砂型铸造工艺设计说明书
铸造工艺设计说明书

铸造⼯艺设计说明书铸造⼯艺设计说明书课程设计:机械⼯艺课程设计设计题⽬:底座铸造⼯艺设计班级:机⾃1103设计⼈:学号:指导教师:张锁梅、贾志新前⾔学⽣通过设计能获得综合运⽤过去所学过的全部课程进⾏机械制造⼯艺及结构设计的基本能⼒,为以后做好毕业设计、⾛上⼯作岗位进⾏⼀次综合训练和准备。
它要求学⽣全⾯地综合运⽤本课程及有关选修课程的理论和实践知识,进⾏零件加⼯⼯艺规程的设计和机床夹具的设计。
其⽬的是:(1)培养学⽣综合运⽤机械制造⼯程原理课程及专业课程的理论知识,结合⾦⼯实习、⽣产实习中学到的实践知识,独⽴地分析和解决机械加⼯⼯艺问题,初步具备设计中等复杂程度零件⼯艺规程的能⼒。
(2)培养学⽣能根据被加⼯零件的技术要求,运⽤夹具设计的基本原理和⽅法,学会拟订夹具设计⽅案,完成夹具结构设计,进⼀步提⾼结构设计能⼒。
(3)培养学⽣熟悉并运⽤有关⼿册、图表、规范等有关技术资料的能⼒。
(4)进⼀步培养学⽣识图、制图、运算和编写技术⽂件的基本技能。
(5)培养学⽣独⽴思考和独⽴⼯作的能⼒,为毕业后⾛向社会从事相关技术⼯作打下良好的基础。
⽬录⼀、⼯艺审核 (1)1.数量与材料 (1)2.图样 (1)3.零件的结构性 (1)⼆、成形⼯艺设计 (1)1.确定⼯艺⽅案 (1)(1)浇注位置的选择 (2)(2)分型⾯的选择 (2)2.确定铸造⼯艺参数 (4)(1)机械加⼯余量和铸出孔 (4)(2)浇注位置的选择 (5)(3)拔模斜度 (5)(4)铸造收缩率 (6)3.砂芯设计 (6)4.浇注系统的设计 (6)5. 冷铁的设置 (6)三、⼼得体会 (7)⼀、⼯艺审核1、数量与材料由零件图可知,该零件结构⽐较简单,但是形状不是很规则,⼯作条件⼀般以承受压⼒为主,故要求该零件有良好的刚性和强度。
另外,根据零件图的要求,该底座零件为单件⼩批量⽣产,另外材料选⽤灰铸铁HT200,流动性较好,适于铸造。
2、图样该零件图给出了主视图、左视图、俯视图3个视图。
铸造工艺设计说明书

铸造工艺设计——打造优质铸件铸造工艺设计是保证铸件质量和铸造效率的关键步骤。
具体来说,它包括了几个方面:
首先,要合理选型。
根据铸件的形状、尺寸和性质,选择合适的
铸造材料。
此外,要结合铸造生产的技术要求,选择适宜的铸型材料
和涂料。
其次,要科学施工。
铸造生产中,各施工环节都要注意严格按照
程序操作,杜绝人为失误。
同时,要利用现代科技手段,提高铸造精
度和生产效率。
再次,要科学排版。
合理布局生产车间,明确职责分工,保证生
产流程顺畅。
此外,还需要严格执行环保标准,保护生态环境。
最后,要严格质量控制。
采用严格的检验标准和检验方法,确保
铸件质量。
对于不合格产品,要及时处理,并总结教训,不断改进工
艺和工艺设备。
总之,铸造工艺设计是保证铸件质量和铸造效率的关键步骤。
只
有科学、规范、精准地实施铸造工艺设计,才能打造出优质、合格的
铸件,为工业生产和国民经济发展做出更大的贡献。
铸造工艺设计说明书
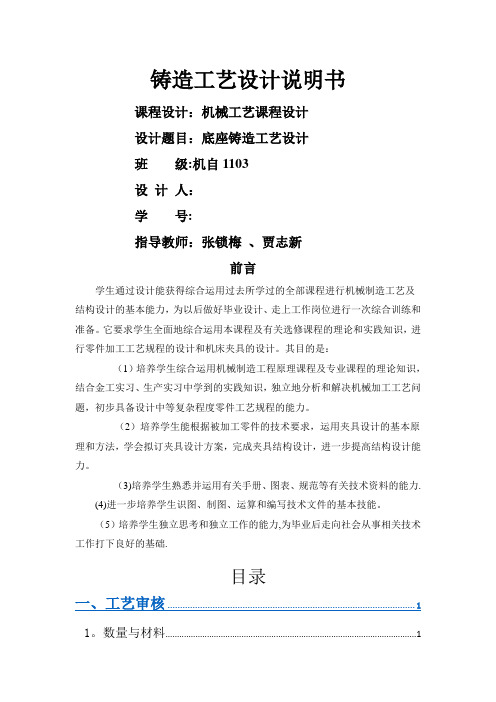
