常用钢材热处理工艺守则
热处理工艺守则

热处理工艺守则1、主题内容和适用范围本规程规定了焊后热处理的条件,热处理方法和工艺规范。
本规程适用于压力容器产品及其零部件的焊后热处理。
2、引用标准下列标准如已修订,则按最新版本执行。
TSG R0004-2009 固定式压力容器安全技术监察规程(简称《固容规》)第4.6条。
GB/T30583-2014 承压设备焊后热处理规程NB/T47015-2011 压力容器焊接规程GB150.4 压力容器制造、检验和验收第8条3、进行热处理的条件3.1 压力容器焊后热处理除遵守本守则外,还应符合设计文件与合同的要求。
3.2 焊后热处理应在产品焊接工作全部结束并且经过检验合格后,在耐压试验前进行。
3.3 钢制压力容器的焊后热处理应遵守GB/T 30583的相应规定。
3.4 碳钢和低合金钢制焊件低于490℃的热作用,高合金钢制焊件低于315℃的热作用均不作为焊后热处理对待。
3.5 《固容规》引用标准要求和设计图样要求进行焊后热处理。
3.6 钢板冷成形受压元件,符合下列任意条件之一,且变形率超过表9-1的范围,应于成形后进行相应热处理恢复材料的性能。
a)盛装毒性为极度或高度危害介质的容器;b)图样注明有应力腐蚀的容器;c)对碳钢、低合金钢,成形前厚度大于16mm者;d)对碳钢、低合金钢,成形后减薄量大于10%者;e)对碳钢、低合金钢,材料要求做冲击试验者。
表 9-1 冷成形件变形率控制指标3.7 GB150.4第8.2.2条规定,容器及其受压元件符合下列条件之一者,应进行焊后热处理,焊后热处理应包括受压元件及其与非受压元件的连接焊缝。
(1)焊接接头厚度(即焊后热处理厚度,δPWHT)符合表9-2的规定者。
(2)图样注明有应力腐蚀的容器。
(3)用于盛装毒性为极度或高度危害介质的碳素钢、低合金钢制容器。
(4)相关标准或图样另有规定时。
3.8 对异种钢材之间的焊接接头,按热处理要求高者确定。
但温度不应超过两者中任一钢号的下相变点A c1。
热处理工艺守则

6、回火检查
检查项目及内容同淬火检查。
编制(日期)
会签(日期)
审定(日期)
热处理工艺曲线图
产品
型号
工艺曲线
备
注
490Q(DI)进排(QZ6)
正
火
+
回
火
云内4100QB-A进排(QZ6)
正
火
+
回
火
4JB1进排
正
火
+
回
火
编制(日期)
会签(日期)
审定(日期)
体化和均匀化,然后出炉,在自然通风的空气中冷却的工艺过程,
为改善材料组织,便于切削加工,为以后热处理作准备,以及消除铸
锻加工中生产的内应力,常用退火及正、熟悉工艺文件,了解材料性能。
1.2、检查设备、仪表是否正常。
1.3、炉温升到规定入炉温度。
1.4、不允许氧化脱碳的工件应用生铁屑或旧渗碳剂装箱保护并密封。
3、淬火操作
(1)、待沪温升到略高于加热温度20-30℃时,放入工件。工件与炉墙及电阻丝的距离,不得少于60mm。当温升淬火温度时开始计算保温时间并保持规定时间。
(2)、工件在炉内加热方式,以受热均匀,不得变形或变形最小为宜。
(3)、将保温后的工件,迅速淬入冷却液中。淬入时保持工件平稳垂直以减小变形,并上下移动避免软点。
(3)、零件淬火后、回火前的硬度值大于规定硬度值的上限
