年产10万吨粗甲醇精馏工艺设计解析
关于对10万t/a甲醇工艺设计的概述

4 结束语
甲醇不仅是重要的基础化工原料 ,而且是重
低 、焦炉气利用率高、一次投资省 , 根据有关资 料 已在焦炉气制合成氨、焦炉气制甲醇工艺装置 中成功应用。本工程转化装置拟计划采用纯氧催
化部分氧化转化工艺。 3 5 甲醇合成 .
要 的二次能源产品,应用范 围不断扩大 ,本项 目
4
新疆化工
21 0 1年第 4期
关于对 1万t 甲醇工艺设计 的概述 O / a
王 博
( 宝钢集团八钢 公司,乌鲁木齐 8 0 2 3 0 2)
摘
要:介绍 了国投 宝地尼勒克焦炉煤气生产 甲醇工艺技术及设备方案设计时的有关选择进行 了说明,
我公 司委托北京众联盛设计院进行设计, 拟计划于 2 1 年 1 月建设投产, 05 1 为进一步完善设计,
变压吸附技术是利用吸附剂对气体混合物 中
各组分 的吸附能力随着压力 的变化而呈现差异的
特性 ,对混合气中的不 同组份进行选择性吸附 , 实现不 同气体分离 的装置。具有工艺简单 、操作
槽把关 ,使气体中的总硫 ≤O1p 。 . m p
3 4 转 化 .
方便、 装置开停车十分方便等优点 , 但产品单一,
塔顶出来的甲醇蒸汽作为常压精馏塔 的热源 ,节
3 1气 柜 .
自焦化装置来 的焦炉煤气的缓冲拟计划选用 容积为 200 00 m 的湿式螺旋气柜一台。
3 2 压缩 .
压缩包括焦炉煤气压缩 ,转化后的合成气和
循 环气 压缩 。焦炉 煤气 压缩 拟计 划采用 往 复式压
缩机对焦炉气进行 四级压缩 ,该压缩机具有 以下
化 、催化部分氧化和非催化部分氧化转化工艺。
采用纯氧 自 热式催化部分氧化转化 , 避免了 蒸汽转化外部间接加热 的形式 ,反应速度 比蒸汽 转化快 ,有利于强化生产 ;部分氧化法不需要昂 贵 的镍铬转化炉管 ,只需一段转化 , 转化炉类似
年产10万吨甲醇工艺设计

甲醇是一种重要的有机化工品,广泛应用于合成有机化合物、涂料、塑料等工业领域。
甲醇工艺设计的关键目标是实现高产量、高质量的甲醇生产,同时考虑能源消耗、环境污染和安全性等方面的要求。
本文将对一种年产10万吨甲醇工艺设计进行详细介绍,包括原料选择、反应过程、设备选型、能源消耗和环境污染控制等方面。
1.原料选择甲醇的主要原料为天然气或煤炭。
在本工艺设计中,我们选择优质天然气作为甲醇的主要原料。
天然气中的甲烷通过蒸汽重整反应生成合成气,包括一氧化碳和氢气。
该合成气经过净化处理后,进入甲醇合成反应器进行反应。
2.反应过程甲醇的合成反应是一种催化反应,主要基于甲醇合成催化剂的作用。
在本工艺设计中,我们选择了高效的铜锌氧化物催化剂,能够在相对低的温度和压力下实现高效率的甲醇合成。
反应过程主要包括气相反应和液相吸收两个步骤。
气相反应器中,一氧化碳和二氧化碳与氢气发生反应生成甲醇。
反应后的气体进入液相吸收器,通过溶剂的吸收和分离,将甲醇从废气中回收。
3.设备选型甲醇生产设备主要包括气体净化、蒸汽重整、合成反应、分离和脱水等装置。
对于年产10万吨甲醇的工艺设计,我们选用了适宜的设备类型和规格,确保设备能够满足预期产量和质量要求。
例如,气体净化装置采用活性炭吸附和分子筛吸附的组合方式,提高气体净化效果。
合成反应器采用多床催化剂装置,提高反应效率和催化剂的使用寿命。
分离装置采用精馏和吸附等工艺,实现甲醇的回收。
4.能源消耗甲醇生产需要消耗大量的能源,包括天然气和蒸汽等。
为了降低能源消耗和提高能源利用效率,我们在工艺设计中采取了多项措施。
例如,在蒸汽重整过程中,我们采用余热回收技术,将废弃热量回收利用。
在合成反应过程中,我们优化反应条件和催化剂的使用方式,降低能源消耗。
此外,我们还考虑了电力和水的节约措施,提高整体能源利用效率。
5.环境污染控制甲醇生产过程中会产生废气、废水和废渣等污染物。
为了控制环境污染,我们在工艺设计中采取了多项措施。
【精品完整版】年产10万吨甲醇精馏工段工艺设计

**学院
毕业设计设计题目:年产10万吨甲醇精馏工段工艺设计
