精密铸造铸件工艺与浇冒口系统设计
精密铸造铸件工艺与浇冒口系统设计
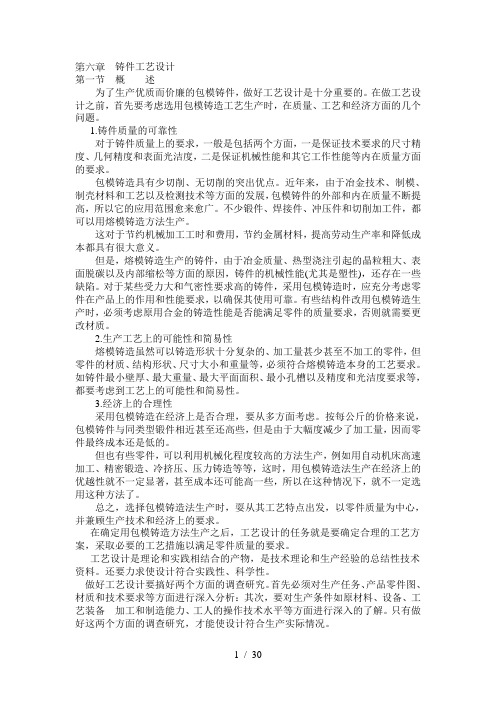
第六章铸件工艺设计第一节概述为了生产优质而价廉的包模铸件,做好工艺设计是十分重要的。
在做工艺设计之前,首先要考虑选用包模铸造工艺生产时,在质量、工艺和经济方面的几个问题。
1.铸件质量的可靠性对于铸件质量上的要求,一般是包括两个方面,一是保证技术要求的尺寸精度、几何精度和表面光洁度,二是保证机械性能和其它工作性能等内在质量方面的要求。
包模铸造具有少切削、无切削的突出优点。
近年来,由于冶金技术、制模、制壳材料和工艺以及检测技术等方面的发展,包模铸件的外部和内在质量不断提高,所以它的应用范围愈来愈广。
不少锻件、焊接件、冲压件和切削加工件,都可以用熔模铸造方法生产。
这对于节约机械加工工时和费用,节约金属材料,提高劳动生产率和降低成本都具有很大意义。
但是,熔模铸造生产的铸件,由于冶金质量、热型浇注引起的晶粒粗大、表面脱碳以及内部缩松等方面的原因,铸件的机械性能(尤其是塑性),还存在一些缺陷。
对于某些受力大和气密性要求高的铸件,采用包模铸造时,应充分考虑零件在产品上的作用和性能要求,以确保其使用可靠。
有些结构件改用包模铸造生产时,必须考虑原用合金的铸造性能是否能满足零件的质量要求,否则就需要更改材质。
2.生产工艺上的可能性和简易性熔模铸造虽然可以铸造形状十分复杂的、加工量甚少甚至不加工的零件,但零件的材质、结构形状、尺寸大小和重量等,必须符合熔模铸造本身的工艺要求。
如铸件最小壁厚、最大重量、最大平面面积、最小孔槽以及精度和光洁度要求等,都要考虑到工艺上的可能性和简易性。
3.经济上的合理性采用包模铸造在经济上是否合理,要从多方面考虑。
按每公斤的价格来说,包模铸件与同类型锻件相近甚至还高些,但是由于大幅度减少了加工量,因而零件最终成本还是低的。
但也有些零件,可以利用机械化程度较高的方法生产,例如用自动机床高速加工、精密锻造、冷挤压、压力铸造等等,这时,用包模铸造法生产在经济上的优越性就不一定显著,甚至成本还可能高一些,所以在这种情况下,就不一定选用这种方法了。
铝合金砂型铸造案例分析- 浇冒口系统设计

横浇道尺寸 内浇口尺寸
使用以上信息,我们就可以建议一模4件的 初始工艺设计方案。
为什么没有加次冒口2、3?
