桥梁工程论文
桥梁工程论文(集锦15篇)
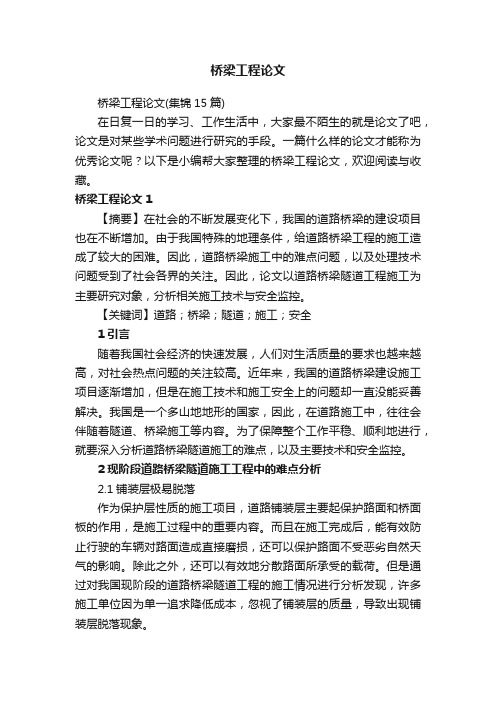
桥梁工程论文桥梁工程论文(集锦15篇)在日复一日的学习、工作生活中,大家最不陌生的就是论文了吧,论文是对某些学术问题进行研究的手段。
一篇什么样的论文才能称为优秀论文呢?以下是小编帮大家整理的桥梁工程论文,欢迎阅读与收藏。
桥梁工程论文1【摘要】在社会的不断发展变化下,我国的道路桥梁的建设项目也在不断增加。
由于我国特殊的地理条件,给道路桥梁工程的施工造成了较大的困难。
因此,道路桥梁施工中的难点问题,以及处理技术问题受到了社会各界的关注。
因此,论文以道路桥梁隧道工程施工为主要研究对象,分析相关施工技术与安全监控。
【关键词】道路;桥梁;隧道;施工;安全1引言随着我国社会经济的快速发展,人们对生活质量的要求也越来越高,对社会热点问题的关注较高。
近年来,我国的道路桥梁建设施工项目逐渐增加,但是在施工技术和施工安全上的问题却一直没能妥善解决。
我国是一个多山地地形的国家,因此,在道路施工中,往往会伴随着隧道、桥梁施工等内容。
为了保障整个工作平稳、顺利地进行,就要深入分析道路桥梁隧道施工的难点,以及主要技术和安全监控。
2现阶段道路桥梁隧道施工工程中的难点分析2.1铺装层极易脱落作为保护层性质的施工项目,道路铺装层主要起保护路面和桥面板的作用,是施工过程中的重要内容。
而且在施工完成后,能有效防止行驶的车辆对路面造成直接磨损,还可以保护路面不受恶劣自然天气的影响。
除此之外,还可以有效地分散路面所承受的载荷。
但是通过对我国现阶段的道路桥梁隧道工程的施工情况进行分析发现,许多施工单位因为单一追求降低成本,忽视了铺装层的质量,导致出现铺装层脱落现象。
2.2钢筋锈蚀情况频出钢筋是支撑桥体质量的重要部分,关系到桥梁的建设和安全使用。
一旦钢筋出现质量问题,不仅会大大缩短桥梁的使用寿命,还会严重威胁人们的生命安全。
因此,我们在进行道路桥梁隧道项目施工时,首先要选择质量较好的钢筋材料,然后在施工中做好钢筋质量防护工作,在道路桥梁隧道的实际使用过程中,做好钢筋质量的维护工作。
桥梁毕业论文范文(6篇)

桥梁毕业论文范文(6篇)桥梁毕业论文范文第1篇近年来我国的各项事业的进展都渐渐的步入正轨,关于道路桥梁的建设要与目前的经济进展速度相适应。
将建筑道路桥梁中预应力的作用充分的展现出来,更好地满意人们对于出行的需要,保证道路桥梁施工的进展迈向更好的方向进展。
1预应力技术1.1预应力技术的优势预应力技术的应用并非是仅仅局限在道路桥梁的结构当中,还更宽阔的应用在山体加固、推顶修理等方面。
预应力技术的使用可以有效地削减道路桥梁施工中材料铺张,同时还兼具有施工设计平安运行便捷的特点。
因此预应力技术的使用对于促进我国整体的道路桥梁修建水平的提高有着非比寻常的作用,我们不难发觉,锚具在该预应力加固中发挥着传达张拉力的作用,而这一作用的发挥就使得混凝土构件的预压应力得以产生,桥梁工程的施工质量就得到了较好保证。
1.2预应力技术的应用(1)钢筋混凝土结构的应用。
钢筋混凝土结构中特殊简单消失混凝土裂缝等难以预防的质量问题,尤其是在道路桥梁等大型钢筋混凝土机构中更是简单消失裂缝[1]。
但通过预应力技术的应用则可以有效地削减这一问题,在道路桥梁的钢筋混凝土结构构建之前要将混凝土内部的受拉区进行拉伸,通过钢筋自身拥有的回力,使得混凝土的受拉区先感受到钢筋赐予的压力。