(4)、重要零件淬火后不允许有软点。若有硬功夫度达不到要求的,可返工重淬,但必须先退火或正火处理,以防炸裂。如工件变形过大、应先校正后重淬。
5、变形检查
零件变形量不大于加工余量的一半。
常用钢材热处理工艺参数
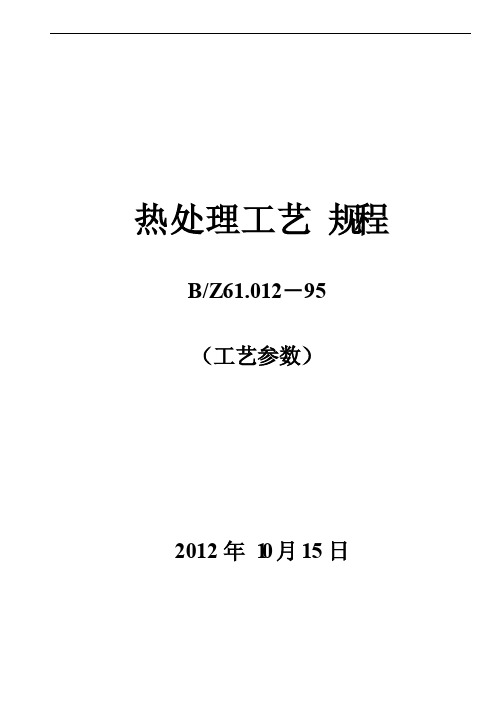
热处理工艺规程B/Z61.012-95(工艺参数)2012年10月15日目录1.主题内容与适用范围 (1)2.常用钢淬火、回火温度 (1)2.1要求综合性能的钢种 (1)2.2要求淬硬的钢种 (4)2.3要求渗碳的钢种 (6)2.4几点说明 (6)3.常用钢正火、回火及退火温度 (7)3.1要求综合性能的钢种 (7)3.2其它钢种 (8)3.3几点说明 (8)4.常用钢去应力温度 (10)5.各种热处理工序加热、冷却范围 (12)5.1淬火……………………………………………………………………………………………1 25.2 正火及退火 (14)5.3回火、时效及去应力 (15)5.4工艺规范的几点说明 (16)6.化学热处理工艺规范 (17)6.1氮化 (17)6.2渗碳 (20)7.锻模热处理工艺规范 (22)7.1锻模及胎模 (22)7.2切边模 (24)7.3锻模热处理注意事项 (25)8.有色金属热处理工艺规范 (26)8.1铝合金的热处理 (26)8.2铜及铜合金 (26)9.几种钢锻后防白点工艺规范 (27)9.1第Ⅰ组钢 (27)9.2第Ⅱ组钢 (28)热处理工艺规程(工艺参数)1.主题内容与适用范围本标准为“热处理工艺规程”(工艺参数),它主要以企业标准《金属材料技术条件》B/HJ-93年版所涉及的金属材料和技术要求为依据(不包括高温合金),并收集了我公司生产常用的工具、模具及工艺装备用的金属材料。
本标准适用于汽轮机、燃气轮机产品零件的热处理生产。
2.常用钢淬火、回火温度2.1 要求综合性能的钢种:表1注:①采用日本材料时,淬火温度为960~980℃,回火温度允许比表中温度高10~30℃。
②有效截面小于20mm者可采用空冷。
2.2要求淬硬的钢种(新HRC>30)表2注:①回火后油冷。
热处理工艺守则

一、热处理代号和材料标注方法(一)热处理代号1. 适用于结构钢和铸件代号:0—自然状态1—正火(或正火+回火)2—退火3—精锻+回火(如精锻或精辊叶片在精锻后只需高温回火)4—淬硬5—调质6—化学热处理(渗碳或氮化)7—除应力(包括活塞环定型处理)9—表面淬火或局部淬火2.适用铸造有色金属和奥氏体钢的代号:0—原始状态1—再结晶退火T—除应力退火T1—人工时效T4—淬火(固溶处理)T5—淬火和不完全时效T6—淬火和完全时效(固溶处理和完全时效到最高硬度)3.压力加工有色金属代号:0—原始状态M—退火C—淬火CZ—淬火和自然时效CS—淬火和人工时效(二)材料的标注方法:1.零件的材料或毛坯(包括铸锻件)如不作任何处理,也不作机械性能检查,则只标材料牌号(其热处理代号“0”在图纸上不标注)如:A3,20,35,ZQSn6-6-3。
2.零件的材料或毛坯在热处理后,不作硬度及机械性能检查者则只标注材料牌号和热处理代号:如:45-1,若有几种热处理,可用热处理代号按工艺路线顺序逐项填写:如:15CrMoA-1+7。
