ST官方电机控制套件用户手册
ST500II使用说明书-全套

ST500智能马达控制器的使用说明书(保护模式)(2003年)苏州智能配电自动化有限公司目录1、控制器的面板及端子功能说明 (1)2、控制器的功能配置一览表 (2)3、控制器应用接线图 (3)4、ST522显示模块 (3)5、控制器的使用说明 (4)5.1 控制器的主要功能 (5)5.2 控制器的参数测量功能 (5)5.3 控制器的报警查询功能 (5)5.4 控制器的故障查询功能 (6)5.5 控制器的维护管理功能 (6)5.6 控制器的输入输出状态查询功能 (7)5.7 控制器的各种保护定值设置功能 (7)5.8 控制器的系统参数设置功能 (16)1、控制器面板及端子标准配置复位”功能按钮或控制器断电一次则可清除热容量,允许立即起动电机。
注②:表中初始状态栏中的“常开”、“常闭”不是继电器的触点状态,而是指继电器线圈是否得电。
“常闭”指控制器上电后继电器线圈立即得电工作,“常开”指控制器上电后继电器线圈不得电。
保护模式下,A继电器的触点(14#/15#)为常闭接点,一般串联在电动机控制接触器线圈回路中,但当控制器上电正常工作时,A继电器立即得电吸合,仅在失电或发生故障保护后方再次断开。
漏电时,接地保护功能自动退出。
②控制器不带通讯功能时型号为ST501,增选通讯功能时型号为ST502(Profibus-DP),ST503(Modbus-RTU)3、控制器保护模式下的典型接线图器才自动闭合,允许电机再次起动运行。
保护模式下控制器提供装置失电/自诊断、故障跳闸等故障接点输出(图中19、20、21),其中自诊断接点为常闭,控制器得电正常工作时为常开,当控制器自检到装置故障或失电时变为常闭。
故障跳闸接点为常开,只有当控制器检测到故障并按规定特性保护动作时变为常闭。
分析排除故障后需按复位按钮方可清除故障指示和故障接点信号。
保护模式下控制器可据用户需要增选电压功能、电动机绕组热保护功能、漏电保护功能、4~20mA模拟量输出功能、通讯功能等。
ST500智能型电机控制器技术说明书
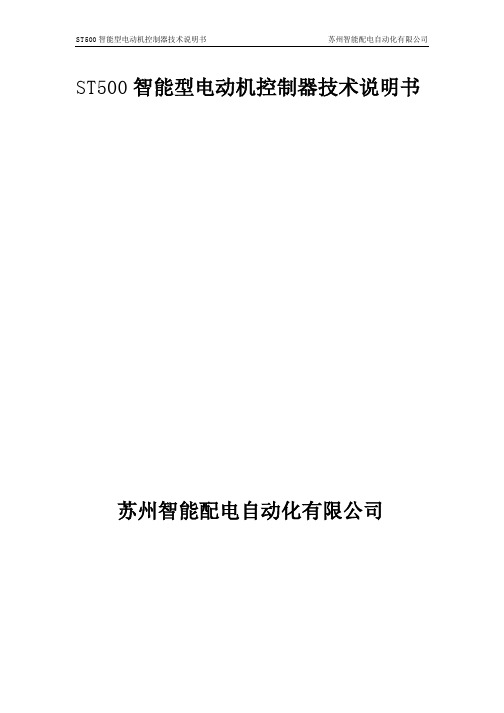
自耦变压器起动(三继电器) 通讯功能 RS485 接口
通讯协议:Modbus-Rtu、Profibus-Dp
苏州智能配电自动化有限公司
功能配置
标配功能
增选功能
√
√
√
√
√
√
√
√ (温度保护)
√ (漏电保护)
√ (电压功能)
√
(选一种)
无
可选一种
4
ST500 智能型电动机控制器技术说明书
二. 技术参数……………………………………………………………………… 17
4.1 符号对照表………………………………………………………………… 17 4.2 测量显示误差……………………………………………………………… 17 4.3 保护设定参数……………………………………………………………… 18 4.4 各种保护特性说明………………………………………………………… 20
4.4.1 过负载保护 4.4.2 缺相不平衡保护 4.4.3 接地漏电保护 4.4.4 欠电流保护 4.4.5 堵转保护 4.4.6 过热保护 4.4.7 欠压保护 4.4.8 过压保护 4.4.9 欠功率保护 4.4.10 起动加速超时保护 4.4.11 外部故障保护 4.4.12 相序保护
五、特殊控制功能说明…………………………………………………… 25
苏州智能配电自动化有限公司
3
ST500 智能型电动机控制器技术说明书
息,报警信息,故障信息,可以进行参数设定(保护定值,系统参数等),可以输入操作控制 命令(如起动,停车等)。
ST500 手持编程器是一种手持设备,可用来对控制器进行参数整定和各种信息查询, 其功能类似于 ST522 显示模块,但不需和控制器一对一配套,仅是在现场调整参数或维护 查询时才用。
接触器配ST500智能型电动机控制器使用说明(直接启动模式)

ST500智能型电动机控制器(直接启动模式)使用说明1、ST500控制器端子功能说明2、控制器的应用电动机的综合保护、测量功能、各种控制功能由ST500完成;参数显示、参数设定、报警、故障、管理信息查询等功能由ST522完成。
当控制器上电时,首先通过控制器检测CJ接触器是否在释放状态,如果接线不正确控制器报“接线错误”;如果接线正确时控制器ST522显示“起动准备就序”缺省信息窗口。
当ST500接收到起动命令时,ST500内部A继电器吸合,则CJ接触器得电吸合,控制器检测到CJ吸合,起动过程中“起动”灯亮,ST522显示“正在起动”进程状况,表示电动机在起动过程中。
起动结束后“起动”灯熄灭,ST522显示“正在运行”的缺省窗口。
停车时,ST500内部A继电器分开,CJ接触器释放,主回路断开,电动机停车。
3、ST522显示模块在保护方式下,ST522操作显示模块和ST500控制器配合使用(通过T9**—02串口线连接),是ST500的可选部件之—,通过ST522可以实时显示电动机的各种测量参数;调整各种参数(保护定值、起动参数、系统参数);查询各种故障信息/报警信息/DI和D0状态;检测各种管理信息。
直接起动模式下ST522面板功能定义如下:3.1 指示灯“停车”指示当前电动机为停车状态。
“起动”指示电动机的停车和运行的中间状态,包括起动和转换过程。
“运行”指示当前电动机处于正常工作状态。
“报警”指示灯点亮时表示有非跳闸故障报警发生。
“故障”闪烁表示有跳闸故障,当前在处理过程中;恒亮表示当前处于故障跳闸状态。
3.2 功能键“起动A”在本地权限下,此按键可以控制电动机起动运行。
该控制按键据需要可锁定不用。
“停车”在本地权限下,此按键可以控制运行电动机停车。
该控制按键据需要可锁定不用。
“复位”清除故障显示,退出故障跳闸状态,但不能清除热容。
“返回”、“确认”“↑”、“↓”四个功能键用于参数设定和参数查询。
ST官方电机控制套件用户手册

ST官⽅电机控制套件⽤户⼿册UM0709User ManualSTM8/128-MCKIT motor control starter kit 1 IntroductionThe STM8/128-MCKIT starter kit is an integrated system designed to provide a complete, ready-to-use motor control application developed around the STMicroelectronics STM8 microcontroller.This starter kit is particularly suited to drive 3-phase brushless motors (either AC induction or permanent magnet types) and demonstrates how effectively the STM8 microcontrollers can be used in real-world motor control applications.●Drive is based on scalar control (BLDC or ACIM) for three-phase motors.●Position and/or speed measurement is implemented using Hall sensors or a tachometer.●Sensorless control is also implemented.●The inverter is driven using the PWM modulation technique.The STM8/128-MCKIT starter kit can be run in various ways:●As a plug-and play demo, out of the box, with the provided BLDC motor, in sensorless speed control mode.●With an AC induction motor, after reprogramming the microcontroller, in open loop or in speed control mode.However, the main advantage of the STM8/128-MCKIT is that you can use it to create your own applications and re-program the STM8 microcontroller. Y ou can develop your own applications using the dedicated software libraries provided in the starter kit in conjunction with a third-party IDE and C compiler.This manual describes:●The STM8/128-MCKIT starter kit components, and how to set up the hardware to runthe provided BLDC motor or an AC induction motor.●How to run the STM8/128-MCKIT starter kit in standalone mode.●The BLDC daughterboard (MB843).For information about the STM8 microcontroller features, refer to the datasheet. The STM8 evaluation board features, peripherals, and connectors are described in the STM8/128-EVAL user manual (UM0482).For information on the BLDC and AC induction motor software libraries and how to use them in motor control application development projects, refer to the STM8S three-phase BLDC software library (UM0708) and the STM8S three-phase AC induction motor software library user manual (UM0712) respectively. Y ou will find these manuals, and all related documentation on the STM8/128-MCKIT CD-ROM.June 2009Doc ID 15774 Rev 21/22/doc/219f7fae551810a6f52486d0.htmlContents UM0709Contents1Introduction . . . . . . . . . . . . . . . . . . . . . . . . . . . . . . . . . . . . . . . . . . . . . . . . 12Safety warnings . . . . . . . . . . . . . . . . . . . . . . . . . . . . . . . . . . . . . . . . . . . . . 42.1General . . . . . . . . . . . . . . . . . . . . . . . . . . . . . . . . . . . . . . . . . . . . . . . . . . . . 42.2Intended use . . . . . . . . . . . . . . . . . . . . . . . . . . . . . . . . . . . . . . . . . . . . . . . 42.3Operation . . . . . . . . . . . . . . . . . . . . . . . . . . . . . . . . . . . . . . . . . . . . . . . . . . 42.4Important notice to users . . . . . . . . . . . . . . . . . . . . . . . . . . . . . . . . . . . . . . 43STM8/128-MCKIT hardware setup . . . . . . . . . . . . . . . . . . . . . . . . . . . . . . 53.1Package checklist . . . . . . . . . . . . . . . . . . . . . . . . . . . . . . . . . . . . . . . . . . . . 53.1.1Hardware . . . . . . . . . . . . . . . . . . . . . . . . . . . . . . . . . . . . . . . . . . . . . . . . . 53.1.2Software . . . . . . . . . . . . . . . . . . . . . . . . . . . . . . . . . . . . . . . . . . . . . . . . . . 63.1.3Documentation . . . . . . . . . . . . . . . . . . . . . . . . . . . . . . . . . . . . . . . . . . . . . 63.1.4Components not provided . . . . . . . . . . . . . . . . . . . . . . . . . . . . . . . . . . . . 63.2Brushless DC motor (default) . . . . . . . . . . . . . . . . . . . . . . . . . . . . . . . . . . . 73.3AC induction motor . . . . . . . . . . . . . . . . . . . . . . . . . . . . . . . . . . . . . . . . . . . 73.4Hardware configuration for a BLDC motor (default) . . . . . . . . . . . . . . . . . . 83.5Hardware configuration for an AC induction motor . . . . . . . . . . . . . . . . . . 113.6Power supply connections . . . . . . . . . . . . . . . . . . . . . . . . . . . . . . . . . . . . 134BLDC daughterboard MB843 . . . . . . . . . . . . . . . . . . . . . . . . . . . . . . . . . 144.1Features . . . . . . . . . . . . . . . . . . . . . . . . . . . . . . . . . . . . . . . . . . . . . . . . . . 144.2Layout . . . . . . . . . . . . . . . . . . . . . . . . . . . . . . . . . . . . . . . . . . . . . . . . . . . . 154.3Jumper configuration . . . . . . . . . . . . . . . . . . . . . . . . . . . . . . . . . . . . . . . . 164.4Schematic . . . . . . . . . . . . . . . . . . . . . . . . . . . . . . . . . . . . . . . . . . . . . . . . . 175Running the starter kit . . . . . . . . . . . . . . . . . . . . . . . . . . . . . . . . . . . . . . 185.1Running the BLDC motor . . . . . . . . . . . . . . . . . . . . . . . . . . . . . . . . . . . . . 185.2Running the AC induction motor . . . . . . . . . . . . . . . . . . . . . . . . . . . . . . . 18 6Creating your custom application . . . . . . . . . . . . . . . . . . . . . . . . . . . . . 19 Appendix A Additional information. . . . . . . . . . . . . . . . . . . . . . . . . . . . . . . . . . . . 20 2/22 Doc ID 15774 Rev 2UM0709ContentsA.1Modification of MB631 for BLDC drive . . . . . . . . . . . . . . . . . . . . . . . . . . . 20A.2Recommended reading. . . . . . . . . . . . . . . . . . . . . . . . . . . . . . . . . . . . . . . 20A.3Software upgrades . . . . . . . . . . . . . . . . . . . . . . . . . . . . . . . . . . . . . . . . . . 20A.4Getting technical support . . . . . . . . . . . . . . . . . . . . . . . . . . . . . . . . . . . . . 20 Revision history . . . . . . . . . . . . . . . . . . . . . . . . . . . . . . . . . . . . . . . . . . . . . . . . . . . . 