也就是说在混凝土受到来自外部的压力的同时要先将承受的来自钢筋的预压力抵消,这就有效地削减了混凝土的延展,以此来达到缓和混凝土结构消失裂缝的问题。
在某道路工程的施工中,施工单位应用了预应力钢筋张拉的施工技术,这一施工技术借助混凝土与预应力筋的粘牢固现了混凝土的预压应力产生,同时又通过应用锚具传达张拉力,实现了混凝土构件的预压应力产生,这就使得该桥梁工程的结构裂缝问题消失得到了较好抑制。
(2)碳纤维片的应用。
介于道路桥梁的跨度较大,整体构件的抗弯性能要求比较的高。
但道路桥梁的钢筋混凝土结构受拉区与受压区的的反应力量都比较的强大,为了更好的解决整个建筑构建的受弯力量,投入的成本比较的高。
道路桥梁工程技术论文
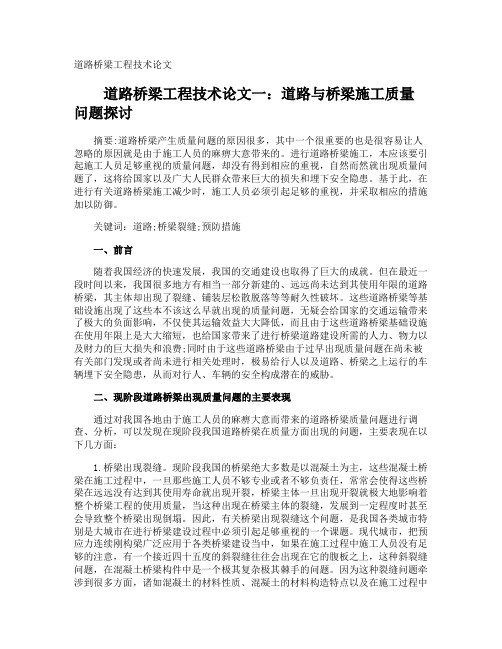
道路桥梁工程技术论文道路桥梁工程技术论文一:道路与桥梁施工质量问题探讨摘要:道路桥梁产生质量问题的原因很多,其中一个很重要的也是很容易让人忽略的原因就是由于施工人员的麻痹大意带来的。
进行道路桥梁施工,本应该要引起施工人员足够重视的质量问题,却没有得到相应的重视,自然而然就出现质量问题了,这将给国家以及广大人民群众带来巨大的损失和埋下安全隐患。
基于此,在进行有关道路桥梁施工减少时,施工人员必须引起足够的重视,并采取相应的措施加以防御。
关键词:道路;桥梁裂缝;预防措施一、前言随着我国经济的快速发展,我国的交通建设也取得了巨大的成就。
但在最近一段时间以来,我国很多地方有相当一部分新建的、远远尚未达到其使用年限的道路桥梁,其主体却出现了裂缝、铺装层松散脱落等等耐久性破坏。
这些道路桥梁等基础设施出现了这些本不该这么早就出现的质量问题,无疑会给国家的交通运输带来了极大的负面影响,不仅使其运输效益大大降低,而且由于这些道路桥梁基础设施在使用年限上是大大缩短,也给国家带来了进行桥梁道路建设所需的人力、物力以及财力的巨大损失和浪费;同时由于这些道路桥梁由于过早出现质量问题在尚未被有关部门发现或者尚未进行相关处理时,极易给行人以及道路、桥梁之上运行的车辆埋下安全隐患,从而对行人、车辆的安全构成潜在的威胁。
二、现阶段道路桥梁出现质量问题的主要表现通过对我国各地由于施工人员的麻痹大意而带来的道路桥梁质量问题进行调查、分析,可以发现在现阶段我国道路桥梁在质量方面出现的问题,主要表现在以下几方面:1.桥梁出现裂缝。
现阶段我国的桥梁绝大多数是以混凝土为主,这些混凝土桥梁在施工过程中,一旦那些施工人员不够专业或者不够负责任,常常会使得这些桥梁在远远没有达到其使用寿命就出现开裂,桥梁主体一旦出现开裂就极大地影响着整个桥梁工程的使用质量,当这种出现在桥梁主体的裂缝,发展到一定程度时甚至会导致整个桥梁出现倒塌。
因此,有关桥梁出现裂缝这个问题,是我国各类城市特别是大城市在进行桥梁建设过程中必须引起足够重视的一个课题。
桥梁工程课题研究论文(五篇):桥梁工程施工中防水层质量问题分析、桥梁工程中沉降段路基路面施工技术…

桥梁工程课题研究论文(五篇)内容提要:1、桥梁工程施工中防水层质量问题分析2、桥梁工程中沉降段路基路面施工技术3、道路桥梁工程中预应力张拉施工要点4、道路桥梁工程伸缩缝施工研讨5、桥梁工程中扩大基础施工技术的运用全文总字数:16800 字篇一:桥梁工程施工中防水层质量问题分析桥梁工程施工中防水层质量问题分析摘要:近几年,屡有报道桥梁事故问题,根据这一现象,我国对于桥梁工程重视程度日益提高。