3.有些材料的技术条件,有几种检查组别,但强度等级只有一种或可按材料截面尺寸来决定强度等级,只注明材料牌号,热处理代号和检查组别:如:45-5(Ⅱ)35CrMoA-5(Ⅱ)4.有些材料的技术条件,有几种组别,在同一热处理状态中有不同的强度等级,则注明材料牌号、热处理代号强度等级和检查组别,不需要规定检查组别时,检查组别可省略。
25Cr2MoV A-5 25Cr2MoV A-5如:735-Ⅲ7355. 有些零件或者是比较重要或者是技术要求比较复杂,用上述标注方法不能说明全部要求者,则应注明标准号,在同一热处理状态中有不同的强度级别时,还应注明强度级别。
35CrMoA-5 35CrMoA-5如:Q/CCF M 3003-2003 590×Q/CCF M 3003-20036. 大锻件如叶轮、铸造轴、整体转子等的材料标注方法钢号锻件级别×标准编号7. 铸钢件:铸铁、铜件:材料牌号类别材料牌号标准号标准号8.铸铁件及有色金属等直接按上述方法标注可能引起误解时,热处理代号加上括号。
钢材热处理规范
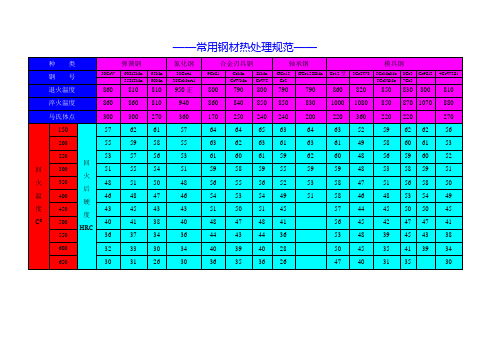
——常用钢材热处理规范——
说明:
1、碳钢一般采用水冷(5-10%食盐或碱水溶液)水温20-400C,合金钢一般采用油冷,油温不得高于1200C,等温淬火时可参考马氏体点选定工艺。
2、弹簧钢一般用中温回火,锰弹簧钢回火后要快冷。
3、氮化钢一般是先经调质处理后用500-6500C进行氮化处理用维氏硬度检验。
4、含铬、锰、镍等元素的调质钢经高温回火(约450-6000C)后须快冷,避免回火脆性。
为消除应力进行低温回火时,一般时间稍长些,采用高频淬火的工件,淬火温度比正常淬火加热温度约高1000C,其回火温度较一般回火约低200C。
5、表中Cr12型钢指一次硬化值,高速钢需经5600C三次回火。
钢制压力容器热处理通用工艺规程范文(二篇)
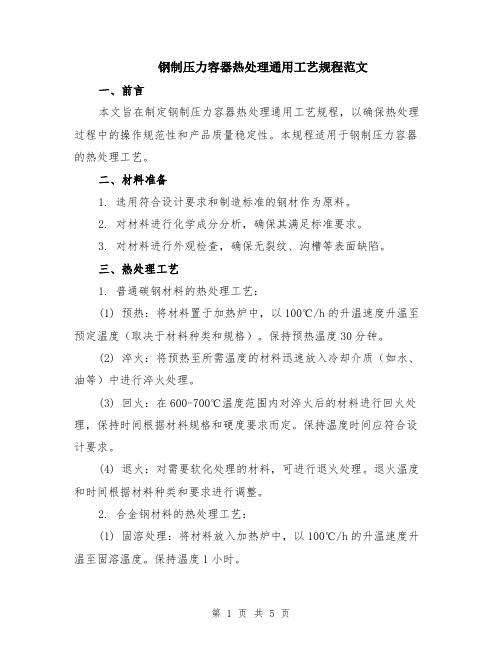
钢制压力容器热处理通用工艺规程范文一、前言本文旨在制定钢制压力容器热处理通用工艺规程,以确保热处理过程中的操作规范性和产品质量稳定性。
本规程适用于钢制压力容器的热处理工艺。
二、材料准备1. 选用符合设计要求和制造标准的钢材作为原料。
2. 对材料进行化学成分分析,确保其满足标准要求。
3. 对材料进行外观检查,确保无裂纹、沟槽等表面缺陷。
三、热处理工艺1. 普通碳钢材料的热处理工艺:(1) 预热:将材料置于加热炉中,以100℃/h的升温速度升温至预定温度(取决于材料种类和规格)。
保持预热温度30分钟。
(2) 淬火:将预热至所需温度的材料迅速放入冷却介质(如水、油等)中进行淬火处理。
(3) 回火:在600-700℃温度范围内对淬火后的材料进行回火处理,保持时间根据材料规格和硬度要求而定。
保持温度时间应符合设计要求。
(4) 退火:对需要软化处理的材料,可进行退火处理。
退火温度和时间根据材料种类和要求进行调整。
2. 合金钢材料的热处理工艺:(1) 固溶处理:将材料放入加热炉中,以100℃/h的升温速度升温至固溶温度。
保持温度1小时。
