选择合适的切削速度、进给速度和切削深度等参数。
合适的工艺参数可以提高加工效率和质量。
3.考虑安全性:在编写宏程序时,需要考虑安全性因素。
例如,在镗孔和攻丝过程中,需要确保刀具和工件没有碰撞的风险,并且在孔的深度和尺寸达到要求之前,需要适时切换到下一个工艺步骤。
4.异常处理:在编写宏程序时,需要考虑到可能出现的异常情况,比如刀具断刀或者刮伤工件表面。
在出现异常情况时,宏程序需要能够自动停止加工并给出相应的报警信息。
5.考虑节约时间和工具寿命:在宏程序编程中,需要尽量减少无效移动和切削,以节约加工时间和延长刀具寿命。
例如,避免多次来回移动或者无效切削,需要根据实际情况来合理设置刀具路径和切削策略。
通过合理规划加工顺序、制定合适的工艺参数、考虑安全性和异常处理以及节约时间和工具寿命等技巧方法,可以更好地编写加工中心宏程序,提高加工效率和精度。
加工中心宏程序编程实例与技巧方法优选文档

加工中心宏程序编程实例与技巧方法优选文档一、编程实例1.实现圆形加工:在加工中心宏程序编程中,圆形加工是比较常见的加工操作。
下面是一个实现圆形加工的编程实例:(1)编程步骤:1)定义圆心坐标和半径;2)使用G90指令将切削模式设置为绝对坐标;3)使用G54指令将工件坐标系设定为程序零点;4)使用G01指令进行直线插补,将刀具移至圆弧起点;5)使用G02或G03指令进行圆弧插补,指定圆心坐标和半径;6)使用M05指令停止主轴转动。
(2)编程样例:```G90G54G01X10Y10G02X20Y10I10J0M05```2.实现孔加工:孔加工是加工中心中常见的操作之一,下面是一个实现孔加工的编程实例:(1)编程步骤:1)定义孔的位置和尺寸;2)使用G90指令将切削模式设置为绝对坐标;3)使用G54指令将工件坐标系设定为程序零点;4)使用G00指令进行快速定位,将刀具移至孔的起始位置;5)使用G01指令进行直线插补,将刀具下移到孔的底部;6)使用G00指令进行快速定位,将刀具抬起。
(2)编程样例:```G90G54G00X20Y20G01Z-10F200G00Z10```二、技巧方法1.合理选择插补指令:在加工中心宏程序编程中,合理选择插补指令可以提高加工效率。
对于直线加工,可以使用G01指令进行直线插补;对于圆弧加工,可以使用G02或G03指令进行圆弧插补。
2.使用子程序:使用子程序可以简化大段的重复代码,在加工中心宏程序编程中尤其有用。
通过使用子程序,可以将常用的加工操作封装为一个子程序,在需要使用时调用即可。
3.合理使用G代码:4.注意安全问题:在加工中心宏程序编程中,安全是最重要的。
编程时应考虑刀具与工件的安全距离,避免发生碰撞等事故。
可以通过设定安全平面、设定限制区域等方式来增加安全性。
总结:加工中心宏程序编程是数控加工的关键环节,掌握加工中心宏程序的编程实例和技巧方法对于提高加工效率和加工精度具有重要意义。
数控车床编程实例详解(30个例子)

车床编程实例一半径编程图半径编程%3110 (主程序程序名)N1 G92 X16 Z1 (设立坐标系,定义对刀点的位置)N2 G37 G00 Z0 M03 (移到子程序起点处、主轴正转)N3 M98 P0003 L6 (调用子程序,并循环6 次)N4 G00 X16 Z1 (返回对刀点)N5 G36 (取消半径编程)N6 M05 (主轴停)N7 M30 (主程序结束并复位)%0003 (子程序名)N1 G01 U-12 F100 (进刀到切削起点处,注意留下后面切削的余量)N2 G03 R8(加工R8 园弧段) N3 R60 (加工R60 园弧段) N4 G02 R40(加工切R40 园弧段) N5 G00 U4 (离开已加工表面)N6 (回到循环起点Z 轴处)N7 G01 F100 (调整每次循环的切削量)N8 M99 (子程序结束,并回到主程序)1直线插补指令编程%3305车床编程实例二图 G01 编程实例N1 G92 X100 Z10 (设立坐标系,定义对刀点的位置)N2 G00 X16 Z2 M03 (移到倒角延长线,Z 轴2mm 处)N3 G01 U10 W-5 F300 (倒 3×45°角)N4 Z-48 (加工Φ26 外圆)N5 U34 W-10 (切第一段锥)N6 U20 Z-73 (切第二段锥)N7 X90 (退刀)N8 G00 X100 Z10 (回对刀点)N9 M05 (主轴停)N10 M30 (主程序结束并复位)圆弧插补指令编程车床编程实例三%3308N1 G92 X40 Z5 (设立坐标系,定义对刀点的位置)N2 M03 S400 (主轴以400r/min 旋转)N3 G00 X0 (到达工件中心)N4 G01 Z0 F60 (工进接触工件毛坯)N5 G03 U24 W-24 R15 (加工R15 圆弧段)N6 G02 X26 Z-31 R5 (加工R5 圆弧段)N7 G01 Z-40 (加工Φ26 外圆)N8 X40 Z5 (回对刀点)N9 M30 (主轴停、主程序结束并复位图 G02/G03 编程实例2倒角指令编程%3310车床编程实例四图倒角编程实例N10 G92 X70 Z10 (设立坐标系,定义对刀点的位置)N20 G00 U-70 W-10 (从编程规划起点,移到工件前端面中心处)N30 G01 U26 C3 F100 (倒3×45°直角)N40 W-22 R3 (倒R3 圆角)N50 U39 W-14 C3 (倒边长为3 等腰直角)N60 W-34 (加工Φ65 外圆)N70 G00 U5 W80 (回到编程规划起点)N80 M30 (主轴停、主程序结束并复位)倒角指令编程%3310车床编程实例五N10 G92 X70 Z10 (设立坐标系,定义对刀点的位置)N20 G00 X0 Z4 (到工件中心)N30 G01 W-4 F100 (工进接触工件)N40 X26 C3 (倒3×45°的直角)N50 Z-21 (加工Φ26 外圆)N60 G02 U30 W-15 R15 RL=3(加工R15 圆弧,并倒边长为4 的直角)N70 G01 Z-70 (加工Φ56 外圆)N80 G00 U10 (退刀,离开工件)N90 X70 Z10 (返回程序起点位置)M30 (主轴停、主程序结束并复位)图倒角编程实例3车床编程实例六圆柱螺纹编程螺纹导程为,δ=,δ '=1mm ,每次吃刀量(直径值)分别为、 mm 、、图螺纹编程实例%3312N1 G92 X50 Z120 (设立坐标系,定义对刀点的位置)N2 M03 S300 (主轴以300r/min 旋转)N3 G00 (到螺纹起点,升速段,吃刀深)N4 G32 Z19 (切削螺纹到螺纹切削终点,降速段1mm)N5 G00 X40 (X 轴方向快退)N6 (Z 轴方向快退到螺纹起点处)N7 (X 轴方向快进到螺纹起点处,吃刀深)N8 G32 Z19 (切削螺纹到螺纹切削终点)N9 G00 X40 (X 轴方向快退)N10 (Z 轴方向快退到螺纹起点处)N11 (X 轴方向快进到螺纹起点处,吃刀深)N12 G32 Z19 (切削螺纹到螺纹切削终点)N13 G00 X40 (X 轴方向快退)N14 (Z 轴方向快退到螺纹起点处)N15 (X 轴方向快进到螺纹起点处,吃刀深)N16 G32 (切削螺纹到螺纹切削终点)N17 G00 X40 (X 轴方向快退)N18 X50 Z120 (回对刀点)N19 M05 (主轴停)N20 M30 (主程序结束并复位)4恒线速度功能编程%3314车床编程实例七图恒线速度编程实例N1 G92 X40 Z5 (设立坐标系,定义对刀点的位置)N2 M03 S400 (主轴以400r/min 旋转)N3 G96 S80 (恒线速度有效,线速度为80m/min)N4 G00 X0 (刀到中心,转速升高,直到主轴到最大限速)N5 G01 Z0 F60 (工进接触工件)N6 G03 U24 W-24 R15 (加工R15 圆弧段)N7 G02 X26 Z-31 R5 (加工R5 