25吨位起重机伸缩机构液压系统设计
汽车起重机液压系统设计方案
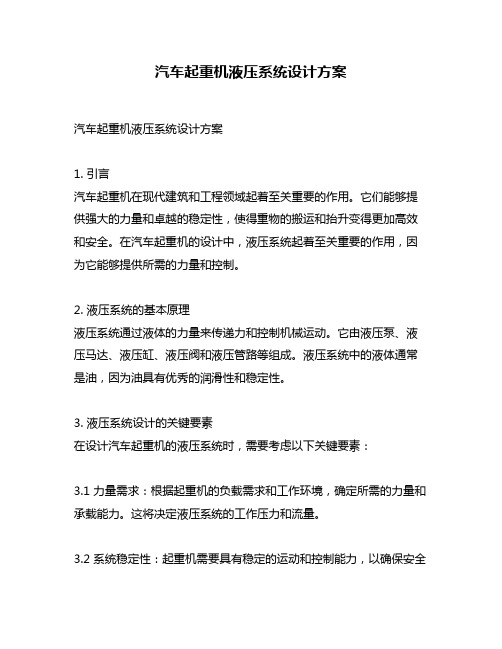
汽车起重机液压系统设计方案汽车起重机液压系统设计方案1. 引言汽车起重机在现代建筑和工程领域起着至关重要的作用。
它们能够提供强大的力量和卓越的稳定性,使得重物的搬运和抬升变得更加高效和安全。
在汽车起重机的设计中,液压系统起着至关重要的作用,因为它能够提供所需的力量和控制。
2. 液压系统的基本原理液压系统通过液体的力量来传递力和控制机械运动。
它由液压泵、液压马达、液压缸、液压阀和液压管路等组成。
液压系统中的液体通常是油,因为油具有优秀的润滑性和稳定性。
3. 液压系统设计的关键要素在设计汽车起重机的液压系统时,需要考虑以下关键要素:3.1 力量需求:根据起重机的负载需求和工作环境,确定所需的力量和承载能力。
这将决定液压系统的工作压力和流量。
3.2 系统稳定性:起重机需要具有稳定的运动和控制能力,以确保安全和高效的工作。
液压系统的稳定性取决于系统中的液压阀和液压缸的设计。
3.3 控制灵活性:液压系统应该具有灵活的控制性能,能够满足不同工作条件下的要求。
这意味着液压系统需要具备多种控制模式和控制阀,以实现精确的运动控制。
3.4 节能性:优化液压系统的设计,以减少能源消耗和排放。
这可以通过使用低压系统、高效液压泵和智能控制等技术来实现。
4. 液压系统设计方案4.1 液压泵选择:根据起重机的力量需求和工作压力范围,选择适合的液压泵类型和规格。
常见的液压泵类型包括齿轮泵、柱塞泵和叶片泵等。
4.2 液压缸设计:根据起重机的负载需求和工作范围,设计合适的液压缸。
液压缸应具有足够的承载能力和精确的控制性能。
4.3 液压阀选择:选择适合的液压阀来实现控制需求。
常用的液压阀类型包括方向控制阀、流量控制阀和压力控制阀等。
4.4 控制系统设计:设计一个灵活和精确的控制系统来实现起重机的运动控制。
控制系统可以采用手动操作、自动控制或远程控制等方式。
4.5 液压管路设计:设计合适的液压管路,以确保液压系统的稳定性和可靠性。
管路应具有足够的强度和耐压能力。
25吨位起重机伸缩机构液压系统设计解析

一、25吨汽车起重机伸缩臂架的设计箱型吊臂连接尺寸的确定包含下列的内容:1)吊臂根部铰点位置的确定;2)吊臂各节尺寸的确定;3)变幅油缸铰点的确定。
1、吊臂根部铰点位置的确定基本臂工作长度l0和吊臂最大工作长度l max的确定:由图2.1可知,设l w为工作长度,则有图2.1 三铰点有关尺寸图l w=(H+b)−ℎ−(e0−e1)cosθsinθ式中:H—基本臂的起升高度,H=10.2m。
b—吊钩滑轮组最短距离,取b=1.5m。
外露空间a大一些,得出l i′′=l i+1′′+(c−a)。
此次设计共有4节臂,其最后一节的搭接长度为l5′′使其等于1/5的外伸长度,现在l max和l0已经得出,则吊臂的各节搭接长度和结构长度分别为,l4′′=0.2l l40=1.2ll3′′=0.2l+(c−a)l30=1.2l+(c−a)l2′′=0.2l+2(c−a)l20=1.2l+2(c−a)l10=1.2l+3(c−a)各节臂长度尺寸的验算计算的基本臂工作长度l0必须满足下面的式子,所计算的各节臂的长度值才能满足需要,l0=l10+a(k−1)≥1.2l+(k−1)c不等式左边为10.95m,右边为10.95m,长度满足要求。
最终求得l0=10.95m,l max=34.95m。
以上所用尺寸如下图所示图2.2 结构尺寸图3、变幅液压缸铰点的确定变幅液压缸的铰点如图3.1所示。
变幅液压缸根部铰点(O1)的位置,一般使其落在回转支撑装置的滚道上,从而改变了平台的受力情况。
采用双作用液压缸,其铰点离回转中心的距离f取决于双缸间的距离B,可通过下式算得:图3.1 主臂铰点位置图f=√(D2)2−(B2)2D—起重机底盘直径,D=2m。
B—吊臂宽度,由于回转支撑装置D和吊臂宽度B都与起重能力有关,一般取D=(2.1~2.4)B,这里取D=2.3B。
铰点O在求得ℎ0和e时已经确定即ℎ0=0.84m,e=2.35m,所以认定铰点O已经确定。
汽车起重机支腿液压系统设计

汽车起重机支腿液压系统设计引言汽车起重机是一种能够进行货物起升、搬运的重型机械设备。
为了确保其安全运行和稳定性,起重机上配备了支腿系统,用于支撑整个机身,使机身保持平衡和稳定。
支腿液压系统是起重机支腿的重要组成部分,本文将介绍汽车起重机支腿液压系统的设计。
液压系统工作原理液压系统采用液体的流动来传递信号和能量,主要由液压泵、液压缸、液压阀和液压油箱等组成。
在汽车起重机支腿液压系统中,液压泵通过驱动液压油流动,产生压力,将能量传递给液压缸,从而实现支腿的伸缩和支撑。
液压系统设计要点1.液压泵选择为了满足起重机支腿液压系统的工作需求,需要选择合适的液压泵。
