电厂脱硫石膏脱水困难的原因及解决方案
某电厂脱硫石膏脱水异常原因分析及控制措施
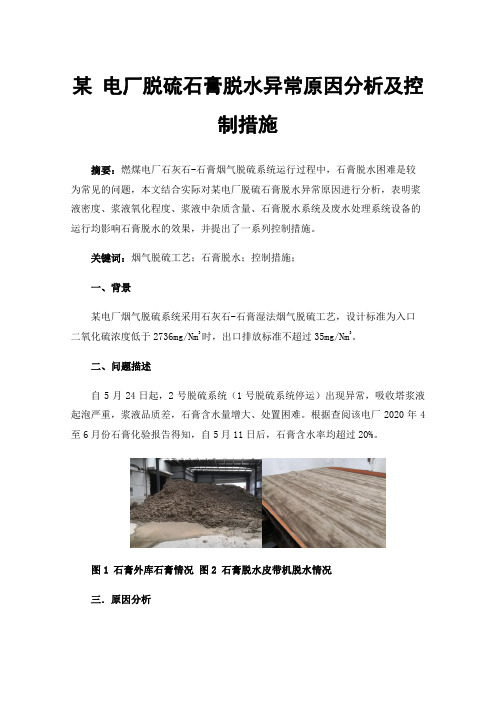
某电厂脱硫石膏脱水异常原因分析及控制措施摘要:燃煤电厂石灰石-石膏烟气脱硫系统运行过程中,石膏脱水困难是较为常见的问题,本文结合实际对某电厂脱硫石膏脱水异常原因进行分析,表明浆液密度、浆液氧化程度、浆液中杂质含量、石膏脱水系统及废水处理系统设备的运行均影响石膏脱水的效果,并提出了一系列控制措施。
关键词:烟气脱硫工艺;石膏脱水;控制措施;一、背景某电厂烟气脱硫系统采用石灰石-石膏湿法烟气脱硫工艺,设计标准为入口二氧化硫浓度低于2736mg/Nm3时,出口排放标准不超过35mg/Nm3。
二、问题描述自5月24日起,2号脱硫系统(1号脱硫系统停运)出现异常,吸收塔浆液起泡严重,浆液品质差,石膏含水量增大、处置困难。
根据查阅该电厂2020年4至6月份石膏化验报告得知,自5月11日后,石膏含水率均超过20%。
图1石膏外库石膏情况图2石膏脱水皮带机脱水情况三.原因分析经过现场收资、数据核算及与电厂运行、设备人员沟通,分析该电厂2号机脱硫石膏异常主要问题如下:通过图2看出,石膏在脱水皮带上脱水效果很好,但石膏落入石膏库后,石膏内水分不久后就会溢出。
后经取样发现,石膏颗粒度小,沉降困难,且浆液中有大量泡沫。
图3、4 2号脱硫浆液取样情况(一)氧化情况6月10日,15:00对2号吸收塔浆液进行取样。
通过检测,半水亚硫酸钙含量0.2%。
依据该电厂运行规程可知FGD入口烟气量为1189756Nm3/h(标态,干基,α=1.4),入口二氧化硫浓度为2736mg/Nm3(标态,干基,α=1.4),出口二氧化硫浓度为30 mg/Nm3(标态,干基,6%O2)。
需要的理论氧气量为:S=(C1-C2) ×Q=(2736-30) ×1189756/64/2=25.15kmol所需空气流量:Qreq=S×22.4/(0.21)=25.15×22.4/0.21=2683 Nm3/h根据经验,氧化空气要考虑利用率,一般利用率在50%,则实际空气供应量Q实际=2683×2=5366Nm3/h。
石膏脱水不干原因分析

⽯膏脱⽔不⼲原因分析⽯灰⽯/⽯膏湿法脱硫的运⾏调整及系统问题处理马俊峰(河北⼤唐国际王滩发电有限责任公司河北唐⼭063611)摘要:本⽂叙述、分析、总结了河北⼤唐王滩发电有限责任公司,在脱硫系统调试及正常运⾏⼯作中所遇到的问题,结合⾃⼰的⼯作体会提出了合理运⾏的调整⽅法,对其它电⼚脱硫运⾏⼯作有⼀定参考借鉴作⽤。
关键词:⽯灰⽯/⽯膏湿法脱硫⼯艺原理;脱硫运⾏调试;系统问题处理。
引⾔随着全球经济的⾼速发展和⼯业化的不断推进,⼤⽓中⼆氧化硫排放量与⽇俱增,造成降⽔pH 值下降,局部地⽅甚⾄形成酸⾬,对⼈体健康和⼤⽓环境带来很⼤影响。
⽬前,随着我国电⼒⼯业的污染物的国家环保排放标准⽇益完善,新建及扩建电⼚必须安装投运脱硫装置。
1 概述⽬前,燃煤电⼚应⽤最⼴泛的是⽯灰⽯/⽯膏湿法脱硫。
⽯灰⽯/⽯膏湿法脱硫的机理是将烟⽓引⼊吸收塔,其中的⼆氧化硫与吸收塔中喷淋的⽯灰⽯浆液(主要成分是CaCO3)在流动(根据⼯艺可分为顺流、逆流、混合流)中反应,⽣成半⽔亚硫酸钙(CaSO3?1/2H2O),再被氧化风机⿎⼊的空⽓强制氧化成⼆⽔硫酸钙(CaSO4?2H2O)晶体,从吸收塔排出的⽯膏经⽔⼒旋流浓缩(50%)和真空脱⽔,使其含⽔量⼩于10%,由⽪带机堆⼊⽯膏库中。
脱硫后的烟⽓除雾器除去雾滴后,经烟囱排⼊⼤⽓。
2 设计条件脱硫装置与发电机组单元匹配,#1、2FGD按锅炉100%全烟⽓量设计,脱硫效率95%以上。
2083 ⽯灰⽯/⽯膏法脱硫⼯艺原理锅炉引风机排出的原烟⽓由增压风机增压后经吸收塔下部进⼊脱吸收塔。
新鲜的⽯灰⽯不断的加⼊吸收塔,吸收塔内的循环浆液从上部若⼲个喷嘴中涌出与塔内逆流⽽上原烟⽓充分接触,进⾏⽓/液接触反应脱除烟⽓中的SO2。
