球墨铸铁浇冒口系统设计的关键 (一)
铸件冒口设计的原则及方法

图 4 冒口放在两热节之间的工艺对比
放在最后凝固的部位和几何热节处,形成 的接触热节和冒口补缩液流通效应的影 响,会使冒口安放处铸件的凝固时间延长, 相应增加对冒口补缩时间的要求,同时也 对热节处的内在质量产生不利的影响。为 此,文献[4]提出了动态顺序凝固的概念。 动态顺序凝固是指冒口离开热节,放在近 热节处,利用冒口根处形成的接触热节和 冒口补缩液的流通效应,实现铸件各部分 朝向冒口的顺序凝固。其实质是使铸件的 几何热节与设置冒口形成的接触热节相分 离,并控制次热节处所形成的接触热节,使 其凝固模数比几何热节的大,比冒口的小, 将凝固顺序由薄壁→次热节→几何热节→ 几何热节处的接触热节→冒口,改变为薄 壁→几何热节→次热节处的接触热节→冒 口,既避免了接触热节处热量过分集中,又 利用接触热节的热效应,在冒口和几何热 节之间形成补缩通道,保证冒口对几何热 节的补缩。
采用模数法计算出的冒口体积,应该
用补缩液量法进行校核,即冒口体积 V 应 r
满足式(1)。
3.2 热节圆比例法
热节圆比例法是一种经验性方法。采
用作图法或几何公式计算出热节圆直径 T, 然后根据铸件不同截面形状确定例系数α的数值多来源于工程实
科技创新导报 Science and Technology Innovation Herald
101
科技创新导报 2008 NO.27 Science and Technology Innovation Herald
工 程 技 术
图 5 冒口直径与铸件厚度热节圆直径的 关系
使膨胀压力得以控制,避免铸型扩大,一般
铸件凝固过程中,冒口液面不断下降, 体积减少,散热表面积增加,冒口模数动态
变小;铸件获得补缩液体后热量增加,凝固
最新冒口系统设计

Mr=1.2Mc=2.3cm
查标准圆柱形暗冒口表:当Mr=2.38cm, 收缩 率为5%、每个暗冒口能补缩的最大铸件体积 为 4.1L ( 重 量 32kg ) 时 , 冒 口 的 尺 寸 为 ¢ 120mm×188mm(h) (h=1.5d) 。 可 见 设 计一个冒口已经足够。
冒口系统设计
一、冒口的作用
为了使铸件在凝固的最后阶段得到补缩,防 止缩孔、缩松、裂纹、变形等产生,则在铸件上 设置冒口。
冒口-储备足量的液态金属,又可排气、集 渣。铸造合金凝固时,均产生体积收缩,凝固后 均会形成孔洞-缩孔、缩松。
三、冒口的设计原则 (一)设置冒口的必要性
(二)、冒口位置选择原则
(2)冒口要能根据设计的要求提供足够的 金属来补偿铸件的液态收缩,凝固收缩以及 由于型腔扩大而增加的体积。而且要力求铸 件的成品率高。
(3)冒口和铸件受补缩部位之间,要保持 一定的温度梯度和凝固梯度,以保证补缩通 道畅通。
(五)校验方向性(顺序)凝固和多冒口的 综合效果
由于冒口的有无及其位置、大小等将直接 影响铸件的温度场,从而影响凝固的进行状 态。此外,在多冒口的情况下还有可能发生 相互间的干扰。因此需要校验是否不产生缺 陷。
3-3冒口的设计及计算
以铸钢件冒口设计为主,凡实行顺序凝 固的一切合金铸件均适用。 冒口的设计: 凝固时间原则:模数法 几何关系原则:缩管法
热节圆法
(一)模数法
模数:体积和散热表面积的比值称模数
M=V/A 其中:M - 模数(m);
V - 铸件体积(m3) A - 散热表面积(m2)
模数法:根据铸件凝固理论,铸件凝固时间决定于 它的体积和表面积的比值,即铸件的模数。M小的 铸件凝固时间短;M大的铸件凝固时间长,模数方 法计算冒口尺寸就是建立在模数的基础之上。
球墨铸铁的一关键环节--球化处理工艺(热加工行业论坛)

损严重、吸收率、低球化剂消耗量大劳动 环境差等缺点.多年来人们一直在利用盖包 法的优点进行球铁生产,同时也在不断地努 力克服工艺在使用中的不足之处: (1)包盖起吊困难,操作难度大;(2)在使用冲 天炉连续出铁时,铁液重量难以精确量化.