铸造工艺设计说明书课程设计:机械工艺课程设计设计题目:底座铸造工艺设计班级:机自1103设计人:学号:指导教师:张锁梅、贾志新前言学生通过设计能获得综合运用过去所学过的全部课程进行机械制造工艺及结构设计的基本能力,为以后做好毕业设计、走上工作岗位进行一次综合训练和准备。
它要求学生全面地综合运用本课程及有关选修课程的理论和实践知识,进行零件加工工艺规程的设计和机床夹具的设计。
其目的是:(1)培养学生综合运用机械制造工程原理课程及专业课程的理论知识,结合金工实习、生产实习中学到的实践知识,独立地分析和解决机械加工工艺问题,初步具备设计中等复杂程度零件工艺规程的能力。
(2)培养学生能根据被加工零件的技术要求,运用夹具设计的基本原理和方法,学会拟订夹具设计方案,完成夹具结构设计,进一步提高结构设计能力。
(3)培养学生熟悉并运用有关手册、图表、规范等有关技术资料的能力.(4)进一步培养学生识图、制图、运算和编写技术文件的基本技能。
(5)培养学生独立思考和独立工作的能力,为毕业后走向社会从事相关技术工作打下良好的基础.目录一、工艺审核 (1)1。
数量与材料 (1)2。
图样 (1)3。
零件的结构性 (1)二、成形工艺设计 (1)1.确定工艺方案 (1)(1)浇注位置的选择 (2)(2)分型面的选择 (2)2。
确定铸造工艺参数 (4)(1)机械加工余量和铸出孔 (4)(2)浇注位置的选择 (5)(3)拔模斜度 (5)(4)铸造收缩率 (6)3.砂芯设计 (6)4.浇注系统的设计 (6)5。
冷铁的设置 (6)三、心得体会 (7)一、工艺审核1、数量与材料由零件图可知,该零件结构比较简单,但是形状不是很规则,工作条件一般以承受压力为主,故要求该零件有良好的刚性和强度.另外,根据零件图的要求,该底座零件为单件小批量生产,另外材料选用灰铸铁HT200,流动性较好,适于铸造。
2、图样该零件图给出了主视图、左视图、俯视图3个视图。
铸造工艺设计说明书

铸造⼯艺设计说明书铸造⼯艺设计说明书⽬录1. 零件结构分析 (3)1.1. 零件信息 (3)1.2. 技术要求 (3)2. 铸造⼯艺⽅案分析 (5)2.1. 铸造⽅法的确定 (5)2.2. 分型⾯的选择 (5)2.3. 铸件浇注位置的确定 (7)3. 铸造⼯艺参数 (9)3.1. 铸件尺⼨公差 (9)3.2. 铸件重量公差 (9)3.3. 机械加⼯余量 (9)3.4. 铸造收缩率 (9)3.5. 起模斜度 (9)3.6. 最⼩铸出孔及槽 (10)3.7. ⼯艺补正量 (10)3.8. 分型负数 (10)3.9. 反变形量 (10)3.10. 砂芯负数 (11)3.11. ⾮加⼯壁厚的负余量 (11)3.12. 分型负数 (11)4. 砂芯设计 (12)4.1. 砂芯的概念 (12)4.2. 芯头设计 (12)5. 浇注系统设计 (16)5.1. 浇注系统设计原则 (16)5.2. 浇注系统位置确定 (17)5.3. 浇注系统类型确定 (17)5.4. 浇注系统尺⼨计算 (17)6. 冒⼝及冷铁 (22)6.1. 冒⼝补缩原则 (22)6.2. 冒⼝及冷铁位置个数的选择 (22)6.3. 冒⼝种类选择及参数计算 (23)6.4. 铸件成品率 (25)1. 零件结构分析1.1. 零件信息产品名称:⽀架材料:铸钢外形尺⼨:91×42×66cm 3 质量:463Kg g 463000cm 58983cm g 85.7v m 33=≈?=?=ρ⽣产批量:成批⼤量⽣产。