21Doc ID 15774 Rev 23/22Safety warnings UM07094/22 Doc ID 15774 Rev 22 Safety warnings2.1 GeneralIn operation, the STM8/128-MCKIT starter kit has non-insulated wires, moving or rotatingparts (when connected to a motor), as well as hot surfaces. In case of improper use, incorrect installation or misuse, there is danger of serious personal injury and damage to property. All operations, installation and maintenance are to be carried out by skilled technical personnel (applicable accident prevention rules must be observed).When the power board is supplied with voltages greater than 30 V AC/DC, all of the board and components must be considered “hot”, and any contact with the board must be avoided. The operator should stay away from the board as well (risk of projection of material in case of components destruction, especially when powering the board with high voltages).The rotating parts of motors are also a source of danger.The STM8/128-MCKIT starter kit contains electrostatic sensitive components which may be damaged through improper use.Note:The board's power supply must be electrically insulated before connecting any cables that link the PC to the board, such as the STX-RLINK or a serial cable. Otherwise an earth/ground loop would occur, as there is no insulation board.2.2 Intended useThe STM8/128-MCKIT starter kit is made of components designed for demonstrationpurposes and must not be included in electrical installations or machinery. Instructions about the setup and use of the STM8/128-MCKIT starter kit must be strictly observed.2.3 OperationAfter disconnecting the board from the voltage supply, several parts and power terminals must not be touched immediately because of possible energized capacitors or hot surfaces.2.4 Important notice to usersWhile every effort has been made to ensure the accuracy of all information in this document, STMicroelectronics assumes no liability to any party for any loss or damage caused by errors or omissions or by statements of any kind in this document, its updates, supplements, or special editions, whether such errors are omissions or statements resulting from negligence, accident, or any other cause.Doc ID 15774 Rev 25/223 STM8/128-MCKIT hardware setupThis section provides a detailed description of the components included in the STM8/128-MCKIT starter kit. It also describes the default settings for a brushless DC motor (BLDC), and explains how to change them to use an AC induction motor.3.1 Package checklistFigure 1 shows the layout and connections of the major components of the STM8/128-MCKIT starter kit.Figure 1.STM8/128-MCKIT layout3.1.1 HardwareThe STM8/128-MCKIT starter kit includes the following items:●The MB459B power board (1): This board is described in the MB459B power boarduser manual (UM0379) provided on the STM8/128-MCKIT CD-ROM.●The MB631 STM8 evaluation board (2): This board is described in the STM8/128-EVAL user manual (UM0482) provided on the STM8/128-MCKIT CD-ROM.●An MB843 BLDC daughterboard (3): This board is described in the chapter BLDC daughterboard MB843. The purpose of the BLDC daughterboard is to implement the BEMF detecting network and the current regulation/limitation network.●An STX-RLink USB–SWIM debugger (4): The RAISONANCE STX-RLink USB-JTAG debugger allows you to reprogram the Flash memory of the STM8 microcontroller and to debug the software before using the application in standalone mode.●A 24V DC SHINANO BLDC motor (5): The motor included in the STM8/128-MCKIT starter kit is a SHINANO inner rotor type 4-pole brushless DC motor with Hall sensor and encoder. For electrical specifications and mechanical dimensions, refer to the SHINANO datasheets on the STM8/128-MCKIT CD-ROM.●An auxiliary power supply block TR30R (6)●The following cables:–Motor cables (7)– A motor connector HE10 34-pin cable (8)– A USB cable (9)–One SWIM cable and the related adapter (10)–An auxiliary connector for BLDC sensorless HE10 20-pin cable (11)● A bag with three 0.1ohm resistors is included to configure the MB459B board toincrease the maximum motor nominal current level up to 5 amps.●The STM3210B-MCKIT CD-ROM.3.1.2 SoftwareThe STM8/128-MCKIT CD-ROM includes the BLDC and AC induction motor softwarelibraries.When you receive the STM8/128-MCKIT, the STM8 microcontroller is programmed bydefault with the BLDC sensorless firmware.3.1.3 DocumentationThe STM8/128-MCKIT CD-ROM also includes the following product documentation in PDFformat:●STM8Sxxx access line and performance line datasheets●STM8Sxxx reference manual●STM8/128-MCKIT motor control kit user manual (UM0709, the present manual)●STM8S three-phase BLDC software library v1.0 user manual (UM0708)●STM8S three-phase AC induction motor software library v1.0 user manual (UM0712)●STM8/128-EVAL user manual (UM0482)●MB459B power board user manual (UM0379)●SHINANO motor datasheet.In the box with the STM8/128-MCKIT, there is also:●The MCD product finder●Product flyers and brochures●The MCD miniROM● A guarantee record cardprovidednot3.1.4 ComponentsThe STM8/128-MCKIT starter kit does not include:● A power supply: To use the STM8/128-MCKIT starter kit with the provided BLDC motor, you need a 24V-3A minimum power supply.●An AC induction motor: The STM8/128-MCKIT can operate with an AC induction motor. The provided firmware is designed to operate with the SELNI induction motor. It can be ordered as an accessory with the following order code: ST7MC-MOT/IND. To use the STM8/128-MCKIT starter kit with the Selni AC induction motor, you need a 42V DC or32Veff AC power supply (polarity not important, earth connection recommended).6/22 Doc ID 15774 Rev 23.2 Brushless DC motor (default)The brushless DC motor (BLDC) is a rotating electric machine where the stator is a classic 3-phase stator like that of an induction motor and the rotor has surface-mounted permanent magnets. In this respect, the BLDC motor is equivalent to an induction motor where the air gap magnetic field is produced by a permanent magnet. The use of a permanent magnet to generate a substantial air gap magnetic flux makes it possible to design highly efficient motors.A BLDC motor is driven by trapezoidal currents coupled with the given rotor position. The generated stator flux together with the rotor flux, which is generated by a rotor magnet, defines the torque, and thus speed, of the motor. The trapezoidal currents have to be applied to the 3-phase winding system in a way that angle between the stator flux and the rotor flux is kept close to 90° to get the maximum generated torque. T o meet this criterion, the motor requires electronic control for proper operation.For a common 3-phase BLDC motor, a standard 3-phase power stage is used.The same power stage is used for AC induction and BLDC motors. The power stage utilizes six power transistors with independent switching. The power transistors are switched in the also called six step operation.3.3 AC induction motorThe AC induction motor is a rotating electric machine designed to operate from a 3-phase source of alternating voltage.The stator is a classic 3-phase stator with the winding displaced by 120°.The most common type of induction motor has a squirrel cage rotor in which aluminum conductors or bars are shorted together at both ends of the rotor by cast aluminum end rings. When three currents flow through the three symmetrically placed windings, a sinusoidally distributed air gap flux generating the rotor current is produced. The interaction of the sinusoidally distributed air gap flux and induced rotor currents produces a torque on the rotor. The mechanical angular velocity of the rotor is lower then the angular velocity of the flux wave by so called slip velocity.In adjustable speed applications, AC induction motors are powered by inverters. The inverter converts DC power to AC power at the required frequency and amplitude.The inverter consists of three half-bridge units where the upper and lower switches are controlled complementarily. As the power device's turn-off time is longer than its turn-on time, some dead-time must be inserted between the turn-off of one transistor of the half bridge and turn-on of its complementary device.The output voltage is mostly created by a pulse width modulation (PWM) technique. The 3-phase voltage waves are shifted 120° to each other and thus a 3-phase motor can be supplied.Doc ID 15774 Rev 27/223.4 Hardware configuration for a BLDC motor (default)This section describes the procedure for operating the STM8/128-MCKIT with a BLDC motor.The default settings that are present on the STM8 evaluation board and on the power board when you receive the STM8/128-MCKIT starter kit are intended for a BLDC motor.When you are using the BLDC motor, follow these steps:1.Verify that all the jumpers on the power board (MB459B) are in their default position. Refer to Table1: MB459B power board jumper settings for a BLDC motor (default) for information on jumper settings, and if necessary, to the MB459B power board User Manual for the location of the jumpers on the board.2. Verify that all of the STM8 evaluation board (MB631) jumpers are in their default position. Refer