盖包法可以大大减少球化剂与空气中 氧的接触几率,从而可以减少镁的氧化烧 损,提高镁元素的吸收率,能有效提高和稳 定球化效果及球铁性能;减少球化剂的加 入量,降低生成本;减少球化时的闪光和烟 尘,降低对环境的污染.由冲入法改为加盖 法时,只需在冲入法球化包上添加一个包 盖,其它和产结构和原料基本不用做任何 调整,符合我国国情,容易在工厂推广.
另一种是利用镁蒸气 在铁液包中自建压力的方 法,球化处理时,通过钟罩 把纯镁加入密封铁液包下 部,镁在包内立即气化,迅 速产生大量的镁蒸气.此蒸 气通过铁液时,一部分被铁 液吸收,另一部分逸出并迅 速在包内上部间隙建立起 与铁液温度相应的饱和蒸 气压(一般0.6~0.8MPa).这 时镁就不再因沸腾汽化而 损失了.
提高时,含镁合金的熔点就会降低,这样包芯线 粉料层的“过程汽化层” 产生镁蒸汽的时间提 前,形成使钢带失效的镁蒸汽量的时间就会提前, 从而导致钢带失效的时间提前,因此,当包芯线 含镁合金的百分比提高时,包芯线喂入包底的喂 线速度就需要相应提高。 (4)包芯线芯剂中镁所处形态的影响:当其 它条件不变时,如果包芯线中的含镁材料由硅镁 合金颗粒变成纯镁颗粒与硅基合金颗粒的混合物, 虽然,包芯线在铁水中各层物料的温度分布没有 发生改变,但由于纯镁颗粒的熔点仅为650℃左 右,包芯线粉料层的“过程汽化层”达到纯镁颗 粒熔点的时间就会大幅度提前,一旦纯镁颗粒熔 化变为镁液,就会迅速向其周围的合金颗粒间隙 中渗透,合金颗粒层的导热能力就会迅速
球墨铸铁的凝固特性和铸件冒口的设置

球墨铸铁的凝固特性和铸件冒口的设置中国铸造协会李传栻一般说来,球墨铸铁件产生缩孔、缩松的倾向比灰铸铁件大得多,防止收缩缺陷往往是工艺设计中十分棘手的问题。
在这方面,从实际生产中总结出来的经验很不一致,各有自己的见解:有人认为应该遵循顺序凝固的原则,在最后凝固的部位放置大冒口,以补充铸件在凝固过程中产生的体积收缩;有人认为球墨铸铁件只需要采用小冒口,有时不用冒口也能生产出健全的铸件。
要在确保铸件质量的条件下最大限度地提高工艺出品率,仅仅依靠控制铸铁的化学成分是不够的,必须在了解球墨铸铁凝固特性的基础上,切实控制铸铁熔炼、球化处理、孕育处理和浇注作业的全过程,而且要有效地控制铸型的刚度。
一、球墨铸铁的凝固特性实际生产中采用的球墨铸铁,大多数都接近共晶成分。
厚壁铸件采用亚共晶成分,薄壁铸件采用过共晶成分,但偏离共晶成分都不远。
共晶成分、过共晶成分的球墨铸铁,共晶凝固时都是先自液相中析出小石墨球。
即使是亚共晶成分的球墨铸铁,由于球化处理和孕育处理后铁液的过冷度增大,也会在远高于平衡共晶转变温度的温度下先析出小石墨球。
第一批小石墨球在1300℃甚至更高的温度下就已形成。
在此后的凝固过程中,随着温度的降低,首批小石墨球有的长大,有的再次溶入铁液,同时也会有新的石墨球析出。
石墨球的析出和长大是在一个很宽的温度范围内进行的。
石墨球长大时,其周围的铁液中碳含量降低,就会在石墨球的周围形成包围石墨球的奥氏体外壳。