圆弧段)N8 G01 Z-40 (加工Φ26 外圆)N9 X40 Z5 (回对刀点)N10 G97 S300 (取消恒线速度功能,设定主轴按300r/min 旋转)N11 M30 (主轴停、主程序结束并复位)车床编程实例八%3317M03 S400 (主轴以400r/min 旋转)G91 G80 X-10 Z-33 F100(加工第一次循环,吃刀深3mm)X-13 Z-33(加工第二次循环,吃刀深3mm)X-16 Z-33(加工第三次循环,吃刀深3mm)M30 (主轴停、主程序结束并复位)图 G80 切削循环编程实例5车床编程实例九G81 指令编程(点画线代表毛坯)图G81 切削循环编程实例%3320N1 G54 G90 G00 X60 Z45 M03 (选定坐标系,主轴正转,到循环起点)N2 G81 X25 F100 (加工第一次循环,吃刀深2mm)N3 X25 (每次吃刀均为2mm,)N4 X25 (每次切削起点位,距工件外圆面5mm,故K 值为)N5 X25 (加工第四次循环,吃刀深2mm)N6 M05 (主轴停)N7 M30 (主程序结束并复位车床编程实例十G82 指令编程(毛坯外形已加工完成)%3323N1 G55 G00 X35 Z104(选定坐标系G55,到循环起点)N2 M03 S300 (主轴以300r/min 正转)N3 G82 C2 P180 F3(第一次循环切螺纹,切深)N4 C2 P180 F3(第二次循环切螺纹,切深)N5 C2 P180 F3(第三次循环切螺纹,切深)N6 C2 P180 F3(第四次循环切螺纹,切深)N7 M30 (主轴停、主程序结束并复位)图G82 切削循环编程实例6车床编程实例十一外径粗加工复合循环编制图所示零件的加工程序:要求循环起始点在A(46,3),切削深度为(半径量)。
数控宏程序编制两例
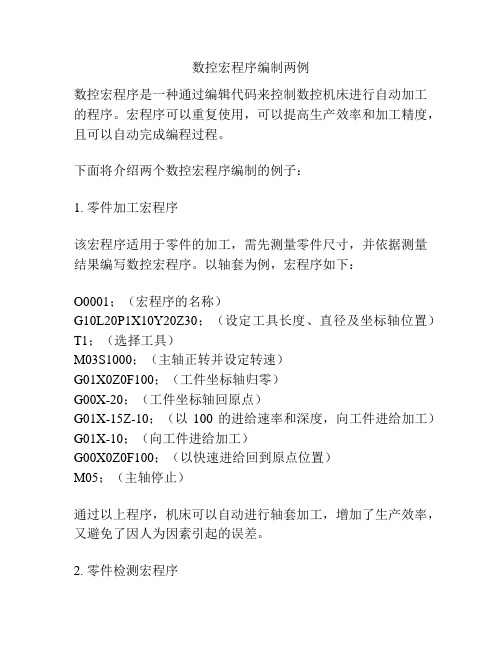
数控宏程序编制两例数控宏程序是一种通过编辑代码来控制数控机床进行自动加工的程序。
宏程序可以重复使用,可以提高生产效率和加工精度,且可以自动完成编程过程。
下面将介绍两个数控宏程序编制的例子:1. 零件加工宏程序该宏程序适用于零件的加工,需先测量零件尺寸,并依据测量结果编写数控宏程序。
以轴套为例,宏程序如下:O0001;(宏程序的名称)G10L20P1X10Y20Z30;(设定工具长度、直径及坐标轴位置)T1;(选择工具)M03S1000;(主轴正转并设定转速)G01X0Z0F100;(工件坐标轴归零)G00X-20;(工件坐标轴回原点)G01X-15Z-10;(以100 的进给速率和深度,向工件进给加工)G01X-10;(向工件进给加工)G00X0Z0F100;(以快速进给回到原点位置)M05;(主轴停止)通过以上程序,机床可以自动进行轴套加工,增加了生产效率,又避免了因人为因素引起的误差。
2. 零件检测宏程序该宏程序适用于零件的检测,可以快速高效地检查零件尺寸是否合格。
以零件平面度检测为例,宏程序如下:O0002;(宏程序的名称)G10L20P1X10Y20Z30;(设定工具长度、直径及坐标轴位置)T2;(选择工具)M03S1000;(主轴正转并设定转速)G01X0Z0F100;(工件坐标轴归零)G00X-20;(工件坐标轴回原点)G01X-10Z-3;(以 50 的进给速率和深度,向工件进给检测)G00X0Z0F100;(以快速进给回到原点位置)M05;(主轴停止)IF[#2 LT 0.01]GOTO5;(IF 判断语句,如果测量值小于 0.01 mm,跳转到标记 5)G01X10Z-3;(以 50 的进给速率和深度,向工件进给检测)G00X0Z0F100;(以快速进给回到原点位置)M05;(主轴停止)通过以上程序,机床可以自动进行零件平面度的检测,并根据实际情况跳转到不同的位置进行处理。
总之,数控宏程序可以方便快捷地控制数控机床进行自动加工和检测,极大提高了生产效率和加工精度。