在初始设计中,我们将验证从主冒口浇注 产生的温度分布变化能否使所有的凝固顺 序都指向主冒口,而不用加次冒口。如果
不行的,再添加冒口或冷铁等。
接下来,对初始设计工艺进行模拟。使用 FLOWCast™模拟充型过程,使用
及最大出品率的冒口尺寸。
联系方式 天津富宇创想科技有限公司
公司网站:
冒口冒口2推荐直径推荐直径15英寸英寸x高高3英寸英寸冒口冒口3尺寸相同直径尺寸相同直径15英寸英寸x高高3英寸英寸接下来使用浇注系统设计向导接下来使用浇注系统设计向导gatingdesignwizard?确定最优浇注时间确定最优浇注时间直浇道横浇道及内浇口尺寸直浇道横浇道及内浇口尺寸最优浇注时间最优浇注时间直浇道形状直浇道形状浇口位置浇口位置浇注系统截面比浇注系统截面比直浇道直径直浇道直径横浇道尺寸横浇道尺寸内浇口尺寸内浇口尺寸使用以上信息我们就可以建议一模使用以上信息我们就可以建议一模4件的初始工艺设计方案
行分析,得到铸件模数*。根据模数就可以
知道铸件每部分的凝固顺序,并用来确定冒 口或浇口放置的最佳位置及给出冒口尺寸。
*注: 传统的模数定义为——体积:表面积,SOLIDCast使用的是热 模数,这比传统的方法要准确的多。
铸件上的模数分布
冒口设计向导(Riser Design Wizard)通 过分析铸件上的模数分布,给出推荐的冒
铸件上的缩松(弥散的缩松)分布
X-Ray View
结论
使用浇注系统设计向导和冒口设计向导, 我们可以很快的设计出铸件工艺方案。使 用FLOWCast和SOLIDCast可以快速验证
精密铸造工艺流程
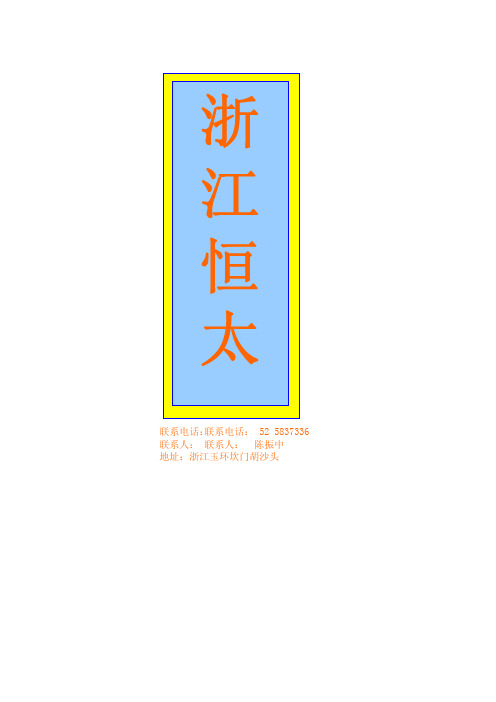
熔模铸件的形状一般都比较复杂,铸件上可铸出孔的最小直径可 达 0.5mm,铸件的最小壁厚为 0.3mm。在生产中可将一些原来由几个 零件组合而成的部件,通过改变零件的结构,设计成为整体零件而直 接由熔模铸造铸出,以节省加工工时和金属材料的消耗,使零件结构 更为合理。
熔模铸件的重量大多为零点几十牛(即几十克到几公斤),太重 的铸件用熔模铸造法生产较为麻烦,但目前生产大的熔模铸件的重量 已达 800 牛左右。
熔模铸造工艺过程较复杂,且不易控制,使用和消耗的材料较贵, 故它适用于生产形状复杂、精度要求高、或很难进行其它加工的小型 零件,如涡轮发动机的叶片等。
图 1 是熔模铸件的照片。熔模铸造的工艺过程见图 2。
图 1 熔模铸件照片
2 熔模的制造
熔模铸造生产的第一个工序就是制造熔模,熔模是用来形成耐火 型壳中型腔的模型,所以要获得尺寸精度和表面光洁度高的铸件,首 先熔模本身就应该具有高的尺寸精度和表面光洁度。此外熔模本身的 性能还应尽可能使随后的制型壳等工序简单易行。为得到上述高质量 要求的熔模,除了应有好的压型(压制熔模的模具)外,还必须选择 合适的制模材料(简称模料)和合理的制模工艺。
铸造工艺流程介绍

铸造生产的工艺流程铸造生产是一个复杂的多工序组合的工艺过程,它包括以下主要工序:1)生产工艺准备,根据要生产的零件图、生产批量和交货期限,制定生产工艺方案和工艺文件,绘制铸造工艺图;2)生产准备,包括准备熔化用材料、造型制芯用材料和模样、芯盒、砂箱等工艺装备;3)造型与制芯;4)熔化与浇注;5)落砂清理与铸件检验等主要工序。