奥氏体外壳形成的时间与铸件在铸型中的冷却速率有关:冷却速率高,铁液中的碳来不及扩散均匀,形成奥氏体外壳就较早;冷却速率低,有利于铁液中的碳扩散均匀,奥氏体外壳的形成就较晚。
奥氏体外壳形成以前,石墨球直接与碳含量高的铁液直接接触,铁液中的碳易于向石墨球扩散,使石墨球长大。
奥氏体外壳形成后,铁液中的碳向石墨球的扩散受阻,石墨球的长大速度急剧下降。
由于自铁液中析出石墨时释放的结晶潜热多,约3600 J/g,自铁液中析出奥氏体时释放的结晶潜热少,约200 J/g,在石墨球周围形成奥氏体外壳、石墨球的长大受阻,就会使结晶潜热的释放显著减缓。
球墨铸铁件冒口设计

2.控制压力冒口(又称释压冒口)
特点:利用部分共晶膨胀量来补偿铸件的凝固收缩 浇注结束,冒口补给铸件的冒口以释放“压力”
应用合理的冒口颈尺寸或一定的暗冒口容积控制回 填程度使铸件内建立适中的内压来克服凝固收缩, 从而获得既无缩孔、缩松又能避免胀大变形的铸件
M颈M冒 (㎝)
图4-40 M冒和M件的关系图 1—冶金质量差 2—冶金质量好
图4-41 需要补缩金属液量和铸件模数的关系 VT—设置冒口部位铸件或热节体积 VC—铸件需补缩体积
(2)冒口的补缩距离 指由凝固部位向冒口
输送回填铁液的距离 与铁水的冶金质量和
铸件的模数密切相关
图4-42 铁液输送距离和冶金质量及铸件模数的关系 1—冶金质量好 2—冶金质量中等 3—冶金质量很差
口体积,只有这部分金属液才能对铸件起补缩作用
冒口有效体积依铸件液态 收缩体积而定,一般比铸件 所需补缩的铁液量大
共晶成分的铸铁,冒口有 效体积取铸件体积的5%
碳当量低的铸件,冒口有 效体积取铸件体积的6%
图4-36 铸铁的ε—t浇曲线 ε—液态体收缩率 t浇—浇注温度
1—CE=4.3% 2—CE=3.6%
冒口颈模数M颈的确定:
M颈t浇 t浇 1111550cl0M件(cm )
式中 M颈 ——冒口颈模数(cm) M件——设置冒口部位的铸件模数(cm) t浇——浇注温度(℃) c ——铁液比热容,c与铁液温度有关,在 1150~1350℃范围内,c为835~963 J/(kg·℃) l ——铸铁结晶潜热为(193~247)×103J/kg
实用冒口的工艺出品率高,铸件质量好,更实用
原理:利用冒口来补缩铸件的液态收缩,而当液态收缩
冒口有效体积依铸件液态收缩体积而定,一般比铸件所需补缩的铁液量大
冒口系统设计

冒口系统设计一﹑冒口设计1. 冒口设计的基本原则1)冒口的凝固时间应大于或等于铸件(被补缩部分)的凝固时间。
2)冒口应有足够大的体积,以保证有足够的金属液补充铸件的液态收缩和凝固收缩,补缩浇注后型腔扩大的体积。
3)在铸件整个凝固的过程中,冒口与被补缩部位之间的补缩通道应该畅通,即使扩张角始终向着冒口。