对于桥梁工程施工问题,一定要重视防水层的施工问题和质量管理问题。
本文以桥梁工程施工中防水层技术介绍、桥梁工程施工中防水层质量检测和控制两方面,详细论述笔者观点,希望可以为我国桥梁工程团队提供施工参考。
关键词:桥梁工程施工;防水层质量问题;控制措施0引言因近几年运输行业飞速发展,为了确保交通安全,保障人民的生命财产,所以,我国对于桥梁的质量安全要求越来越高,不断地学习先进的桥梁施工技术和施工方法,完善桥梁结构设计和防水能力设计。
在对桥梁工程施工中,防水层的质量进行控制和管理时,一定要重视两个方面,一方面是,技术施工方面,另一方面是,质量检测方面,双管齐下,才能更好的提升桥梁工程施工防水层的质量安全。
1桥梁工程施工中防水层技术介绍(一)施工准备工作在对桥面防水层施工前,一定要检查好桥梁结构面板之间、主梁之间的距离。
正常情况下,两个单位平方米内,必须要保持基本的平缓,将凹凸平面度限制在五毫米范围内。
一旦超过正常范围区间,必须要运用砂浆进行找平,填补桥梁结构之间的错台,使凹凸不平变得工整平缓,以便于之后的桥梁防水层施工。
在此过程中,一定要确定找平层的清洁和平整,另外,还要确保找平层内施工的泥沙,具有一定的摩擦感和干燥度。
其中,最重要的是,要确保水乳型聚合物沥青防水材料,水分含量低并且无积水,防水卷材和溶剂型聚合物沥青防水涂料,含水小于百分九。
(二)桥梁沥青防水层施工第一步,沥青防水材料的融化升温,在这一步,要做好沥青脱桶融化升温的工作,必须要将沥青融温升至200℃,在这个温度下,沥青融化最充分,之后才能顺利的展开洒布工作。
桥梁工程施工技术论文10篇【论文】

桥梁工程施工技术论文10篇【论文】研究背景桥梁工程是现代社会中重要的基础设施之一。
在桥梁工程的施工过程中,施工技术的应用起着至关重要的作用。
本文旨在探讨桥梁工程施工技术的相关问题,并提供十篇相关论文供参考。
论文1: 桥梁基础施工技术本文研究来自于对桥梁基础施工技术的调研。
论文探讨了不同桥梁基础施工技术的特点,并分析了其适用性和效果。
论文2: 桥梁浇筑工艺优化研究本文研究桥梁浇筑工艺的优化问题。
论文讨论了不同浇筑工艺对桥梁质量和施工效率的影响,并提出了优化建议。
论文3: 桥梁梁体施工技术的研究与应用本文研究了桥梁梁体施工技术的相关问题。
论文探讨了不同梁体施工技术的特点,并评估了其在实际施工中的应用效果。
论文4: 桥梁施工中的安全管理研究本文研究桥梁施工中的安全管理问题。
论文分析了安全管理的重要性,并探讨了在桥梁施工中如何有效进行安全管理的方法和策略。
论文5: 桥梁施工环境保护技术研究本文研究了桥梁施工环境保护技术的问题。
论文探讨了施工过程中对环境的影响,并提出了相应的环境保护技术措施。
论文6: 桥梁施工中的机械化应用研究本文研究桥梁施工中的机械化应用问题。
论文讨论了机械化施工对施工效率和质量的影响,并探索了如何合理利用机械化技术进行桥梁施工的方法与策略。
论文7: 桥梁施工中的材料选择与应用研究本文研究了桥梁施工中的材料选择与应用问题。
论文探讨了材料的选取对桥梁结构性能的影响,并提出了材料选择和应用的相关建议。
论文8: 桥梁试验与检测技术研究本文研究了桥梁试验与检测技术的问题。
论文讨论了桥梁试验和检测技术的方法和应用,以及其对桥梁结构安全性的重要性。
论文9: 桥梁施工中的质量控制与管理研究本文研究桥梁施工中的质量控制与管理问题。