系别:环境与化学工程系
班级:
姓名:
指导教师:
2011年6月 3 日
唐山学院毕业设计(论文)任务书
环境与化学工程系化学工程与工艺专业班姓名:
毕业设计(论文)时间:2011 年 3 月21 日至2011 年 6 月 3 日
年产10万吨甲醇精馏工段工艺设计
摘要
甲醇作为重要的有机化工原料,对其质量提出了更多更高的要求。
如今了解和熟悉甲醇精制的过程变得越来越普遍。
而通过精馏操作,可以将粗甲醇进行精制。
本设计需要将原料粗甲醇精制到含醇量99.95%的纯度。
根据现代对甲醇精馏工艺设计的了解,甲醇三塔精馏技术以其能耗低、产品质量好的优点领先于其他工艺。
所以本设计以三塔精馏工艺为依据,通过对粗甲醇进行物料衡算、能量衡算,设备选型,以及对主要设备常压塔的工艺尺寸计算,车间布局等完成本次初步设计,对提纯粗甲醇有更深刻的认识。
关键词:甲醇工艺设计三塔精馏常压塔。
年产十万吨甲醇设计
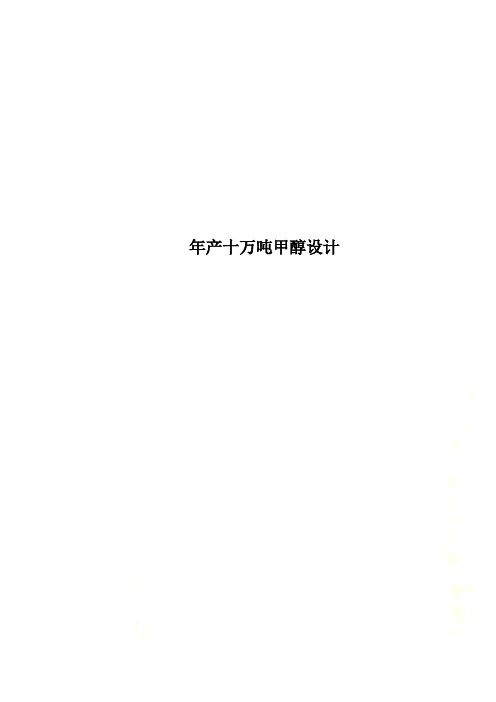
年产十万吨甲醇设计学号:题目:院(部)系所学专业年级、班级完成人姓名指导教师姓名专业技术职称年月日论文原创性保证书我保证所提交的论文都是自己独立完成,如有抄袭、剽窃、雷同等现象,愿承担相应后果,接受学校的处理。
专业:班级:签名:年月日摘要本设计重点描述了甲醇合成工艺流程。
甲醇是重要的化工原料和燃料,应用于多个领域。
首先简单地介绍了甲醇的生产发展、甲醇合成的反应热力学和动力学、甲醇反应需要的催化剂、甲醇合成工艺和甲醇的发展前景。
其中,甲醇合成催化剂和工艺选择关系着甲醇合成产量。
中低压、铜基催化剂的条件有利于甲醇合成。
紧接着介绍了甲醇合成工艺。
甲醇合成首先要进行造气。
造气选用煤作原料,得到的粗煤气经脱硫、脱碳等净化操作后进入合成塔合成甲醇。
甲醇合成工艺选择Luigi低压合成,合成气于5MPa、220℃下进入Luigi管壳式反应器。
从合成塔得到的粗甲醇必须要进行精馏。
本设计需要将原料粗甲醇精制到含醇量99.95%的纯度。
根据现代对甲醇精馏工艺设计的了解,甲醇三塔精馏技术以其能耗低、产品质量好的优点领先于其他工艺。
所以本设计采用三塔精馏工艺。
再接着对甲醇的生产合成和精馏过程进行了详细的物料衡算。
最后进行了常压精馏塔的计算,包括设备选型、塔的外形设计以及塔板流体力学验算。
通过本次设计,对合成甲醇以及提纯甲醇有更深刻的认识。
关键词:甲醇;合成;工艺设计;三塔精馏;常压塔AbstractThis design for methanol synthesis processes were described emphatically. Methanol is an important chemical raw material and fuel, is applied to the fields. First simply introduces the methanol production development, the reaction thermodynamics and kinetics of methanol synthesis, methanol reaction requires a catalyst, methanol synthesis process and the development prospects of methanol. Methanol synthesis catalyst and process selection is one of the relationship between the yield of methanol synthesis. In conditions of low pressure, copper base catalyst for methanol synthesis. Followed by methanol synthesis process was