液压泵的选择应根据液压系统的工作流量和工作压力来确定。
工作流量与液压缸的活塞面积和速度相关,工作压力与液压系统的负荷和阻力相关。
2.液压缸设计液压缸是起重机支腿液压系统的核心部件,主要用于驱动支腿的伸缩和支撑。
液压缸的设计应考虑到起重机的用途和工作条件。
液压缸的活塞直径和行程决定了液压缸的工作力和位移,需要根据起重机的负荷和高度来选择合适的液压缸。
3.液压阀选择液压阀是液压系统中的控制元件,主要用于调节液压系统的压力和流量,实现液压缸的伸缩和支撑等功能。
液压阀的选择应根据液压系统的需求来确定,常见的液压阀有溢流阀、比例阀和换向阀等。
4.液压油选用液压油是液压系统中的工作介质,负责传递能量和冷却液压系统。
液压油的选用应考虑到起重机的工作环境和温度,一般应选择具有良好的抗氧化性、抗磨性和粘温性的液压油。
5.液压系统的安全措施为了确保起重机支腿液压系统的安全运行,需要在设计中考虑相应的安全措施。
例如,在液压系统中加装过载保护装置,当超负荷时能够自动停止液压泵的运行,避免对起重机和人员的伤害。
此外,还需要在液压系统中设置液压缸行程限位开关,防止液压缸过度伸缩或缩回,影响起重机的工作效果和安全性。
总结汽车起重机支腿液压系统是重要的功能性系统,能够实现起重机的支撑和平衡。
25吨位起重机伸缩机构液压系统设计说明

25吨位起重机伸缩机构液压系统设计说明设计说明:25吨起重机伸缩机构液压系统一、系统需求分析根据25吨起重机的要求,其伸缩机构需要能够稳定可靠地实现起重机整体的伸缩操作。
因此需要设计一个液压系统,满足以下要求:1.传动功率大:能够承受25吨重物的伸缩操作,需要具备足够的工作压力和流量来传递高功率。
2.稳定可靠:液压系统需要具备稳定可靠的性能,能够在长时间工作中保持压力和流量的稳定。
3.速度控制:需要有控制装置来调节伸缩速度,使其能够根据实际需要实现快速、慢速或中速伸缩。
4.具备安全保护:系统需要具备过载保护、液压缸行程限位以及紧急停机装置等安全保护功能。
5.维护方便:设计需要考虑系统的布局合理性,便于维护和检修。
二、系统设计方案根据以上需求分析,设计的液压系统方案如下:1.液压泵和液压马达:选择适合的液压泵和液压马达,根据起重机的工作要求,确定泵的排量和转速以及马达的扭矩和转速,保证足够的工作压力和流量。
2.液压控制阀:选用符合起重机伸缩机构要求的液压控制阀,能够实现伸缩的快速、慢速和中速调节,同时具备压力和流量稳定的能力。
3.液压缸:选用具备足够承载力和行程的液压缸,能够实现起重机的伸缩操作。
需要具备行程限位和缓冲装置,保证伸缩过程的稳定可靠性。
4.液压储气罐和滤油器:设置液压储气罐用于储存液压系统的过剩液体和气体,保持系统的稳定压力。
同时安装滤油器来过滤液体中的杂质,提高系统的工作效率和寿命。
5.安全保护:设置过载保护阀,当系统受到过载时能够及时减少压力,保护系统的安全。
同时设置液压缸行程限位开关,当液压缸达到极限位置时能够自动停止工作,避免超过承载能力。
还应设置紧急停机按钮,当遇到紧急情况时能够快速停止起重机的伸缩操作。
6.维护方便:设计合理的管路布局,保证液压系统的布局紧凑,方便维护和检修。
并设有液压油温度和压力监测仪器,实时监测和掌握系统的工作状态。
三、液压系统的工作原理液压系统的工作原理是通过液压泵将液体压力传递给液压缸,从而推动起重机的伸缩机构实现伸缩操作。
25吨位起重机支腿机构液压系统设计
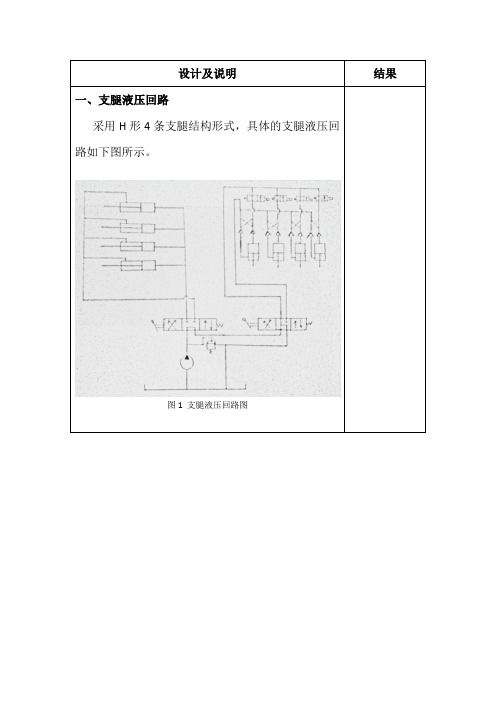
4、开锁压力 的确定
5、控制活塞直径 的确定
—起重机不吊重时的支腿反力(N)
—垂直支腿液压缸大腔面积,
6、验算开锁的必要条件是否满足
—支腿回路溢流阀的调定压力,为12MPa
经验算满足开锁的必要条件。
16.6mm
取为12mm
设支腿液压回路工作压力为p=12MPa。
2、支腿液压回路流量的确定
设泵流量即为支腿液压回路流量。
p=12MPa
五、垂直支腿液压缸基本参数的确定
1、垂直支腿液压缸内径D的计算
F—垂直液压缸工作载荷(N)
P—支腿油路工作压力(pa)
求出液压缸内径D之后,根据工程机械用液压缸内径系列相关标准取标准值。
2、活塞杆直径d的计算
—起重机吊重时垂直液压缸最大闭锁力
—材料的许用应力,
求出活塞杆直径d之后,根据工程机械用液压缸内径系列相关标准取标准值。
3、计算垂直液压缸速比
4、闭锁压力的计算
最大闭锁压力
5、垂直支腿液压缸行程的确定
设垂直支腿液压缸行程为 450mm。
89.479mm
取为90mm
取为40mm
六、水平支腿液压缸基本参数的确定
1、水平支腿液压缸内径D的计算
F—水平液压缸工作载荷(N)
P—支腿油路工作压力(pa)
求出液压缸内径D之后,根据工程机械用液压缸内径系列相关标准取标准值。
2、活塞杆直径d的计算