造型⽅法:⼿⼯造型其零件⽰意图如下图1.2. 技术要求铸件重要的⼯作表⾯,在铸造是不允许有⽓孔、砂眼、渣孔等缺陷。
2.铸造⼯艺⽅案分析2.1.铸造⼯艺的确定铸造⼯艺包括:造型⽅法、造芯⽅法、铸造⽅法及铸型种类的选择2.1.1.造型⽅法、造芯⽅法的选择根据⼿⼯造型和机器造型的特点,选择⼿⼯造型2.1.2.铸造⽅法的选择根据零件的各参数,对照表格中的项⽬⽐较,选择砂型铸造。
支座砂型铸造工艺设计说明书
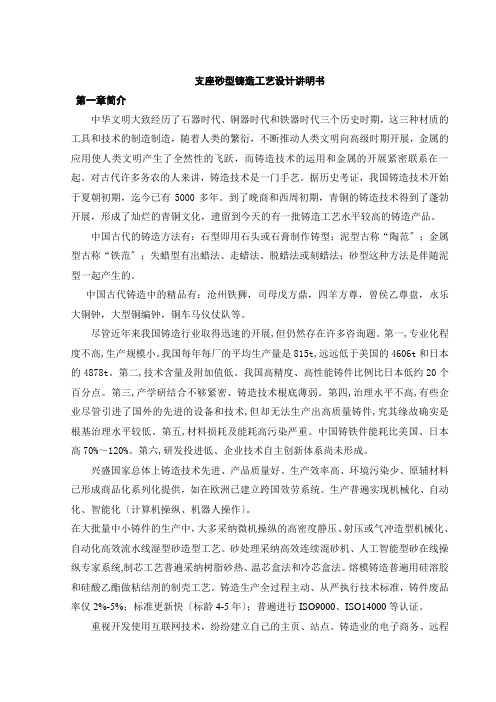
支座砂型铸造工艺设计讲明书第一章简介中华文明大致经历了石器时代、铜器时代和铁器时代三个历史时期,这三种材质的工具和技术的制造制造,随着人类的繁衍,不断推动人类文明向高级时期开展,金属的应用使人类文明产生了全然性的飞跃,而铸造技术的运用和金属的开展紧密联系在一起。
对古代许多务农的人来讲,铸造技术是一门手艺。
据历史考证,我国铸造技术开始于夏朝初期,迄今已有5000多年。
到了晚商和西周初期,青铜的铸造技术得到了蓬勃开展,形成了灿烂的青铜文化,遗留到今天的有一批铸造工艺水平较高的铸造产品。
中国古代的铸造方法有:石型即用石头或石膏制作铸型;泥型古称“陶范〞;金属型古称“铁范〞;失蜡型有出蜡法、走蜡法、脱蜡法或刻蜡法;砂型这种方法是伴随泥型一起产生的。
中国古代铸造中的精品有:沧州铁狮,司母戊方鼎,四羊方尊,曾侯乙尊盘,永乐大铜钟,大型铜编钟,铜车马仪仗队等。
尽管近年来我国铸造行业取得迅速的开展,但仍然存在许多咨询题。
第一,专业化程度不高,生产规模小。
我国每年每厂的平均生产量是815t,远远低于美国的4606t和日本的4878t。
第二,技术含量及附加值低。
我国高精度、高性能铸件比例比日本低约20个百分点。
第三,产学研结合不够紧密、铸造技术根底薄弱。
第四,治理水平不高,有些企业尽管引进了国外的先进的设备和技术,但却无法生产出高质量铸件,究其缘故确实是根基治理水平较低。
第五,材料损耗及能耗高污染严重。
中国铸铁件能耗比美国、日本高70%~120%。
第六,研发投进低、企业技术自主创新体系尚未形成。
兴盛国家总体上铸造技术先进、产品质量好、生产效率高、环境污染少、原辅材料已形成商品化系列化提供,如在欧洲已建立跨国效劳系统。
生产普遍实现机械化、自动化、智能化〔计算机操纵、机器人操作〕。
在大批量中小铸件的生产中,大多采纳微机操纵的高密度静压、射压或气冲造型机械化、自动化高效流水线湿型砂造型工艺。
砂处理采纳高效连续混砂机、人工智能型砂在线操纵专家系统,制芯工艺普遍采纳树脂砂热、温芯盒法和冷芯盒法。
砂型铸造工艺设计..