introduced. Gasification methanol synthesis should first. Gasification coal as raw materials, the raw coal gas after desulfurization and decarbonization purification operation into the synthesis of methanol synthesis tower. Choose Luigi low-pressure synthesis methanol synthesis process, synthesis gas in 5 mpa, 220 ℃ under into Luigi tubular reactor. From the crude methanol synthesis tower has to be distillation. This design need to be material crude methanol refining to the alcohol content of 99.95% purity. According to the modern understanding of the methanol distillation process design, methanol tower distillation technology for its low energy consumption, product quality good advantage ahead of other technology. So this design USES three tower distillation process. We'll go on with the production of methanol synthesis and material balance of distillation process in detail. Finally, the calculation of atmospheric distillation column was carried out, including equipment type selection, design of the tower and tray hydrodynamics calculation. Through the design, for methanol synthesis and purification of methanol has a more profoundunderstanding.Keywords:methanol;synthetic ;process design ;three tower distillation ;atmospheric column目录第一章前言 (1)1. 概述 (1)1.1 生产及技术发展 (1)2. 甲醇合成 (2)2.1 合成反应热力学 (2)2.2 合成反应动力学 (3)2.3 合成反应催化剂 (3)2.4 合成工艺 (4)2.5 合成甲醇的目的和意义 (5)第二章工艺概述 (6)1. 造气工段 (6)1.1 原料 (6)1.2 原料气的制备 (7)1.3 工艺概述 (7)1.4 净化工段 (8)2. 合成工段 (8)3. 精馏工段 (9)第三章工艺计算 (12)1. 甲醇生产的物料平衡计算 (12)1.1 合成塔物料平衡计算 (12)1.2 甲醇精馏的物料平衡计算 (15)第四章常压精馏塔计算 (18)1.基础数据 (18)2. 塔板数的计算 (19)2.1 处理能力 (19)2.2 最小理论板数 (19)2.3 最小回流比 (20)2.4 理论板数 (20)2.5 进料位置 (20)2.6 全塔效率的估算 (20)3. 精馏段与提馏段的体积流量 (21)3.1 精馏段 (21)3.2 提馏段 (23)4. 