基于PLC控制的窑炉温度控制系统设计 2
基于PLC和MCGS的炉窑温度控制系统
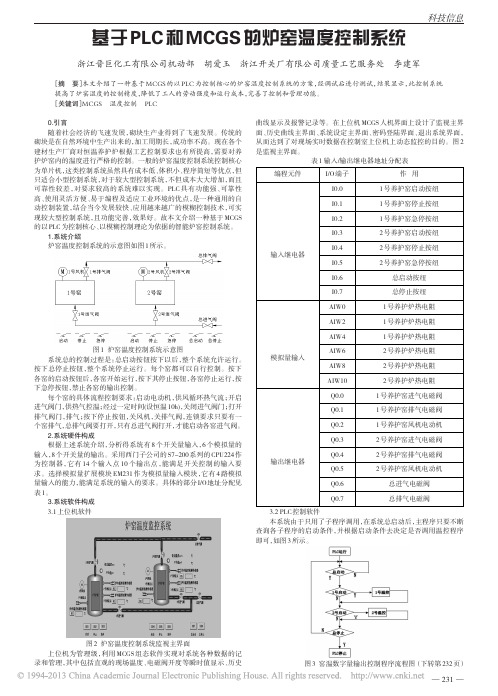
0.引言 随着社会经济的飞速发展,砌块生产业得到了飞速发展。传统的 砌块是在自然环境中生产出来的,加工周期长,成功率不高。现在各个 建材生产厂商对恒温养护炉根据工艺控制要求也有所提高,需要对养 护炉窑内的温度进行严格的控制。一般的炉窑温度控制系统控制核心 为单片机,这类控制系统虽然具有成本低、体积小、程序简短等优点,但 只适合小型控制系统,对于较大型控制系统,不但成本大大增加,而且 可靠性较差,对要求较高的系统难以实现。PLC 具有功能强、可靠性 高、使用灵活方便、易于编程及适应工业环境的优点,是一种通用的自 动控制装置,结合当今发展较快、应用越来越广的模糊控制技术,可实 现较大型控制系统,且功能完善,效果好。故本文介绍一种基于 MCGS 的以 PLC 为控制核心、以模糊控制理论为依据的智能炉窑控制系统。 1.系统介绍 炉窑温度控制系统的示意图如图 1 所示。
科技信息
基于 PLC 和 MCGS 的炉窑温度控制系统
浙江晋巨化工有限公司机动部 胡爱玉 浙江开关厂有限公司质量工艺服务处 李建军
[摘 要]本文介绍了一种基于 MCGS 的以 PLC 为控制核心的炉窑温度控制系统的方案,经调试后进行测试,结果显示,此控制系统 提高了炉窑温度的控制精度,降低了工人的劳动强度和运行成本,完善了控制和管理功能。 [关键词]MCGS 温度控制 PLC
(上ห้องสมุดไป่ตู้第 231 页) 4.结束语 本文介绍了利用 MCGS 组态软件、以 PLC 为控制核心的炉窑温度
控制系统的设计方案,并给出了软、硬件设计。经调试后进行测试,结 果显示,此控制系统提高了炉窑温度的控制精度,降低了工人的劳动强 度和运行成本,完善了控制和管理功能。
参考文献
— 232 —
[1]曹辉,马栋萍.组态软件技术及应用.北京:电子工业出版社, 2009
基于PLC的内模PID窑炉温度控制系统设计
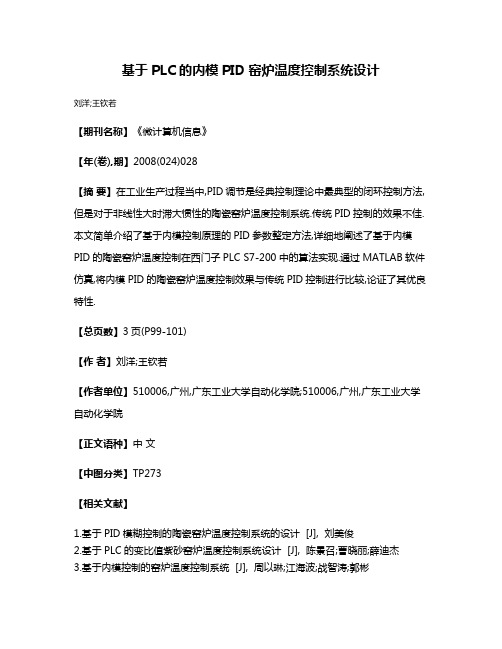
基于PLC的内模PID窑炉温度控制系统设计
刘洋;王钦若
【期刊名称】《微计算机信息》
【年(卷),期】2008(024)028
【摘要】在工业生产过程当中,PID调节是经典控制理论中最典型的闭环控制方法,但是对于非线性大时滞大惯性的陶瓷窑炉温度控制系统.传统PID控制的效果不佳.本文简单介绍了基于内模控制原理的PID参数整定方法,详细地阐述了基于内模PID的陶瓷窑炉温度控制在西门子PLC S7-200中的算法实现.通过MATLAB软件仿真,将内模PID的陶瓷窑炉温度控制效果与传统PID控制进行比较,论证了其优良特性.