论文探讨了质量控制与管理在桥梁施工过程中的作用和方法,并提出了相关的管理策略。
论文10: 桥梁施工中的项目管理研究本文研究桥梁施工中的项目管理问题。
论文分析了项目管理对施工进度和成本的影响,并探讨了如何进行有效的项目管理来提高桥梁施工效率。
桥梁加固论文六篇

桥梁加固论文六篇桥梁加固论文范文1关键词:大路桥梁;加固;施工技术前言随着我国交通量日益增加,单车重量也不断增大。
为了适应道路运输载重量不断进展的要求,人们发觉桥梁的混凝土开裂、剥落、衰变及钢筋的锈蚀(管道灌浆不饱满普遍存在)对桥梁的损害问题特别严峻,需要大量的资金来维护或改建,现实使人们开头重视混凝土桥梁的耐久性。
提高混凝土桥梁耐久性的技术途径有两个,一是采纳高性能混凝土,以提高混凝土的抗渗性、匀质性、抗冻性,从而提高混凝土反抗碳化和冷冻侵袭的力量;另外一种是提高既有桥梁耐久性的有效途径即对缺陷桥梁进行加固改造,延长其使用寿命。
一、工程概况某桥为一斜腿刚架钢筋混凝土桥,1973年建成,通车至今已30多年。
全桥在横桥向由六个刚架片组成,刚架片之间通过桥面连续以及横隔板连接,每个刚架片在拱脚和跨中铰接,形成三铰斜腿刚架桥。
边跨梁一端直接搁置在桥台上,另一端搁置在中跨主梁端部的牛腿上。
主桥计算跨径21.65M。
全桥长26M,桥面净宽7M。
设计荷载汽一26,拖一100。
由于种种缘由,桥梁结构消失了一些病害,主要有斜腿主筋、箍筋消失锈蚀,铁锈膨胀引起混凝土爱护层剥落等。
二、桥粱加固的基本方法与原则1、加固原则加固设计以原桥为基础,在不转变原桥结构型式的前提下,对原桥主要受力构件进行加固,加固设计必需考虑以下几个重点:1、下部结构具有足够的潜力。
2、加固后必需要达到能通过重吨的单车的要求。
3、由于下部是航道,所以在跨中腹板和斜腿加固过程中,应尽量保持原有净空,不得使下部空间削减过多。
4、对各开裂构件的表面进行修补,保证构件表面光滑而连续。
5、在补强的同时,应留意加固物本身自重对原桥的影响。
6、加固后保持桥梁的整体美观。
2、加固方法依据目前该桥的交通状况,通过加固,将原桥设计荷载提高为能通过单车重车吨加固设计、加固施工完成后,还要对该桥进行静力荷载试验,以检测桥梁加固工程是否合格,确保其平安性。
加固盖梁和桥墩,待桥墩压浆完毕,桥梁整体稳定后再进行封闭盖粱与桥墩裂缝,盖梁底部消失裂缝的部位作环氧硅,增加盖梁截面积,盖梁侧面粘贴钢板桥墩外侧先纵向粘贴碳纤维片,再环向粘贴碳纤维片将裂缝部位封住。
桥梁工程专业本科毕业设计论文
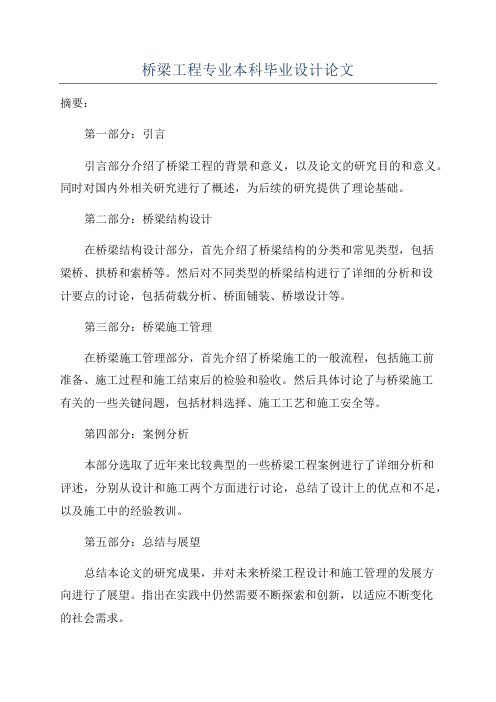
桥梁工程专业本科毕业设计论文
摘要:
第一部分:引言
引言部分介绍了桥梁工程的背景和意义,以及论文的研究目的和意义。
同时对国内外相关研究进行了概述,为后续的研究提供了理论基础。
第二部分:桥梁结构设计
在桥梁结构设计部分,首先介绍了桥梁结构的分类和常见类型,包括
梁桥、拱桥和索桥等。
然后对不同类型的桥梁结构进行了详细的分析和设
计要点的讨论,包括荷载分析、桥面铺装、桥墩设计等。
第三部分:桥梁施工管理
在桥梁施工管理部分,首先介绍了桥梁施工的一般流程,包括施工前
准备、施工过程和施工结束后的检验和验收。
然后具体讨论了与桥梁施工
有关的一些关键问题,包括材料选择、施工工艺和施工安全等。
第四部分:案例分析