成形原理铸造生产是将金属加热熔化,使其具有流动性,然后浇入到具有一定形状的铸型型腔中,在重力或外力(压力、离心力、电磁力等)的作用下充满型腔,冷却并凝固成铸件(或零件)的一种金属成形方法。
图1 铸造成形过程铸件一般作为毛坯经切削加工成为零件。
但也有许多铸件无需切削加工就能满足零件的设计精度和表面粗糙度要求,直接作为零件使用。
型砂的性能及组成1、型砂的性能型砂(含芯砂)的主要性能要求有强度、透气性、耐火度、退让性、流动性、紧实率和溃散性等。
2、型砂的组成型砂由原砂、粘接剂和附加物组成。
铸造用原砂要求含泥量少、颗粒均匀、形状为圆形和多角形的海砂、河砂或山砂等。
铸造用粘接剂有粘土(普通粘土和膨润土)、水玻璃砂、树脂、合脂油和植物油等,分别称为粘土砂,水玻璃砂、树脂砂、合脂油砂和植物油砂等。
为了进一步提高型(芯)砂的某些性能,往往要在型(芯)砂中加入一些附加物,如煤份、锯末、纸浆等。
型砂结构,如图2所示。
图2 型砂结构示意图工艺特点铸造是生产零件毛坯的主要方法之一,尤其对于有些脆性金属或合金材料(如各种铸铁件、有色合金铸件等)的零件毛坯,铸造几乎是唯一的加工方法。
与其它加工方法相比,铸造工艺具有以下特点:1)铸件可以不受金属材料、尺寸大小和重量的限制。
铸件材料可以是各种铸铁、铸钢、铝合金、铜合金、镁合金、钛合金、锌合金和各种特殊合金材料;铸件可以小至几克,大到数百吨;铸件壁厚可以从0.5毫米到1米左右;铸件长度可以从几毫米到十几米。
2)铸造可以生产各种形状复杂的毛坯,特别适用于生产具有复杂内腔的零件毛坯,如各种箱体、缸体、叶片、叶轮等。
镁合金熔模精密铸造技术研究现状
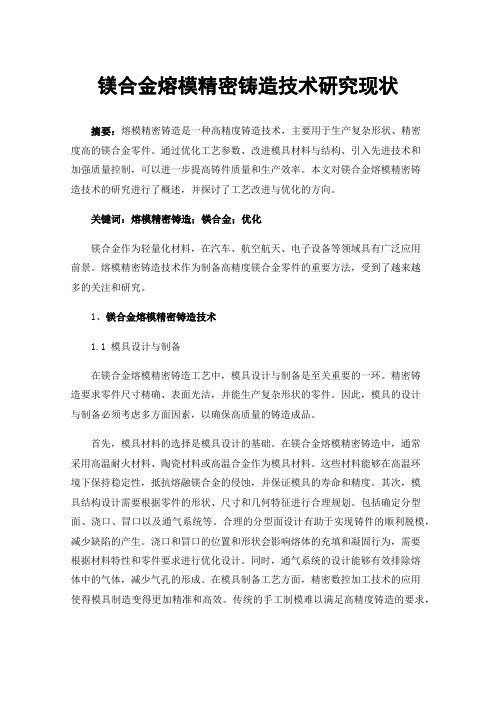
镁合金熔模精密铸造技术研究现状摘要:熔模精密铸造是一种高精度铸造技术,主要用于生产复杂形状、精密度高的镁合金零件。
通过优化工艺参数、改进模具材料与结构、引入先进技术和加强质量控制,可以进一步提高铸件质量和生产效率。
本文对镁合金熔模精密铸造技术的研究进行了概述,并探讨了工艺改进与优化的方向。
关键词:熔模精密铸造;镁合金;优化镁合金作为轻量化材料,在汽车、航空航天、电子设备等领域具有广泛应用前景。
熔模精密铸造技术作为制备高精度镁合金零件的重要方法,受到了越来越多的关注和研究。
1、镁合金熔模精密铸造技术1.1 模具设计与制备在镁合金熔模精密铸造工艺中,模具设计与制备是至关重要的一环。
精密铸造要求零件尺寸精确、表面光洁,并能生产复杂形状的零件。
因此,模具的设计与制备必须考虑多方面因素,以确保高质量的铸造成品。
首先,模具材料的选择是模具设计的基础。
在镁合金熔模精密铸造中,通常采用高温耐火材料、陶瓷材料或高温合金作为模具材料。
这些材料能够在高温环境下保持稳定性,抵抗熔融镁合金的侵蚀,并保证模具的寿命和精度。
其次,模具结构设计需要根据零件的形状、尺寸和几何特征进行合理规划。
包括确定分型面、浇口、冒口以及通气系统等。
合理的分型面设计有助于实现铸件的顺利脱模,减少缺陷的产生。
浇口和冒口的位置和形状会影响熔体的充填和凝固行为,需要根据材料特性和零件要求进行优化设计。
同时,通气系统的设计能够有效排除熔体中的气体,减少气孔的形成。