【总页数】3页(P99-101)
【作者】刘洋;王钦若
【作者单位】510006,广州,广东工业大学自动化学院;510006,广州,广东工业大学自动化学院
【正文语种】中文
【中图分类】TP273
【相关文献】
1.基于PID模糊控制的陶瓷窑炉温度控制系统的设计 [J], 刘美俊
2.基于PLC的变比值紫砂窑炉温度控制系统设计 [J], 陈景召;曹晓丽;薛迪杰
3.基于内模控制的窑炉温度控制系统 [J], 周以琳;江海波;战智涛;郭彬
4.基于PLC的电炉PID温度控制系统设计 [J], 吴慧君;韩志引
5.基于模糊内模-PID的包装机热封切刀温度控制 [J], 覃羡烘
因版权原因,仅展示原文概要,查看原文内容请购买。
基于PLC的智能炉温网络控制系统设计

基于PLC的智能炉温网络控制系统设计环形炉温控制系统的良好设计,将直接关系到炉的燃烧质量和燃料的节约,以及减少对污染气体的排放。
近几年,由于智能化的炉温控制系统越来越成熟,对以后的工业发展显得越来越重要,也是社会的发展趋势。
标签:PLC;智能控制系统;炉温;设计引言燃炉主要运用于冶金、采矿等众多工业领域,智能炉温控制系统通过PLC 的智能调节系统,能够很好地实时监测和调整炉温,使炉内的燃料尽量达到完全燃烧,减少对燃料的浪费,降低对空气的污染。
基于PLC智能控制系统的设计和应用,将在很大程度上减少了人力的投入,也保证了燃炉的安全性和高效性。
1 系统结构设计该系统的主要结构由PLC以及MCF5272构成,系统的运行部件由电动部件和切向调节阀构成,并且微处理器会自动把数据处理后传输给PLC。
而PLC会通过模糊的智能控制系统把数据处理好后输出给系统,制动调节水位的装置会根据智能控制系统反馈的信息,把水位调节到与闸门相平衡的位置。
这样始终保持锅炉中的水位与水蒸气蒸发掉的水位保持平衡,达到自动控制的目的。
1.1 搭建硬件平台给燃炉搭建一个合适的平台,通过预先输入实测的温度值,经过预设系统进行计算。
不断调整系统的参数,使实测值与计算值相符,以达到对水位的及时调整,保证蒸汽量的持续输出。
将数据处理器处理后的数据传输到PLC,这样PLC 就可以不用再对数据进行处理,直接对接受的信号做出相应的反应。
PLC智能控制系统,既保证了运行的安全性又大大地减少了人力,对以后的锅炉发展有大大的好处。
下面,通过一张图纸,更清晰地了解搭建平台的具体布置。
1.2 实现系统软件的控制在平台上通过软件的方式对锅炉进行实时控制,防止锅炉出现危险,并且当锅炉出现危险时,系统通过报警器自动发出警报,这时还可以通过人为的方式进行手动控制,来应对不可逆转的过程。
而在正常情况下,还是主要采取智能控制的方式为主,人为控制的方式为辅。
1.3 应用WISMO2C通信控制模块系统中装入SIM卡,不仅可以方便地输入和输出數据,还可以实时地进行一些漏洞的修补,以便系统能够更好地运行。
基于PLC控制的加热炉温度控制系统设计

基于PLC控制的加热炉温度控制系统设计概述加热炉是工业生产中常见的设备之一,其主要作用是提供高温环境用于加热物体。
为了确保加热炉的稳定性和安全性,需要设计一个可靠的温度控制系统。
本文将介绍一个基于PLC(可编程逻辑控制器)控制的加热炉温度控制系统设计方案。
系统设计原理在加热炉温度控制系统中,PLC作为核心控制器,通过监测温度传感器的输出信号,根据预设的温度设定值和控制策略,控制加热炉的加热功率,从而实现对加热炉温度的稳定控制。
以下是系统设计的主要步骤:1.硬件设备选择:选择适合的温度传感器和控制元件,如热电偶、温度控制继电器等。
2.PLC选型:根据实际需求,选择合适的PLC型号。
PLC需要具备足够的输入输出点数和计算能力。
3.传感器连接:将温度传感器接入PLC的输入端口,读取实时温度数据。
4.温度控制策略设计:根据加热炉的特性和工艺需求,设计合适的温度控制策略。
常见的控制策略包括比例控制、积分控制和微分控制。
5.控制算法实现:根据温度控制策略,编写PLC程序,在每个采样周期内计算控制算法的输出值。
6.加热功率控制:使用控制继电器或可调功率装置,控制加热炉的加热功率。