to T able2: STM8 evaluation board jumper settings for a BLDC motor (default) for information on jumper settings, and if necessary, to the STM8/128-EVAL board User Manual for the location of jumpers on the board.3. Verify that all of the BLDC daughterboard (MB843) jumpers are in their default position. Refer to Table3: BLDC daughterboard MB843 jumper settings for a BLDC motor (default) for information on jumper settings.4. Verify that the BLDC daughterboard (MB843) is fitted on top of STM8/128-EVAL board through the CN1 and CN5 connectors (see Figure2).5. Verify that the adapter board (MB844) is fitted on top of power board (MB459B) through the J4 connector (see Figure2).6. Verify that the BLDC daughterboard (MB843) and the adapter board (MB844) are connected with the provided 20-pin auxiliary connector cable for BLDC sensorless (see Figure2).7. Verify that the BLDC motor cables are correctly plugged into the power board's MOTOR connectors (J5 and J8). The power board (MB459B), the STM8 evaluation board(MB631), and the provided BLDC motor are already assembled together over a metal support when you receive the kit.8. Power up the STM8 evaluation board with the auxiliary power supply block TR30R.9. Power up the power board by connecting the output terminals of your DC power supply to the MAINS connector (J3). The provided voltage must be 24V DC and your power supply must be able to provide a current of 3A.The STM8/128-MCKIT is now ready to run with the BLDC motor.8/22 Doc ID 15774 Rev 2Doc ID 15774 Rev 29/22Figure 2.STM8/128-MCKIT assembly Caution:Before supplying the board, double check proper connections, make sure that there are no metal parts on, below or around the PCB and that there are no undesired earth/ground loops due to measuring equipment such as an oscilloscope.Caution:Be sure that the STM8/128-EVAL used is marked with (MB631/2) or with (MB631); in the second case you must also check the required modifications reported in the Appendix Section A.1: Modification of MB631 for BLDC drive .Note:Not all the default positions of the jumper are coincident with the silk-screen printing. The jumper settings that are different from the silk-screen printing are highlighted in the Table 1: MB459B power board jumper settings for a BLDC motor (default) and Table 2: STM8 evaluation board jumper settings for a BLDC motor (default).Table 1.MB459B power board jumper settings for a BLDC motor (default)Jumper Setting for the SHINANO 24VBLDC motor providedSetting for a high-voltageBLDC motorW1“<35V only”“<35V only” or “HIGH VOLTAGE”W4Not presentW5PresentW6PresentW7Not presentW8Not presentW9Not presentW10Present and soldered on reverse position of silk-screen printingW11PresentW12Not presentW13Not presentW14PresentW15Not presentW16Present and set on reverse position of silk-screen printingW17Not presentW18Not presentW19Not presentTable 2.STM8 evaluation board jumper settings for a BLDC motor (default) Jumper SettingJP1Present between 1-2JP2PresentJP3Set to PSU position to supply the STM8 evaluation board through the jack (CN6) And set to DTB position to supply the BLDC daughterboard (MB843)JP4PresentJP5Not presentJP6Present between 1-2 JP7Not presentJP8PresentJP9Not presentJP10PresentJP11Present between 2-3 JP12Present between 1-2JP13Present between 1-2 to configure the HW for the DAC functionality Or present between 2-3 to configure the HW for the dissipative brakeJP14Not present10/22 Doc ID 15774 Rev 2Table 3.BLDC daughterboard MB843 jumper settings for a BLDC motor (default)Jumper SettingJ1Present and set on default position of silk-screen printingJ2Present and set on default position of silk-screen printingJ3Present and set on default position of silk-screen printingJ4Present and set on default position of silk-screen printingJ5Present and set on default position of silk-screen printing (SENSORLESS)J13Present and set on default position of silk-screen printing (VARIABLE)3.5 Hardware configuration for an AC induction motorThis section describes the procedure for operating the STM8/128-MCKIT with an ACinduction motor. Y ou must change the default settings that are present on the STM8evaluation board and on the power board when you receive the STM8/128-MCKIT starter kitbecause they are intended for a PMSM motor. When you are running the AC inductionmotor, follow these steps:1.Remove the BLDC daughterboard (MB843) from the STM8/128-EVAL evaluation board(MB631).2. Remove the adapter board (MB844) from the power board (MB459B).3. Change the jumpers on the power board (MB459B) to the settings required for runningwith an AC induction motor. Refer to Table4: MB459B power board jumper settings foran AC induction motor for information on jumper settings, and if necessary, to theMB459B power board user manual for the location of the jumpers on the board.4. If the peak value of the motor phase current should be greater than 3 ampere, replacethe R4 shunt resistor on the power board (MB459B) by the 0.1ohm resistor included inthe bag delivered with the kit.5. Verify that the jumpers on the STM8/128-EVAL evaluation board (MB631) are in theirdefault position. Refer to T able5: STM8 eval board jumper settings for an AC inductionmotor for information on jumper settings, and if necessary, to the STM8/128-EVALboard user manual for the location of jumpers on the board.6. Disconnect the PMSM motor from the power board's MOTOR connectors (J5 and J8).The power board (MB459B), the STM8/128-EVAL evaluation board (MB631), and theprovided PMSM motor are already assembled together over a metal support when youreceive the kit.7. Connect your AC induction motor to the power board by connecting the three phases tothe J5 connector, and the tachometer cables to the J6 connector.8. Power up STM8/128-EVAL evaluation board with auxiliary power supply block TR30R.9. Power up the power board by connecting the output terminals of your DC power supplyto the MAINS connector (J3). The provided voltage must not be higher than 42V DC or32Veff AC (GND recommended).After re-programming the STM8S microcontroller with the ACIM motor control firmware, theSTM8/128-EVAL is now ready to run with your AC induction motor.Caution:Before supplying the board, double check proper connections, make sure that there are no metal parts on, below or around the PCB and that there are no undesired earth/groundloops due to measuring equipment such as an oscilloscope.Doc ID 15774 Rev 211/22Table 4.MB459B power board jumper settings for an AC induction motorJumper Settings for AC induction motor with tachometer feedbackW1“<35V only” or “HIGH VOLTAGE”W4Not presentW5PresentW6PresentW7Not presentW8Not presentW9Not presentW10Present and soldered on reverse position of silk-screen printingW11PresentW12PresentW13Not presentW14Not PresentW15Not presentW16Present and set on reverse position of silk-screen printingW17Not presentW18Not presentW19Not present12/22 Doc ID 15774 Rev 2Doc ID 15774 Rev 213/22Note:The jumper settings that are different from the silk-screen printing are highlighted in the Table 4: MB459B power board jumper settings for an AC induction motor and Table 5: STM8 eval board jumper settings for an AC induction motor .3.6 Power supply connectionsJ1 connector of power board (MB459B) provides a completely independent control of the DC bus voltage (power) and the +15V supply for the gate drivers. This is interesting for development purposes, when one needs to smoothly increase the motor's operating voltage from zero, while the gate drivers are operating with their nominal supply.When supplying the power stage with an external +15V power supply using the J1 connector, special care must be taken that:1. No jumpers are connected on jumper W1.2. The short circuit that replaces the D3 diode footprint must be open. This is to avoid having reverse current in the L7815 voltage regulator.Table 5.STM8 eval board jumper settings for an AC induction motorJumper Setting JP1Present between 1-2JP2PresentJP3Set to PSU position to supply the STM8 evaluation board through the jack (CN6)JP4Present JP5Not present JP6Present between 1-2JP7Not present JP8PresentJP9Present, if required to filter the noise from the tachogenerator signalJP10Present JP11Present between 2-3JP12Present between 1-2JP13Present between 1-2 to configure the HW for the DAC functionality Or present between 2-3 to configure the HW for the dissipative brakeJP14Not presentBLDC daughterboard MB843UM0709 4 BLDC daughterboard MB8434.1 FeaturesThe BLDC daughterboard MB843 is an extension of the STM8/128-EVAL evaluation boardMB631 required to implement the BLDC drive.It includes:● A BEMF detection network,● A current regulation/regulation network,● A