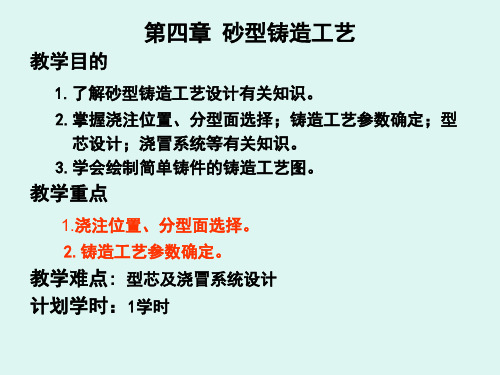
(3)中间注入式浇注系统
62
中注式浇注系统
这是一种介于顶注和底注之间的注 入方法,既降低了液流落下的高度,又 使温度的分布较为均匀,内浇道处在分 型面上,便于开设和选择部位。因此, 这种浇注系统的应用很广。
63
(4)阶梯注入式浇注系统
阶梯注入式浇注系统
阶梯注入式浇注系统亦称阶梯式浇注 系统,是在铸件高度上设二层或二层以 上的内浇道,它兼备了顶注式、底注式 和中间注入式浇注系统的优点。
对于要求比较高的单件生产的重要铸件和大量生产的铸件,除要 详细绘制铸造工艺图,填写工艺卡以外,还应绘制铸件图、铸型装配 图以及大量的工装图,如模样图、模板图、砂箱图、芯合图、下芯夹 具图,检验样板及量具图等。
三、铸造工艺设计的一般步骤
1.对零件图纸进行审核和进行铸造工艺性分析 2.选择铸造方法 3.确定铸造工艺方案 4.绘制铸造工艺图 5.绘制铸件图 6.填写铸造工艺卡和绘制铸型装配图 7.绘制各种铸造工艺装备图纸
1.分型面应设在铸件最大截面处,以保证模样从型腔中顺利取出
2.应使造型工艺简化 ★应尽量使分型面平直,以简化模具制造及造型工艺,避免挖砂造型
★尽可能减少铸件的分型面,尽量做到只有一个分型面
★应使型芯和活块数量尽量减少。
3.应使铸件全部或大部放在同一砂箱。
4.应尽量使型腔及主要型芯位于下型,以便于造型、下芯、 合型及检验。
<50 3.5~4.5 2.5~3.5 4.0~5.0 3.0~4.0 4.5~6.0 3.5~4.5 5.0~7.0 4.0~5.0 6.0~7.0 4.0~5.5 50~120 4.0~4.5 3.0~3.5 4.5~5.0 3.5~4.0 5.0~6.0 4.0~4.5 6.0~7.0 4.5~5.0 6.5~7.5 5.0~5.5 5.0~5.5 4.0~4.5 6.0~7.0 4.5~5.0 6.5~7.0 4.5~5.5 7.0~8.0 5.0~6.0 6.5~7.0 5.0~6.0 7.0~8.0 5.0~6.0 7.5~8.0 5.5~6.0 7.5~9.0 6.5~7.0 8.0~9.0 5.5~7.0 8.5~10 6.5~7.5 120~260 260~500 500~800 800~1250ຫໍສະໝຸດ 60顶注式浇注系统
第四章砂型铸造工艺设计

第四章砂型铸造工艺设计1.引言砂型铸造是一种常见的金属成型工艺,广泛应用于各种金属件的生产。
本章将介绍砂型铸造工艺的设计过程,包括模具设计、砂型制备、铸造工艺参数的确定等。
2.模具设计模具设计是砂型铸造工艺的基础,直接影响到铸件的质量和生产效率。
在模具设计中,需要考虑以下几个方面的因素:2.1铸件结构首先需要根据铸件的结构确定模具的形状和尺寸。
一般情况下,模具应该尽量符合铸件的外形,并考虑到铸件的收缩率和加工余量。
2.2浇注系统浇注系统是指从熔融金属到铸件腔室的流动路径。
浇注系统应该保证金属液能够均匀地填充整个铸件腔室,并避免产生气孔和夹杂物。
一般情况下,浇注系统包括浇口、浇杯、导流槽等。
2.3排气系统排气系统是指从砂型中排出空气和燃烧产物的通道。
排气系统应该保证空气能够顺利地从砂型中排出,避免产生气孔和夹杂物。
一般情况下,排气系统包括排气槽、排气孔等。
2.4垫块和芯垫块和芯是为了形成复杂形状的内部空间而使用的辅助构件。
垫块和芯应该和模具保持一定的间隙,并考虑到铸件的收缩率和加工余量。