在模具制备工艺方面,精密数控加工技术的应用使得模具制造变得更加精准和高效。
传统的手工制模难以满足高精度铸造的要求,而数控加工可以实现复杂形状的精密加工,确保模具的尺寸和表面质量符合设计要求。
1.2 材料选用与准备材料选用与准备在镁合金熔模精密铸造工艺中是确保铸件性能和质量的关键步骤。
合理的材料选择和精心的准备过程对于获得高品质的镁合金铸件至关重要。
首先,针对不同应用和性能要求,需要仔细选择合适的镁合金材料。
铸造工艺流程介绍

铸造生产的工艺流程铸造生产是一个复杂的多工序组合的工艺过程,它包括以下主要工序:1)生产工艺准备,根据要生产的零件图、生产批量和交货期限,制定生产工艺方案和工艺文件,绘制铸造工艺图;2)生产准备,包括准备熔化用材料、造型制芯用材料和模样、芯盒、砂箱等工艺装备;3)造型与制芯;4)熔化与浇注;5)落砂清理与铸件检验等主要工序.成形原理铸造生产是将金属加热熔化,使其具有流动性,然后浇入到具有一定形状的铸型型腔中,在重力或外力(压力、离心力、电磁力等)的作用下充满型腔,冷却并凝固成铸件(或零件)的一种金属成形方法。
图1 铸造成形过程铸件一般作为毛坯经切削加工成为零件.但也有许多铸件无需切削加工就能满足零件的设计精度和表面粗糙度要求,直接作为零件使用。
型砂的性能及组成1、型砂的性能型砂(含芯砂)的主要性能要求有强度、透气性、耐火度、退让性、流动性、紧实率和溃散性等。
2、型砂的组成型砂由原砂、粘接剂和附加物组成。
铸造用原砂要求含泥量少、颗粒均匀、形状为圆形和多角形的海砂、河砂或山砂等。
铸造用粘接剂有粘土(普通粘土和膨润土)、水玻璃砂、树脂、合脂油和植物油等,分别称为粘土砂,水玻璃砂、树脂砂、合脂油砂和植物油砂等.为了进一步提高型(芯)砂的某些性能,往往要在型(芯)砂中加入一些附加物,如煤份、锯末、纸浆等。
型砂结构,如图2所示。
图2 型砂结构示意图工艺特点铸造是生产零件毛坯的主要方法之一,尤其对于有些脆性金属或合金材料(如各种铸铁件、有色合金铸件等)的零件毛坯,铸造几乎是唯一的加工方法。
与其它加工方法相比,铸造工艺具有以下特点: 1)铸件可以不受金属材料、尺寸大小和重量的限制.铸件材料可以是各种铸铁、铸钢、铝合金、铜合金、镁合金、钛合金、锌合金和各种特殊合金材料;铸件可以小至几克,大到数百吨;铸件壁厚可以从0.5毫米到1米左右;铸件长度可以从几毫米到十几米.2)铸造可以生产各种形状复杂的毛坯,特别适用于生产具有复杂内腔的零件毛坯,如各种箱体、缸体、叶片、叶轮等。
铸铁件浇冒口系统的设计与应用
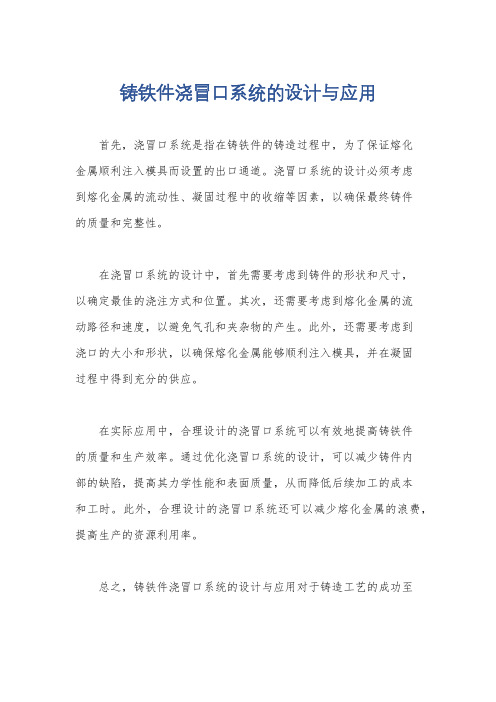
铸铁件浇冒口系统的设计与应用
首先,浇冒口系统是指在铸铁件的铸造过程中,为了保证熔化
金属顺利注入模具而设置的出口通道。
浇冒口系统的设计必须考虑
到熔化金属的流动性、凝固过程中的收缩等因素,以确保最终铸件
的质量和完整性。
在浇冒口系统的设计中,首先需要考虑到铸件的形状和尺寸,
以确定最佳的浇注方式和位置。
其次,还需要考虑到熔化金属的流
动路径和速度,以避免气孔和夹杂物的产生。
此外,还需要考虑到
浇口的大小和形状,以确保熔化金属能够顺利注入模具,并在凝固
过程中得到充分的供应。
在实际应用中,合理设计的浇冒口系统可以有效地提高铸铁件