数控车床宏程序编程实例

数控车床宏程序编程实例
首先,我们将介绍一些数控车床宏程序的基本概念。
宏程序是一种编写在机床控制器内部的程序,它可以包含一系列的指令和操作,从而完成一定的加工工艺。
宏程序可以使操作员在加工过程中减少输入指令的时间和精力,提高加工精度和效率。
接下来,我们将通过实例来介绍数控车床宏程序的编程方法。
假设我们需要在数控车床上加工一个圆柱形工件,其直径为100mm,长度为200mm。
我们可以编写一个宏程序来完成这个加工过程。
具体步骤如下:
1. 首先,我们需要定义一个宏程序,命名为“CYLINDER”。
2. 接下来,我们需要设置加工过程中所需用到的切削工具和切削速度等参数。
3. 然后,我们需要编写加工程序的主体部分,即定义加工路径。
在本例中,我们需要使用G代码来定义加工路径,例如:“G00 Z5.0;G00 X0;G00 Z0;G01 X50 F200;G01 Z-100 F100;G02 X0 Z-200 I-50;G01 X-50 F200;G01 Z0 F100;G02 X0 Z100 I50;G00 Z5.0”。
4. 最后,我们需要定义程序结束的指令,例如:“M30”。
完成上述步骤后,我们就可以将宏程序保存在机床控制器内部。
需要加工圆柱形工件时,我们只需要调用宏程序“CYLINDER”,即可自动完成加工过程。
总之,数控车床宏程序编程是一种非常实用的编程方式,能够大大提高机床操作的效率和精度。
通过本文的介绍,相信读者能够更加
深入地了解宏程序的编写方法和调用方式,为实际工作提供帮助。
数控车宏程序编程方法及技巧

END 2 G0 U2; Z26;(退刀) IF [#20 GE 0] GOTO 100;
(如果余量大于等于0跳转到100句)
G0 X100; M05; M30;
3.抛物线类零件的宏程序编制 抛物线的一般方程:
X 2 2PZ(或Z2 2PX)
在数控车床编程中,宏程序编
程灵活、高效、快捷。宏程序不仅 可以实现象子程序那样,对编制相 同加工操作的程序非常有用,还可 以完成子程序无法实现的特殊功能, 例如: 系列零件加工宏程序、椭圆
加工宏程序、抛物线加工宏程序、 双曲线加工宏程序等。
主要内容
数控车床宏程序编程特征 宏程序中的变量 宏程序变量间的运算指令 宏程序的控制语句 数控车床宏程序编程技巧编程实例 宏程序用于系列零件的加工 椭圆类零件的宏程序编制 抛物线类零件的宏程序编制 双曲线过渡类零件的宏程序编制
两者不为一个值,关系为
tan
a b
tan
椭圆宏程序结构流程:
1.开始 2.给常量赋值
3.给变量赋值
4.计算坐标值
5.指令机床沿曲线移动X,Z坐标
6.变量递增或递减
7.判断是否到达终点
未到终点返回4.计算坐标值
8.到终点结束
椭圆加工: 零件材料 45钢,毛 坯为 φ50mm×1 00mm,按 图要求完 成数控加 工程序。
【解答】
O0001; T0101 ; M03 S800; G0 X51. Z2.; G71 U1.5 R1. ;(粗车右端外形轮廓) G71 P10 Q20 U0.5 W0.1 F150 ; N10 G1 X25.966;(椭圆处外径) Z0.; Z-19.; X35.988 Z-29.; Z-46; X44.; X45.992 Z-47.; N20 Z-55.; G70 P10 Q20 S1000 F120;(精车右端外形轮廓) G00 X100.; Z50.;
加工中心宏程序编程实例与技巧方法

G00 X45 Y-15 ;
Z3
Z3
G01 Z-5 F100
G01 Z-5 F100
#10=0;给角度赋0初值 R10=0;给角度赋0初值
WHILE #10 LE 360 DO 1;AA:
#11=40*COS[#10]; R11=40*COS(R10);
#12=30*SIN[#10];
R12=30*SIN(R10);
G01 X#11 Y#12 ;
G01 X=R11 Y=R12 ;