对于结晶温度间隔较宽、易于产生分散性缩松的合金铸件,还需要注意将冒口与浇注系统、冷铁、工艺补贴等配合使用,使铸件在较大的温度梯度下,自远离冒口的末端区逐渐向着冒口方向实现明显的顺序凝固2. 冒口设计的基本内容1)冒口的种类和形状(1)冒口的种类⎧⎧⎧⎪⎪⎪⎨⎪⎪⎪⎪⎪⎨⎩⎪⎪⎪⎧⎪⎪⎨⎪⎪⎩⎩⎪⎧⎧⎪⎪⎪⎪⎨⎪⎪⎪⎪⎪⎨⎩⎪⎪⎪⎧⎪⎪⎪⎪⎪⎪⎪⎨⎨⎪⎪⎪⎪⎪⎪⎩⎪⎪⎪⎪⎪⎪⎪⎪⎪⎪⎪⎩⎩顶冒口依位置分侧冒口贴边冒口普通冒口明冒口依顶部覆盖分暗冒口大气压力冒口依加压方式分压缩空气冒口通用冒口(传统)发气压力冒口保温冒口发热冒口特种冒口依加热方式分加氧冒口电弧加热冒口,煤气加热冒口易割冒口直接实用冒口(浇注系统当铸铁件的实用冒口(均衡凝固)⎧⎪⎪⎪⎪⎪⎪⎪⎪⎪⎪⎪⎪⎪⎪⎨⎪⎪⎪⎪⎪⎪⎪⎪⎪⎪⎪⎧⎪⎪⎨⎪⎪⎪⎩⎩冒口)控制压力冒口冒口无补缩 图1 冒口分类(2)冒口的形状常用的冒口有球形、圆柱形、长方体形、腰圆柱形等。
对于具体铸件,冒口形状的选择主要应考虑以下几方面:a)球形 b)球顶圆柱形 c)圆柱形 d)腰圆柱形(明) e)腰圆柱形(暗)图2 常用的冒口形状①冒口的补缩效果: 冒口的形状不同,补缩效果也不同,常用冒口模数(M)的大小来评定冒口的补缩效果(M=冒口体积/冒口散热面积),在冒口体积相同的情况下,球形冒口的散热面积最小,模数最大,凝固时间最长,补缩效果最好,其它形状冒口的补缩效果,依次为圆柱形,长方体形等。
②铸件被补缩部位的结构情祝: 冒口形状的选泽还要考虑铸件被补缩部位的结构形状和造型工艺是否方便。
球墨铸铁件常见缺陷的分析与对策(1)
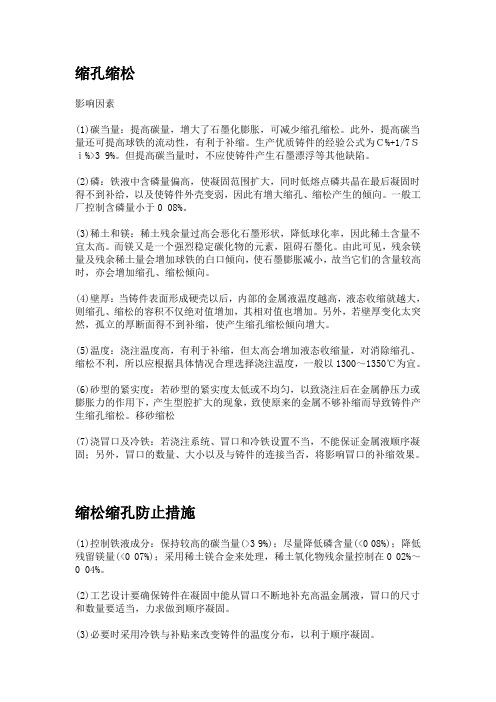
缩孔缩松影响因素(1)碳当量:提高碳量,增大了石墨化膨胀,可减少缩孔缩松。
此外,提高碳当量还可提高球铁的流动性,有利于补缩。
生产优质铸件的经验公式为C%+1/7Si%>3 9%。
但提高碳当量时,不应使铸件产生石墨漂浮等其他缺陷。
(2)磷:铁液中含磷量偏高,使凝固范围扩大,同时低熔点磷共晶在最后凝固时得不到补给,以及使铸件外壳变弱,因此有增大缩孔、缩松产生的倾向。
一般工厂控制含磷量小于0 08%。
(3)稀土和镁:稀土残余量过高会恶化石墨形状,降低球化率,因此稀土含量不宜太高。
而镁又是一个强烈稳定碳化物的元素,阻碍石墨化。
由此可见,残余镁量及残余稀土量会增加球铁的白口倾向,使石墨膨胀减小,故当它们的含量较高时,亦会增加缩孔、缩松倾向。
(4)壁厚:当铸件表面形成硬壳以后,内部的金属液温度越高,液态收缩就越大,则缩孔、缩松的容积不仅绝对值增加,其相对值也增加。
另外,若壁厚变化太突然,孤立的厚断面得不到补缩,使产生缩孔缩松倾向增大。
(5)温度:浇注温度高,有利于补缩,但太高会增加液态收缩量,对消除缩孔、缩松不利,所以应根据具体情况合理选择浇注温度,一般以1300~1350℃为宜。
(6)砂型的紧实度:若砂型的紧实度太低或不均匀,以致浇注后在金属静压力或膨胀力的作用下,产生型腔扩大的现象,致使原来的金属不够补缩而导致铸件产生缩孔缩松。
移砂缩松(7)浇冒口及冷铁:若浇注系统、冒口和冷铁设置不当,不能保证金属液顺序凝固;另外,冒口的数量、大小以及与铸件的连接当否,将影响冒口的补缩效果。
缩松缩孔防止措施(1)控制铁液成分:保持较高的碳当量(>3 9%);尽量降低磷含量(<0 08%);降低残留镁量(<0 07%);采用稀土镁合金来处理,稀土氧化物残余量控制在0 02%~0 04%。