脱硫后含有饱和⽔的静烟⽓的带有⼤量⽔珠,在流经格栅状除雾器时被除去,最后静烟⽓经烟道进⼊烟囱外排⼤⽓。
脱硫的性能通过⾃动控制系统对PH值和⽯膏浆液浓度进⾏调节,实现⾃动控制。
脱硫石膏脱水困难原因分析及解决方案

大同分公司脱硫石膏脱水困难的原因分析及解决方案1石膏脱水困难的现象极其原因分析1.1现象1)滤布成型的石膏饼中出现分层现象,上层较湿,下层较干,或上层干下层湿;2)石膏饼表面有一层湿黏,发亮的物质;3)石膏病断层有气泡破裂后留下的小孔。
4)下料口不结块、不滑落,成稀泥状,甚至出现下部粘稠、上部成流水状。
1.2原因分析影响石膏脱水的因素比较多,归纳起来,不外乎吸收塔物理化学反应过程的参数控制和脱水设备的运行状况。
参数控制参数控制因素对于吸收塔,除了粉尘,上游烟气因素已不可控,因而在运行过程中,主要要控制吸收塔本身的浆液PH值、浆液密度。
吸收塔液位,粉尘含量和氧化风量,这些参数,影响石膏的结晶和水分的脱出,因为在石膏的生成过程中,如果参数控制不好,往往会生成层状、针状晶体,进一步向片状、簇状或花瓣形发展,其粘性大难以脱水,xx硫酸钙晶体。
而石膏晶体应是短柱状,比前者颗粒大,易脱水。
另外,颗粒较小的物质如石灰石和粉尘等杂质,游离于石膏晶体之间,堵塞水分脱出通道,是水分难以脱出。
.1浆液PH值。
浆液PH是控制脱硫反应过程的一个重要参数。
控制PH值就是控制过程的一个重要参数。
控制PH值就是控制进入吸收塔的石灰石浆液量。
因为SO2溶解过程中,离解出大量的H+,高PH的控制有助于SO2的溶解,而石灰石的溶解过程中,离解出大量的OH-,低PH值的控制有助于石灰石的溶解,所以PH值得过高过低都不利于石膏的形成,必须确定一个合理的PH值,否则过高的PH值使大量的石灰石混入石膏,无论是石灰石还是亚硫酸盐,由于其粒径比硫酸钙晶体小,不但降低石膏纯度,而且造成石膏脱水困难。
.2浆液密度。
石膏的浆液密度反映了吸收塔中浆液的饱和情况,密度过低,则表明吸收塔石膏含量低,碳酸钙含量相对较大,此时如果将石膏浆液排除吸收塔,将导致石膏中的碳酸钙增加,浪费石灰石,由于其粒径小,既降低石膏品质又使石膏脱水困难;密度过高,则表明石膏浆中石膏和碳酸钙都过量,过量的硫酸钙抑制SO2的吸收,不利于碳酸钙溶解,此时若排除石膏,由于碳酸钙粒径小,造成石膏脱水困难。
脱硫石膏脱水困难原因分析与解决方案

大同分公司脱硫石膏脱水困难的原因分析及解决方案1石膏脱水困难的现象极其原因分析1.1现象1)滤布成型的石膏饼中出现分层现象,上层较湿,下层较干,或上层干下层湿;2)石膏饼表面有一层湿黏,发亮的物质;3)石膏病断层有气泡破裂后留下的小孔。
4)下料口不结块、不滑落,成稀泥状,甚至出现下部粘稠、上部成流水状。
1.2原因分析影响石膏脱水的因素比较多,归纳起来,不外乎吸收塔物理化学反应过程的参数控制和脱水设备的运行状况。
1.2.1 参数控制参数控制因素对于吸收塔,除了粉尘,上游烟气因素已不可控,因而在运行过程中,主要要控制吸收塔本身的浆液PH值、浆液密度。
吸收塔液位,粉尘含量和氧化风量,这些参数,影响石膏的结晶和水分的脱出,因为在石膏的生成过程中,如果参数控制不好,往往会生成层状、针状晶体,进一步向片状、簇状或花瓣形发展,其粘性大难以脱水,如亚硫酸钙晶体。
而石膏晶体应是短柱状,比前者颗粒大,易脱水。
另外,颗粒较小的物质如石灰石和粉尘等杂质,游离于石膏晶体之间,堵塞水分脱出通道,是水分难以脱出。
1.2.1.1浆液PH值。
浆液PH是控制脱硫反应过程的一个重要参数。
控制P H值就是控制过程的一个重要参数。
控制P H值就是控制进入吸收塔的石灰石浆液量。
因为SO2溶解过程中,离解出大量的H+,高PH的控制有助于SO2的溶解,而石灰石的溶解过程中,离解出大量的OH-,低PH值的控制有助于石灰石的溶解,所以PH值得过高过低都不利于石膏的形成,必须确定一个合理的PH值,否则过高的PH值使大量的石灰石混入石膏,无论是石灰石还是亚硫酸盐,由于其粒径比硫酸钙晶体小,不但降低石膏纯度,而且造成石膏脱水困难。