F—水平液压缸工作载荷(N)
—材料的许用应力,
求出活塞杆直径d之后,根据工程机械用液压缸内径系列相关标准取标准值。
3、水平支腿液压缸行程的确定
按三点支承计算支腿反力,假设吊臂位置在离起重机纵轴线(X轴) 角处,如下图所示。
QAY25全地面起重机液压系统优化设计
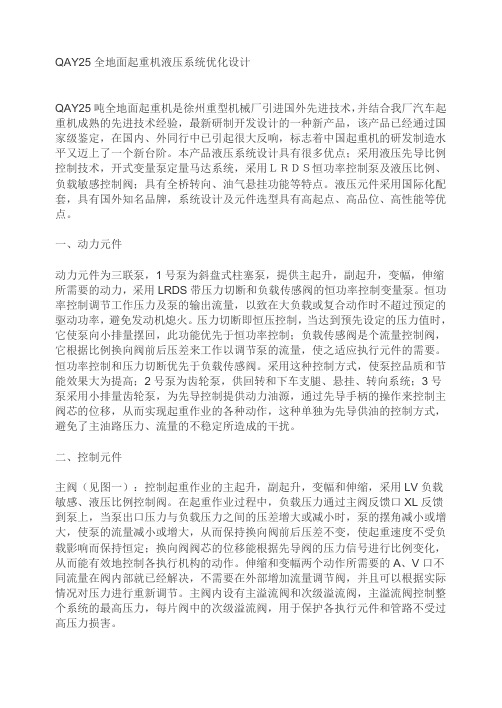
QAY25全地面起重机液压系统优化设计QAY25吨全地面起重机是徐州重型机械厂引进国外先进技术,并结合我厂汽车起重机成熟的先进技术经验,最新研制开发设计的一种新产品,该产品已经通过国家级鉴定,在国内、外同行中已引起很大反响,标志着中国起重机的研发制造水平又迈上了一个新台阶。
本产品液压系统设计具有很多优点;采用液压先导比例控制技术,开式变量泵定量马达系统,采用LRDS恒功率控制泵及液压比例、负载敏感控制阀;具有全桥转向、油气悬挂功能等特点。
液压元件采用国际化配套,具有国外知名品牌,系统设计及元件选型具有高起点、高品位、高性能等优点。
一、动力元件动力元件为三联泵,1号泵为斜盘式柱塞泵,提供主起升,副起升,变幅,伸缩所需要的动力,采用LRDS带压力切断和负载传感阀的恒功率控制变量泵。
恒功率控制调节工作压力及泵的输出流量,以致在大负载或复合动作时不超过预定的驱动功率,避免发动机熄火。
压力切断即恒压控制,当达到预先设定的压力值时,它使泵向小排量摆回,此功能优先于恒功率控制;负载传感阀是个流量控制阀,它根据比例换向阀前后压差来工作以调节泵的流量,使之适应执行元件的需要。
恒功率控制和压力切断优先于负载传感阀。
采用这种控制方式,使泵控品质和节能效果大为提高;2号泵为齿轮泵,供回转和下车支腿、悬挂、转向系统;3号泵采用小排量齿轮泵,为先导控制提供动力油源,通过先导手柄的操作来控制主阀芯的位移,从而实现起重作业的各种动作,这种单独为先导供油的控制方式,避免了主油路压力、流量的不稳定所造成的干扰。
二、控制元件主阀(见图一):控制起重作业的主起升,副起升,变幅和伸缩,采用LV负载敏感、液压比例控制阀。
在起重作业过程中,负载压力通过主阀反馈口XL反馈到泵上,当泵出口压力与负载压力之间的压差增大或减小时,泵的摆角减小或增大,使泵的流量减小或增大,从而保持换向阀前后压差不变,使起重速度不受负载影响而保持恒定;换向阀阀芯的位移能根据先导阀的压力信号进行比例变化,从而能有效地控制各执行机构的动作。
25吨通用门式起重机械机构设计说明书
目录引言 ............................................................ - 5 - 第1章 小车主起升机构计算 ...................................... - 8 -1.1 确定传动方案,选择滑轮组和吊钩组 ........................ - 8 -1.2 选择钢丝绳 .............................................. - 8 -1.3 确定卷筒尺寸,转速及滑轮直径 ............................. - 8 -1.4 计算起升静功率 ......................................... - 10 -1.5 初选电动机 ............................................. - 11 -1.6 选用减速器 ............................................. - 11 -1.7 电动机过载验算和发热验算 ............................... - 11 -1.8 选择制动器 ............................................. - 12 -1.9 选择联轴器 ............................................. - 13 -1.10 验算起动时间 .......................................... - 13 -1.11 验算制动时间 .......................................... - 14 -1.12高速轴计算 ............................................. - 15 -1.12.1疲劳计算 ......................................... - 15 -1.12.2静强度计算 ....................................... - 16 - 第二章 小车副起升机构计算 ..................................... - 17 -2.1 确定传动方案,选择滑轮组和吊钩组 ........................ - 17 -2.2 选择钢丝绳 ............................................. - 17 -2.3 确定卷筒尺寸并验算强度 ................................. - 18 -2.4 计算起升静功率 ......................................... - 19 -2.5 初选电动机 ............................................. - 20 -2.6 选用减速器 ............................................. - 20 -2.7 电动机过载验算和发热验算 ............................... - 21 -2.8 选择制动器 ............................................. - 21 -2.9 选择联轴器 ............................................. - 22 -2.10 验算起动时间 .......................................... - 22 -2.11 验算制动时间 .......................................... - 23 -2.12 高速轴计算 ............................................ - 24 -2.12.1疲劳计算: ....................................... - 24 -2.12.2静强度计算 ....................................... - 25 - 第三章 小车运行机构计算 ....................................... - 26 -3.1 确定机构传动方案 ....................................... - 26 -3.2 选择车轮与轨道并验算其强度 ............................. - 26 -3.2.1疲劳计算 .......................................... - 26 -3.2.2强度校核 .......................................... - 27 -3.3 运行阻力计算 ........................................... - 27 -3.4 选电动机 ............................................... - 28 -3.5验算电动机发热条件 ...................................... - 29 -3.6 选择减速器 ............................................. - 29 -3.7 验算运行速度和实际所需功率 ............................. - 29 -3.8 验算起动条件 ........................................... - 30 -3.9 按起动工况校核减速器功率 ............................... - 31 -3.10 验算起动不打滑条件 .................................... - 31 -3.11 选择制动器 ............................................ - 32 -3.12 选择联轴器 ............................................ - 33 -3.12.1机构高速轴上联轴器的计算扭矩 ..................... - 33 -3.12.2低速轴的计算扭矩 ................................. - 34 -3.13 验算低速浮动轴强度 .................................... - 34 -3.13.1疲劳计算 ......................................... - 34 -3.13.2 静强度计算 ....................................... - 35 -3.14 小车安全装置计算 .................................... - 35 -3.14.1 小车缓冲器 ....................................... - 35 -3.14.2 缓冲行程 ......................................... - 35 -3.14.3 缓冲能量 ......................................... - 35 -3.14.4 最大缓冲力 ....................................... - 36 -3.14.5 橡胶缓冲器的主要尺寸 橡胶断面积A ................ - 36 -3.14.6 缓冲器的额定缓冲行程,额定缓冲容量和极限缓冲力: .. - 36 -3.14.7 实际的缓冲行程,最大缓冲力和最大减速度 ........... - 37 - 第四章 大车运行机构的设计计算 ................................. - 38 -4.1车轮与轨道的选择 ........................................ - 38 -4.2 运行阻力计算: ......................................... - 39 -4.2.1 摩擦阻力的计算: ................................... - 39 -4.2.2 坡度阻力的计算: .................................. - 39 -4.2.3 风阻力的计算: .................................... - 39 -4.2.4 运行总阻力: ...................................... - 40 -4.3 电动机的选择 ........................................... - 40 -4.4 选择减速器 ............................................. - 41 -4.5 选择连轴器 ............................................. - 41 -4.6 电动机的验算 ........................................... - 42 -4.6.1 电动机的过载能力验算 .............................. - 42 -4.6.2电动机的发热验算 .................................. - 42 -4.6.3 启动时间的验算 .................................... - 43 -4.7减速器的验算 ............................................ - 44 -4.8制动器的选择 ............................................ - 45 -4.9起动和制动打滑验算 ...................................... - 46 -4.9.1起动时期不打滑验算 ................................ - 46 -4.9.2 制动不打滑验算 .................................... - 47 - 设计心得 ....................................................... - 48 - 致谢 ........................................................... - 49 -32/5吨通用门式起重机设计摘 要:次设计的为通用A型双梁门式起重机,我主要负责设计门式起重机的小车及大车运行机构。
汽车起重机的液压系统设计
汽车起重机的液压系统设计1.液压系统的基本组成液压泵负责将液压油从油箱中吸出,通过压力油路输送至执行元件,实现起重机的各种功能。
液压泵的选择应根据起重机的动力需求和工作压力来确定。
执行元件主要包括液压缸和液压马达,用于转化液压能为机械能。
液压缸负责推动伸缩臂的伸缩和旋转平台的旋转,液压马达则用于提供旋转力矩。
控制元件主要包括液控阀、压力阀、流量阀等,用于控制液压系统的流量、压力和方向。
液控阀用于控制执行元件的运动方向,压力阀用于控制系统的工作压力,流量阀用于调节系统的流量。
2.系统设计考虑的主要因素(1)起重机的工作负荷和工作范围:根据起重机的工作负荷确定液压系统的工作压力和流量,根据起重机的工作范围确定液压缸和液压马达的尺寸。
(2)系统的平稳性和安全性:起重机的运行要求平稳性高,液压系统设计应考虑减少振动和冲击的因素,采用减压阀和缓冲装置等来保证系统的稳定性。