3.砂型制备砂型制备是砂型铸造工艺的核心环节,直接影响到铸件的表面质量和尺寸精度。
在砂型制备中,需要注意以下几个方面的问题:3.1砂料的选择砂料的选择应该根据铸件的材质和尺寸来确定。
一般情况下,砂料应该具有一定的粘结力和抗压强度,并且易于流动和散落。
3.2砂型的填充砂型的填充应该保证砂料能够均匀地填充整个模具腔室,并且能够与铸件的表面接触紧密。
填充过程中需要注意控制填充速度和压实度,避免产生气孔和夹杂物。
3.3砂型的硬化砂型的硬化是指将填充好的砂料固化成为坚硬的砂型。
硬化过程中需要注意控制硬化时间和硬化温度,避免产生裂纹和变形。
4.铸造工艺参数的确定铸造工艺参数的确定是砂型铸造工艺的重要环节,直接影响到铸件的质量和生产效率。
在确定铸造工艺参数时,需要考虑以下几个方面的因素:4.1浇注温度浇注温度应该根据铸件的材质和尺寸来确定。
砂型铸造说明书
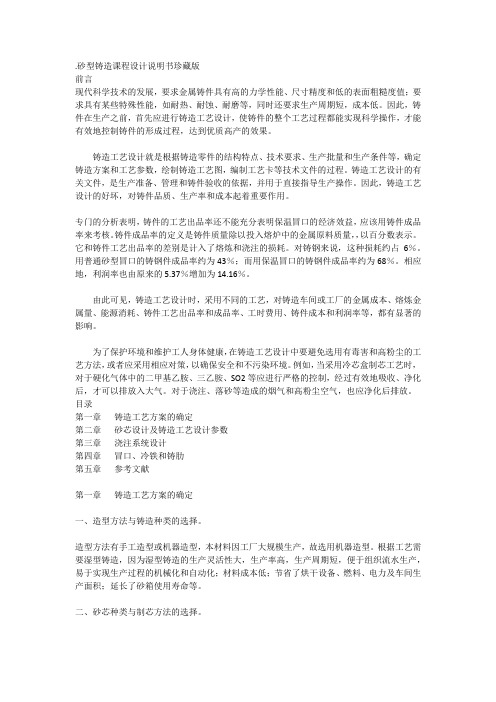
.砂型铸造课程设计说明书珍藏版前言现代科学技术的发展,要求金属铸件具有高的力学性能、尺寸精度和低的表面粗糙度值;要求具有某些特殊性能,如耐热、耐蚀、耐磨等,同时还要求生产周期短,成本低。
因此,铸件在生产之前,首先应进行铸造工艺设计,使铸件的整个工艺过程都能实现科学操作,才能有效地控制铸件的形成过程,达到优质高产的效果。
铸造工艺设计就是根据铸造零件的结构特点、技术要求、生产批量和生产条件等,确定铸造方案和工艺参数,绘制铸造工艺图,编制工艺卡等技术文件的过程。
铸造工艺设计的有关文件,是生产准备、管理和铸件验收的依据,并用于直接指导生产操作。
因此,铸造工艺设计的好坏,对铸件品质、生产率和成本起着重要作用。
专门的分析表明,铸件的工艺出品率还不能充分表明保温冒口的经济效益,应该用铸件成品率来考核。
铸件成品率的定义是铸件质量除以投入熔炉中的金属原料质量,,以百分数表示。
它和铸件工艺出品率的差别是计入了熔炼和浇注的损耗。
对铸钢来说,这种损耗约占6%。
用普通砂型冒口的铸钢件成品率约为43%;而用保温冒口的铸钢件成品率约为68%。
相应地,利润率也由原来的5.37%增加为14.16%。
由此可见,铸造工艺设计时,采用不同的工艺,对铸造车间或工厂的金属成本、熔炼金属量、能源消耗、铸件工艺出品率和成品率、工时费用、铸件成本和利润率等,都有显著的影响。
为了保护环境和维护工人身体健康,在铸造工艺设计中要避免选用有毒害和高粉尘的工艺方法,或者应采用相应对策,以确保安全和不污染环境。
例如,当采用冷芯盒制芯工艺时,对于硬化气体中的二甲基乙胺、三乙胺、SO2等应进行严格的控制,经过有效地吸收、净化后,才可以排放入大气。
对于浇注、落砂等造成的烟气和高粉尘空气,也应净化后排放。
目录第一章铸造工艺方案的确定第二章砂芯设计及铸造工艺设计参数第三章浇注系统设计第四章冒口、冷铁和铸肋第五章参考文献第一章铸造工艺方案的确定一、造型方法与铸造种类的选择。
- 1、下载文档前请自行甄别文档内容的完整性,平台不提供额外的编辑、内容补充、找答案等附加服务。
- 2、"仅部分预览"的文档,不可在线预览部分如存在完整性等问题,可反馈申请退款(可完整预览的文档不适用该条件!)。
- 3、如文档侵犯您的权益,请联系客服反馈,我们会尽快为您处理(人工客服工作时间:9:00-18:30)。
