统计过程控制之通用控制图
SPC统计过程管制与控制图
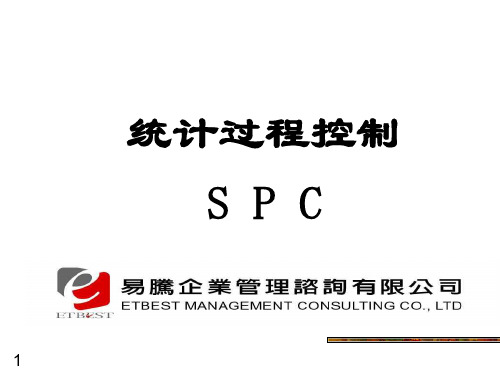
2、控制图的发展
1924年发明
W.A. Shewhart
1931发表
1931年Shewhart发表了 “Economic Control of Quality of
Manufacture Product”
1941~1942 制定成美国标准
4
Z1-1-1941 Guide for Quality Control Z1-2-1941 Control Chart Method for
输出
识别不断变化 的需求和期望
顾客的声音 8
三、基本的统计概念
1、数据的种类
计量型 计数型
2、波动(变差)——波动的概念、原理及波动的 种类
3、普通原因/异常原因
4、基础的统计量——平均值X、中位数X~、极差R
标准偏差、S
9
1、数据的种类
计量型 特点:可以连续取值,也称连续型数据。 如:零件的尺寸、强度、重量、时间、温度等。
有控制限的过程控制图。 (备注:管理用控制图必须要有控制限!)
19
3、“”及“”风险定义
根据控制限作出的判断也可能产生错误。可能产生的错
误有两类:
第一类错误是把正常判为异常,它的概率为,也就是
说,工序过程并没有发生异常,只是由于随机的原因引起了
数据过大波动,少数数据越出了控制限,使人误将正常判为
异常,从而虛发警报。由于徒劳地查找原因并为此采取了相
应的措施,从而造成损失。因此第一种错误又称为徒劳错误。
(X1+X2+……+Xn)/n
2、中位数~X
将数据按数值大小顺序排列后,位于中间位置的书,
称为中位数。
如:5,9,10,4,7,
X~=7;
统计过程控制SPC第二版

例如,原材料的质量不符合规定要求;机 器设备带病运转;操作者违反操作规程; 测量工具带系统性误差,等等。由于这些 原因引起的质量波动大小和作用方向一般 具有一定的周期性或倾向性,因此比较容 易查明,容易预防和消除。又由于异常波 动对质量特性值的影响较大,因此,一般 说来在生产过程中是不允许存在的。
是
否
np或p图 p图
关心的是 单位零件缺陷数吗?
是
样本容量 是否恒定?
是
否
C或U图 U图
二、控制图
计量型控制图
二、控制图 计数型控制图
二、控制图 4、控制图应用的二个阶段
从生产过程中,定期抽取样本,测量各样 本的质量特性值,然后将测得的数据加以 统计分析,判断过程是否处于稳定受控状 态,从中发现过程异常原因(特殊原因), 从而及时采取有效对策,使过程恢复到正 常稳定受控状态。
预防与检测
检测——容忍浪费
在生产部门,通过检查最终产品并剔除不合格产品。不合格的总是不合格。 在管理部门,经常靠检查或重新检查工作来找出错误 这实质上是“死后验尸”,造成时间和材料等的浪费
计数型:通常是指不用仪器即可测出的数 据。计件如不合格件数;计点如PCB上的 漏焊数、溢胶数等
计量型 计数型
计件型 计点型
二、控制图 2、控制图的构成
18 17 16 15 14 13 12 11 10
9 8 7 6 5
1
2
3
4
点落在该区间的概率为99.7%
5
6
7
8
9
+3
Average
-3
10
二、控制图
▪ ……
二、控制图
计数型控制图
不良率控制图(P图) 不良品数控制图(Pn图) 缺陷数控制图(C图) 单位缺陷数控制图(U图)