(2) 淬火:将固溶处理后的材料迅速放入冷却介质(如水、油等)中进行淬火处理。
(3) 回火:在450-600℃温度范围内对淬火后的材料进行回火处理,保持时间根据材料规格和硬度要求而定。
保持温度时间应符合设计要求。
四、操作注意事项1. 操作人员应经过相关培训,熟悉工艺要求和操作规程,严格按照规程进行操作。
2. 加热炉和冷却介质的温度应定期校准,确保温度准确性。
3. 热处理过程中,应定期检查冷却介质的质量,如有杂质应及时更换。
4. 淬火工艺中,应控制冷却介质的冷却速率,以避免材料出现裂纹等缺陷。
5. 温度控制器和计时器的准确性需要定期检查和校准。
五、质量控制1. 热处理后的材料应进行硬度测试和金相组织检查,确保满足标准要求。
2. 对热处理过程进行记录,包括材料种类、规格、加热炉温度、保温时间等重要参数。
常用金属材料热处理规范
常用金属材料热处理规范热处理是指通过加热、保温和冷却等工艺方法,使金属材料在固态下发生化学、物理或机械性能变化的过程。
热处理可以提高金属材料的硬度、强度、韧性、耐磨性等性能,从而满足具体的应用要求。
下面将介绍几种常用金属材料的热处理规范。
1.碳钢的退火处理碳钢是最常见的金属材料之一,经过退火处理后可以提高其塑性和韧性。
通常将碳钢加热至800-900°C,保温时间由材料厚度决定,通常是每25mm厚度增加1小时。
然后将材料冷却到室温,这样可以得到具有良好塑性和韧性的碳钢。
2.不锈钢的固溶处理不锈钢具有优良的耐腐蚀性能,但在焊接后会出现晶间腐蚀的问题。
固溶处理是为了解决晶间腐蚀问题而进行的热处理过程。
通常将不锈钢加热至1050-1150°C,保温时间取决于材料的厚度。
然后将材料迅速冷却到室温,这样可消除晶界处的过饱和元素,减少晶界的碳化物析出,从而提高不锈钢的耐腐蚀性能。
3.铸铁的正火处理铸铁是一种含碳量较高的金属材料,通过正火处理可以提高其硬度和强度。
通常将铸铁加热至850-950°C,保温时间由材料的厚度决定,通常是每25mm厚度增加1小时。
然后将材料冷却到室温。
正火处理可以改善铸铁的组织和性能,提高其机械性能。
4.铝合金的时效处理铝合金具有良好的强度和韧性,但在加工过程中可能会出现软化现象。
时效处理是为了提高铝合金的强度和稳定性的热处理过程。
通常将铝合金加热至150-200°C,保温时间由材料的合金组成决定,通常是几小时至几十小时。
然后将材料迅速冷却到室温。
以上是几种常用金属材料的热处理规范,不同的金属材料可能需要不同的热处理工艺。
在进行热处理时,需要严格控制加热温度、保温时间和冷却速度等参数,以保证热处理的效果。
同时,需要根据具体应用要求选择适当的热处理工艺,以获得期望的材料性能。
结构钢热处理工艺守则
XXX 有限公司企业标准Q/XXX004—2006 代替Q/XXX351—20041范围本标准规定了常用结构钢常规热处理的材料规格、设备与工具、准备工作、工艺规范、设备要求、操作方法与注意事项、常见缺陷及补救措施、安全注意事项等。
本标准适用于45、40Cr 、40CrMn 、65Mn 、GCr15>20CrMnTi 等结构钢的各种常规热处理(包括正火、退火、淬火、回火处理)操作。
不包括化学热处理、感应加热及火焰加热热处理等热处理方法。