塔径计算 (24)4.1 精馏段 (24)4.2 提馏段 (25)5. 塔内件设计 (26)5.1 溢流堰的设计 (26)5.2 溢流装置 (26)5.3 塔板布置及浮阀数目与排列 (27)6. 塔板流体力学验算 (29)6.1 塔板压降 (29)6.2 液泛 (29)6.3 雾沫夹带 (30)7. 塔板负荷性能图 (31)7.1 雾沫夹带线 (31)7.2 液泛线 (31)7.3 液相负荷上限线 (32)7.4 漏液线 (32)7.5 液相负荷下限线 (33)8. 常压塔工艺计算汇总 (34)9. 常压塔塔高计算 (35)第五章 Aspen Plus 的模拟计算 (36)第一章前言1. 概述甲醇是最简单的化学品之一,是重要的化工基础原料和清洁液体燃料,广泛应用于有机合成、染料、医药、农药、涂料、汽车和国防等工业中。
年产10万吨煤合成甲醇工厂设计要点

年产10万吨煤合成甲醇工厂设计要点煤合成甲醇工厂设计要点煤合成甲醇工厂是利用煤作为原料制备甲醇的生产设备。
煤作为一种丰富的化石燃料,具有储量大、价格低廉以及可再生的特点,因此利用煤来生产甲醇具有较大的经济和环境优势。
下面我们将介绍设计一个年产10万吨煤合成甲醇工厂的要点。
1. 工艺选择煤合成甲醇工厂的工艺选择对于整个工厂的设计有至关重要的影响。
目前常见的工艺路线有间接法、直接法和半直接法等。
在选择工艺路线时需要考虑甲醇产率、甲醇纯度、能耗和设备投资等因素,综合比较各种工艺路线的优势和劣势,选择适合的工艺路线。
2. 原料处理煤是煤合成甲醇工厂的主要原料,但煤中含有许多杂质,如灰分、硫分、氮分等,需要进行原料处理。
原料处理的主要目的是去除杂质,提高煤的纯度,减少后续工艺过程中的能耗和设备磨损。
原料处理的主要工艺包括煤炭碎煤、煤炭洗选、煤泥脱水等。
3. 反应和分离煤合成甲醇的反应过程是核心环节,主要包括原料气化、合成气净化、合成气变换和甲醇合成等。
在反应过程中,需要注意反应温度、反应压力、反应速率等参数的控制,以保证反应的高效进行。
在分离过程中,主要包括甲醇的分离和副产物的回收利用。
4. 能源利用煤合成甲醇工厂需要大量的能源供应,包括煤炭燃烧产生的热能、原料气化产生的合成气以及电力等。
在能源利用上需要考虑能源的高效利用和节能减排。
通过合理设计能源系统,进行余热回收、废气处理和烟气排放控制等措施,以减少能源消耗和环境污染。
5. 设备选型煤合成甲醇工厂设备的选型对于工艺的高效运行和产品质量的保证至关重要。
设备选型需要考虑设备的质量、性能、可靠性和维修保养等方面。
此外,还需要考虑设备的运行安全和环境保护要求,选择符合国家标准和行业规范的设备。
6. 自动化控制煤合成甲醇工厂的生产过程复杂,需要进行自动化控制来实现对生产过程的监控和调控。
自动化控制系统可以实现对设备运行状态、工艺参数和产品质量等方面的实时监测和调节,提高生产效率和产品质量。
年产10万吨甲醇生产工艺

可见,以煤为原料制取甲醇的投资和成本最高。但是,随着能源的紧张,石油 价格的大幅增长,世界煤的储藏量远远超过天然气和石油,我国情况更是如此。从 长远的战略观点来看,将来终将以煤制取甲醇的原料路线占主导地位。 因此,从长远角度分析,本设计决定选用煤制甲醇原料气。
德士古煤气化工艺流程示意图 1、球磨机 2、煤浆槽 3、煤浆泵 4、气化炉 5、激冷器 6、灰渣锁斗 7、灰渣收集槽 8、筛网 9、文丘里洗涤器 10、洗涤塔 11、澄清槽 12、激冷泵 13、洗涤泵
Lurgi型甲醇合成塔
甲醇的精馏工艺
双效法三塔粗甲醇精馏工艺流程图 1、预精馏塔 2、第一精馏塔(加压) 3、第二精馏塔(常压) 4、回流液收集槽 5、冷凝器 6、再沸器 7、冷凝再沸器 8、回流泵 9、冷却器
甲醇合成塔计算
已知:年产100000吨精甲醇,每年以320个工作日计算。 精甲醇中甲醇含量(wt):99.95%
我国甲醇生产制造原料气的原料有气体、液体和固体原料。 气体原料有天然气、焦炉气、乙炔尾气、炼厂气、高炉气等。 液体原料有石脑油、重油、渣油等。