设计说明书题目:砂型铸造压工艺及模具设计年级、专业:姓名:学号:指导教师:完成时间:目录第一章、简介 (5)1.1.我国铸造技术发展现状 (5)1.2.我国铸造未来发展趋势 (5)第二章、铸造工艺方案的确定 (6)2.1.产品的生产条件、结构及技术要求 (6)2.2.零件铸造工艺性 (6)2.3.造型,造芯方法的选择 (7)2.4.浇注位置的确定 (8)2.5.分型面的确定 (9)2.6.砂箱中铸件数量及排列方式确定 (9)第三章、铸造工艺参数及砂芯设计 (11)3.1.工艺设计参数确定 (11)3.1.1.铸件尺寸公差 (11)3.1.2.机械加工余量 (11)3.1.3.铸造收缩率 (12)3.1.4.起模斜度 (12)3.1.5.最小铸出孔和槽 (12)3.1.6.铸件在砂型内的冷却时间 (13)3.1.7.铸件重量公差 (13)3.1.8.工艺补正量 (13)3.1.9.分型负数 (13)3.2.砂芯设计 (13)3.2.1.芯头的设计 (15)3.2.2.砂芯的定位结构 (16)3.2.3.芯骨设计 (17)3.2.4.砂芯的排气 (17)第四章、浇注系统及冒口、出气孔等设计 (18)4.1.浇注系统的设计 (18)4.1.1.选择浇注系统类型 (18)4.1.2.确定内浇道在铸件上的位置、数目、金属引入方向 (18)4.1.3.决定直浇道的位置和高度 (19)4.1.4计算浇注时间并核算金属上升速度 (20)4.1.5.计算阻流截面积 (20)4.1.6.计算直浇道截面积 (20)4.1.7.浇口窝的设计 (21)4.2.冒口的设计 (22)4.3.出气孔的设计 (22)第五章、铸造工艺装备设计 (23)5.1.模样的设计 (23)5.1.1.模样材料的选用 (23)5.1.2.金属模样尺寸的确定 (23)5.1.3.壁厚与加强筋的设计 (23)5.1.4.金属模样的技术要求 (23)5.1.5.金属模样的生产方法 (24)5.2.模板的设计 (24)5.2.1.模底板材料的选用 (24)5.2.2.模底板尺寸确定 (24)5.2.3.模底板与砂箱的定位 (24)5.3.芯盒的设计 (25)5.3.1.芯盒的类型和材质 (25)5.3.2.芯盒的结构设计 (25)5.4.砂箱的设计 (25)5.4.1.砂箱的材质及尺寸 (25)5.4.2.砂箱型壁尺寸及圆角尺寸 (25)5.4.3.砂箱排气孔尺寸 (26)第六章、砂型铸造设备选用 (27)6.1.造型工部设备选用 (27)6.2.制芯工部设备选用 (27)6.3.溶化工部设备选用 (27)6.4.砂处理工部设备选用 (27)6.5.清理工部设备选用 (27)总结 (28)参考文献 (29)第一章、简介1.1.我国铸造技术发展现状尽管近年来我国铸造行业取得迅速的发展,但仍然存在许多问题。
第一,专业化程度不高,生产规模小。
我国每年每厂的平均生产量是815t,远远低于美国的4606t和日本的4878t。
第二,技术含量及附加值低。
我国高精度、高性能铸件比例比日本低约20个百分点。
第三,产学研结合不够紧密、铸造技术基础薄弱。
第四,管理水平不高,有些企业尽管引进了国外的先进的设备和技术,但却无法生产出高质量铸件,究其原因就是管理水平较低。
第五,材料损耗及能耗高污染严重。
中国铸铁件能耗比美国、日本高70%~120%。
第六,研发投入低、企业技术自主创新体系尚未形成。
1.2.我国铸造未来发展趋势自中国加入WTO以来,我国铸造行业面临机遇与挑战。
其未来发展将集中在以下几方面。