(2)工艺设计要确保铸件在凝固中能从冒口不断地补充高温金属液,冒口的尺寸和数量要适当,力求做到顺序凝固。
(3)必要时采用冷铁与补贴来改变铸件的温度分布,以利于顺序凝固。
球墨铸铁浇口和冒口

球墨铸铁浇口和冒口的应用罗通 全国铸造委员会消失模与V法铸造技术委员会浇注系统的基本功能跟冒口系统是根本的区别。
前者的目的是让铁水充满型腔,而同时把渣撇掉。
冒口系统的目的是提供无缺陷的铸件没改缺陷可能是由于石墨铸铁进行凝固与冷却时期产生的体积变化而引起的。
1.在有些时候,浇注系统能引起冒口的作用。
(即能补偿冷却期间的体积变化)。
2.内浇道位置影响着刚浇完的铸件内部的温度分布。
温度分布又影响着凝固与冷却的型式。
3.假如设计要求冒口保持液体的时间尽可能的长,那么最好是把铁水引入冒口并经过冒口(热冒口)充满整个型腔。
(1).冒口和铸件的连接处能更长时间的保持液态。
(2).冒口得到的最热的铁水,这样的设计通常是限于侧冒口,另一方面,中大型铸件上的顶冒口也由于热流水输送到顶部,而把较冷的铁水输送到底部(3). 内浇道总的横截面面积通常是控制浇注期间的温度损失。
4.冒口也受到影响,因为浇注完了的液体温度比起浇注温度本身更为重要地影响到冒口系统的设置。
冒口位置影响浇口设计,尤其是在通过冒口(热的)引入铁水时更是这样。
消失模最常见的错误时省去内浇道而直接把铁水引入铸件或冒口,即使将横浇道通到铸件或冒口处的横截面面积减少,应该强烈反对这样的实践。
推荐两种做的理由是在横浇道中的铁水要直流,而且在经过内浇道时也要这样流,由于弯曲而引起紊流,这就很容易造成一些初期的含渣较多的铁水进入内浇道。
横浇道末端下部设置一个凹坑,此方案是很好的经验,当没有足够的地方供横浇道延长时尤为优越.内浇道之间的距离越大,(放在横浇道下的内浇道)以及横浇道顶部越高, 则该系统越安全,因渣子的比重比铁水小并倾向于上浮, 在冲型初期的紊流.115内浇道应是薄而宽, 厚宽比为1;4,为防止浇注期间内浇道凝固, 要使拨模斜度尽可小.横浇道应是高而窄. 高与宽比约为2;1.两个薄且窄的内浇道比既厚又宽的内浇道为好,内浇道长度可按布置要求设计, 它们输送是无渣的铁水,当然形状弯曲的布置也是允许的, 设计内浇道长度等于其宽度.当浇注系统被充满直浇道中的渣粒向下移动而进入铸件内的唯一可能性,措施是直浇道与第一个内浇道之间的距离尽可能大,(但这不是靠减少最后一个内浇道到横浇道末端的长度来实现) 假如位置是足够, 该距离等于横浇道的延长距离。
- 1、下载文档前请自行甄别文档内容的完整性,平台不提供额外的编辑、内容补充、找答案等附加服务。
- 2、"仅部分预览"的文档,不可在线预览部分如存在完整性等问题,可反馈申请退款(可完整预览的文档不适用该条件!)。
- 3、如文档侵犯您的权益,请联系客服反馈,我们会尽快为您处理(人工客服工作时间:9:00-18:30)。
球磨铸铁浇冒口设计的关键
第一部分
浇流道系统设计
1.0浇流道系统设计
1.1要求