固体原料有焦炭、无烟煤、褐煤等。
以不同原料制取甲醇的经济效果,可以单纯地对比如下(以褐煤为100)。
投资 成本 褐煤 100 100 焦炉气 70~85 90 天然气 65 50~55 乙炔尾气 35 40
由以上模拟结果看出,模拟出的甲醇纯度为98.2%,塔径为1.55m,与计算结果相差不大。
结论
鲁奇低压生产甲醇工艺,是目前为止甲醇生产工艺中较为先进的方法, 较其他甲醇生产工艺更为清洁、节能、生产效率更高。本设计从鲁奇低压生 产甲醇工艺入手,通过论述生产过程、计算生产以及精制粗甲醇精馏塔计算 、Aspen Plus仿真模拟,较为全面地展现出年产10万吨甲醇的生产流程。 针对于当代甲醇精馏工艺,在保证纯度要求的基础上,三塔精馏以其节 能明显优益于其他工艺,所以,本设计采用了这个工艺。 对于塔设备的选择,通过对各种塔的比较,得出F1重型浮阀塔最适合本 设计。因为其优点明显:第一,生产能力大;第二,操作弹性大;第三,塔 板的效率高;第四,气体的压强降及液面落差比较小;第五,塔的造价低。 本设计对精馏的常压塔阶段进行工艺设计,并对该塔进行了简单的设计 。
年产10万吨甲酸精馏工段设计毕业设计

年产10万吨甲酸精馏工段设计毕业设计概述本文档将介绍年产10万吨甲酸精馏工段的设计方案。
甲酸精馏工段是甲酸生产过程中的重要环节,通过精馏工序将甲酸进行分离和纯化,以满足市场需求。
设计目标本设计的目标是达到年产10万吨甲酸的产量,并确保产品质量稳定可靠。
同时,设计方案应该提供高效的操作过程和可持续的生产方式,以降低能耗和环境影响。
设计方案1. 工段流程:采用多级精馏塔工艺,将原料甲酸进行连续精馏,分离出高纯度的甲酸产品。
具体的工段流程将根据实际工艺要求进行设计,并充分考虑工段间的热量和物料传递。
2. 设备选型:根据设计产能和产品要求,选择合适的精馏塔、冷凝器、加热炉等设备。
设备选型应考虑设备的耐腐蚀性、传热效率和操作稳定性,并确保设备能够满足工段的运行需求。
3. 能源优化:在设计方案中,应采用节能措施,如余热回收、换热器优化等,以降低能耗和生产成本。
同时,应考虑使用清洁能源替代传统能源,以减少对环境的影响。
4. 安全考虑:在设计中应充分考虑工段的安全性,确保关键设备的可靠性和操作的安全性。
应设置合理的安全装置,并进行必要的安全评估和风险控制。
5. 自动化控制:设计方案中应考虑自动化控制系统的应用,以提高生产效率和产品质量的稳定性。
自动化控制系统应能够实时监测和控制工段的各项参数,确保生产过程的可控性和可靠性。
结论通过以上设计方案的实施,预计能够实现年产10万吨甲酸的产量目标,并提供高质量的甲酸产品。
该方案不仅考虑了工段的操作效率和产品质量,还注重了能源优化和安全性的考虑。
同时,自动化控制系统的应用将提高工段的生产效率和运行稳定性。
最终,这个设计方案将为甲酸精馏工段的优化提供一个可行且可持续的解决方案。
年产10万吨甲醇工厂模拟设计
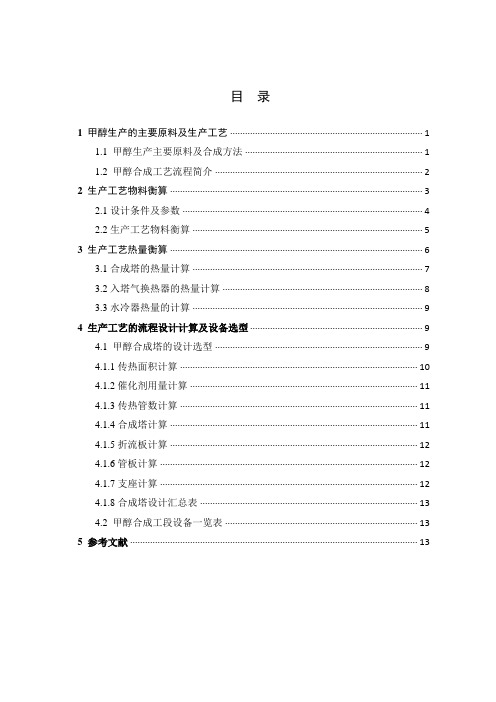
目录1甲醇生产的主要原料及生产工艺 (1)1.1甲醇生产主要原料及合成方法 (1)1.2甲醇合成工艺流程简介 (2)2生产工艺物料衡算 (3)2.1设计条件及参数 (4)2.2生产工艺物料衡算 (5)3生产工艺热量衡算 (6)3.1合成塔的热量计算 (7)3.2入塔气换热器的热量计算 (8)3.3水冷器热量的计算 (9)4生产工艺的流程设计计算及设备选型 (9)4.1甲醇合成塔的设计选型 (9)4.1.1传热面积计算 (10)4.1.2催化剂用量计算 (11)4.1.3传热管数计算 (11)4.1.4合成塔计算 (11)4.1.5折流板计算 (12)4.1.6管板计算 (12)4.1.7支座计算 (12)4.1.8合成塔设计汇总表 (13)4.2甲醇合成工段设备一览表 (13)5参考文献 (13)甲醇生产的主要原料及生产工艺1.1甲醇生产主要原料及合成方法我国甲醇生产制造原料气的原料有气体、液体和固体原料。