的质量和生产效率。
通过优化浇冒口系统的设计,可以减少铸件内
部的缺陷,提高其力学性能和表面质量,从而降低后续加工的成本
和工时。
此外,合理设计的浇冒口系统还可以减少熔化金属的浪费,提高生产的资源利用率。
总之,铸铁件浇冒口系统的设计与应用对于铸造工艺的成功至
关重要。
通过科学合理的设计和精心的应用,可以有效地提高铸铁件的质量和生产效率,从而为工业生产带来更大的价值和效益。
熔模精密铸造实践报告总结(2篇)

第1篇一、引言熔模精密铸造是一种先进的铸造技术,具有精度高、表面光洁、机械性能好等优点,广泛应用于航空航天、汽车、医疗器械等领域。
本报告主要对熔模精密铸造的实践过程进行总结,分析存在的问题及改进措施,以期为今后类似项目的实施提供参考。
二、熔模精密铸造实践过程1. 原材料准备熔模精密铸造的原材料主要包括蜡、石英砂、粘土、水、耐火材料等。
在实践过程中,首先要对原材料进行筛选和加工,确保其质量符合要求。
2. 熔模制作熔模制作是熔模精密铸造的关键环节。
具体步骤如下:(1)蜡模制作:根据产品图纸,采用手工或机器加工方法制作蜡模,要求蜡模表面光滑、尺寸准确。
(2)蜡模组合:将多个蜡模组合成一个整体,以便后续进行熔模铸造。
(3)熔模组装:将蜡模组合体放入砂箱中,进行熔模组装,确保砂箱内的蜡模组合体与砂箱内壁之间形成良好的密封。
3. 熔模铸造熔模铸造主要包括以下步骤:(1)预热:将砂箱内的熔模预热至一定温度,以降低蜡模熔化时的收缩应力。
(2)熔化蜡模:将预热后的熔模放入熔化炉中,熔化蜡模。
(3)浇注:将熔化的金属液浇注到砂箱内的蜡模中,使金属液填充蜡模空腔。
(4)冷却凝固:待金属液凝固后,取出砂箱,去除砂模,得到铸件。
4. 铸件后处理铸件后处理主要包括以下步骤:(1)打磨:对铸件表面进行打磨,去除浇注系统和浇注冒口等。
(2)热处理:根据铸件材料性能要求,进行相应的热处理。
(3)检验:对铸件进行尺寸、形状、表面质量、机械性能等方面的检验。
三、存在问题及改进措施1. 问题一:蜡模精度不足原因分析:蜡模制作过程中,手工加工误差较大,导致蜡模精度不足。
改进措施:采用高精度加工设备,如数控机床等,提高蜡模加工精度。
2. 问题二:熔模铸造过程中出现缩孔、裂纹等缺陷原因分析:熔模铸造过程中,金属液冷却速度过快,导致缩孔、裂纹等缺陷。
改进措施:优化熔模设计,采用合理的浇注系统,降低冷却速度,提高铸件质量。
3. 问题三:铸件表面质量差原因分析:铸件表面质量受多种因素影响,如熔模表面质量、浇注温度、冷却速度等。
- 1、下载文档前请自行甄别文档内容的完整性,平台不提供额外的编辑、内容补充、找答案等附加服务。
- 2、"仅部分预览"的文档,不可在线预览部分如存在完整性等问题,可反馈申请退款(可完整预览的文档不适用该条件!)。
- 3、如文档侵犯您的权益,请联系客服反馈,我们会尽快为您处理(人工客服工作时间:9:00-18:30)。
第六章铸件工艺设计第一节概述为了生产优质而价廉的包模铸件,做好工艺设计是十分重要的。
在做工艺设计之前,首先要考虑选用包模铸造工艺生产时,在质量、工艺和经济方面的几个问题。
1. 铸件质量的可靠性对于铸件质量上的要求,一般是包括两个方面,一是保证技术要求的尺寸精度、几何精度和表面光洁度,二是保证机械性能和其它工作性能等内在质量方面的要求。