本部分选取了近年来比较典型的一些桥梁工程案例进行了详细分析和
评述,分别从设计和施工两个方面进行讨论,总结了设计上的优点和不足,以及施工中的经验教训。
第五部分:总结与展望
总结本论文的研究成果,并对未来桥梁工程设计和施工管理的发展方
向进行了展望。
指出在实践中仍然需要不断探索和创新,以适应不断变化
的社会需求。
关键词:桥梁工程、设计、施工管理、案例分析、发展方向
总结:本论文主要对桥梁工程的设计和施工管理进行了研究,通过分析桥梁结构的不同类型和施工过程中需要注意的问题,总结了一些设计上的优点和施工中的经验教训。
同时对未来桥梁工程设计和施工管理的发展方向进行了展望,为相关领域的研究和实践提供了参考。
有关桥梁工程论文4100字_有关桥梁工程毕业论文范文模板

有关桥梁工程论文4100字_有关桥梁工程毕业论文范文模板有关桥梁工程论文4100字(一):桥梁工程建设中预制T形梁的施工技术研究论文摘要:在目前的桥梁工程建设中,预制梁由于施工技术较为简单、结构稳定性较高而得到了广泛的应用。
在桥梁工程建设中,预制T形梁如果施工不当,很容易出现强度低、拱度高、外观缺陷等问题,因此,需加强T形梁的施工控制。
文章结合实际案例,研究桥梁工程建设中预制T形梁的施工技术。
关键词:桥梁工程;预制T形梁;施工技术0引言预制梁是一种在预制厂中制造梁板之后再在桥面上进行架设的一种建筑材料,不同于在桥面上铺置钢筋之后再浇筑混凝土的做法,相比之下,预制梁施工技术较为简单,施工量较小,耗费的时间也较少。
预制梁提前完成梁板的建造之后,在桥梁工程中只需要架构并固定梁板,但预制梁的缺点也较为明显,和混凝土浇筑的做法对比,预制梁因为强度小更容易出现断裂。
1预制T形梁施工的难点1.1施工场地的选择预制T形梁往往具备自然体积大、自重大的特点,因此在实际的桥梁工程建设中,通常使用现场预制的方式进行制作安装。
由于对施工场地具有较高的要求,因此施工场地的选择是预制T形梁施工的重难点。
在进行施工场地的选择时要考虑到预制T形梁的安全方法与工艺,施工场地需要交通便利且便于施工,同时需要对施工场地进行加固处理,以避免对施工产生影响。
1.2吊装要求高在我国,许多桥梁工程建设都在偏远地区和交通不便的地区开展,在这种施工环境下,大型吊装机械往往很难进入到施工现场,这也对T形梁的吊装提出了更高的要求。
因此,在实际的桥梁工程建设中,要充分考量T形梁的各种吊装工艺,根据工程的实际情况进行有针对性的选择。
其中需要考量的重点包括吊机的性能、工作半径、吊装的能力等,在具体问题具体分析的基础上,制定出与工程实际情况相适配的施工方案。
1.3混凝土浇筑质量控制要求高T形梁混凝土的施工对混凝土浇筑质量的控制有着很高的要求,如果桥梁工程是在偏远地区或者交通不便的地区开展,应采用商用混凝土。
- 1、下载文档前请自行甄别文档内容的完整性,平台不提供额外的编辑、内容补充、找答案等附加服务。
- 2、"仅部分预览"的文档,不可在线预览部分如存在完整性等问题,可反馈申请退款(可完整预览的文档不适用该条件!)。
- 3、如文档侵犯您的权益,请联系客服反馈,我们会尽快为您处理(人工客服工作时间:9:00-18:30)。
如何做好钻孔灌注桩水下混凝土施工内容提要:本文阐述了新建铁路沪昆客专十一标岔河大桥线钻孔灌注桩水下混凝土施工工艺、施工过程中对施工质量的控制以及施工中所遇到技术难题和防治措施。