气体原料有天然气、焦炉气、乙炔尾气、炼厂气、高炉气等。
液体原料有石脑油、重油、渣油等。
固体原理有焦炭、无烟煤、褐煤等[1]。
目前甲醇生产技术主要采用低压法和中压法两种工艺,并且以低压法为主,这两种方法生产的甲醇约占世界甲醇产量的80%以上。
高压法:(19.6-29.4Mpa)是最初生产甲醇的方法,采用锌铬催化剂,反应温度360-400℃,压力19.6-29.4Mpa。
高压法由于原料和动力消耗大,反应温度高,生成粗甲醇中有机杂质含量高,而且投资大,其发展长期以来处于停顿状态。
低压法:(5.0-8.0 Mpa)是20世纪60年代后期发展起来的甲醇合成技术,低压法基于高活性的铜基催化剂,其活性明显高于锌铬催化剂,反应温度低(240-270℃)。
在较低压力下可获得较高的甲醇收率,且选择性好,减少了副反应,改善了甲醇质量,降低了原料消耗。
此外,由于压力低,动力消耗降低很多,工艺设备制造容易。
中压法:(9.8-12.0 Mpa)随着甲醇工业的大型化,如采用低压法势必导致工艺管道和设备较大,因此在低压法的基础上适当提高合成压力,即发展成为中压法。
- 1、下载文档前请自行甄别文档内容的完整性,平台不提供额外的编辑、内容补充、找答案等附加服务。
- 2、"仅部分预览"的文档,不可在线预览部分如存在完整性等问题,可反馈申请退款(可完整预览的文档不适用该条件!)。
- 3、如文档侵犯您的权益,请联系客服反馈,我们会尽快为您处理(人工客服工作时间:9:00-18:30)。
摘要 (3)第1章甲醇合成的基本概念 (4)1.1 甲醇的合成方法 (4)1.常用的合成方法 (4)2.本设计所采用的合成方法 (4)1.2 甲醇的合成路线 (5)1.常用的合成工艺 (5)2.本设计的合成工艺 (6)1.3合成甲醇的目的和意义 (7)1.4 本设计的主要方法及原理 (8)造气工段:使用二步法造气 (8)合成工段 (8)第2章生产工艺及主要设备计算 (9)2.1 甲醇生产的物料平衡计算 (10)2.1.2 粗甲醇精馏的物料平衡计算 (19)2.2 甲醇生产的能量平衡计算 (22)2.2.1 合成塔能量计算 (22)2.2.2 常压精馏塔能量衡算 (24)2.3.1 常压精馏塔计算 (27)2.3.2 初估塔径 (29)2.3.3 理论板数的计算 (31)2.3.4 塔内件设计 (34)2.3.5 塔板流体力学验算 (37)2.3.6 塔板负荷性能 (39)2.3.7 常压塔主要尺寸确定 (41)2.3.8 辅助设备 (43)参考文献 (44)致谢 (45)摘要甲醇作为及其重要的有机化工原料,是碳一化学工业的基础产品,在国民经济中占有重要地位。
长期以来,甲醇都是被作为农药,医药,染料等行业的工业原料,但随着科技的进步与发展,甲醇将被应用于越来越多的领域。
甲醇是一种无色、透明、易燃、易挥发的有毒液体,略有酒精气味。
分子量32.04,相对密度0.792(20/4℃),熔点-97.8℃,沸点64.5℃,闪点12.22℃,自燃点463.89℃,蒸气密度1.11,蒸气压13.33KPa(100mmHg 21.2℃),蒸气与空气混合物爆炸下限6~36.5 % ,能与水、乙醇、乙醚、苯、酮、卤代烃和许多其他有机溶剂相混溶,遇热、明火或氧化剂易燃烧。
甲醇用途广泛,是基础的有机化工原料和优质燃料。
主要应用于精细化工,塑料等领域,用来制造甲醛、醋酸、氯甲烷、甲氨、硫酸二甲脂等多种有机产品,也是农药、医药的重要原料之一。
甲醇在深加工后可作为一种新型清洁燃料,也加入汽油掺烧。
我国的甲醇工业经过十几年的发展,生产能力得到了很大提高。
1991年,我国的生产能力仅为70万吨,截止2004年底,我国甲醇产能已达740万吨,117家生产企业共生产甲醇440.65万吨,2005年甲醇产量达到500万吨,比2004年增长22.2%,进口量99.1万吨,因此下降3.1%。
于上世纪末相比,现在新建甲醇规模超过百万吨的已不再少数。
在2004——2008年新建的14套甲醇装置中平均规模为134万t/a,其中卡塔尔二期工程项目高达230万t/a。