neutral voltage reconstruction network.The board has been designed to be compatible with the voltage level applicable to thepower board MB459B (“<35V only” or “HIGH VOLTAGE”).The BEMF detection network allows the following strategies of BEMF sampling:●BEMF sampling during off time (ST patented method),●BEMF sampling during on time,●Dynamic method based on the duty cycle applied.For more details see the STM8S three-phase BLDC software library v1.0 (UM0708). Note:For applications that require a limited range of motor speed, for example if the ratio between maximum and minimum speed is below 4, it is possible to replace the BEMF detectingnetwork with a simple resistive voltage divider.The current regulation/regulation network is used to adapt the signal to perform the currentcontrol in the BLDC drive. Control is made possible by a special characteristic of the STM8microcontroller. See for more details the STM8S three-phase BLDC software library v1.0(UM0708).The neutral voltage reconstruction network is used to reconstruct the neutral voltage (alsocalled star point) of the motor in order to perform the BEMF sampling during the on time.Two strategies of the neutral point reconstruction are implemented by the board:●Bus voltage partitioning,●Star point reconstruction starting from the motor phases.Note:It is possible to configure either method (see Section4.3: Jumper configuration) but only the first is implemented by the firmware.Note:Even if bus partitioning is also performed in the power board MB459B, the partitioning performed by the MB843 makes use of a voltage partitioning that allows a better resolutionin the neutral voltage reconstruction.The board is easily configurable to run the BLDC drive in sensorless mode, or to use theHall sensors as position/speed feedback.14/22 Doc ID 15774 Rev 2UM0709BLDC daughterboard MB843Doc ID 15774 Rev 215/224.2 LayoutFigure 3.BLDC daughterboard MB843 layout1.J8-J12 connector for the 20-pin auxiliary connector cable for BLDC sensorless. This is used to provide the three motor phase voltage signals and the bus voltage signal to the daughterboard MB843. 2.Auxiliary phase voltage connector CN2 (optional input). It can be used alternatively to the J8-J12 connecting directly the motor phase voltage signals using custom wire connections. Using that connector you can tighten the cables with a screwdriverconnecting motor phase A in the pin 1, motor phase B in the pin 2, motor phase C in pin 3, the DC bus voltage in pin 4 and the ground in pin 5.3. Jumper J5 sets sensorless or sensored configuration.4. Jumper J13 sets the current reference or limitation.5.Potentiometer P1 sets the fixed current limitation.6. Jumper J47. Jumper J38. Jumper J29. Jumper J1BLDC daughterboard MB843UM070916/22 Doc ID 15774 Rev 24.3 Jumper configurationTable 6 describes the jumpers.Table 6.BLDC daughterboard MB843 jumper settingsJumperSettingDescriptionJ1Selects the motor neutral voltage reconstruction networkSet to default position of silk-screen printingBus voltage partitioningSet to reverse position of silk-screen printingStar point reconstruction starting from the motor phasesJ2,J3,J4Configures the BEMF attenuation networkSet to default position of silk-screen printingThree GPIOs perform the dynamic attenuation of the BEMFsignal this allows the sampling during off time, during ontime and the dynamic selection of the two methods.Set to reverse position ofsilk-screen printing Fixes the BEMF signals attenuation and frees the three GPIOsNot present。
SQX STX INTELLI+系列 电动执行机构使用手册说明书

SQX & STX INTELLI+系列电动执行机构使用手册(ATEX & IECEx)N R 1179_r e v .06_C NSQX STX系列1 安全须知下列文档也应被参考:a)IEC/ E N60079-14 标准 (易爆气体环境下的电气安装),b)IEC/EN60079-17 标准 (危险区域内的检查与维护操作),c) 其它涉及必须安装执行机构的区域的法令、政府规定、法律、指令、标准、流程及其它文档。
伯纳德不对因不遵守规则的行为而引起的后果负责。
我们的执行机构设计可用于易爆环境:组别 II -类别 2 蒸汽、雾气或气体 (G) 或粉尘 (D)。
对于气体可使用在区域 1 或 2,对于粉尘可使用在区域 21 或 22 。
执行机构 CE 标识我们的设备符合 ATEX 2014/34/UE 指令要求执行机构 IECEx 标识我们的设备符合 IECEx 认证执行机构 INMETRO IEx 标识我们的设备符合 INMETRO IEx 认证请仔细检查铭牌上的标识与安装区域的易爆环境类型、环境温度及允许设备表面温度是否相符。
执行机构的安装与维护必须由合格的、经过培训和认证的人员实施。
1.1 标识ATEX隔爆 “d”IECEx 隔爆 “d”IEx 隔爆 “d”制造商名称与地址BERNARD CONTROLS 4 rue d’Arsonval 95505Gonesse FranceBERNARD CONTROLS 4 rue d’Arsonval 95505Gonesse FranceBERNARD CONTROLS 4 rue d’Arsonval 95505Gonesse France执行机构类型Type STX...Type STX...Type STX...序列号与生产年份99605 001 - 201199605 001 - 201199605 001 - 2011认证号码INERIS 10 ATEX 0045 XIECEx INE 10.0017XIEx 12-IEx0226X特定标识II 2 GDc T135°C 认可审核机构号码 0080气体标识Ex d IIB T4 Gb Ex d IIB T4 Gb Ex d IIB T4 Gb 粉尘标识Ex tb IIIC T135°C DbEx tb IIIC T135°C DbEx tb IIIC T135°C Db环境温度-20°C +70°C-20°C +70°C-20°C +70°C警告使用前请仔细阅读本文件1.2 安装区域执行机构为 2 类防爆设备,根据标识可以使用在下面的区域:EPL = 设备保护等级. b= 高等级气体 (G) 与粉尘 (D).区域 1 (气体)与 21(粉尘):在正常操作过程中可能会偶尔出现易爆环境。
ST-3500 操作手冊说明书
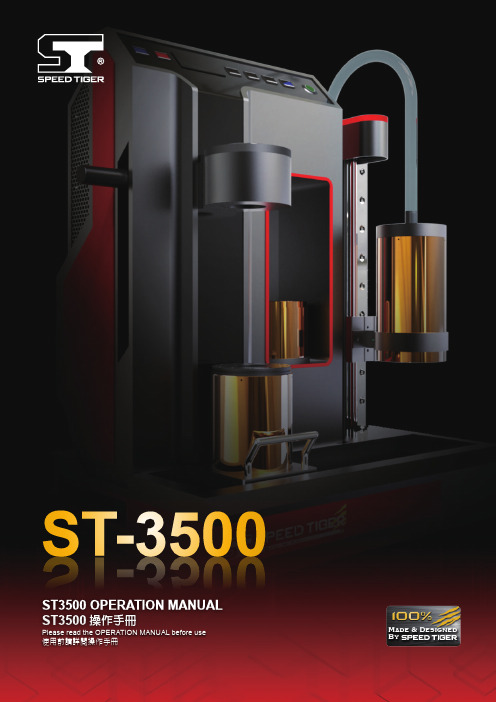
Made & Designed ByST-3500ST-3500ST3500 OPERATION MANUAL ST3500操作手冊Please read the OPERATION MANUAL before use 使用前請詳閱操作手冊ST3500ST3500 OPERATION MANUALT3500操作手冊Heating Sleeve 導熱套筒T oolholder Extension Base刀桿延長桿基座↓Round Tray刀桿隔環↓Index索 引▓Introduction產品介紹▓Standard Mode Operation標準模式操作說明Insert the tool燒結刀具Take out the tool取出刀具操作▓Custom Mode Operation自選模式操作說明▓Heating Sleeve Instruction導熱套筒使用說明▓Shrink Fit Program for Dual End Set雙頭龍燒結操作說明T wo M odes I ntroduction模式介紹Standard Mode 標準模式Heating time have been set up according to the size of shank. This setting is based on YAMAKEN's actual test results. If you would like to adjust heating seconds, please choose Custom Mode Operation.燒結時間已根據刀桿內孔徑不同設定完成。
燒結時間設定是依據山謙Move the induction coil to the properposition. (The distance from the top ofinduction coil to the top of chuck is about25 ~ 30mm)手持握把將加熱線圈移動至適合的位置(加熱頭端部至燒結刀桿鼻端距離約25~30mm)。
ST Power Module用户指南说明书
ST Power Module User GuideTable of Contents1 Introduction (3)1.1 Description (3)1.2 Features (3)1.3 Reference Design (3)1.4 Ordering Information (3)2 Functional Description (4)2.1 Block Diagram (4)2.2 Power Module Interfaces (4)2.3 DDR Memory Voltage Select Jumper (5)2.4 Remote Sense (6)2.5 Sequencing and Startup (6)2.6 Mechanical (7)2.7 Board Image (8)2.8 Revisions (8)1IntroductionThe purpose of this manual is to describe the functionality and contents of the ST Power Module from Avnet Electronics Marketing. This document includes instructions for operating the board, descriptions of the hardware features and explanations of the header signals and functionality.1.1 DescriptionThe Power Module is designed to be used with the Avnet Mini-Module Plus developmentsystem, or any system that meets the mechanical interconnect, pinout, voltage and currentrequirements set forth in this document. The power module operates off a 12VDC inputprovided from the target baseboard. The following table shows the output voltages generated by the power module, as well as the voltage banks each rail is tied to through the baseboard when used in the Mini-Module Plus system.Xilinx power bank / FMC Voltage Voltage (V) Max Current (A)Tolerance Vccint/Vccbram 16 3.00% Vcco 1.5 / 1.354 5.00% Vccaux/Vccaux_io/Vccadc/Vcco/MGTVccaux 1.86 5.00% Vccaux_io 22 3.00% Vcco 2.58 5.00% Vcco 3.38 5.00% MGTAVcc 16 3.00% MGTAVtt/MGTAVTTrcal 1.24 2.50%Table 1 – Output Voltages1.2 FeaturesThe Power Module provides a complete power solution through the use of 3 headers. 2 headers are used to provide power between the Avnet Power Module and the target board. The 3rd header is used to provide access to remote sensing for increased regulation accuracy.There is one configurable supply provided on the board which is selectable to be either 1.5V output or 1.35V output. This supply configurability allows the Power Module to work with the Mini-Module Plus system, supporting Mini Module cards populated with either 1.5V or 1.35V DDR3 memory.1.3 Reference DesignReference design files for this board are available at:/pom-sgs11.4 Ordering InformationPart Number HardwareAES-POM-SGS1-G ST Power Module2 Functional DescriptionThe power module provides 8 sequenced output voltages with controlled rise times from a 12VDC input. The supplies are designed to meet the current and regulation tolerances outlined in table 1.2.1 Block DiagramFigure 1 - Block Diagram2.2 Power Module InterfacesThe following tables show the pinouts for J1, J2 and J3. J1 and J2 provide power and ground to and from the baseboard. J1 (Samtec part # HPM-10-05-T-S) and J2 (Samtec part # HPM-08-05-T-S) provide power to and from the board. On the baseboard, J1 mates with Samtec part # HPF-10-01-T-S and J2 mates with Samtec part # HPF-08-01-T-S.Pin 1 2 3 4 5 6 7 8 9 10 Signal GND 1.5V/1.35V GND 1.8V GND2V GND 3.3V GND12VTable 2 - J1 PinoutPin1 2 3 4 5 6 7 8Signal GND 1V GND1V(MGT)GND 1.2V GND 2.5VTable 3 - J2 PinoutJ3 (Samtec part # FW-05-05-F-D-361-085) is in place to provide access for remote voltage sense. The mating connector on the baseboard is Samtec part # CLP-105-02-F-D. The signals on this header are tied directly to the load voltage pins. This header is pinned out left to right down the header as illustrated below:1 23 45 67 89 10Table 4 - J3 DiagramPins are defined as follows:Pin 2 4 6 8 10Signal 2.5Vrm 1Vmgtrm2Vrm 1.2Vrm GNDPin 1 3 5 7 9Signal 3.3Vrm 1.8Vrm 1Vrm 1.5Vrm GNDTable 5 - J3 PinoutPin 1 location on J3 is indicated on the silk screen on the PCB. Pin 1 on J1 and J2 are the right most pins when viewing the board header side up. Refer to Figure 2 for an illustration of these pin positions.2.3 DDR Memory Voltage Select JumperJP1 sets the output of the 1.5V / 1.35V regulator. JP1 is a 2 pin header with a jumper used to connect pins 1-2. Place the jumper on pins 1-2 to set the voltage to 1.5V. Leave the jumper open to set the voltage to 1.35V. The table below shows the jumper settings and corresponding output voltage.JP1 setting Output voltageON 1.5VOFF 1.35VTable 6 – JP1 Jumper SettingsSetting the voltage to 1.5V or 1.35V is dependent on the type of memory utilized on the target board. In the case of the K7 Mini-Module for example, the DDR memory used is 1.5V.WARNING: Do NOT power up the Power Module without the jumper set to either 1.5V or 1.35V.Powering the board without the jumper in place can result in board failure.2.4 Remote SenseRemote sense is used to compensate for the power supplies being located far from the load. J3 provides a low impedance path directly to the voltage pins on the load. By allowing access to the voltage actually being seen by the load, the regulator can adjust the output to be more accurate and compensate for impedance losses through components and the PCB.When using remote sense, the signals tied to the header are traces that are terminated right at the pin of the target load. In the Mini-Module Plus case, these voltage pins are terminated right at the pins on the FPGA. The signals are then routed as traces back to the remote sense header. It is important that the signals originate from as close to the target load as possible.The signals on these pins are then used as the set point by the regulators to regulate the output voltage. By using a signal directly tied to the load as the set point, the power supplies are able to better regulate the voltage at the intended load.2.5 Sequencing and StartupSequencing of the output voltages follows Xilinx specification for 7 Series devices as follows: Vccint (1V) -> Vccaux (1.8V) -> Vccaux_io (2V) -> VccoNote that sequencing requirements are not specified for the MGT rails, they may be powered at any point during start up. The diagram below illustrates the start up sequencing of the power module.1V Vccint1.8V Vccaux2V Vccaux_io1.35V / 1.5V Vcco2.5V Vcco3.3V Vcco1V MGT1.2V MGTTiming DiagramEach rail starts up between 0.2ms and 50ms to meet ramp requirements, as well as havemonotonic rises. The requirement for power down sequencing states that the 3.3V Vcco railcannot exceed the 1.8V Vccaux rail during shut down by more than 2.625V for longer than500ms. No additional power down circuitry is needed in the power module to meet thisrequirement.2.6 MechanicalThe Power Module meets the following geometry requirements:Max Component Height 0.4”Max Board Width 3.5”Max Board Length 5.5”Clearance Between Mated Boards0.45”(power module and baseboard)Table 5Along with meeting these geometry requirements, headers J1, J2, and J3 are placed on the bottom of the board according to the definition below:Figure 1 – Mechanical Header and Mounting Hole Locations These locations are based on a topside view looking through the board. The headers are placed on the bottom. J3 is measured to the center of the connector. The mounting holes are plated through holes with a 125mil diameter. The mounting holes are not electrically connected on the module.Pin 1 locations for J1, J2 and J3 are illustrated below in Figure 2. The view is looking down on the board with the connectors facing up.Figure 2 – Header Pin 1 Locations2.7 Board Image2.8 Revisions01 Initial Release Chris Ammann。
结构化文本(ST)编程参考手册
相 模块 在本手册中,将 GX Developer 软件包、可编程控制器 CPU 通过以下的总称、简称表
示。需要标明 关型号时,将记述 的型号。
总称/简称 ST FB
GX Developer
基本模式 QCPU 高性能模式 QCPU 过程 CPU 冗余 CPU
QCPU(Q 模式)
内容/对象模块 结构化文本的简称。 功能块的简称。 产品型号为 SW8D5C-GPPW、SW8D5C-GPPW-A、SW8D5C-GPPW-V、SW8D5C-GPPW-VA 的产 品统称名。 功能版本 B 以后的 Q00JCPU、Q00CPU、Q01CPU 的总称。 Q02(H)CPU、Q06CPU、Q12HCPU、Q25HCPU 的总称。 Q12PHCPU、Q25PHCPU 的总称。 Q12PRHCPU、Q25PRHCPU 的总称。 QOOJ、Q00、Q01、Q02(H)、Q06H、Q12H、Q12PH、Q12PRH、Q25H、Q25PH、 Q25PRHCPU 的总称。
1 概要
1 - 1到1 - 2
2 ST 程序创建步骤
2 - 1到2 - 2
3 ST 编程
3 - 1 到 3 - 16
新建用于 ST 的工程 .....................................................................3 - 1 定义标识 ..............................................................................3 - 3 输入程序 ..............................................................................3 - 8 对 ST 程序进行转换(编译)................................................................3 - 14
STM23Q集成式步进电机用户手册说明书
STM23Q集成式步进电机用户手册上海安浦鸣志自动化有限公司版本:1.001/07/2011版本:1.0 01/07/2011目录1 产品介绍 (4)1.1 特性 (4)1.2 功能框图 (5)1.3 安全须知 (6)2 开始前的准备 (7)2.1 安装上位机软件 (7)2.2 安装集成式电机 (7)2.3 选择合适的电源 (8)2.3.1 选择电源电压 (8)2.3.2 选择电源电流 (9)3 安装及接线 (12)3.1 连接电源 (12)3.2 通信接线 (13)3.2.1 用RS-232连接到PC (13)3.2.2 RS-422/485的通信接线 (14)3.2.3 分配地址 (16)3.3 输入与输出 (17)3.3.1 连接器引脚图 (17)3.3.2 STEP & DIR 数字输入信号 (18)3.3.3 EN 数字输入信号 (19)3.3.4 模拟量输入 (20)3.3.5 可编程输出 (20)4 软件配置 (22)4.1 软件菜单 (22)4.1.1 文件下拉菜单 (22)4.1.2 驱动器下拉菜单 (22)4.1.3 帮助菜单 (23)4.2 驱动器型号及固件版本 (23)4.3 电机参数配置(集成式电机) (24)4.3.1 运行电流 (24)4.3.2 加速/减速电流 (24)4.3.3 空闲电流 (24)4.3.4 空闲电流延时 (25)24.3.5 负载惯量 (25)4.3.6 电子阻尼/抗中频共振 (25)4.3.7 波形平滑 (25)4.4 控制模式及输入输出设置 (26)4.4.1 方向脉冲模式 (26)4.4.2 速度模式 (29)4.4.3 SCL 模式 (31)4.5 编码器功能 (33)4.6 上传/下载 (34)5 操作示例 (35)6 错误代码 (37)7 参考资料 (38)7.1 机械尺寸 (38)7.2 技术规格 (39)7.3 力矩速度曲线 (41)7.4 SCL 指令参考 (42)7.5 散热 (43)8 联系 MOONS’ (45)本用户手册所述内容仅适用于以下机型:3版本:1.001/07/20114版本:1.001/07/20111 产品介绍感谢您选择鸣志STM23Q 集成式电机产品。
ST500使用说明书
ST500智能型电动机控制器的使用说明书调试手册苏州万龙集团有限公司2006年4月目录一、控制器面板及端子布置 (3)1.1 控制器正面布置 (3)1.2 控制器侧边端子的端子号布置图及功能说明 (4)1.3控制器端子号定义 (4)二、ST522显示模块功能介绍 (7)三、普通用户菜单功能介绍 (7)四、高级用户菜单功能介绍 (10)五、参数设置参考 (11)5.1各种保护特性说明k系数设置参照表 (11)5.2 系统参数设置 (12)5.3 电动机功率范围和额定电流关系5.4 控制权限设定表六、各种运行方式典型二次接线图 (18)6.1、直接起动典型接线图6.2、保护模式下的典型接线图6.3、双向/可逆启动模式的典型接线图6.4、星三角起动模式的典型接线图七、常见故障分析及排除方法 (18)八、安全事项 (17)一、控制器面板及端子布置1.1 控制器正面布置(控制器的DI/DO端子功能可编程,其不同功能见1.3定义)万龙电器图1 控制器面板布置图序1: 开关量输入公共端(对应端子号1)。
序2: DI1开关量,按逆时针顺序 DI1~DI9 共9个可编程光隔开关量输入端。
序3:开关量输出 DO1,DO2公共端。
序4:开关量输出DO1。
序5:开关量输出DO2。
序6:开关量输出 DO3,DO4公共端。
序7:开关量输出 DO3,一般为常闭,正常工作时为常开。
序8:开关量输出 DO4。
序9:电源输入端子(对应端子号17,18)。
序10:指示灯:故障指示灯,在故障报警延时过程中闪烁,发生故障跳闸后恒亮。
总线提示灯,在远程通讯建立后恒亮,未建立时不亮。
运行指示灯,在运行状态下闪烁,在停车时恒亮。
序11:复位按键,用于清除状态指示和故障报警接点信号。
序12:通讯接口,用于连接远程通讯网络。
序13:用于连接显示模块ST522接口。
插页:为增加继电器的容量,采用增加ST202模块的方法,具体接线图如下:101817B C COM DA DO2DO1DO4DO3A DCOMC B ST202模块苏州万龙集团有限公司- 5 -1.3.2 控制器DI/DO端子的可编程功能编号说明见下表控制器光隔开关量输入端子最多同时用9个,继电器输出最多同时用4个。
- 1、下载文档前请自行甄别文档内容的完整性,平台不提供额外的编辑、内容补充、找答案等附加服务。
- 2、"仅部分预览"的文档,不可在线预览部分如存在完整性等问题,可反馈申请退款(可完整预览的文档不适用该条件!)。
- 3、如文档侵犯您的权益,请联系客服反馈,我们会尽快为您处理(人工客服工作时间:9:00-18:30)。
UM0709User ManualSTM8/128-MCKIT motor control starter kit 1 IntroductionThe STM8/128-MCKIT starter kit is an integrated system designed to provide a complete,ready-to-use motor control application developed around the STMicroelectronics STM8microcontroller.This starter kit is particularly suited to drive 3-phase brushless motors (either AC inductionor permanent magnet types) and demonstrates how effectively the STM8 microcontrollerscan be used in real-world motor control applications.●Drive is based on scalar control (BLDC or ACIM) for three-phase motors.●Position and/or speed measurement is implemented using Hall sensors or atachometer.●Sensorless control is also implemented.●The inverter is driven using the PWM modulation technique.The STM8/128-MCKIT starter kit can be run in various ways:●As a plug-and play demo, out of the box, with the provided BLDC motor, in sensorlessspeed control mode.●With an AC induction motor, after reprogramming the microcontroller, in open loop or inspeed control mode.However, the main advantage of the STM8/128-MCKIT is that you can use it to create yourown applications and re-program the STM8 microcontroller. Y ou can develop your ownapplications using the dedicated software libraries provided in the starter kit in conjunctionwith a third-party IDE and C compiler.This manual describes:●The STM8/128-MCKIT starter kit components, and how to set up the hardware to runthe provided BLDC motor or an AC induction motor.●How to run the STM8/128-MCKIT starter kit in standalone mode.