包模铸造具有少切削、无切削的突出优点。
近年来,由于冶金技术、制模、制壳材料和工艺以及检测技术等方面的发展,包模铸件的外部和内在质量不断提高,所以它的应用范围愈来愈广。
不少锻件、焊接件、冲压件和切削加工件,都可以用熔模铸造方法生产。
这对于节约机械加工工时和费用,节约金属材料,提高劳动生产率和降低成本都具有很大意义。
但是,熔模铸造生产的铸件,由于冶金质量、热型浇注引起的晶粒粗大、表面脱碳以及内部缩松等方面的原因,铸件的机械性能(尤其是塑性),还存在一些缺陷。
对于某些受力大和气密性要求高的铸件,采用包模铸造时,应充分考虑零件在产品上的作用和性能要求,以确保其使用可靠。
有些结构件改用包模铸造生产时,必须考虑原用合金的铸造性能是否能满足零件的质量要求,否则就需要更改材质。
2. 生产工艺上的可能性和简易性熔模铸造虽然可以铸造形状十分复杂的、加工量甚少甚至不加工的零件,但零件的材质、结构形状、尺寸大小和重量等,必须符合熔模铸造本身的工艺要求。
如铸件最小壁厚、最大重量、最大平面面积、最小孔槽以及精度和光洁度要求等,都要考虑到工艺上的可能性和简易性。
3. 经济上的合理性采用包模铸造在经济上是否合理,要从多方面考虑。
按每公斤的价格来说,包模铸件与同类型锻件相近甚至还高些,但是由于大幅度减少了加工量,因而零件最终成本还是低的。
但也有些零件,可以利用机械化程度较高的方法生产,例如用自动机床高速加工、精密锻造、冷挤压、压力铸造等等,这时,用包模铸造法生产在经济上的优越性就不一定显著,甚至成本还可能高一些,所以在这种情况下,就不一定选用这种方法了。
总之,选择包模铸造法生产时,耍从其工艺特点出发,以零件质量为中心,并兼顾生产技术和经济上的要求。
在确定用包模铸造方法生产之后,工艺设计的任务就是要确定合理的工艺方案,采取必要的工艺措施以满足零件质量的要求。
工艺设计是理论和实践相结合的产物,是技术理论和生产经验的总结性技术资料。
还要力求使设计符合实践性、科学性。
做好工艺设计要搞好两个方面的调查研究。
首先必须对生产任务、产品零件图、材质和技术要求等方面进行深入分析:其次,要对生产条件如原材料、设备、工艺装备加工和制造能力、工人的操作技术水平等方面进行深入的了解。
只有做好这两个方面的调查研究,才能使设计符合生产实际情况。
工艺设计的好坏也要从质量、工艺和经济这三方面去衡量。
一项良好的工艺 设计应当能在正常的生产条件下, 稳定铸件质量,简化生产工艺,效率高而成本 低。
熔模铸造工艺设计通常包括下列几项内容,(1).分析铸件结构工艺性,(2)确定工艺方案和工艺参数,(3)设计浇冒口系统,⑷绘 制工艺图或铸件图。
第二节铸件结构工艺性分析铸件结构工艺性对于零件质量,生产工艺的可能性和简易性以及生产成本等 影响很大。
结构工艺性不好的铸件,往往孕育着产生缺陷和废品的可能性, 也会 增加制造成本。
所以,做工艺设计时,首先要审查零件图,审查的目的有二:一 是审查零件结构设计是否符合包模铸造的生产特点,对于那些设计不合理的部分 进行修改。
第二个目的是根据已定的零件结构和技术要求, 采取相应措施以保证 质量。
根据熔模铸造生产特点,零件结构工艺性要考虑以下要求。