控制图(control charts)
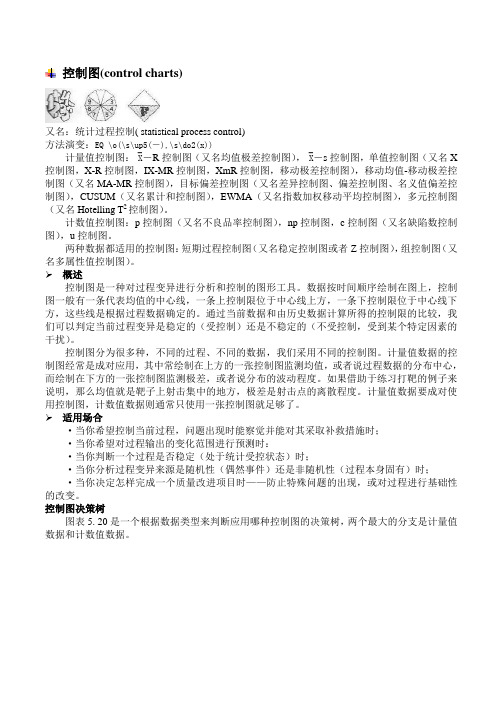
控制图(control charts)又名:统计过程控制( statistical process control)方法演变:EQ \o(\s\up5(-),\s\do2(x))计量值控制图:⎺X-R控制图(又名均值极差控制图),⎺X-s控制图,单值控制图(又名X 控制图,X-R控制图,IX-MR控制图,XmR控制图,移动极差控制图),移动均值-移动极差控制图(又名MA-MR控制图),目标偏差控制图(又名差异控制图、偏差控制图、名义值偏差控制图),CUSUM(又名累计和控制图),EWMA(又名指数加权移动平均控制图),多元控制图(又名Hotelling T2控制图)。
计数值控制图:p控制图(又名不良品率控制图),np控制图,c控制图(又名缺陷数控制图),u控制图。
两种数据都适用的控制图:短期过程控制图(又名稳定控制图或者Z控制图),组控制图(又名多属性值控制图)。
概述控制图是一种对过程变异进行分析和控制的图形工具。
数据按时间顺序绘制在图上,控制图一般有一条代表均值的中心线,一条上控制限位于中心线上方,一条下控制限位于中心线下方,这些线是根据过程数据确定的。
通过当前数据和由历史数据计算所得的控制限的比较,我们可以判定当前过程变异是稳定的(受控制)还是不稳定的(不受控制,受到某个特定因素的干扰)。
控制图分为很多种,不同的过程、不同的数据,我们采用不同的控制图。
计量值数据的控制图经常是成对应用,其中常绘制在上方的一张控制图监测均值,或者说过程数据的分布中心,而绘制在下方的一张控制图监测极差,或者说分布的波动程度。
如果借助于练习打靶的例子来说明,那么均值就是靶子上射击集中的地方,极差是射击点的离散程度。
计量值数据要成对使用控制图,计数值数据则通常只使用一张控制图就足够了。
适用场合·当你希望控制当前过程,问题出现时能察觉并能对其采取补救措施时;·当你希望对过程输出的变化范围进行预测时:·当你判断一个过程是否稳定(处于统计受控状态)时;·当你分析过程变异来源是随机性(偶然事件)还是非随机性(过程本身固有)时;·当你决定怎样完成一个质量改进项目时——防止特殊问题的出现,或对过程进行基础性的改变。
统计过程控制(SPC)
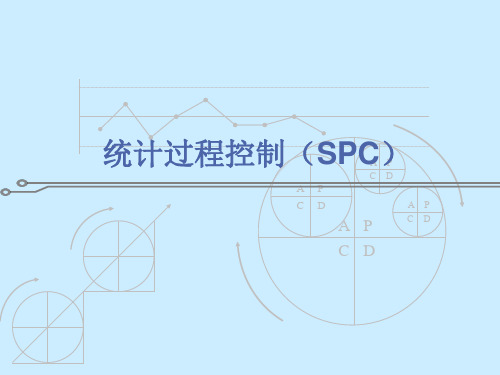
CD
AP
CD
AP
AP
CD
CD
统计过程控制(SPC)
SPC的基本概念 控制图原理 常规(休哈特)控制图 控制图的判断准则 常用控制图的计算 通用控制图 过程能力与过程能力指数
统计过程控制(SPC)
SPC的基本概念
• SPC的涵义 SPC是英文Statistical Process Control(统计过程控制)
C B A
准则:连续9点落在中心线同一側。
LCL
准则:连续6点递增或递减。
准则:连续14点中相邻点上下交替。
准则:连续3点中有2点落在中心线同一側的B区之外。
准则:连续5点中有4点落在中心线同一側的C区之外。
准则:连续15点在C区的中心线上下。
准则:连续8点在中心线两側,但无一在C区中。
统计过程控制(SPC)
统计过程控制(SPC)