快速浇铸:使充型过程中温度损失最小
使冶金学性能衰减最小
使氧化物最少
清洁浇铸:避免浇铸过程中产生炉渣(浮渣)
设计的经济性:使铸件产量最大化
1.2关键组成:
所示的所有组成部分要求炉渣缺陷最小化
1.3规划
考虑设计基本设计:优化对铸件的空间利用;冒口设计方法的选择;设置分型面以最小化对模芯的需求;铸件设置在上模中;平稳填充;简单对称的设计系统;同一铸件使用相同的浇冒口;可能的话,在多个铸件上使用一个冒口;在分型面上给浇冒口系统留下足够的空间;
具体设计如下:
1.4阻流阀的作用
定义:阻流阀是浇道系统中一块横截面积,它决定充型时间
有两个正确的位置设置阻流阀,因此有两个基本的浇道系统:
在简单的浇注系统中,1)阻流阀位于流道和浇口的连接处。
2)阻流阀位于直浇道与横浇道的连接处。
1.5 选择浇流系统类型
在浇口-横浇道系统中,铸件分别被一个或多个阻流阀或浇口阻挡。
在直浇道-横浇道系统中,很可能几个铸件共用一个阻流阀。
使用直浇道-横浇道系统在一个模具里生产大量小型件,这是不切实际的对每个铸件分别设置阻流阀(阻流阀尺寸非常小),极大的依赖于模具技术及浇注温度
大部分情况下是使用浇口-横浇道系统
浇口-横浇道系统与直浇道-横浇道系统特点的结合形成混合系统。
这通常用在要求运输铁水到复杂的铸件型腔的流道系统中。
1.6摩擦
并非直浇道顶部所有铁水的潜能都可以转换为铸造型腔中的机械能
随着铁水与型腔内壁的撞击和铁水之间的撞击,一些潜能损失在摩擦上
由于摩擦造成的损失,延长了模型填充时间,必须考虑何时计算阻流阀截面积和浇铸时间。
选择fr,摩擦损失因子,作为能量损失的估计值
对于薄壁平板:fr—0.2
对于厚重立方体:fr---0.8
1.7浇铸时间
尽可能快的符合人们的能力及生产例程
推荐的浇注时间:
非常近似的指导,铸件质量+冒口质量
1.8阻流阀的横截面积
对总的浇铸质量选择最快的实际浇铸时间(t,sec.)
选择合适的fr值
确定总的浇铸体积/阻气阀(V)
V是所有铸件及冒口,特定阻流阀的下游之和
体积=质量/密度
液态铸铁,密度=0.25磅/立方英尺或0.007KG/cm3
Determine effective ferrostatic head in sprue (H.)
确定铸件在上模中的高度(b.)
根据Torricelli,铁水在阻流阀的流速
当铸件完全处在下模,
当铸件完全位于上模,
当铸件位于上模和下模中,
可以从下面的图谱中,选择合适的Ac
图谱数据基于平均上模高度(依铸造不同而变化)。
大部分情况下,这种方法引人的误差微乎其微。
模具填充过程应该计时,如果时间填充时间非常不同于选择的填充时间,那么阻流阀应该根据以上方程充型设计。
1.9 阻流阀结构
浇口-流道系统:总的阻流阀横截面积是各个浇口横截面积之和
总的阻流阀=Ac=A1+A2+ +An
根据铸件质量选择Ac。
多个阻流阀(A1,A2),各个阻流阀横截面积的选择是根据:(总铸件+冒口质量)/阻流阀数目
单个浇口尺寸:使阻流阀尺寸=4a宽*厚4a2=A1=A2 因此,a,4a。