1.2.1.2浆液密度。
石膏的浆液密度反映了吸收塔中浆液的饱和情况,密度过低,则表明吸收塔石膏含量低,碳酸钙含量相对较大,此时如果将石膏浆液排除吸收塔,将导致石膏中的碳酸钙增加,浪费石灰石,由于其粒径小,既降低石膏品质又使石膏脱水困难;密度过高,则表明石膏浆中石膏和碳酸钙都过量,过量的硫酸钙抑制SO2的吸收,不利于碳酸钙溶解,此时若排除石膏,由于碳酸钙粒径小,造成石膏脱水困难。
脱硫石膏脱水困难原因分析及解决方案

大同分公司脱硫石膏脱水困难的原因分析及解决方案1石膏脱水困难的现象极其原因分析1.1现象1)滤布成型的石膏饼中出现分层现象,上层较湿,下层较干,或上层干下层湿;2)石膏饼表面有一层湿黏,发亮的物质;3)石膏病断层有气泡破裂后留下的小孔。
4)下料口不结块、不滑落,成稀泥状,甚至出现下部粘稠、上部成流水状。
1.2原因分析影响石膏脱水的因素比较多,归纳起来,不外乎吸收塔物理化学反应过程的参数控制和脱水设备的运行状况。
1.2.1 参数控制参数控制因素对于吸收塔,除了粉尘,上游烟气因素已不可控,因而在运行过程中,主要要控制吸收塔本身的浆液PH值、浆液密度。
吸收塔液位,粉尘含量和氧化风量,这些参数,影响石膏的结晶和水分的脱出,因为在石膏的生成过程中,如果参数控制不好,往往会生成层状、针状晶体,进一步向片状、簇状或花瓣形发展,其粘性大难以脱水,如亚硫酸钙晶体。
而石膏晶体应是短柱状,比前者颗粒大,易脱水。
另外,颗粒较小的物质如石灰石和粉尘等杂质,游离于石膏晶体之间,堵塞水分脱出通道,是水分难以脱出。
1.2.1.1浆液PH值。
浆液PH是控制脱硫反应过程的一个重要参数。
控制PH值就是控制过程的一个溶解过程中,离解重要参数。
控制P H值就是控制进入吸收塔的石灰石浆液量。
因为SO2的溶解,而石灰石的溶解过程中,离解出大量的出大量的H+,高PH的控制有助于SO2OH-,低PH值的控制有助于石灰石的溶解,所以PH值得过高过低都不利于石膏的形成,必须确定一个合理的PH值,否则过高的PH值使大量的石灰石混入石膏,无论是石灰石还是亚硫酸盐,由于其粒径比硫酸钙晶体小,不但降低石膏纯度,而且造成石膏脱水困难。
1.2.1.2浆液密度。
石膏的浆液密度反映了吸收塔中浆液的饱和情况,密度过低,则表明吸收塔石膏含量低,碳酸钙含量相对较大,此时如果将石膏浆液排除吸收塔,将导致石膏中的碳酸钙增加,浪费石灰石,由于其粒径小,既降低石膏品质又使石膏脱水困难;密度的吸收,不利于过高,则表明石膏浆中石膏和碳酸钙都过量,过量的硫酸钙抑制SO2碳酸钙溶解,此时若排除石膏,由于碳酸钙粒径小,造成石膏脱水困难。
脱硫石膏脱水困难原因分析及解决方案

脱硫石膏脱水困难原因分析及解决方案脱硫石膏是从燃煤发电厂烟气中的脱硫废水中提取出的一种固体废弃物。
由于脱硫石膏中含有大量的水分,为了减少废物的体积和转运成本,通常需要对脱硫石膏进行脱水处理。
然而,在脱水过程中常常会遇到一些困难,本文将对这些困难进行分析,并提出相应的解决方案。
1.石膏颗粒细小:脱硫石膏是通过将石膏浆液进行喷雾或喷淋造粒制成的颗粒状物料,这些颗粒的直径通常在几毫米到几十毫米之间。
由于颗粒细小,颗粒之间的接触面积大,导致水分难以从颗粒表面迅速挥发出去。
2.石膏含水率高:脱硫石膏的含水率通常在60%到80%之间,高含水率会导致脱水过程中所需的能量和时间增加。
3.石膏颗粒松散:脱硫石膏颗粒松散,比重小,容易形成块状,使得水分无法从颗粒内部透出。
针对以上问题,可以采取以下解决方案:1.按照颗粒大小分类处理:颗粒大小对脱水效果有很大影响。
可以将颗粒按照大小进行分类处理,将大颗粒和小颗粒分开处理。
大颗粒可以采用机械挤压等方式进行脱水,小颗粒可以使用薄膜蒸发、离心等方法进行脱水。
2.提高石膏含水率:通过蒸发等方式,将脱硫石膏的含水率提高到更高的水平,可以进一步减少脱水过程中所需的能量和时间。