第一,鼓励企业重组发展专业化生产,包括铸件大型化和轻量化生产。
第二,加大科技投入切实推动自主创新,实现铸件的精确化生产和数字化铸造。
第三,培养专业人才加强职工技术培训。
第四,大力降低能耗抓好环境保护,实现清洁化铸造。
第二章、铸造工艺方案的确定2.1.产品的生产条件、结构及技术要求●产品生产性质——中批量生产●零件材质——HT20-40●零件的外型示意图如图2.1所示,外形轮廓尺寸为234×178×225mm,主要壁厚10-22mm,最大壁厚22mm,为一小型铸件;铸件除满足几何尺寸精度及材质方面的要求外,无其他特殊技术要求。
图2.1.零件图2.2.零件铸造工艺性零件结构的铸造工艺性是指零件的结构应符合铸造生产的要求,易于保证铸件品质,简化铸件工艺过程和降低成本。
审查、分析应考虑如下几个方面:1.铸件应有合适的壁厚,为了避免浇不到、冷隔等缺陷,铸件不应太薄。
2.铸件结构不应造成严重的收缩阻碍,注意薄壁过渡和圆角,铸件薄厚壁的相接拐弯等厚度的壁与壁的各种交接,都应采取逐渐过渡和转变的形式,并应使用较大的圆角相连接,避免因应力集中导致裂纹缺陷。
3.铸件内壁应薄于外壁,铸件的内壁和肋等,散热条件较差,应薄于外壁,以使内、外壁能均匀地冷却,减轻内应力和防止裂纹。
4.壁厚力求均匀,减少肥厚部分,防止形成热节。
5.利于补缩和实现顺序凝固。
6.防止铸件翘曲变形。
7.避免浇注位置上有水平的大平面结构。
对于该产品的铸造工艺性审查、分析如下:产品轮廓尺寸为234×178×225mm。
砂型铸造条件下该轮廓尺寸允许的最小壁厚查《铸造工艺学》表3-2-1得:最小允许壁厚为6~8 mm。
而本次设计的产品的最小壁厚为10mm。
符合要求。
产品设计壁厚较为均匀,两壁相连初采用了加强肋,可以有效构成热节,不易产生热烈。
2.3.造型,造芯方法的选择产品轮廓尺寸为234×178×225mm,铸件尺寸较小,属于中型零件,且要大批量生产。
采用湿型粘土砂造型灵活性大,生产率高,生产周期短,便于组织流水生产,易于实现机械化和自动化,材料成本低,节省烘干设备、燃料、电力等,还可延长砂箱使用寿命。
因此,采用湿型粘土砂机器造型,模样采用金属模是合理的。
在造芯用料及方法选择中,如用粘土砂制作砂芯原料成本较低,但是烘干后容易产生裂纹,容易变形。
在大批量生产的条件下,由于需要提高造芯效率,且常要求砂芯具有高的尺寸精度,此工艺所需的砂芯采用热芯盒法生产砂芯,以增加其强度及保证铸件质量。
选择使用射芯工艺生产砂芯。
采用热芯盒制芯工艺热芯盒法制芯,是用液态固性树脂粘结剂和催化剂制成的一种芯砂,填入加热到一定的芯盒内,贴近芯盒表面的砂芯受热,其粘结剂在很短的时间内硬化。
而且只要砂芯表层有数毫米的硬壳即可自芯取出,中心部分的砂芯利用余热可自行硬化。
2.4.浇注位置的确定铸件的浇注位置是指浇注时铸件在型内所处的状态和位置。
确定浇注位置是铸造工艺设计中重要的环节,关系到铸件的内在质量,铸件的尺寸精度及造型工艺过程的难易程度。
初步对本次设计产品的浇注位置的确定有:方案如图2.2图2.2 浇注位置确定方案确定浇注位置应注意以下原则:1.铸件的重要部分应尽量置于下部2.重要加工面应朝下或直立状态3.使铸件的答平面朝下,避免夹砂结疤内缺陷4.应保证铸件能充满5.应有利于铸件的补缩6.避免用吊砂,吊芯或悬臂式砂芯,便于下芯,合箱及检验综合以上原则,本设计中的方案合理,科学,可行。
2.5.分型面的确定分型面是指两半铸型相互接触的表面。