2材料规格 1.1 化学成分常用结构钢的化学成分见表U表1常用结构钢的化学成分2. 2钢的临界点常用结构钢的临界点见表2。
表2常用结构钢的临界点单位:℃3设备与工具 3.1加热设备 3.1.1 45kW 台车式中温箱式炉,附温度自动控制记录仪表。
3.1.2 20kW 高温箱式炉,附温度自动控制记录仪表。
3.1.3 12kW 高温箱式炉,附温度自动控制仪表。
3.1.410kW 高温箱式炉,附温度自动控制仪表。
结构钢热处理工艺守则2006-08-08发布2006-08-28实施3.1.5 75kW埋入式电极盐浴炉,附温度自动控制记录仪表。
3.1.6 24kW井式回火炉,附温度自动控制记录仪表。
3.1.7 外热式硝盐炉,附温度自动控制仪表。
3.2冷却设备3. 2.1淬火水槽,2500rmιX1500πmX1500m∏o3. 2.2淬火油槽,10OOrrniX10OOrrmX10OOmmo3. 2.3外热式硝盐炉,附温度自动控制仪表。
3. 3清理设备3. 3.1碱水槽,1000mm×700mm×1000mmo3. 3.2热水槽,1400mm×10OOrnm×1000mm o3. 3.3清水槽,10OOmrn×700mm×10OOrnm o3. 3.4卧式离心研磨机。
3. 4辅助设备行车等。
3.5工具各种钳子、钩子、铁箱、吊具、淬火夹具等。
(工艺技术)热处理工艺守则
QB/HT-RQ-14-07 山东有限公司企业标准热处理通用工艺守则编制审核批准发放单位接收单位接收人:1.0总则1.1本守则规定了本公司常用碳钢、低合金钢、不锈钢钢材质制造的压力容器热处理通用操作工艺技术要求和质量验收标准。
1.2本守则适用于压力容器热处理工作,对于非压力容器的热处理工作也可参考。
1.3压力容器的热处理工作应遵照设计文件的规定,并应符合本守则的具体要求。
1.4压力容器的热处理工作应符合本守则外,还应符合国家劳动部颁发的《压力容器安全监察规程》及国家有关压力容器的相关规定。
2、术语与符号本守则所用术语、符号与《锅炉压力容器制造许可条件》、《压力容器安全技术监察规程》、GB150—1998、GB151—1999相同。
3、引用标准中华人民共和国质量技术监督局《锅炉压力容器制造许可条件》中华人民共和国质量技术监督局《锅炉压力容器制造监督管理制度》中华人民共和国劳动部《压力容器安全技术监察规程》GB150—1998 《钢制压力容器》GB151—1999 《钢制管壳式换热器》JB/T4709—2000 《压力容器焊接规程》QS/HT-2007-2 《压力容器制造质量手册》QG/GL-07 《压力容器制造程序文件及管理制度汇编》4.0通用要求容器及其受压部件,符合下列条件之一者,应进行消除应力的退火热处理:4.1A、B类焊缝处的钢板厚度δs符合下列条件者:a)碳素钢、07MnCrMoVR厚度δs大于32mm(如焊前预热100℃以上时,δs大于38mm);b)16MnR、16Mn厚度δs大于30mm(如焊前预热100℃以上时,δs大于34mm);c)15MnVR、15MnV厚度δs大于28mm(如焊前预热100℃以上时,δs大于32mm);d)任意厚度的15MnVNR、18MnMoNbR、13MnNiMoNbR、15CrMoR、14Cr1MoR、12Cr2Mo1R、20MnMo、20MnMoNb、15CrMo、12Cr1MoV、12Cr2Mo1和1Cr5Mo钢;e)焊接接头厚度大于16mm的碳素钢的低合金钢制低温压力容器或元件;f)对于钢材厚度δs不同的焊接接头,上述所指厚度按较薄者考虑。