关键词:钻孔桩水下混凝土施工技术质量控制防治措施1. 前言钻孔灌注桩作为一种基础承载结构和地基支撑的构造物形式是施工建设中应用比较普及的技术内容。
但是钻孔灌注桩作为隐蔽工程,其内部质量无法观察和监控,加之施工难度大,通常都会影响工程质量和滞后施工进度。
因此,在施工中都把它当作一项关键性工程看待,并且在人员配制、施工质量监控、施工管理上加大力度,把握和分析施工过程中可能会发生的问题,将一切不良隐患消除在成桩之前。
特别是水下混凝土灌注施工对于工程实体的影响尤为重要,它决定着桩身的强度、完整性和桩身整体质量能否达到设计要求,所以水下混凝土施工经常作为一个重点课题来研究。
下面就钻孔灌注桩水下混凝土施工工艺中的一些主要问题和施工中的难点及防治措施,谈谈自己的体会和经验。
2. 工程概况沪昆客专十一标岔河大桥位于贵州省兴义市普安县和晴隆县境内,主要为跨越岔河沟谷而设。
大桥起讫里程桩号为DK896+416.11〜DK896+897.64,桥梁全长481.53m。
桥梁设计纵坡0%。
、处于半径为11000m 的平曲线上。
桥跨结构为:主跨(88+168+88)m连续刚构+引桥(33+56+33)m 连续梁。
桥梁下部结构为:桩基+承台+空心薄壁墩柱(实心墩),桥台为空心桥台;桥梁上部结构采用预应力连续刚构及预应力连续梁。
桩基础施工设计图纸为钻孔桩。
全桥共计桩基98根,其中© 1.5m桩基63根,© 2.5m桩基17根,© 2.8桩基有18根,最大桩长51m,最短桩长9m。
3. 水下混凝土施工工艺3.1 水下混凝土的性能参数3.1.1 水下混凝土原料基本要求3.1.1.1 水泥水泥宜采用硅酸盐类水泥,确保水泥的保水性,保水性差的水泥应采取相应的措施保证混凝土不离析和泌水。
3.1.1.2 粗骨料粗骨料宜采用连续级配良好的碎石、卵石,含泥量小于2%,其针、片状颗粒含量不宜大于10%,以提高混凝土的流动性。
3.1.1.3 外加剂混凝土中宜掺用泵送剂或减水剂,并宜掺用粉煤灰或其他活性矿物外加剂。
3.1.2 混凝土配合比注意事项3.1.2.1 外加剂掺入量水下混凝土的用水量与水泥和矿物外加剂的总量之比宜在0.5〜0.6之间,即水胶比宜在0.5〜0.6之间。
3.1.2.2 胶凝材料水下灌注混凝土的胶凝材料总量不宜小于400kg/m3。
3.1.2.3 含砂率水下灌注混凝土的砂率宜在35%- 40%之间。
3.1.3 混凝土初凝时间一般混凝土初凝时间仅3 -5小时,只能满足浅孔小桩径灌注要求,而深桩灌注时间约为5-7 小时,因此应加缓凝剂,使混凝土初凝时间大于8 小时。
3.1.4 混凝土搅拌方法和搅拌时间为使混凝土具有良好的保水性和流动性,应按合理的施工配合比将水泥、碎石、砂子倒入料斗后,先开动搅拌机并加入30%的水,然后与拌合料一起均匀加入60%的水,最后再加入10%的水(如砂、石含水率较大时,可适当控制此部分水量),最后加水到出料时间控制在60-90秒内。
3.1.5 混凝土坍落度选择坍落度应控制在180-220毫米之间,混凝土灌注距桩顶约5米处时,坍落度控制在160- 170 毫米,以确保桩顶浮浆,不过高。
气温高、成孔深,导管直径在250毫米之内,取高值,反之取低值。
3.2 水下混凝土的施工工艺3.2.1 灌注前的施工准备3.2.1.1 验孔验孔主要注意两点,一孔的垂直度、二是孔的深度。
因为钻孔灌注桩的垂直度是保证基础承载力和围护结构稳定性、建筑尺寸准确性的重要一环,而孔的深度是否达到设计要求,更会影响灌注桩的承载力,所以在灌注水下混凝土之前,应严格控制以上两个指标。