3.改善石膏颗粒结构:可以通过添加细粉煤灰等物料,改善脱硫石膏颗粒的结构,使其变得更加致密,减少颗粒间的接触面积,从而提高脱水效果。
4.优化脱水工艺参数:根据脱硫石膏的性质和特点,优化脱水工艺参数,如温度、压力、滤饼厚度等,以提高脱水效果。
总之,脱硫石膏脱水困难的原因主要是石膏颗粒细小、含水率高和颗粒松散等。
通过分类处理、提高石膏含水率、改善颗粒结构和优化脱水工艺参数等措施,可以有效地解决这些问题,提高脱硫石膏的脱水效果。
脱硫石膏脱水异常原因分析及控制措施
脱硫石膏脱水异常原因分析及控制措施摘要:燃煤电厂石灰石-石膏烟气脱硫系统运行过程中,石膏脱水困难是较为常见的问题,本文结合实际对某发电公司脱硫石膏脱水异常原因进行分析,表明浆液密度、石膏结晶情况对石膏脱水效果有较大影响,并提出了一系列控制措施。
关键词:烟气脱硫工艺;石膏脱水;控制措施;一、企业脱硫系统概况东南某发电公司烟气脱硫系统采用石灰石-石膏湿法烟气脱硫工艺,脱硫系统采用石灰石-石膏湿法烟气脱硫,一炉一塔配置,吸收塔包括4层喷淋装置和1套除雾器,每层喷淋装置对应1台吸收塔浆液循环泵,设计标准为入口二氧化硫浓度低于1600mg/Nm3时,出口排放标准不超过35mg/Nm3。
二、异常情况简介2020年12月1~4 号机组相继出现脱硫石膏脱水困难异常现象,脱硫系统产生的石膏含水率达到 50%以上,异常初期电厂先后对1~4号脱硫系统采取更换至不同皮带机脱水、不同配比混合脱水、增开氧化风机、降低脱硫浆液pH等措施,石膏脱水情况没有好转,至 12月31日,石膏含水率达到 53.2%。
异常期间,大量泥状石膏无法有效处置和综合利用,严重影响机组的正常运行。
三、异常原因分析湿法脱硫工艺主要经历吸收、中和、氧化、结晶 4 个反应步骤,各反应步骤的影响因素均会对烟气中二氧化硫的脱除与石膏副产物的形成产生不同程度的影响。
造成石膏无法正常脱水的主要原因可能为:(1)吸收塔浆液氧化不充分,半水亚硫酸钙含量高;(2)石膏浆液里碳酸钙含量高;(3)吸收塔入口烟尘浓度高;(4)真空皮带机故障;(5)工艺水、石灰石品质异常等;(6)脱硫运行参数异常。
对此,通过调阅脱硫系统运行历史资料、结合实验室化验分析等方式对这些影响因素展开分析。
3.1浆液CaSO3·1/2H2O氧化效果分析3.1.1 浆液中 CaSO3·1/2H2O含量化验2020 年12月24日~2021年1月1日,机组浆液中的 CaSO3·1/2H2O 质量分数均控制在0.3%以下,对比2020年度吸收塔浆液CaSO3·1/2H2O历史化验结果,可知脱硫浆液中CaSO3·1/2H2O含量正常,说明吸收塔内氧化效果较好。
火电厂湿法烟气脱硫脱硫石膏脱水问题分析及改进措施
火电厂湿法烟气脱硫脱硫石膏脱水问题分析及改进措施前言火电厂是我国电力生产的重要组成部分。
烟气中含有大量的二氧化硫,对环境和人类健康造成了较大的影响。
因此,如何有效地控制二氧化硫排放是火电厂排放控制工作的重点之一。
而湿法烟气脱硫技术作为目前主要的脱硫手段,已经被广泛应用。
然而,湿法烟气脱硫会产生大量的石膏脱水问题,给环境和设备带来了一系列的问题,如何解决这些问题是当前工程师们亟待解决的难题。
本文将从湿法烟气脱硫原理入手,分析湿法烟气脱硫脱硫石膏脱水问题,并提出改进措施。
湿法烟气脱硫原理湿法烟气脱硫的原理是在烟气中加入一定量的氧化剂(通常为空气),将硫化氢等二氧化硫的前体气体氧化成硫酸气体,再将其与石灰水反应得到石膏。
石膏是一种水合硫酸钙(CaSO4·2H2O),具有广泛的应用价值。
然而,石膏具有较高的含水量,常需要在火电厂内进行进一步的脱水处理。
湿法烟气脱硫中的脱硫石膏脱水问题问题描述在湿法烟气脱硫过程中,石膏会被产生并输送到水洗池(或水泵中)降低其含水量。
但是这种处理方式会产生一定的问题:•造成降解:石膏在水中的储存时间增加会导致其一定程度的降解,难以达到进一步的稳定化处理。