7.温度反馈控制:通过监测实际加热炉温度和设定值之间的差异,不断修正加热功率控制,使加热炉温度稳定在设定值附近。
系统硬件设计基于PLC控制的加热炉温度控制系统的硬件设计主要包括以下几个方面:1.温度传感器:常用的温度传感器有热电偶和热敏电阻。
根据加热炉的工艺需求和温度范围,选择适合的温度传感器。
2.PLC:选择适合的PLC型号,根据实际需求确定PLC的输入输出点数和计算能力。
3.控制继电器或可调功率装置:用于控制加热炉的加热功率。
根据加热炉的功率需求和控制方式,选择合适的继电器或可调功率装置。
4.运行指示灯和报警器:用于显示系统的运行状态和报警信息。
PLC程序设计PLC程序是基于PLC的加热炉温度控制系统的关键部分,其主要功能是实现温度控制算法。
《基于PLC的环形炉温度控制系统设计与应用》范文

《基于PLC的环形炉温度控制系统设计与应用》篇一一、引言随着工业自动化技术的不断发展,温度控制系统的设计与应用在工业生产中显得尤为重要。
环形炉作为许多工业生产过程中的关键设备,其温度控制系统的稳定性和精确性直接影响到产品的质量和生产效率。
因此,基于PLC的环形炉温度控制系统应运而生,本文将介绍其设计思路和应用效果。
二、系统设计1. 系统构成基于PLC的环形炉温度控制系统主要由PLC控制器、温度传感器、执行机构、人机界面等部分组成。
其中,PLC控制器作为系统的核心,负责接收温度传感器的信号,根据设定的控制算法输出控制信号,驱动执行机构进行温度调节。
2. PLC控制器设计PLC控制器是整个系统的“大脑”,其设计应考虑到系统的实时性、稳定性和可扩展性。
首先,应选择合适的PLC型号,根据环形炉的规模和工艺要求,确定I/O点的数量和类型。
其次,编写控制程序,实现温度的实时监测、报警、自动调节等功能。
此外,还应考虑到系统的故障诊断和保护功能,确保系统的稳定运行。
3. 温度传感器和执行机构的选择温度传感器是测量环形炉温度的关键部件,应选择具有高精度、高稳定性的传感器。
执行机构则是根据PLC控制器的指令进行温度调节的部件,常见的有电动调节阀、电动执行器等。
在选择时,应考虑到其响应速度、调节精度和可靠性等因素。
4. 人机界面设计人机界面是操作人员与系统进行交互的界面,应设计得简洁、直观、易操作。
通过人机界面,操作人员可以实时监测环形炉的温度、设定温度目标值、查看报警信息等。
此外,还应具备历史数据查询、报表生成等功能,方便操作人员进行生产管理和数据分析。
三、系统应用基于PLC的环形炉温度控制系统在实际应用中取得了显著的效果。
首先,该系统具有较高的控制精度和稳定性,能够实时监测环形炉的温度,并根据设定的控制算法自动调节执行机构,使温度保持在设定范围内。
其次,该系统具有丰富的功能,如温度报警、历史数据查询、报表生成等,方便操作人员进行生产管理和数据分析。
基于PLC的锅炉温度控制系统设计方案

基于PLC的锅炉温度控制系统设计方案目录摘要 (1)第一章绪论 (3)1.1课题背景及研究目的和意义 (3)1.2国内外研究现状 (3)1.3项目研究内容 (4)第二章 PLC和组态软件基础 (5)2.1可编程控制器基础 (5)2.1.1可编程控制器的产生和应用 (5)2.1.2可编程控制器的组成和工作原理 ············错误!未定义书签。
2.1.3可编程控制器的分类及特点 (7)2.2组态软件的基础 (8)2.2.1组态的定义 (8)2.2.2组态王软件的特点 (8)2.2.3组态王软件仿真的基本方法 (8)第三章 PLC控制系统的硬件设计 (9)3.1 PLC控制系统设计的基本原则和步骤 (9)3.1.1 PLC控制系统设计的基本原则 (9)3.1.2 PLC控制系统设计的一般步骤 (9)3.1.3 PLC程序设计的一般步骤 (10)3.2 PLC的选型和硬件配置 (11)3.2.1 PLC型号的选择 (11)3.2.2 S7-200CPU的选择 (12)3.2.3 EM235模拟量输入/输出模块 (12)3.2.5 可控硅加热装置简介 (12)3.3 系统整体设计方案和电气连接图 (13)3.4 PLC控制器的设计 (14)3.4.1 控制系统数学模型的建立 (14)3.4.2 PID控制及参数整定 (14)第四章 PLC控制系统的软件设计 (16)4.1 PLC程序设计的方法 (16)4.2 编程软件STEP7--Micro/WIN 概述 (17)4.2.1 STEP7--Micro/WIN 简单介绍 (17)4.2.2 计算机与PLC的通信 (18)4.3 程序设计 (18)4.3.1程序设计思路 (18)4.3.2 PID指令向导 (19)4.3.3 控制程序及分析 (25)第五章组态画面的设计 (29)5.1组态变量的建立及设备连接 (29)5.1.1新建项目 (29)5.2创建组态画面 (33)5.2.1新建主画面 (33)5.2.2新建PID参数设定窗口 (34)5.2.3新建数据报表 (34)5.2.4新建实时曲线 (35)5.2.5新建历史曲线 (35)5.2.6新建报警窗口 (36)第六章系统测试 (37)6.1启动组态王 (37)6.2实时曲线观察 (38)6.3分析历史趋势曲线 (38)6.4查看数据报表 (40)结束语 (43)参考文献 (44)摘要从上世纪80年代至90年代中期,PLC得到了快速的发展,在这时期,PLC在处理模拟量能力、数字运算能力、人机接口能力和网络能力得到大幅度提高,PLC 逐渐进入过程控制领域,在某些应用上取代了在过程控制领域处于统治地位的DCS系统。
3909_基于Plc加热炉温度控制系统设计

基于PLC加热炉温度控制系统设计【摘 要】温度控制系统在国内各行各业的应用虽然已经十分广泛,但从国内生产的温度控制器来讲,总体发展水平仍然不高,同国外的日本、美国、德国等先进国家相比,仍然有着较大的差距。
加热炉的温度控制系统具有较大的容量滞后,采用单回路控制往往会出现较大的动态偏差,很难达到好的控制效果,为提高系统对负荷变化较大或其他扰动比较剧烈时的控制质量,采用基于PLC的加热炉温度控制系统来提高加热炉的燃烧效率。
可编程序控制器(PLC)是一种新型的通用的自动控制装置,它将传统的继电器控制技术、计算机技术和通讯技术融为一体,是功能加强、编程简单、使用方便以及体积小、重量轻、功耗低等一系列优点。
PLC的应用领域已经拓宽到了各个领域,PLC的发展历程在工业生产过程中,大量的开关量顺序控制,它按照逻辑条件进行顺序动作,并按照逻辑关系进行连锁保护动作的控制,及大量离散量的数据采集。
在传统上,这些功能是通过气动或电气控制系统来实现的。
PLC最基本最广泛的用于开关量的逻辑控制,它取代传统的继电器电路,实现逻辑控制,顺序控制,既可用于单台设备的控制,也可用于多机群控及自动化流水线。
如注塑机,印刷机,订书机,组合抢答器,磨床,包装等。
目前,PLC在国内外已广泛应用于钢铁,石油,化工,电力,建材,机械制造,汽车,轻纺,交通运输,环保及文化娱乐等各个行业,使用广泛。
本设计将以PLC为核心设计了系统结构图、程序指令、梯形图以及输入输出端子的分配方案,在保留了原始加热炉温度控制系统的基本功能的同时又增加了一系列的实用功能并简化其电路结构,其将以控制方便,灵活,只要改变输入PLC的控制程序,就能够实现对加热炉温度的控制。
【关键词】加热炉温度控制系统可编程控制器燃烧效率System design of heating furnace temperaturecontrol based on PLC【Abstract】:Pneumatic manipulator is a automated devices thatcan mimic the human hand and arm movements to do something,aslo can according to a fixed procedure to moving objects or control tools. It can replace the heavy labor in order to achieve the production mechanization and automation, and can work in dangerous working environments to protect