3.2.1.2 泥浆制备和清孔清孔则是利用泥浆在流动时所具有的动能冲击桩孔底部的沉渣,使沉渣中的岩粒、砂粒等处于悬浮状态,再利用泥浆胶体的粘结力使悬浮着的沉渣随着泥浆的循环流动被带出桩孔,最终将桩孔内的沉渣清干净。
灌注桩成孔至设计标高,应充分利用钻杆在原位进行第一次清孔,直到孔口返浆比重持续小于1.10〜1 .20,测得孔底沉渣厚度小于50 mm,即抓紧吊放钢筋笼和沉放混凝土导管。
沉放导管时检查导管的连接是否牢固和密实,以防止漏气漏浆而影响灌注。
3.2.2 水下混凝土的施工工艺3.2.2.1 首批混凝土灌注混凝土灌注量与泥浆至混凝土面高度、混凝土面至孔底高度、泥浆的密度、导管内径及桩孔直径有关。
首批灌注的混凝土量必须满足导管埋深不能小于1.5M,所以漏斗和储料斗及漏斗和输送泵的混凝土储存数量要充足。
根据导管内混凝土压力与管外水压力平衡的原则, 导管内混凝土必须保持的最小高度为:Hd =R wHw /R c。
而管中混凝土的体积就应为Vd =nd 2 •Hd /4 (d为导管直径)。
孔径越大,首批灌注的混凝土量越多,所以由于混凝土量大,搅拌时间长,因此可能出现离析现象,首批混凝土在下落过程中,由于和易性变差,受的阻力变大,常出现导管中堵满混凝土,甚至漏斗内还有部分混凝土,此时应加大设备的起重能力,以便迅速向漏斗加混凝土,然后再稍拉导管,若起重能力不足,则应用卷扬机拉紧漏斗晃动,这样能使混凝土顺利下滑至孔底,下灌后,继续向漏斗加入混凝土,进行后续灌注。
3.2.2.2 后续混凝土灌注后续混凝土灌注中,当出现非连续性灌注时,漏斗中的混凝土下落后,应当牵动导管,并观察孔口返浆情况,直至孔口不再返浆,再向漏斗中加入混凝土,同时在灌注过程中,应经常用测锤探测混凝土面的上升高度,并适时提升、逐级拆卸导管,保持导管的合理埋深。
此时要注意,混凝土灌到孔口不再返出泥浆时可以微向上提动导管,而如果要提升导管0.5 到1M以上才能灌入混凝土就应该拆除部分导管。
要注意观察孔口是否返出泥浆。
当混凝土接近钢筋笼时,宜使导管埋得较深。
要注意正确控制导管埋深,如果导管埋人混凝土过深,易使导管与混凝土间摩擦阻力过大,致使导管无法拔出造成事故。
而提管过程中要缓缓上提,如过猛易使导管被拉断。
所以埋管深度一般应控制在2〜6m或使用附着式震捣器,使导管周围的混凝土不致过早的初凝。
同时应注意灌注速度。
3.2.2.3 后期混凝土的灌注在混凝土灌注后期,由于孔内压力较小,往往上部混凝土不如下部密实,这时应稍提漏斗增大落差,以提高其密实度。
3.2.2.4 混凝土的灌注速度在控制混凝土初凝时间的同时,必须合理地加快灌注速度,这对提高混凝土的灌注质量十分重要,因此应做好灌注前的各项准备工作,以及灌注过程中各道工序的密切配合工作。
4. 施工难点及防治措施4.1 钢筋笼上浮4.1.1 原因分析4.1.1.1 混凝土下降冲击力造成的上浮当混凝土灌注至钢筋笼下,若此时提升导管,导管底端距离钢筋笼仅有1 米左右的距离时,由于浇注的混凝土自导管流出后冲击力较大,推动了钢筋笼上浮。
4.1.1.2 混凝土向上顶升造成的上移由于混凝土灌注过钢筋笼且导管埋置深较大时,其上层混凝土因浇注时间较长,已近初凝,表面形成硬壳,混凝土与钢筋笼有一定握裹力,如果此时导管底端未及时提到钢筋底部以上,混凝土在导管流出后将以一定的速度向上顶升,同时也带运钢筋笼的上移。