焊后热处理工艺守则
1.主题内容与适用范围本守则对焊后热处理工艺文件的编制作了规定。
2.总则压力容器产品有其独立的规范及制造标准,使用本守则应与产品图样、标准、相关工艺文件同时使用。
3.工艺内容与技术要求压力容器制造中应严格执行GB150标准对焊后热处理的规定。
容器及其受压元件符合下列条件之一者应进行焊后热处理。
3.1A、B类焊接接头处的钢材名义厚度6s符合以下条件者1.1.1.1碳素钢、15MnNbR、07MnCrMoVRδs>32mm(如焊前预热IoOoC以上时,δs>38mm)1.1.1.2Q345R及16Mnδs>30mm(如焊前预热IoOoC以上时,δs>34mm)1.1.1.315MnVR及15MnVδs>28mm(如焊前预热IoOoC以上时,δs>32mm)1.1.1.4任意厚度的18MnMONbR、ISMnNiMoNbR、15CrMoR s14Cr1MoR x12Cr2Mo1R s20MnMo.20MnMoNb x15CrMo x1 2Cr1MoV s12Cr2Mo1和1Cr5Mo钢;1.1.1.5对予钢材厚度δs不同的焊接接头,上述厚度按薄者考虑,对予异种钢材相焊的焊接接头,按热处理严重者确定,但温度不应超过两者中任一钢号的下临界点Ac1o1.1.1.6除图样另有规定,奥化体不锈钢的焊接接头可不进行热处理。
3.1.2图样注明有应力腐蚀的容器,如盛装液化石油气,液氨等的容器3.1.3图样注明盛装毒性与报废或高度危害介质的容器3.1.4需要焊后进行消氢处理的容器,如焊后随即进行焊后热处理时,则可免做消氢处理4.焊后热处理方法4.1焊后热处理应优先采用在炉内加热的方法,其操作规范如下:4.1.1焊件进炉时,炉内温度≤400°C4.1.2焊件按功率升温至400。
C后加热区升温速度≤5000∕δs℃/h,且最高不得超过200o C∕h,最低可为50o C∕h o4.1.3升温时,加热区内任意500mm长度内的温差≤12(ΓC°4.1.4保温时间,温度见附表4.1.5保温时,加热区内任意500mm长度内的温差≤65°C°4.1.6升温及保温时,应控制加热区气氛,防止焊件表面过度氧化。
- 1、下载文档前请自行甄别文档内容的完整性,平台不提供额外的编辑、内容补充、找答案等附加服务。
- 2、"仅部分预览"的文档,不可在线预览部分如存在完整性等问题,可反馈申请退款(可完整预览的文档不适用该条件!)。
- 3、如文档侵犯您的权益,请联系客服反馈,我们会尽快为您处理(人工客服工作时间:9:00-18:30)。
1 适用围
本守则作为我公司常用钢材的各种热处理规及注意事项。
为一般件热处理的主要技术依据,对结构复杂和工艺上有特殊要求的零件和成批生产的零(部)件,则按专用工艺规程执行。
2 名词术语
2.1 正火
将钢材或钢件加热到临界点Ac3或Acm以上的适当温度,保持一定时间后在空气中冷却,得到珠光体类组织的热处理工艺。