#10=#10+1;
R10=R10+1;
END 1
IF R10<= 360 GOTOB AA
X45 Y15;
X45 Y15;
G00 Z30
G00 Z30
X0 Y0 M05
X0 Y0 M05
M30
M30
数控加工技术
三、SIEMENS参数编程程序跳转
1.无条件跳转
GOTOB LABEL (向后跳转, 向程序头跳转)
GOTOF LABEL (向前跳转, 向程序尾跳转)
2.条件跳转
IF 表达式 GOTOB LABEL(向后 跳转,向程序头跳转) ○ IF 表达式 GOTOF LABEL( 向前跳转,向程序尾跳转)
LABEL 为程序段标示符
数控加工技术
数控加工技术
四、编程示 例
数控加工技术
五、SIEMENS与FANUC用户宏程序20编24/11/11 程对照
长半轴40、短半轴30的椭圆
G54 G90 G00 Z30
G54 G90 G00 Z30
M03 S800
M03 S800
G00 X45 Y-15 ;
用户宏程序编程
- 1、下载文档前请自行甄别文档内容的完整性,平台不提供额外的编辑、内容补充、找答案等附加服务。
- 2、"仅部分预览"的文档,不可在线预览部分如存在完整性等问题,可反馈申请退款(可完整预览的文档不适用该条件!)。
- 3、如文档侵犯您的权益,请联系客服反馈,我们会尽快为您处理(人工客服工作时间:9:00-18:30)。
论文:数控机床宏程序编程的技巧和实例西北工业集团有限公司白锋刚2018年8月11日前言随着工业技术的飞速发展,产品形状越来越复杂,精度要求越来越高,产品更新换代越来越快,传统的设备已不能适应新要求。
现在我国的制造业中已广泛地应用了数控车床、数控铣床、加工中心机床、数控磨床等数控机床。
这些先进设备的加工过程都需要由程序来控制,需要由拥有高技能的人来操作。
要发挥数控机床的高精度、高效率和高柔性,就要求操作人员具有优秀的编程能力。
常用的编程方法有手工编程和计算机编程。
计算机编程的应用已非常广泛。
与手工编程比较,在复杂曲面和型腔零件编程时效率高、质量好。
因此,许多人认为手工编程已不再重要,特别是比较难的宏程序编程也不再需要。
只须了解一些基本的编程规则就可以了。
这样的想法并不能全面。
因为,计算机编程也有许多不足:1、程序数据量大,传输费时。
2、修改或调整刀具补偿需要重新后置输出。
3、打刀或其他原因造成的断点时,很难及时复位。
手工编程是基础能力,是数控机床操作编程人员必须掌握的一种编程方法。
手工编程能力是计算机编程的基础,是刀具轨迹设计,轨迹修改,以及进行后置处理设计的依据。
实践证明,手工编程能力强的人在计算机编程中才能速度快,程序质量高。
在程序中使用变量,通过对变量进行赋值及处理使程序具有特殊功能,这种有变量的程序叫宏程序。
宏程序是数控系统厂家面向客户提供的的二次开发工具,是数控机床编程的最高级手工方式。
合理有效的利用这个工具将极大地提升机床的加工能力。
作为一名从事数控车床、数控铣床、加工中心机床操作编程二十多年的技师,在平时的工作中,常常用宏程序来解决生产中的难题,因此对宏程序的编程使用积累了一些经验。
在传授指导徒弟和与同事探讨中,总结了许多学习编制宏程序应注意的要点。
有关宏编程的基础知识在许多书籍中讲过,我们在这里主要通过实例从编制技巧、要点上和大家讨论。
一、非圆曲面类的宏程序的编程技巧1、非圆曲面可以分为两类;<1)、方程曲面,是可以用方程描述其零件轮廓的曲面的。
如抛物线、椭圆、双曲线、渐开线、摆线等。
这种曲线可以用先求节点,再用线段或圆弧逼近的方式。
以足够的轮廓精度加工出零件。
选取的节点数目越多,轮廓的精度越高。
然而节点的增多,用普通手工编程则计算量就会增加的非常大,数控程序也非常大,程序复杂也容易出错。
不易调试。
即使用计算机辅助编程,其数据传输量也非常大。
而且调整尺寸补偿也很不方便。
这时就显出宏程序的优势了,常常只须二、三十句就可以编好程序。
而且理论上还可以根据机床系统的运算速度无限地缩小节点的间距,提高逼近精度。