the personal safety, Therefore widely used in machine building, metallurgy, electronics, light industry and atomic energy sectors.This article is mainly of the PLC manipulator the overall design, and pneumatic design. This mechanism of manipulator includes cylinders and claws and connectors parts, it can move according to the due track on the movement of grabbing, carrying and unloading. The pneumatic part of the design is primarily to choose the right valves and design a reasonable pneumatic control loop, by controlling and regulating pressure, flow and direction of the compressed air to make it get the necessary strength, speed and changed the direction of movement in the prescribed procedure work.It can replace the heavy labor in order to achieve the production mechanization and automation, and can work in dangerous working environments to protect the personal safety, Therefore widely used in machine building, metallurgy, electronics, light industry and atomic .The principle, technical pare-maters, transmiting system and main parts structure of mincing ma-chine were introduced.The PLC was analysed.Keywords Mincing machine Holds plate Cutting blade Transfer auger【Keywords】:pneumatic manipulator PLC pneumatic loop Four degrees of freedom.目录第一章、绪论 (5)1.1 本课题的发展概况 (6)1.2 加热炉温控系统的实现过程概述 (6)1.3 本课题研究的内容和意义 (7)1.4 PLC简介 (7)1.4.1 PLC的定义 (9)1.4.2 PLC的基础知识 (11)1.4.3 PLC的用途 (12)1.5 PLC的组成 (13)1.5.1中央处理单元 (13)1.5.2存储器 (15)1.5.3输入输出单元 (15)1.5.4通讯接口 (16)1.5.5智能接口模块 (16)1.5.6编程装置 (16)1.5.7电源 (16)第二章、加热炉温度控制系统总体方案与PID算法的设计 (17)2.1 总体方案的设计 (17)2.1.1硬件模块的设计 (17)2.1.2软件模块的设计 (17)2.2 PID控制算法的介绍 (17)2.2.1 PID控制算法的设计 (17)2.2.2 PID控制器参数的整定 (17)第三章、加热炉温度控制系统的PLC设计 (17)3.1 输入输出点分配 (18)3.2 PLC的选择 (19)3.3 加热炉温度控制系统PLC控制系统接线图 (20)3.4 加热炉温度控制系统主程序流程图的确定 (20)3.5 加热炉温度控制系统温度控制系统图的确定 (20)第四章、加热炉温度控制系统PLC控制程序 (21)4.1西门子S7-200的介绍 (22)4.2加热炉温度控制系统西门子S7-200程序的实现 (24)结论 (25)致谢 (26)参考文献 (27)第一章绪论1.1 本课题的发展概况温度控制系统在工业生产中获得了广泛的应用,在工农业生产、国防、科研以及日常生活等领域占有重要的地位。