•污染环境:将高含水量的石膏排放到水体中,会造成一定的污染问题。
•设备泛腐:石膏中含有较高的酸度和氯离子,长时间的接触会对设备造成腐蚀影响。
这些问题给火电厂的生产和环保工作带来了不小的困扰。
问题分析以上问题主要由以下原因引起:1.单一的脱水方法:目前的湿法烟气脱硫中只采用了一种方式进行石膏脱水,而这种方式难以应对多种情况下的需要。
2.水质和石膏产生的化学反应:石膏和水泵中的水会进行一系列的化学反应,而这些反应会产生不同的化合物(如亚硫酸钙),这些化合物会对设备和环境造成腐蚀和污染。
改进措施为了解决以上问题,我们可以采取以下措施:1.多种脱水方式的组合应用:可通过提高脱水设备的性能、结合真空脱水、离心脱水、压滤脱水等多种方式进行组合应用,达到更为彻底的石膏脱水效果。
湿法脱硫石膏脱水困难原因分析及控制对策
湿法脱硫石膏脱水困难原因分析及控制对策摘要:在湿法烟气脱硫系统中,常出现因石膏含水率高而导致石膏品质下降的问题。
文章针对石膏脱水困难的问题,从原料品质、浆液成分、运行设备等方面总结了出现该问题的原因,提出了相应的预防措施。
优选的解决方法是从源头上控制原料品质,并且从监控手段和运行调整上进行预防,以期解决石膏脱水困难的问题,进而提高石膏的品质。
关键词:湿法脱硫;脱水困难;原料品质;措施1、石膏的生成及脱水工艺烟气中的SO2与石灰石浆液中的CaCO3反应生成Ca CO3•1/2H2O,经过氧化反应生成Ca SO4•2H2O,含有Ca SO4•2H2O晶体的吸收塔浆液经由石膏排出泵打到石膏旋流站进行一级脱水,石膏旋流站的溢流浆液流入滤液水箱,底部的石膏浆液进入到真空皮带脱水机进行二次脱水。
2、含水率超标情况若石膏旋流站的不能使浆液脱水至40%-50%,多出的水分就要进入真空皮带脱水机,进而影响真空皮带机的脱水效果。
某电厂脱硫石膏化学成分抽样分析结果见表1。
根据对电厂石膏的抽样检测可以得出,Ca2+与SO42-具有同离子增长效应,与Cl具有负相关的线性关系,Ca SO3•1/2H2O与Ca CO3具有同步增减的趋势。
而石膏含水率与石膏中残留的碳酸钙的增减起伏大致相同,初步推测石膏中CaSO3•1/2H2O及残留的碳酸钙的含量可以表征石膏中的含水率。
3、石膏脱水效果的影响因素3.1脱硫反应条件3.1.1浆液p H浆液p H对石膏品质具有重要影响,在实际脱硫生产运行中,浆液p H理论上应控制在5.0-5.8左右,浆液p H偏高有利于SO2的吸收,不利于Ca CO3的溶解,p H偏高将导致过量的残余石灰石进入到石膏中。
p H偏低将生成大量的亚硫酸盐。
在监测期间脱硫塔浆液的p H平均值为6.6,超出理论标准值,残余的的石灰石进入到石膏中,从而影响石膏的脱水效果。
因此,为了确保后期石膏的品质,应建议适当的降低石灰石的供浆量,将浆液的p H稳定在标准范围内。
火电厂脱硫系统石膏脱水困难案例分析及对策
火电厂脱硫系统石膏脱水困难案例分析及对策所属行业: 水处理关键词:烟气脱硫脱硫工艺脱硫废水结合山西大土河焦化有限责任公司热电一分厂3×75t/h循环流化床锅炉石灰石-石膏湿法烟气脱硫工程实例,针对石膏脱水异常导致脱硫系统无法正常运行的问题,采用定性分析方法,根据浆液颜色其及沉降分离状况,以及浆液脱水滤饼外观,快速准确地判断出其主要原因为浆液中飞灰、CaSO38226;1/2H2O和未溶解的氢氧化钙含量过高。
采用降低飞灰含量,疏通氧化空气管路,投加石膏晶种和及时调整运行状态的方法,使问题得以解决。
所采用的定性分析方法适用于脱硫工程中的应急处理。
石灰石-石膏湿法烟气脱硫是目前应用很广泛的一种脱硫技术,其原理是采用石灰粉制成浆液作为脱硫吸收剂,其与进入吸收塔的烟气逆流接触烟气中的SO2与浆液中的氢氧化钙以及鼓入的氧化空气进行化学反应,最终生成石膏。
石膏浆液脱水是石灰石-石膏湿法烟气脱硫装置中必不可少的环节。