●The BLDC daughterboard (MB843).For information about the STM8 microcontroller features, refer to the datasheet. The STM8evaluation board features, peripherals, and connectors are described in the STM8/128-EVAL user manual (UM0482).For information on the BLDC and AC induction motor software libraries and how to use themin motor control application development projects, refer to the STM8S three-phase BLDCsoftware library (UM0708) and the STM8S three-phase AC induction motor software libraryuser manual (UM0712) respectively. Y ou will find these manuals, and all relateddocumentation on the STM8/128-MCKIT CD-ROM.June 2009Doc ID 15774 Rev 21/22Contents UM0709Contents1Introduction . . . . . . . . . . . . . . . . . . . . . . . . . . . . . . . . . . . . . . . . . . . . . . . . 12Safety warnings . . . . . . . . . . . . . . . . . . . . . . . . . . . . . . . . . . . . . . . . . . . . . 42.1General . . . . . . . . . . . . . . . . . . . . . . . . . . . . . . . . . . . . . . . . . . . . . . . . . . . . 42.2Intended use . . . . . . . . . . . . . . . . . . . . . . . . . . . . . . . . . . . . . . . . . . . . . . . 42.3Operation . . . . . . . . . . . . . . . . . . . . . . . . . . . . . . . . . . . . . . . . . . . . . . . . . . 42.4Important notice to users . . . . . . . . . . . . . . . . . . . . . . . . . . . . . . . . . . . . . . 43STM8/128-MCKIT hardware setup . . . . . . . . . . . . . . . . . . . . . . . . . . . . . . 53.1Package checklist . . . . . . . . . . . . . . . . . . . . . . . . . . . . . . . . . . . . . . . . . . . . 53.1.1Hardware . . . . . . . . . . . . . . . . . . . . . . . . . . . . . . . . . . . . . . . . . . . . . . . . . 53.1.2Software . . . . . . . . . . . . . . . . . . . . . . . . . . . . . . . . . . . . . . . . . . . . . . . . . . 63.1.3Documentation . . . . . . . . . . . . . . . . . . . . . . . . . . . . . . . . . . . . . . . . . . . . . 63.1.4Components not provided . . . . . . . . . . . . . . . . . . . . . . . . . . . . . . . . . . . . 63.2Brushless DC motor (default) . . . . . . . . . . . . . . . . . . . . . . . . . . . . . . . . . . . 73.3AC induction motor . . . . . . . . . . . . . . . . . . . . . . . . . . . . . . . . . . . . . . . . . . . 73.4Hardware configuration for a BLDC motor (default) . . . . . . . . . . . . . . . . . . 83.5Hardware configuration for an AC induction motor . . . . . . . . . . . . . . . . . . 113.6Power supply connections . . . . . . . . . . . . . . . . . . . . . . . . . . . . . . . . . . . . 134BLDC daughterboard MB843 . . . . . . . . . . . . . . . . . . . . . . . . . . . . . . . . . 144.1Features . . . . . . . . . . . . . . . . . . . . . . . . . . . . . . . . . . . . . . . . . . . . . . . . . . 144.2Layout . . . . . . . . . . . . . . . . . . . . . . . . . . . . . . . . . . . . . . . . . . . . . . . . . . . . 154.3Jumper configuration . . . . . . . . . . . . . . . . . . . . . . . . . . . . . . . . . . . . . . . . 164.4Schematic . . . . . . . . . . . . . . . . . . . . . . . . . . . . . . . . . . . . . . . . . . . . . . . . . 175Running the starter kit . . . . . . . . . . . . . . . . . . . . . . . . . . . . . . . . . . . . . . 185.1Running the BLDC motor . . . . . . . . . . . . . . . . . . . . . . . . . . . . . . . . . . . . . 185.2Running the AC induction motor . . . . . . . . . . . . . . . . . . . . . . . . . . . . . . . 18 6Creating your custom application . . . . . . . . . . . . . . . . . . . . . . . . . . . . . 19 Appendix A Additional information. . . . . . . . . . . . . . . . . . . . . . . . . . . . . . . . . . . . 20 2/22 Doc ID 15774 Rev 2UM0709ContentsA.1Modification of MB631 for BLDC drive . . . . . . . . . . . . . . . . . . . . . . . . . . . 20A.2Recommended reading. . . . . . . . . . . . . . . . . . . . . . . . . . . . . . . . . . . . . . . 20A.3Software upgrades . . . . . . . . . . . . . . . . . . . . . . . . . . . . . . . . . . . . . . . . . . 20A.4Getting technical support . . . . . . . . . . . . . . . . . . . . . . . . . . . . . . . . . . . . . 20 Revision history . . . . . . . . . . . . . . . . . . . . . . . . . . . . . . . . . . . . . . . . . . . . . . . . . . . . 21Doc ID 15774 Rev 23/22Safety warnings UM07094/22 Doc ID 15774 Rev 22 Safety warnings2.1 GeneralIn operation, the STM8/128-MCKIT starter kit has non-insulated wires, moving or rotatingparts (when connected to a motor), as well as hot surfaces. In case of improper use,incorrect installation or misuse, there is danger of serious personal injury and damage toproperty. All operations, installation and maintenance are to be carried out by skilledtechnical personnel (applicable accident prevention rules must be observed).When the power board is supplied with voltages greater than 30 V AC/DC, all of the boardand components must be considered “hot”, and any contact with the board must be avoided.The operator should stay away from the board as well (risk of projection of material in caseof components destruction, especially when powering the board with high voltages).The rotating parts of motors are also a source of danger.The STM8/128-MCKIT starter kit contains electrostatic sensitive components which may bedamaged through improper use.Note:The board's power supply must be electrically insulated before connecting any cables thatlink the PC to the board, such as the STX-RLINK or a serial cable. Otherwise anearth/ground loop would occur, as there is no insulation board.2.2 Intended useThe STM8/128-MCKIT starter kit is made of components designed for demonstrationpurposes and must not be included in electrical installations or machinery. Instructionsabout the setup and use of the STM8/128-MCKIT starter kit must be strictly observed.2.3 OperationAfter disconnecting the board from the voltage supply, several parts and power terminalsmust not be touched immediately because of possible energized capacitors or hot surfaces.2.4 Important notice to usersWhile every effort has been made to ensure the accuracy of all information in this document,STMicroelectronics assumes no liability to any party for any loss or damage caused byerrors or omissions or by statements of any kind in this document, its updates, supplements,or special editions, whether such errors are omissions or statements resulting fromnegligence, accident, or any other cause.Doc ID 15774 Rev 25/223 STM8/128-MCKIT hardware setupThis section provides a detailed description of the components included in the STM8/128-MCKIT starter kit. It also describes the default settings for a brushless DC motor (BLDC),and explains how to change them to use an AC induction motor.3.1 Package checklistFigure 1 shows the layout and connections of the major components of the STM8/128-MCKIT starter kit.Figure 1.STM8/128-MCKIT layout3.1.1 HardwareThe STM8/128-MCKIT starter kit includes the following items:●The MB459B power board (1): This board is described in the MB459B power board user manual (UM0379) provided on the STM8/128-MCKIT CD-ROM.●The MB631 STM8 evaluation board (2): This board is described in the STM8/128-EVAL user manual (UM0482) provided on the STM8/128-MCKIT CD-ROM.●An MB843 BLDC daughterboard (3): This board is described in the chapter BLDCdaughterboard MB843. The purpose of the BLDC daughterboard is to implement theBEMF detecting network and the current regulation/limitation network.●An STX-RLink USB–SWIM debugger (4): The RAISONANCE STX-RLink USB-JTAGdebugger allows you to reprogram the Flash memory of the STM8 microcontroller andto debug the software before using the application in standalone mode.●A 24V DC SHINANO BLDC motor (5): The motor included in the STM8/128-MCKITstarter kit is a SHINANO inner rotor type 4-pole brushless DC motor with Hall sensorand encoder. For electrical specifications and mechanical dimensions, refer to theSHINANO datasheets on the STM8/128-MCKIT CD-ROM.●An auxiliary power supply block TR30R (6)●The following cables:–Motor cables (7)– A motor connector HE10 34-pin cable (8)– A USB cable (9)–One SWIM cable and the related adapter (10)–An auxiliary connector for BLDC sensorless HE10 20-pin cable (11)● A bag with three 0.1ohm resistors is included to configure the MB459B board toincrease the maximum motor nominal current level up to 5 amps.●The STM3210B-MCKIT CD-ROM.3.1.2 SoftwareThe STM8/128-MCKIT CD-ROM includes the BLDC and AC induction motor softwarelibraries.When you receive the STM8/128-MCKIT, the STM8 microcontroller is programmed bydefault with the BLDC sensorless firmware.3.1.3 DocumentationThe STM8/128-MCKIT CD-ROM also includes the following product documentation in PDFformat:●STM8Sxxx access line and performance line datasheets●STM8Sxxx reference manual●STM8/128-MCKIT motor control kit user manual (UM0709, the present manual)●STM8S three-phase BLDC software library v1.0 user manual (UM0708)●STM8S three-phase AC induction motor software library v1.0 user manual (UM0712)●STM8/128-EVAL user manual (UM0482)●MB459B power board user manual (UM0379)●SHINANO motor datasheet.In the box with the STM8/128-MCKIT, there is also:●The MCD product finder●Product flyers and brochures●The MCD miniROM● A guarantee record cardprovidednot3.1.4 ComponentsThe STM8/128-MCKIT starter kit does not include:● A power supply: To use the STM8/128-MCKIT starter kit with the provided BLDC motor,you need a 24V-3A minimum power supply.