• 控制图的作用 控制图的作用是:及时告警。体现SPC与SPD的贯彻
预防原则。 控制图是SPC与SPD的重要工具,用以直接控制与诊断 过程,故为质量管理七个工具的核心。
质量管理七个工具:因果图(Cause-effect diagram), 排列图(Pareto diagram),直方图(Histogram),散 步图(Scatter diagram),控制图(Control chart),分 层法(Stratification),检查表(Check list)。 贯彻预防原则的“20字方针”:
u控制图的控制线为:
UCL = u + 3 u / n CL = u
LCL = u - 3 u / n
式 否中则:控u制=线 呈ci /凹凸ni 状,。ci为样本的不合格数。样本容量n最好恒定,
统计过程控制之通用控制图

统计过程控制(SPC)与休哈特控制图(三)第六章通用控制图世界各国的控制图大多采用3σ方式。
在应用控制图时,需要计算控制图的控制界限并根据实测数据计算出所控制的统计量,在控制图中描点。
这两项都需要一定的工作量,尤其是p图与pn图、u图与c图,由于控制界限计算公式中含有样本大小n,控制界线随着n的变化而呈凹凸状,作图十分不便,也难于判稳、判异。
若n变化不大,虽可用n 的平均数n代替n,但不精确,当点子接近控制界限时有误报与漏报异常的可能。
1981年我国张公绪教授与阎育苏教授提出的通用控制图解决了上述问题。
在通用控制图上,控制界线是直线,而且判断异常的结果也是精确的。
通用控制图已于1986年发布为国家标准GB6381。
通用控制图主要包括两个内容:标准变换和直接打(描)点法。
一、标准变换与通用图所谓随机变量的标准变换是指经过变换后随机变量的平均值变成0、方差变成1的变换,即:变换后的随机变量=(随机变量一μ)/σ这是可以理解的。
随机变量的取值减去其平均值后的平均值应为0;其次,分母为标准差,也就是说用标准差作尺度,这样,变换后的标准差应为1。
现在,对3σ控制界限的一般公式UCL=μ+3σCL=μLCL=μ-3σ进行标准变换,于是得到UCLt=(UCL-μ)/σ=3CLt=(UCL-μ)/σLCLt=(UCL+μ)/σ=3式中,下标t表示标准变换后,也表示通用的“通"。
这样,任何3σ控制图都统一变换成式(3.6. 1一2)的控制图,称为通用控制图。
通用图的优点是控制界限统一成3,0,-3,可以事先印好,简化控制图,节省管理费用,在图上容易判断稳态和判断异常。
通用图的缺点是在图中打(描)点也需要经过标准变换,计算要麻烦些。
为了解决这个问题,需要应用直接打点法。
二、直接打点法控制图判断异常的准则主要有下列两点:(1)点子出界或恰在控制界限上;(2)界内点子的排列非随机。
前者对于点子位置要求精确,后者对于点子位置要求相对精确就可以了。
SPC统计过程控制

SPC统计过程控制—控制图连续数据和离散数据连续型:使用测量的可以有意义地无限分割的连续数值。
(时间,长度)离散型:类别信息,可以计数但是不能有意义的分割。
(合格/不合格)控制图由中心线,控制上限(UCL)及控制下限(LCL)组成。
注意控制限和规格限的区别,控制极限(UCL,LCL)是根据平均值计算得出的,是按过程中心值+/- 3个标准偏差计算出来的。
即控制极限是根据样本数据计算得出的,是过程的内部特征。