1)经济性 在精密铸造的生产中,其 蜡型是。
在包模铸造上,金属模的目的 是在在射蜡机中,利用压力将液态、糊 态或半固态的蜡挤射入金属模内,生 产蜡型或塑料型,这些型是用来生产陶 瓷模的,不论是实体模或型壳模。
所有的模型都是可逝性的。
在制模的关键性问题上,是如何将蜡型或塑料型从模具中 取出,以及如何将芯子从模型中取出等。
至于其它的制模问题,用于砂模铸造的图2铸件内角的重设计⑵在图1中,一个包模铸件因为内 部有一圆角,而且需要用两个抽芯,A 及B 两个芯子进出的方向如图1(a)所示,要想将有倒钩的芯子抽出而又不伤 损工件是根本不可能。
于是,重新设计工件,如图 1(b),将内圆角取消,以避开 这种芯子有倒钩无法抽出的困绕。
倘若要生产原设计有内圆角的工件,惟有舍弃 金属抽芯,而用成本较高的水溶性芯子,随 同蜡型一起自模中取出,再用酸蚀及水溶法 将芯子自蜡型中除去,如此可保持工件的内 圆角而又不会损伤蜡型。
图2系一个有弧形通道的工件,同样如 图2(a)的设计也无法用金属抽芯来制模, 改为图2(b)的设计,将内圆角改为尖角,可以用两支抽芯做出弧形通道的内孔 图3刀具余隙的再设计为了后继的加工,往往在工件设计时,一般为避免撞机的困绕,预先留有一 个让出刀具到位时的间隙,如图3(a)所示,但无法抽出金属芯子,若改为图3(b)图1铸件内角的重设计(1)原理同样适用于包模铸造彌11⑹改良拥I可大幅度提高生产效率及降的设计,就可以用金属抽芯直接做出 刀具余隙。
另外如图4 (a )之原始设计虽 然内孔通道很圆滑,但必须要用较昂 贵的水溶性芯子或陶瓷芯子,而且, 在铸造后,清除孔道中陶瓷材料非常 困难,若改为(b )的设计,可直接 由六个金属抽芯来射制蜡型,另在一个多出的孔洞则可在铸件完成后再设法塞上或焊死。
低成本。
2).现实性 精密铸造与其它的制造方法一样,有其一定的极限,因此,在铸 件精度的考虑上,应面对现实,设计可以达得到的标准,否则,良品率太低,就 丧失了用精密铸造降低生产成本,提高生产效率的目的了。
当铸件芯子部位因受炽热的金属围绕,内外部份的散热状况不一致,内部陶 瓷受高温而膨胀,但外部因有金属包覆又无法自由伸展, 陶瓷材料因而有强烈的 弯曲变形的应力,此时,外部热的不均匀内孔的长度in. 壁厚的公差in.v 2 ±).005 2〜4 ±).010 >4 ±).012分布,芯部自然向高温部分扭曲变形,便 使铸件的壁厚产生了不均匀的结果。
其变 化差异如下長度直徑Y. 晨小墜F Z in. in.—般的包橫簾鋼件 0.250 0.125 0.030 0,500 0.250 0.04001500.375 0.050 1.000 0.500 0.060 1.250 0.750 0.060 1,500 1-000 0.060 2.000 1.500 0.060 2.500 1.7500.060有孔空心包模铸造件根据可能的精度 其设计通则: 鑄胚真圖度 (HR), in.内輕A, in.0.092 to 0.250 0.251 to 0.500 0.501 to 1.000 mLOOO .0.012 0.0160,020 号加 03Q inJin图4内孔通道的再设计鑄胚A 内徑B 外徑 同心度in.in.