2.2 退火
将钢材或钢件加热到适当温度,保持一定时间,随后缓慢冷却以获得接近平衡状态组织的热处理工艺。
2.3 淬火
将钢奥氏体化后以适当的冷却速度冷却,使工作在横截面全部或一定的围发生马氏体等不稳定组织结构转变的热处理工艺。
2.4 回火
将经过淬火的工件加热到临界点Ac1以下的适当温度保持一定时间,随后用符合要求的方法冷却,以获得所需要的组织和性能的热处理。
2.5 有效加热区
炉膛炉温均匀性符合热处理工艺要求的装料区域。
有效加热区的确定,按JB2251—78《电阻炉基本技术条件》中规定的有关试验方法进行。
2.6 冷却速度
在冷却过程中某一时间或者一定时间间隔工件表面或心部温度下降的变
化率。
2.7 热处理变形
工件热处理时所引起的形状尺寸偏差,垂直于长度向上的变形叫弯曲。
3 热处理加热设备
3.1 正火和退火所使用的加热设备必须满足下列要求。
3.1.1 在加热设备正常装炉的情况下,有效加热区的温度偏差应按下表所列的精度进行调节和控制。
3.1.2 燃料加热炉,其火焰尽量不直接接触工件,以免使工件局部过热。
当火焰直接与工件接触时,加热炉结构应使处理工件质量不显著损坏。
3.1.3 热浴加热炉,其热浴对工件不能有腐蚀及其它有害作用。
3.1.4 工件加热后在随炉冷却的过程中,应尽量保证各部位的冷却速度均匀一致。
3.2 淬火、回火加热设备
3.2.1 淬火、回火加热设备必须满足下列要求,有效加热区的温度按下表所列的精度进行调节和控制。
3.2.2 热浴槽中的热浴,对工件不能有腐蚀作用。
当采用盐浴炉加热时,应按盐浴脱氧制度对盐浴进行充分脱氧。
3.2.3 燃料加热炉,其火焰尽量不直接接触工件,以免工件过热。
当火焰直接与工件接触时,加热炉结构应使处理工件质量不受显著影响。
3.2.4 保护气氛加热炉应根据处理工艺要求能调节和控制炉气氛的成分。
3.2.5 真空炉应能根据处理目的对真空度和炉保持气氛的组成进行调节。
4 淬火冷却介质及设备
4.1 淬火冷却介质的使用温度及适用围应符合下表规定。
4.2 淬火冷却设备应保证工件表面各部位均匀冷却。
冷却槽中应配有冷却介质适当循环的搅拌装置或有同样效果的装置。
4.3 水槽中的水、水溶液或混合水溶液(包括新型水溶性淬火介质),不应含有过量的有害物质。
水溶液或混合水溶液的成分及浓度应适合淬火要求。
4.4 油槽中的油,应符合有关淬火油的标准。
4.5 淬火用热浴应具有符合淬火要求的冷却性能,不易老化,成分均匀,不含有过量的有害杂质,对工件不能有腐蚀及其它有害作用。
5 加热保温和冷却时间计算
5.1 零件加热保温时间按表一计算,回火保温时间按表二计算,密集堆放时应适当延长保温时间。
加热保温时间按式L=α×D计算。
表一
注:1、L ——加热保温时间(分),D ——零件有效厚度(mm ),α——加热系数(分/mm )
2、预热温度推荐500~600℃,预热时间可按回火加热时间计算。
高合金钢预热采用800~850℃。
表二
注:对于较小厚度(直径)的零件(<20或φ<20 mm =回火,保温时间(静止或循环空气炉<300℃)按30分+2分/ mm 计算。
5.2 零件的有效厚度计算 5.2.1 圆柱型零件按外径计算。
5.2.2 方型零件按厚度计算。