最小规模的是智利甲醇项目,产能也达84万t/a,一些上世纪末还称得上经济规模的60万t/a装置因失去竞争力而纷纷关闭。
大型甲醇生产装置必须具备与其规模相适应的甲醇反应器和反应技术。
传统甲醇合成反应器有ICI的冷激型反应器,Lungi的管壳式反应器,Topsdpe的径向流动反应器等,近期出现的新合成甲醇反应器有日本东洋工程的MRF--Z反应器等,而反应技术方面则出现了Lurgi推出的水冷一气冷相结合的新流程。
通常的甲醇合成工艺中,未反应气体需循环返回反应器,而KPT则提出将未反应气体送往膜分离器,并将气体分为富含氢气的气体,前者作燃料用,后者返回反应器。
传统甲醇合成采用气相工艺,不足之处是原料单程转化率低,合成气净化成本高,能耗高。
相比之下,液相合成由于使用了比热容高,导热系数大的长链烷烃化合物作反应介质,可使甲醇合成在等温条件下进行。
关键词:设计工艺合成第1章甲醇合成的基本概念1.1 甲醇的合成方法1.常用的合成方法当今甲醇生产技术主要采用中压法和低压法两种工艺,并且以低压法为主,这两种方法生产的甲醇约占世界甲醇产量的80%以上。
高压法:(19.6-29.4Mpa)是最初生产甲醇的方法,采用锌铬催化剂,反应温度360-400℃,压力19.6-29.4Mpa。
高压法由于原料和动力消耗大,反应温度高,生成粗甲醇中有机杂质含量高,而且投资大,其发展长期以来处于停顿状态。
低压法:(5.0-8.0 Mpa)是20世纪60年代后期发展起来的甲醇合成技术,低压法基于高活性的铜基催化剂,其活性明显高于锌铬催化剂,反应温度低(240-270℃)。
在较低压力下可获得较高的甲醇收率,且选择性好,减少了副反应,改善了甲醇质量,降低了原料消耗。
此外,由于压力低,动力消耗降低很多,工艺设备制造容易。
中压法:(9.8-12.0 Mpa)随着甲醇工业的大型化,如采用低压法势必导致工艺管道和设备较大,因此在低压法的基础上适当提高合成压力,即发展成为中压法。
中压法仍采用高活性的铜基催化剂,反应温度与低压法相同,但由于提高了压力,相应的动力消耗略有增加。
目前,甲醇的生产方法还主要有①甲烷直接氧化法:2CH4+O2→2CH3OH.②由一氧化碳和氢气合成甲醇,③液化石油气氧化法2.本设计所采用的合成方法比较以上三者的优缺点,以投资成本,生产成本,产品收率为依据,选择中压法为生产甲醇的工艺,用CO和H2在加热压力下,在催化剂作用下合成甲醇,其主要反应式为:CO+ H2→CH3OH1.2 甲醇的合成路线1.常用的合成工艺虽然开发了高活性的铜基催化剂,合成甲醇从高压法转向低压法,完成了合成甲醇技术的一次重大飞跃,但仍存在许多问题:反应器结构复杂;单程转化率低,气体压缩和循环的耗能大;反应温度不易控制,反应器热稳定性差。
所有这些问题向人们揭示,在合成甲醇技术方面仍有很大的潜力,更新更高的技术等待我们去开发。
下面介绍20世纪80年代以来所取得的新成果。
(1) 气液固三项合成甲醇工艺首先由美国化学系统公司提出,采用三相流化床,液相是惰性介质,催化剂是ICI的Cu-Zn改进型催化剂。
对液相介质的要求:在甲醇合成条件下有很好的热稳定性和化学稳定性。
既是催化剂的硫化介质,又是反应热吸收介质,甲醇在液相介质中的溶解度越小越好,产物甲醇以气相的形式离开反应器。
这类液相介质有如三甲苯,液体石蜡和正十六烷等。
后来Berty等人提出了相反的观点,采用的液相介质除了热稳定性及化学稳定性外,要求甲醇在其溶液中的溶解度越大越好,产物甲醇不是以气相形式离开反应器,而是以液相形式离开反应器,在反应器外进行分离。
经试验发现四甘醇二甲醚是极理想的液相介质。
CO和H2在该液相中的气液平衡常数很大,采用Cu-Zn-Al 催化剂,其单程转化率大于相同条件下气相的平衡转化率。
气液固三相工艺的优点是:反应器结构简单,投资少;由于介质的存在改善了反应器的传热性能,温度易于控制,提高了反应器的热稳定性;催化剂的颗粒小,内扩散影响易于消除;合成甲醇的单程转化率高,可达15%-20%,循环比大为减小;能量回收利用率高;催化剂磨损少。