(TIR)( H0.250 0550 0.008 0^00 1.000 0.010 0550 1.500 0.016 1.000 2.0000.020A diom0 250 0t8fi 0 1S80.500 0.260 0.250 0750 O.COO 0J12 1.000 0.63& 0J751.25Q 0,750 0438 0* 15* 1J500 075G 仇500 A 1$2.000 1000 OW 0- 15J2.500 LOGO 0.635OTF厂協小孔徑V 「我畫 鹽非聲金拔模推拔inY.in F I bni VR0A25 0.250 0.125 0,250 0.5Q0 1.000 2,0000.250 0.500 0,750 L000 0,500 0.500 2 500±0.004 0125 ±0.003 土0.005 0.250 ^0.004 土0.005 0 500 ^0.005 ±0*OQ5 0,750 ±0,005 =bQ,008 0 250 ±6005 ±0.010 0.250 ±0.008 *0.015 1500 ±0.010426666/6/3/1/1/1/1律111111Y. in.X*fT min0.250 15'±1'0.500 30"±1* 1.00045*X diam. in. Y, in.Z" a f0.250 0 500 15'士(T 30dO.&OO 0.750 30B±『30'0.250 0.500 00° ±ov<r 0.500 0.750 90° ±0* 45’ 0550"00乩更疗13€* ±(r wA* in*R* in. C ± IK.D, IB . E, in(lit 熾縮陷「L 二二士弋」-t¥raxapproi 此轴陷弋「° 70.500 L0000.250 0.750 0.315 ^0.004 0 750 L500 0.500 1.000 0.500 ±0006 1,000 2.000 0.750 1.500 0.750 ±0.00S L250 2.500 1.000 2.000 1.000 ^0.010L DEX diam *4 I*■*— B di a m—Adiam3)铸造性 a)壁薄的包模铸件包模铸造工艺几乎制造任何金属的复杂铸件,也可以在小零件的设计及生产 上,有助于达到轻薄短小的目的,获得最大的强度重量比值。
在设计最小壁厚时, 金属熔液的流动性是一个非常重要的考虑因素,因为它直接影响到金属液对模穴 充填的能力。
几乎同等重要的另一要素,是熔液在充填模穴时,金属液的浇注补 充距离,以及铸件表面积之大小,金属的凝固状况,固、液相线的差异度,都归 纳于铸造性中,尤其对薄壁铸件特别重要。
可铸出的最小壁厚与合金种类、浇注工艺 方法、以及铸件的轮廓尺寸等因素有关。
表2列举的是1、i n.长管件对各种金属包模铸件之 最小壁厚。
其实这些数值并不是真正的最小壁 厚,诚如前述,金属液的浇注过热温度、浇注 速率、壳模预热温度、铸件的形状及薄壁部分 的表面积等都会影响最小壁厚的尺寸,这个表 中之建议值为工业生产上的经验值。
在这个标 准下生产,良品率最好,亦即浇不足及微缩孔 的现象最少。
在Fig. 7的上图表显示一个在最小厚度与最大长度的相互关系,而下图表则显示在铸件有通孔或盲孔时, 孔径与孔深的关 系。