分型面的优劣在很大程度上影响铸件的尺寸精度、成本和生产率。
初步对产品图进行分型有:方案如图2.3:图2.3 分型面确定方案一而选择分型面时应注意一下原则:应使铸件全部或大部分置于同一半型内应尽量减少分型面的数目分型面应尽量选用平面便于下芯、合箱和检测不使砂箱过高受力件的分型面的选择不应削弱铸件结构强度注意减轻铸件清理和机械加工量2.6.砂箱中铸件数量及排列方式确定产品单件质量约为16.5kg,因此看铸件为中小型简单件。
考虑到年产量不是很高,因此采用一箱一件结构,减少模具成本。
初步选取砂箱尺寸由《铸造实用手册》查表1.5-45得:上箱为500×400×357mm 下箱为500×400×347mm铸件在砂箱中排列最好放模具中心,这样金属液作用于上砂型的抬芯力均匀,也有利于浇注系统安排,在结合已经确定分型面及浇注位置以及砂箱尺寸,基本确定铸件在砂箱内的位置。
第三章、铸造工艺参数及砂芯设计3.1.工艺设计参数确定铸造工艺设计参数通常是指铸型工艺设计时需要确定的某些数据,这些工艺数据一般都与模样及芯盒尺寸有关,及与铸件的精度有密切关系,同时也与造型、制芯、下芯及合箱的工艺过程有关。
这些工艺数据主要是指加工余量、起模斜度、铸造收缩率、最小铸出孔、型芯头尺寸、铸造圆角等。
工艺参数选取的准确、合适,才能保证铸件尺寸精确,使造型、制芯、下芯及合箱方便,提高生产率,降低成本。
3.1.1.铸件尺寸公差铸件尺寸公差是指铸件公称尺寸的两个允许的极限尺寸之差。
在两个允许极限尺寸之内,铸件可满足机械加工,装配,和使用要求。
本次产品为砂型铸造机器造型中批量生产,由《铸造工艺设计》查表1-10得:尺寸公差为CT8~12级,取CT9级。
轮廓尺寸为234×178×225mmmm,由《铸造工艺设计》查表1-9得:尺寸公差数值为2mm。
3.1.2.机械加工余量机械加工余量是铸件为了保证其加工面尺寸和零件精度,应有加工余量,即在铸件工艺设计时预先增加的,而后在机械加工时又被切去的金属层厚度。
由《铸造工艺设计》查表1-13得:加工余量为E~G级,取G级。
轮廓尺寸为φ234×178×225mm,由《铸造工艺设计》查表1-12得:加工余量数值为2-2.25m,取2mm。
但在分型面及浇注系统设置中,不得已将重要加工面底面朝上放置,这样使其容易产生气孔、非金属夹杂物等缺陷,所以将采取适当加大加工余量的方法使其在加工后不出现缺陷。
将底面的加工余量调整为0.5mm,可以忽略不计。
3.1.3.铸造收缩率铸造收缩率又称铸件线收缩率,用模样与铸件的长度差除以模样长度的百分比表示:ε=[(L1-L2)/L1]*100%ε—铸造收缩率L1—模样长度L2—铸件长度产品受阻收缩率由《铸造工艺设计》查表1-14得:受阻收缩率为0.9-0.95%。
3.1.4.起模斜度为了方便起模,在模样、芯盒的出模方向留有一定斜度,以免损坏砂型或砂芯。
这个斜度,称为起模斜度。
起模斜度应在铸件上没有结构斜度的,垂直于分型面的表面上应用。
初步设计的起模斜度如下:外型模的边高357mm的起模斜度由《铸造工艺设计》查表1-15得:粘土砂造型外表面起模斜度为а=0°15',a=1.2mm3.1.5.最小铸出孔和槽零件上的孔、槽、台阶等,究竟是铸出来好还是靠机械加工出来好,这应该从品质及经济角度等方面考虑。
一般来说,较大的孔、槽等应该铸出来,以便节约金属和加工工时,同时还可以避免铸件局部过厚所造成热节,提高铸件质量。