控制极限是由过程能力决定的。
规格极限(USL,LSL)是由执行的标准决定的,是过程的外部特征。
大多数规格是关于个体数值的,是由客户的要求决定的。
控制图上表现出来的波动分为由一般原因引起的波动和由特殊原因引起的波动,对于特殊原因引起的波动更加容易发现,比如超出了控制上限或控制下限或者常说的控制图七点判异规则。
控制图的作用就是要发现这些异常,并且分析根源采取纠正措施。
控制图的使用和选择连续的分组数据:XBar-R控制图和XBar-S控制图。
连续的单值数据:I-MR控制图。
离散的符合二项分布的不合格品数:(分组样品容量相等用nP控制图,不等用P控制图) 离散的符合泊松分布的缺陷数:(分组样品容量相等用C控制图,不等用U控制图) XBar-R控制图XBar(平均值控制图)反映变量X随时间的集中趋势及分组样本之间的变动性。
注意控制图中的每个点是每个分组的平均值,而控制图的中心线是分组的平均值的平均值。
R(极差控制图)极差控制图监测的是分组样本内部随时间的变动。
该图的中心线代表长期的分组样本之极差的平均值,或称为R。
对于R控制图只适合于样本容量较小的场合。
XBar-S控制图XBar(平均值控制图)反映变量X随时间的集中趋势及分组样本之间的变动性。
这个同XBar-R控制图。
对于S控制图是值标准差,标准差控制图监测的是分组样本内部随时间的变动。
该图的中心线代表长期的分组样本之标准偏差的平均值,标准差图可适用于分组样本容量(即n)大于2的任何场合。
第三章 统计过程控制(SPC)与常规控制图

两个重要的参数:
• µ (mu)--- 位置参数和平均值(mean value) ,表 示 分布的中心位置和期望值 • (sigma) --- 尺度参数,表示分布的分散程度和标 准偏差 (standard deviation),
20字真经 查出异因, 采取措施, 保证消除, 不再出现, 纳入标准。
5. 统计控制状态
任何技术控制都有一个标准作为基准。 统计 过程控制(SPC)的基准是统计控制状态 (State in Statistical Control) 简称控制状态(state in control)或稳态(stable state): 指过程中只有偶因(而无异因)产生 的变异状态。 当过程仅受随机因素影响时,过程处于统计 控制状态(简称受控状态);当过程中存在 系统因素的影响时,过程处于统计失控状态 (简称失控状态)。由于过程波动具有统计 规律性,当过程受控时,过程特性一般服从 稳定的随机分布;而失控时,过程分布将发 生改变。SPC正是利用过程波动的统计规律 性对过程进行分析控制的。 通过对过程不断调整,从理论上讲,控制状 态是可以达到的,虽然质量变异不能完全消 除,应用控制图使得质量变异成为最小的有 效工具。
• 本步骤最困难,最费时。 制订过程控制标准 对过程进行监控 对过程进行诊断并采取措施解决问题
5.推行ISO9000国际标准与推行SPC和 SPD的关系
在ISO9000族标准中运用统计技术的目 的在于:通过对统计技术的适当运用以 解决组织的问题和做出有效决策,提高 管理效率并促进质量管理体系的持续改 进和产品质量的不断提高。推行SPC和 SPD是推行ISO9000国际标准的一项重 要基础工作。
控制图(control charts)