同时,系统设计应考虑到安全性,通过设置安全装置来保护起重机在紧急情况下的安全运行。
(3)系统的能效:液压系统的工作效率对于起重机的能耗和功率需求有着重要影响。
设计时应合理选择液压泵和马达的类型和规格,以提高系统的能效。
(4)系统的维护和保养:液压系统的维护和保养是确保系统长期稳定运行的关键。
设计时应考虑到易于维护和保养的因素,如设备的布局合理化、易于更换和维修的部件等。
3.系统设计步骤(1)确定起重机的工作要求和技术指标,包括工作负荷、工作范围、速度等。
(2)根据需求计算液压系统的工作压力、流量和功率等参数。
(3)选择适合的液压泵、液压缸和液压马达等执行元件,并计算其尺寸。
(4)选择合适的液控阀、压力阀、流量阀等控制元件,并设计其控制电路。
(5)设计液压系统的油路,包括油箱容积、油管路的布置和连接方式等。
(6)制定液压系统的维护保养计划,包括定期更换液压油、清洗油路、检查和更换部件等。
总之,汽车起重机的液压系统设计需要全面考虑起重机的工作要求和技术指标,并根据液压原理和技术规范来选择和设计各个组成部分,以实现系统的高效、平稳和安全运行。
25K-1徐工汽车起重机技术参数
QY25K-Ⅰ汽车起重机技术规格伸缩臂汽车式起重机型号:QY25K-Ⅰ;最大额定起重量:25t;一、技术介绍1、底盘部分徐工设计、制造,全头驾驶室,3桥底盘,驱动/转向:6×4×2。
1.1、车架徐工设计、制造,优化结构设计,防扭转箱型结构,高强度钢材。
支腿箱体位于1桥和2桥之间以及车架后端。
具有前后牵引挂钩。
1.2、底盘发动机制造商:上海柴油机股份有限公司;型号:SC8DK280Q3(东风牌);型式:直列六缸、水冷却、蜗轮增压、电控高压共轨、压燃式柴油发动机;环保性:符合欧洲Ⅲ标准燃料箱容量:约300L1.3、动力传动系统1.3.1变速箱机械操纵,6档变速箱,控制后桥驱动。
1.3.2车桥高强度承载桥,维护方便。
第一桥:单胎,转向但不驱动;第二桥:双胎,驱动但不转向。
一级主减速加轮边减速;第三桥:双胎,驱动但不转向。
一级主减速加轮边减速。
1.3.3驱动轴驱动轴均采用端面齿连接,优化动力传输,传递扭矩大。
维护简便,方便拆卸和安装。
1.4、全桥悬挂前悬挂:纵置钢板弹簧式,筒式减震器;后悬架:双轴平衡、纵置板簧式,板簧与推力杆导向。
1.5、转向机械式转向机构,带有液压助力。
方向盘位置可调。
1.6、轮胎斜交轮胎,适用于重型汽车,通用性强。
标配1个备胎。
1.7、制动行车制动:脚踏板操纵的双回路气压制动。
第一回路作用于一轴车轮上,第二回路作用于二、三轴车轮上;驻车制动:放气制动,作用于后面两根轴上,通过各轴上的弹簧储能气室起作用;辅助制动:发动机排气制动。
1.8、底盘驾驶室新型豪华全宽驾驶室,配CD音响,可调式座椅和方向盘,大视野后视镜,电控洗窗器,电子门窗升降器。
空调:标配暖风和单冷空调。
1.9、液压系统四联齿轮泵通过取力器联接至发动机,控制辅助转向、下车液压支腿。
1.10、液压支腿“H”型支腿,4点支撑,水平和垂直支腿全液压操纵,底盘两侧装有操纵手柄,操纵手柄旁装有水平仪和油门操纵开关。
QY25起重机臂架及其液压系统设计(机械CAD图纸)
摘要随着国家现代化建设的飞速发展,科学技术的不断进步,现代施工项目对汽车起重机的要求也越来越高,高、深、尖液压技术在汽车起重机上的应用也越来越广泛,汽车起重机液压系统展示了强大的发展趋势。
汽车起重机液压系统一般由起升、变幅、伸缩、回转、控制、支腿六个主回路组成。
为了使起重机能够满足高性能、高可靠性、操作更方便、舒适、安全的要求,以及使起重机能够向智能、高性能、灵活、适应性强、多功能、吊重量大、起升高度、幅度更大的大吨位方向发展方向发展,设计者不但要改进起重机的结构和提高材料的强度,更重要的是在这六个液压系统上下工夫。
本文主要讨论伸缩主回路及其液压系统的设计。
关键词:汽车起重机,伸缩机构,液压系统ABSTRACTWith the rapid development of the country's modernization, the improvement of science and technology, modern construction projects on the truck crane requirements are increasingly high, high, deep, sharp hydraulic technology application in automobile cranes, cranes and more extensive hydraulic system demonstrates strong development trend.Truck crane hydraulic system