若塔内浆液不能正常脱水,随着反应的进行,塔内只有石灰浆液加入而没有石膏浆液排出,其结果将导致一系列问题的发生:浆液密度越来越大,塔内浆液液位升高甚至出现溢流,循环泵电流和氧化风机电流增大,搅拌装置超负荷运行,塔底出现大量沉淀,管路堵塞、磨损严重等,并最终导致系统被迫停运。
由此可见,石膏脱水系统的正常运行是脱硫系统运行中极为重要的一环,因而成为近年来研究的热点。
本文结合山西大土河焦化有限责任公司热电一分厂3x75t/h循环流化床锅炉石灰石-石膏湿法烟气脱硫系统石膏脱水困难的实例,对石膏脱水系统是否出现异常提出了一种简单有效的定性分析判断方法及解决问题的对策。
1工程概况山西大土河焦化有限责任公司热电一分厂3x75t/h循环流化床锅炉烟气脱硫系统选择传统的石灰石-石膏湿法脱硫工艺,工艺参数如表1所示。
表1:3x75t/h循环流化床锅炉烟气脱硫系统工艺参数脱硫系统采用1炉1塔,3套系统共用1套石灰制浆系统,2台氧化风机(1用1备)和1套石膏脱水系统,工艺流程如图1所示。
- 1、下载文档前请自行甄别文档内容的完整性,平台不提供额外的编辑、内容补充、找答案等附加服务。
- 2、"仅部分预览"的文档,不可在线预览部分如存在完整性等问题,可反馈申请退款(可完整预览的文档不适用该条件!)。
- 3、如文档侵犯您的权益,请联系客服反馈,我们会尽快为您处理(人工客服工作时间:9:00-18:30)。
电厂脱硫石膏脱水困难的原因及解决方案我厂脱硫采用电石渣-石膏湿法脱硫技术,一炉一塔,不设增压风机、GGH。
设计入口SO2≦8000mg/m3,出口SO2≦35mg/m3。
电石渣浆液在吸收塔内对烟气进行逆流洗涤,通过物理、化学反映使烟气中的SO2与电石渣中钙离子发生反应,生成半水亚硫酸钙,再被鼓入浆液中的空气强制氧化生成二水硫酸钙,形成电石渣石膏浆液,由排浆泵将吸收塔内的浆液抽出,送往一级水力旋流器进行粒径╱密度分离,含固量5%左右的溢流,主要包括电石渣,灰尘等细小杂质颗粒重新返回吸收塔,含固量40%左右的底流,主要为石膏晶体送往二级真空皮带脱水机机进行脱水,形成含水量小于10%、石膏纯度90%以上的石膏饼,运送至厂外综合利用处理,从而除去烟气中98%以上的SO2污染物。
1石膏脱水困难的现象极其原因分析1.1现象1)滤布成型的石膏饼中出现分层现象,上层较湿,下层较干:2)石膏饼表面有一层湿黏,发亮的物质;3)石膏病断层有气泡破裂后留下的小孔。
4)下料口不结块、不滑落,成稀泥状,甚至出现下部粘稠、上部成流水状。
1.2原因分析影响石膏脱水的因素比较多,归纳起来,不外乎吸收塔物理化学反应过程的参数控制和脱水设备的运行状况。
1.2.1参数控制参数控制因素对于吸收塔,除了粉尘,上游烟气因素已不可控,因而在运行过程中,主要要控制吸收塔本身的浆液PH值、浆液密度。
吸收塔液位,粉尘含量和氧化风量,这些参数,影响石膏的结晶和水分的脱出,因为在石膏的生成过程中,如果参数控制不好,往往会生成层状、针状晶体,进一步向片状、簇状或花瓣形发展,其粘性大难以脱水,如亚硫酸钙晶体。
而石膏晶体应是短柱状,比前者颗粒大,易脱水。
另外,颗粒较小的物质如电石渣和粉尘等杂质,游离于石膏晶体之间,堵塞水分脱出通道,是水分难以脱出。
1.2.1.1浆液PH值。
浆液PH是控制脱硫反应过程的一个重要参数。
控制PH值就是控制过程的一个重要参数。
控制PH值就是控制进入吸收塔的电石渣浆液量。
因为SO2溶解过程中,离解出大量的H+,高PH的控制有助于SO2的溶解,而电石渣的溶解过程中,离解出大量的OH-,低PH值的控制有助于电石渣的溶解,所以PH值得过高过低都不利于石膏的形成,必须确定一个合理的PH值,否则过高的PH值使大量的电石渣混入石膏,无论是电石渣还是亚硫酸盐,由于其粒径比硫酸钙晶体小,不但降低石膏纯度,而且造成石膏脱水困难。
1.2.1.2浆液密度。
石膏的浆液密度反映了吸收塔中浆液的饱和情况,密度过低,则表明吸收塔石膏含量低,碳酸钙含量相对较大,此时如果将石膏浆液排除吸收塔,将导致石膏中的碳酸钙增加,浪费电石渣,由于其粒径小,既降低石膏品质又使石膏脱水困难;密度过高,则表明石膏浆中石膏和碳酸钙都过量,过量的硫酸钙抑制SO2的吸收,不利于碳酸钙溶解,此时若排除石膏,由于碳酸钙粒径小,造成石膏脱水困难。