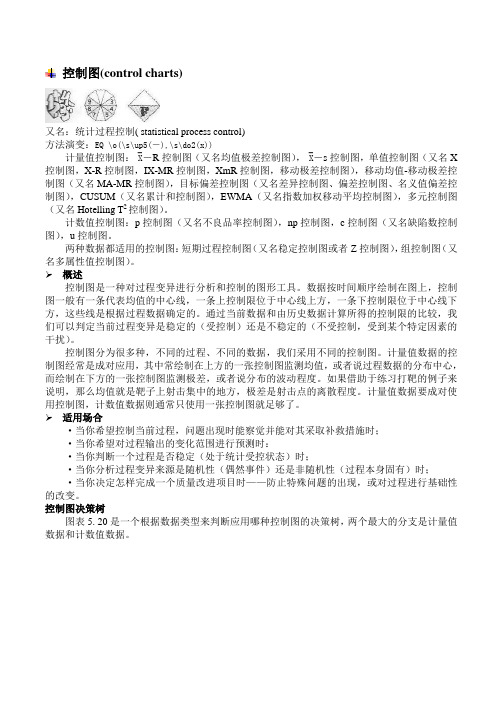
控制图(control charts)又名:统计过程控制( statistical process control)方法演变:EQ \o(\s\up5(-),\s\do2(x))计量值控制图:⎺X-R控制图(又名均值极差控制图),⎺X-s控制图,单值控制图(又名X 控制图,X-R控制图,IX-MR控制图,XmR控制图,移动极差控制图),移动均值-移动极差控制图(又名MA-MR控制图),目标偏差控制图(又名差异控制图、偏差控制图、名义值偏差控制图),CUSUM(又名累计和控制图),EWMA(又名指数加权移动平均控制图),多元控制图(又名Hotelling T2控制图)。
计数值控制图:p控制图(又名不良品率控制图),np控制图,c控制图(又名缺陷数控制图),u控制图。
两种数据都适用的控制图:短期过程控制图(又名稳定控制图或者Z控制图),组控制图(又名多属性值控制图)。
概述控制图是一种对过程变异进行分析和控制的图形工具。
数据按时间顺序绘制在图上,控制图一般有一条代表均值的中心线,一条上控制限位于中心线上方,一条下控制限位于中心线下方,这些线是根据过程数据确定的。
通过当前数据和由历史数据计算所得的控制限的比较,我们可以判定当前过程变异是稳定的(受控制)还是不稳定的(不受控制,受到某个特定因素的干扰)。
控制图分为很多种,不同的过程、不同的数据,我们采用不同的控制图。
计量值数据的控制图经常是成对应用,其中常绘制在上方的一张控制图监测均值,或者说过程数据的分布中心,而绘制在下方的一张控制图监测极差,或者说分布的波动程度。
如果借助于练习打靶的例子来说明,那么均值就是靶子上射击集中的地方,极差是射击点的离散程度。
计量值数据要成对使用控制图,计数值数据则通常只使用一张控制图就足够了。
适用场合·当你希望控制当前过程,问题出现时能察觉并能对其采取补救措施时;·当你希望对过程输出的变化范围进行预测时:·当你判断一个过程是否稳定(处于统计受控状态)时;·当你分析过程变异来源是随机性(偶然事件)还是非随机性(过程本身固有)时;·当你决定怎样完成一个质量改进项目时——防止特殊问题的出现,或对过程进行基础性的改变。
- 1、下载文档前请自行甄别文档内容的完整性,平台不提供额外的编辑、内容补充、找答案等附加服务。
- 2、"仅部分预览"的文档,不可在线预览部分如存在完整性等问题,可反馈申请退款(可完整预览的文档不适用该条件!)。
- 3、如文档侵犯您的权益,请联系客服反馈,我们会尽快为您处理(人工客服工作时间:9:00-18:30)。
统计过程控制(SPC)与休哈特控制图(三)第六章通用控制图世界各国的控制图大多采用3σ方式。
在应用控制图时,需要计算控制图的控制界限并根据实测数据计算出所控制的统计量,在控制图中描点。
这两项都需要一定的工作量,尤其是p图与pn图、u图与c图,由于控制界限计算公式中含有样本大小n,控制界线随着n的变化而呈凹凸状,作图十分不便,也难于判稳、判异。
若n变化不大,虽可用n的平均数n代替n,但不精确,当点子接近控制界限时有误报与漏报异常的可能。
1981年我国公绪教授与阎育教授提出的通用控制图解决了上述问题。
在通用控制图上,控制界线是直线,而且判断异常的结果也是精确的。