generally by hoisting, luffing, scalable and rotary, control, teams composed of main loop leg six. In order to make the crane can satisfy the high performance, high reliability, the operation more convenient, comfortable and safe requirements, and make crane to intelligence, high-performance, flexible, adaptable, multi-function, hang a big weight, lifting height, amplitude greaterlarge-tonnage direction development direction, designers not only to improve the structure and improve material crane of strength, more important is in these six hydraulic system fluctuate. This paper mainly discusses the main loop and telescopic hydraulic system design.Keywords:truck crane;telescopic institutions;hydraulic system目录1绪论 (6)1.1汽车起重机的概念 (6)1.2 汽车起重机的用途 (6)1.3我国汽车起重机发展状况 (6)1.5三一25吨汽车起重机介绍 (7)2 25吨汽车起重机臂架系统 (10)2.1 25吨汽车起重机臂架系统的组成 (10)2.2主起重臂结构 (10)2.3副起重臂 (13)2.4 伸缩机构 (13)2.5 臂端滑轮 (13)3臂架结构的设计和计算 (14)3.1臂架截面参数 (14)3.2吊臂工况计算 (15)3.2.1 伸缩臂载荷计算 (15)3.2.2 伸缩臂的临界力计算 (17)3.2.3伸缩臂的强度计算 (18)3.2.4伸缩臂整体稳定性计算 (20)4液压系统原理设计 (22)4.1 典型工况分析及对系统要求 (22)4.1.1伸缩机构的作业情况 (22)4.1.2副臂的作业情况 (22)4.1.3三个以上机构的组合作业情况 (22)4.1.4典型工况的确定 (22)4.1.5系统要求 (24)4.2 液压系统类型选择 (25)4.2.1 本机液压系统分析 (25)4.2.2 各机构动作组合、分配及控制 (26)4.3 各种执行元件的选择 (27)5 伸缩液压回路组成原理和性能分析 (29)5.1性能要求 (29)5.2主要元件 (30)5.3主要回路 (30)5.4功能实现和工作原理 (30)6 伸缩液压系统设计计算 (32)6.1伸缩机构主要参数 (32)6.2伸缩油缸的选择 (32)6.3 伸缩油路 (33)6.4 伸缩机构液压阀的选择 (34)6.4.1变幅伸缩多路阀 (34)6.4.2平衡阀 (35)6.5液压辅助元件选择 (35)6.5.1油路的通径 (35)6.5.2滤油器的选择 (35)7伸缩机构回路性能验算 (36)7.1伸缩回路功率选取 (36)7.2 伸缩回路容积效率 (36)7.3伸缩机构压力效率 (36)7.4伸缩回路性能验算 (36)7.5伸缩时间 (36)7.6伸缩速度 (37)8 起重机的使用要求及简单的故障分析与排除 (39)8.1 起重机作业时应注意的事项 (39)8.2作业前的准备 (40)8.3 溢流阀与液压泵的维修 (41)8.3.1 溢流阀的维修 (41)8.3.2 液压泵的修理 (43)8.3.3 油泵的修复 (44)9.4 液压缸自行回缩 (44)结束语 (48)致谢 (49)参考文献 (50)1绪论1.1汽车起重机的概念通常把装在通用或专用载重汽车底盘上的起重机称为汽车起重机。
- 1、下载文档前请自行甄别文档内容的完整性,平台不提供额外的编辑、内容补充、找答案等附加服务。
- 2、"仅部分预览"的文档,不可在线预览部分如存在完整性等问题,可反馈申请退款(可完整预览的文档不适用该条件!)。
- 3、如文档侵犯您的权益,请联系客服反馈,我们会尽快为您处理(人工客服工作时间:9:00-18:30)。
设计及说明结果一、25吨汽车起重机伸缩臂架的设计
箱型吊臂连接尺寸的确定包含下列的内容:1)吊臂根部铰点位
置的确定;2)吊臂各节尺寸的确定;3)变幅油缸铰点的确定。
1、吊臂根部铰点位置的确定
基本臂工作长度和吊臂最大工作长度的确定:
由图可知,设为工作长度,则有