●An AC induction motor: The STM8/128-MCKIT can operate with an AC induction motor.The provided firmware is designed to operate with the SELNI induction motor. It can beordered as an accessory with the following order code: ST7MC-MOT/IND. To use theSTM8/128-MCKIT starter kit with the Selni AC induction motor, you need a 42V DC or32Veff AC power supply (polarity not important, earth connection recommended).6/22 Doc ID 15774 Rev 23.2 Brushless DC motor (default)The brushless DC motor (BLDC) is a rotating electric machine where the stator is a classic3-phase stator like that of an induction motor and the rotor has surface-mounted permanentmagnets. In this respect, the BLDC motor is equivalent to an induction motor where the airgap magnetic field is produced by a permanent magnet. The use of a permanent magnet togenerate a substantial air gap magnetic flux makes it possible to design highly efficientmotors.A BLDC motor is driven by trapezoidal currents coupled with the given rotor position. Thegenerated stator flux together with the rotor flux, which is generated by a rotor magnet,defines the torque, and thus speed, of the motor. The trapezoidal currents have to beapplied to the 3-phase winding system in a way that angle between the stator flux and therotor flux is kept close to 90° to get the maximum generated torque. T o meet this criterion,the motor requires electronic control for proper operation.For a common 3-phase BLDC motor, a standard 3-phase power stage is used.The same power stage is used for AC induction and BLDC motors. The power stage utilizessix power transistors with independent switching. The power transistors are switched in thealso called six step operation.3.3 AC induction motorThe AC induction motor is a rotating electric machine designed to operate from a 3-phasesource of alternating voltage.The stator is a classic 3-phase stator with the winding displaced by 120°.The most common type of induction motor has a squirrel cage rotor in which aluminumconductors or bars are shorted together at both ends of the rotor by cast aluminum endrings. When three currents flow through the three symmetrically placed windings, asinusoidally distributed air gap flux generating the rotor current is produced. The interactionof the sinusoidally distributed air gap flux and induced rotor currents produces a torque onthe rotor. The mechanical angular velocity of the rotor is lower then the angular velocity ofthe flux wave by so called slip velocity.In adjustable speed applications, AC induction motors are powered by inverters. Theinverter converts DC power to AC power at the required frequency and amplitude.The inverter consists of three half-bridge units where the upper and lower switches arecontrolled complementarily. As the power device's turn-off time is longer than its turn-ontime, some dead-time must be inserted between the turn-off of one transistor of the halfbridge and turn-on of its complementary device.The output voltage is mostly created by a pulse width modulation (PWM) technique. The 3-phase voltage waves are shifted 120° to each other and thus a 3-phase motor can besupplied.Doc ID 15774 Rev 27/223.4 Hardware configuration for a BLDC motor (default)This section describes the procedure for operating the STM8/128-MCKIT with a BLDCmotor.The default settings that are present on the STM8 evaluation board and on the power boardwhen you receive the STM8/128-MCKIT starter kit are intended for a BLDC motor.When you are using the BLDC motor, follow these steps:1.Verify that all the jumpers on the power board (MB459B) are in their default position.Refer to Table1: MB459B power board jumper settings for a BLDC motor (default) forinformation on jumper settings, and if necessary, to the MB459B power board UserManual for the location of the jumpers on the board.2. Verify that all of the STM8 evaluation board (MB631) jumpers are in their defaultposition. Refer to T able2: STM8 evaluation board jumper settings for a BLDC motor(default) for information on jumper settings, and if necessary, to the STM8/128-EVALboard User Manual for the location of jumpers on the board.3. Verify that all of the BLDC daughterboard (MB843) jumpers are in their default position.Refer to Table3: BLDC daughterboard MB843 jumper settings for a BLDC motor(default) for information on jumper settings.4. Verify that the BLDC daughterboard (MB843) is fitted on top of STM8/128-EVAL boardthrough the CN1 and CN5 connectors (see Figure2).5. Verify that the adapter board (MB844) is fitted on top of power board (MB459B) throughthe J4 connector (see Figure2).6. Verify that the BLDC daughterboard (MB843) and the adapter board (MB844) areconnected with the provided 20-pin auxiliary connector cable for BLDC sensorless (seeFigure2).7. Verify that the BLDC motor cables are correctly plugged into the power board's MOTORconnectors (J5 and J8). The power board (MB459B), the STM8 evaluation board(MB631), and the provided BLDC motor are already assembled together over a metalsupport when you receive the kit.8. Power up the STM8 evaluation board with the auxiliary power supply block TR30R.9. Power up the power board by connecting the output terminals of your DC power supplyto the MAINS connector (J3). The provided voltage must be 24V DC and your powersupply must be able to provide a current of 3A.The STM8/128-MCKIT is now ready to run with the BLDC motor.8/22 Doc ID 15774 Rev 2Doc ID 15774 Rev 29/22Figure 2.STM8/128-MCKIT assembly Caution:Before supplying the board, double check proper connections, make sure that there are nometal parts on, below or around the PCB and that there are no undesired earth/groundloops due to measuring equipment such as an oscilloscope.Caution:Be sure that the STM8/128-EVAL used is marked with (MB631/2) or with (MB631); in thesecond case you must also check the required modifications reported in the AppendixSection A.1: Modification of MB631 for BLDC drive .Note:Not all the default positions of the jumper are coincident with the silk-screen printing. Thejumper settings that are different from the silk-screen printing are highlighted in the Table 1:MB459B power board jumper settings for a BLDC motor (default) and Table 2: STM8evaluation board jumper settings for a BLDC motor (default).Table 1.MB459B power board jumper settings for a BLDC motor (default)Jumper Setting for the SHINANO 24VBLDC motor providedSetting for a high-voltageBLDC motorW1“<35V only”“<35V only” or “HIGH VOLTAGE”W4Not presentW5PresentW6PresentW7Not presentW8Not presentW9Not presentW10Present and soldered on reverse position of silk-screen printingW11PresentW12Not presentW13Not presentW14PresentW15Not presentW16Present and set on reverse position of silk-screen printingW17Not presentW18Not presentW19Not presentTable 2.STM8 evaluation board jumper settings for a BLDC motor (default) Jumper SettingJP1Present between 1-2JP2PresentJP3Set to PSU position to supply the STM8 evaluation board through the jack (CN6) And set to DTB position to supply the BLDC daughterboard (MB843)JP4PresentJP5Not presentJP6Present between 1-2 JP7Not presentJP8PresentJP9Not presentJP10PresentJP11Present between 2-3 JP12Present between 1-2JP13Present between 1-2 to configure the HW for the DAC functionality Or present between 2-3 to configure the HW for the dissipative brakeJP14Not present10/22 Doc ID 15774 Rev 2Table 3.BLDC daughterboard MB843 jumper settings for a BLDC motor (default)Jumper SettingJ1Present and set on default position of silk-screen printingJ2Present and set on default position of silk-screen printingJ3Present and set on default position of silk-screen printingJ4Present and set on default position of silk-screen printingJ5Present and set on default position of silk-screen printing (SENSORLESS)J13Present and set on default position of silk-screen printing (VARIABLE)3.5 Hardware configuration for an AC induction motorThis section describes the procedure for operating the STM8/128-MCKIT with an ACinduction motor. Y ou must change the default settings that are present on the STM8evaluation board and on the power board when you receive the STM8/128-MCKIT starter