通用控制图已于1986年发布为国家标准GB6381。
通用控制图主要包括两个容:标准变换和直接打(描)点法。
一、标准变换与通用图所谓随机变量的标准变换是指经过变换后随机变量的平均值变成0、方差变成1的变换,即:变换后的随机变量=(随机变量一μ)/σ这是可以理解的。
随机变量的取值减去其平均值后的平均值应为0;其次,分母为标准差,也就是说用标准差作尺度,这样,变换后的标准差应为1。
现在,对3σ控制界限的一般公式UCL=μ+3σCL=μLCL=μ-3σ进行标准变换,于是得到UCLt=(UCL-μ)/σ=3CLt=(UCL-μ)/σLCLt=(UCL+μ)/σ=3式中,下标t表示标准变换后,也表示通用的“通"。
这样,任何3σ控制图都统一变换成式(3.6. 1一2)的控制图,称为通用控制图。
通用图的优点是控制界限统一成3,0,-3,可以事先印好,简化控制图,节省管理费用,在图上容易判断稳态和判断异常。
通用图的缺点是在图中打(描)点也需要经过标准变换,计算要麻烦些。
为了解决这个问题,需要应用直接打点法。
二、直接打点法控制图判断异常的准则主要有下列两点:(1)点子出界或恰在控制界限上;(2)界点子的排列非随机。
前者对于点子位置要求精确,后者对于点子位置要求相对精确就可以了。
这就启控制图判断异常的准则主要有下列两点:(1)点子出界或恰在控制界限上;(2)界点子的排列非随机。
前者对于点子位置要求精确,后者对于点子位置要求相对精确就可以了。
这就启发我们在通用图上作出K=-3,-2,...3,3的七根水平横线,把整个通用图分成Ⅰ,Ⅱ,...,Ⅷ共八个区域,如图3.6.2一1所示。
如果点子落在区域Ⅰ或Ⅷ中,则点子显然出界,而且其结果是精确的;如果点子落在其余区域,则只需将此点描在该区域中即可,其具体位置不要求那么精确。
将通用图分成Ⅰ,Ⅱ,...,Ⅷ共八个区域的七根线:K=-3,K=-2,...,K=2,K=3称为标杆线。
如果在现场数据中找出与此对应的七个数据(可称之为现场标杆数据),则在现场测得所控制质量指标的数据后,将它与这七个现场标杆数据相比较,便立刻知道应在通用图上哪个区域中描点。
这就是直接打(描)点法。
直接打(描)点法的公式仍然从标准变换公式导出。
从式(3.61-1)有K=(现场标杆数据一μ)/σ于是现场标杆数据=μ+Kσ (K=-3,-2,-1,0,1,2,3)这就是直接打点公式。
根据具体的控制图,得出相应的均值与标准差数据,代人上式,可以列出直接打点表。
现场工人可根据现场实测数据,查直接打点表,然后直接在通用图中描点,无需任何计算,十分方便。
实践证明,这对于推广控制图十分重要。
三、Pt(通用不合格晶率)控制图和pnt(通用不合格品数)控制图p图的统计量为样本不合格品率p=D/n,这里D为样本不合格品数,n为样本大小。
pn图的统计量为样本不合格品数D=np 。
若过程的不合格品率P 已知,则从式(3.6.1-1)知,统计量户经过标准变换后为pt=n P P P p /)1(--=)1(P nP nP np --=)1(P nP nPD --=Dt从上式可见,经过标准变换后,p 图的统计量pt 与pn 图的统计量Dt 恒等,即对同一个二项分布总体的数据而言,无论应用统计量pt 还是应用统计量Dt,在通用图上都得到相同的图形。