基于PLC电热炉温度控制系统设计

基于PLC电热炉温度控制系统设计随着工业自动化的不断发展,PLC(可编程逻辑控制器)在工业生产中的应用越来越广泛。
其中,电热炉温度控制系统是一个重要的应用领域。
本文将就基于PLC电热炉温度控制系统设计展开深入的研究,以期能为相关领域的工程师和技术人员提供有价值的参考。
首先,我们将介绍PLC电热炉温度控制系统的基本原理和工作流程。
在一个典型的电热炉中,温度是一个重要参数,它直接影响着产品质量和生产效率。
传统上,人工操作是常用的温度控制方法。
然而,这种方法存在许多缺点,如操作不稳定、效率低下等。
而基于PLC技术设计的电热炉温度控制系统能够自动化地实现对温度进行精确、稳定地控制。
接下来我们将详细介绍PLC在电热炉温度控制系统中所起到的作用。
首先是传感器部分,在这个部分中我们会介绍温度传感器的种类和工作原理,并详细解释如何选择合适的传感器以及如何进行正确的安装和校准。
接下来是控制器部分,我们将介绍PLC控制器的基本原理以及其在温度控制中的应用。
此外,我们还将讨论PLC在数据采集和通信方面的作用,以及如何进行数据处理和分析。
然后,我们将详细介绍PLC电热炉温度控制系统设计中所需要考虑的关键因素。
首先是系统稳定性和可靠性。
在电热炉温度控制系统中,稳定性是至关重要的因素。
我们将讨论如何通过合适的控制算法来实现系统稳定,并介绍一些常用的控制算法,如PID(比例-积分-微分)算法等。
此外,我们还将讨论硬件设计方面需要考虑的因素,如电路设计、电源设计等。
接下来是安全性问题。
在一个工业生产环境中,安全问题是非常重要且不可忽视的因素。
我们将讨论一些常见安全问题,并提出相应解决方案。
最后,在本文中我们还将介绍一些实际案例,并对其进行分析和评估。
这些案例将涵盖不同的行业和应用领域,以期能够提供更多的实践经验和参考。
综上所述,本文将从基本原理、PLC技术应用、关键因素考虑以及实际案例分析等方面对基于PLC电热炉温度控制系统设计展开深入研究。
- 1、下载文档前请自行甄别文档内容的完整性,平台不提供额外的编辑、内容补充、找答案等附加服务。
- 2、"仅部分预览"的文档,不可在线预览部分如存在完整性等问题,可反馈申请退款(可完整预览的文档不适用该条件!)。
- 3、如文档侵犯您的权益,请联系客服反馈,我们会尽快为您处理(人工客服工作时间:9:00-18:30)。
名称
地址
名称
地址
启动
I0.0
绿灯亮
Q0.2
停止
I0.1
黄灯亮Q0.3Fra bibliotek加热Q0.0
警报响
Q0,4
红灯亮
Q0.1
热敏电阻
I0.2
第四章 软件系统的设计
4.1 S7—200软件的介绍
S7—200 PLC编程软件是由西门子公司专为S7-200系列PLC设计开发,它功能强大,主要为用户开发控制程序使用,例如创建用户程序、修改和编辑原有的用户程序,编辑过程中编辑器具有简单语法检查功能。同时它还有一些工具性的功能,例如用户程序的文档管理和加密等。此外,还可直接用软件设置PLC的工作方式、参数和运行监控等。
(2)开关量I/O扩展模块当CPU的I/0点数不够用或需要进行特殊功能的控制时,就要进行I/O扩展,I/O扩展包括I/O点数的扩展和功能模块的扩展。通常开关量I/O模块产品分3种类型:输入模块,输出模块以及输入/输出模块。为了保证PLC的工作可靠性,在输入模块中都采用提高可靠性的技术措施。如光电隔离,输入保护(浪涌吸收器,旁路二极管,限流电阻),高频滤波,输入数据缓冲器等。由于PLC要控制的对象有多种,因此输出模块也应根据负载进行选择,有直流输出模块,交流输出模块和交直流输出模块。按照输出开关器件种类不同又分为3种:继电器输出型,晶体管输出型和双向晶闸管输出型。这三种输出方式中,从输出响应速度来看,晶体管输出型最快,继电器输出型最差,晶闸管输出型居中;若从与外部电路安全隔离角度看,继电器输出型最好。在实际使用时,亦应仔细查看开关量I/O模块的技术特性,按照实际情况进行选择。