<2)、列表曲面,其轮廓外形由实验方法得来。
如飞机机翼、汽车的外形由风洞实验得来。
是用一系列空间离散点表示曲线或曲面。
这些离散点没有严格一定的连接规律。
而在加工中则要求曲线能平滑的通过各坐标点,并规定了加工精度。
加工列表曲线的方法很多,可以采用计算机辅助编程,利用离散点形成曲面模型,再生成加工轨迹和加项目序。
对于一些老机床或无法传送数据的机床,我们也可以将轮廓曲线按曲率变化分成几段,每段分别求出插值方程。
采用宏程序加密逼近曲线的方法。
2、非圆曲面类的宏程序的编程的要点有:建立数学模型和循环体<1)、数学模型是产生刀具轨迹节点的一组运算赋值语句。
它可以计算出曲面上每一点的坐标。
它主要从描述其零件轮廓的曲面的方程转化而来。
<2)、循环体是由一组或几组循环指令和对应的加法器组成。
它的作用是将一组节点顺序连接成刀具轨迹,再依次加工成曲面。
3、下面根据两个实例,按宏程序的编制过程将各步骤的要点和技巧进行详细说明。
图1—1、椭圆曲面零件实例1、如图1-1数控车加工一个椭圆面。
椭圆的长轴60,短轴40.步骤1:根据加工轨迹确定椭圆曲线的起始点A和终点B坐标。
这里的要点是分清编程坐标系和椭圆坐标系、A点在编程坐标系中的坐标为X=113.742、Z=27.252这里为适应数控车床的编程习惯x采用直径坐标,A点以椭圆的中心为原点的坐标为X=113.742 Z=40—27.252 B点的编程坐标是X=37.907 椭圆坐标为X=37.907步骤2:确定在曲线方程中的主变量和从变量。
这要根据实际情况来选择。
有以下几点原则:①变量的起点、终点已知的。
②变量在坐标中的变化方向一致。
③变量的变化对曲线的精度影响较大。
根据以上原则我选X坐标为主变量、Z是从变量。
步骤3:将标准方程化为从变量赋值的形式。
如图1-1以其中心为原点,椭圆方程为 X²/a² +Z²/b²=1化为Z= SQRT[(1-X*X/a*a>*b*b 这一步很关键。
因为曲线只在椭圆坐标系的第一象限Z为正值。
以上三步就是建立数学模型。
在这个模型里X的一个坐标值,可以计算出它对应的Z坐标值。
要注意,这两个坐标是以椭圆中心为原点的,要特别注意。
也就是说,如果和这个零件一样,椭圆中心和你设定的编程坐标系原点不重合,进入数学模型和从数学模型输出的数值,都是以椭圆中心为原点的。
刀具运动指令的坐标值是以编程坐标系为原点。
因此,需要设计计算方法将数学模型的输出数据转化成编程坐标系的数值。
许多多年从事数控机床操作的人一直不能用宏程序,就是在这里犯了糊涂。
步骤4:画流程图确定宏程序的过程图1-2流程图是建立和检查循环体的最好工具。
这一步的关键点是:分清计算过程、运动指令、加法器的排列顺序;循环体中条件转移语句和加法器的配合,产生正确的循环控制,而不是死循环。
;赋初始值<注意是椭圆坐标系);循环体开始,判断是否结束。
;计算、运动指令;加法器,改变动参数图1—2步骤5:根据流程图编写程序程序如下O1001应注意的要点有:<1)、当采用刀尖圆弧补偿方式编程时,循环体的轨迹第一点不能和起始点重合,否则系统会显示出错。
<2)要注意循环体内计算语句、运动语句和加法器语句的顺序不能错。
该零件如图右端内部椭圆面的数控车精车程序如下:O1001。
重点说明T0101。
G90G40G0X200.0Z200.0M03。
G41G00X135.0Z5.0M08。
G01Z-25.0F0.1。
G03X#1Z-27.252。
#1=113.742-0.1。
将循环开始点错开#2=40-27.252。
Z值从编程坐标系转变到椭圆坐标系WHIFL[#1GT37.907] DO 1 。
循环体开始,X轴坐标逐渐减小#1=#1/2;将直径值转化成半径值#2=SQRT[[1-#1*#1/[60*60]]*40*40]。
#2=#2-40 Z值从椭圆坐标系转变到编程坐标系#1=#1*2 将半径值转化成直径值G01X#1Z#2F0.08。