这样,在原来应用p 图或如图的场合都可采用pnt 图,以便直接利用不合格品数D 。
现在给出pnt 图的直接打点公式,以便作出pnt 图的直接打点表。
令DK,n 为对应于通用图上标杆线K 和样本大小n 的现场标杆数据,于是从式(3.6.2一2),有DK,n=n p +K)1(p p n -,(K=-3,-2,-1,0,1,2,3,)式中,p 为P 的估计量。
例 用通用图重做例3.5.7一1并与p 图比较。
;解 采用Pnt 图重做例3.5.7一1。
进行步骤如下:步骤1: 计算样本平均不合格品率p 。
参见表 3.5.7一1末, p =0.93890步骤2: 选择参数n的围。
由于在表3.5.7一1中n的最小值为55,最大值为99,所以pnt图的直接打点表最好选择n为50,55,60,...,100,105,以包括可能出现的n的数值。
步骤3: 计算直接打点表。
根据式(3.6.3一2)计算如T图的直接打点表,如表3.6.3-1所示。
例如,表中,当K=3,n=55时D3,55=55×0.0389+3)55-⨯=6.4.0.0038903891(其余类推。
注:由于DK,n不可能为负,故表中每列只列出第一个负数以估计描点之用。
步骤4: 应用直接打点表在通用图上描点。
例如,对于第一组样本,n=85,D=2,从表3.6.3一1中n=85的这一列查得D=2在D0.85=3.3和D-1.85=1.5之间。
故第一组样本的点子应描在K=0与K=-1这两根标杆线之间。
再如,对于第27组样本,n=99,D=10,从表16.3一1中与n=99最接近的n=100这一列查得D=10>D3.100=9.7,于是判断该样本的点子超过上控制界限,过程失控。
其余类推,如图3.6.3一1所示。
由图可见,pnt图和p图的性状一致,但pnt图的控制界线为直线,而且所得结果是精确的,要方便得多。
此外,无论样本大小n是否为常数,pnt图均可用。
所以通用图不但减少了常规控制图的种类,由8种减为6种,而且也扩大了休哈特控制图(Pn图与C图)的应用围。
四、Ct(通用缺陷数)控制图和Ut(通用单位缺陷数)控制图c图的统计量为样本(即一定检查单位)的缺陷数c。
u图的统计量为样本的单位缺陷数u =C/。
若过程的平均缺陷数λ已知,则从式(3.6.1一1)知,统计量u 经过标准变换后为 Ut=n U U U u /)1(--=n n C //λλ-=λλn n C -=λλ''-C式中,λ'=n λ',它是与n 个检查单位的总缺陷数C 对应的过程参数。
从上式可见,经过标准变换 后,u 图的统计量Ut 与c 图的统计量Ct 恒等,即对同一个泊松分布总体的数据而言,无论应用统计量Ut 还是应用统计量Ct,在通用图上都得到相同的图形。
这样,在原来应用u 图或c 图的场合都可采用Ct 图,以便直接利用缺陷数c 。
由于Ct 图的控制界线为直线,而且所得结果是精确的,所以要比价图方便得多。
此外,wu 无论样本大小n 是否为常数,Ct 图均可用。
因此,通用图不但减少了常规控制图的种类,而且也扩大了休哈特控制图的应用围。
第七章两种质量诊断理论本章将讨论生产线的分析方法,两种质量的基本概念,两种质量诊断理论。
一、两种质量诊断理论1.生产线的分析方法通常,一个产品在生产过程中要经过若干道工序加工才能完成。