图三铰点有关尺寸图
式中:H—基本臂的起升高度,。
b—吊钩滑轮组最短距离,取。
、—根部铰点和头部滑轮轴心离吊臂基本截面中心线的距离,并带有符号。
由于此项数值较小,所以计算时可以忽略不计。
—吊臂仰角,取。
h—根部铰接点离地距离,取。
吊臂根部离铰点的距离e
—最小工作幅度,取。
吊臂根部铰点离回转平面的高度
—回转支承装置的高度,
—起重机汽车底盘的高度,
主吊臂最大长度
—最长主臂起升高度,
a,r,b,h同上。
2、吊臂各节尺寸的确定
主吊臂的最长长度是由基本臂结构长度和外伸长度所组成。
、、—各节臂的伸缩长度,在设计中伸缩长度往往取同一数值,即。
外伸长度。
、、—为二、三、四节臂缩回后外漏部分的长度,在计算时取同一数值(a=)
若假设为臂头滑轮中心离基本臂端面的距离,则基本臂结构长度加上即为基本臂的工作长度。
所以有
从中可以求出
k—吊臂的节数。
—主臂最大长度,初取35m。
—主臂最小长度,初取11m。
通常搭接长度应该短些,以减轻吊臂重量。
但是,太短将搭接部分反力增大了,引起搭接部分吊臂的盖板或侧板局部失稳,同时,也使吊臂的间隙变形增大。
因此搭接部分要根据实际经验和优化设计而定,一般为伸缩臂外伸长度的1/4—1/5(吊臂较长者取后者,较短者取前者,同步伸缩者可取后者)。
从而搭接长度为
在第i节臂退回后,除外露部分长度a外,在前节(i-1)节臂中的长度加上伸出后仍在前节臂中的那部分搭接长度。
第i节臂插在前节臂内的长度为(),设第i节臂的结构长度为,则
各节伸缩臂插入前一节都留有一段距离c,这是结构的需要,在此距离内要设置伸缩油缸的铰支座和其他的结构构件,其大小视情况而定,在此次设计中选择c=。
因此前后两节臂有这样的关系,
从而得到
已知,,,从上式可知,后一节的搭接长度比前一节的搭接长度小一些,因为一般情况下结构空间c比外露空间a大一些,得出。
此次设计共有4节臂,其最后一节的搭接长度为使其等于1/5的外伸长度,现在和已经得出,则吊臂的各节搭接长度和结构长度分别为,
各节臂长度尺寸的验算
计算的基本臂工作长度必须满足下面的式子,所计算的各节臂的长度值才能满足需要,
不等式左边为,右边为,长度满足要求。
最终求得,。
以上所用尺寸如下图所示
图结构尺寸图
3、变幅液压缸铰点的确定
变幅液压缸的铰点如图所示。
变幅液压缸根部铰点()的
位置,一般使其落在回转支撑装置的滚道上,从而改变了平台的
受力情况。
采用双作用液压缸,其铰点离回转中心的距离f取决
于双缸间的距离B,可通过下式算得:
图主臂铰点位置图
e=
D—起重机底盘直径,D=2m。
B—吊臂宽度,由于回转支撑装置D和吊臂宽度B都与起重能力有关,一般取,这里取D=。
铰点O在求得和e时已经确定即,e=,所以认定铰点O已经确定。
因为铰点离滚道面的距离是构造所定,一般取。
在图中可以看出,只有在基本臂上固定的铰点尚未确定。
铰点的确定要满足下述条件,在变幅缸缩回时,吊臂位在行驶状态,液压缸长度为最短长度;而当全伸时吊臂位在最大仰角状态,液压缸长度达到最大长度。
在中,在中。
而角是OB和水平线的夹角,它可由下式求得:
式中:,e=,,。
在O和确定后,用三角公式求得的位置,
已知,,,并带入上述两式并消去、,可得的二次方程式:
式中:,
的值是根据实际情况而定,在设计中,大体是所设计的铰
点应位于基本臂工作长度的中点处,有利于起重机的受力分布,使支点能够达到最大的作用效果。
根据上几式得出:时,或,
时,或,
时,或,
在时,比较接近中点值,所以铰点位置确定为:时,或,在时,根部铰点的位置落在前方轨道上,
时,根部铰点落在后方轨道上。
根据上述计算,汽车起重机的铰点位置已经确定。
4、吊臂截面的选择及截面尺寸确定
吊臂截面上半部分采用矩形,下半部分采用外凸折板形最好。
参见徐工25吨汽车起重机主臂设计尺寸,确定基本尺寸为780 650。
其余各节臂尺寸,如下图所示。
图各节臂截面尺寸的确定
二、变幅机构液压回路设计
采用液压缸驱动刚性变幅机构,其液压回路和受力简图如下两图所示。
对臂转动铰点A取矩,,则变幅液压缸推力为
L—工作臂的长度;取
—铰点A到臂重心的距离;取
—铰点A到活塞杆和臂铰点的距离;取
h—起升钢丝绳到铰点A的垂线距离;取h=
—工作臂和水平线夹角(幅角);
—变幅缸的轴线和水平线夹角;
Q—工作负载,包括吊具重量(N);
G—臂架自重,包括伸缩机构的重量;
、—分别作用在负载上和臂架上的风负载;均设为零。
S—起升钢丝绳拉力;S=
假设当相关数据如上取值时得到变幅缸所需最大推力,并以此
作为计算马达排量和变幅缸的缸径的依据。
刚性变幅机构液压缸缸径D由下式确定:
p—变幅液压缸入口压力(Pa),取为20 MPa
—回油压力(Pa)
d —缸活塞杆直径。
令回油为0,则上式可简化为
液压泵输出流量可由下式确定:
取为350mm
—缸活塞缸伸出速度,取s。