参考文献…………………………………………………………….23
第一章炉窑温度控制系统设计的内容及要求
1.1任务描述
在传统窑炉温控PLC控制装置的基础上,设计一种自适应的温控PLC控制实训装置,该装置需要具备以下主要功能:(1)断窑时自动控制好窑炉温度(2)实时利用传感器体现窑炉温度(3)精确控制所需温度。逻辑图如图1.1(额定值设置为100-120):
S7-200系列可以根据对象的不同,可以选用不同的型号和不同数量的模块。并可以将这些模块安装在同一机架上。
控制核心采用西门子PLC的CPU224,提供数字量输入点数14点,数字量输出点数10点(提供给扩展单元DC5V电流能力为660mA),完全满足系统的数字量和开关量输入输出点数的要求。CPU224本身不具备模拟量输入和输出单元,
热敏电阻:由具有很高电阻温度系数的固体半导体材料构成的热敏类型的温度检测元件。热敏电阻器是敏感元件的一类,按照温度系数不同分为正温度系数热敏电阻(PTC)和负温度系数热敏电阻器(NTC)。热敏电阻器的典型特点是对温度敏感,不同的温度下表现出不同的电阻值。正温度系数热敏电阻器(PTC)在温度越高时电阻值越大,负温度系数热敏电阻器(NTC)在温度越高时电阻值越低,它们同属于半导体器件。热电偶温度传感器的工作原理:两种不同的金属A和B构成闭合回路,当两个接触端T﹥T0时,则在该回路中就会产生电动势,这种现象称为热电效应,该电动势称为热电势。这两种不同材料的导体或半导体的组合称为热电偶,导体A、B称为热电极。两个接点,一个称热端,又称测量端或工作端,测温时将它置于被测介质中;另一个称冷端,又称参考端或自由端,它通过导线与显示仪表相连。
第三章 I/O地址的分配
3.1 I/O地址的简介
输入/输出信号在PLC接线端子上的地址分配是进行PLC控制系统设计的基础。对软件来说,I/O地址分配以后才可进行编程;对控制柜及PLC的外围接线来说,只有I/O地址确定以后,才可以绘制电气接线图、装配图,让装配人员根据线路图和安装图安装控制柜。
3.2系统各元件对应的I/O地址
图2.1炉窑温度控制系统流程图
流程图是流经一个系统的信息流、观点流或部件流的图形代表。在企业中,流程图主要用来说明某一过程。这种过程既可以是生产线上的工艺流程,也可以是完成一项任务必需的管理过程。
流程图作为一种直观的图形,对准确了解事情是如何进行的,以及决定应如何改进过程极有帮助。画出正确的流程图不仅可以帮我们直观的分析设计的过程,也能让我们更清楚明了的看见控制系统运作方向。
3.2系统各元件对应的I/O地址…………………………….10
第四章 软件系统的设计…………………………………………10
4.1S7—200软件的介绍.............................10
4.2程序编辑和调试………………………………………… 11
第五章总结………………………………………………………22
由于本系统是单回路的反馈系统,CPU224XP相比与其他型号具有更好的硬件指标,其上自带有模拟量的输入和输出通道,因此节省了元器件的成本,CPU224XP自带的模拟量I/O规格如表:
表2.1模拟量I/O配置表
I/O信号信号类型
电压信号
电流信号
模拟量输入*2
±10V
/
模拟量输出
0~10V
0~20mA
CPU224XP自带的模拟量输入通道有2个,模拟量输出通道1个。
在S7-200中,单极性模拟量的输入/输出信号的数值范围是0~32000,双极性模拟信号的数值范围是-32000~+32000
2.2温度传感器的选择
在此设计中,炉窑窑顶安装两个热电偶传感器进行炉内温度采集。按照测温的范围,选择热电偶传感器。热电偶传感器的测量范围为-50℃~1600℃,精度为±(1%~5%)。1号炉和2号炉的温度分别由两个热敏电阻传感器进行采集。按照测温的范围,选择热敏电阻传感器。