1.2.1.3吸收塔液位吸收塔液位影响亚硫酸盐的充分氧化和石膏在塔内的停留时间。
液位低,使收塔中的氧化区缩短,亚硫酸盐得不到重复氧化,同时是储存在吸收塔中的石膏浆液相对减少,容易石浆液密度超限,使补入的电石渣浆液得不到充分的循环反映就排出吸收塔;液位高,氧化区延长,石膏纯度高,电石渣浆液循环反应充分,但密度一旦超限,由于石膏出不急,会发生密度过高使石膏出不急,会发生密度过高使石膏难于脱水的问题。
1.2.1.4粉尘含量原烟气中的飞灰进入吸收塔浆液中在一定程度上阻碍了SO2与脱硫剂的接触,降低了电石渣中Ca2+的溶解速率,同时飞灰中不断溶出的一些重金属如Hg、Mg、Cd、Zn等离子会抑制Ca2+与HSO3-的反应,“封闭”了吸收剂的活性。
一般要求吸收塔入口的烟尘含量不能超过200mg/m3,如果超过300mg/m3以上就容易出现这种现象。
如果烟尘含量测量仪表不准,最直接的方法可以取样沉淀,如果沉淀的固体物质中上部的黑色灰状物质超过总量的1/3(正常的应在1/4以下),就说明入口的烟尘含量太大了(如下图)。
现在由于电除尘器效率不是很好,吸收塔变成了吸尘器,吸收塔浆液发黑,起泡,脱水时在石膏表明有一层黑色物质,在这种状况下再坚持运行可想而知。
吸收塔浆液极易“中毒”。
一旦发生“中毒”现象,就需要将浆液全部排出臵换新鲜的浆液,造成很大的浪费,并影响脱硫系统的正常投入。
吸收塔浆液“中毒”后,需要半月时间纠正才能彻底改善,在此期间会浪费大量电石渣,排放大量浆液,提高了运行成本。
图片:左侧为浆液含灰量大沉淀的取样照片,右侧为正常浆液取样沉淀后的照片1.2.1.5氧化风量氧化风量影响亚硫酸盐的氧化,风量足则氧化充分,生成粗壮的石膏晶体,极易脱水,则,生成粘度较大的、颜色发黑,晶格不规则的小粒径亚硫酸盐的晶体,不利于石膏脱水。
同时,可溶性亚硫酸盐能提供可溶性碱量,当亚硫酸盐相对饱和度较高时,亚硫酸盐形成的碱性环境控制碳酸钙的溶解,从而导致浆液中的碳酸钙含量增大,使石膏纯度降低并难以脱水。
燃煤含硫量突然增大,而鼓入吸收塔的氧化空气量并未随之增加。
特别当SO2浓度超过设计值,氧化风量也是无法改变,由于严重氧化不足,会造成石膏结晶困难,增加脱水的难度。
氧化率下降时,浆液中的可溶性亚硫酸盐浓度增大,将拟制电石渣的溶解反应,石膏纯度也将下降,其中的电石渣将增大,由于电石渣的粒径较小,容易吸附到真空皮带机的滤布上,从而造成脱水困难。
这时若从吸收塔取样可以发现,浆液成灰白色,沉淀速度较慢,正常石膏浆液完全沉淀时间越20分钟,此时需要1小时左右。
1.2.1.6灰分等杂质含量一方面,由于氯根离子较碳酸根离子强,氯根极易与钙离子结合,并以氯化钙的形式存在于浆液中,从而使浆液中的钙离子浓度增大,由于氯离子效应,将抑制电石渣的离解,同时由于氯根较亚硫酸氢根离子强,因而抑制SO2溶解生成亚硫酸氢根,不利于石膏晶体的形成。
另一方面,杂质夹杂在石膏结晶之间,堵塞了游离水在结晶之间的通道,是石膏脱水变得困难,吸收塔内杂质含量的高低,可从皮带机上的石膏滤饼表面颜色间接了解,吸收塔内杂质的含量高时,石膏饼表面被一层呈深褐色物质覆盖,这层物质手感很黏,且很快会析出水分,这是因为杂质大多为烟气中的飞灰,质量相对较轻,当石膏浆液流入皮带机滤布上时,轻轻的杂质漂浮的将也得上部,而杂质颗粒较石膏颗粒细且粘性的,水分不易脱除。
1.2.2设备原因1.2.2.1石膏旋流器出现异常判断旋流器工作是否正常,可以采取检查及测量的方法。
测量的方法十分简单,分别取进石膏旋流器进口、出口的浆液,沉淀30分钟,对比一下含固量的差别,如果入口的含固量为出口的40-60%说明旋流子运行正常,如果高于60%以上就要检查更换旋流子了。
可想而知,如果进入真空皮带机的石膏浆液过稀,负压析出的水量过大。