kitbecause they are intended for a PMSM motor. When you are running the AC inductionmotor, follow these steps:1.Remove the BLDC daughterboard (MB843) from the STM8/128-EVAL evaluation board(MB631).2. Remove the adapter board (MB844) from the power board (MB459B).3. Change the jumpers on the power board (MB459B) to the settings required for runningwith an AC induction motor. Refer to Table4: MB459B power board jumper settings foran AC induction motor for information on jumper settings, and if necessary, to theMB459B power board user manual for the location of the jumpers on the board.4. If the peak value of the motor phase current should be greater than 3 ampere, replacethe R4 shunt resistor on the power board (MB459B) by the 0.1ohm resistor included inthe bag delivered with the kit.5. Verify that the jumpers on the STM8/128-EVAL evaluation board (MB631) are in theirdefault position. Refer to T able5: STM8 eval board jumper settings for an AC inductionmotor for information on jumper settings, and if necessary, to the STM8/128-EVALboard user manual for the location of jumpers on the board.6. Disconnect the PMSM motor from the power board's MOTOR connectors (J5 and J8).The power board (MB459B), the STM8/128-EVAL evaluation board (MB631), and theprovided PMSM motor are already assembled together over a metal support when youreceive the kit.7. Connect your AC induction motor to the power board by connecting the three phases tothe J5 connector, and the tachometer cables to the J6 connector.8. Power up STM8/128-EVAL evaluation board with auxiliary power supply block TR30R.9. Power up the power board by connecting the output terminals of your DC power supplyto the MAINS connector (J3). The provided voltage must not be higher than 42V DC or32Veff AC (GND recommended).After re-programming the STM8S microcontroller with the ACIM motor control firmware, theSTM8/128-EVAL is now ready to run with your AC induction motor.Caution:Before supplying the board, double check proper connections, make sure that there are no metal parts on, below or around the PCB and that there are no undesired earth/groundloops due to measuring equipment such as an oscilloscope.Doc ID 15774 Rev 211/22Table 4.MB459B power board jumper settings for an AC induction motorJumper Settings for AC induction motor with tachometer feedbackW1“<35V only” or “HIGH VOLTAGE”W4Not presentW5PresentW6PresentW7Not presentW8Not presentW9Not presentW10Present and soldered on reverse position of silk-screen printingW11PresentW12PresentW13Not presentW14Not PresentW15Not presentW16Present and set on reverse position of silk-screen printingW17Not presentW18Not presentW19Not present12/22 Doc ID 15774 Rev 2Doc ID 15774 Rev 213/22Note:The jumper settings that are different from the silk-screen printing are highlighted in the Table 4: MB459B power board jumper settings for an AC induction motor and Table 5: STM8 eval board jumper settings for an AC induction motor .3.6 Power supply connectionsJ1 connector of power board (MB459B) provides a completely independent control of the DC bus voltage (power) and the +15V supply for the gate drivers. This is interesting for development purposes, when one needs to smoothly increase the motor's operating voltage from zero, while the gate drivers are operating with their nominal supply.When supplying the power stage with an external +15V power supply using the J1 connector, special care must be taken that:1. No jumpers are connected on jumper W1.2. The short circuit that replaces the D3 diode footprint must be open. This is to avoid having reverse current in the L7815 voltage regulator.Table 5.STM8 eval board jumper settings for an AC induction motorJumper Setting JP1Present between 1-2JP2PresentJP3Set to PSU position to supply the STM8 evaluation board through the jack (CN6)JP4Present JP5Not present JP6Present between 1-2JP7Not present JP8PresentJP9Present, if required to filter the noise from the tachogenerator signalJP10Present JP11Present between 2-3JP12Present between 1-2JP13Present between 1-2 to configure the HW for the DAC functionality Or present between 2-3 to configure the HW for the dissipative brakeJP14Not presentBLDC daughterboard MB843UM0709 4 BLDC daughterboard MB8434.1 FeaturesThe BLDC daughterboard MB843 is an extension of the STM8/128-EVAL evaluation boardMB631 required to implement the BLDC drive.It includes:● A BEMF detection network,● A current regulation/regulation network,● A neutral voltage reconstruction network.The board has been designed to be compatible with the voltage level applicable to thepower board MB459B (“<35V only” or “HIGH VOLTAGE”).The BEMF detection network allows the following strategies of BEMF sampling:●BEMF sampling during off time (ST patented method),●BEMF sampling during on time,●Dynamic method based on the duty cycle applied.For more details see the STM8S three-phase BLDC software library v1.0 (UM0708). Note:For applications that require a limited range of motor speed, for example if the ratio between maximum and minimum speed is below 4, it is possible to replace the BEMF detectingnetwork with a simple resistive voltage divider.The current regulation/regulation network is used to adapt the signal to perform the currentcontrol in the BLDC drive. Control is made possible by a special characteristic of the STM8microcontroller. See for more details the STM8S three-phase BLDC software library v1.0(UM0708).The neutral voltage reconstruction network is used to reconstruct the neutral voltage (alsocalled star point) of the motor in order to perform the BEMF sampling during the on time.Two strategies of the neutral point reconstruction are implemented by the board:●Bus voltage partitioning,●Star point reconstruction starting from the motor phases.Note:It is possible to configure either method (see Section4.3: Jumper configuration) but only the first is implemented by the firmware.Note:Even if bus partitioning is also performed in the power board MB459B, the partitioning performed by the MB843 makes use of a voltage partitioning that allows a better resolutionin the neutral voltage reconstruction.The board is easily configurable to run the BLDC drive in sensorless mode, or to use theHall sensors as position/speed feedback.14/22 Doc ID 15774 Rev 2UM0709BLDC daughterboard MB843Doc ID 15774 Rev 215/224.2 LayoutFigure 3.BLDC daughterboard MB843 layout1.J8-J12 connector for the 20-pin auxiliary connector cable for BLDC sensorless. This is used to provide the three motor phase voltage signals and the bus voltage signal to the daughterboard MB843.2.Auxiliary phase voltage connector CN2 (optional input). It can be used alternatively to the J8-J12 connecting directly the motor phase voltage signals using custom wire connections. Using that connector you can tighten the cables with a screwdriverconnecting motor phase A in the pin 1, motor phase B in the pin 2, motor phase C in pin 3, the DC bus voltage in pin 4 and the ground in pin 5.3. Jumper J5 sets sensorless or sensored configuration.4. Jumper J13 sets the current reference or limitation.5.Potentiometer P1 sets the fixed current limitation.6. Jumper J47. Jumper J38. Jumper J29. Jumper J1BLDC daughterboard MB843UM070916/22 Doc ID 15774 Rev 24.3 Jumper configurationTable 6 describes the jumpers.Table 6.BLDC daughterboard MB843 jumper settingsJumperSettingDescriptionJ1Selects the motor neutral voltage reconstruction networkSet to default position of silk-screen printingBus voltage partitioningSet to reverse position of silk-screen printingStar point reconstruction starting from the motor phasesJ2,J3,J4Configures the BEMF attenuation networkSet to default position of silk-screen printingThree GPIOs perform the dynamic attenuation of the BEMFsignal this allows the sampling during off time, during ontime and the dynamic selection of the two methods.Set to reverse position ofsilk-screen printing Fixes the BEMF signals attenuation and frees the three GPIOsNot presentRemoves the attenuation of the BEMF signalsJ5Sets sensorless or sensored configurationSet to default position of silk-screen printingSets the sensorless configurationSet to reverse position of silk-screen printingSets the Hall sensor configurationJ13Sets the current reference or limitationSet to default position of silk-screen printing With this setting the current reference or limitation isdynamically selected by the microcontroller using a filtered PWM signal. Is the only configuration that allows thecurrent regulation.Set to reverse position of silk-screen printingThe current limitation is fixed and the potentiometer P1 is used to set this value. In this case is possible to free the microcontroller PWM resource.。