第一章炉窑温度控制系统设计的内容及要求··············4
第二章 系统硬件设计…………………………………………… 6
2.1选取PLC的类型及容量……………………………………6
2.2温度传感器的选择…………………………………………7
第三章I/O地址的分配………………………………………… 9
3.1I/O地址的简介……………………………………………9
SiemensS7-200主要功能模块介绍:
(1)CPU模块S7-200的CPU模块包括一个中央处理单元,电源以及数字I/O点,这些都被集成在一个紧凑,独立的设备中。CPU负责执行程序,输入部分从现场设备中采集信号,输出部分则输出控制信号,驱动外部负载.从CPU模块的功能来看, CPU模块为CPU22*,它具有如下五种不同的结构配置CPU单元:①CPU221它有6输入/4输出,I/0共计10点.无扩展能力,程序和数据存储容量较小,有一定的高速计数处理能力,非常适合于少点数的控制系统。②CPU222它有8输入/6输出,I/0共计14点,和CPU 221相比,它可以进行一定的模拟量控制和2个模块的扩展,因此是应用更广泛的全功能控制器。③CPU224它有14输入/10输出,I/0共计24点,和前两者相比,存储容量扩大了一倍,它可以有7个扩展模块,有内置时钟,它有更强的模拟量和高速计数的处理能力,是使用得最多S7-200产品。④CPU226它有24输入/16输出,I/0共计40点,和CPU224相比,增加了通信口的数量,通信能力大大增强。它可用于点数较多,要求较高的小型或中型控制系统。⑤CPU226XM它在用户程序存储容量和数据存储容量上进行了扩展,其他指标和CPU226相同。
下,输出基准量时被控制温度接近较佳值。
(3)系统组成总体结构
根据本次设计系统具体指标要求,可以对每一个具体部分进行分析设计。整个控制系统分为硬件设计和软件设计两部分。
系统硬件框图如下图所示:
整个控制系统是一个相对联系的结合体,但是又可以分开讨论。
当被控对象为炉内温度,温度传感器检测炉内的温度信号,经变送器将温度值转换成电信号送入PLC模块。PLC将这个测量信号与设定值比较得到偏差,经计算后,发出控制信号,经电动调节阀的控制,达到温度的恒温控制,下面为温度控制流程图:
Y
N N
Y Y Y Y
N N
图1.1逻辑控制图
1.2控制要求
将被控系统的温度控制在给定值之间,当温度低于或高于给定值时,应能自动进行调整,当调整3分钟后仍不能脱离不正常状态,则应采用声光报警,以提醒操作人员注意排除故障。
系统设置一个启动按纽-启动控制程序,设置绿,红,黄3个指示灯来指示温度状态。被控温度在要求范围内,绿灯亮,表示系统运行正常。当被控温度超过上限或低于下限时,经调整3分钟后仍不能回到正常范围,则红灯或黄灯亮,并有声音报警,表示温度超过上限或低于下限。
毕业设计(论文)
题目:基于PLC的立体保险柜控制系统的设计
系(部):机械电子工程系
专业班级:机械一
姓名:汤其东
学号:12242513503
指导教师:陈洪亮
2013年 4月 6日
前言
PLC即可编程逻辑控制器(可编程控制器件)。
可编程逻辑控制器(Programmable Logic Controller,PLC),它采用一类可编程的存储器,用于其内部存储程序,执行逻辑运算、顺序控制、定时、计数与算术操作等面向用户的指令,并通过数字或模拟式输入/输出控制各种类型的机械或生产过程。
第二章系统硬件设计
2.1选取PLC的类型及容量
S7-200系列PLC是由德国西门子公司生产的一种超小型系列可编程控制器,它能够满足多种自动化控制的需求,其设计紧凑,价格低廉,并且具有良好的可扩展性以及强大的指令功能,可代替继电器在简单的控制场合,也可以用于复杂的自动化控制系统。由于它具有极强的通信功能,在大型网络控制系统中也能充分发挥作用。
流量传感器是对进入养护炉空气流量的检测部件,在此论文中选择法兰式V锥流量传感器FFM61S。
工作原理:V锥流量计是由V锥传感器和差压变送器组合而成的一种差压流量计,可精确测量宽雷诺数(8×103≤Re≤5×107)范围内各种介质的流量。