5.2.3 圆锥零件按厚度计算。
5.2.4 套筒零件,孔较小(径/外径≤1/5)按外径计算;孔较大(径/外径>1/5
)按壁厚计算。
5.2.5 球按0.75×球直径计算。
5.3 冷却时间按下表计算。
6 回火工艺规程
6.1 回火温度和回火时间由待回火的钢种、性能要求等确定。
对具有第一类回火脆性的钢种必须避开回火脆性区间。
对具有第二类回火脆性的钢种,在回火脆性温度区间加热后应采用油冷或水冷却。
6.2 经淬火后的工件应及时回火,油淬零件的间隔时间最长也不允许超过四小时。
6.3 淬火零件回火前应将残油、残渣等污物清理干净。
7 不锈钢件热处理
7.1 表面清理及要求
不锈钢构件、板材及管材等热处理前必须严格清除表面油污及油漆等脏物,不允许带有上述脏物的工件装炉热处理 7.2 对炉子气氛的要求
不锈钢的热处理通常应在电炉、盐炉或其它中性气氛设备中加热。
特殊情况允许在烧油炉加热,但应尽量控制炉子气氛保持中性或略带氧化性,同时热处理后零件表面必须进行金相检验,不允许有渗碳层出现。
出现渗碳层应按检查渗层厚度再加厚度10%的厚度,用机械抛光法清除干净(金相检查可以在随炉试片上进行)。
8 关于质量检验工作的规定
8.1 工件质量检验由质量管理部门负责执行。
在热处理工段(车间)或小组应设立检查站进行日常质量检查工作。
8.2 检验人员应按照工艺、图样、有关标准及规定的检验方法,进行首件检验、中间抽验、工序间检验和最后成品检验(具体方法及容由工艺或相应的技术文件规定)
,并监督工艺执行情况以防止废品产生。
8.3 质量检验容及要求 8.3.1 外观
热处理工件表面不能有裂纹及伤痕等缺陷。
8.3.2 硬度
8.3.2.1 退火、正火硬度围不应超过下表的规定。
2、单件硬度误差是指抽验单件时表面硬度值的不均匀度;同一批件硬度误差是指用同一批材料在同一热处理条件的工件表面硬度值的偏差围。
3、大型工件的硬度误差可按照图样规定执行。
此外,当工件硬度误差围超过上表的规定时,可与有关单位协调决定。
8.3.2.2 淬火、回火硬度围,根据不同类型的淬火回火件,不能超过表三、表四的规定。
表三
表四
注:单件表面硬度误差是指随机抽样单件时硬度值的不均匀度;同一批表面硬度误差是指用同一批材料在同一淬火、回火条件下工件表面硬度值的偏差围。
8.3.3 变形
工件变形应不影响其以后的机械加工和使用。
弯曲的允许值不应超过表五和表六的规定
表五
注:1类:指工件原样使用,或者进行磨削或部分磨削加工。
2类:指难以矫正的或随后进行切削加工或部分切削加工的工件。
表六
注:1、1类:成品原样使用,或者进行研磨或进行部分磨削。
2类:毛坯进行切削加工或部分切削加工。
2、零件变形经校直后,应进行回火处理。
回火温度应低于原回火温度10~
20℃。
8.3.4 质量试验方法:
8.3.4.1 硬度试验
硬度试验应按下列任一种方法进行。
GB230—83《金属洛氏硬度试验法》
GB231---63《金属布氏硬度试验法》
YB53---64《金属维氏硬度试验法》
8.3.4.2 金相组织检验:
YB27---77《钢的晶粒度测定法》
GB224---78《钢的脱碳测定法》
GB2849---80《钢铁零件渗氮层金相检验》。