因此,每道工序都对产品的最终质量起作用。
对于由若干道工序组成的一条生产线应如何分析和评价呢?传统的休哈特分析方法是道道工序把关,即上工序只允许把合格品送往下工序加工,这样就可以保证产品的最终质量。
这种场合的分析方法是假定上道工序的产品总是合格品,从而无需考虑上工序对下工序的影响。
因此,在分析生产线时,每道工序都看成是独立的,参见下图的模型Ⅰ。
换言之,在传统分析方法中各工序都假定与其余工序是统计独立的。
这时若分析某道工序的质量问题,只需考虑该工序本身的质量因素就行了,所以这种模型的优点是分析简单。
传统生产线分析模型Ⅰ在现实生活中,对于上下无联系的工序,如机械加工中的镗圆与钻孔,这种传统方法是有效的。
但在许多场合,上下工序是相关的而不是统计独立的,如石油、化工等流程式生产或制药、食品加工等有严格时限要求的场合,传统的道道把关实际上做不到。
因此,传统分析方法有局限性,需要采用新的选控分析方法。
在选控分析方法中(如上图所示),认为上工序对下工序的影响,或多或少,始终存在,即上下工序间都是相关的。
上下工序不相关(上工序影响为零)仅仅是本情况的特例。
换言之,下图的模型Ⅱ更一般,更符合实际,且把上图的模型Ⅰ作为其特例。
…………选控生产线分析模型Ⅱ在模型Ⅰ中,各工序间是统计独立的,故分析工序时只需要考虑本工序的质量因素;而在模型Ⅱ中,各工序是相关的,故分析工序时除去考虑本工序的质量因素以外,还需考虑上工序的影响。
为了简化模型Ⅱ的分析,需要提出两种质量的概念。
二、两种质量为了简化分析图选控生产线分析模型Ⅱ,需要提出两种质量的概念。
例如,在第n道工序(这里可以是生产线的任一道工序),根据质量涵义所涉及的围大小,存在以下两种质量:1. 工序综合质量,简称总质量。
总质量不但包括第n道工序的加工质量,而且综合了所有上道工序的加工质量在。
总质量就是通常意义下的产品质量,不过强调一个“总”,字而已。
总质量的特点是:它可以由用户直接感受到。
对于负责整个生产线的主管人员来说,他当然要关心总质量,因为总质量直接为用户感受到。
但是,只关心总质量是不够的,当总质量发生问题时,往往不能立刻判定究竟是哪道工序造成的。
因此,他还需关心第二种质量,即工序固有质量。
2.工序固有质量,简称分质量。
分质量是指该工序本身的加工质量,而不包括上工序的影响。
分质量是一种新的质量概念。
分质量的特点是:它反映了该工序的工作质量。
事实上,影响一道工序的因素按照来源的不同可分为人、机、料、法、环五大类因素(即4M1E)。
其中,料即原材料、半成品,它来自上道工序,与本工序元关;环即环境,由于整条生产线大多处于相同的环境下,故可将环境看成是一个共同的因素而不必给予特殊的考虑。
而其余的人(操作人员)、机(设备,其可用性与人的维护好坏有关)和法(操作法)都与人的因素有关。
所以说,分质量反映了该工序的工作质量。
总质量是在上道工序提供的半成品(它的特征值反映了上工序的影响水平)的基础上,经过本工序的加工综合而成的产品质量。
总质量和分质量二者的关系可概括表示如下;分质量上工序的影响(简称上影)由此可见,分质量只是形成总质量的一部分。
分质量与上工序无关,如果能够针对每道工序的分质量进行控制,那么就在分析上切断了下工序与上工序的联系(当然,在实际的生产线中,不可能切断上下工序间的联系。