4.1.2 防治措施4.1.2.1 适当提升导管在灌注混凝土的过程中应随时掌握混凝土浇注标高及导管埋深,当混凝土埋过钢筋笼底端2〜3米时,应及时将导管提至钢筋笼底端以上。
4.1.2.2 加固当发现钢筋笼上浮时,应暂停浇注,在孔口对钢筋笼采取加固措施,防止钢筋笼再次上浮。
4.2 孔壁塌孔4.2.1 原因分析4.2.1.1 泥浆造成的夹泥层泥浆过稠,增加了浇注混凝土的阻力,如泥浆比重大且泥浆中夹有较大的泥块,在施工中经常发生导管堵管,流动不畅等现象,有时甚至灌满导管还是不行,最后只好提导管上下振动,而埋管又过浅,导致管内储存大量混凝土,一旦流出其势甚猛,在混凝土流出导管后,即冲破泥浆最薄弱处急速返上,并将泥浆夹裹于桩内,造成夹泥层。
4.2.2 防治措施4.2.2.1 控制泥浆浓度认真做好清孔,控制好泥浆浓度,防止孔壁塌孔,4.3 断桩4.3.1 原因分析4.3.1.1 导管造成的夹泥层和断桩灌注混凝土过程中,因导管漏水或导管提漏而二次下球也是造成夹泥层和断桩的原因。
导管提漏有两种原因:a,当导管堵塞时,一般采用上下振击法,使混凝土强行流出,但此时导管埋深很浅,极容易提漏。
b,因泥浆过稠,如果估算或测混凝土面难,在测量导管埋深时,对混凝土浇注高度判断错误,而在卸下导管时多提,使导管提离混凝土面,也就产生提漏,引起断桩。
4.3.1.2 灌注时间造成的断桩灌注时间过长,而上部混凝土已接近初凝。
形成硬壳,而且随时间增长,泥浆中残渣将不断沉淀,从而加厚了积聚在混凝土表面的沉淀物,造成混凝土灌注极为困难,造成堵管与导拔不上来,引发断桩事故。
4.3.2 防治措施4.3.2.1 提高浇筑速度尽可能提高混凝土浇注速度:a, 开始浇注混凝土时,计算出首批混凝土的数量,确保混凝土能埋导管0.5 米以上,同时让混凝土产生大的冲击力可以克服泥浆阻力。
B, 快速连续浇注,使混凝土和泥浆一直保持流动状态,可防止导管堵塞。
4.3.2.2 控制导管提升频率提升导管时要根据埋管深度指挥,不得小于最小埋深,灌注混凝土过程中随时测量导管埋深,并严格遵守操作规程。
4.4 泥浆进入导管造成夹泥层4.4.1 原因分析4.4.1.1 导管埋置深度造成泥浆进入导管导管埋得太深,拔出时底部已接近初凝,导管拔上后混凝土不能及时冲填,造成泥浆进入。
4.4.2 防治措施4.4.2.1 试验保证导管是否漏水灌注水下混凝土前导管一定要做水压试验,加水15 分钟密封加压,看是否漏水,直到合格为止,有问题及时更换。
4.5 灌入阻力造成的桩身质量4.5.1 分析原因4.5.1.1 灌入阻力造成的桩身质量由于灌注桩不能像上部结构施工那样逐层振捣,而且存在一定的混凝土灌入阻力,致使灌注混凝土时因为无法克服灌入阻力而保证不了桩身质量4.5.1 防治措施4.5.1.1形成强大的冲击力在巨大的冲击作用下,混凝土的向上顶力和册向挤压力就有了保证,桩的摩阻力和桩身混凝土密实性都可以得到保证。
4.5.1.2首斗混凝土的冲击力首斗混凝土灌注冲击力必须足够大,确保沉渣、沉淤被完全溅开,桩端与持力层能较好地结合,确保端承力的发挥4.体会⑴工程实践证明:严格控制水下混凝土的施工质量和对施工工艺的坚决履行,成为钻孔灌注桩实体合格的决定因素。
⑵通过钻空灌注桩和水下混凝土灌注施工,特别是对于几点防治措施的学习应用,对水下混凝土的施工技术积累了一定的施工经验。