运动指令#1=#1-0.1。
递减加法器END 1。
循环体结束G01X37.907Z-2.048。
G01X35.0。
G00Z200.0。
G00X260.0M09。
M30。
图1--3实例2、在加工中心上加工抛物线球面。
比较加工中心或数控铣床上铣削曲面和数控车床车削曲面,有许多差别:<1)、加工方式不同。
(2>、车削曲面需要计算沿一条轮廓素线的若干个节点;铣削曲面需要计算整个曲面上若干个轮廓素线的若干节点。
计算量大,宏程序非常复杂。
编制铣削曲面宏程序确实非常难,然而只要我们抓住几个关键要点,做好流程图和数学模型,勤于实践,也是一定能够掌握这个技能的。
下面把编制铣削曲面宏程序的过程分成几步:步骤1、分析曲面的构成特点确定加工路线如图1-3、这个曲面是由一条抛物线以与它共面水平直线为轴线旋转切成的。
加工轨迹可以有两种,一种是水平层切、一种是垂直层切。
我们用垂直层切的方式。
其轨迹如图1-4,每个层切面上的刀具轨迹都是一个YZ平面的圆弧。
图1--4步骤2、选择合适的编程坐标系,确定主、从变量。
如图1-3把坐标系原点设置形腔上表面的中心,可以简化计算。
Z为主变量。
取Z=0 为起点,Z=20为终点。
步骤3、抛物线方程X²=36<Z-20)转化为X=SQRT[36*[Z-20]] 和X=-SQRT[36*[Z-20]]、这里需要注意两个象限的变化,要设计两个循环体,用控制指令“换向”。
步骤4、设计流程图,实验循环体程序框架。
步骤5、根据流程图编制程序。
注意程序的加工平面为y-z<G18)平面。
流程图和程序如下图1—5,O1002O1002。
G0X0Y0M8。
G54G18G90G40。
G43G0Z100H1M3S3000T1M6。
Z5。
#1=0。
WHILE[#1GT-20] DO 1#2=SQRT[36*[#1-20]]。
G1X#2F500。
G41G1Y#1D1G1Z0G2Y-#1J-#1G40G1Y0。
#1=#1-0.1END 1。
#1=-20WHILE[#1LT0] DO 2#2=-SQRT[36*[#1-20]]G01X#2F500G41G1Y#1D1G2Y-#1J-#1G40G1Y0#1=#1+0.1图1—5 END 2。
G00Z200M9M30二、用宏程序开发对零件自动找正功能图2---11、开发过程某零件如图2-1。
工艺安排卧式加工中心上一次装夹将四个Φ8孔加工完成,保证其位置精度。
但是工件在夹具中定位后,B向旋转无法用夹具精确定位。
当时的方法是:①每个零件装夹后单独用百分表找平。
或者用自动测量触头取值,手工计算偏转角。
②修改程序中新的B向坐标基准值。
整个过程用时较长须用时长,对操作工的技能要求也较高。
这种零件数量多,工期紧,要想办法节约时间。
我就想利用宏程序计算功能和机床具备的自动测量触头功能可以实现自动找正。
2、自动找正零件功能的工作原理<1)、零件夹具中设计一个粗定位圆柱销,使零件粗定位,保证测量精度和测量工具的安全。
.<2)、选择零件基准面上较远的两个点采值,如图a、b两点。
分别放入#1和#2参数在。
<3)、计算差值及偏转角。
<4)、输入编程坐标系G54的B轴。
另一台四轴加工中心没有自动测量功能,我们用采用百分表触测零件基准面,目测记录差值,手工输入参数表中。
宏程序自动计算并找正。
速度和准确率提高了很多,保证了生产任务按时完成。
3、编制宏程序自动找正功能的开发并不复杂,使用的是宏程序对内部系统变量读取和赋值功能。
程序如下:O2001T3M6。
G54G90G0X40Y300B0。
G43G0Z200H3。
G0Y15Z60。
运动到预备测量a位置G31G91Z-52F500。
执行G31测量a点坐标存入#5000G90G0Y100Z200。
#1=#5000; #5000系统参数记录a点的坐标值,赋给#1G0X-40。
G0Y15Z60。
G31G91Z-52F500。
执行G31测量b点G0G90Y200Z200。