脱水过程中形成不了真空,从而脱水效果也就变差。
1.2.2.2真空皮带机异常真空皮带机是石膏二次脱水的重要设备,脱水效果与浆液的性质、滤布的清洁程度有较大的关系。
汽液分离器的表计直观地反映了皮带机的真空,真空皮带机的真空与石膏含水率呈有规律的变化,皮带机真空升高,反映出滤水通过滤布时的压降增加,反应出石膏含水率增大。
其增加的原因,一是脱水设备运行不正常,如滤布冲洗不干净或滤布使用周期过长都会使皮带机脱水效果变差,脱水不畅;二是石膏浆液本身性质的变化,如浆液中小颗粒石膏晶体增多或浆液中的杂质含量增加等引起滤布过滤通道的堵塞,使浆液中的水不容易从滤布孔隙分离出来。
若要达到一定的固液分离效果,必须使真空升高。
根据现场取样化验以及运行调整等方面的情况分析,脱硫石膏脱水困难的原因有以下几个原因:1、电除尘投运率不能保证,电厂除灰运行经常出现退电场情况,造成脱硫吸收塔入口烟气含尘量增加,影响电石渣浆液分解反应吸收,长时间运行会造成浆液“中毒”。
根据化验取样化验分析,吸收塔浆液已属于“中毒”范畴。
2、吸收塔入口SO2含量长时间超出设计要求,氧化风机风量无法增加,造成吸收塔氧化率下降,浆液中的可溶性亚硫酸盐浓度增大,将拟制CaCO3的溶解,石膏纯度也将下降,其中的CaCO3将增大,由于CaCO3的粒径较小,容易吸附到真空皮带机的滤布上,从而造成脱水困难。
利旧真空皮带机出力有限,新增脱水机运行过程中故障,不能满足石膏脱水要求,造成吸收塔石膏浆液长时间高浓度,影响电石渣浆液分解,使浆液中电石渣含量增加,既浪费电石渣,又不能很好地脱除SO2。
2解决问题的对应方法2.1对电除尘全面检查,确保高压电场投入以及输灰系统的正常运行需要对加强对电除尘的规范运行及全面检查,分别查看各个高压柜的二次电流是否在合适的范围内。
在此提一点,如果发现高压柜全部在投,且电压正常,但效果还是较差时,就要对现在常用的顶部电场振打进行检查,振打好坏,频率如何都是关键。
再一个是灰斗振打,要保证定时振打,确保下灰顺畅。
输灰系统是否能满足输灰要求也是影响电场能否正常运行的重要因素,对除灰运行对输灰系统频次、时间以及输灰空气压力合理的调整,保证输灰畅通,进而保证电场的投运。
2.2严密监督电石渣质量。
我公司是采用电石渣,对此制定严格的管理制定,确保车车监督,严格考核。
日常积极与供货厂家沟通,让厂家清楚脱硫生产过程,明白脱硫的重要性及严肃性,加强前期管理,让电石渣供应明白只有脱硫稳定运行才能正常消耗电石渣,才能给集团带来利润。
通过我们的各项工作之后,目前质量非常稳定。
2.3降低燃煤含硫量大的问题,积极协调燃料配煤通过厂内燃煤管理部门,将先一日脱硫入口含硫量的数据通报给燃料搀配采购分配部门,及时指导其配煤工作,确保按脱硫运行中的烟气含硫量在设计值之内。
因此如果烟气中的含硫量过大,可以采取提高PH值的办法暂时维持脱硫运行。
但长时间还是以降低采购合格含硫量的燃煤为根本。
2.4加强对旋流站的监控及维修对于石膏旋流站的操作并不多,除了调整压力以外并没有太多手段。
日常要加强检查底流口液体流出的状态,根据经验判断,当沉砂嘴喷出的为雾状时效果为最佳,接近直流时效果已经变差(见下图),此时可以考虑更换沉砂嘴。
也可以测量一下,旋流后达不到40-50%的脱水效果就要考虑更换旋流器了。
再者就是停运后增加冲洗时间,防止浆液在旋流子中沉淀结垢。
图片:左侧为正常状态,右侧为沉砂嘴更换前的状态2.5保持真空皮带机的最佳工作状态皮带机的问题也就是关注滤布的状况,当被油污染后也会影响脱水效果,保持稳定的滤布冲洗水压力,调整合理的皮带转速,发现真空异常时及时清理真空罐中的杂物等等。
2.6提高浆液氧化程度若发现氧化风机电流、升高,氧化风压力升高,估计氧化风管已经结垢堵塞严重,在吸收塔检修的过程中要对氧化风管进行清垢处理。
减少电石渣供浆量及石膏浆液的排出量,加大浆液在吸收塔内的停留时间。
同时降低PH 的控制要求,一般保持在4.5-5.0即可。