缺点是三相反应器压降较大,液相内的扩散系数比气相小的多。
(2) 液相法合成甲醇工艺液相合成甲醇工艺的特点是采用活性更高的过度金属络合催化剂。
催化剂均匀分布在液相介质中,不存在催化剂表面不均一性和内扩散影响问题,反应温度低,一般不超过200℃,20世纪80年代中期,美国Brookhaven国家实验室开发了活性很高的复合型催化剂,其结构为,其中M代表过渡金属Ni,Pd或Co,R为低碳烷基,当M为Ni,NaOH-RONa-M(OAc)2R为叔戊烷基时催化剂性能最好,液相介质为四氢呋喃,反应温度为80-120℃,压力为2MPa左右,合成气单程转化率高于80%,甲醇选择性高达96%。
当该催化剂与第Ⅵ族金属的羰基络合物混合使用时,能得到更好的效果,他能激活CO,并有较好的耐硫性,当合成气中还有1670×10-6的H2S时,其甲醇产率仍达33%。
Mahajan等人研制了由过渡金属络合物与醇盐组成的符合催化剂,如四羰基镍和甲醇钾,以四氢呋喃为液相介质,反应温度为125℃,CO转化率大于90%,选择性达99%。
目前液相合成甲醇研究仍处在实验室阶段,尚未工业化,但它是一种很有开发前景的合成技术。
该法的缺点是由于反应温度低,反应热不易回收利用;CO2和H2O容易使复合催化剂中毒,因此对合成气体的要求很苛刻,不能还有CO2和H2O,还需进一步研究。
(3) 新型GSSTFR和RSIPR反应器系统该系统采用反应,吸附和产物交换交替进行的一种新型反应装置。
GSSTFR是指气-液-固滴流流动反应系统,CO 和H2在催化剂的作用下,在此系统内进行反应合成甲醇,该甲醇马上被固态粉状吸附剂所吸附,并滴流带出反应系统。
RSIPR是级间产品脱出反应系统,当以吸附气态甲醇的粉状吸附剂流入该系统时,与该系统内的液相四甘醇二甲醚进行交换,气态的甲醇被液相所吸附,然后再将四甘醇二甲醚中的甲醇分离出来。
这样合成甲醇反应不断向右进行,CO的单程转化率可达100%,气相反应物不循环。
这项新工艺仍处在研究之中,尚未投入工业生产,还有许多技术问题需要解决和完善。
2.本设计的合成工艺经过净化的原料气,经预热加压,于5 Mpa、220 ℃下,从上到下进入Lurgi 反应器,在铜基催化剂的作用下发生反应,出口温度为250 ℃左右,甲醇7%左右,因此,原料气必须循环,则合成工序配置原则为图2-2。
甲醇的合成是可逆放热反应,为使反应达到较高的转化率,应迅速移走反应热,本设计采用Lurgi管壳式反应器,管程走反应气,壳程走4MPa的沸腾水粗甲醇驰放气图1-1合成合序配置原则甲醇合成的工艺流程(图①)这个流程是德国Lurgi公司开发的甲醇合成工艺,流程采用管壳式反应器,催化剂装在管内,反应热由管间沸腾水放走,并副产高压蒸汽,甲醇合成原料在离心式透平压缩机内加压到5.2 MPa (以1:5的比例混合) 循环,混合气体在进反应器前先与反应后气体换热,升温到220 ℃左右,然后进入管壳式反应器反应,反应热传给壳程中的水,产生的蒸汽进入汽包,出塔气温度约为250 ℃,含甲醇7%左右,经过换热冷却到40 ℃,冷凝的粗甲醇经分离器分离。
分离粗甲醇后的气体适当放空,控制系统中的惰性气体含量。
这部分空气作为燃料,大部分气体进入透平压缩机加压返回合成塔,合成塔副产的蒸汽及外部补充的高压蒸汽一起进入过热器加热到50 ℃,带动透平压缩机,透平后的低压蒸汽作为甲醇精馏工段所需热源。
1.3合成甲醇的目的和意义甲醇是极为重要的有机化工原料,在化工、医药、轻工、纺织及运输等行业都有广泛的应用,其衍生物产品发展前景广阔。
目前甲醇的深加工产品已达120多种,我国以甲醇为原料的一次加工产品已有近30种。
在化工生产中,甲醇可用于制造甲醛、醋酸、氯甲烷、甲胺、甲基叔丁基醚(MTBE)、聚乙烯醇(PVA)、硫酸二甲酯、对苯二甲酸二甲酯(DMT)、二甲醚、丙烯酸甲酯、甲基丙烯酸甲醇等。
以甲醇为中间体的煤基化学品深加工产业:从甲醇出发生产煤基化学品是未来C1化工发展的重要方向。